Vers une fabrication numérique de fibres multimatériaux intelligentes
Résumé
Les fibres sont omniprésentes et généralement passives. L'optoélectronique réalisée dans une fibre pourrait révolutionner de multiples domaines d'application, notamment l'électronique biosynthétique et portable, la détection environnementale et la récupération d'énergie. Cependant, la réalisation d'électronique haute performance dans une fibre reste un défi exigeant en raison du caractère insaisissable d'une stratégie de traitement des matériaux qui permettrait d'envelopper des dispositifs fabriqués dans des semi-conducteurs cristallins, tels que le silicium, dans une fibre dans un ordre ordonné, adressable, et de manière évolutive. Les approches actuelles de fabrication de capteurs à fibre sont soit non évolutives, soit limitent le choix des semi-conducteurs aux semi-conducteurs amorphes, tels que les verres chalcogénures, inférieurs au silicium dans leurs performances électroniques, ce qui entraîne une bande passante et une sensibilité limitées de ces capteurs par rapport à un silicium standard. photodiode. Notre groupe justifie une fabrication universelle dans la fibre de circuits logiques et de systèmes sensoriels analogues à l'intégration à très grande échelle (VLSI), qui a permis l'émergence du microprocesseur moderne. Nous développons une méthodologie de fabrication hybride polyvalente qui assemble des architectures de matériaux dans la fibre typiques des dispositifs et systèmes microélectroniques intégrés en silice, silicium et métaux à haute température. Cette méthodologie, baptisée « VLSI for Fibers » ou « VLSI-Fi », combine l'impression 3D de préformes, un étirage thermique des fibres et un assemblage post-étirage de dispositifs intégrés intégrés dans les fibres au moyen d'une rupture capillaire spatialement cohérente et sélective du matériau. des noyaux de fibres. Nous pensons que cette méthode fournira une nouvelle classe de dispositifs à fibre optique omniprésents, durables et à faible coût, permettant l'intégration de tissus rencontrés avec des objets fabriqués par l'homme, tels que des meubles et des vêtements, dans l'Internet des objets (IoT). En outre, cela stimulera l'innovation dans l'impression 3D, étendant l'approche de fabrication numérique au domaine de la nanoélectronique.
Introduction
Bien que les fibres étirées de verre remontent à l'époque romaine, les premières fibres optiques fonctionnelles ont été fabriquées en 1792 par les frères français Chappe à des fins de communication [1]. En 1842, Jean-Daniel Colladon, un physicien suisse, montra que la lumière pouvait être guidée de l'intérieur par un jet d'eau [2]. Ces deux découvertes ont donné naissance à des décennies d'améliorations en matière d'ingénierie optique et matérielle menant aux fibres efficaces d'aujourd'hui, permettant des télécommunications à haut débit et le stockage de données sur des kilomètres de distance à travers le monde, comme le câble sous-marin transpacifique (TPC) de 25 000 km de long achevé en 1996 [3, 4]. De plus, les capteurs à fibre optique (FOS) sont utilisés pour une grande variété d'applications biomédicales, pétrolières et gazières, marines, architecturales, chimiques et aérospatiales [5, 6].
Le contrôle et l'amélioration des performances de propagation de la lumière à l'aide de fibres à cristaux photoniques (PCF) développées en 1996 par Philip Russel ont ouvert les portes à des recherches sur des structures fonctionnelles internes de fibres plus complexes [7,8,9]. De nouvelles microstructures ont également accueilli l'intégration de la diversité des matériaux dans leur constitution [10, 11] pour concevoir des fibres intelligentes pour l'électronique [12], l'optoélectronique [11], la synthèse in-fiber [13], la microfluidique [14], les systèmes microélectromécaniques [15, 16], et l'interfaçage biosynthétique [17]. Les fibres intelligentes diffèrent des fibres traditionnelles en incluant une fonction non traditionnelle au-delà de la communication optique et de l'utilisation typique des fibres dans les tissus commerciaux. Les fibres intelligentes peuvent être utilisées pour l'esthétique dans les textiles électroniques en contrôlant l'aspect coloré des fibres en raison des interférences optiques dans leur microstructure [18] ou pour améliorer les performances, par exemple dans le cas des guides de fibres optiques classiques et du revêtement miroir diélectrique permettant le guidage de la lumière. par voie aérienne [19, 20].
Pour rendre une fibre fonctionnelle, elle doit être composée de matériaux aux propriétés électroniques variables, son architecture doit être spécifiquement conçue pour remplir une fonction donnée, et ses caractéristiques internes doivent être réduites à l'échelle nanométrique, des ordres de grandeur plus petits que le cœur des télécommunications actuelles. fibres. Les fibres sont généralement créées par des procédés de fabrication de fibres optiques, c'est-à-dire qu'elles sont étirées thermiquement à partir de tiges macroscopiques cylindriques ou cuboïdes appelées « préformes ». Le processus de fabrication commence par une sélection de matériaux de noyau et de gaine appropriés, tels que les métaux, les isolants et les semi-conducteurs. Par exemple, la première fibre comprenant des structures métal-isolant-semiconducteur a été développée en 2004 pour la photodétection [21]. Les matériaux pour la préforme sont sélectionnés de telle sorte que leurs viscosités, μ , sont comparables à la température d'étirage, tombant approximativement dans la fenêtre de 4 < log(μ )[poise] < 6. Ceci est nécessaire pour empêcher les écoulements de cisaillement et les instabilités capillaires qui autrement déforment la géométrie du dispositif à fibre. Les matériaux pour lesquels cette exigence est inaccessible, tels que les métaux ou les semi-conducteurs cristallins qui sont très minces sous leur forme liquide lors du fibrage, doivent être confinés dans des canaux à faible allongement, avec une géométrie proche de l'équilibre.
La préforme, qui est essentiellement une version agrandie de la fibre, peut être construite à l'aide de diverses techniques telles que le roulement de feuilles de matériau comme un tapis, l'empilement de pièces fraisées comme un puzzle ou l'impression 3D, comme le montre la figure 1a. (I) et discuté dans cette revue, puis consolidé par un frittage sous vide. La préforme est ensuite chauffée dans un four et allongée en une fibre comme un caramel ou une tire (voir le cône de dessin sur la figure 1a (II)), tout en préservant sa disposition en coupe transversale basée sur les propriétés thermomécaniques données d'une construction telles que les viscosités, l'interface énergies, adhérence mutuelle et dilatation thermique différentielle (Fig. 1a (III)) [22]. Ce procédé, pour le cas d'une préforme imprimée en 3D, est illustré schématiquement sur la figure 1a. Un tirage typique peut produire des kilomètres de fibre avec des diamètres de section transversale nanométriques très fins d'environ 5 nm [23, 24].
