Qu'est-ce que l'extrusion ? Différents types de processus d'extrusion ?
Le processus d'extrusion est l'un des types de processus de formage en vrac dans lequel le métal de travail est forcé ou comprimé à travers un trou de matrice pour obtenir une certaine forme de section requise.
En termes simples, l'extrusion est une procédure de travail des métaux qui consiste à forcer le métal à travers un trou de matrice sous une pression accrue pour comprimer sa section transversale.
Depuis l'évolution du processus d'extrusion, le monde est devenu dépendant de l'extrusion pour produire des barres, des tubes et des profilés de toutes formes, creux ou pleins.
Du fait que cette opération implique de pousser ou de tirer une billette à travers la filière, les forces nécessaires pour extruder la billette sont assez importantes. L'extrusion à chaud est la méthode la plus courante car la résistance à la déformation du métal est faible à haute température, tandis que l'extrusion à froid est généralement réalisée uniquement sur des métaux mous.
Historique :
Bien que le concept d'extrusion soit né du processus de formage. Il est rapporté qu'en 1797, un ingénieur du nom de Joseph Bramah a breveté le procédé d'extrusion.
L'essai impliquait de préchauffer le métal puis de le forcer à travers une cavité de matrice pour fabriquer un tuyau à partir de la billette. Il a utilisé un piston manuel pour forcer le métal.
Bramah a ensuite inventé le procédé hydraulique après l'invention de l'extrusion. Ensuite, Thomas Burr a utilisé la technologie de la presse hydraulique et la technique d'extrusion de base combinant les technologies individuelles pour produire un tuyau (creux). Il a également été ensuite breveté en 1820.
La technologie est alors devenue un besoin fondamental dans le monde en pleine croissance, alors que le procédé ne pouvait pas fonctionner sur les métaux durs. En 1894, Thomas Burr a introduit l'extrusion avec des alliages de cuivre et de laiton qui ont apporté une évolution dans la technique d'extrusion.
Depuis l'invention de la technique d'extrusion, le processus a évolué vers une variété de techniques capables de produire une large gamme de produits avec des structures complexes au moindre coût possible.
Classification ou types de processus d'extrusion :
Différents types de processus d'extrusion :
- Extrusion à chaud
- Extrusion à froid
- Extrusion chaude
- Extrusion par friction
- Micro-extrusion
- Extrusion directe
- Extrusion indirecte
- Extrusion hydrostatique et
- Extrusion par impact Processus.
#1. Processus d'extrusion à chaud :
Dans ce processus d'extrusion à chaud, la billette est travaillée au-dessus de sa température de recristallisation. Ce travail à chaud permet d'éviter que la pièce ne s'écrouisse et permet au vérin de la pousser facilement à travers la matrice.
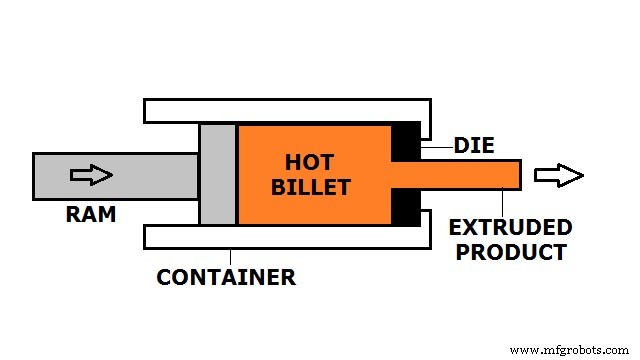
Les extrusions à chaud sont généralement réalisées sur des presses hydrauliques horizontales. La pression impliquée dans ce processus peut varier de 30 MPa à 700 MPa. Pour préserver la haute pression, la lubrification est utilisée. L'huile ou le graphite est utilisé comme lubrifiant dans les extrusions à basse température et la poudre de verre est utilisée pour les extrusions à haute température.
