Formation à chaud
Cette barre latérale en ligne pour l'article de mars 2021, « Advancing the OOA infused wing box » vise à rassembler ce que CW a écrit sur la formation de draps chauds au fil des ans en un seul endroit et, espérons-le, fournira une ressource utile. Vous trouverez ci-dessous des extraits de plusieurs articles (de 2010 à 2020) avec des photos pour montrer comment le formage par drapage à chaud aide à automatiser la production de composites.
2010, GKN Aerospace, longerons A400M
Extrait de :« Les longerons d'aile composites transportent les énormes turbopropulseurs »
Phil Grainger, directeur technique et technologue en chef de GKN Aerospace, explique que la construction manuelle d'une si grande pièce, comme cela a été fait sur les premiers longerons de l'A400M, est lente, avec généralement un taux de pose de 0,75 kg/h (1,5 lb/h). Cependant, lors de la production en série, la pièce sera posée à plat, à l'aide d'une couche de ruban automatisée (ATL) et ensuite formé à chaud dans la forme de la section C. À ce stade, des taux de drapage de 25 kg/h (50 lb/h) seront réalisables. Grainger souligne qu'il s'agit de taux moyens réalisables sur un quart de travail, sur des pièces réelles.
Pour automatiser le processus, GKN Aerospace a investi dans un grand ATL avec un lit de 20 m/63 pieds, fabriqué par MTorres (Navarre, Espagne). L'ATL est capable de poser les préformes complexes dans leurs formes développées à partir de préimprégnés unidirectionnels, en utilisant un ruban uni en fibre de carbone/époxyde renforcé 977-2 fourni par Cytec Engineered Materials Ltd. (maintenant Solvay, Wrexham, Royaume-Uni). Pour former la section en C, la préforme sera déplacée de la couche de ruban vers un formateur à chaud fourni par le fabricant d'équipement Aeroform Ltd. (Poole, Dorset, Royaume-Uni). Pour faciliter la mise sous vide, le drapage sera pris en sandwich entre deux diaphragmes fabriqués à partir d'un film de polyimide Kapton, fourni par DuPont Electronic Technologies (Circleville, Ohio). L'espace entre les films sera évacué puis un chauffage infrarouge sera appliqué par le dessus de la pièce pour élever la température à 60°C/140°F sur une période d'une heure. Cela garantit que même le matériau au centre de la section la plus épaisse à l'extrémité de la racine est réchauffé uniformément à la même température. Une pression sera ensuite appliquée doucement pour former le stratifié, contraint par les deux diaphragmes sur un outil léger qui représente avec précision la surface intérieure du longeron. Ce processus de formation de C est réalisé très lentement sur une période de 20 minutes. (Après formage, les films Kapton sont jetés.)
2014, FACC, volets A321
De :« FACC AG :centrale d'aérocomposites »
Dans l'usine 3, une grande variété de volets, de carénages et de surfaces de contrôle de vol sont fabriqués. Ici aussi, les gains d'efficacité de la pose automatisée de ruban (ATL) et du formage à chaud sont exploités. Ce dernier applique de la chaleur et de la pression aux préformes ATL plates à l'aide d'un noyau et d'un tampon de formage flexible pour produire des formes tridimensionnelles (voir Fig. 7). Un exemple est en cours A321 production de volets, qui utilise une cellule de travail automatisée de pointe conçue sur mesure par Fill (Gurten, Autriche).
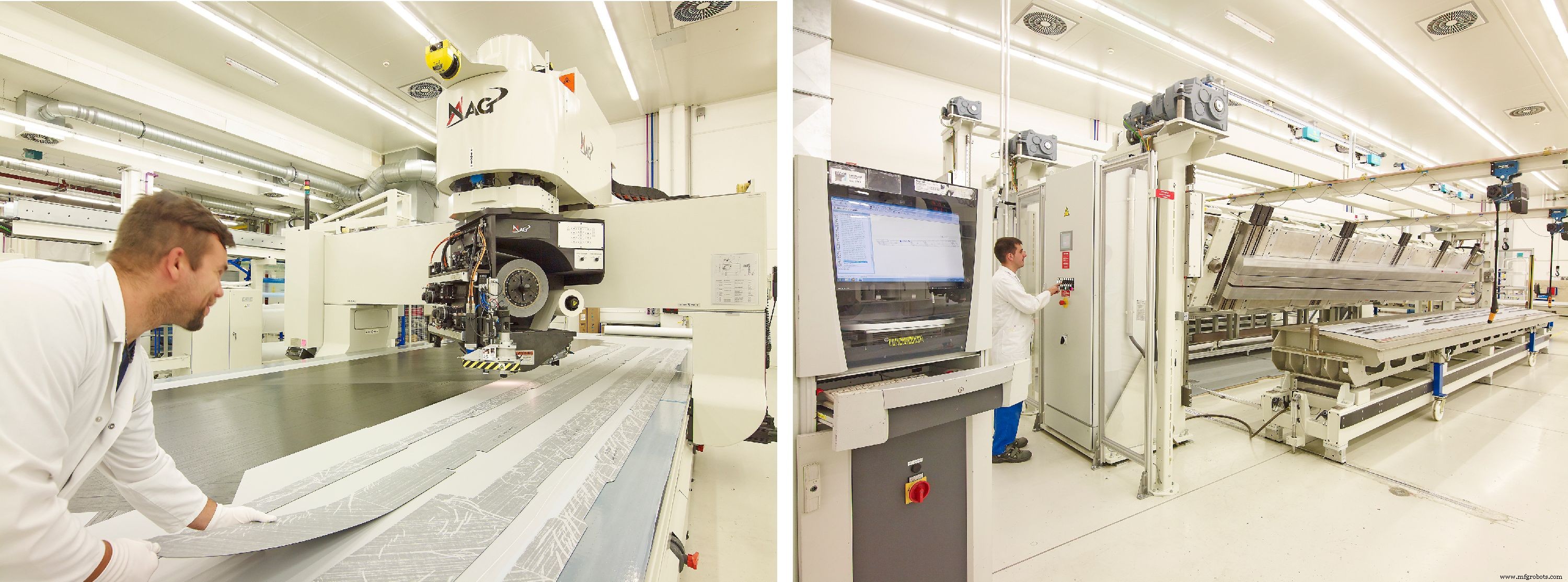
2018, Remplissage, préformage automatisé
Extrait de :« Préformage automatisé, partie 7 :Remplir la Gesellschaft »
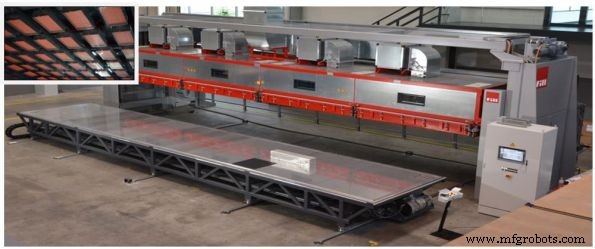
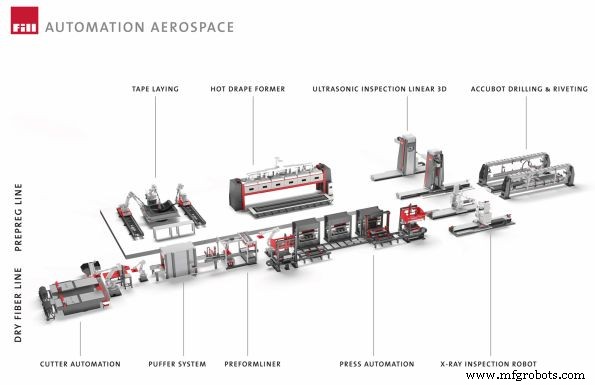
Dans les récents articles de tournée que Sara Black et moi avons écrits sur les composites haute performance en Israël, nous avons noté que la plupart des entreprises utilisaient le formage par drapage à chaud . En fait, à Elbit Cyclone, notre guide touristique Jonathan Hulaty a déclaré :« Je ne sais pas comment vous faites ce type de production de pièces préimprégnées à haut débit sans formage à chaud », se référant aux poutres et aux chandeliers pour les assemblages Boeing 787. Formes de drapage à chaud (HDF) sont également considérés comme indispensables par FBM et Israel Aerospace Industries.
Fill fournit des systèmes HDF depuis des années, dont plusieurs unités en production chez FACC. Ce sont essentiellement des systèmes de formage sous vide, équipés d'éléments chauffants infrarouges ou d'autres types et d'une membrane en caoutchouc de silicone réutilisable pour chauffer et comprimer - réduire en vrac - les couches de préimprégné sur leurs outils avant le durcissement. HDF devient un élément clé de la chaîne de production complète d'aérocomposites illustrée ci-dessous.