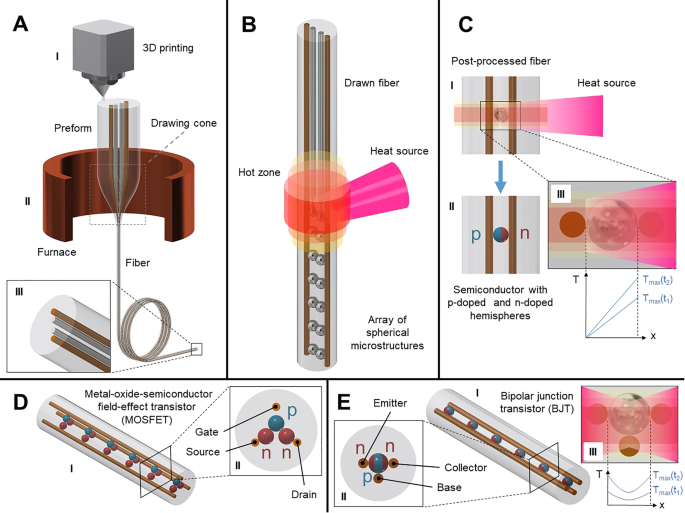
VLSI-Fi :Schémas conceptuels de la technique VLSI-Fi représentant l'approche « 2D + 1D + 0D ». a La préforme imprimée en 3D a (I) est étiré thermiquement a (II) en une fibre longue et fine qui préserve la géométrie de la section transversale de la préforme (2D). b Motif axial de la fibre via une rupture capillaire spatialement cohérente et sélective du matériau (+1D), résultant en l'assemblage de noyaux séparés initialement continus en réseaux de dispositifs discrets mis en contact en parallèle. c Contrôle du dopage basé sur la ségrégation dans les particules semi-conductrices post-éclatement, permettant le contrôle de l'architecture interne d'un appareil individuel c (II) par gradient thermique c (III). d (I) Illustration schématique du transistor à effet de champ métal-oxyde-semiconducteur (MOSFET) via VLSI-Fi, où les semi-conducteurs de type p et de type n sont indiqués en bleu et en rouge, respectivement. Les tiges continues dorées noyées dans une fibre de silice servent de grille, de source et de drain. La section transversale de fibre résultante est indiquée dans d (II). De même, e (I) montre une image schématique d'un transistor à jonction bipolaire (BJT) réalisé par VLSI-Fi, réalisé avec des sources de chaleur incidentes des côtés émetteur et collecteur. La section transversale de la fibre e (II) montre l'émetteur, le collecteur et la base du BJT (tiges continues intégrées dans la fibre), avec les semi-conducteurs de type p et de type n de la jonction n-p-n indiqués en bleu et en rouge, respectivement
Dans une étape post étirage, jouant sur les instabilités capillaires, la fibre peut être reliquéfiée par chauffage pour permettre la rupture des coeurs d'une manière sélective de matériau spatialement cohérente, permettant un contrôle axial sur les structures fibrées [25,26, 27] comme illustré sur la figure 1b. Des techniques alternatives pour modeler les noyaux axialement incluent l'exposition aux UV à travers des photomasques dans des noyaux photopolymères, résultant en des microparticules de forme non triviale [28]. D'autres techniques de fonctionnalisation hybride incluent le revêtement des surfaces des fibres avec des matériaux fonctionnels [10, 29] et le confinement d'une gaine de fibre par un tirage [12] à un réseau de dispositifs optoélectroniques fabriqués par la fabrication standard de métal-oxyde-semiconducteur complémentaire (CMOS).
Les fibres peuvent être tissées dans des tissus ou des filets pour atteindre une fonctionnalité collective qui dépasse celle d'une fibre individuelle [30]. Conçues par biomimétisme, les fibres peuvent être façonnées en fonction des caractéristiques utiles de la nature pour améliorer la fonctionnalité du tissu, telles que l'hydrophobie [31]. Les fibres peuvent également être conçues comme des plates-formes de synthèse pour la production de matériaux peu coûteux tels que la conversion de noyaux d'aluminium en silicium dans des fibres gainées de silice [13] ou la fabrication thermiquement induite de structures poreuses par séparation de phases [32]. Les fibres peuvent également servir à la détection de signaux distants et distribués, comme la détection chimique environnementale de substances volatiles dangereuses [29]. La flexibilité de la conception des fibres est telle que plusieurs modalités fonctionnelles peuvent être intégrées dans une seule fibre pour des applications complexes telles que la stimulation spino-corticale profonde et la surveillance chez la souris pour la recherche sur les maladies neurodégénératives [33]. Ces exemples montrent une partie de la variété des domaines dans lesquels les fibres intelligentes sont la solution naturelle.
Motivation
Même si les fibres sont universellement omniprésentes, l'intégration de systèmes microélectroniques performants au sein d'une fibre mince reste un défi majeur [11, 12]. Différentes approches répondant à ce défi ont été proposées, avec des efforts principalement concentrés sur les matériaux à basse température. Par exemple, le dépôt chimique en phase vapeur à haute pression (HPCVD) a été utilisé pour intégrer des semi-conducteurs composés dans des fibres optiques microstructurées (MOF) [34], ainsi que pour créer des fibres à jonction p-i-n flexibles en silicium [35]. Alternativement, un CO2 le laser a été utilisé pour la recristallisation du cœur de SiGe dans des fibres de silice afin de concevoir leurs propriétés électroniques [36]. De telles approches aboutissent soit à des dispositifs avec une bande passante électronique limitée, comme c'est le cas avec les matériaux de chalcogénure, qui sont intrinsèquement amorphes ou sont intrinsèquement non évolutifs.
À ce titre, le Laboratoire des systèmes activés pour la fabrication de fibres et d'additifs (Laboratoire FAMES) a développé et met actuellement en œuvre une technique de contrôle de l'architecture 3D des fibres, qui est décrite dans cette revue. Étant donné que la complexité de la fibre finale est corrélée à la complexité de la section transversale de la préforme, la fabrication sous forme libre de préformes permet des fonctionnalités de dispositif à fibre inaccessibles autrement. De plus, l'impression 3D est largement accessible, ce qui en fait une alternative technologique rentable et conviviale aux méthodes traditionnellement utilisées, permettant une large gamme de matériaux, des thermoplastiques aux matériaux haute température, en passant par les biomatériaux [37].
De plus, le FAMES Lab a la capacité de traiter des matériaux à haute température, parallèlement à l'utilisation plus traditionnelle des thermoplastiques dans la fabrication additive, nous permettant de profiter de propriétés telles que la mobilité électronique élevée dans Si/Ge [38], ainsi que comme utilisation future du titanate de zirconate de plomb (PZT)/BaTiO3 composites pour applications piézoélectriques ayant de grands coefficients piézoélectriques par rapport aux polymères [39, 40] et une bande passante acoustique plus élevée [41].
Avec ces défis à l'esprit, nous proposons des solutions d'optimisation utilisant la fabrication additive pour réaliser une fabrication de préformes plus rapide et plus complexe, des simulations de rupture capillaire pour optimiser le contrôle axial de la fibre et des combinaisons de nos fibres avec l'ingénierie tissulaire. Ces stratégies permettent la création de plates-formes biomédicales réalistes dotées de capacités de biodétection et de biofonctionnalisation pour l'analyse de médicaments et de traitements in vitro, l'une des applications prometteuses des dispositifs à fibres.
Concept
Afin de réaliser des fibres fonctionnelles, nous nous inspirons de l'intégration à très grande échelle (VLSI) - une technique de conception et de fabrication numérique qui a donné naissance au microprocesseur moderne dans les années 1970. Cette technique utilise la photolithographie et le traitement chimique/thermique des zones exposées de la plaquette de substrat semi-conducteur pour définir les caractéristiques du circuit intégré dans cette couche (2D) tandis que la fabrication d'un circuit complet progresse par empilement de ces couches individuelles dans la direction perpendiculaire à la surface de la plaquette (+1D). De plus, le dopage électronique des composants individuels du circuit (+0D) peut être contrôlé par implantation et activation thermique [42]. Notre approche des fibres, baptisée « VLSI for Fibers » ou « VLSI-Fi », est analogue :tout d'abord, la fabrication additive et l'étirage thermique d'une préforme définissent la géométrie de la section transversale du dispositif fibre (2D); deuxièmement, la fibre résultante peut ultérieurement être configurée axialement (+1D), permettant l'assemblage de réseaux de dispositifs discrets intégrés à partir de cœurs initialement continus mais séparés ; et troisièmement, une structuration basée sur la ségrégation de dispositifs individuels intégrés dans la fibre (0D) peut être effectuée. Le tableau 1 dresse une comparaison entre les deux techniques, mettant en évidence la correspondance entre chaque degré de contrôle géométrique rendu possible par chaque technique (« 2D + 1D + 0D »). Les schémas des étapes décrites sont présentés en détail sur la figure 1, où des exemples de dispositifs intégrés dans la fibre possibles pourraient être réalisés à l'aide de la technique VLSI-Fi.
