Passivation des métaux :empêcher le fer et l'acier de devenir actifs
Couches chimiques qui protègent le métal de la corrosion
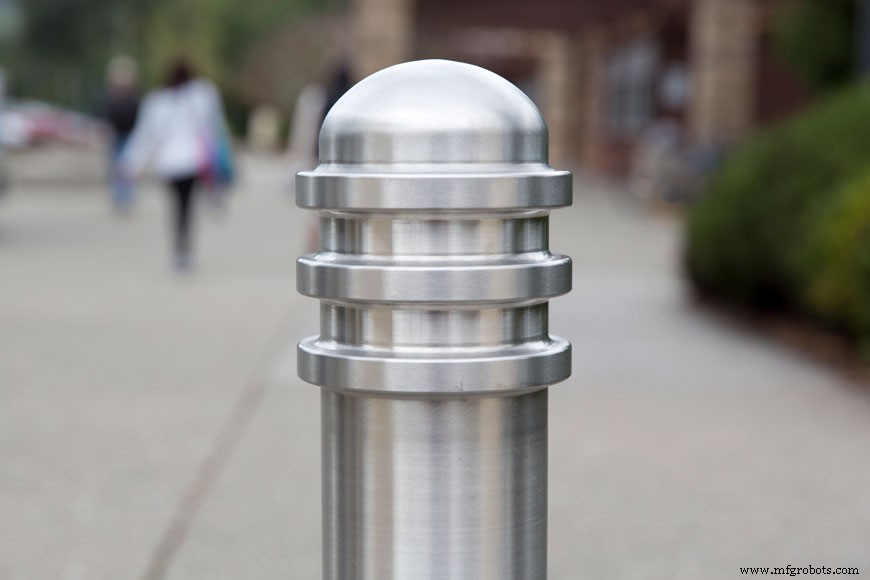
De nombreux métaux sont vulnérables à la corrosion lorsqu'ils sont exposés à l'air et à l'eau. La corrosion peut provoquer des contraintes sur le métal et une défaillance des pièces, c'est pourquoi les métallurgistes cherchent des moyens de la vaincre. L'une de ces méthodes est la passivation des métaux, une méthode moins connue de protection contre la corrosion d'une surface qui utilise une fine couche chimique comme joint. La passivation peut se produire naturellement ou être favorisée par les procédés de fabrication.
Qu'est-ce que la corrosion ?
La corrosion des métaux se produit lorsque les molécules d'un alliage métallique actif réagissent dans leur environnement pour devenir électrochimiquement plus stables. Les oxydes, les hydroxydes et les sulfures sont les principaux composés de corrosion. Une simple exposition peut entraîner la réaction, comme la rouille du fer dans l'eau et l'air. Les processus électrochimiques peuvent également provoquer la réaction, comme la corrosion galvanique entre le nickel et le cadmium dans une batterie.
Il existe des métaux qui résistent à la corrosion. Les métaux nobles comme l'or, l'argent et le platine sont chimiquement stables dans de nombreuses conditions. Les métaux nobles ne sont pas insensibles à la corrosion, mais le processus se déroule lentement ou avec des molécules moins courantes. Par exemple, le ternissement noir épais de l'argent est généralement causé par le sulfure d'hydrogène plutôt que par l'oxygène et l'eau. Les métallurgistes vérifient le potentiel actif des métaux à l'aide de l'échelle galvanique ou de l'indice anodique. Ceux situés près du sommet sont moins sujets à la corrosion.
Les métaux « actifs », ou ceux qui se trouvent plus près du bas de l'échelle, sont chimiquement moins stables et donc plus enclins à réagir avec d'autres éléments de l'environnement. Pour éviter cela, des processus actifs ou passifs sont utilisés pour réduire la corrosion. Ces processus fonctionnent généralement en "scellant" le métal avec une couche supérieure, empêchant l'air et l'eau d'atteindre le métal en dessous. La couche peut être artificielle :la peinture, le revêtement en poudre et l'huile sont tous des produits d'étanchéité courants. S'ils sont rayés, cependant, la corrosion se faufile.
