Assemblez-vous avec des pièces fonctionnelles imprimées en 3D !
L'un des avantages de travailler pour une entreprise d'impression 3D de qualité industrielle est que vous avez toujours accès à la création de pièces solides et fonctionnelles chaque fois qu'une idée surgit. Au cours des deux dernières années, il y a eu une forte augmentation de la prévalence des pièces imprimées en 3D fonctionnelles apparaissant dans la vie de nos employés - des brosses à dents et des porte-stylos aux charnières de porte en Kevlar de remplacement (nous ne savons pas exactement comment des parties anonymes ont perdu un charnière de porte…), et un support GPS pour guidon de vélo de route pour n'en citer que quelques-uns. Il est incroyablement facile de fabriquer des composants uniques, à haute résistance et personnalisés avec une imprimante 3D Mark Two, et avec une grande ferme d'imprimantes interne nécessitant en permanence de nouvelles pièces pour tester les performances de nos machines, il est courant de voir votre conception se matérialiser rapidement.
Ce fut le cas lorsque Maggie, une de nos ingénieurs mécaniciens, a souhaité moderniser sa sacoche de vélo pour la rendre plus facile à transporter. Les sacoches sont des sacs (généralement étanches) qui se montent de chaque côté des roues avant ou arrière d'un vélo, comme vous pouvez le voir sur l'image ci-dessous. Les sacoches sont également monnaie courante dans les bureaux de Markforged - une partie importante de nos vélos de bureau au travail et elles constituent une excellente solution pour transporter du matériel vers et depuis le bureau.
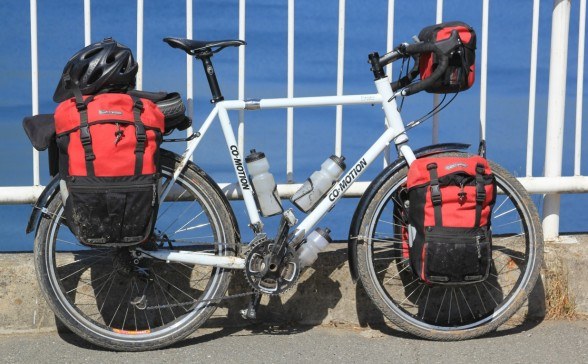
Les sacoches ont parfois des sacs à dos ou des bretelles, mais pas souvent, et Maggie a trouvé difficile de transporter sa sacoche entièrement chargée lorsqu'elle la transportait de son vélo. Sans se décourager, elle a décidé de concevoir une solution qui tirerait parti à la fois de la haute résistance à la traction de notre filament Kevlar CFF et de la fiabilité d'impression et d'oubli du Mark Two. Cela lui a permis de parcourir rapidement une série de conceptions fonctionnelles avant de produire deux adaptateurs de bandoulière haute résistance finis avec un impact minimal sur son programme d'ingénierie chargé (juste la planification et l'exécution de la quasi-totalité des tests d'impression de notre nouveau filament composite en fibre de verre HSHT, pas de gros affaire !).
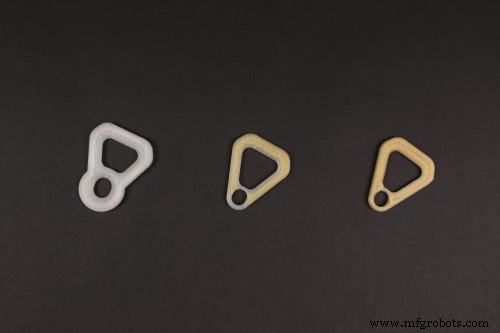
L'adaptateur permettait d'attacher une bandoulière de sac de sport standard aux clips en plastique qui maintiennent normalement la sacoche sur un porte-vélos en acier à l'arrière du vélo. Les clips de sacoche étaient le point de montage parfait pour ajouter une bandoulière, mais la sangle elle-même se terminait par son propre ensemble de clips en plastique qui ne pouvaient pas s'interfacer avec la sacoche à un angle confortable pour porter le sac. Il était clair pour Maggie qu'un adaptateur serait nécessaire pour faire avancer ce projet.
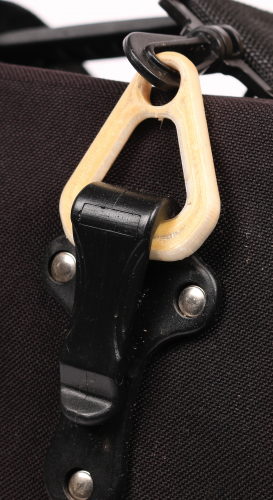
La première itération a été faite avec les dimensions approximatives des points de montage des clips de sacoche et de bandoulière. Il était fonctionnel, mais le trou rond pour le montage de la bandoulière était trop épais et le clip de la bandoulière ne pouvait pas bouger facilement, ce qui rendait le positionnement difficile lors du transport du sac.
