Entretien d'experts :Joachim Zettler, PDG d'APWORKS, sur la recherche de la bonne analyse de rentabilisation pour l'impression 3D métal
Si vous n'avez jamais entendu parler d'APWORKS, vous avez probablement entendu parler du Light Rider :le premier au monde moto jamais imprimée en 3D. Dévoilée en 2016 par APWORKS, la moto électrique a été félicitée pour sa conception légère, ses performances améliorées et ses géométries complexes - un brillant exemple de ce qui peut être réalisé avec la fabrication additive.
Fondée en 2013 en tant que spin-off d'Airbus, APWORKS est l'un des principaux fournisseurs de solutions de fabrication additive métallique. La société couvre l'éventail complet de la FA métallique, y compris l'optimisation des pièces et la production en série qualifiée. La société a également développé et breveté son propre alliage d'aluminium à haute résistance, Scalmalloy®, qui a été utilisé pour le projet Light Rider.
Récemment acquis par Premium AEROTEC, un fournisseur de premier plan de composants métalliques pour les avions Airbus (et une filiale d'Airbus à part entière), APWORKS sert une large clientèle qui comprend principalement l'aérospatiale, l'automobile et les industries de la robotique.
Cette semaine, nous discutons avec le PDG d'APWORKS, Joachim Zettler, pour discuter des raisons pour lesquelles les entreprises doivent trouver la bonne analyse de rentabilisation pour la FA, pourquoi la technologie est parfaite pour l'industrie automobile et ce que l'avenir nous réserve pour l'industrie dans son ensemble.
Pouvez-vous me parler un peu d'APWORKS et de votre mission en tant qu'entreprise ?
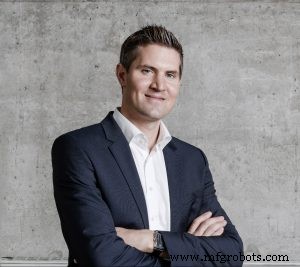
APWORKS a été créée en 2013 en tant que filiale d'Airbus.
L'an dernier, nous avons été acquis par Premium AEROTEC, un fournisseur de fabrication aérospatiale. Premium AEROTEC est un fournisseur de premier plan d'Airbus et est l'un des plus grands constructeurs aérospatiaux au monde.
Premium AEROTEC se concentre fortement sur la fabrication additive et la décision était donc assez naturelle. Et bien que cela ne change rien en interne pour APWORKS, nous avons désormais un actionnaire plus orienté production dans Premium AEROTEC.
Pour APWORKS, notre mission est toujours la même :nous voulons être un fournisseur unique de composants industriels fabriqués de manière additive pour nos clients, et pas seulement pour les industries réglementées. L'automobile est également une clientèle assez large que nous servons, par exemple.
Nous considérons également que notre rôle est d'éduquer nos clients, car nous avons des clients qui viennent nous voir sans aucune connaissance ou expérience préalable de la fabrication additive.
D'autre part, avec les clients qui ont déjà une certaine connaissance de l'additif, nous nous assurons de pouvoir les aider à développer des applications qui ont du sens avec la technologie.
Cela inclut l'aide à la refonte et à l'optimisation des composants ainsi qu'à la production de pièces avec la fabrication additive.
La taille des projets sur lesquels nous travaillons varie énormément, de la production en petits lots à des projets dans l'industrie de l'optique où nous produisons environ 20 000 unités par an.
C'est une autre partie de notre mission :établir une analyse de rentabilisation pour les additifs dans tous les secteurs et devenir un partenaire de choix pour nos clients.
Vous avez mentionné l'automobile comme étant une industrie importante pour APWORKS. De quelles manières l'industrie automobile peut-elle bénéficier de la fabrication additive ?
Si nous regardons les véhicules de sport automobile ou même de luxe comme Bugatti ou Ferrari, les constructeurs automobiles de ce secteur sont généralement intéressés par la réduction des délais, que ce soit pendant la phase de développement du produit ou dans un scénario de pièces de rechange comme la Formule 1, où ils doivent atteindre des sommets. pièces fonctionnelles de qualité assez rapide.
