Optez pour des performances sans temps d'arrêt en "testant le sang de la machine"
Au milieu des années 2000, le système d'air comprimé de l'usine Toyota North America de Georgetown, KY, s'est écrasé en moyenne plus d'une fois par an. Cela a amené certains employés de l'usine à se demander si l'utilisation de l'apprentissage automatique et de l'IA pouvait résoudre ce problème en permettant la détection des anomalies, l'identification des défauts et, surtout, la prédiction des défaillances imminentes avant qu'elles ne surviennent.
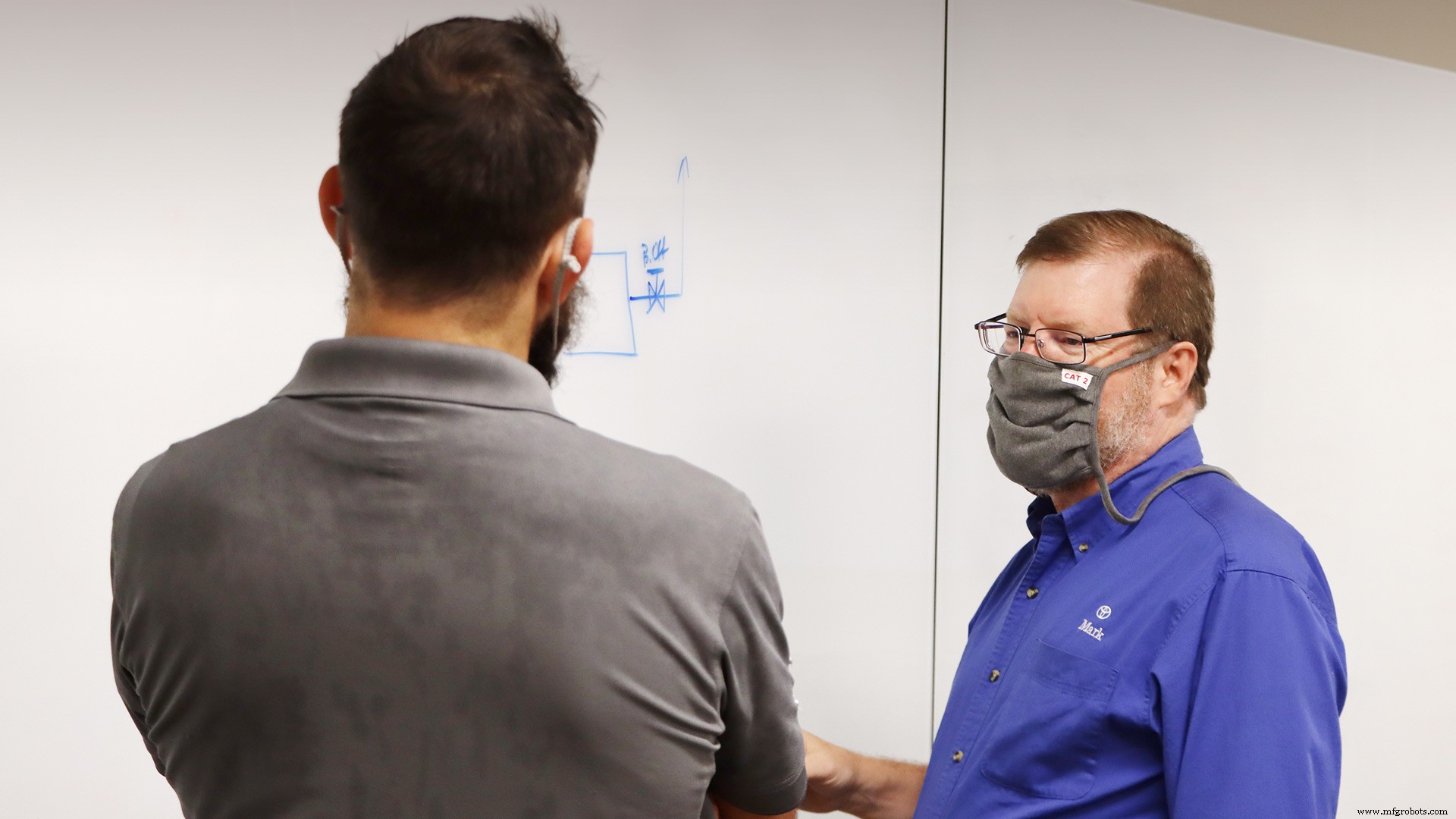
Les arrêts imprévus du système d'air comprimé signifiaient, bien sûr, que toute l'usine avait un problème. L'atelier de peinture utilisait de l'air comprimé pour pulvériser la peinture des nouveaux véhicules. Le système a donné vie aux outils pneumatiques, et rien de comparable à l'air comprimé pour souffler le ponçage et autres résidus.
