Spécification et commande de pièces moulées en métal personnalisées :un guide
9 considérations importantes pour assurer le succès de vos projets de moulage de métal sur mesure
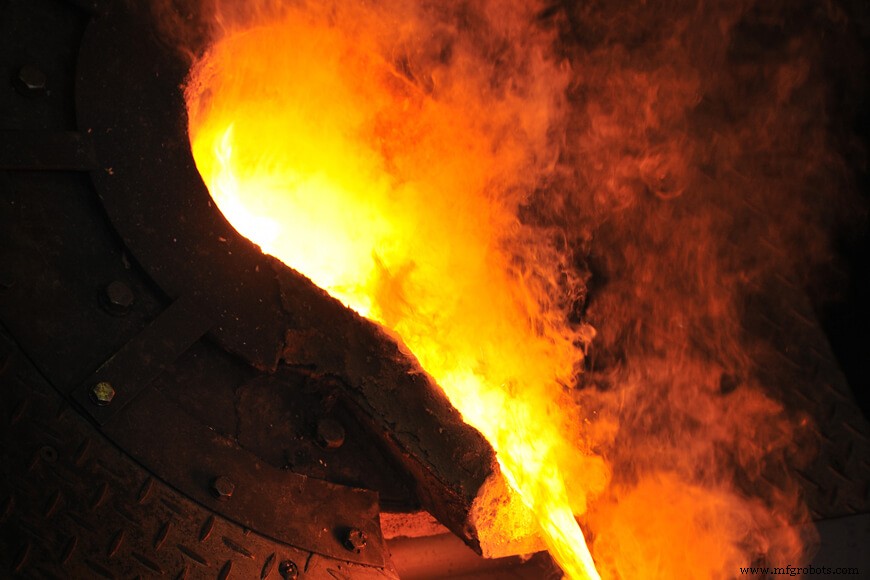
La coulée de métal est un processus qui produit des formes (pièces moulées) en remplissant les vides dans les moules avec du métal liquide. Les produits en métal coulé offrent une résistance et une durabilité exceptionnelles, ce qui les rend utiles pour les applications de machines lourdes dans les industries liées à l'agriculture, l'automobile, les chemins de fer, les appareils électroménagers, l'architecture du bâtiment, la construction navale, l'extraction de pétrole et de gaz, le traitement de l'eau, la foresterie et l'exploitation minière, pour n'en nommer qu'un peu.
Qualifier une fonderie de fournisseur et commander des pièces moulées en métal peut être une épreuve chronophage, mais ce n'est pas obligatoire. Des gaffes coûteuses peuvent être évitées en comprenant le processus de cotation et de casting. Une communication claire et approfondie avec la fonderie du fournisseur se traduira par un produit final bien conçu et économique.
Demander un devis
Le but de demander un devis pour un moulage est d'établir l'équilibre optimal entre le coût du moulage acheté, la qualité et le délai de livraison. Bien qu'il puisse être tentant de sélectionner automatiquement le prix le plus bas proposé, cela peut entraîner un retard de livraison ou un casting de qualité inférieure, les deux pouvant être plus coûteux à long terme.
Un client avisé doit peser toutes les dispositions du devis reçu, y compris les exigences d'outillage, les tolérances et les tolérances de finition, ainsi que toutes les exceptions apportées aux dessins, spécifications et exigences de traitement. D'autres facteurs, tels que la réduction du travail des machines, l'amélioration des conditions de livraison et l'expérience et la fiabilité des fonderies du fournisseur, sont particulièrement importants pour déterminer le coût réel par rapport à la valeur de la pièce coulée.
Il y a au moins neuf considérations importantes à prendre en compte lors de la demande de prix de coulée de métal auprès d'un fournisseur de fonderie :
- Conception préliminaire du moulage
- Quantité
- Spécifications
- Fiabilité
- Tests et inspection
- Poids
- Modèles
- Usinage
- Calendriers de production et de livraison
1. Conception préliminaire du moulage
Une pièce en métal coulé doit être conçue pour tirer pleinement parti du processus de coulée. Pour une production efficace et sensible aux coûts, la conception de la fonderie doit sélectionner les méthodes de production les plus simples qui se traduiront par les propriétés physiques souhaitées, les exigences de forme nette et l'apparence esthétique.