La billette reçoit une chaleur comprise entre 0,5 Tm et 0,75 Tm pour obtenir un fonctionnement de qualité.
Les températures d'extrusion à chaud de quelques matériaux couramment utilisés sont indiquées :
Matériel | Température (˚C) |
Aluminium | 350 à 500 |
Cuivre | 600 à 1100 |
Magnésium | 350 à 450 |
Nickel | 1000 à 1200 |
Acier | 1200 à 1300 |
Titane | 700 à 1200 |
PVC | 180 |
Nylon | 290 |
Avantages du processus d'extrusion à chaud :
- La déformation peut être contrôlée selon les exigences.
- La billette n'est pas soumise à un renforcement dû à l'écrouissage.
- Des forces moindres sont nécessaires pour appuyer.
- Les matériaux présentant des fissures prématurées peuvent également être travaillés.
Inconvénients du processus d'extrusion à chaud :
- Mauvaise finition de surface.
- La précision dimensionnelle est compromise.
- Réduction de la durée de vie du conteneur.
- Possibilité d'oxydation de surface.
#2. Extrusion à froid :
C'est le processus de façonner le métal en le frappant avec une balle. Cette frappe est réalisée à l'aide d'un poinçon ou d'un bélier dans une cavité fermée. Le bélier force le métal à travers la cavité de la matrice pour transformer la billette solide en une forme solide.
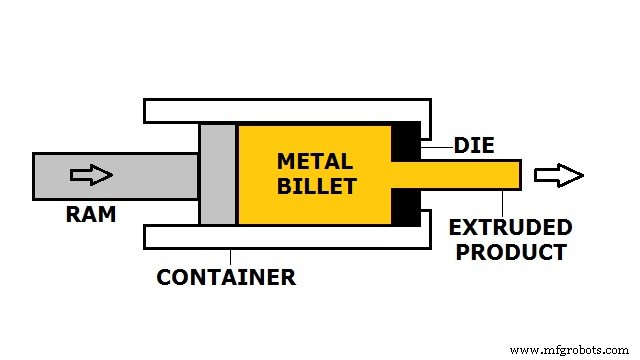
Dans ce processus, la pièce est soumise à une déformation à température ambiante ou légèrement au-dessus de la température ambiante.
Pour que les efforts demandés soient trop élevés, une presse hydraulique puissante est utilisée dans cette technique. La pression varie jusqu'à 3000 MPa.
Avantages :
- Pas d'oxydation.
- Amélioration de la résistance du produit.
- Tolérances plus étroites.
- Finition de surface améliorée.
- La dureté est améliorée.
Inconvénients :
- Des forces supérieures sont nécessaires.
- Plus de puissance est nécessaire pour fonctionner.
- Les matériaux non ductiles ne peuvent pas être travaillés.
- L'écrouissage du matériau extrudé est une limitation.
#3. Processus d'extrusion à chaud :
L'extrusion à chaud est le processus d'extrusion d'une billette au-dessus de la température ambiante et en dessous de la température de recristallisation du matériau. Ce processus est utilisé lorsque le matériau doit être protégé contre les changements microstructuraux qui se produisent pendant le processus d'extrusion.
Ce processus est important pour atteindre le bon équilibre entre les forces et la ductilité requises. La température de tout métal utilisé dans cette opération peut être comprise entre 424 degrés Celsius et 975 degrés Celsius.
Avantages du processus à chaud :
- Force améliorée.
- Cela a amélioré la dureté du produit.
- Manque d'oxydation.
- Des tolérances très étroites peuvent être atteintes.
Inconvénients :
- Les matériaux non ductiles ne peuvent pas être extrudés.
- Un équipement de chauffage est supplémentaire.
#4. Extrusion par friction :
Dans la technique d'extrusion par friction, la billette et le conteneur sont forcés de tourner l'un contre l'autre tandis qu'au travail simultanément, la billette est poussée à travers la cavité de la matrice pour produire le matériau souhaité.