2018, FBM, 787 pièces
Extrait de :"La fusion d'entreprises entrepreneuriales centrées sur les métaux revendique la priorité aux composites"
CW est d'abord conduit à une salle blanche, où les ouvriers déposent diverses pièces. Aujourd'hui, dans un certain nombre de stations, chacune équipée d'un écran d'ordinateur assisté par ordinateur, l'accent est mis sur les pièces du Boeing 787. Des écrans tactiles faciles à comprendre montrent clairement les angles de layup pour chaque pli, et comment ils sont à positionner sur chaque outil. Une machine « guillotine » de Century Design (San Diego, CA, États-Unis), avec une table rotative de 2 m de diamètre et une lame de couteau au centre, permet une coupe rapide des plis angulaires du préimprégné carbone/époxy. Les outils pour les encadrements de porte 787 sont des mandrins en acier façonnés, généralement plus longs que larges, de quelques centimètres à environ 2 m de long, utilisés pour produire des centaines de cadres, supports et clips. Une table de découpe à plat automatisée d'Assyst-Bullmer Inc. (Wakefield, Royaume-Uni) est utilisée par les techniciens de drapage pour découper jusqu'à 50 plis empilés en une seule opération.
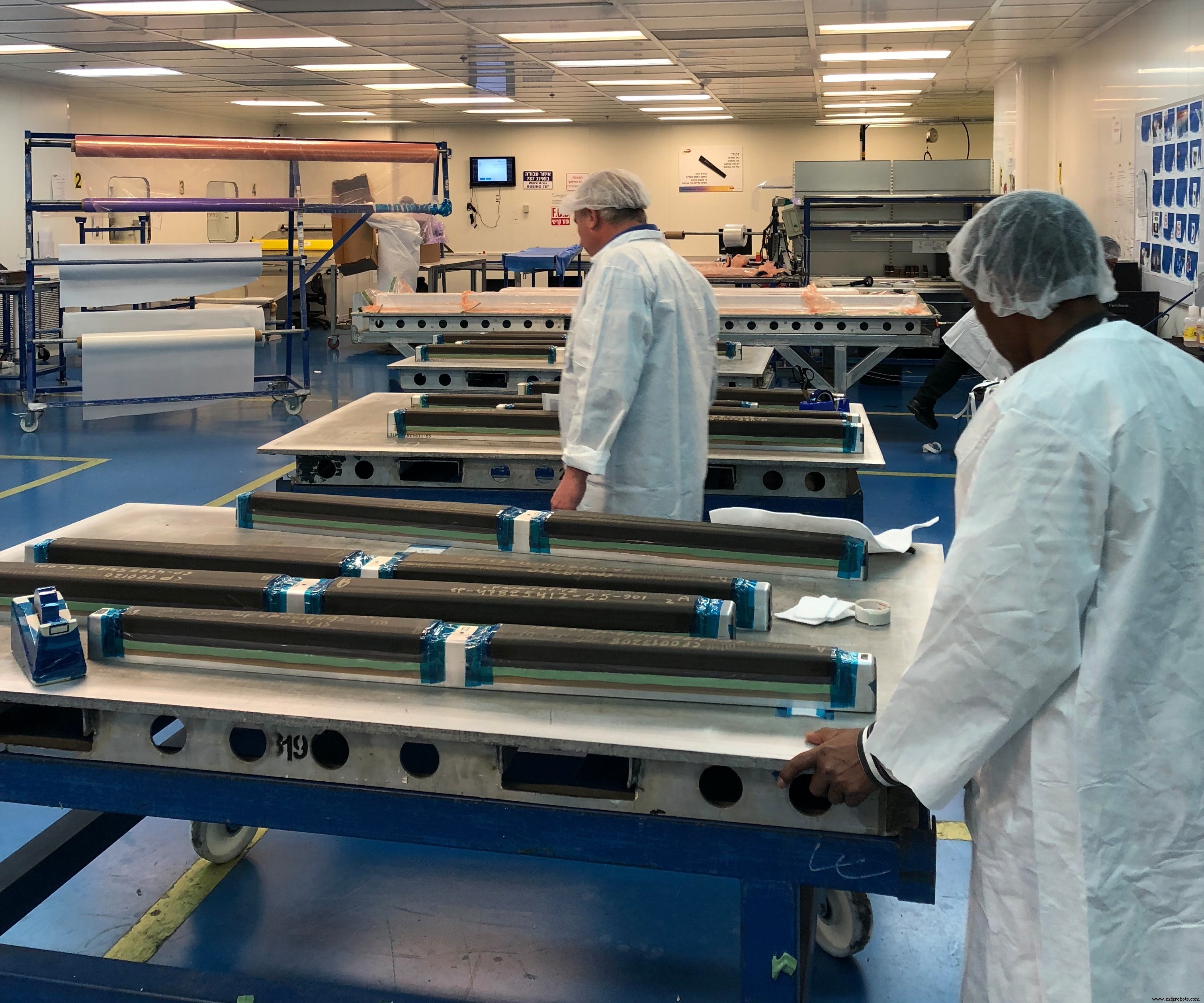
Découpe, mise en kit et superposition de petites pièces dans la salle blanche de FBM pour une grande variété de petites pièces autoclavées. Crédit photo :CW , Sara Black.
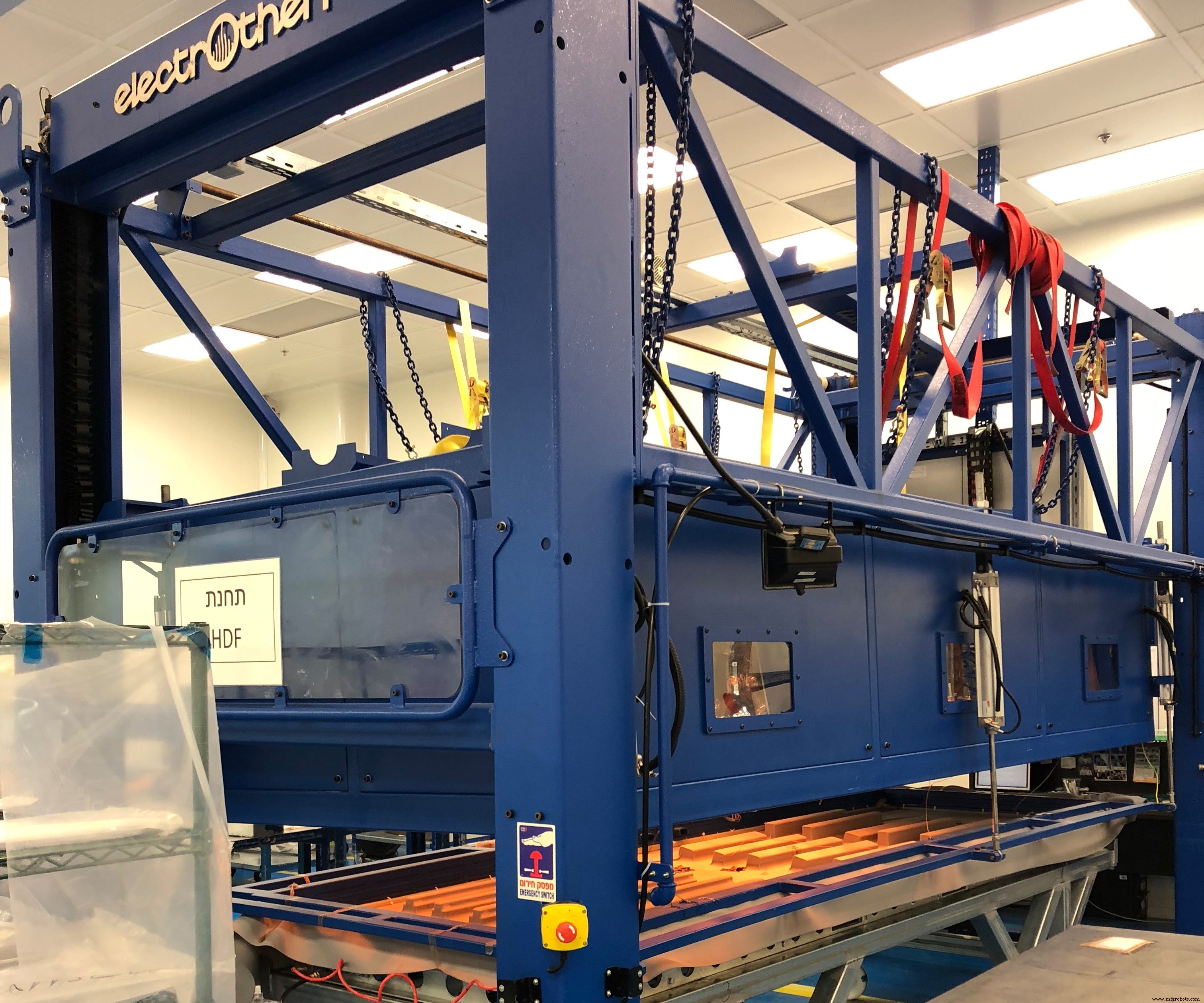
La machine de formage à chaud de FBM, fournie par la société israélienne Electrotherm Industry, supprime les étapes de réduction intermédiaires, formant jusqu'à 50 plis unidirectionnels en une seule fois, et est créditée d'avoir accéléré le processus de drapage de FBM avant le durcissement. Crédit photo :CW , Sara Black.
