Maintenance autonome :qu'est-ce que c'est et pourquoi c'est important
Maintenance autonome augmente l'efficacité en formant les opérateurs à effectuer des tâches de maintenance mineures. Ci-dessous, nous discutons de la mise en œuvre de la maintenance autonome, de sa pérennité et plus encore.
Qu'est-ce que la maintenance autonome ?
La maintenance autonome est définie comme une stratégie de maintenance dans laquelle les opérateurs de machines surveillent en permanence leur équipement, effectuent des réglages et effectuent des tâches de maintenance mineures sur leurs machines. Cela se fait plutôt que d'affecter un technicien de maintenance dédié pour effectuer la maintenance et l'entretien régulier.
La maintenance autonome est le premier pilier de la stratégie de maintenance productive totale. Un opérateur formé à la maintenance autonome signifie qu'il ou elle a une connaissance complète des tâches de routine comme le nettoyage, la lubrification et l'inspection. Elle oblige les opérateurs à s'approprier leurs équipements et leur environnement. Cela commence par amener la machine à un niveau de propreté « comme neuf » et par la maintenir à cet endroit, en veillant à ce que les opérateurs soient formés aux compétences techniques appropriées pour effectuer des inspections de routine et en normalisant un calendrier d'inspection autonome.
La maintenance autonome suit deux principes fondamentaux :
- Pour éviter la détérioration de l'équipement grâce à un fonctionnement correct, et ;
- Apporter et maintenir l'équipement à l'état "comme neuf" grâce à une restauration et une gestion appropriée.
Une grande partie de cela repose sur le fait que les opérateurs savent quand une mise à niveau de la machine est nécessaire ou quand une simple solution peut remettre la machine en marche rapidement. La maintenance autonome exige des opérateurs qu'ils maîtrisent des compétences telles que la détection d'anomalies en comprenant les composants de la machine, en apportant des améliorations, en identifiant d'éventuels problèmes de qualité et en déterminant leurs causes.
L'objectif ultime de la maintenance productive totale étant d'améliorer l'efficacité globale de l'équipement de votre organisation, il y a une raison pour laquelle cela commence par la maintenance autonome. Cela évite au personnel de maintenance qualifié d'avoir à se soucier des tâches de maintenance simples et banales, afin qu'il puisse se concentrer sur des projets de maintenance spécialisés. Cela conduit à de multiples avantages tels que :
- Amélioration des connaissances des opérateurs sur leur équipement
- Maintenir les équipements dans un état "comme neuf", en s'assurant qu'ils sont propres et lubrifiés
- La capacité de détecter les problèmes émergents avant qu'ils ne deviennent des échecs
En permettant aux opérateurs de machines de s'attaquer à ces inspections et tâches de maintenance de routine, le TRS est encore maximisé grâce à la réduction des pannes et de la détérioration de l'équipement.
Comment mettre en œuvre la maintenance autonome
La mise en œuvre de la maintenance autonome peut varier légèrement en fonction du fonctionnement de chaque usine, mais elle se décompose généralement en sept étapes.
- Améliorer les connaissances des opérateurs. Les opérateurs sont peut-être les maîtres du fonctionnement de leur machine au maximum de leur capacité, mais pour que la maintenance autonome soit efficace, ils doivent connaître les tenants et les aboutissants de leur machine. Cela implique une formation des techniciens de maintenance sur les détails techniques du fonctionnement des composants de la machine et de leur objectif, ainsi qu'une formation sur les compétences de résolution de problèmes. En bref, les opérateurs doivent avoir quatre compétences liées aux équipements :
- Détection des anomalies
- Corriger et restaurer les anomalies
- Définition des conditions optimales d'équipement
- Maintenir ces conditions optimales d'équipement
Une fois ces compétences passées en revue dans une salle de classe, les opérateurs peuvent effectuer des tâches de maintenance de base sur leurs machines pendant que les techniciens de maintenance observent pour s'assurer que tout est couvert.