Section expérimentale
Dans cette section, nous décrivons d'abord nos travaux sur l'impression 3D de préformes en polycarbonate, suivis des avancées récentes dans l'impression 3D du verre par stéréolithographie. Ensuite, nous abordons la configuration axiale des fibres à travers une rupture capillaire spatialement cohérente et sélective du matériau, qui permet l'assemblage de noyaux séparés initialement continus en réseaux de dispositifs discrets mis en contact en parallèle. Enfin, nous proposons l'application de nos fibres de biointerfaçage, combinées à l'ingénierie tissulaire pour surveiller la croissance des tissus viables in vitro. Les fonctions sont activées en utilisant des canaux microfluidiques dans la fibre pour fournir des cellules et des produits biochimiques de signalisation et des fils en alliage à mémoire de forme pour le contrôle des mouvements, et des éléments piézoélectriques pour cartographier l'environnement par ondes ultrasonores.
Dessin de préformes imprimées en 3D
Comme indiqué précédemment, les techniques de fabrication de préformes conventionnelles, telles que le laminage de couches minces et l'empilage et le brut [10], sont limitées dans la production de structures géométriques complexes, prennent un temps considérable dans le processus d'étirage des fibres et nécessitent des compétences qualifiées. main-d'œuvre et équipements coûteux. L'impression 3D résout ces problèmes à l'aide d'un matériau de support soluble et de son processus en partie automatisé et convivial. Cela permet d'imprimer facilement des géométries très complexes dans un laps de temps relativement court.
Afin d'évaluer l'influence de l'angle d'impression des préformes en polycarbonate (Hatchbox 3D), des tiges cylindriques et carrées ont été imprimées à l'aide d'une imprimante FDM Prusa i3 MK2 à une tête. Les températures de l'extrudeuse et du lit d'impression ont été réglées à 235 °C et 105 °C, respectivement, et l'imprimante a été réglée pour produire des préformes de remplissage à 100 % avec une buse de 0,35 mm. L'orientation des couches dans la préforme dépend de l'orientation horizontale de la pièce par rapport au lit d'impression, et lorsque la préforme est introduite dans le four lors du tirage thermique, le flux thermique est affecté par l'orientation des couches. Pour tester quelle orientation était la mieux adaptée pour l'étirage thermique, des préformes avec des orientations de 0°, 15°, 30°, 45° et 90° ont été imprimées. Tous les angles ont été mesurés entre l'axe longitudinal de la préforme et l'axe horizontal. Les préformes imprimées en 3D ont subi le processus d'étirage thermique dans un four avec trois zones de température de 90 °C, 100 °C et 200 °C. Pour les préformes cylindriques, le tirage thermique a été réussi aux angles 0° et 45°. Les tirages de préformes à 90° échouent toujours en raison du délaminage de la couche.
Nous avons également réussi à dessiner des structures hors d'équilibre telles qu'une tige carrée avec un motif de remplissage improvisé, comme le montre la figure 2a (I), où au lieu du motif de remplissage rectiligne, le remplissage a également été configuré pour suivre les périmètres et imprimer dans une structure ordonnée. L'étirage de la préforme à base carrée à 0° a été un succès, et bien qu'il se soit légèrement déformé, la fibre était toujours capable de conserver la forme de la préforme. Des fibres avec des dimensions aussi faibles que 40 m × 60 m ont été étirées avec succès et sont illustrées sur la figure 2a, sans délaminage des couches. De plus, toutes les couches ont été correctement consolidées. Un exemple d'une section transversale de fibre est montré dans la Fig. 2a (IV), et des images d'une fibre avant et après recuit sont montrées dans Fig. 2a (V) et 2a (VI), respectivement, où nous voyons que la fibre recuite atteint une transparence optique, qui sera caractérisée dans des travaux futurs. De ces expériences, nous concluons que les préformes les plus réussies sont celles imprimées à 0°, alors que 90° se délaminent toujours pendant le processus d'emboutissage. La consolidation des couches dans les fibres étirées thermiquement s'est améliorée à mesure que l'angle d'orientation de la préforme imprimée en 3D diminuait.
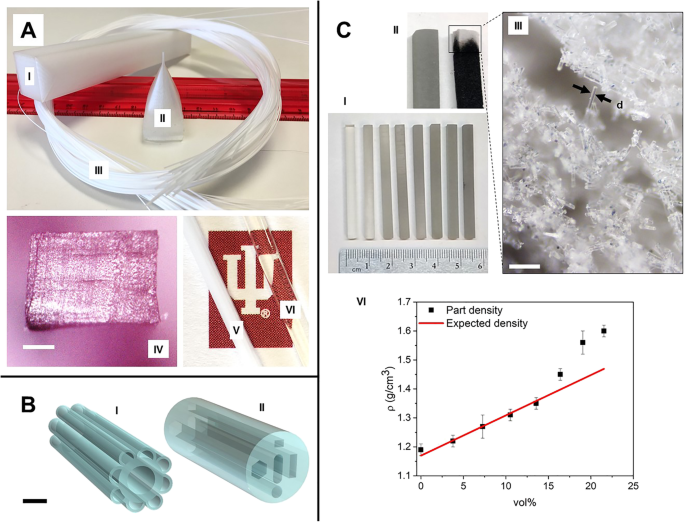
Préformes imprimées en 3D :a (I) Préforme en polycarbonate imprimée en 3D à base carrée. un (II) Cône de dessin. un (III) Fibre de polycarbonate résultante après étirage thermique. un (IV) Section transversale de la fibre après le processus d'étirage, sans délaminage de la couche. La section transversale est rectangulaire en raison de la porosité non isotrope du motif de remplissage (barre d'échelle 200 μm). un (V) Fibre étirée avant recuit. un (VI) Fibre étirée après recuit avec transparence optique apparente. b Modèles CAO de préformes en verre, réalisées avec succès en verre sodocalcique avec impression 3D par extrusion de haute précision. b (I) La structure imite les cheveux bleus de tarentule. b (II) Modèle de préforme avec géométrie de section transversale hors d'équilibre (barre d'échelle 1 cm). c (I) Échantillons de verre de forme carrée avec remplissage de verre croissant (de gauche à droite), imprimés avec la technique SLA. c (II) Détail de l'échantillon de verre avant la cuisson (à gauche) et pendant la cuisson (à droite). Dans ce dernier, il est possible de voir la coloration noire résultant des résidus carbonisés de résine, tandis que la pointe présente une coloration blanche après que ces résidus ont été cendrés. c (III) Image au microscope de la section cendrée (barre d'échelle 200 μm), où la coloration blanche est le résultat de la couleur naturelle des fibres broyées compactées dans une structure poreuse interconnectée. De plus, la largeur nominale de la fibre de verre, indiquée dans l'image par d, est corrélée aux valeurs attendues de 16 μm (#38 Fiber Glast). c (IV) Un tracé des densités des préformes de verre imprimé (ρ ) en fonction de la fraction volumique de fibres de verre mélangées à de la résine, ainsi que de la densité moyenne du matériau d'impression
Impression 3D de préformes en verre
Au-delà des thermoplastiques, les verres, y compris le quartz fondu, ont d'importantes applications scientifiques et techniques dans les domaines de l'optique, des communications et de l'électronique [43]. Les fibres de silice structurées pourraient bénéficier à de multiples applications, par exemple la coloration sans colorant des tissus pour la mode, les fibres à cristaux photoniques pour la détection optique-chimique ou les fibres monomodes pour les télécommunications et la focalisation étroite de la lumière. Ces fibres sont généralement fabriquées par un procédé en 2 étapes :la fabrication des préformes et l'étirage thermique des préformes en une fibre. Alors que le processus d'étirage est relativement simple et bon marché, la fabrication de la préforme, à ce stade, nécessite un traitement au cas par cas, et pour chaque configuration de préforme spécifique, une technologie distincte doit être développée et appliquée.