La salle blanche est dominée par une formeuse à drap chaud (HDF) . Fabriquée par ElectroTherm Industry (Migdal HaEmek, Israël), la machine statique (la société fabrique également des versions mobiles sur des chariots) est un système de formage sous vide sur mesure, équipé d'éléments chauffants infrarouges et d'une membrane en caoutchouc de silicone pour chauffer et comprimer le composite drapages sur les outils, avant le durcissement. Le HDF peut façonner jusqu'à 50 plis empilés, explique Poliker, sans aucune étape de réduction intermédiaire :« Nous cherchions à éliminer la complexité du processus, nous formons donc les couches en une seule fois. » Une fois le préimprégné chauffé et consolidé dans le HDF , une calotte est placée sur l'ensemble du drapage, avant l'ensachage. Fabriqué avec un composite de fibre de carbone, le calage présente une finition de surface rugueuse. Poliker ne révélera pas les détails du matériau exclusif, mais dit qu'il peut prendre les températures de durcissement de l'autoclave de 177 ° C :« Il simule un outil à matrice assortie. Il ajoute que les outils de mandrin sont reconditionnés en interne, au besoin. L'ensachage et les consommables sont fournis par Airtech International (Huntington Beach, CA, US).
2018, Elbit Cyclone, 787 pièces
Extrait de :"Au service du monde des composites en Israël et aux États-Unis"
À droite, les travailleurs de la salle blanche pour les pièces du Boeing 787 déposent du préimprégné pour une gamme de pièces, des petits clips et montants aux poutres complexes en J, I et C, ainsi que des portes de train d'atterrissage avant en plusieurs pièces. Le préimprégné est coupé à l'aide d'un coupe-tissu automatisé Assyst Bullmer (Wakefield, Royaume-Uni) et d'une machine à guillotine pour couper des piles épaisses à n'importe quel angle. Le congélateur préimprégné est adjacent à la salle blanche. Hulaty note que parfois des piles de préimprégnés sont coupées, emballées et remises au congélateur. Les systèmes de projection laser Aligned Vision (Chelmsford, MA, États-Unis) situés dans toute la salle blanche assistent la pose des mains.
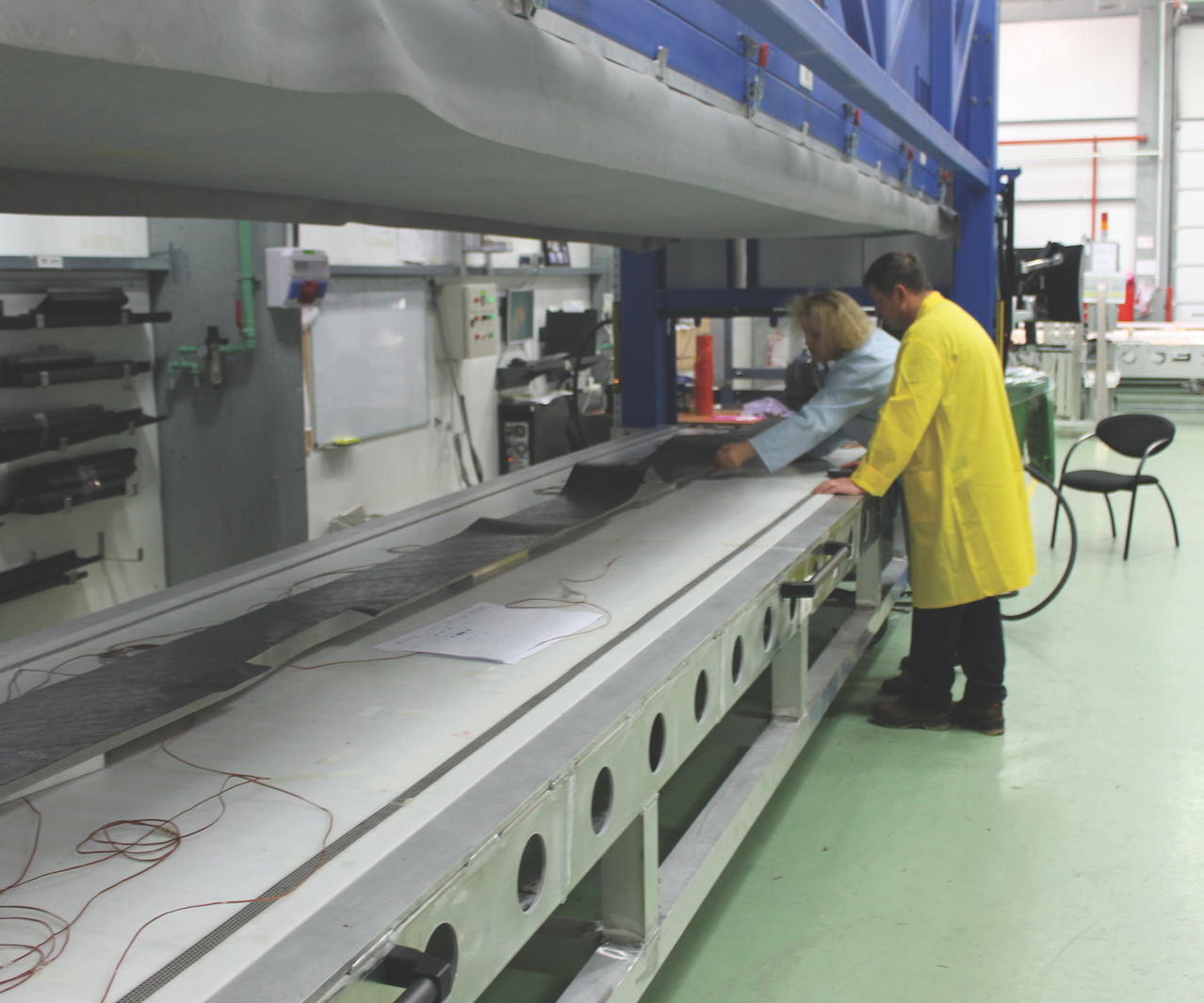
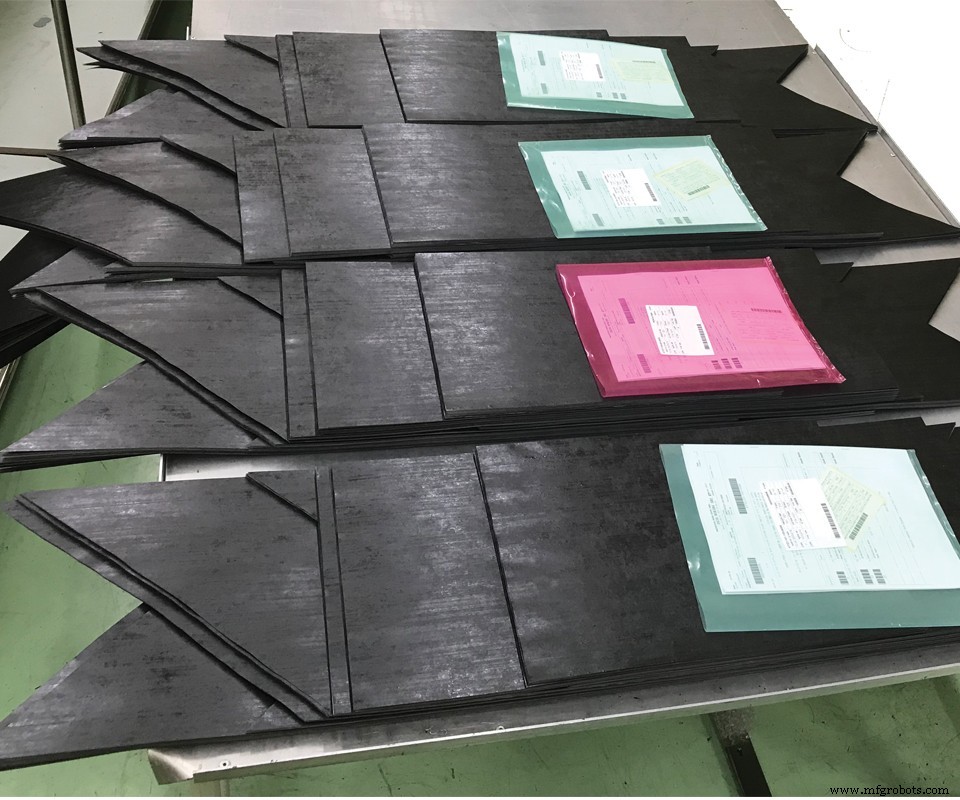
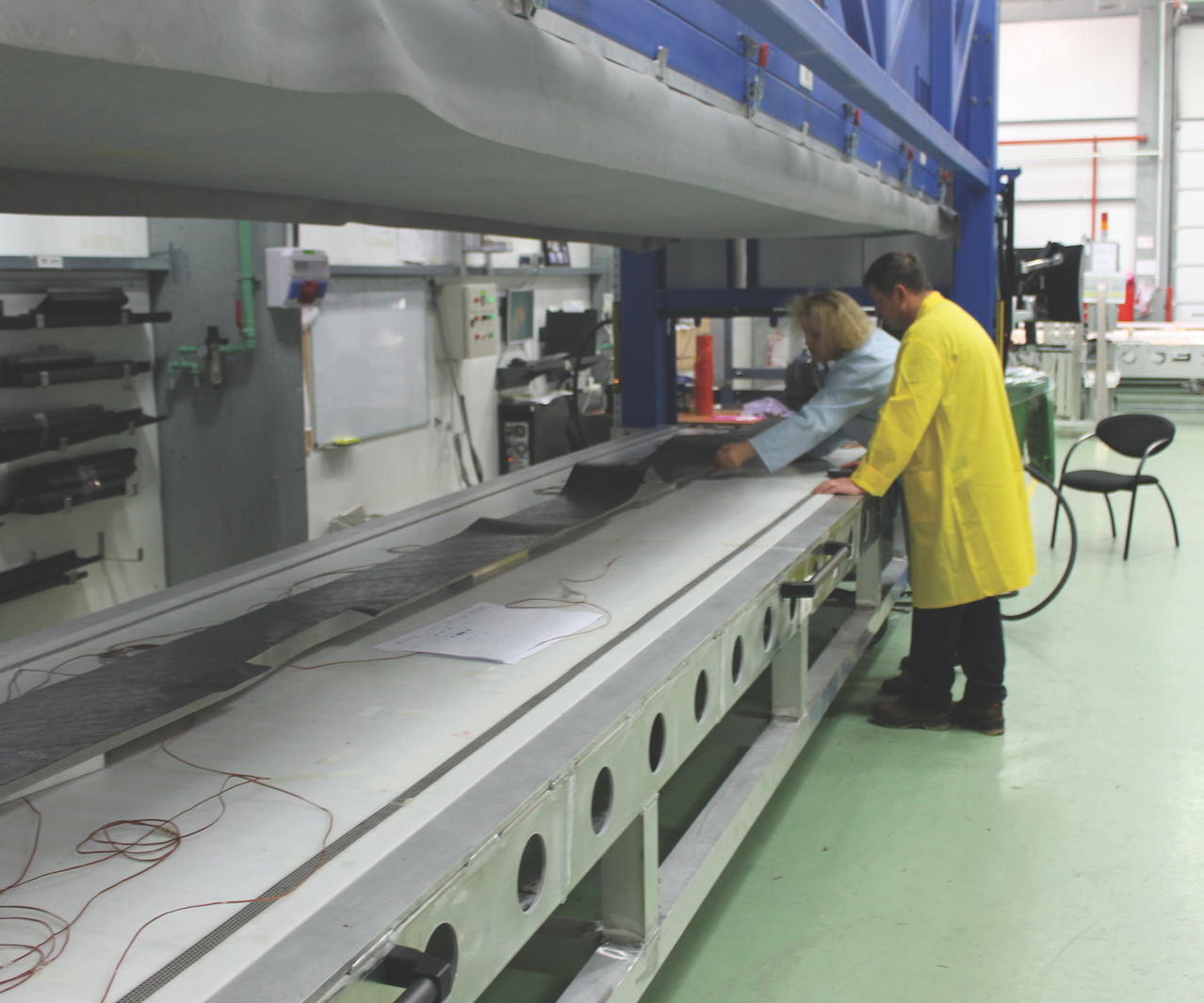
Les pièces de poutre de plancher en plastique renforcé de fibres de carbone (PRFC) sont posées sur des mandrins métalliques mâles. Hulaty détaille le processus rationalisé :« Nous déposons d'abord les piles de préimprégnés, puis les appliquons sur le mandrin. Cela permet d'économiser une tonne de temps par rapport à l'application au coup par coup sur l'outil. Les layups sont ensuite recouverts d'un revêtement CFRP de notre propre conception, ce qui permet d'assurer une répétabilité à 100 % des pièces. »
