L'utilitaire bénéficie de la surveillance de l'état, de la mise à niveau du système de contrôle
Cette année, le Les États-Unis consommeront environ 3,3 térawatts, soit un peu plus de 20 % de l'électricité utilisée dans le monde, selon l'Agence internationale de l'énergie (AIE). La consommation mondiale d'électricité est en augmentation et pourrait doubler d'ici 2050, selon les projections de l'AIE, en raison de la croissance démographique mondiale et de l'amélioration du niveau de vie dans les pays en développement. Alors que la consommation d'électricité continue d'augmenter et que les réseaux électriques sont poussés à la limite, les entreprises de services publics recherchent des moyens de production électrique supplémentaires pour s'assurer qu'elles peuvent répondre de manière adéquate à la demande.
Pour un grand service public du Sud qui génère de l'électricité pour environ 600 000 clients de détail et de gros, un examen des techniques précédemment appliquées contribue à améliorer la production d'électricité aujourd'hui et pour les années à venir.
Le service public a dépoussiéré une flotte de moteurs à turbine à gaz à combustion inutilisés et souhaitait les moderniser pour produire de l'électricité de secours pendant les périodes de pointe de consommation d'énergie. HPI LLC, un développeur de projet spécialisé dans la fourniture de contrôles de modernisation pour la production d'électricité à turbine à gaz et à vapeur, les compresseurs et les systèmes d'entraînement mécanique, a été chargé de remplacer les systèmes de contrôle vieillissants des moteurs. HPI, dont le siège est à Houston, a ouvert ses portes en 2002 et a depuis réalisé plus de 70 modèles de turbines à gaz différents pour plus de 20 fabricants. L'entreprise conçoit, assemble, teste et emballe des systèmes de remplacement à l'aide de contrôleurs programmables à haute vitesse, à la pointe de la technologie et prêts à l'emploi.
Un contrôleur ControlLogix et des modules XM offrent une fiabilité et un contrôle amélioré de la turbine.
Défi
Lorsque le client a décidé de mettre à jour quatre groupes turbo-alternateur General Electric MS5001 (cadre 5), il voulait que les moteurs soient en ligne le plus rapidement possible. Le principal obstacle était le système de contrôle obsolète dans les moteurs.
En plus d'une technologie de contrôleur obsolète et d'un câblage vieillissant, le système de contrôle existant avait un besoin urgent d'une surveillance de l'état et d'une protection contre les vibrations mises à jour. Le contrôleur d'un moteur à turbine à gaz garantit que la turbine démarre et s'arrête lorsqu'elle est sollicitée, tandis que les systèmes de surveillance de l'état et de protection aident le moteur à fonctionner de manière sûre et efficace.
Défaillance du contrôleur ou de la protection sur une turbine à gaz est une proposition coûteuse et dangereuse. Le système de protection contre les vibrations existant du service public était composé d'une combinaison du système General Electric Speedtronic et d'un système de surveillance et de surveillance des vibrations Bently Nevada 3300. Pour réduire les coûts, le client souhaitait conserver les sondes de vibration General Electric existantes, mais comme le système de vibration et de surveillance Bently ne s'interface pas directement avec les sondes existantes, il était nécessaire pour HPI d'explorer d'autres solutions.
En plus du système de maintenance conditionnelle et de vibration, HPI avait besoin de mettre à jour un autre circuit de protection critique :le système de protection contre les survitesses. Dans les situations de modernisation, les clients de HPI disposent généralement d'un système de protection contre la survitesse qui est soit obsolète, soit hydraulique, ce qui rend le système difficile à tester et à entretenir. C'était le cas pour le projet de service public du Sud, et HPI avait besoin d'un système de remplacement fiable et facile à entretenir.
