Célébration des cinq dernières années
Le mois dernier, nous avons fêté les cinq ans depuis qu'une poignée de personnes dans un garage ont conçu la première imprimante 3D en fibre de carbone. Merci à nos clients d'avoir contribué à notre succès et d'avoir cru en nous au cours des cinq dernières années. Voici l'histoire de nos débuts, des premiers utilisateurs qui ont cru en nous et de la façon dont nos clients nous ont permis de continuer sur la voie de l'innovation.
Le Mark One
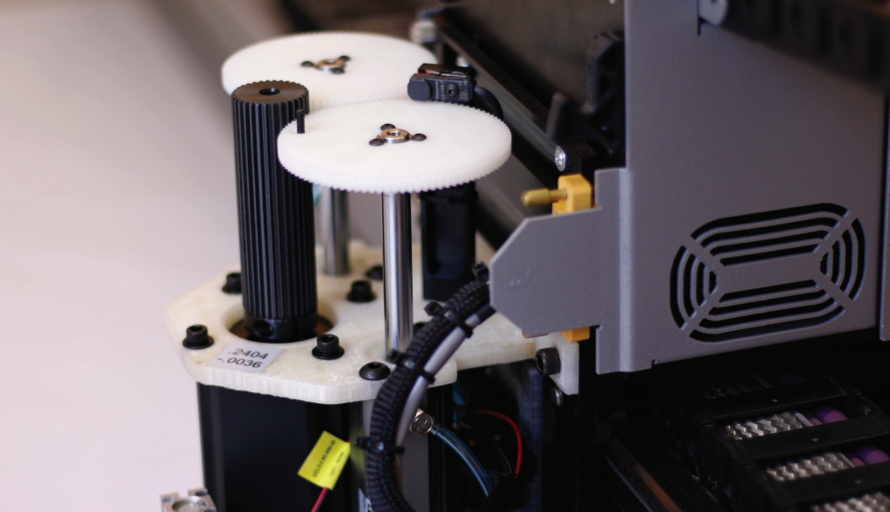
En janvier 2014, nous avons lancé la première imprimante 3D au monde capable d'imprimer en fibre de carbone continue à SolidWorks World :The Mark One. Autometrix a cru au concept et a acheté l'une des premières imprimantes Markforged.
Autometrix fournit des équipements de coupe et des logiciels de modelage à une variété d'applications industrielles, utilisées pour tout, du transport aux dispositifs médicaux. L'entreprise souhaitait intégrer le prototypage en interne, mais les ingénieurs « devaient s'assurer que les résultats du processus de prototypage correspondaient à ce qu'ils essayaient de concevoir », selon Tyler Green, ingénieur électricien chez Autometrix. Après s'être rendu compte que l'équipe pouvait imprimer en 3D une pièce renforcée de fibres qui fonctionnait réellement sur leur tête de coupe, l'équipe a été vendue sur le Mark One.
C'était juste le début. Autometrix a ensuite imprimé une tête de coupe entière à l'aide du Mark One, et les ingénieurs ont découvert que la tête de coupe imprimée pesait une demi-livre de moins que son homologue en aluminium. Les pièces légères fabriquées sur le Mark One ont résisté à tous les impacts de leurs homologues métalliques et plus encore, permettant à Green et à d'autres ingénieurs d'Autometrix d'améliorer et d'étendre leurs systèmes mécaniques.