Un formage à chaud la machine se trouve le long de la paroi arrière de la salle blanche, permettant le dégrossissage de nombreuses pièces par cycle. "Je ne sais pas comment vous faites ce type de production de pièces préimprégnées à haute cadence sans formage par drapage à chaud", explique Hulaty en référence à des pièces telles que des poutres et des montants. Et pourtant, il reconnaît que cette étape n'est pas le goulot d'étranglement, pas plus que l'autoclave. « L'usinage à la fin, après le durcissement, est le goulot d'étranglement », affirme-t-il, expliquant que pour les pièces de poutre de plancher longues, il est plus rapide d'empiler une simple pile et de l'usiner après durcissement. « L'autoclave n'est pas le problème car nous pouvons empiler de nombreuses pièces à polymériser en même temps », ajoute-t-il. « Donc, nous obtenons en fait un bon taux de production par cycle de durcissement. »
2018, IAI, aérostructures
Extrait de :"La pierre angulaire de l'aérodéfense d'Israël prête pour une plus grande portée mondiale"
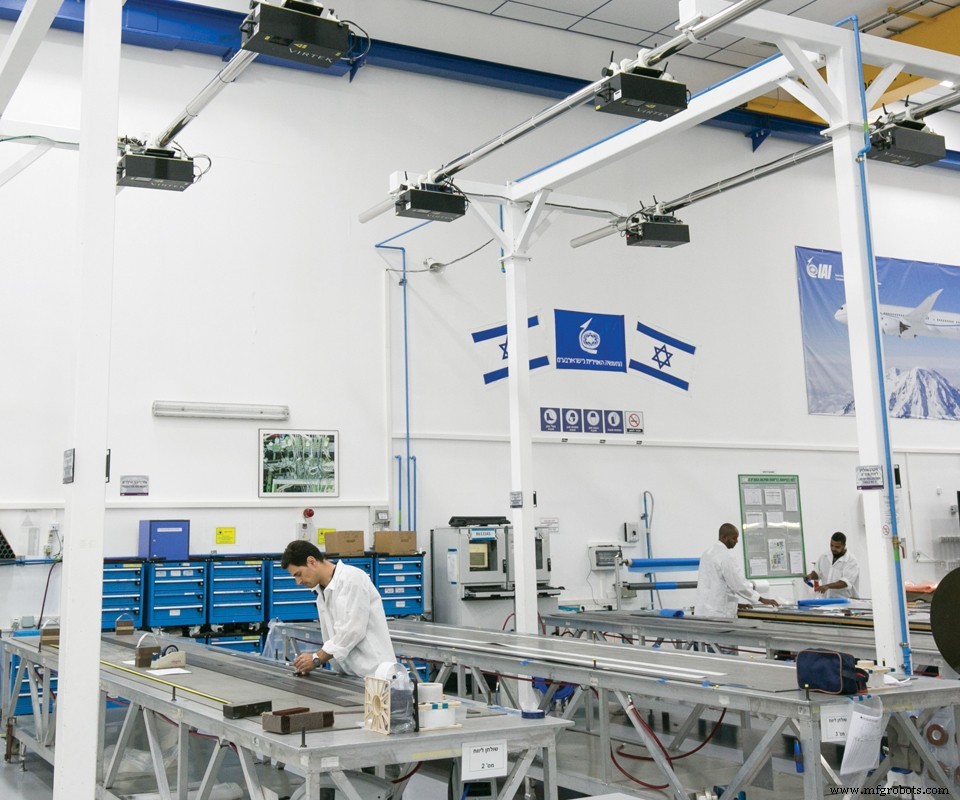
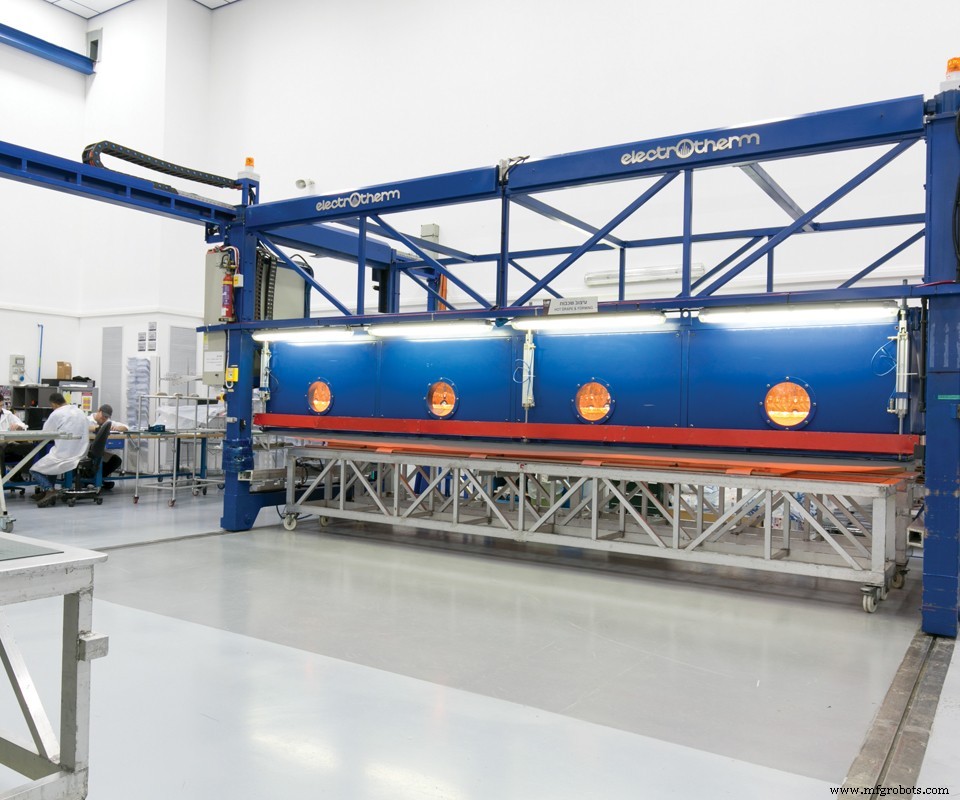
IAI utilise une machine de formage à chaud pour réduire en masse les couches épaisses de préimprégné, éliminant ainsi le besoin d'étapes de réduction intermédiaires conventionnelles. Crédit photo :Israel Aerospace Industries
Les activités d'IAI dans le domaine des composites couvrent la fabrication de pièces et l'assemblage de jets d'affaires et d'avions commerciaux, de véhicules aériens sans pilote (UAV) et d'avions militaires. Les pièces produites comprennent des stabilisateurs verticaux et horizontaux, des gouvernails, des structures d'aile, des nacelles de moteur, des poutres de plancher, des encadrements de porte, des cloisons structurelles, des nervures et des raidisseurs, des gouvernes, des carénages et des radômes. Parmi ses capacités de fabrication figurent le drapage manuel préimprégné et le drapage automatisé de bande (ATL), le formage par drapage à chaud , autoclave et durcissement hors autoclave (OOA), y compris les processus de moulage liquide, tels que l'infusion de résine et le moulage par transfert de résine (RTM), ainsi que le collage et l'assemblage complexes. L'entreprise conçoit et fabrique également ses propres outils, détient toutes les certifications de qualité clés pour l'aérospatiale et les composites et fournit une assurance qualité via des tests et des inspections non destructifs complets.