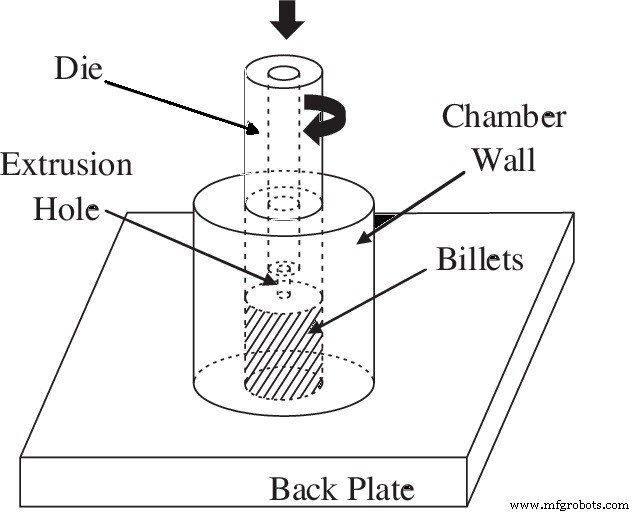
Le processus est influencé par la vitesse de rotation relative entre la billette et la matrice. Le mouvement de rotation relatif de la charge et de la matrice a une implication significative sur le processus.
Tout d'abord, il en résulte la génération d'un grand nombre de contraintes de cisaillement entraînant une déformation plastique de la billette. Deuxièmement, une grande quantité de chaleur est générée pendant le mouvement relatif entre la billette et la matrice, ainsi, aucun préchauffage n'est nécessaire, ce qui rend le processus plus efficace.
Il peut générer des fils, des tiges, des tubes et d'autres géométries métalliques non circulaires sensiblement consolidés directement à partir d'une variété de charges précurseurs, telles que la poudre métallique, les flocons, les déchets d'usinage (copeaux ou copeaux) ou les billettes solides.
Avantages du processus de friction :
- Aucun chauffage n'est nécessaire.
- La génération de contraintes de cisaillement améliore la résistance à la fatigue du produit.
- Tout type de matériau peut être utilisé comme billette, ce qui rend ce processus économique.
- Faible consommation d'énergie.
- Meilleure résistance à la corrosion.
Inconvénients du frottement Processus :
- Oxydation prévue.
- Configuration initiale élevée.
- Machines complexes.
#5. Processus de micro-extrusion :
On entend par sa nomenclature que ce procédé concerne la fabrication de produits de gamme submillimétrique.
Semblable à l'extrusion au niveau macro, la billette est ici forcée à travers l'orifice de la filière pour générer la forme attendue sur la billette. La sortie peut passer à travers un carré de 1 mm.
La microextrusion en avant ou directe et en arrière ou indirecte sont les deux techniques les plus fondamentales utilisées à cette époque pour produire des microéléments.
La microextrusion vers l'avant a le vérin qui entraîne la billette vers l'avant et la billette se déplaçant dans la même direction, tandis que la microextrusion vers l'arrière a le vérin et la billette se déplaçant dans des directions opposées.
La microextrusion est largement utilisée dans la production de composants pour dispositifs médicaux résorbables et implantés, allant des stents biorésorbables aux systèmes de libération contrôlée de médicaments.
Alors que, dans le domaine mécanique, l'application peut être largement observée dans la fabrication de minuscules engrenages, de minuscules tuyaux, etc.
Avantages du microprocessus :
- Des coupes transversales très complexes peuvent être réalisées.
- De minuscules éléments peuvent être produits.
- Tolérances géométriques améliorées.
Inconvénients :
- Créer une petite matrice et un contenant pour répondre à nos besoins est un défi.
- Un ouvrier qualifié est nécessaire.