Le Mark Two
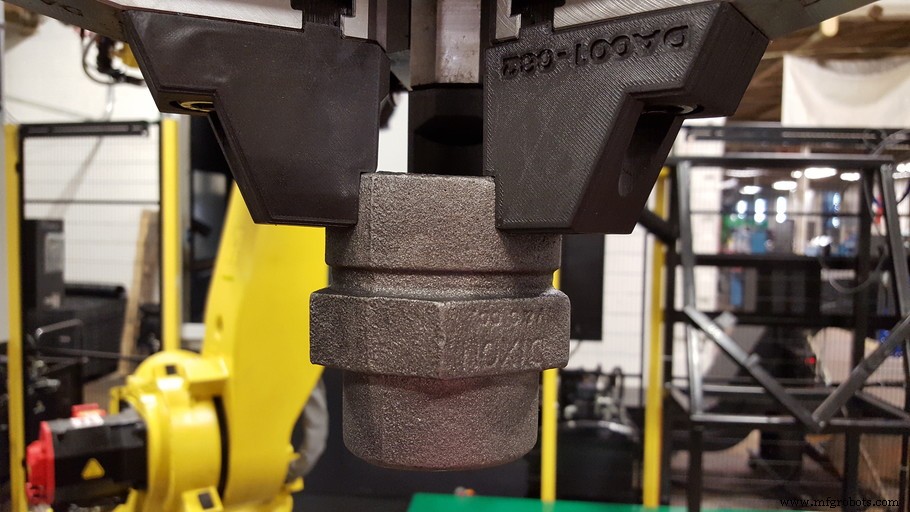
Nous avons lancé le Mark Two – la prochaine génération du Mark One – en février 2016. Le Mark Two comportait un système d'impression composite entièrement repensé qui permettait des pièces plus résistantes et de meilleure qualité que son prédécesseur. Le fabricant de raccords et de vannes Dixon Valve avait besoin d'une imprimante capable de créer des pièces à haute résistance, faisant de la Mark Two un excellent potentiel pour l'entreprise.
Vanne Dixon cherchait à améliorer ses solutions de ligne de production. Les ingénieurs Max de Arriz et J.R. Everett avaient besoin de créer des mâchoires de préhension à haute résistance pour les bras robotiques industriels dans leur processus de fabrication. Le bras robotique transfère plusieurs pièces différentes entre deux centres de tournage verticaux, et l'entreprise avait besoin que les mâchoires soient solides, sûres et résistantes aux produits chimiques. Chaque configuration de gamme de produits nécessitait un équipement personnalisé pour maintenir efficacement des pièces spécifiques. L'entreprise savait qu'elle avait besoin d'une imprimante 3D pour les pièces personnalisables, ce qui a conduit ses ingénieurs à la Mark Two.
"Avec le Mark Two, nous avons pu ré-outiller un bras robotique dans une cellule de fabrication en moins de 24 heures", s'est exclamé Everett. Le Mark Two a permis à Dixon Valve de produire de nouvelles solutions de fabrication à une vitesse et à un coût sans précédent, offrant à l'entreprise un nouvel outil puissant dans sa boîte à outils. Everett estime que le Mark Two est un élément essentiel du processus de conception de l'entreprise, affirmant que « cela change vraiment notre façon de travailler au point où nous modifions réellement nos procédures et nos plans pour adapter ce produit révolutionnaire. »
L'introduction de l'Onyx
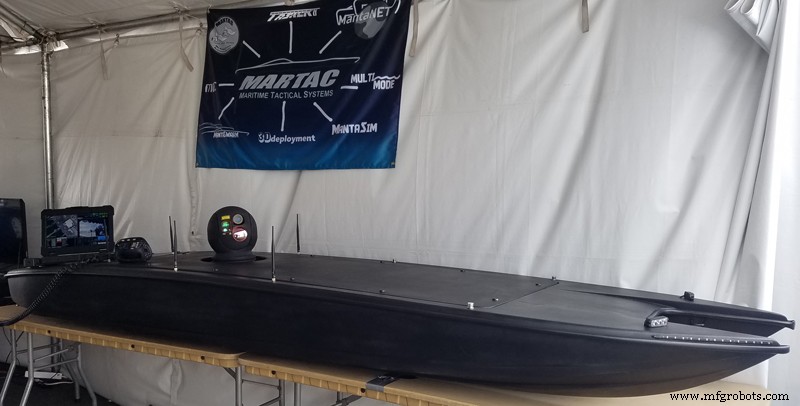
En 2016, nous avons lancé Onyx, notre thermoplastique renforcé de composite de nouvelle génération, parfaitement adapté aux environnements de fabrication. Comme Onyx a une stabilité thermique très élevée, il n'est pas sujet au gauchissement. Il a une résistance et une rigidité supérieures, et est un matériau de haute précision et de haute répétabilité. C'est cette haute précision qui a d'abord attiré MARTAC vers l'impression en Onyx.