- Nettoyage et inspection initial de la machine. Cette étape est celle où l'équipement est ramené à un état « de base » dans le but de le ramener à un état « comme neuf ». Toutes les mains sont sur le pont pour cette tâche, y compris les membres de la production, de la maintenance, de l'ingénierie et des opérateurs. Non seulement l'équipement est entièrement révisé et nettoyé, mais la zone environnante est également nettoyée. L'objectif est de restaurer entièrement chaque pièce d'équipement à sa pleine performance en identifiant et en éliminant les signes de détérioration. Les équipes doivent rechercher et corriger des éléments tels que :
- Fuites
- Boulons desserrés
- Lubrification appropriée
- Fissures – apparentes et non apparentes
- Taux de contamination des fluides
- Élimination des matières de l'eau et de l'huile
- Élimination de la poussière et de la saleté
- Restriction de conductibilité dans la fabrication d'électricité en raison de dépôts d'huile et/ou de poussière
- Élimination des arrêts dus à l'accumulation de poussière
C'est une bonne idée de documenter le protocole tout en effectuant ce nettoyage en profondeur afin que les problèmes puissent être facilement tracés et que les opérateurs aient accès à quelque chose qui contient des étapes faciles à suivre.
- Éliminez la cause de la contamination et améliorez l'accès. Maintenant que le nettoyage initial est terminé et que tout l'équipement est restauré, assurez-vous qu'il ne se détériore pas à nouveau. Ceci peut être réalisé en éliminant toutes les sources possibles de contamination et en améliorant l'accessibilité pour le nettoyage et l'entretien.
Cette étape prend également en considération la sécurité. L'entretien d'une machine en marche est dangereux, il est donc primordial d'améliorer la sécurité et la visibilité grâce à de meilleurs points d'accès. Une façon courante de procéder consiste à remplacer les couvercles opaques par des couvercles transparents pour une visualisation rapide et facile des pièces en fonctionnement. L'élimination de la cause de la contamination peut être effectuée par :
- Établir et respecter les normes de nettoyage.
- Éviter les salissures. Un scellage de qualité et des couvercles de machine sont de bons points de départ, mais une certaine contamination ne peut être contenue qu'en investissant dans des éléments tels que des pompes ou un dépoussiérage - soit par voie pneumatique, soit par tamisage à sec.
- Promouvoir la propreté. Répétez continuellement la propreté lors des inspections et de l'entretien.
- Promouvoir l'ordre. S'assurer que les outils ont leur place et y restent augmente l'efficacité.
- Développer des normes pour la lubrification et l'inspection. Cette étape peut être ajustée selon les besoins en fonction de chaque équipement et de son opérateur. L'établissement de normes pour les opérateurs sur le nettoyage, l'inspection et la lubrification doit commencer par la documentation actuelle au dossier et se terminer par des moyens améliorés d'accomplir ces procédures. Les normes doivent indiquer quels composants doivent être nettoyés et lubrifiés, comment ils doivent être nettoyés et lubrifiés, et toutes les autres responsabilités de maintenance à attribuer. Les normes varieront selon que la machine est considérée comme non critique ou critique.
- Pour les machines non critiques, les opérateurs sont formés par un ingénieur de maintenance expérimenté pour suivre les normes établies. Les opérateurs peuvent alors établir leur propre routine.
- Pour les machines critiques, une équipe d'ingénieurs de maintenance dédiée aux méthodes de maintenance peut être créée pour développer des normes.
Une fois finalisées, toutes les normes doivent être documentées et mises à la disposition des opérateurs.
- Inspection et surveillance. Maintenant qu'ils ont un ensemble de normes à suivre, les opérateurs peuvent modifier leur routine de maintenance de base pour rationaliser et améliorer les tâches. Les tâches de maintenance de l'opérateur sont suivies et comparées aux propres calendriers du service de maintenance (généralement via un système de gestion de maintenance informatisé) pour garantir que la duplication des tâches n'est pas un problème. Les opérateurs effectuent les tâches de maintenance de base, souvent négligées, telles que la vérification des niveaux de lubrification, la localisation des fuites, le serrage des boulons, la recherche de problèmes mécaniques imminents tels que les fissures et l'usure, et la réalisation de réglages mécaniques tels que les mesures de tension, la régulation des capteurs, etc.