La figure 2b montre des modèles de conception assistée par ordinateur (CAO) de préformes en verre sodocalcique qui ont été réalisés avec succès avec une haute précision dans une technologie d'impression par extrusion similaire aux produits décrits par la société Micron3DP [44]. Ce matériau possède des propriétés optiques prometteuses en particulier dans les grandes longueurs d'onde telles que l'IR [45], ce qui en fait un candidat intéressant pour la fabrication de fibres avec de nouvelles fonctionnalités optiques. Le modèle de préforme illustré sur la figure 2b (I) imite la structure des cheveux de tarentule bleue, similaire à la structure présentée dans [46], et sur la figure 2b (II), la section transversale de la préforme contient des géométries non équilibrées et est donc sujette au remodelage en raison de la minimisation de la tension superficielle. Ces modèles ont été conçus et réalisés comme une vérification de la possibilité d'obtenir des sections transversales de préformes complexes et hors d'équilibre.
Étant donné que la structure de gaine assure l'intégrité mécanique de la fibre pendant le processus d'étirage - étant composée du matériau le plus visqueux - nos efforts se sont jusqu'à présent concentrés sur ce composant de la fibre, où nous visons finalement la conservation de la géométrie de la section transversale. de la préforme. A terme, nous visons à développer des techniques d'extrusion multimatériaux, qui nous permettront d'intégrer plusieurs matériaux de manière monolithique dans une même impression. Alternativement, il est possible de remplir la structure avec des matériaux en poudre tels que Si ou Ge. La structure chargée peut ensuite être frittée afin d'obtenir la préforme. Gumennik et al. ont décrit une approche similaire [47].
S'il y a un intérêt à produire une fibre avec du verre sodocalcique comme matériau d'âme, une approche simple consisterait à imprimer une préforme à âme suspendue. Les fibres à âme suspendue présentent un intérêt pour diverses applications, notamment la détection [48] et le guidage térahertz à faibles pertes [49], et sont généralement réalisées avec des polymères [49]. Dans ce type de géométrie de fibre, le noyau est soutenu par des entretoises qui le relient à la couche externe. Après étirage, ces structures sont réduites à des dimensions de l'ordre de la longueur d'onde d'intérêt, de sorte que, pour la lumière guidée, l'effet est celui d'un noyau suspendu. Monro et al. ont rapporté des fibres à noyau suspendu dans divers matériaux tels que la silice et le verre de bismuth [48]. Ils fournissent également une série d'exemples d'applications de détection de ces fibres, en particulier dans la détection biologique et chimique, confirmant la viabilité de ces géométries de fibres.
De nouvelles approches de l'impression 3D de verre basée sur la stéréolithographie à l'aide de résines personnalisées ont été conçues à l'aide d'un nanocomposite de silice photodurcissable [50]. Ici, nous proposons une méthode dans laquelle les préformes en fibre de verre sont fabriquées par impression 3D à partir de résines commerciales standard, ce qui en fait une méthode rentable et plus simple pour réaliser des pièces en verre imprimées en 3D à l'aide de la stéréolithographie (SLA). L'imprimante SLA (Form 2 by Formlabs) fonctionne à l'aide d'un laser d'une longueur d'onde de 405 nm pour réticuler la résine à travers le fond de la cuve alors que la plate-forme construite s'élève progressivement couche par couche.
Afin d'obtenir des impressions sur verre, nous utilisons un mélange de résine transparente commerciale (Formlabs FLGPCL04 Clear) avec des fibres de verre borosilicaté de 0,79 mm (1/32") (#38 Fiber Glast) pour le processus d'impression. Cela permet un grand contrôle de la composition finale du matériau d'impression et flexibilité pour obtenir les propriétés souhaitées de la fibre. Les fibres de verre ont été dispersées dans une résine transparente à l'aide d'un agitateur magnétique. Le verre est ajouté par petits incréments et homogénéisé pendant environ 3 min après chaque ajout. Pour le processus d'impression, l'imprimante a été réglée en mode ouvert pour permettre l'utilisation de notre résine personnalisée. Des préformes cuboïdes de dimensions 4 × 4 × 50 mm ont été imprimées à une orientation de 90°. Après l'impression, les pièces ont été immergées dans de l'isopropanol pendant 10 min pour éliminer l'excès de résine , et post-polymérisé avec une lumière UV pendant 30 min à 60 ° C. Les préformes en verre durci avec un rapport volumique croissant de fibres de verre mélangées à la résine d'impression (de gauche à droite) sont illustrées à la figure 2c (I).
Les préformes sont ensuite post-traitées afin de délianter la résine résiduelle et de fritter les particules de verre, résultant en une pièce entièrement composée de verre. Les effets de ces processus sur la préforme sont illustrés sur la figure 2c (II), où l'on voit une préforme après durcissement (à gauche) et après le processus de cuisson (à droite). Dans ce dernier, on peut voir la coloration noire résultant de la cuisson dans un four à incinération, tandis que la pointe présente une coloration blanche après déliantage. La figure 2c (III) montre une prise d'image au microscope d'une préforme avant frittage, où l'on peut voir que toute la résine est en effet cuite hors de la pièce, résultant en une structure interconnectée formée uniquement par les fibres de verre. Plusieurs paramètres doivent être contrôlés, tels que la température de cuisson et le profil de chauffe, afin de contrôler les réactions chimiques et le retrait. Le déliantage thermique du liant a été réalisé à l'aide d'un four à incinération. Les pièces brunes résultantes ont été frittées dans un four tubulaire à haute température. Le frittage a été réalisé à une température de 1300 °C et une pression de 5 × 10 −2 mbar, en suivant le protocole prescrit dans [51]. Une phase de maintien à 800°C a été réglée pour évaporer l'eau liée aux molécules et les groupes silanol liés à la surface. Le frittage sous vide améliore la transparence optique car il réduit le piégeage d'air à l'intérieur de la pièce en verre fritté [52].
Après le post-traitement, le volume et le poids des pièces sont mesurés afin d'obtenir la densité. Ceci est ensuite comparé à la densité moyenne du matériau d'impression - composé du mélange de résine durcissable et de fibres de verre - qui est calculée par ρ moyenne = ρ résine (1 − χ v ) + ρ verre (χ v ), où ρ résine = 1.17 g/cm 3 est la densité de la résine transparente durcie, ρ verre = 2,55 g/cm 3 est la densité des fibres de verre broyées, et χ v est le rapport volumique des fibres de verre mélangées à la résine.
Les résultats sont présentés dans le tableau 2 et graphiquement sur la figure 2c (IV), où nous présentons la densité des pièces imprimées pour différentes proportions volumiques de fibre de verre dans la résine, par rapport à la densité moyenne du matériau d'impression. On observe que, pour des ratios volumiques de verre mélangés à la résine plus faibles, les résultats obtenus sont conformes aux attentes. À des concentrations de verre plus élevées, cependant, nous constatons un écart par rapport au comportement linéaire de la densité idéale. Cela peut être attribué à la sédimentation pendant l'impression, qui devient importante à ces rapports de volume, produisant ainsi effectivement des concentrations plus élevées de verre dans ces impressions. Le processus d'impression se déroule au fond du réservoir, où la concentration de verre, due à la sédimentation, augmente constamment pendant l'impression. Il commence à partir (et au-dessus) de la concentration uniforme initiale qui devrait tomber sur la courbe calculée.
À partir du tableau 2, nous pouvons voir qu'à 21,54 vol% de pièces de remplissage en fibres de verre broyées, la densité mesurée était de 1,61 g/cm 3 , ce qui signifie que la proportion de volume réelle est de 31,88 vol%. Au cours du processus d'expérimentation, nous avons obtenu un échantillon avec un remplissage réel de 34,78 % en volume de fibres de verre broyées. Ce résultat n'était pas très éloigné du remplissage de silice à 37,5% en volume qui a été fabriqué par Kotz et al. [53], où une résine personnalisée a été développée, contrairement à la résine commerciale que nous utilisons dans ce travail. Les orientations futures de ce travail comprennent les procédures de traitement thermique, le frittage des pièces et l'étude des propriétés mécaniques et optiques des pièces résultantes.