« Si la protection contre les survitesses tombait en panne, l'unité entière serait probablement détruite, », a déclaré Wheelwright. « Pour un client comme celui-ci, cela signifierait des millions de dollars pour acheter une nouvelle unité et des mois, voire une année complète, pour être à nouveau opérationnel. »
Solutions
fournies par HPI une solution de système de contrôle numérique standardisé pour le service public qui offrait une fiabilité améliorée, des informations de contrôle et de diagnostic de turbine améliorées et des capacités de démarrage à distance.
Le succès du nouveau système repose sur l'utilisation d'un contrôle complémentaire, d'une mise en réseau et technologies de visualisation – au cœur de l'architecture intégrée de Rockwell Automation. Conçu pour faciliter l'intégration transparente de l'entreprise, le système d'information et de contrôle de la production à architecture intégrée se compose de la plate-forme de contrôle Logix et de la suite intégrée de production et de performance FactoryTalk.
Tirant parti du contrôleur d'automatisation programmable (PAC) ControlLogix d'Allen-Bradley , les réseaux ControlNet et EtherNet/IP et le logiciel d'interface homme-machine (IHM) FactoryTalk View SE, le client dispose d'un système de contrôle de turbine cohérent. Cela se traduit par des activités étroitement coordonnées et un meilleur partage des informations.
HPI a choisi ControlLogix en raison de sa capacité à intégrer la gamme complète des disciplines d'automatisation, y compris les systèmes discrets, de mouvement, de contrôle de processus, de lots, d'entraînement et de sécurité à l'aide d'un environnement de développement unique et un protocole de communication unique et ouvert.
« Nous avions l'habitude d'acheter des contrôleurs séparés et de les câbler ensemble, mais le contrôleur Logix de Rockwell Automation nous permet de fournir des solutions clé en main qui vont au-delà du simple gaz contrôle de la turbine », a déclaré Jerry Wheelwright, vice-président de l'ingénierie, HPI.
Un autre avantage important du remplacement pour le client est venu avec le schéma de mise en réseau et la solution de visualisation. Modules d'E/S Allen-Bradley FLEX en réseau HPI avec communications réseau ControlNet et EtherNet/IP cuivre et fibre optique utilisant des modules 1756-ENTB et des modules 1756-CNB. À l'aide de ce schéma de mise en réseau, ils ont construit un PAC distant monté sur panneau qui comprend des modules d'E/S FLEX numériques, analogiques et de surveillance de la température. Pour réduire la quantité de câblage requis sur site, tous les terminaux, fusibles, relais et conduits ont été préinstallés dans des sous-panneaux.
En utilisant à la fois les réseaux ControlNet et EtherNet/IP, le client a profité des communications natives de ControlLogix sur une topologie de réseau standard. EtherNet/IP étend l'Ethernet commercial standard avec un protocole industriel ouvert à des fins d'automatisation - le même protocole utilisé dans le réseau ControlNet.
Le système de contrôle basé sur l'information permet au client de fonctionner le système, qui est piloté par un contrôleur ControlLogix à partir d'un site à huit kilomètres de la turbine physique.
« La capacité de surveiller et de contrôler les turbines à tout moment de la journée à partir d'un emplacement distant est un avantage significatif pour ce client », a déclaré Wheelwright. « Le service public peut disposer de turbines à gaz réparties dans tout l'État et exécuter les commandes via de plus grandes usines de turbines à vapeur qui fonctionnent 24 heures sur 24, éliminant ainsi le besoin de personnel pour chaque site. »
Parce que HPI utilisé la plate-forme de contrôle Logix pour standardiser les panneaux de commande, l'intégration des modules de la série XM de Rockwell Automation pour la surveillance des conditions était une solution naturelle. HPI a utilisé le module de mesure dynamique XM-120 pour la protection contre les vibrations. Le module XM-120 est un moniteur intelligent à deux canaux à usage général qui a permis au client d'utiliser ses sondes de vibration existantes.