#6. Extrusion directe ou directe :
Dans le processus d'extrusion directe, une billette de métal est d'abord placée dans le conteneur. Le récipient a un trou de matrice profilé. Un vérin est utilisé pour faire passer la billette métallique à travers le trou de la matrice et le produit est fabriqué.
Dans ce type, le sens du flux de métal est le même que celui du sens de déplacement du vérin.
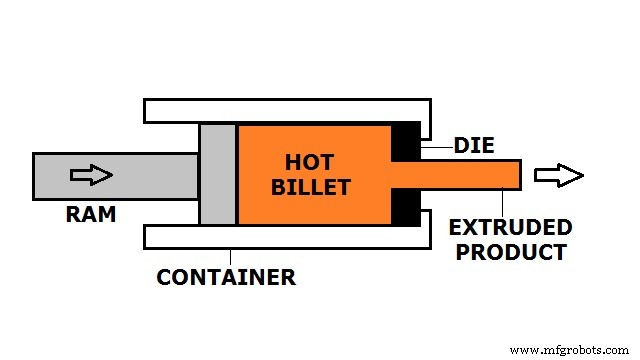
Lorsque la billette est forcée de se déplacer vers l'ouverture de la filière, une grande quantité de frottement est produite entre la surface de la billette et les parois du récipient. L'existence de frottement nécessite une augmentation significative de la force du vérin consommant ainsi plus de puissance.
Dans ce processus, l'extrusion de métaux fragiles tels que les alliages de tungstène et de titane est difficile car ils se fracturent au cours du processus. Les forces de traction tout au long du processus induisent la formation rapide de microfissures, entraînant des fractures.
L'extrusion de métaux fragiles tels que les alliages de tungstène et de titane est difficile car ils se fracturent pendant le processus. Les forces de traction induisent la formation rapide de microfissures, entraînant des fractures.
De plus, la présence d'une couche d'oxyde sur la surface de la billette intensifie le frottement. Cette couche d'oxyde a le potentiel de provoquer des défauts dans le produit extrudé.
Afin de surmonter ce problème, un bloc factice est placé entre le vérin et la billette de travail pour aider à atténuer la friction.
Les tubes, les canettes, les gobelets, les engrenages de petite taille, les arbres et autres produits extrudés en sont des exemples.
Certaines parties de la billette restent toujours à la fin de chaque extrusion. C'est ce qu'on appelle le cul . Il est retiré du produit en le coupant immédiatement après la sortie de la matrice.
Avantages du processus direct :
- Le processus est capable d'extruder des pièces plus longues.
- Amélioration des propriétés mécaniques du matériau.
- Bon état de surface.
- Les extrusions à froid et à chaud sont possibles.
- Capacité à fonctionner en continu.
Inconvénients du processus direct :
- Les métaux fragiles ne peuvent pas être extrudés.
- Grande force et exigence de puissance élevée.
- Possibilité d'oxydation.
#7. Extrusion indirecte ou vers l'arrière :
Dans ce processus d'extrusion vers l'arrière, la filière reste immobile, tandis que la billette et le conteneur se déplacent ensemble. La matrice est montée sur le vérin plutôt que sur le conteneur.
Le métal s'écoule à travers le trou de matrice du côté du vérin dans le sens opposé du mouvement du vérin lorsqu'il est comprimé par le vérin.
Lorsque la billette est comprimée, la matière va passer entre le mandrin et donc l'ouverture de la matrice.
Puisqu'il n'y a pas de mouvement relatif entre la billette et le conteneur, aucun frottement n'est enregistré. Cela élève le processus par rapport au processus d'extrusion directe, ce qui fait que la force de frappe utilisée est plus faible que dans l'extrusion directe.
Afin de maintenir la matrice immobile, une "tige" plus longue que la longueur du conteneur est utilisée. La résistance de la colonne de la tige détermine la longueur d'extrusion finale et maximale.
Parce que la billette se déplace en combinaison avec le conteneur, toutes les forces de frottement sont facilement éliminées.