- Standardiser la maintenance visuelle. La standardisation de la maintenance autonome et de la "visibilité" des équipements est une étape importante pour maintenir l'intégrité de chaque machine. Comment rendre l'équipement visuel ? Les exemples incluent l'identification du flux de fluides à travers les tuyaux, le remplacement des revêtements opaques par des revêtements transparents lorsque cela est possible, l'étiquetage du sens d'ouverture/fermeture des vannes et des leviers, et le marquage des valeurs de fonctionnement « sûres » ou « normales » sur les jauges et les voyants en vert avec dangereux niveaux en rouge. Bref, rendez les choses sur la machine aussi évidentes que possible.
- Amélioration continue. Prendre périodiquement du temps pour prendre du recul et analyser les processus standardisés pour voir où il y a place à l'amélioration est important pour vous assurer que vous fonctionnez efficacement. Il est essentiel de conserver de bons enregistrements des pannes pour fournir des données que les ingénieurs de maintenance peuvent utiliser lors de la conception des futures machines, ce qui les rend encore plus faciles d'accès et de maintenance.
L'amélioration continue peut également provenir des chefs d'équipe et des techniciens de maintenance qui auditent régulièrement le travail des opérateurs. Non seulement cela leur permet de signaler les domaines d'amélioration, mais cela leur donne également l'occasion de féliciter les opérateurs pour leur bon travail.
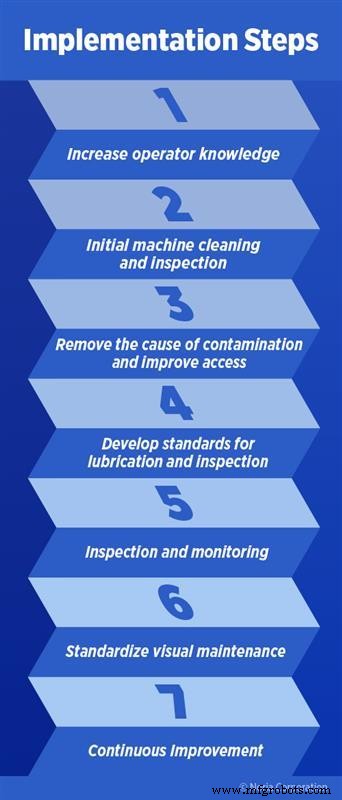
Maintenir la maintenance autonome
Une fois que vos opérateurs sont correctement formés à la maintenance autonome, que les procédures sont standardisées et qu'un système d'audit est en place, il est temps de se concentrer sur la pérennité de ce processus. Il existe quelques outils simples que vous pouvez intégrer à votre routine quotidienne pour vous aider à maintenir le processus de maintenance autonome.
Une réunion debout quotidienne est un excellent moyen pour les opérateurs et leurs managers directs de se réunir chaque matin pour discuter de la façon dont les choses se passent. Ces réunions fonctionnent en faisant le tour du cercle et en permettant à chacun de discuter de ce qui fonctionne bien et de mentionner les problèmes qu'il a rencontrés. Les autres points à l'ordre du jour incluent les leçons apprises, l'état de la main-d'œuvre, les mises à jour de la gestion et les objectifs et actions de la journée. Les réunions debout quotidiennes peuvent mettre en évidence les difficultés auxquelles les opérateurs sont confrontés ou introduire des changements de la part de la haute direction qui doivent être intégrés.