HPI a utilisé deux modules sur chacune des quatre turbines. Le module prend en charge la surveillance des vibrations de l'arbre, du carter ou du socle dans les équipements rotatifs, tels que les turbines, où une surveillance ou une protection de l'état en temps réel est requise. Le module XM-120 s'interface avec l'équipement via les modules d'interface ControlNet vers DeviceNet.
Le remplacement du système de protection contre les survitesses a également été simplifié à l'aide de la plate-forme de contrôle Logix. HPI a remplacé le système de protection contre la survitesse obsolète par le module à double vitesse XM-220. Le module XM-220 est un module de mesure intelligent à deux canaux qui accepte l'entrée de deux tachymètres. Le module mesure la vitesse, l'accélération du rotor et la vitesse de pointe, et est capable de détecter la vitesse nulle, le rotor bloqué et la rotation inverse.
En tant que premier système de surveillance et de protection des machines de l'industrie qui relie avec succès les outils de maintenance au architecture de contrôle, le module XM-220 peut être déployé sur un bus industriel standard ouvert, permettant une surveillance et une protection continues et rentables des actifs critiques.
Résultats
Le système de contrôle de remplacement de HPI a fourni la client avec des performances cohérentes, reproductibles et fiables. Les turbines du service public n'ont pas connu d'échec de démarrage depuis la mise à niveau du contrôle. HPI était tellement satisfait de la flexibilité de la série XM, de la facilité de configuration et de la possibilité de voir que les circuits de protection fonctionnent, que la société a décidé de standardiser l'équipement pour les futures mises à niveau.
« Nous choisi la série XM pour deux raisons », a déclaré Wheelwright. « L'un était la disponibilité. C'était sur l'étagère quand nous en avions besoin. La deuxième raison était sa capacité à s'interfacer avec d'autres sondes et le reste du système. »
En raison de la simplicité de la plate-forme de contrôle Logix, HPI peut construire des sous-panneaux modulaires ou construire une armoire entièrement nouvelle qui répond les exigences d'espace spécifiques d'une usine.
HPI offre un service et une assistance technique 24h/24. En utilisant la plate-forme ControlLogix et les produits Allen-Bradley, ses clients peuvent obtenir le matériel dont ils ont besoin chez n'importe quel distributeur Rockwell Automation dans le monde. Les clients peuvent ensuite installer le matériel eux-mêmes. Depuis son siège à Houston, HPI enverra par e-mail les correctifs logiciels, travaillera sur les systèmes de contrôle et s'assurera que le modèle d'E/S est intégré.
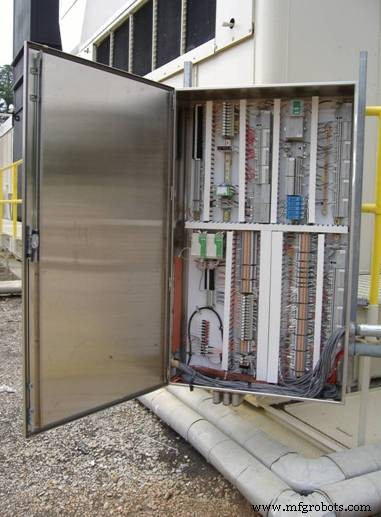
Pour réduire la quantité de câblage sur site requis, HPI préinstallé toutes les bornes, fusibles, relais et conduits dans les sous-panneaux.
Entretien et réparation d'équipement
- GEA bénéficie du système de gestion des utilisateurs étendu d'IXON Cloud
- Comment la surveillance des conditions améliore un programme PdM
- Un système de surveillance continue vous convient-il ?
- L'usine de moteurs Honda bénéficie de la surveillance des machines
- Comment une usine Nucor bénéficie de la surveillance de l'état
- Conception du système de contrôle :des conceptions les plus simples aux plus complexes
- Avantages de la convergence du contrôle industriel
- Intégration du système de contrôle
- 4 avantages de la surveillance de l'état des équipements rotatifs