Comment optimiser l'usinage de l'aluminium dans l'industrie automobile
Avec le secteur automobile augmentant son utilisation de pièces de moteur, de groupe motopropulseur, de pompe à eau et de système de freinage fabriquées en aluminium, le défi pour les équipementiers et leurs partenaires de la chaîne d'approvisionnement est de fournir des opérations de fraisage plus productives. La sélection de l'outillage est la clé d'une véritable différenciation sur le marché dans ce segment, où l'application correcte de fraises optimisées sur toute la gamme des opérations d'usinage des composants du moteur peut rapporter des dividendes significatifs.
Le nombre de moteurs en aluminium produits continue d'augmenter d'une année sur l'autre, tant pour les voitures particulières conventionnelles qu'hybrides. En fait, près de 100 millions sont désormais fabriqués chaque année. Ces moteurs abritent des pièces aux formes souvent complexes et qui, après fonderie, nécessitent une succession de fraisages variés mais indispensables.
Sandvik Coromant propose désormais une offre complète pour l'usinage de l'aluminium dans l'industrie automobile, du premier étage de cubage à l'ébauche, la semi-finition et la finition. Chaque outil de fraisage technique, cinq au total, est conçu pour offrir une qualité et un coût par pièce optimisés. Pour aider à atteindre ce dernier, certains outils de la gamme remplissent une combinaison de tâches, comme effectuer à la fois l'ébauche et la finition en une seule opération pour réduire les temps de cycle.
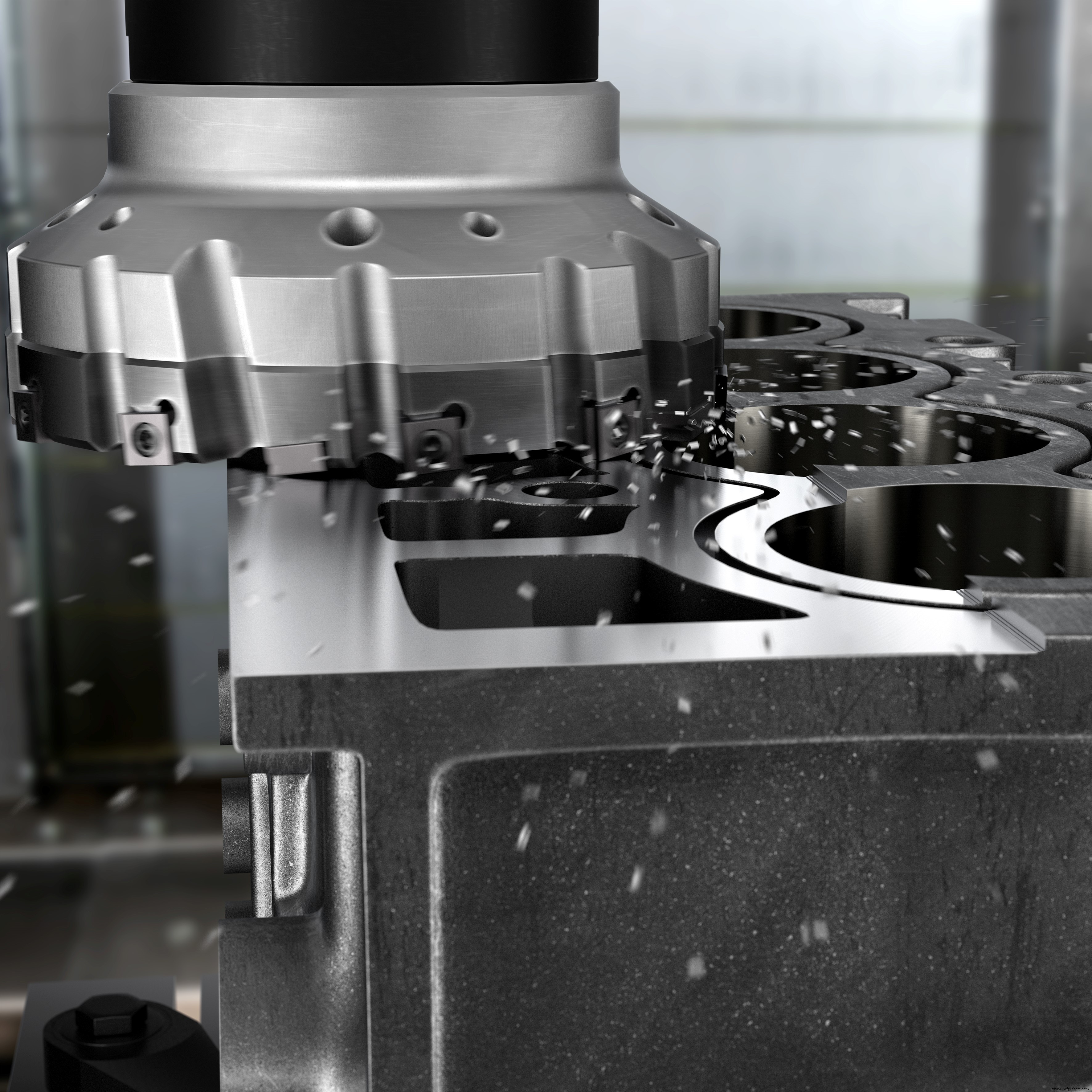
Un bon exemple est le M5C90, une fraise innovante qui combine ébauche et semi-finition en un seul outil. Le M5C90 est un outil de surfaçage à grande vitesse conçu sur mesure pour éliminer les longs temps de configuration chez le client. M5C90 travaille avec un nombre de dents réduit par rapport aux fraises conventionnelles, principalement grâce au positionnement radial et axial unique de la plaquette sur sa rangée de finition/diamètre intérieur (aucun réglage de la plaquette n'est nécessaire). Ce positionnement garantit un fraisage sans bavure et une finition de surface optimale sur les culasses, les blocs-cylindres, les pièces du système de freinage et tous les composants en aluminium où un large engagement de la fraise peut être obtenu (non applicable sur les pièces à paroi mince).