Avec un véhicule fini sortant de l'une des trois lignes de l'usine toutes les 25 secondes pendant deux quarts de travail, les conséquences étaient importantes en cas de panne du service d'air comprimé.
"La dépense, si la ligne tombe en panne, est énorme", a déclaré Mark Rucker, chef de projet et expert en matière d'électricité à l'usine. "Donc, il y a là une bonne incitation à avoir un bon service public fiable et stable."
Le système d'air comprimé de plusieurs millions de dollars est composé d'une douzaine de compresseurs d'air centrifuges Ingersoll Rand, chacun de la taille d'un petit semi-remorque. Les aubes d'étage final de chaque compresseur tournent à 20 000 tr/min à une fraction de pouce de leur logement. Si une lame fonctionne le moins hors des spécifications et touche le boîtier, c'est fichu. L'ensemble de la machine doit être reconstruit pour un coût d'environ 100 000 $.
L'oscillation de la lame n'est pas la cause d'un accident, cependant; c'est le résultat.
L'accident - alias une surtension ou un flux inversé :se produit lorsque quelque chose provoque l'inversion du flux d'air normal du compresseur vers un tuyau et que l'air dans le tuyau est repoussé.
La fréquence, le coût et les conséquences des accidents ont incité Toyota à appeler Jay Lee, directeur fondateur d'Intelligent Maintenance Systems, pour obtenir de l'aide.
Jay Lee était en avance sur la courbe de l'industrie 4.0
Au début du nouveau millénaire, avant l'appel de Toyota, Lee était un professeur d'ingénierie à l'Université de Cincinnati qui envisageait toutes les machines d'une usine connectées et fournissant des données pour une maintenance intelligente. À cette époque, cependant, une grande partie de la technologie nécessaire pour concrétiser la vision de Lee n'existait pas encore.
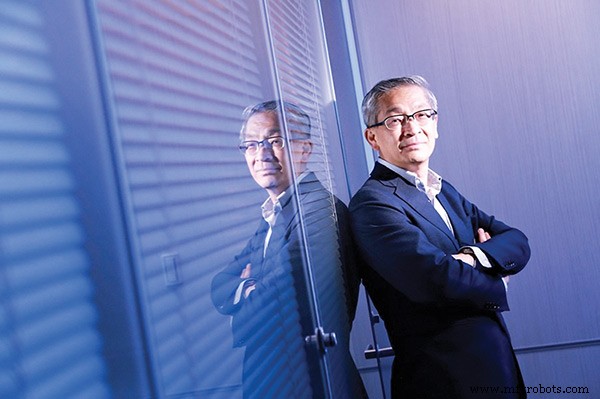
"Il y a vingt ans, très peu de gens pensaient que c'était possible", a déclaré Lee, qui est actuellement en congé d'enseignement et est vice-président et membre du conseil d'administration de Foxconn Technology Group dans le Wisconsin.
Dans sa vision industrielle, les machines sont comme des patients et les données recueillies par les capteurs qui surveillent les machines fournissent des informations sur leur santé. Les experts obtiennent des pronostics en interprétant les données qu'ils collectent et analysent.
"J'ai dit:" Pourquoi ne pas tester le sang de la machine? " Et quel est le sang de la machine?" dit Lee. "Données. La question est :« Quelles données voulez-vous obtenir ? » Cela dépend de ce que vous voulez analyser. Nous devons comprendre le contexte et le contenu, et formuler davantage un modèle de relation entre les inconnues invisibles."
Caché dans les données se cache le sens du comportement déviant d'une machine ou d'un processus. Libérer ce sens conduit à prédire la qualité, à déterminer la stabilité de la machine ou du processus et à prévenir les défaillances potentielles. "C'est exactement ce qu'est l'industrie 4.0 aujourd'hui", a déclaré Lee.
Le terme "Industrie 4.0", bien sûr, n'a été popularisé qu'à l'époque de l'initiative du gouvernement allemand en 2013.