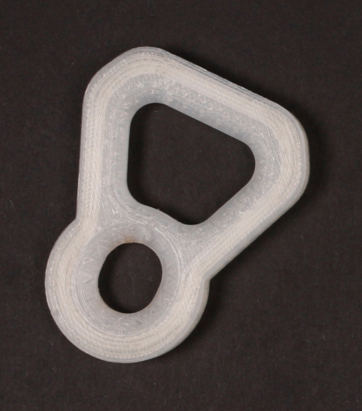
Dans la deuxième itération, Maggie a réduit la taille du trou du clip de sangle et a repensé le corps global de l'adaptateur pour avoir un design plus mince et plus élégant qui s'adapte mieux à l'esthétique du sac et de la sangle. En un clic, elle a mis à jour le fichier STL à découper, en utilisant le bouton « Mettre à jour STL » dans Eiger (surligné en rouge dans l'image ci-dessous). Elle a également changé le type de fibre pour le Kevlar, car il est capable de conserver une plus grande résistance à la traction que la fibre de verre ou la fibre de carbone, au cas où un sac surchargé déformerait la pièce elle-même.
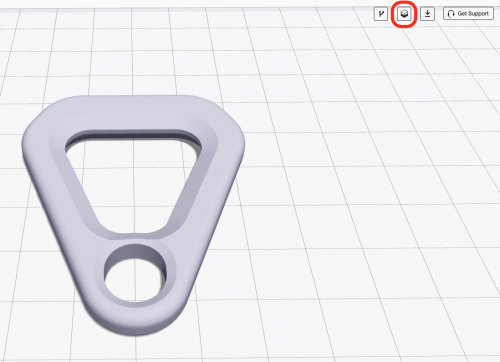
L'itération de conception finale n'impliquait aucun changement de géométrie et utilisait en fait le même fichier STL, mais nécessitait à la place une modification des paramètres de découpage. Maggie a aimé la façon dont la pièce était sortie, mais elle voulait une pièce plus forte que celle imprimée lors de la deuxième itération. Elle a modifié les paramètres Eiger pour incorporer des fibres dans toutes les couches, plutôt que quelques-unes en haut et en bas de la pièce, pour une pièce globalement plus solide.
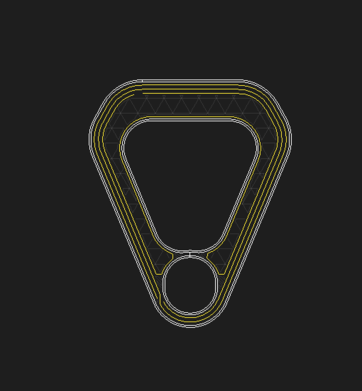
Une fois l'itération finale terminée, Maggie en a imprimé une autre copie et a assemblé le sac ci-dessous. Pièces fonctionnelles – dès la sortie de l'imprimante !
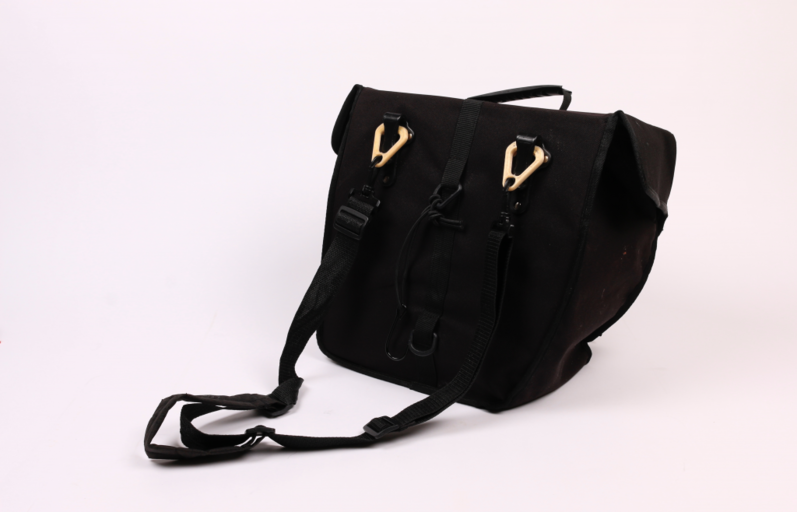
impression en 3D
- Mémoire avec pièces mobiles :« Drives »
- Finir des pièces imprimées en 3D avec… des crayons ?
- Faire des pièces métalliques plus légères avec l'impression 3D en métal
- Impression du fusible 1 avec le fusible 1
- Meilleur contrôle qualité avec les pièces imprimées en 3D
- Inspection en cours :amélioration des pièces imprimées en 3D
- Réimaginer le Go Kart avec des pièces imprimées en 3D
- Drones extrêmes imprimés en 3D
- Précision dimensionnelle des pièces imprimées en 3D