Cours à point unique sont excellents pour aider les membres de l'équipe à mettre en œuvre des changements, les aidant à ne pas oublier une étape dont ils ont du mal à se souvenir ou à communiquer les problèmes qui se sont produits dans le passé pour éviter qu'ils ne se reproduisent. Les leçons à un point sont généralement axées sur les sous-systèmes d'équipement, les points de sécurité et les informations de fonctionnement de base. Un exemple de leçon en un point serait de créer une étiquette autocollante à placer directement sur un levier ou une protection pour rappeler à un opérateur qui a du mal à se rappeler de remettre le levier ou une protection en position de sécurité avant de continuer vers le procédure suivante.
D'autres étapes pour maintenir la maintenance autonome incluent :
- Suivre les pannes et les pannes : Ces données sont essentielles lorsque vous commencez à former vos procédures de maintenance autonome. Non seulement cela guide vos opérateurs sur l'équipement qui nécessite le plus d'attention, mais le suivi de ces données au fil du temps vous permet de suivre l'amélioration.
- Utiliser les métriques : Des mesures établies sont la clé du contrôle et du suivi de l'efficacité globale de l'équipement en ce qui concerne les réparations et les performances. L'analyse des modèles de choses comme le temps moyen entre les pannes et le temps moyen de réparation vous aide à apprendre à prévoir et même à prévenir les pannes futures.
- Usure des composants du document : Utilisez d'autres moyens pour suivre l'usure des composants. Les technologies de maintenance telles que l'analyse de l'huile, l'analyse des vibrations et la thermographie infrarouge peuvent vous donner un aperçu supplémentaire des pannes d'équipement.
- Normalisation de la création des bons de travail : L'utilisation d'un logiciel de commande de travail permet d'automatiser et de suivre les données de création et de maintenance des commandes de travail. Un logiciel intégré à un système informatisé de gestion de la maintenance (GMAO) vous permet de créer un journal de maintenance pour chaque équipement de votre usine. Ici, vous pouvez enregistrer chaque instance de défaillance, de remplacement et lorsque l'état des composants change.
Avantages de la maintenance autonome
La plupart des organisations investissent massivement dans l'embauche, la formation et le développement d'une équipe de maintenance hautement qualifiée pour déterminer pourquoi les actifs critiques échouent, puis les réparer. La maintenance autonome vise à libérer ces techniciens d'effectuer des tâches peu qualifiées comme les inspections, la lubrification et les réglages mineurs. Entre autres, il y a trois avantages majeurs que la maintenance autonome apporte à une organisation.
Le principal avantage est la baisse des coûts de main-d'œuvre. Cela inclut la diminution des inefficacités liées au temps de déplacement et à l'attente de disponibilité. En ayant un opérateur qui est à côté d'une machine à tout moment, ces types de problèmes sont considérablement réduits.
Un autre avantage de la maintenance autonome est d'augmenter la disponibilité d'un personnel de maintenance hautement qualifié afin qu'il puisse répondre à des besoins plus critiques. L'utilisation de la maintenance autonome permet même aux services de maintenance les plus restreints de s'occuper des problèmes critiques sans sacrifier la maintenance de routine.
Enfin, la maintenance autonome améliore la cohésion d'équipe en éliminant l'état d'esprit « nous/ils ». Traditionnellement, l'opérateur a un état d'esprit « j'utilise », tandis que le technicien de maintenance a un état d'esprit « je maintiens et répare ». La maintenance autonome transforme cela en une attitude plus cohésive « nous maintenons » qui s'intègre directement dans les piliers de la maintenance productive totale.
Entretien et réparation d'équipement
- L'usine numérique :qu'est-ce que c'est et pourquoi c'est important
- Qu'est-ce que l'entretien des plantes ?
- Qu'est-ce que la Maintenance Usine ?
- Qu'est-ce que la maintenance d'urgence ?
- Qu'est-ce que la Maintenance Prédictive ?
- Qu'est-ce que la Maintenance Préventive ?
- Qu'est-ce que la maintenance prédictive pour les grues et pourquoi est-ce important ?
- Qu'est-ce qu'un directeur de maintenance et que fait-il ?
- Qu'est-ce que la maintenance durable et pourquoi est-ce important ?