Une autre option utilisée pour sceller le métal est chimique, où des réactions chimiques sont utilisées à la place de matériaux fabriqués. Un processus chimique est la passivation.
Qu'est-ce que la passivation ?
La passivation, généralement associée à l'acier inoxydable, est une méthode de traitement pour protéger le métal de la corrosion à travers, ce qui rend le matériau "passif" au milieu environnant. La passivation, peut-être contre-intuitive, encourage la corrosion à se produire sur la surface, créant une fine couche d'un nouveau produit chimique non réactif. Cette couche supérieure reste étroitement liée au métal, créant un joint naturel qui empêche les éléments de corroder les couches suivantes du métal. Un métal est passivé lorsque chaque surface est recouverte d'une couche de corrosion étroitement liée. Cette couche peut se former naturellement (passivement) au fil du temps, mais les fabricants peuvent également l'induire activement.
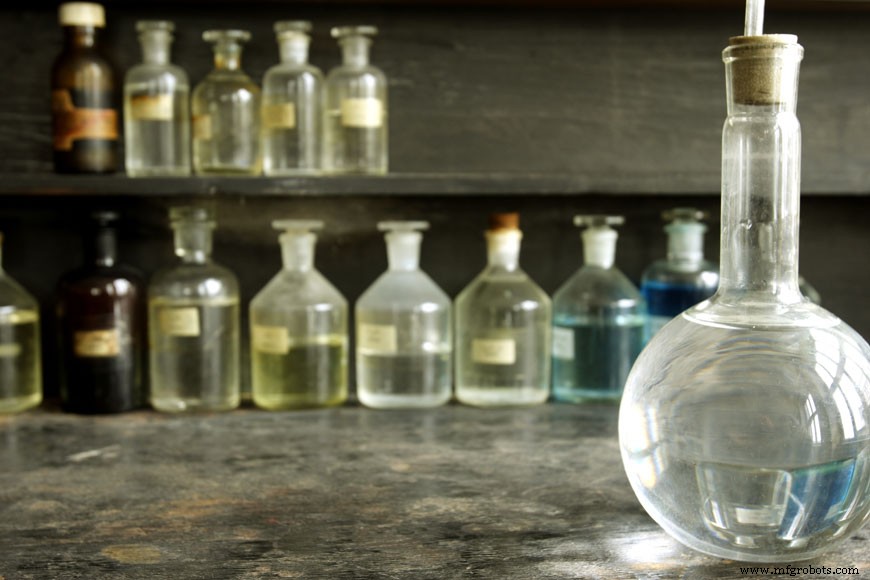
L'histoire de la passivation
La passivation a été découverte par des scientifiques effectuant des expériences électrochimiques, mais ils n'ont pas immédiatement reconnu l'utilité du processus pour une utilisation générale. En 1790, le chimiste James Keir a observé qu'un bain d'acide nitrique fort ne corrodait pas le fer. Il a noté que lorsque la même solution était diluée dans l'eau, le fer se corrodait immédiatement, créant une solution bouillonnante d'eau brun foncé. En 1836, le chimiste suisse Christian Friedrich Schönbein a précisé l'expérience plus loin. Il a démontré qu'un morceau de fer immergé dans de l'acide nitrique faible se dissout et produit de l'hydrogène, comme l'a noté Keir. Pourtant, si le fer était d'abord plongé dans un acide fort, il pourrait alors résister à l'acide dilué. Les éléments corrosifs de l'eau semblaient être tenus à distance, au moins pendant un certain temps.
Michael Faraday, l'électrochimiste britannique, a été le premier à expliquer pourquoi. Il a émis l'hypothèse à Schönbein qu'une peau d'oxyde créée par l'acide fort pourrait provoquer la condition passive. Alors que les chimistes et les métallurgistes exploraient l'idée d'une "peau" chimique, ils cherchaient des techniques pour fabriquer ou améliorer la passivation, et des alliages qui créeraient des joints passifs de manière organique.