Pour donner un exemple des gains potentiels offerts par l'utilisation du M5C90, considérons un essai client en cours impliquant une soupape de corps de système de freinage en AlSi12Cu1. Doté d'un réseau de diamètre extérieur de 10 inserts en carbure et d'un diamètre intérieur de quatre inserts (plus un insert Wiper), l'outil est déployé à une vitesse de broche de 8000 tr/min, une vitesse de coupe de 4021 m/min. (13 192 pieds/min.) et une avance de 0,25 mm/dent (0,009 pouce/dent). De plus, la profondeur de coupe axiale est de 2 mm (0,078 po) avec une profondeur de coupe radiale de 140 mm (5,51 po), produisant un taux d'enlèvement de métal de 5 600 cm 3 /min. (342 po 3 /min.). Bien que la durée de vie totale de l'outil reste à déterminer, le même outil est toujours dans la machine après 18 mois de service.
Pour ceux qui ont besoin d'une fraise capable également de finir des pièces en aluminium à parois minces telles que des carters de boîtes de vitesses et des carters, Sandvik Coromant propose une autre fraise tout aussi efficace, la M5F90. Le M5F90 est un autre outil d'ébauche et de finition monocoup. Dédié à l'usinage de pièces en aluminium à paroi mince et aux opérations de surfaçage, le corps de fraise (25-80 mm, 0,98-3,15 pouce de diamètre) abrite des pointes PCD brasées. Chaque pointe contient à la fois une arête de dégrossissage et une arête de finition. La zone d'ébauche fonctionne comme un outil de fraisage conventionnel, avec toutes les arêtes de coupe sur le même diamètre et la même hauteur, tandis que la zone de finition se compose d'arêtes de coupe étagées radiales et axiales. Ce concept permet un pas serré pour un usinage sans bavure et une finition de surface exceptionnelle. Dans la courte vidéo ci-dessous, Sandvik présente les fraises de la série M5 pour l'usinage de l'aluminium automobile.
Des gains de temps impressionnants sont possibles, comme le montre un essai client impliquant le surfaçage d'une culasse en aluminium (haute teneur en Si). Ici, l'utilisation de M5F90 contre une fraise PCD spéciale fabriquée par un concurrent a non seulement permis de gagner 150 % de temps de cycle, mais a également éliminé la génération de bavures. Données de coupe incluses :vitesse de broche de 15 915 tr/min; 2000 m/min. (6562 pi/min.) vitesse de coupe ; une vitesse d'avance de 0,16 mm/dent (0,006 pouce/dent); et profondeur de coupe de 1,5 mm (0,06 po).
Dans un autre exemple M5F90, des réductions de temps de cycle de 44 % ont été obtenues sur un carter de chaîne en aluminium par rapport à l'utilisation d'une fraise indexable concurrente de 63 mm (2,48 po) de diamètre dotée de six plaquettes PCD. De plus, la solution a éliminé une opération d'ébavurage à la brosse auparavant nécessaire.
Un autre nouvel outil d'ingénierie est le M610, qui a été développé pour fraiser la face/le dessus du pont des blocs-cylindres de moteur avec des interfaces bimétalliques, généralement de l'aluminium et de la fonte grise (CGI).
Une gamme de propriétés thermiques et mécaniques rend l'usinage difficile lorsqu'il s'agit de matériaux bimétalliques. Les fraises existantes pour cette application sont complexes et nécessitent un ajustement, ce qui entraîne des débits compromis. De plus, ces outils provoquent souvent des éclats sur les parties GCI du composant.