Contrôle cohérent de rupture capillaire et de ségrégation sélective des matériaux du dopage
Une fois qu'une préforme est étirée thermiquement, le résultat est une fibre longue et mince dans laquelle la section transversale est préservée, comme le montre la figure 1a (III). Dans le cas d'une fibre avec un ou plusieurs cœurs, ceux-ci peuvent être structurés axialement grâce à un processus de rupture capillaire spatialement cohérent et sélectif du matériau [26], illustré à la Fig. 3. Alors que le modèle Tomotika explore la formation d'instabilités périodiques dans un cylindre de fluide infini et uniformément chauffé, tenant compte des effets du fluide environnant [55], propageant les instabilités de Rayleigh introduit le concept de propagation de front [56]. Bien que plusieurs exemples de traitements mathématiques des instabilités capillaires puissent être trouvés dans la littérature, comme dans Liang et al. [57], ces travaux se concentrent principalement sur les régimes isothermes, qui ne sont pas applicables dans notre cas. De plus, notre cas présente une complication supplémentaire de propagation du gradient thermique et donc du gradient de viscosité. En tant que tel, il est probablement plus proche du processus basé sur des critères d'instabilité marginale, comme mentionné dans Powers et al. [56]. En combinant à la fois nos résultats informatiques et expérimentaux, nous visons à établir un modèle mathématique pour la rupture de la fibre via des phénomènes de gradient thermique axial.
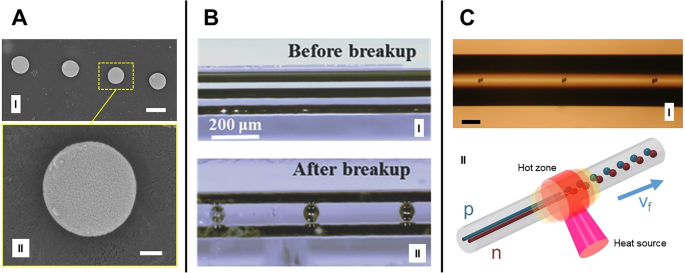
Rupture capillaire :a (I) Coupe de fibre montrant des sphères de Si formées par rupture capillaire (barre d'échelle 0,5 μm). un (II) Image d'une seule sphère représentant la qualité de la forme (barre d'échelle 100 nm), de Gumennik et al. [26]. b (I) Exemple de dispositif photodétecteur métal-semiconducteur-métal dans une seule fibre de silice avant b (I) et après b (II) processus de rupture, de Wei et al. [54]. c (I) Rupture d'une fibre à double cœur en clusters bi-sphériques (barre d'échelle 100 m), de Gumennik et al. [26]. c (II) Représentation schématique du processus montré en c (I), avec des noyaux de type p et n indiqués respectivement en bleu et en rouge
La présente étape de simulation de rupture capillaire se concentre sur le régime stationnaire. Nous nous intéressons à l'analyse de la façon dont les instabilités se développent d'abord dans une fibre initialement stationnaire soumise à un gradient thermique. Ce processus est analogue à l'étape initiale des expériences de rupture capillaire réalisées par Gumennik et al. [26], où une fibre de silice avec un noyau de Si de 4 m d'épaisseur est alimentée à travers la zone chaude d'une flamme hydrogène-oxygène à des débits de 0,3 et 0,1 L/min, respectivement. Bien que la température maximale atteignable avec ce type de torche puisse atteindre jusqu'à 2800 °C, la température maximale subie par la fibre doit être inférieure au point d'ébullition de la silice de 2230°C.
Considering that the flame width is between 3 and 3.5 mm and that the fiber has a diameter of about 300 μm, it is easy to understand why it is not feasible to experimentally measure the temperature gradient to which the fiber is exposed. Furthermore, the dynamic nature of the breakup process and the fact that it involves multiple materials with varying emissivities further adds to the complexity of the problem, while the fiber’s high aspect ratio and sharp viscosity ratios render the numerical simulation of the full Navier-Stokes equations computationally challenging.
In our simulations (using COMSOL Multiphysics® 5.3a, with its Microfluidics and Heat Transfer modules) shown in Fig. 4a, we assume an axisymmetric fiber with radius r fiber = 140 μm, composed of a thin Silicon core (r core = 2 μm) enclosed in a Silica cladding. Initial heat-transfer simulations showed that a fiber length of 15 mm is sufficient to ensure that the fiber extremities remain at room temperature, thus avoiding influence from the boundaries to the breakup process. Through the sweep of different parameters such as heat source length and distance to the fiber surface, as well as power, we can observe the changes produced in the breakup behavior, thus collecting information about the temperature gradient. Also of importance are the breakup period and speed, parameters which can be compared to experimental results and used for the refinement of the simulations.
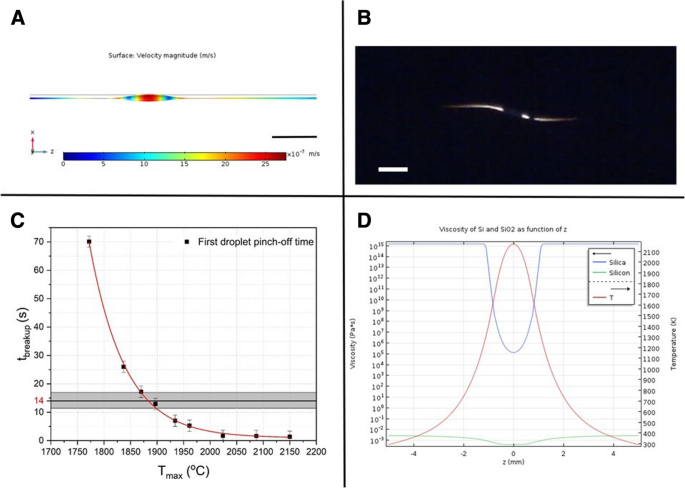
Capillary breakup simulations:a Image of the simulated Si core during the first droplet formation, right before the pinch-off for T max = 1900 °C. Color scale represents surface velocity (scale bar = 50 μm). b Snapshot of fiber breakup experiment recording just after the first droplet pinch-off, indicating a breakup time of 14 ± 3 s (scale bar = 60 μm). c Breakup time t breakup for different values of T max . The exponential dependence of t breakup on T max is evident, a behavior that is expected due to the dependence of t breakup on the core’s viscosity, which in turn depends exponentially on the temperature. The shaded rectangle encompasses the temperature range compatible with this breakup time-scale. d Si core and SiO2 cladding viscosities as a function of axial position, with temperature pro le over-imposed, for T max = 1900 °C
The simulations are performed in two steps:first, the steady-state temperature profile is calculated for different heat source powers, in order to achieve the desired maximum temperature T max . The results are then exported to a time-dependent fluid-flow simulation, where the Navier-Stokes equation is solved with time steps of 0.05 s, from 0 s until the first droplet pinch-off (t breakup ), which is dependent on T max , as can be seen in Fig. 4c, where t breakup is plotted for different values of T max . It is possible to observe that t breakup has an exponential dependence on T max , which is expected since t breakup is proportional to the core’s viscosity, which in turn is exponentially dependent on the temperature.
The relevant parameters used in these simulations are listed in Table 3. Preliminary simulations indicate that the phase transition of the Si core has no significant influence on the steady-state temperature pro le obtained, neither on the subsequent fluid-flow simulations since, in the entire region where the capillary instabilities occur, the temperature is higher than the melting point of Si. Therefore, in order to maintain the model as less computationally intensive, we simulate a core of liquid Si as a first approximation. Moreover, although a fully coupled heat-transfer and fluid-flow simulation is preferable, we consider that the effects of coupling bring second-order corrections to the solution and thus can be neglected at this stage. An image of the simulated core during the first droplet formation, right before the pinch-off, is shown in Fig. 4a, for T max = 1900 °C. A plot of the densities of silica and silicon, as a function of the axial position (in the simulation, the z-axis) for this particular simulation, is presented in Fig. 4d, with the temperature profile over-imposed.