Couches d'oxyde passif
Comme les métaux sont exposés à l'environnement environnant, s'ils ne sont pas bloqués par la peinture ou le revêtement en poudre, ils se corroderont naturellement, créant la peau ou la couche d'étanchéité. La plupart des films passifs sont constitués d'oxydes, des combinaisons de métal et d'oxygène, on les appelle donc des couches d'oxyde passives.
L'un des plus grands avantages des couches d'oxyde passives est que lorsqu'elles apparaissent naturellement, elles "guérissent" aussi naturellement si la surface du métal est rayée ou autrement endommagée, car la prochaine couche de molécules se liera alors aux éléments environnementaux. /P>
L'efficacité des couches d'oxydes passifs dépend du type d'éléments impliqués. Toutes les couches d'oxyde ne sont pas protectrices :si l'oxyde est suffisamment poreux pour que l'oxygène puisse passer à travers, aucun joint ne se formera et le métal en dessous continuera à se corroder. Par exemple, l'oxyde de magnésium forme une couche à forte porosité de surface qui n'arrête pas la corrosion. Les molécules d'oxygène circulent toujours et réagissent avec le magnésium en dessous.
De même, les éléments du milieu environnant comptent également. L'acier inoxydable, par exemple, peut être attaqué par des dépôts de sel ou de fer. Si la chimie globale de la surface ne se passive plus naturellement, la rouille s'installera.
Passivation forcée
Pour certains alliages, la passivation naturelle peut être longue; pour d'autres, il peut se développer de manière inégale, avec des variations du grain du métal ou en présence de dépôts superficiels. Les métallurgistes ont créé des méthodes de passivation active pour accélérer et standardiser le processus afin de créer des produits immédiatement utilisables.
Le "bleuissement" des armes à feu était l'un des premiers exemples de passivation forcée par des moyens de fabrication chimique. L'un des oxydes de fer est la magnétite, un oxyde noir (Fe3O4), et cet oxyde ne s'écaille pas comme le ferait la rouille (Fe3O3). Plusieurs procédés chimiques peuvent être utilisés pour créer ces oxydes noirs en utilisant de la chaleur et des solutions caustiques. Cependant, bien que le bleuissement protège contre la corrosion, une couche endommagée ne « guérit » pas dans des conditions normales. Le bleuissement est donc un scellant manufacturé qui a besoin d'entretien et de soins.
Aujourd'hui, les traitements courants de passivation active comportent plusieurs étapes :
- Nettoyer l'article pour éliminer l'huile de surface et les impuretés. Il ne doit y avoir aucune zone isolée du bain d'acide par un revêtement externe.
- Passivation dans des bains d'acide nitrique ou d'acide citrique, ou en utilisant un procédé électrochimique. Pour l'acier inoxydable, cette étape élimine tout dépôt libre de fer qui empêcherait l'acier inoxydable de former un film passif solide. Au niveau microscopique, un dépôt de fer libre empêcherait la couche passive d'oxyde de chrome de former un joint continu. La couche de passivation après le bain d'acide nitrique est en Cr2O3.
- Rincer l'article de toute trace de la solution acide, en emportant avec lui le fer libre restant.
- L'article est placé dans des conditions qui favorisent l'oxydation. Les conditions incluent une combinaison de température et d'humidité accrues, et l'utilisation d'agents favorisant la rouille tels que le brouillard salin, le sulfate de cuivre ou le ferricyanure de potassium.