En revanche, le M610 ne nécessite aucune configuration ni aucun réglage, et permet de déployer des vitesses d'avance élevées sans écaillage, bavure ou rayure des pièces. Cette capacité est importante car les imperfections de surface ont le potentiel de produire des fuites entre le bloc-cylindres et la culasse, ce qui compromet à son tour la puissance et les performances. Certains équipementiers automobiles mondiaux bénéficient déjà de l'adoption du M610.
Pour référencer un client en particulier, un énorme gain de compétitivité a été réalisé lors de la finition de la face de combustion sur les blocs moteurs bi-métalliques. Comparée à la fraise réglable à cartouches d'un concurrent, la M610 a amélioré la durée de vie de l'outil de 833 %, complétant plus de 4 000 pièces, par rapport à la fraise concurrente 480. De plus, la M610 a fonctionné à 10 fois la vitesse. Données de coupe pour la M610 à 15 plaquettes incluses :3000 m/min. (9843 pi/min.) vitesse de coupe ; une vitesse d'avance de 5720 mm/min. (225 pouces/min.); une vitesse de broche de 3820 RPM; une vitesse d'avance de 0,15 mm/dent (0,006 pouce/dent); et une profondeur de coupe sur l'aluminium de 0,5 mm (0,02 po) et sur la fonte de 0,05 mm (0,002 po).
D'autres outils de la famille incluent la fraise d'ébauche tangentielle M5Q90, qui effectue le cubage de première étape (premier usinage des faces après la coulée) en une seule opération sans bavure. L'outil est équipé de plaquettes tangentielles PCD qui offrent une action de coupe douce et stable pour réduire la consommation d'énergie et éliminer les vibrations.
Les culasses et les blocs en aluminium font partie des composants bénéficiant du M5Q90. A titre d'exemple, l'opération de cubage sur une culasse coulée consisterait typiquement à usiner la face d'arbre à cames, la face d'admission/sortie et la face de combustion. Dans une étude de cas client, le surfaçage rugueux de culasses moulées en alliage d'aluminium AS-9 sur un centre d'usinage horizontal a produit des résultats de durée de vie d'outil très impressionnants. A 3000 m/min. (9843 po/min.) vitesse de coupe, avance par dent de 0,2 mm (0,008 po) et profondeur de coupe axiale de 2,0 mm (0,079 po) (entièrement engagée à 40 mm (1,57 po), plus de 10 000 composants ont été terminés.
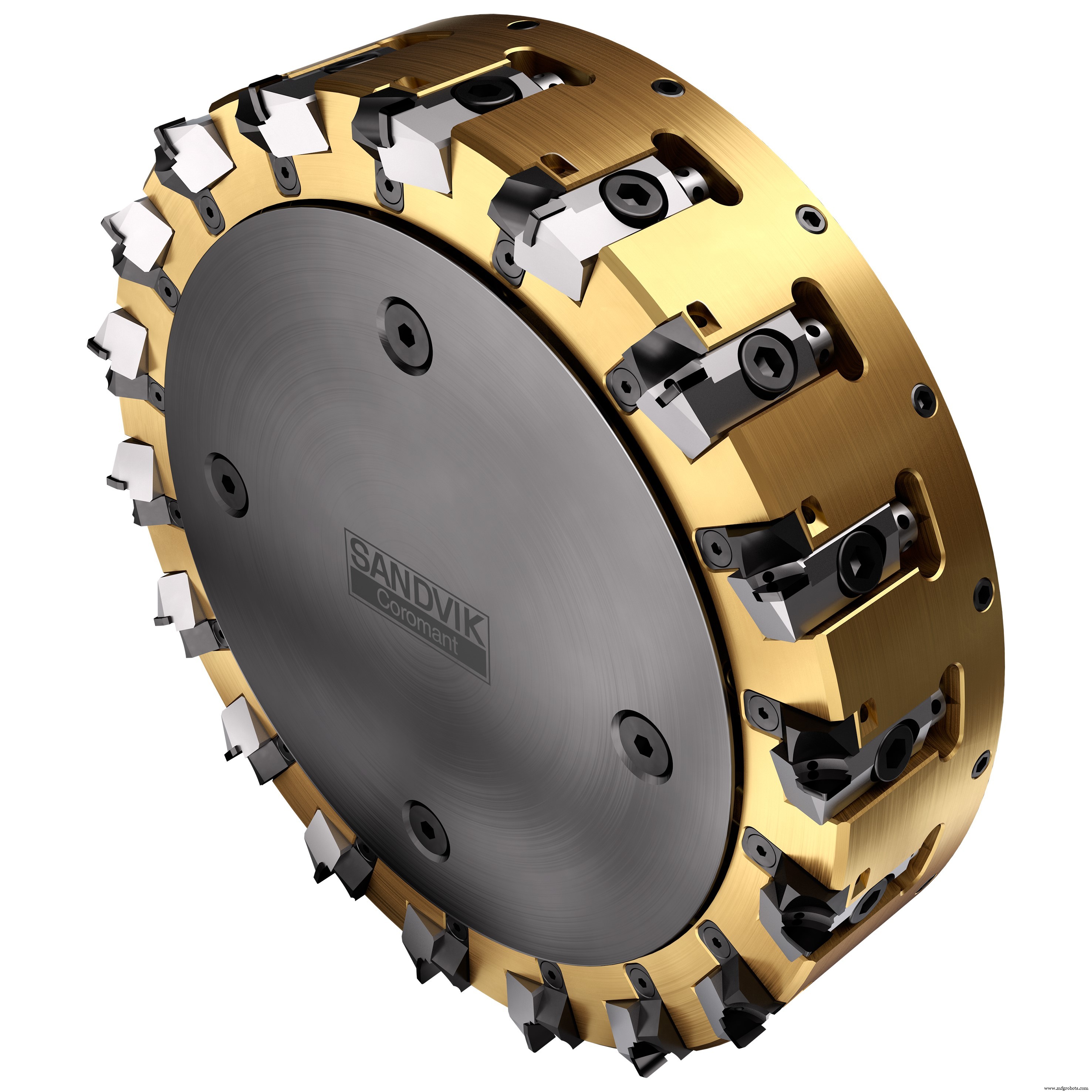
Un autre outil est le M5R90 pour l'ébauche/semi-finition de deuxième étape. Cette fraise standard fonctionne avec des cartouches réglables et prend en charge une profondeur de coupe allant jusqu'à 8 mm (0,315 po) avec un rayon de 0,4 ou 0,8 mm (0,016 ou 0,031 po) selon la cartouche utilisée. Les cartouches faciles à régler sont avantageuses dans de nombreuses applications automobiles, comme on a pu le constater lors d'un récent essai client impliquant le surfaçage d'un capot de moteur. Moulé à partir d'alliage d'aluminium MRHB Si12, le M5R90 s'est comporté