Aucun plantage depuis 2006
Une fois chez Toyota, Lee et son équipe d'analystes de données se sont joints à Rucker et à un groupe de techniciens de maintenance et d'ingénieurs d'usine qualifiés pour résoudre le problème du système d'air comprimé.
La simplicité de leurs questions démentait la complexité de la tâche à accomplir.
« Pouvons-nous prédire un problème de flux inversé avant qu'il ne provoque un crash ? » dit Rucker. "Pouvons-nous voir quelque chose se développer à temps pour faire quelque chose ?"
Au cours de mois d'essais et d'erreurs en 2005, l'équipe a collecté et analysé des données haute fidélité de l'un des compresseurs et recherché des anomalies. Parfois, l'équipe créait une condition de surtension ou d'approche de la surtension afin de forcer la machine à commencer à afficher un comportement déviant et de voir à quoi cela ressemblait dans l'ensemble de données.
Finalement, le travail de l'équipe a porté ses fruits. Ses membres ont vu que le meilleur prédicteur d'une condition de surtension naissante se produisait à l'étape deux (sur les quatre étapes que traverse le compresseur qui passe de la pression normale à 120 livres de pression par pouce carré, ou PSI).
"Quelle est la physique derrière cela, pourquoi est-ce le prédicteur?" dit Rucker. «Je ne sais pas, je m'en fous. Nous venons de voir que cela prédit de manière fiable une future poussée, et il la prédit avec quelques secondes d'avertissement. »
L'étape suivante consistait à placer un capteur différentiel sur chaque compresseur et à créer un algorithme d'apprentissage automatique pour l'unité de contrôle centrale. Les tests ont confirmé que dès que l'étage deux commençait à "osciller", le compresseur commençait à reculer.
"Chaque fois que nous l'avons testé, cela nous a évité les ennuis", a-t-il déclaré. "Nous n'avons eu aucun crash depuis 2006."
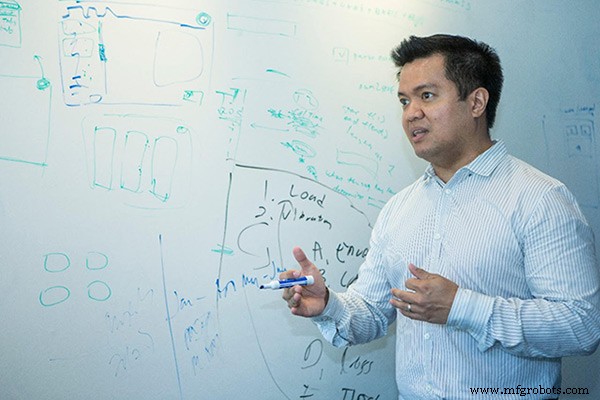
Alors que le projet de surtension du compresseur a été un succès, un autre qui visait à prédire la durée de vie des roulements dans les mastodontes de l'air comprimé a échoué. L'équipe n'a pas pu trouver suffisamment de données de maintenance fiables et les associer aux données opérationnelles de la machine pour établir des corrélations utiles, a déclaré Rucker.
"C'est probablement le bon mélange de R&D", a-t-il déclaré. « Vous essayez des trucs, et vous ne savez pas si ça va marcher ou pas. Et si la moitié du temps vous récupérez votre argent, c'est une victoire. Et de temps en temps, vous trouvez celui qui paie pour tout le reste, comme le contrôle des surtensions. »
La flexibilité est essentielle
Lee a ensuite publié un article sur le projet Toyota et, en 2013, a aidé à co-fonder Predicttronics avec Patrick Brown, un employé d'Intelligent Maintenance Systems, et deux de ses étudiants universitaires, David Siegel et Edzel Lapira. Marron. Lapira et Siegel forment la suite Predicttronics C.
Comme Rucker de Toyota a fait appel à Lee pour obtenir de l'aide en matière d'IA, les entreprises se tournent vers Predicttronics pour obtenir de l'aide dans leurs aspirations à zéro temps d'arrêt.
"Différents clients sont généralement à différents niveaux de maturité", a déclaré Lapira, qui est PDG. « Nous avons certains clients qui ont déjà mis en place une structure de collecte de données :ils ont un lac de données, mais ils ne savent pas quoi faire avec les données. Nous avons aussi des clients qui doivent repartir de zéro. »
Les clients avec des actifs de 50 ou 60 ans doivent commencer à un stade encore plus précoce.