- La capacité de production d'IAI est importante, avec 10 autoclaves, dont sept appartiennent à la division Aéro-assemblages. et la taille varie de 4,5 m de long et 2 m de diamètre, au plus grand à 14 m de long et 4,7 m de diamètre.
- Les couches de préimprégné sont réduites en masse avant le durcissement à l'aide d'un formage à chaud machine (6,9 x 2,7 x 3,1 m) d'Electrotherm Industry (Migdal HaEmek, Israël).
2020, Strata, volets intérieurs A350-900
De :"Strata livre 100 ensembles de volets intérieurs pour l'A350-900"
Conçu pour augmenter la capacité de portance totale de l'aile d'un avion, un IBF [volet intérieur] est monté sur le bord de fuite de l'aile pour augmenter la surface de l'aile pendant le décollage et l'atterrissage et améliorer la stabilité pendant le vol. Strata a annoncé son intention d'automatiser entièrement le processus de fabrication IBF, en utilisant le formage par drapage à chaud (HDF) et des machines robotisées de superposition de bandes automatisées (ATL) contrôlées par ordinateur, qui ont obtenu la qualification de première pièce (FPQ) et les vérifications de conception et de qualité FAI au début de cette année.
Dans le cadre du processus, la société affirme que la machine HDF préforme des composants en fibre de carbone pour les pièces d'avion, permettant une production plus rapide de pièces composites de haute qualité, et son système de chauffage par rayonnement infrarouge ramollit rapidement et uniformément la fibre de carbone pour fournir des pièces précises qui sont dites exemptes de plis de contrainte. De plus, les deux machines ATL de Strata déposent des matériaux préimprégnés unidirectionnels sur un plateau avant d'être transférés dans un moule pour un traitement ultérieur. Selon Strata, son enveloppe de travail de 2,5 mètres sur 10 mètres permet le traitement automatisé de grandes couches composites, éliminant le besoin d'une machine de découpe à ultrasons séparée et réduisant les temps de traitement.
2020, Techni-Modul, nervure d'aile et longeron
Extrait de :« Compression RTM pour la production des futures aérostructures »
« Pour nous, OPTICOMS était aussi une question d'automatisation », explique Chevallet. Techni-Modul Engineering a fourni non seulement un système d'injection C-RTM pour le projet OPTICOMS, mais également un robot pick-and-place et un formage à chaud (HDF) machine, le tout intégré dans une cellule de production entièrement automatisée. … « Nous avons automatisé l'empilage manuel classique des plis par pick and place robotisé », précise Chevallet. « Le robot récupère les plis d'un coupeur automatisé et les transfère vers l'outil de préforme chauffé qui repose sur une table de compactage [Étapes 1 et 6]. Une couche pelable (film bleu à l'étape 6), un reniflard (matériau blanc à l'étape 6) et une membrane sous vide réutilisable à charnière (bleu clair à gauche aux étapes 2 et 6) sont appliqués, suivis d'un aspirateur et de la chaleur pour préformer et éliminer l'air du pile textile (formage à chaud, HDF ) tout en fondant les voiles thermoplastiques minces pour créer une préforme compactée.
Nervure et longeron d'aile OPTICOMS
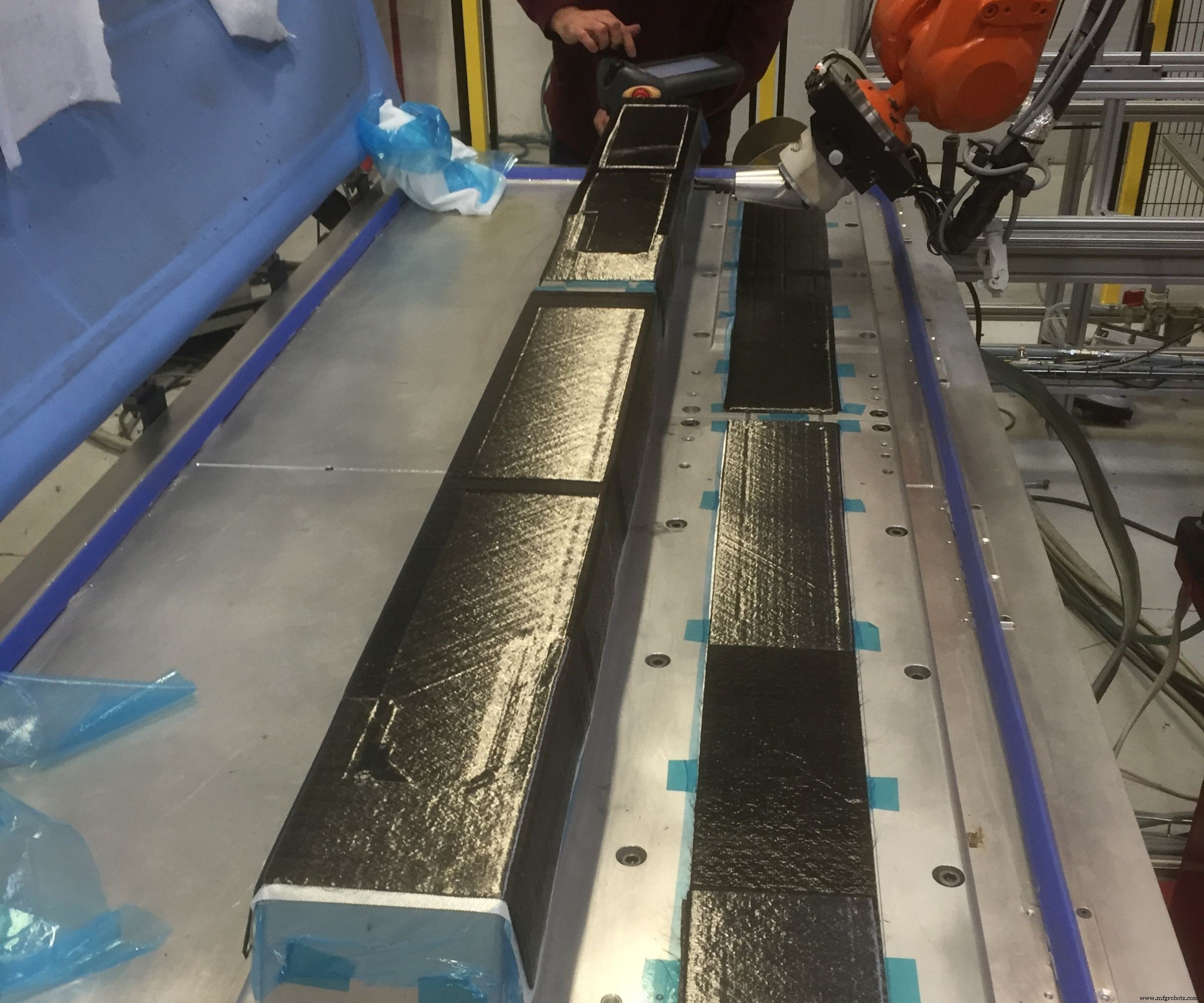
Étape 2. Les outils de préformage reposent sur une table de compactage avec une membrane sous vide réutilisable à charnière (bleue, à gauche) utilisée pour terminer un dégrossissage chauffé tous les 5 à 8 plis pendant le drapage. Crédit photo toutes les images :Tecni-Modul Engineering.