En plus des délais, je dirais aussi que le coût est un autre problème pour le secteur.
Avec cela à l'esprit, la question devient comment pouvez-vous vous assurer que les délais et les coûts sont réduits avec les additifs ? Ceci est important, en particulier par rapport aux méthodes de fabrication traditionnelles.
La consolidation des pièces en est une partie importante. Cela pourrait signifier, par exemple, être capable d'imprimer une pièce auparavant composée de 10 composants individuels, en une seule fois. C'est génial car cela conduit à moins d'inspections de qualité et, bien sûr, à moins de temps d'assemblage.
En même temps, si nous concevons une pièce pour additif, nous devons nous assurer que ces composants sont optimisé. Cette optimisation conduit généralement à une augmentation des performances et cette amélioration des performances a tendance à être une excellente analyse de rentabilisation pour nos clients.
C'est aussi ce que le sport automobile recherche en permanence :la réduction des délais est certainement toujours le principal moteur, mais cela est lentement remplacé par des problèmes plus axés sur les performances. Étonnamment, la réduction du poids n'est généralement pas un facteur déterminant lorsque nous reconcevons des composants pour les constructeurs automobiles.
Pensez-vous que les entreprises qui sollicitent vos services ont déjà une bonne compréhension de la FA, ou sont-elles vraiment au début de la compréhension de ce qui peut être fait avec la technologie ?
L'industrie a vraiment changé au cours des dernières années.
Lorsque nous avons lancé APWORKS en 2013, la plupart de nos clients avaient très peu de connaissances sur ce que la technologie peut faire.
Fait intéressant, bien que nous ayons encore quelques clients avec peu de connaissances en FA, nous avons un nombre croissant de clients qui sont conscients des avantages de la technologie et de ce qu'on peut en faire. C'est formidable, car ces clients comprennent vraiment où se situe l'analyse de rentabilisation et comment tirer le meilleur parti de la fabrication additive.
Pour nos clients qui ont besoin de plus d'informations sur les additifs, cela peut prendre beaucoup de temps. Ils doivent retourner dans leurs entreprises, diffuser l'idée de l'additif et essayer d'étudier une voie appropriée qui a du sens pour l'additif. Bien entendu, nous accompagnons nos clients dans ce voyage.
Si je devais chiffrer, je dirais qu'environ 60% de nos clients connaissent très bien la FA. Les 40 % restants ont encore besoin d'un peu d'éducation.
Vous avez évoqué l'importance d'avoir une analyse de rentabilisation pour la FA. De quelles manières les entreprises peuvent-elles identifier les bonnes applications pour la FA ?
Il n'y a pas de réponse unique à cette question; cela dépend beaucoup de l'industrie et de l'application spécifique.
Avec nos clients, nous avons tendance à repartir de zéro, avec une approche green field pour ainsi dire. Nous ne voulons donc pas savoir à quoi ressemblait la pièce avant, ni quelle méthode de production a été utilisée. Au lieu de cela, nous collectons des conditions aux limites pour essayer de proposer une nouvelle conception multiphysique optimisée avec des performances améliorées - qui ne peuvent être obtenues qu'avec l'impression 3D.
Nos clients souhaitent généralement que nous réduisions les délais et réalisions des économies de matière. Avec ces informations, sachant ce que veut un client, nous pouvons facilement déterminer s'il y a ou non une analyse de rentabilisation à avoir. Nous affinons ensuite notre entonnoir de sélection de pièces pour sélectionner les pièces qu'il est logique d'examiner de plus près. Ensuite, en fonction de ces intrants et des divers besoins et demandes des clients, nous élaborons généralement une analyse de rentabilisation.
Beaucoup a été dit sur la nécessité d'une approche de conception différente en matière de FA. Comment APWORKS relève-t-il le défi de la conception pour la fabrication additive ?
Premièrement, nous essayons d'avoir des ingénieurs qui sont doués dans au moins une discipline de l'environnement additif, que ce soit dans la conception ou la production.