De plus en plus, Predicttronics est approché par des clients possédant des machines héritées. Lapira et ses collègues les envoient acheter des composants comme des accéléromètres et des transducteurs.
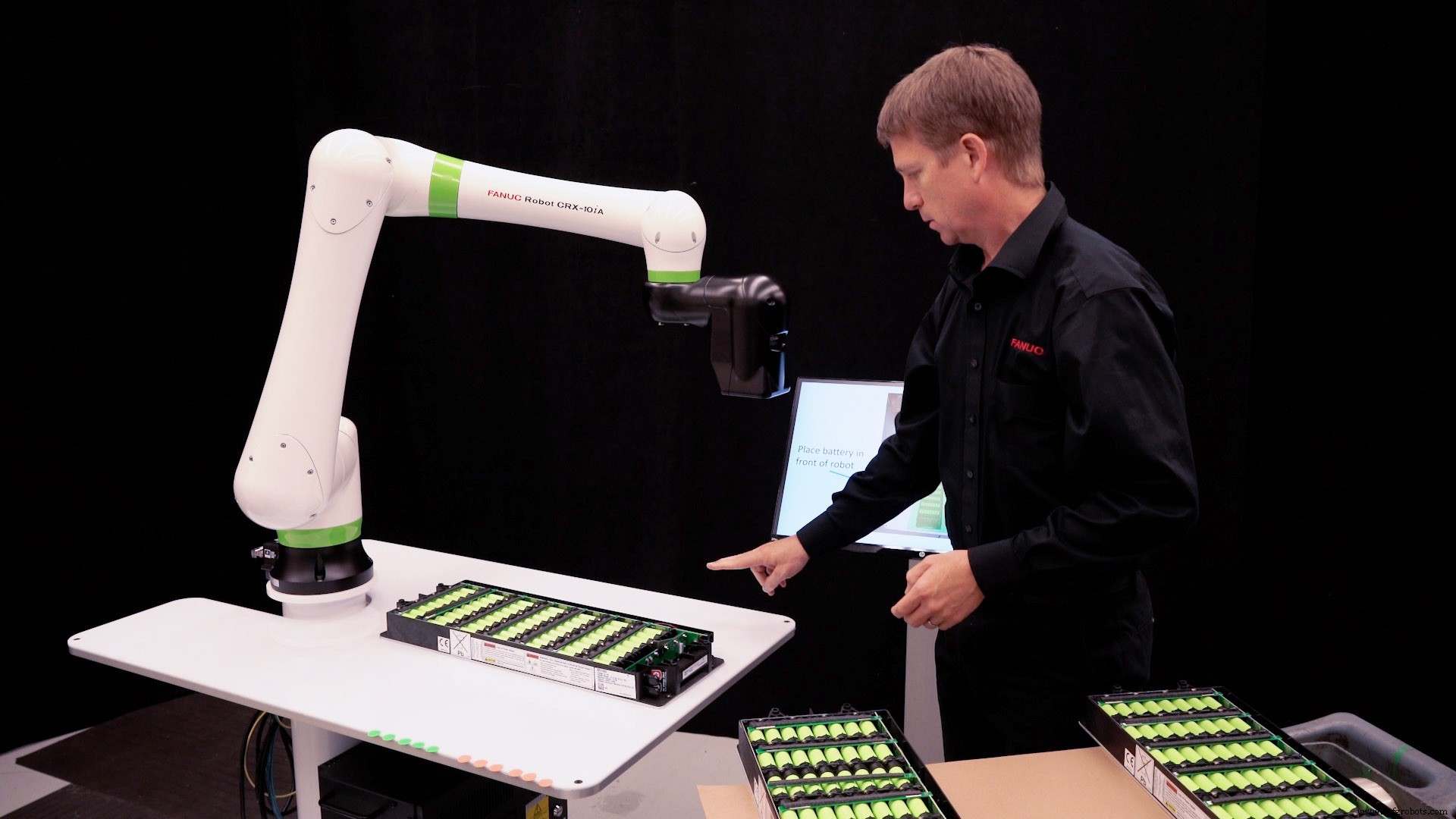
"Ce sont les différents convertisseurs analogique-numérique dont nous avons besoin pour extraire ces données", a-t-il déclaré.
Depuis sa création en 2013, Predicttronics a aidé plus de 70 usines avec des solutions d'IA, dont beaucoup d'entreprises Fortune 500.