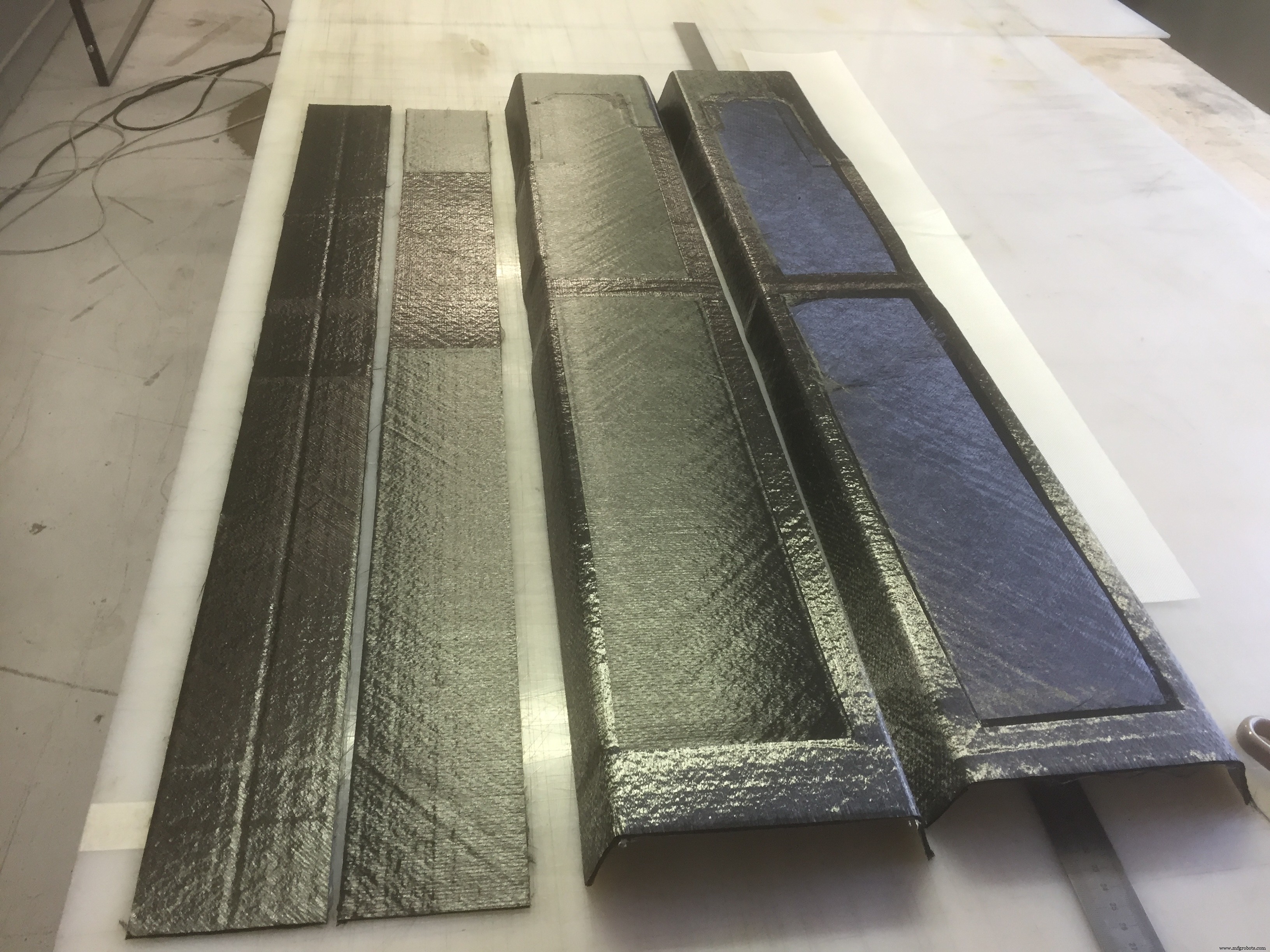
Étape 3. Chaque cycle de préformage des longerons produit une préforme de poutre en C (deux comprennent l'âme de la poutre en I) et une préforme de semelle plate. Deux ensembles requis pour chaque longeron de poutre en I sont illustrés ici.
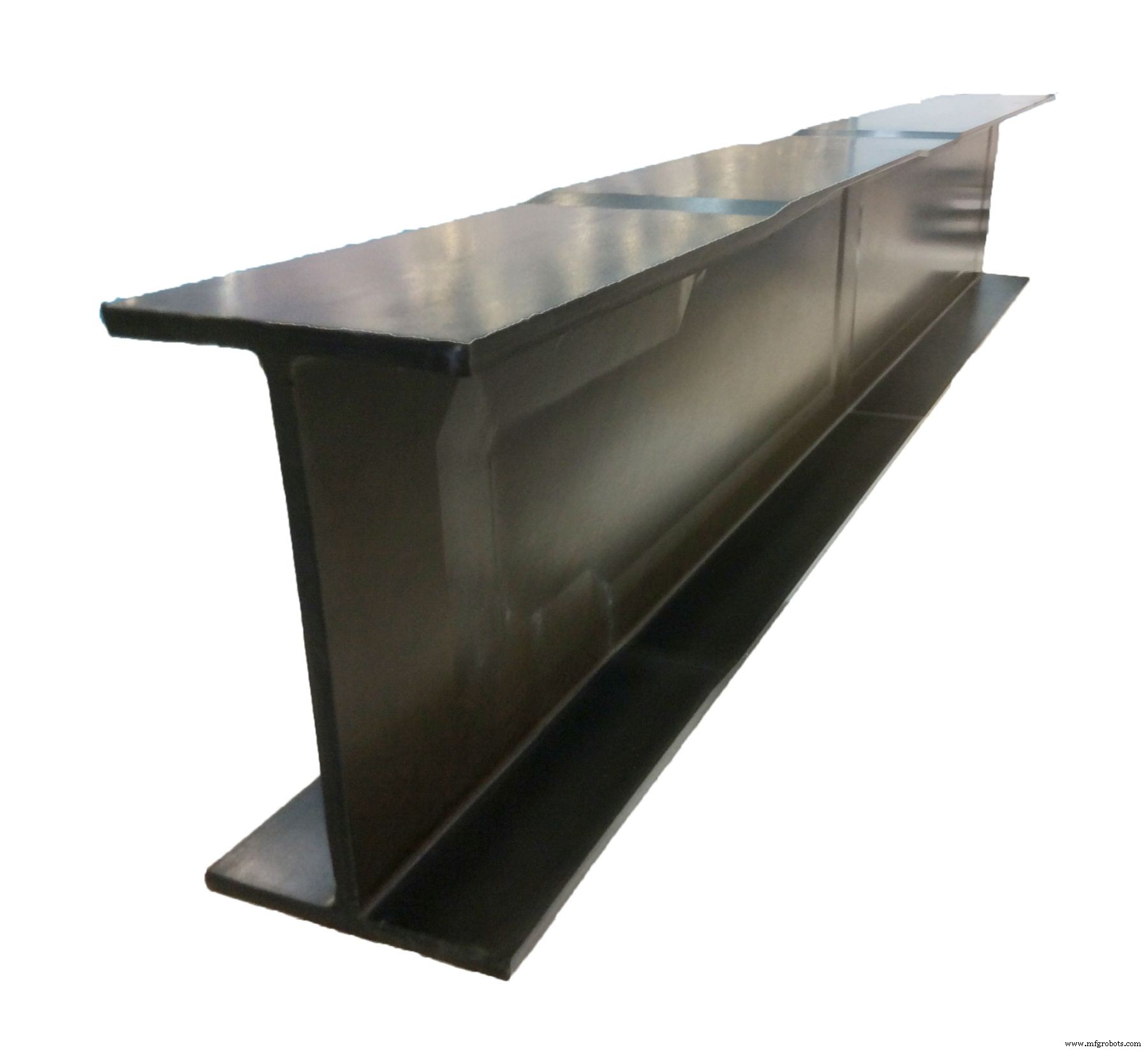
Étape 5. Limon en I réalisé à l'aide de préformes HDF et RTM pour le projet Clean Sky 2 OPTICOMS.
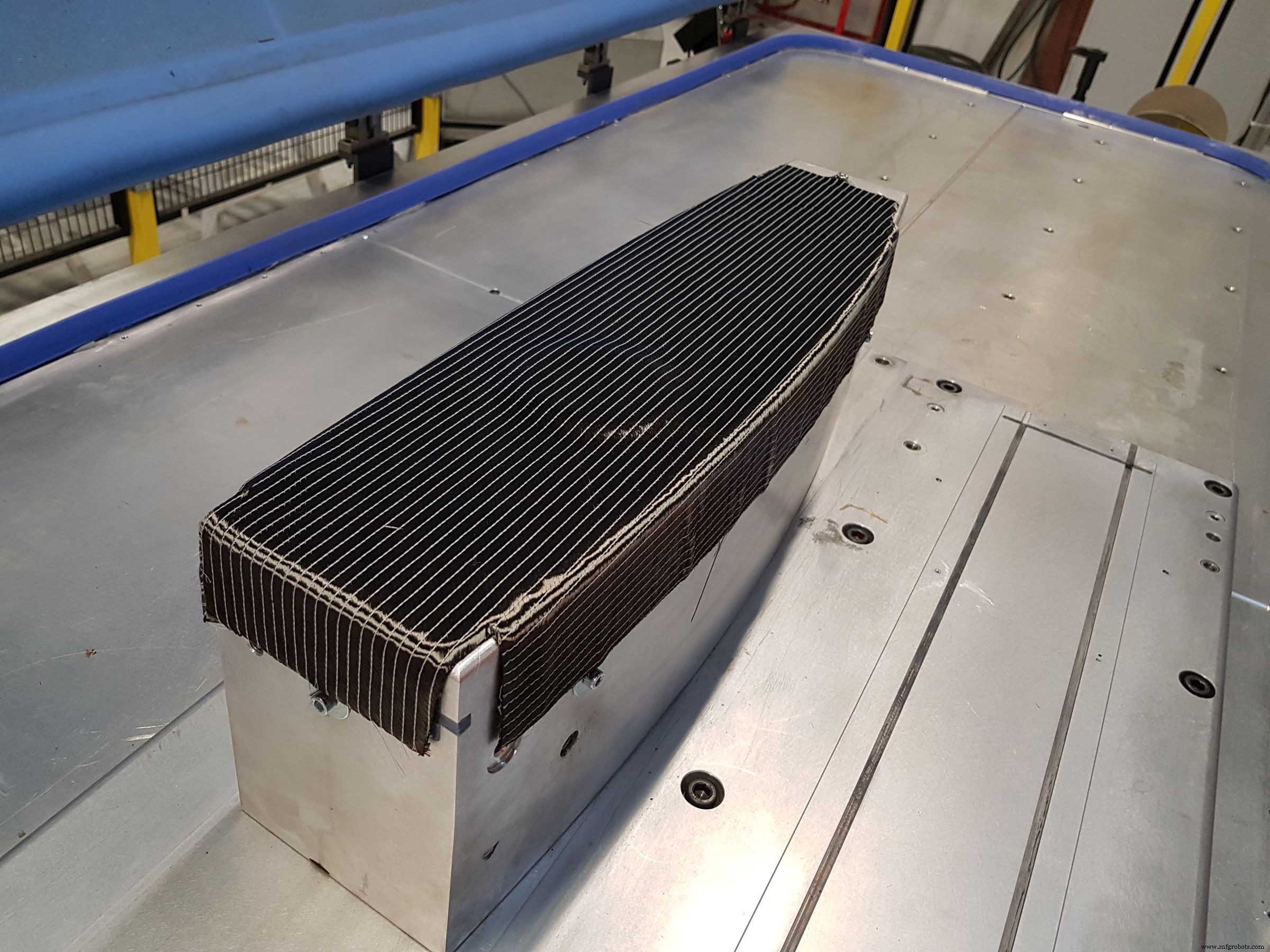
Étape 6. Un robot place des plis coupés sur l'outil de préforme chauffé. Tous les 5 à 8 plis, un dégrossissage chauffé est effectué pour compacter la préforme.