Our results allow us to define the ranges of viscosities for which the time scales for breakup are comparable to those observed experimentally, thus assessing qualitatively the temperature profile imposed on the fiber. Fig. 4b shows a snapshot of a fiber breakup experiment recording just after the first droplet pinch-off, at the frame corresponding to t = 39 s. Since the resolution of the images before this frame is not ideal, judging on the basis of the symmetry of the breakup behavior, it is possible to assess that the pinch-off of the first droplet occurs at t = 35 ± 3 s, which translates to a breakup time after the temperature steady-state regime is achieved, of 14 ± 3 s. The shaded rectangle in Fig. 4c encompasses the temperature range compatible with this breakup time-scale, from which we can infer that the maximum temperature to which the fiber is exposed is 1885 ± 15 °C. With the collection of statistics on the breakup behavior in the future, we aim to develop a procedure for the temperature measurement of the process, which is otherwise unattainable by conventional means [26, 58, 59].
Moreover, segregation-driven control of doping in post-breakup semiconducting particles is attainable, allowing to control an individual device’s internal architecture. It is possible to control the structure of a single sphere, as was demonstrated by Gumennik et al. [47] shown in Fig. 5. When the droplet is exiting the flame, it experiences a thermal gradient:it is colder on the end distant from the flame, and consequently, it is expected to solidify laterally, starting from the colder side. If the sphere is doped with a material that is more soluble in a liquid than in a solid, this dopant will be repelled into the liquid as the solidi cation front propagates, collecting predominantly on the hot side. This effect is shown schematically in Fig. 1c and can be used to synthesize structured particles, composed for example of Ge-rich Si, (as shown in Fig. 5):Starting with 50:50 Si-Ge mixture in the fiber core, after the breakup the sphere will solidify, such that the Ge is extruded into the melt as the solidi cation evolves, leading to anisotropic distribution and resulting in axially oriented Janus particle heterojunctions [47]. This method can be extremely useful in assembling complex fiber-embedded devices such as heterojunctions, as shown in Fig. 1d and e.
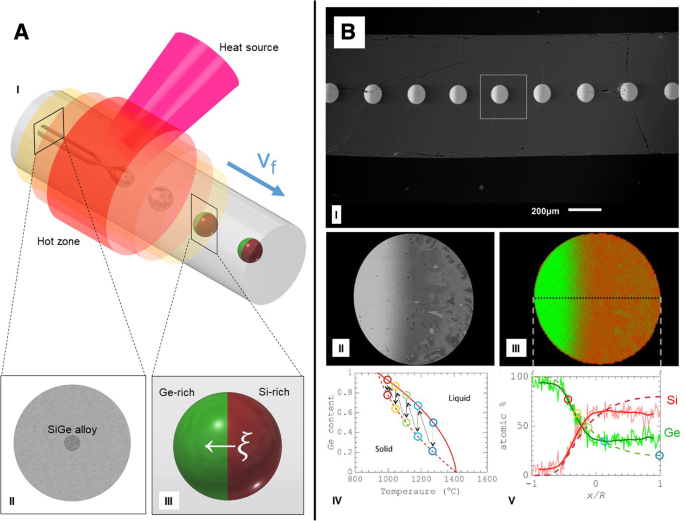
Segregation control of doping:a (I) Schematic illustration of the segregation-driven control of doping in post-breakup semiconducting particles. Details:cross section of a Ge-rich Silicon continuous core in silica fiber a (II) and post-breakup schematic drawing of doping-segregated sphere, or Janus particle, with the Ge-rich side indicated in green a (III). b (I) Scanning Electron Microscope image in backscattered mode of the fiber, polished along its axis, showing an array of Janus particles. b (II) Detail of single Janus particle cross section. b (III) Energy-dispersive X-ray spectroscopy (EDS) map of Janus particle, indicating non-homogeneous distribution of Ge along the cross section, from overlaid maps of Si (in red) and Ge (in green). b (IV) Si-Ge equilibrium phase diagram, liquidus (solid line), and solidus (dashed line). b (V) SiGe atomic content distribution along the dashed line in b (III). (From Gumennik et al. [47])
Biomedical Application
Fiber technology is frequently utilized in various biomedical applications as chemical, biological, and physical sensors. Fiber-embedded sensors have been designed to monitor physical parameters such as stresses, temperature, pressure, and humidity or chemical parameters such as pH level, oxygen concentrations, and carbon dioxide concentrations [60]. Fiber bundles are beneficial to embed multiple sensors together in a single system and in increasing signal reception levels, resulting in higher signal-to-noise ratios. Lightness, flexibility, and unique optical properties are the main characteristics that lead the demand for fiber sensors in biomedical studies. To meet clinical usage requirements, preforms must be fabricated from biocompatible, non-toxic, and chemically inert materials to prevent immune reaction from the patient. Examples of smart fiber development include a neural fiber probe composed of a polymer and metal core composition that enables flexibility and bending stiffness of the neural probe as it provides in vivo optogenetic stimulation and delivers drugs as an input in order to record feedback electrical and physiological output signals [33]. Another example is a fiber integrating microfluidic principles with complex cross-sectional geometries and meter-long microchannels which analyzes cell separation by dielectrophoresis (DEP). Live and dead cells are separated by inertial and dielectrophoretic forces by sheathless, high-throughput microfluidic cell separator which contains conductive materials in the microchannels [14]. The following strategies show a new array of possibilities where smart fibers can be used in biological interfacing.
Consider an artificial gut that can serve as a bioactivity testing platform at the microscale and at the macroscale. With today’s progress in tissue engineering, a variety of functionalities can be integrated in bioink-coated fibers co-extruded using a bioprinter for tissue fabrication, as shown in Fig. 6(I). Traditionally, bioprinting research aims at creating tissue grafts for regenerative medical practice and does so by carefully designing the hydrogel (Fig. 6(II)) with the appropriate nutrition and signaling molecules for the type of cells required based on the application (Fig. 6(III)). Tissue engineering is very challenging to study as the whole biology of the system completely changes microseconds after the experiment has been launched. Monitoring and regularly tuning a tissue’s maturation remains very complex.
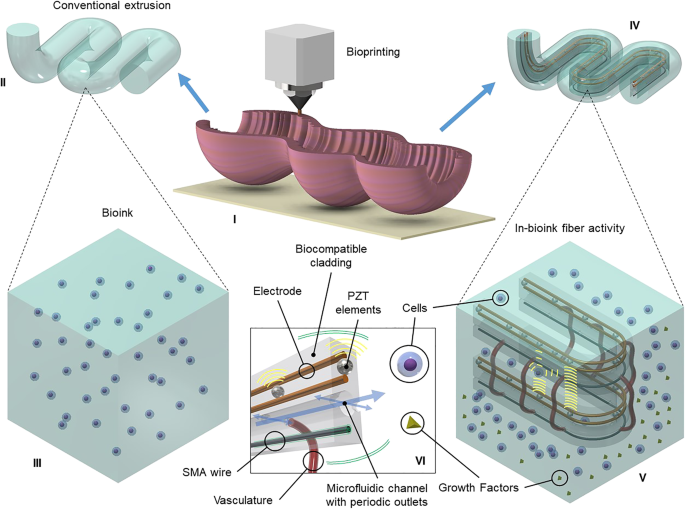
Biological interfacing. (I) Three-dimensional bioprinting of a tissue. (II) Standard microextrusion of bioink. (III) Conventional bioink with cells suspended in hydrogel. (IV) Novel coaxial microextrusion of biointerfacing fiber coated in bioink. (V) Close-up view of fiber where biointerfacing occurs:epithelial cells and vascular epithelial growth factors are excreted from different microchannels and result in cellular self-assembled vasculature between two orifices; piezoelectric elements measure surrounding cell density by ultrasound; and shape memory alloy wires provide peristaltic motion in the tissue. (VI) Visualization of biointerfacing fiber and its components
We propose here a solution by introducing smart fibers in the design (Fig. 6(IV)) to provide a better understanding of the climate and environmental growth. The embedded fiber holds multiple functionalities (Fig. 6(VI)) such as inducing vasculogenesis, ultrasonic imaging, peristaltic movement, and microfluidic flow. Control of the microenvironment takes place via the fiber hooked to syringe pumps and wired to an analytical software. The features of this application (Fig. 6(V)), including pilot experimental data, are detailed in the next subsections.