extrêmement favorablement par rapport au coupeur concurrent en place. Basé sur des données de coupe identiques, le M5R90 a prolongé la durée de vie de l'outil de 8 000 à 10 000 pièces. De plus, la fraise concurrente devait être ajustée toutes les 1 000 pièces en raison du mouvement de la cartouche qui compromettait la finition de surface. En revanche, le M5R90 a produit 8 000 pièces avant qu'un ajustement de la cartouche ne soit nécessaire.
Également incluse dans la famille, la fraise à surfacer de superfinition M5B90 avec son positionnement axial et radial unique des plaquettes. Cette configuration, associée à la plaquette Wiper, garantit une coupe sans bavure avec une excellente qualité de surface, comme l'a récemment découvert un fabricant de culasses pour voitures particulières. L'entreprise rencontrait une instabilité de processus et des problèmes de bavures, tandis qu'un autre problème était la durée de vie imprévisible de l'insert, qui dépendait des réglages de la cartouche qui différaient d'une configuration à l'autre. Le passage à la fraise M5B90 a permis une opération de finition en douceur avec une usure prévisible et sans bavure. L'outil ne produit que des copeaux très fins, qui sont facilement éliminés pendant le processus de coupe pour éviter tout dommage à la face du composant. De plus, le passage au M5B90 a prolongé la durée de vie de l'outil de 30 000 à 45 000 pièces en moyenne.
CoroDrill ® et CoroTap ® Les outils de perçage et de taraudage de la famille peuvent également être proposés aux clients dans le cadre de la même famille de solutions pour l'usinage de composants automobiles en aluminium, tout comme la fraise standard CoroMill ® Fraise à surfacer Century 590.
Dans tous les cas, le potentiel de réduction des temps de cycle et du coût par pièce, tout en améliorant la durée de vie et la qualité de l'outil, est bien réel, comme le montrent les exemples de cas clients décrits. Dans l'industrie automobile, où la production à grand volume est répandue, même une petite économie de temps de cycle peut équivaloir à des rendements financiers importants. Dans cette optique, toute technologie capable de démontrer sa capacité à générer des gains plus importants est difficile à ignorer.
Technologie industrielle
- La valeur de la fabrication additive dans l'industrie automobile
- Comment l'impression 3D transforme-t-elle l'industrie automobile ? (2021)
- Comment le secteur de la logistique automobile affronte le COVID-19
- Comment la technologie IoT supervise les opérations dans l'industrie automobile
- Certification NADCAP et comment elle s'applique à l'industrie de l'usinage de précision
- Usinage CNC dans l'industrie automobile
- Comment l'aluminium est utilisé dans l'industrie navale
- Les propriétés d'usinage des nuances d'aluminium 6061
- Usinage du laiton par rapport à l'aluminium :l'avantage de la tradition