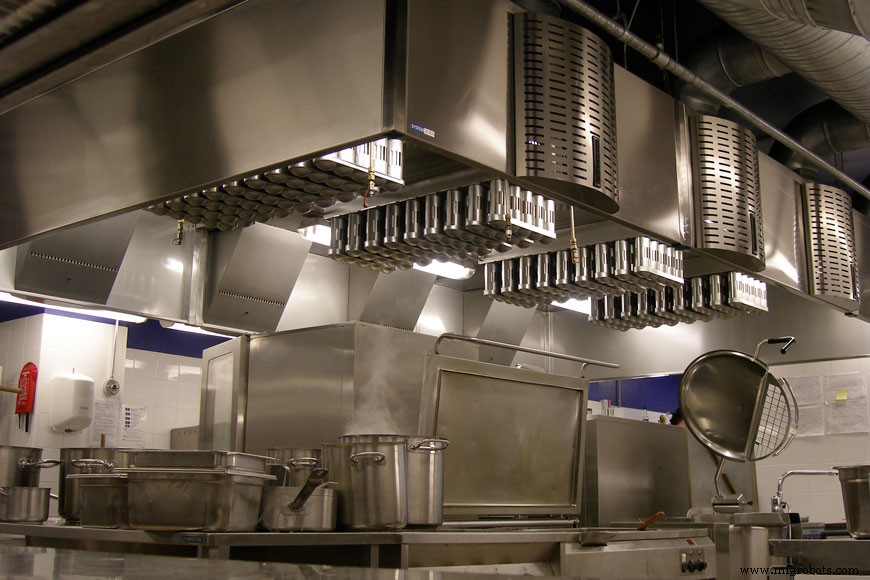
Acier inoxydable et autres alliages auto-passivants
L'acier inoxydable est un métal résistant qui résiste à la corrosion grâce à une passivation naturelle. Depuis son invention en 1913, de nombreuses industries en sont venues à s'appuyer sur le métal. Cependant, il n'est pas garanti qu'il soit exempt de rouille.
L'acier inoxydable, comme les autres aciers, est principalement composé de fer et de carbone. L'ajout révolutionnaire à l'alliage est le chrome. Le chrome, exposé à l'air, forme rapidement une couche d'oxyde passif qui scelle le fer et le protège. Différentes qualités d'acier inoxydable contiennent différents métaux de support :le molybdène, le silicium et d'autres constituants offrent tous un support passif pour différentes applications. Certaines nuances sont supérieures pour gérer la chaleur, d'autres pour résister à la corrosion due au sel :le mélange chimique de l'alliage modifie son comportement dans différentes conditions. Les dépôts de fer, la chaleur, le contact avec d'autres métaux, le sel et les acides peuvent tous défier la couche d'oxyde.
L'aluminium est un autre métal qui se passive naturellement. L'oxyde d'aluminium se forme sur la plupart (mais pas tous) des alliages d'aluminium lorsqu'ils sont exposés à l'air, ce qui rend la surface auto-protectrice. L'oxyde d'aluminium peut être attaqué par le sel, le stress électrochimique ou l'humidité piégée. Avec l'acier inoxydable et l'aluminium, les processus de fabrication sont utilisés pour favoriser la création de couches passives d'une épaisseur ou d'une uniformité supérieures à celles qui pourraient se produire naturellement.
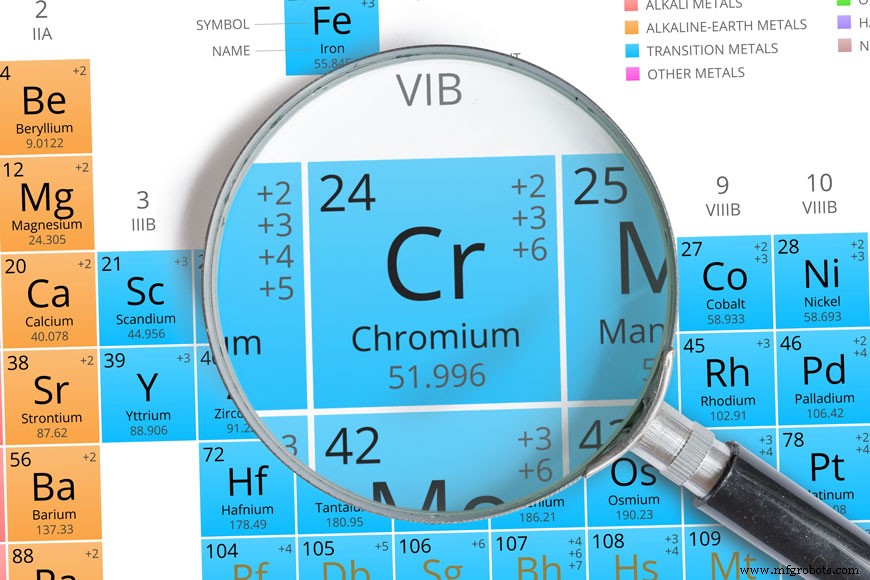
Normes de passivation pour l'acier inoxydable et l'aluminium
L'acier inoxydable et l'aluminium sont tous deux des matériaux auto-passivants, mais ils ne sont pas insensibles à la corrosion. Les irrégularités du grain, créées par la fabrication ou les traitements thermiques, peuvent créer une faiblesse. Les dépôts superficiels d'huile ou d'autres produits chimiques peuvent également interrompre le film passif. Pour garantir la qualité des nuances d'acier inoxydable et d'aluminium, il existe désormais des processus et des tests de passivation standard.