MARTAC (Maritime Tactical Systems) conçoit et fabrique des navires aquatiques sans pilote de haute performance. L'entreprise cherchait à créer des prises d'eau géométriquement complexes qui pourraient aider à acheminer l'eau de mer à travers des canaux de refroidissement. En imprimant en 3D cette pièce en Onyx, MARTAC a pu créer une géométrie complexe et personnalisée qui n'avait pas besoin de se conformer aux contraintes d'usinage soustractives.
L'onyx est désormais le matériau principal des navires MARTAC. "Ce qui est bien avec l'utilisation de l'Onyx, c'est qu'il ne se corrode pas en étant constamment dans l'eau salée. Ces pièces se sont également avérées assez résistantes aux débris dans l'eau », explique Ian Weaver, coordonnateur des opérations chez MARTAC. L'impression de ces apports a considérablement réduit les coûts de fabrication pour l'entreprise sur ce qui serait une pièce incroyablement difficile à fabriquer.
Devenir industriel
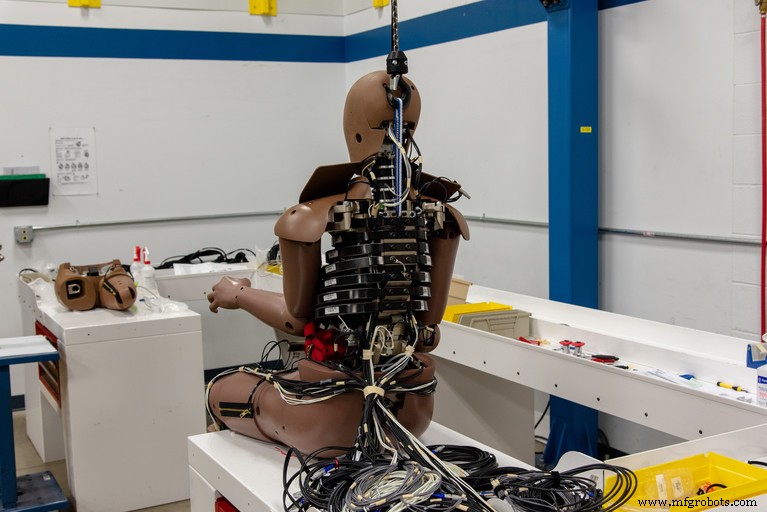
Avec près de trois fois le volume de fabrication et une suite de capteurs d'autosurveillance avancés, la X7 a été notre première imprimante 3D au format industriel. Humanetics - le premier fournisseur mondial de mannequins de crash test - avait besoin d'une nouvelle technologie pour accélérer son processus de remplacement de grandes pièces. Le X7 était la solution parfaite pour eux.
Humanétique Les mannequins de crash test sont utilisés dans les industries automobile, militaire et aérospatiale. Face au problème de l'usure trop rapide des moules, Humanetics recherchait un moyen rentable de fabriquer des pièces durables qui résisteraient à des températures élevées. Kris Sullenberger, ingénieur de conception chez Humanetics, s'est penché sur les moules d'impression 3D pour les pièces factices de crash test et est tombé sur le X7.