Nous priorisons également la formation. Nous proposons de nombreuses formations sur le tas, en veillant à combiner la capacité de conception avec la connaissance des processus dont vous avez besoin afin de concevoir en conséquence.
C'est donc tout à fait la configuration que nous avons chez APWORKS :notre personnel n'est pas seulement doués pour la conception, mais ils ont aussi plus ou moins une formation en production. Tout ce que nous concevons, nous pouvons également le produire.
Un défi auquel beaucoup de nos clients sont confrontés est que leurs ingénieurs ne savent souvent pas comment concevoir pour les additifs. C'est pourquoi nous essayons également de transférer les connaissances que nous avons à nos clients.
Pour nous, cette approche a du sens car une fois que vous transférez ces connaissances, les entreprises reviendront généralement vers vous car elles sont plus informées. et sont en mesure d'aller plus vite.
Nous voyons cela comme une opportunité pour APWORKS, car même dans les universités, du moins en Allemagne, le design pour la FA n'est pas encore très largement enseigné, du moins pas à ma connaissance.
L'année dernière, APWORKS a dévoilé sa poudre métallique à haute résistance, Scalmalloy®. Quels sont certains des avantages du matériau - et avez-vous des plans pour un développement ultérieur du matériau à l'avenir ?
L'argument de vente unique de Scalmalloy® est qu'il combine une résistance élevée avec un niveau élevé de ductilité. En règle générale, vous avez soit un matériau fragile qui est très résistant, soit un matériau très ductile qui est relativement faible. Scalmalloy® combine le meilleur des deux mondes.
Nous recevons parfois des clients qui nous demandent si nous pouvons développer des matériaux personnalisés. Avec Scalmalloy®, nous avons eu la chance que ce matériau révèle exactement les propriétés matérielles que nous attendions d'un alliage d'aluminium à haute résistance.
Cependant, nous ne nous concentrons généralement pas beaucoup sur le développement de nouveaux matériaux à partir de zéro. Au lieu de cela, nous prenons des matériaux existants, tels que Ti6Al4V, AlSi10Mg et 316L, et utilisons les paramètres de processus de notre système pour adapter le matériau à un cas d'utilisation spécifique.
C'est beaucoup plus efficace que de devoir constamment développer des matériaux complètement nouveaux. Par exemple, nous avons pu développer un paramètre de procédé optimisé pour le Ti64 afin d'augmenter sa résistance ultime à la traction de près de 30 %, tout en conservant le même allongement à la rupture. Ceci a été réalisé simplement en faisant varier les paramètres de processus en conséquence.
La façon dont nous avons tendance à aborder le développement de matériaux est la suivante :un client nous aborde avec un certain problème et nous essayons de trouver la bonne approche de conception pour résoudre le problème. Cette approche de conception est généralement liée au matériau. Ainsi, même si nous utilisons un matériau assez standard comme le Ti64, nous pouvons toujours expérimenter avec les paramètres du processus pour tirer le meilleur parti du matériau.
Côté logiciel, APWORKS a développé son logiciel AMXpert. Pouvez-vous m'en dire plus sur le logiciel et pourquoi vous l'avez développé ?
Le logiciel que nous utilisons a deux objectifs principaux. La première consiste à fournir aux clients un moyen d'obtenir rapidement des offres et des devis dans notre système.
Vous pouvez télécharger la géométrie, sélectionner le matériau que vous souhaitez et vous obtenez un devis, ou vous pouvez même le commander tout de suite. C'est donc un système de manipulation.
Deuxièmement, les clients peuvent utiliser le logiciel pour filtrer leurs portefeuilles de pièces. Vous pouvez facilement télécharger des centaines de milliers de pièces et de géométries. Le système est rattaché à notre base de données de connaissances interne, où sont stockés tous les travaux que nous avons imprimés au cours des cinq dernières années.