Les spécifications ASTM A380 et A967 définissent des normes et des procédures de test de qualité pour la passivation de l'acier inoxydable à l'aide d'acide nitrique, d'acide citrique ou par des moyens électriques.
Le chrome est parfois utilisé pour passiver d'autres matériaux, mais souvent par application plutôt que d'être intégré à l'alliage. Un processus appelé conversion du chrome est utilisé pour l'aluminium et d'autres métaux, tels que le zinc et le nickel. Dans cette technique, un gel de chrome est peint sur la surface métallique. Le produit chimique se lie à la surface du métal, créant une couche passive qui présente une résistance élevée à la corrosion. Une passivation d'une rayure à une conversion de chrome subira un processus d'auto-guérison. Le chrome autour de la rayure se déplace pour lier et recréer la couche de passivation. Cependant, la rayure doit être suffisamment petite pour que cela soit possible avec le chrome environnant.

Décapage vs passivation de l'acier inoxydable
La passivation de l'acier est un processus qui utilise un bain acide pour laisser une couche d'oxyde. Le décapage est un autre traitement par bain d'acide, mais il a le but opposé :le décapage utilise un acide pour nettoyer les oxydes de la surface du métal.
Lorsque les oxydes recouvrent la surface d'un métal, l'article devient plus difficile à usiner. Les oxydes provoquent une plus grande contrainte sur les outils et peuvent déjouer les tentatives de sceller la surface avec de la peinture ou un revêtement en poudre. Le décapage élimine tous les oxydes, y compris ceux qui fonctionnent comme une couche passive. L'acier et le fer sont généralement décapés.
Lors de la production d'une pièce métallique, la pièce peut être décapée, usinée, puis passivée.
Électropolissage de l'acier inoxydable et d'autres métaux
Le polissage électrolytique est une étape de finition du métal qui ébavure et lisse, laissant une surface propre et brillante. Il peut être utilisé sur de nombreux métaux, y compris ceux qui ne sont pas encouragés à passiver, comme le cuivre. Sur un métal passivant, une surface lisse peut créer des couches passives ininterrompues et résistantes.
Un objet à électropolir reçoit une charge positive et est plongé dans un bain d'électrolyte. Les cathodes environnantes tirent les molécules de surface de l'objet, rasant sa couche supérieure. Les saillies dentelées sont les premières à être retirées. Aux niveaux macroscopique et microscopique, le métal électropoli présente peu d'irrégularités ou de crevasses.
Lors du polissage électrolytique de l'acier inoxydable, le fer est préférentiellement éliminé, laissant plus de chrome à la surface. Une surface lisse et ininterrompue sans fer favorise naturellement une couche de passivation solide sur l'acier inoxydable.
Lorsque la passivation échoue
La passivation n'est pas toujours la solution idéale; les problèmes potentiels couvrent un large éventail de variables. Certains types de métaux sont incapables de passiver, car le métal s'écaille en se corrodant. Si un métal est structurellement capable de passiver, les choses peuvent toujours mal tourner pendant le processus de bain acide. D'un autre côté, même un métal parfaitement passivé peut ne pas être utilisable dans certaines industries - la chimie peut causer des problèmes dans les applications électrochimiques.