Humanetics a imprimé entre cinq et dix moules et prévoit de remplacer bon nombre des 150 moules de l'entreprise par des impressions Markforged. En plus des avantages en termes de coût et de durabilité, Kris a découvert que les moules imprimés donnent de meilleures pièces. Là où les moules en silicone laissent des coutures et d'autres imperfections, l'ajustement précis des moules imprimés donne une pièce presque parfaite. De l'impression de pièces factices de crash test de production pour son équipe de conception au remplacement d'équipements massifs et vieillissants pour les techniciens d'assemblage, Humanetics a presque toujours la machine à imprimer. Kris aime la façon dont il peut choisir de dépenser « des milliers et des milliers de dollars pour les faire usiner ou produire à l'extérieur » ou « les faire en interne pour littéralement des dizaines ou des centaines de dollars. »
Métal X
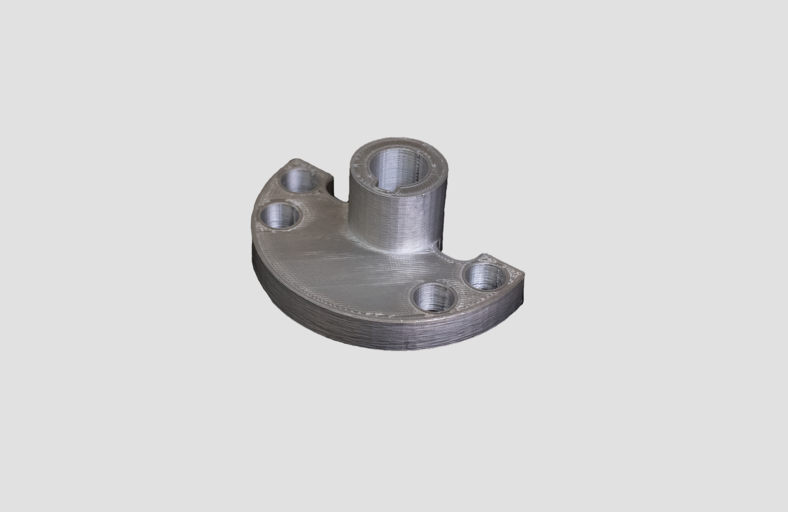
Au cours de la dernière année, nous avons ajouté l'impression 3D métal à notre gamme de produits sous la forme de la Metal X. La possibilité d'imprimer des pièces en acier inoxydable ouvre de nouvelles opportunités pour imprimer des remplacements identiques pour une grande variété de gammes de produits. . Stanley Infrastructure a adopté le Metal X pour étudier le remplacement de pièces sur mesure coûteuses par des pièces imprimées bon marché.
Infrastructure Stanley , une division de Stanley Black &Decker, est le plus grand fabricant d'outils hydrauliques portatifs au monde. L'entreprise avait besoin d'une pièce pour maintenir les roues de guidage réglables sur une meuleuse à grenouilles de chemin de fer, qui était difficile à usiner. Les ingénieurs ont choisi d'usiner les arbres de roue à partir d'un seul bloc d'acier, mais environ 90 % du matériau de base a été gaspillé dans chaque pièce en raison du diamètre de la bride et de la longueur de l'arbre. Avec l'aide des ingénieurs de Markforged, Stanley Infrastructure a repensé l'arbre de roue pour en faire un assemblage en trois parties. En achetant un arbre et une clavette du commerce, l'entreprise a pu imprimer facilement la bride la plus complexe sur un métal X. Le nouvel assemblage a réussi les tests de durabilité et de chute abusive.
Selon un ingénieur de Stanley Infrastructure Innovation, « il est tout à fait possible de tirer parti de la plate-forme Metal X pour fabriquer de manière additive le boîtier de l'actionneur discuté avec un investissement en capital et en temps très minime. Depuis l'achat de l'imprimante, Stanley Infrastructure s'est concentré sur l'impression de pièces de haute qualité, ce qui a minimisé le temps d'usinage et réduit les coûts.
Qu'est-ce qui suit ?
Des entreprises Fortune 100 aux fabricants familiaux, des milliers d'entreprises utilisent la technologie Markforged pour améliorer leurs produits et processus. Et, tout comme ces entreprises, nous recherchons constamment de nouvelles façons de rendre nos produits et processus meilleurs que jamais.
C'est parti pour de nombreuses années d'innovation de la part de nos clients !
Vous voulez tester la puissance de nos imprimantes ? Demandez un échantillon de pièce Markforged gratuit ici .
Vous voulez voir plus de messages comme celui-ci ? Suivez-nous sur Facebook , Twitter , Instagram , et LinkedIn pour plus de mises à jour !
impression en 3D
- Célébration des 10 ans de l'impression 3D Formlabs
- Guide de Carl Calabria sur l'utilisation des encarts sur le Mark One
- Comment utiliser le bâton de colle sur votre lit d'impression Mark One
- Amazon-Whole Foods :deux ans après l'accord
- Cinq façons d'atteindre un dernier kilomètre plus écologique
- Les cinq entreprises d'équipement de construction les plus populaires
- Les revenus de la 5G IoT vont monter en flèche au cours des cinq prochaines années
- La fabrication numérique a triplé en deux ans
- ProtoPumpkins au fil des ans