The Extracellular Matrix and Vasculature
Tissue engineering is widely explored with the increase of artificial tissue needs [61, 62], and the ability to bioprint realistic tissue has an important role to play in tomorrow’s drug and treatment development [63, 64]. One of the biggest challenges is the design of the extracellular matrix (ECM), composed of proteins, growth factors, and other biomolecules, that guide the cell’s contribution to the tissue [65]. Naturally, the ECM gives purpose and structure to the cells, and its extraction typically works by decellularizing tissue and recycling or reusing the ECM for a new cellular construct. The ECM comes in the form of solvents, hydrogels, biopolymers, bioceramics, aerogels, or foams to provide biodegradable or resorbable structure to the tissue [66]. Due to tissue engineering’s high complexity in defining the specifics of the biosystem—mechanical properties, scaffold dissolvability or absorption rates, initial cell types, nutrition, density and ratios, growth factors introduction, and its resulting bioactivity and tissue self-assembly—it is vital to assess the behavior of different types of naturally produced ECM or artificially developed biomaterials in the presence of interacting cells. Moreover, viable tissue requires an organized vascular system that supplies nutrition and oxygen to the tissue for the health and growth of cells. Vascularization provides the natural microfluidic feed of biochemicals to initiate proliferation, specialization, interactions, and motion. The vascular network is formed by vasculogenesis, arteriogenesis, and angiogenesis. Vasculogenesis develops its network through the differentiation and division of endothelial stem cell [67]. Angiogenesis forms new sprouts from existing vessels that are formed in the early embryonic vasculogenesis stage [68].
In-Fiber Microfluidic Feed
Microfluidic conduits with periodic microchannels for content delivery can be used to weave microfluids to specific locations in tissue constructs. The liquefaction front at the boundary of the hot zone defines the droplets’ pinch-off location as described previously. Multiple cores can therefore be broken up in a spatially coherent manner. For example, a silica fiber including a platinum and a silicon core can become a fiber tube with multiple outlets, by inducing the silicon core into an array of spheres and then thinning the fiber using hydrogen fluoride, etching the silicon spheres with potassium hydroxide and etching the platinum core with regal water. An example of the result is shown in Fig. 6(V). The flexibility of fibers allows the microfluidic feed to be integrated in multiple ways in tissue construct. In Fig. 6(IV), the microfluidic channels are used to provide the necessary cell type and growth factors to initiate vascularization and angiogenesis as the tissue reaches maturity.
Biomaterial and Biochemical Testing
In parallel to fiber development, a new testing platform (Fig. 7a (I)) was designed to analyze vascularization and cell-to-cell interactions in the presence of growth factors (Fig. 7a (II)). The platforms were printed in high resolution at an orientation of 30 from biocompatible resin by stereolithography (Formlabs’ Form 2 and Dental LT Clear resin). The print result, shown in Fig. 7a (III), was assembled with two glass capillary tubes with outer diameters of 1.8 mm and 1.0 mm where biological agents are fed. Initial trials will assess diffusion parameters of biochemicals and the growth of cellular colonies in various biocompatible materials. These platforms are designed to be single-use. In 2 h, 24 testing wells can be printed at a relatively low cost. The distance between each capillary outlet of two parallel fibers can be adjusted between 100 and 400 m to investigate the optimum vasculogenesis range that is accepted around 200 m [67]. The medium of interaction in the well’s chamber will first host commercial bioinks (Cellink, USA), one containing sodium alginate and nanofibrillar cellulose and the other containing gelatin methacryloyl, before developing our own in-house biomaterials. The glass capillary tubes shown in Fig. 7a (I) will eventually be replaced by the microfluidic fiber shown in Fig. 6a (V) which will be discussed in the next section.
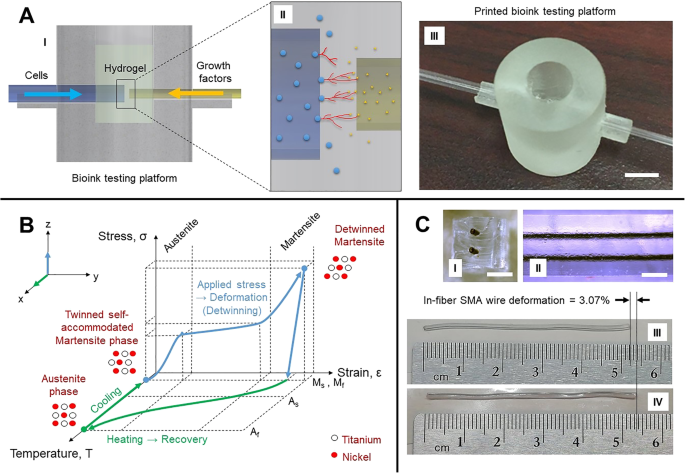
Pilot experiments for biointerfacing:a (I) Cross section of biotesting well showing fluidic feed. un (II) Example of the interaction of epithelial cells (blue circles on the left) with vascular endothelial growth factors (yellow dots on the right) resulting in vasculogenesis excreted by the cells (red lines in the center). un (III) Printed testing platform in biocompatible resin (scale bar = 5 mm). b Temperature-stress-strain graph of the shape memory effect. c (I) Cross section of in-fiber SMA wires (scale bar = 1 mm). c (II) Side view of in-fiber SMA wires (scale bar = 1 mm). c (III) 5.2-mm segment of an in-fiber SMA wire in contraction after being heated at 80 °C. c (IV) 5.36-mm segment of extended in-fiber SMA wire at room temperature
Peristaltic Motion
Shape memory alloy (SMA) wires are lightweight, non-corrosive, and cost-efficient actuating materials for refined applications in a variety of applications such as prosthetic biomimicry [69], self-expandable surgical implants [70], and aerospace engineering [71].
SMAs are metal compounds known for their shape memory effect and pseudoelasticity. Although such properties are typically found in nickel-titanium, these properties can be found in a range of different other metal alloys. Figure 7(b) shows the shape memory effect in terms of temperature, stress, and strain. As shown, at low temperatures, the SMA in its martensite solid state can be deformed by mechanical force, and when thermally induced, goes through a non-diffusive molecular reordering, converting to an austenite solid state. When cooled, the material will return to its initial martensite form, hence the shape memory effect. This thermal cycle is defined by four temperatures, the starting and finishing martensite and austenite temperatures (M s, M f , A s , and A f ), which specifies the start and end of transition periods between states. When the SMA is deformed in as martensite, the molecular de-ordering is defined as detwinning, and it allows the material to experience elongation, which is particularly useful for actuation applications. Essentially, the shape memory effect cycle can occur hundreds of times for an average elongation of 6% and contraction [72], hence its nickname “muscle wire” for its close similarity to muscular myofibrils.
This unique characteristic was first reported by Alden Greninger and Victor Mooradian in 1938 [73], can also be triggered by magnetic field energy [74], namely ferromagnetic shape memory alloys (FSMA), and can be found in polymers (SMP) as well [75]. Today, SMA’s mechanical fatigue and fracture, elasticity, and thermodynamics have been characterized well experimentally [76] and mathematically [77], and its behavior has been modeled [78].