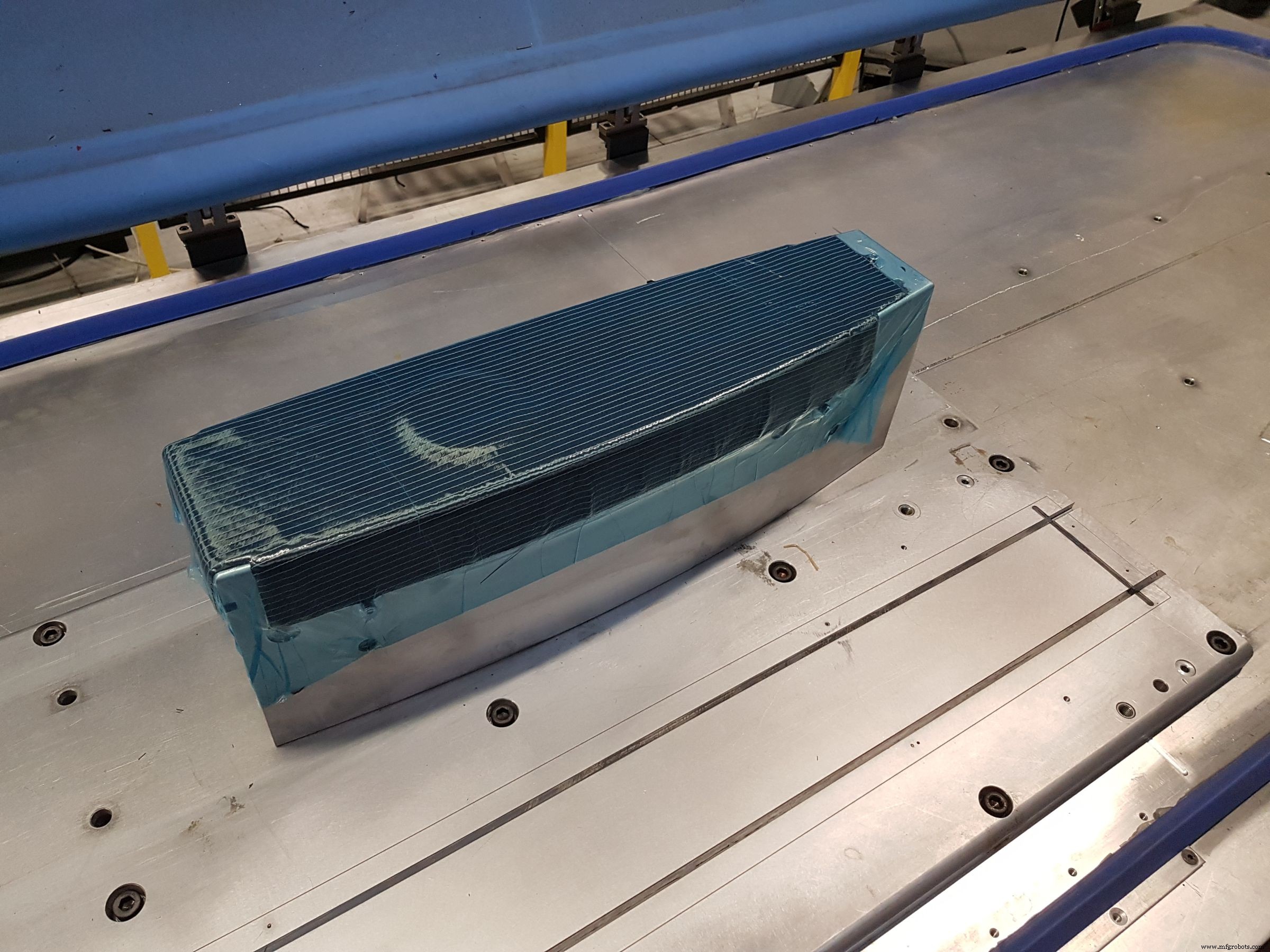
Avant le dégrossissage, un film antiadhésif bleu est appliqué.
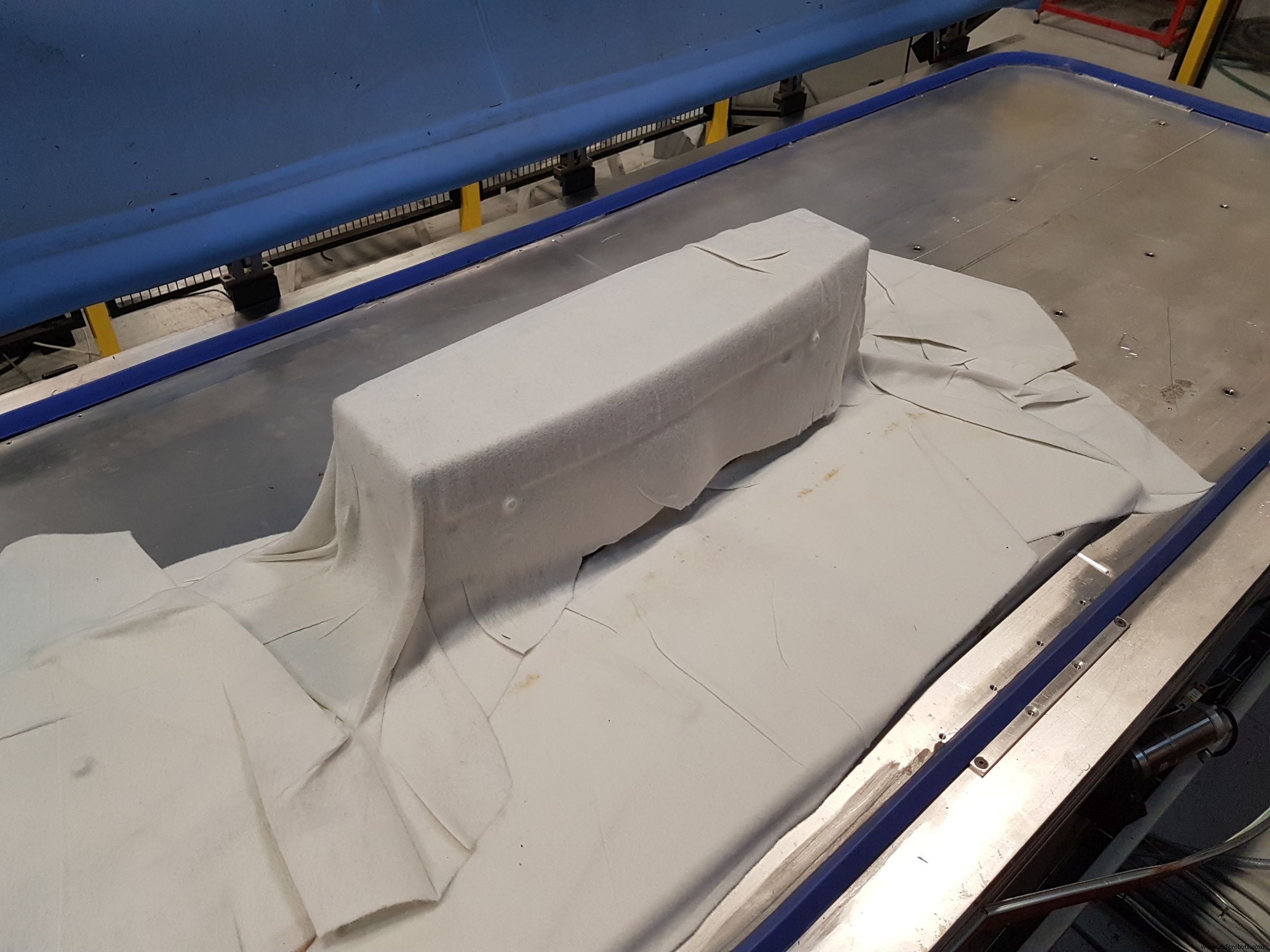
Le reniflard est utilisé pour extraire l'air à travers la préforme.