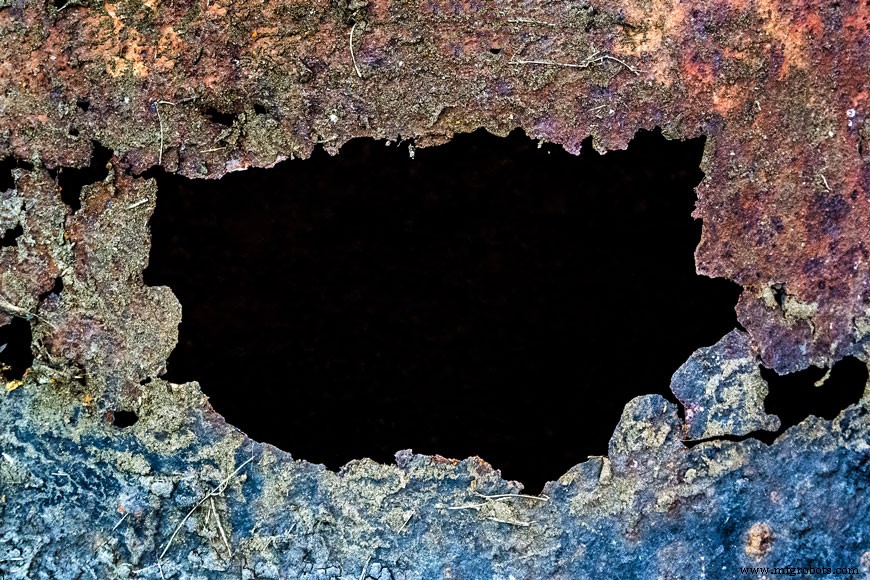
Pourquoi certains métaux s'écaillent-ils lorsqu'ils se corrodent ?
Les oxydes métalliques peuvent avoir une structure cristalline plus grande que leurs molécules métalliques constitutives. Par exemple, l'oxyde de fer (III), le sous-produit de la corrosion rouge mieux connu sous le nom de rouille, a une structure plus grande, et donc une plus grande surface, que le fer élémentaire qui le produit. Cette plus grande surface force l'oxyde à se soulever de la surface du métal en dessous, provoquant des bulles et des écailles. La séparation de l'oxyde du métal expose la couche suivante à l'air et à l'humidité, et le cycle continue, ronge la surface.
Dans les situations où les oxydes, les hydroxydes ou les sulfures ont une surface plus grande que le métal dont ils proviennent, aucune couche de passivation ne se forme.
Attaques éclair de passivation
Parfois, un fabricant constatera que dans un lot d'articles de passivation, un ou plusieurs deviennent noirs et commencent à graver même dans un bain d'acide nitrique fort. Cet état actif est appelé « attaque flash ». Cela peut être assez déroutant, car parfois il peut attaquer certains articles mais en laisser d'autres seuls dans le même panier de trempage.
Les raisons de l'attaque éclair sont liées à la consistance des produits chimiques impliqués dans la fabrication du film passif. Si le bain d'acide nitrique a été utilisé pendant une longue période, il peut avoir accumulé des sels ou de l'eau. Les pièces elles-mêmes sont souvent un problème :il peut y avoir de l'huile de coupe sur les pièces de la machine, ou les traitements thermiques ou le contrôle thermique pendant l'usinage peuvent avoir modifié de manière inégale la structure moléculaire de la pièce. Il peut également y avoir des inclusions ou des incohérences dans l'alliage lui-même.
Éviter la passivation
Il y a des moments où la passivation peut poser des problèmes pour le bon fonctionnement d'une pièce métallique.
Les traitements électrochimiques nécessitent souvent des cathodes et des anodes métalliques pour faire passer un courant électrique dans une solution. Ces systèmes peuvent favoriser la formation d'oxydes qui s'accrochent à l'extérieur des cathodes. Au fur et à mesure que les cathodes sont encrassées par les oxydes, le système devient moins efficace.