Cette base de données contient des analyses de tous les travaux que nous avons effectués dans le passé, y compris ce qui a échoué dans le passé, quelle combinaison de matériaux et de conception est logique, épaisseur de paroi minimale et ainsi de suite. Essentiellement, cela vient avec toutes ces leçons que nous avons apprises au cours des années où nous utilisons la FA.
Nous permettons à nos clients d'utiliser AMXpert gratuitement parce que nous voulons éduquer les clients dans leur processus de sélection de pièces afin qu'ils puissent facilement identifier les pièces qu'il est logique de produire avec un additif.
Y a-t-il des histoires de réussite que vous pouvez partager ?
Malheureusement, une grande partie de notre travail est confidentielle.
Cependant, nous avons beaucoup travaillé dans l'industrie de la mode. Nous avons également produit des pièces pour diverses équipes de Formule 1, principalement en prototypage, ainsi que des pièces pour l'industrie de la robotique. L'outillage pour l'automobile est une autre application populaire.
Notre projet le plus médiatisé à ce jour est peut-être notre vélo Light Rider que nous avons développé en 2016. Le Light Rider est la première moto imprimée en 3D au monde et utilise notre métal Scalmalloy®. C'est une moto électrique légère et 30% plus légère que les motos électriques de fabrication traditionnelle.
Au départ, nous voulions être une vitrine intéressante, mais nous avons maintenant beaucoup de clients qui souhaitent acheter la moto ! La question pour nous, comme toujours, est de trouver l'analyse de rentabilisation pour vendre le vélo dans le commerce, d'autant plus qu'il est assez coûteux à produire.
Mais qui sait, peut-être que dans quelques années vous verrez le Light Rider dans les rues.
Les problèmes liés à la certification et à la qualité des pièces sont deux sujets de discussion clés dans l'industrie. Est-ce que vous avez également rencontré ces défis chez APWORKS ?
Je pense que l'industrie est encore en train de comprendre ces choses. Être capable de remplir certains critères de qualification est particulièrement important si vous souhaitez utiliser des additifs dans des marchés hautement réglementés comme l'aérospatiale.
Les grands équipementiers ont tous certains critères de qualité et vous, en tant que fournisseur, devez les respecter.
Parfois, ces exigences sont venues de technologies existantes comme le forgeage, le moulage et l'usinage , mais sont simplement appliqués à la FA sans même penser qu'il s'agit probablement d'un mode de production complètement différent. Cela le rend assez difficile de temps en temps.
Si vous avez des pièces forgées aujourd'hui et que vous souhaitez les imprimer demain, vous devrez bien sûr remplir les mêmes critères de propriété matérielle avec votre pièce imprimée en 3D, ce qui est presque impossible.
Mais avec la bonne approche et certaines connaissances de qualité, cela peut être fait.
Et avec le temps, nous verrons davantage de normes se développer pour la FA. L'un des défis actuels est qu'il n'y a tout simplement pas encore assez de règles pour la FA. L'industrie essaie de normaliser les processus de production et le fonctionnement des différentes méthodes de production, par exemple. Cela inclut non seulement le fonctionnement des machines, mais également la caractérisation des poudres, l'apparence de la chaîne de post-traitement, la formation que les opérateurs de machines doivent avoir, etc.
Pour ceux qui débutent dans l'impression 3D métal, comment peuvent-ils être sûrs de la technologie qu'ils doivent envisager pour une application spécifique ?
Cela peut souvent être une question complexe pour les entreprises.
En tant que petite ou moyenne entreprise qui débute dans le domaine des additifs, vous pouvez le faire comme la plupart des autres entreprises :acheter une imprimante et peut-être engager un consultant pour vous aider à fabriquer les bonnes pièces et les bonnes décisions.
Mais cette approche peut souvent être une perte de temps et d'argent, car les entreprises n'ont pas d'abord développé une analyse de rentabilisation pour la FA. Nous l'avons vu maintes et maintes fois, où des entreprises ont investi dans des imprimantes 3D pour découvrir qu'elles n'avaient aucune analyse de rentabilisation, aucune charge sur leurs machines - et elles finissent par être amèrement déçues.