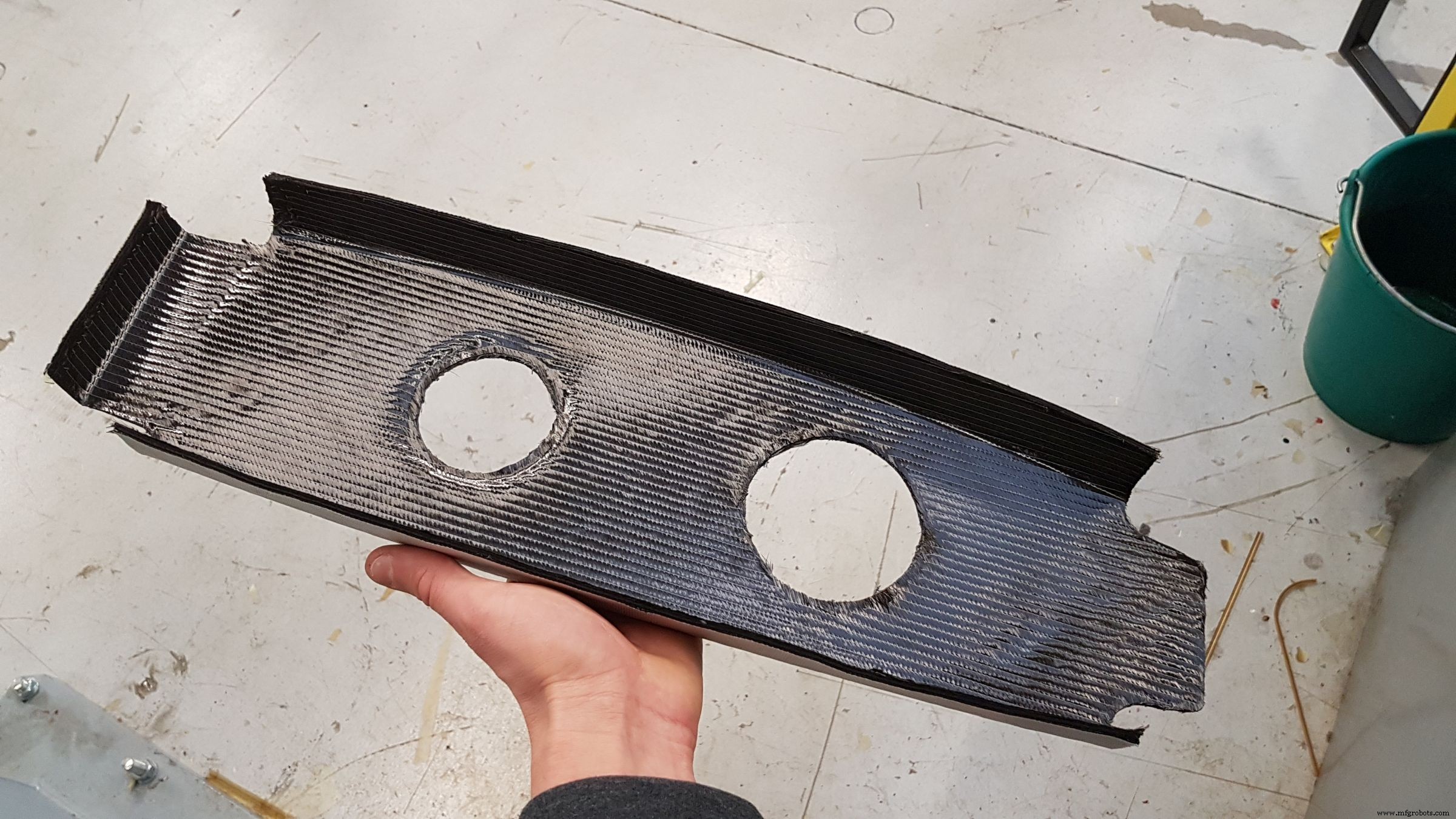
Après le dégrossissage final, la préforme est refroidie sur l'outil et les découpes sont rognées.
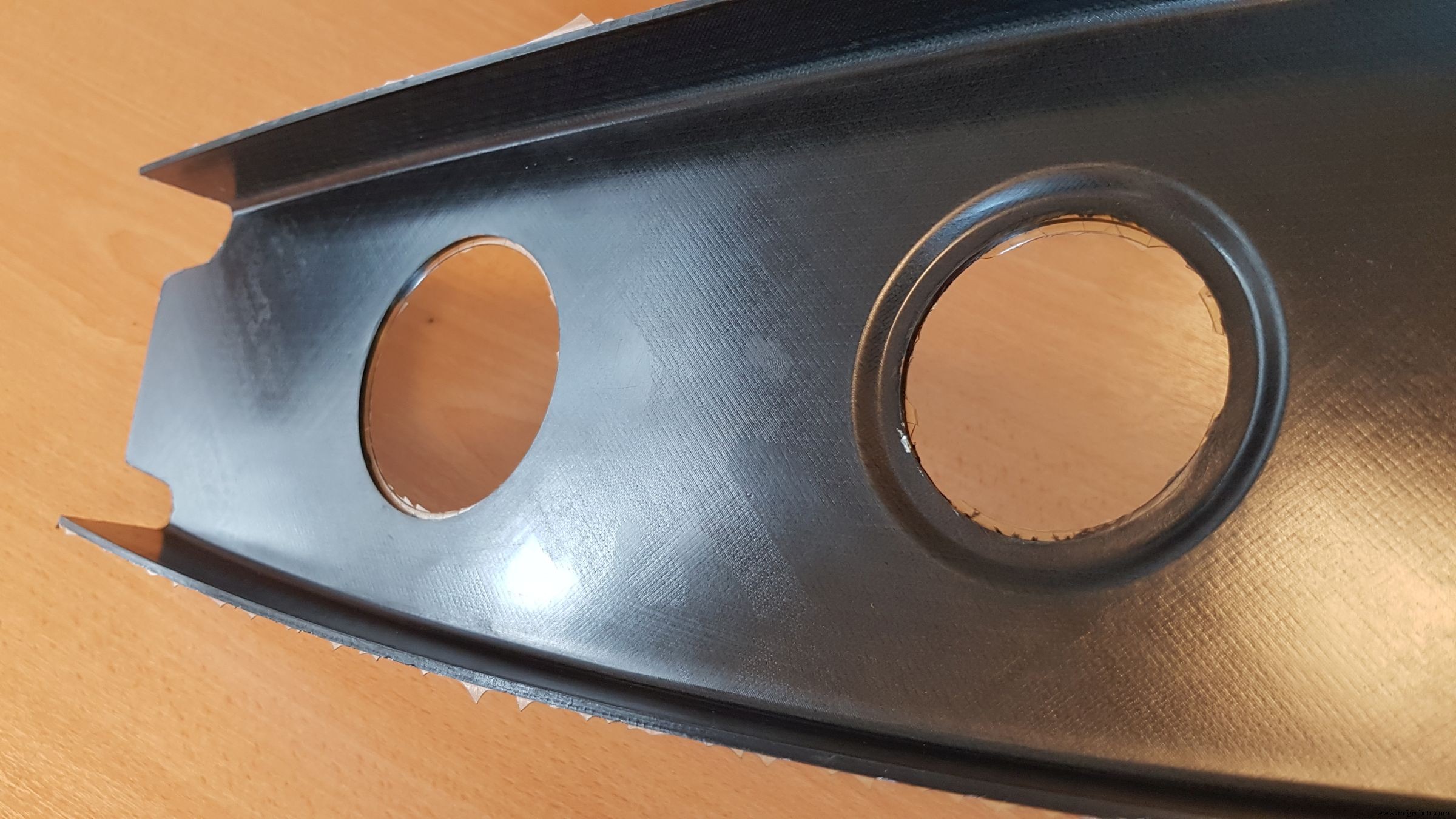
Étape 10. La préforme de nervure est moulée à l'aide de RTM et de résine époxy.
Précédent Suivant« Le nombre de plis que vous pouvez compacter à la fois dépend des matériaux et de la forme de la pièce », explique Chevallet. « Pour les pièces à faible courbure, comme une peau d'aile, vous pouvez éventuellement compacter tous les 50 plis. La nervure OPTICOMS, cependant, a des angles de 90 degrés, et le longeron de la poutre en I de test a des formes en T, vous devez donc faire attention à ne pas former de plis dans les plis pendant le préformage. Il ajoute que ces formes complexes peuvent nécessiter un compactage tous les 5 à 8 plis, mais peuvent toujours faire partie d'un processus industrialisé à grand volume :plis empilés, compactage HDF en 2 minutes , rouvrir et empiler à nouveau, suivis de cycles de compactage répétés avec un refroidissement final de la préforme sur l'outil avant transfert dans le moule RTM.
fibre