Predicttronics a travaillé avec un client, un fabricant de semi-conducteurs, pour établir une solution prédictive de métrologie virtuelle capable d'apprendre la relation entre le capteur et les variables de mesure.
Le projet était difficile en raison des centaines de signaux mesurés émis par l'équipement à semi-conducteurs.
Mais il existe des méthodes statistiques bien connues pour réduire le nombre de possibilités, a déclaré Siegel.
"En plus de ces méthodes, au cours des dernières années, c'est davantage la communauté de l'apprentissage automatique qui a développé des méthodes qui intègrent un algorithme de régression de classification qui comporte une partie intégrée de sélection de variables", a-t-il déclaré. "Donc, cela le réduit aux 10, 20 ou 30 principales variables. Ensuite, vous travaillez avec le client ou utilisez vos propres connaissances pour déterminer ce qui est le plus logique à inclure dans le logiciel et le modèle d'analyse."
Qu'il s'agisse d'appliquer les connaissances acquises lors de l'expérience précédente dans son approche basée sur des modèles, ce qui permet de réduire les coûts, ou d'une solution formulée dans une partie d'une entreprise qui peut ensuite être mise à l'échelle en interne, "trouver une solution qui répond directement aux problèmes les plus critiques mais est également suffisamment flexible pour être appliqué à d'autres problèmes est essentiel », a déclaré Brown.
IA de diligence raisonnable
Les usines qui recherchent un fournisseur de solutions d'IA comme Toyota l'a fait pour son problème d'air comprimé doivent faire preuve de diligence raisonnable pour trouver la bonne solution.
Il est utile de connaître les bonnes questions à poser, ont déclaré les experts de Predicttronics :
Où avez-vous déjà utilisé vos services ?
Votre solution a-t-elle démontré une nette amélioration des opérations commerciales en termes de réduction des temps d'arrêt ou d'amélioration de la qualité ?
Votre solution a-t-elle été utilisée dans mon secteur ?
Votre équipe a-t-elle des connaissances dans le domaine industriel ?
Votre solution fonctionne-t-elle avec les anciens équipements ?
Votre solution fonctionne-t-elle avec une variété de capteurs ?
Votre solution utilise-t-elle l'apprentissage automatique ?
Combien de données faut-il pour entraîner le modèle ?
A-t-il seulement besoin des données d'une machine saine ou des données d'une machine dégradée ou défectueuse également pour apprendre ?
Les robots aussi veulent l'IA
Alors que les machines-outils d'un atelier fonctionnent mieux sous l'influence de l'IA, il n'y a aucune raison pour que les robots ne puissent pas faire de même.
Fanuc America a récemment ajouté "AI Error Proofing" à son contrôleur de robot et à la fonction de vision des robots, iRVision, qui utilise l'apprentissage automatique (ML) pour l'inspection des pièces.
Grâce à la fonction anti-erreur, un opérateur utilise des images pour entraîner le ML à vérifier deux situations distinctes (si un écrou soudé est présent ou absent, par exemple) et à accepter ou rejeter une pièce.
Étant donné qu'iRVision peut prendre en charge jusqu'à 27 caméras, la fonction anti-erreur peut agir à autant d'étapes du processus de fabrication.
"Vous voulez identifier les rejets ou les erreurs avant de continuer à ajouter de la valeur à une pièce défectueuse", a déclaré Josh Person, ingénieur du personnel du groupe de vision industrielle de Fanuc.
"Souvent, vous pouvez voir une erreur à un moment donné et la prochaine étape la couvrirait", a-t-il ajouté.
Lors de la configuration, l'opérateur peut présenter plusieurs exemples de pièces et les classer en deux catégories :bonnes et mauvaises. Si l'exemple n'appartient à aucune des deux classes, il affichera "indéterminé". Des exemples indéterminés peuvent ensuite être ajoutés pour améliorer le modèle appris.
Système de contrôle d'automatisation
- SIGHT :For the Blind
- Évaluer les avantages de DevOps pour les tests de performances IoT
- Automatisation :ce que cela signifie pour l'avenir de l'entreprise
- L'avenir de la livraison sans contact
- Merci pour les souvenirs!
- Les avantages de l'automatisation pour votre entreprise
- Comment choisir le bon filtre pour votre application
- Cinq façons de trouver le bon compresseur pour l'amateur à domicile
- Lignes directrices pour sélectionner le bon fournisseur de services d'air comprimé