Dans ces systèmes, la passivation est un problème. Changer de polarité résout parfois le problème. Des impulsions électriques opposées permettent aux oxydes de tomber des cathodes. Les boues d'oxyde ou les scories peuvent tomber et ne pas interférer avec l'activité électrochimique du processus.
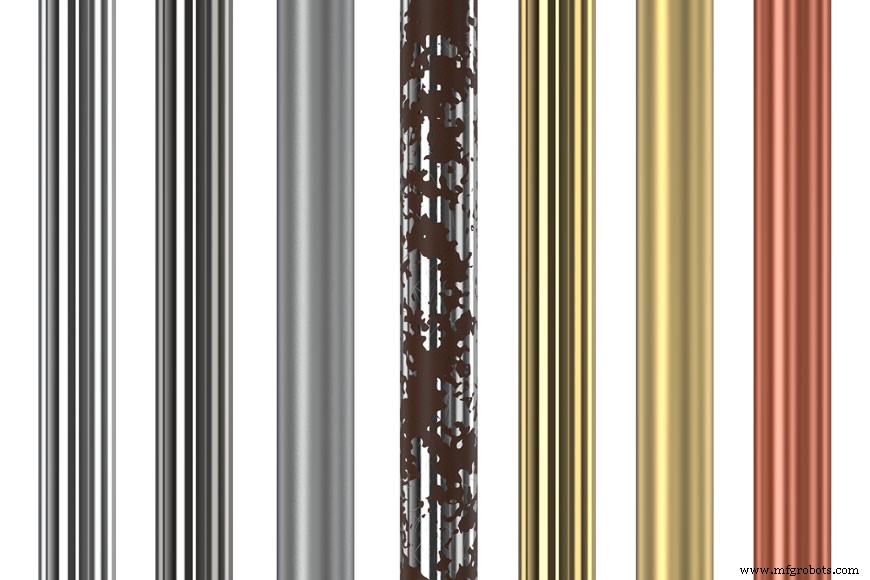
Couches de passivation pour sceller et protéger
De nombreux métaux réagissent avec l'environnement en produisant des oxydes, des hydroxydes ou des sulfures. Ces produits de corrosion se présentent de manière similaire mais ont des propriétés différentes.
Le ternissement de l'argent, apparaissant lentement lorsque l'argent se combine avec les sulfures dans l'air, agit comme une couche passive. Il émousse la surface du métal et est souvent poli. En comparaison, la patine verte du cuivre, ou vert-de-gris, est souvent un prix esthétique pour la profondeur et la gamme de couleur verte qu'elle produit. Le vert-de-gris est un mélange de carbonates, de sulfures, de sulfates et de chlorures, créé par la réaction du cuivre aux pluies acides ou aux dioxydes de carbone. La rouille, l'oxyde de fer le plus courant, produit un pigment orange ou rouge brique. Contrairement au vert-de-gris, il doit être soigneusement contrôlé afin que la surface bouillonnante ne permette pas à l'acier en dessous de rouiller.
Les couches de passivation scellent et protègent un objet métallique d'une oxydation supplémentaire. Avec les couches passives à base de chrome, comme sur l'acier inoxydable, ce film est souvent suffisamment fin pour ne pas modifier l'aspect de surface ou la fonction du métal. La passivation fine ne modifie souvent le métal que dans des contextes très spécifiques, tels que le soudage, l'usinage ou les systèmes électrochimiques. Le plus grand avantage fourni par les métaux auto-passivants est la capacité de « s'auto-guérir ». Pour une protection maximale contre la corrosion, associez un métal auto-passivant à un mastic appliqué tel qu'une huile, un revêtement en poudre ou une peinture.
Métal
- 4 types de métaux résistants à la corrosion ou ne rouillent pas
- D'où viennent les métaux ?
- 6 conseils pour prévenir la rouille
- Comment rouiller le métal
- Qu'est-ce qu'un métal ferreux ? – Un guide complet
- Qu'est-ce que la Corrosion ? - Définition et prévention
- Comment prévenir la corrosion dans votre équipement métallique
- Comment prévenir la corrosion des métaux
- Qu'est-ce que l'acier argenté ?