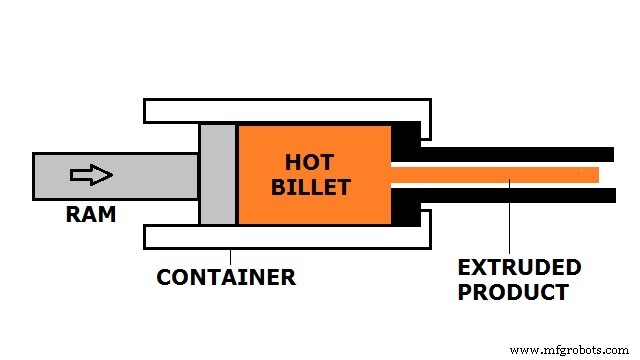
Avantages des processus indirects :
- Moins de force d'extrusion est nécessaire.
- Des sections plus petites peuvent être extrudées.
- Réduction des frottements de 30 %.
- Vitesse de fonctionnement améliorée.
- Très peu d'usure est enregistrée.
- Les défauts d'extrusion ou les zones annulaires à gros grains sont moins susceptibles de se produire car l'écoulement du métal est plus constant.
Inconvénients du processus indirect.
- La section transversale du matériau extrudé est limitée par la taille de la tige utilisée.
- Possibilité de contraintes résiduelles après l'extrusion.
- Les impuretés et les défauts affectent la finition de surface et rendent le produit compromis.
#8. Extrusion hydrostatique :
Dans le processus d'extrusion hydrostatique, la billette est entourée de fluide à l'intérieur du conteneur, qui est poussé contre la billette par le mouvement vers l'avant du vérin. Il n'y a pas de frottement à l'intérieur du récipient en raison du fluide, et il y a très peu de frottement au niveau du trou de la filière.
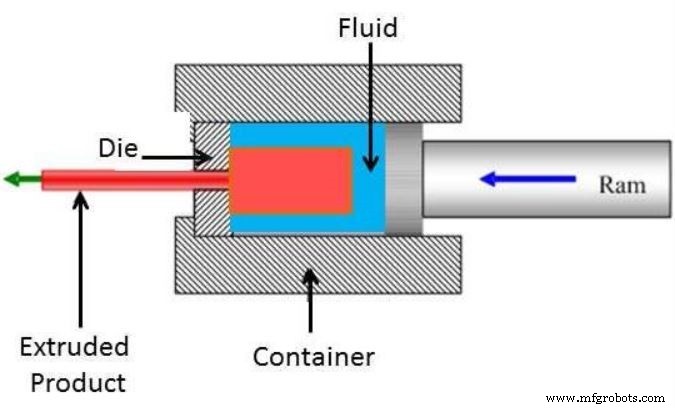
La billette n'est pas perturbée lors du remplissage de l'alésage du récipient puisqu'elle est soumise à une pression hydrostatique uniforme. Cela se traduit avec succès par une billette avec un rapport longueur / diamètre énorme, même des bobines de fil peuvent être parfaitement extrudées ou une section transversale inégale.
La principale différence entre les extrusions hydrostatiques et directes est qu'il n'y a pas de contact direct entre le conteneur et la billette lors de l'extrusion hydrostatique.
Travailler à des températures élevées nécessite l'utilisation de fluides et de procédés spécialisés.
Lorsqu'un matériau est soumis à une pression hydrostatique et qu'il n'y a pas de frottement, sa ductilité augmente. Par conséquent, cette méthode peut être utilisée sur des métaux trop fragiles pour les méthodes d'extrusion typiques.
Cette approche est utilisée sur les métaux ductiles et permet des rapports de réduction élevés.
Avantages :
- Les produits extrudés ont un excellent poli de surface et sont dimensionnellement précis.
- Pas question de friction.
- Forces requises minimisées.