Although the shape memory effect allows for nice contraction behavior of a material, for appropriate robotic applications, the motion needs to be reversable. Typically, an SMA is set in tandem with an opposite mechanism, such as springs, electric drives, elastic bands, or simply another SMA wire. Furthermore, the assembly changes whether it is a linear or rotatory actuation and if the opposing contractions of the actuation are equal. Although wires are thin and weak alone, they can be bundled together to reach the desired force and keep its shape memory effect response time. SMA wires can also be coiled around a capstan to provide greater elongation over shorter distances. Various strategies have been reviewed and chosen for specific applications [79]. The thermal induction is typically best controlled by powering the SMA wire and varying the input current of the order of hundreds of milliamperes. Cooling can be done naturally or by including heat sinks and ventilation.
Fiber drawing technology allows us to play on different material characteristics and to provide to an SMA wire an elastic coating that helps preserve the disorder state of the SMA fiber. As shown in Fig. 7c (I) and c (II), a fiber can be drawn with multiple embedded SMA wires. Styrene-ethylene-butylene-styrene (SEBS) was chosen as the surrounding structure to the SMA wires. SEBS is a copolymer elastomer that can withstand the drawing temperature of 80 °C. While preliminary results show that the actuation can work but with lower efficiency than bare SMA wires, the back-and-forth motion through heating (Fig. 7c (III)) and cooling (Fig. 7c (IV)) cycles is observed for a deformation of approximately 3.07%. More research is required to optimize the setup, but this early stage of experimentation in-fiber SMA actuation shows promising outlooks. The wires were physically pulled and heated using a hot plate to prove the concept. Heating by current would allow speeding up the shape memory effect and controlling better the heat’s diffusion through the fiber. The 5.35-mm wire was measured to have a diameter of 0.11 mm and a resistance of 18.2 was recorded across the fiber segment. To provide a frame of reference, according to SMA wire manufacturers (Dynalloy, Inc.), a 0.1-mm-thick wire made of nickel and titanium requires approximately 200 mA of current for a 1 s contraction. Controlling each wire individually would allow for directional movement, and adding more SMA wires to the design would allow multi-directional motion and greater contraction strength. Moreover, if ferromagnetic SMA wires were used, the control of the motion could become locally controllable via tuning of the interacting magnetic field. Additionally, the FAMES Lab’s drawing tower having the ability to rotate a preform as it is drawing into a fiber enables the possibility to manufacture spring-like structures of SMA wires in the fiber which allows for greater deformation, similar to commercially available SMA springs. Clearly, varieties of strategies are enabled with in-fiber SMA wires.
Biosensing
Biosensors are developed in a wide variety of ways. They can be designed label-based or label-free to detect specific expressions from biological elements such as cells, bacteria, hormones, proteins, DNA, and more [80, 81], from sampling blood, urine, saliva, sweat, or tears. Psychophysiological conditions can be observed from real-time biofeedback such as blood pressure, electrodermal activity, skin conductance, respiration and heart rates, and more [82, 83]. Bioimaging has been done by optical imaging, ultrasound, magnetic resonance frequency, computed tomography, near-infrared spectroscopy, quantum dot probing, and by many more techniques [84].
In optical fiber research, previous biosensing fibers have been fabricated relying on silicon photonic crystal detection of biological radiation [85]. Photonic crystal technology has been used before to monitor in label-free real-time cellular morphology and survival [86]. Such progress in biophotonics has led to hollow-core microstructured fibers visible under magnetic resonance imaging (MRI) [87]. The hollow core allows the propagation of the optical radiations along the fiber over very long distances. The geometry of the hollow fibers varies to tune the photonic bandgaps and dispersion of different detected wavelengths. The inner walls of these hollow tubes are coated with oppositely charged polyelectrolytes and magnetite nanoparticles which are used as contrast agents for MRI. Such design therefore enables new biomedical precision diagnosis opportunities, for example, in the observations of neural activity in vivo [87, 88].
Ultrasonography technology enables us to observe density of cells in liquid or gel in a non-intrusive manner [89, 90]. Ultrasonic probes typically function according to the piezoelectric effect (generation of electricity from applied stress), which was first discovered by Jacques and Pierre Curie in 1880 [91]. The inverse piezoelectric effect (deformation of a piezoelectric crystal from an applied electric field) was induced mathematically by Gabriel Lippmann in 1881 [92] and later in 1916, Chilowsky Constantin and Paul Langevin developed ultrasonic submarine detection for World War I military applications [93]. Thereon, sonar applications have been diverse, such as underwater imaging and fish-finding [94, 95] and energy harvesting [96, 97].
The piezoelectric elements convert electrical energy to and from mechanical energy and transmit sound waves between each other. All frequency and bandwidth parameters require precise regulation, and good energy transmission requires good acoustic and damping matching impedances. Two fibers with integrated piezoelectric elements, designed as pulsing emitter and receiver, can create an ultrasonic waveguide between each other to measure density over the wave’s trajectory. This fiber enables us to sense the microstructures of the environment as the tissue reaches maturation. The piezoelectric elements are created by capillary breakup from a PZT core for example. PZT elements have an acoustic impedance of 33.7 × 10 6 kg/m 2 s with a resonance frequency below 25 MHz. The produced spheres are lined with conductive electrodes to a transducer. This setup provides the feedback in a control system to better adjust microfluidic and motion feed. The in-fiber ultrasonic imaging of the microenvironment clearly helps understand how the tissue environment behaves over time.
Conclusions
We have formulated the concept of VLSI for fibers (VLSI-Fi)—a combination of liquid-phase processing techniques in microelectronic materials forming a toolbox for fabrication of high-performance devices and systems in fibers and textiles. Our experimental work focuses on a set of demonstrations substantiating our control over narrower aspects of VLSI-Fi, such as preform 3D printing, in-fiber circuit assembly by material-selective spatially coherent capillary instability, and segregation-driven doping control at the level of an individual fiber-embedded device. We envision that VLSI-Fi will enable realization of product in multiple technological areas, one of which is fabrication of active biomimetic scaffolds for engineered tissues with realistic microstructures.
Disponibilité des données et des matériaux
Non applicable.
Abréviations
- BJT:
-
Bipolar junction transistor
- CAD:
-
Computer-aided design
- CMOS :
-
Métal-oxyde-semi-conducteur complémentaire
- DEP:
-
Dielectrophoresis
- ECM :
-
Matrice extracellulaire
- EDS :
-
Spectroscopie à rayons X à dispersion d'énergie
- FAMES Lab:
-
Fibers and Additive Manufacturing Enabled Systems Laboratory
- FOS:
-
Fiber optic sensors
- FSMA:
-
Ferromagnetic shape memory alloys
- HPCVD:
-
High-pressure chemical vapor deposition
- IoT:
-
Internet of Things
- MOF:
-
Microstructured optical fibers
- MOSFET:
-
Metal-oxide-semiconductor field-effect transistor
- IRM :
-
Imagerie par résonance magnétique
- PCF:
-
Photonic crystal fiber
- PZT:
-
Lead zirconate titanate
- SEBS:
-
Styrene-ethylene-butylene-styrene
- SLA:
-
Stereolithography
- SMA:
-
Shape memory alloy
- SMP:
-
Shape memory polymers
- TPC:
-
Trans-Pacific undersea cable
- UV :
-
Ultraviolet
- VLSI:
-
Very large-scale integration
- VLSI-Fi:
-
Very large-scale integration for fibers
Nanomatériaux
- Optimisation de la transformation numérique dans la fabrication CPG
- GE ouvre une usine intelligente en Alabama
- L'arrivée de l'âge pour le fil numérique dans la fabrication intelligente
- Défis de fabrication basés sur les données
- Qu'est-ce que la transformation numérique dans la fabrication ?
- Tirer parti de la technologie numérique dans la fabrication
- L'usine numérique :la fabrication intelligente propulse l'industrie 4.0
- GE Digital :transformer la fabrication avec Smart MES
- Fabrication intelligente Autodesk