Donc, avant de dépenser de l'argent ou d'investir dans des machines, je conseillerais aux entreprises de parler d'abord avec d'autres qui ont utilisé avec succès l'impression 3D pour générer des bénéfices. Apprenez de ceux qui ont déjà réussi dans le domaine et connaissent très bien la FA.
Comment voyez-vous l'industrie de la FA évoluer au cours des cinq prochaines années ?
L'industrie évolue de plus en plus et se dirige vers l'industrialisation.
Au fur et à mesure que l'industrie s'industrialise, se pose la question de savoir comment gagner de l'argent avec la technologie maintenant. Il ne s'agit plus de R&D; il s'agit de faire une analyse de rentabilisation avec la technologie.
De plus, à mesure que de plus en plus de clients se familiarisent avec la FA, nous croyons fermement que l'industrie s'oriente vers la production en série. En fait, c'est ce que nous faisons au quotidien.
De plus, les universités et les entreprises comme APWORKS proposent de plus en plus d'enseignements, et nous voyons de plus en plus d'applications qui ont du sens d'un point de vue commercial.
Ce qui va aider, c'est le fait que les machines s'améliorent d'année en année. Plus les machines sont efficaces et productives, plus il est facile de réaliser une analyse de rentabilisation pour votre application.
Cela dit, l'additif sera toujours une méthode de production pour des applications de niche. Je ne pense pas que cela remplacera un jour l'usinage ou même le moulage.
Mais si vous deviez me poser à nouveau cette question dans cinq ans, je dirais que non seulement nous avons beaucoup plus d'applications pour l'additif, mais c'est vraiment devenu une méthode de production normalisée, comme le moulage ou l'usinage.
Enfin, que réserve le reste de l'année 2019 à APWORKS ?
Jusqu'à présent, nous nous sommes consacrés à éduquer notre clientèle et à les aider à produire et à concevoir des pièces et des produits optimisés grâce à la fabrication additive. Cela ne changera pas.
Mais ce qui a changé, c'est que notre entreprise est de plus en plus axée sur les produits. En plus du travail de production que nous réalisons pour nos clients, nous voulons également nous concentrer sur la sortie de notre premier produit. Les détails sont encore confidentiels, mais nous sommes actuellement en train de développer un nouveau produit qui utilise la FA de la meilleure façon possible.
Nous nous concentrons également sur l'expansion. À l'heure actuelle, APWORKS opère principalement depuis l'Europe, mais nous cherchons à évoluer rapidement en tant qu'entreprise. Pour y parvenir, nous visons à accroître notre présence aux États-Unis cette année, afin de fournir une assistance sur site à nos clients aux États-Unis.
Pour en savoir plus sur APWORKS, visitez : https://apworks.de/
Entrevues d'experts
La série d'entretiens d'experts d'AMFG présente des entreprises et des individus innovants qui contribuent à façonner l'avenir de la fabrication additive. Pour plus d'informations sur la participation à la série, veuillez contacter [email protected].
impression en 3D
- Scalmalloy :le dernier matériau hautes performances pour l'impression 3D sur métal
- Entretien d'experts :Duncan McCallum, PDG de Digital Alloys, sur l'impression Joule et l'avenir de l'impression 3D sur métal
- Entretien d'experts :Guillaume de Calan, PDG de Nanoe, sur l'avenir de l'impression 3D céramique
- Entretien d'experts :John Kawola, président d'Ultimaker, sur l'avenir de l'impression 3D
- Comment Ford Motor Company innove l'impression 3D pour l'industrie automobile :entretien d'expert avec Harold Sears
- Entretien d'experts :Simon Fried, cofondateur de Nano Dimension, sur l'essor de l'impression 3D pour l'électronique
- Entretien d'experts :PDG de PostProcess Technologies sur la résolution du goulot d'étranglement du post-traitement pour la fabrication additive
- Trouver les bons outils pour le prototypage à petit budget
- Le cas de l'impression 3D dans le secteur manufacturier