- Aucun résidu de billette ne reste dans le processus.
- Le flux de matière est régulier.
Inconvénients :
- En cas de fonctionnement à des températures élevées, des fluides et des procédures spéciaux doivent être utilisés.
- Chaque billette doit être préparée et effilée à une extrémité avant le travail.
- Il est difficile de contenir le liquide.
#9. Extrusion par impact :
L'extrusion par impact est une autre méthode majeure de production de profilés métalliques extrudés. Contrairement au processus d'extrusion traditionnel, qui nécessite des températures élevées pour ramollir le matériau, l'extrusion par impact utilise souvent des billettes métalliques froides. Ces billettes sont extrudées à haute pression et efficacité.
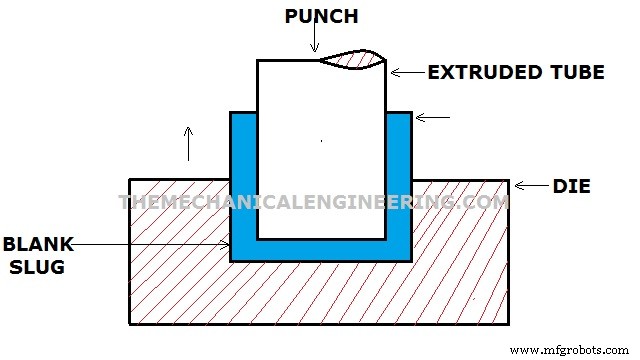
Une pastille convenablement lubrifiée est placée dans une cavité de filière et frappée avec un poinçon en un seul coup lors d'une opération d'extrusion par impact conventionnelle. Cela fait refluer le métal autour du poinçon à travers un espace entre la matrice et le poinçon.
Ce processus fonctionne mieux avec des matériaux plus tendres tels que le plomb, l'aluminium ou l'étain.
Ce processus est toujours effectué à froid. Le processus d'impact vers l'arrière permet des parois très minces. Fabriquez des tubes de dentifrice ou des boîtes à piles, par exemple.
Il est effectué à un rythme plus rapide et avec des coups plus courts. Au lieu d'exercer une pression, une pression d'impact est utilisée pour extruder la billette à travers la filière. L'impact, en revanche, peut être effectué par extrusion vers l'avant ou vers l'arrière, ou un mélange des deux.
Avantages :
- Grande réduction de taille.
- Processus rapide. Temps d'usinage réduit jusqu'à 90 %.
- Taux de production accru.
- Intégrité de tolérance accrue.
- Jusqu'à 90 % d'économie de matière première.
Inconvénients :
- Une force de compression très élevée est nécessaire.
- La taille de la billette est une limite.
Facteurs affectant la force d'extrusion :
Les facteurs suivants affectent la force d'extrusion sont :
- Température de travail.
- Conception de l'équipement, horizontal ou vertical.
- Type d'extrusion.
- Le rapport d'extrusion.
- Quantité de déformation.
- Paramètres de frottement.
Application ou utilisations du processus d'extrusion :
- Il est largement utilisé dans la production de tubes et de tuyaux creux. Et est également utilisé pour produire des objets en plastique.
- Le processus d'extrusion est utilisé pour produire des cadres, des portes, des fenêtres, etc. dans l'industrie automobile.
- Le métal Aluminium est utilisé dans les travaux de structure dans de nombreuses industries.
Technologie industrielle
- Qu'est-ce que le brochage ? - Processus, travail et types
- Qu'est-ce que le forgeage ? - Définition, processus et types
- Qu'est-ce que l'extrusion ? - Fonctionnement, types et application
- Quels sont les différents types de cintrage de tubes ?
- Quels sont les différents types d'agents d'entretien ?
- Quels sont les différents types de soudage ?
- Quels sont les différents types de prototypage ?
- Quels sont les 4 types de processus de fabrication ?
- Différents types de procédés de soudage à l'arc électrique