Des dessins détaillant les dimensions exactes de la pièce requise doivent être joints à toute demande de devis.
Il existe plusieurs éléments clés de la conception où une compréhension des processus de fonderie et/ou des communications avec les fonderies fournisseurs aidera à déterminer les conceptions les plus rentables du point de vue de la fonderie.
Épaisseur minimale de la section
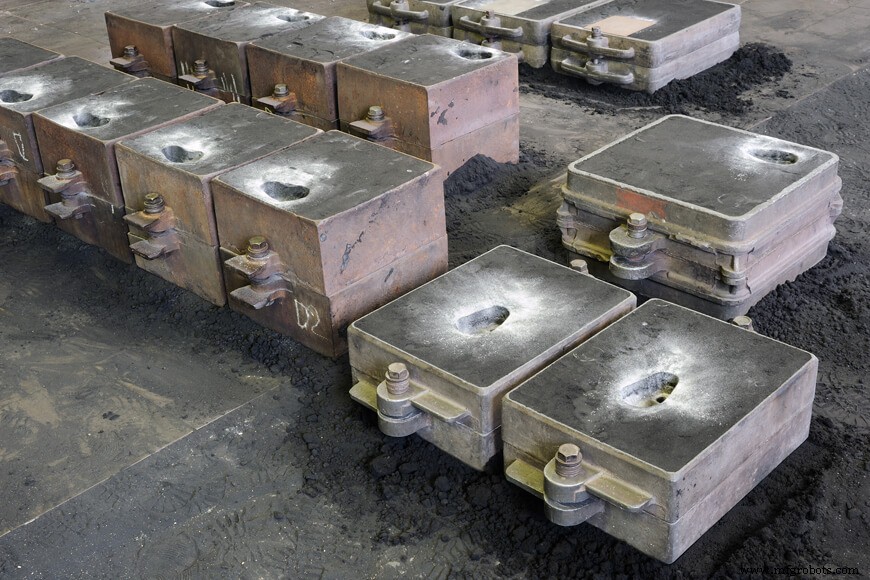
Chaque moulage a une épaisseur minimale déterminée par sa résistance et sa rigidité. Les conceptions plus minces que les spécifications peuvent rendre le projet incastable. Pour réussir, la conception d'un moulage doit permettre au métal liquéfié de remplir le moule dans les sections les plus minces.
Le métal liquéfié (fondu) se refroidit à une vitesse exceptionnellement rapide. Il peut refroidir trop rapidement pour entrer dans des sections minces éloignées de la porte du moule. En règle générale, les conceptions ne doivent pas avoir de zones plus minces que 0,25 po (6 mm) lorsque des procédés conventionnels sont utilisés. Le moulage à modèle perdu permet un plus grand niveau de liberté et l'épaisseur de paroi peut chuter jusqu'à 0,030 po (0,76 mm).
Brouillon et noyau
Le terme "ébauche" fait référence à la conicité sur les faces verticales d'un motif. Une ébauche est nécessaire pour extraire le motif du moule sans perturber les parois du moule. Ignorer les limites de ces angles entraînera la déchirure du moule lorsqu'il sera retiré du moulage.
Plusieurs facteurs affecteront la quantité de tirage requise pour chaque moulage :le processus de fabrication, la taille du moulage et le fait que le moulage soit effectué à la main ou à la machine modifieront tous le degré de tirage requis. Moins de tirage est nécessaire pour les moulages moulés à la machine. Les moulages produits avec des moules en sable vert, cependant, nécessiteront plus de tirage que d'habitude. La règle générale est de permettre 3/16 po de tirant d'eau par pied (environ 1,5 degré).
Un noyau est un espace creux créé dans un moulage par un morceau de sable de moulage. Les noyaux sont nécessaires lorsque les espaces ou les cavités ne peuvent pas être créés avec le motif seul. L'utilisation de noyaux peut éliminer le besoin de tirage, mais leur utilisation doit être limitée car ils augmentent le coût de la coulée.
Trois facteurs affectent le diamètre minimum d'un noyau pouvant être placé dans un moulage :
- L'épaisseur ou la profondeur de la zone dans laquelle le noyau sera placé,
- La longueur du noyau, et
- La méthode de moulage que la fonderie du fournisseur utilisera.
Ligne de séparation
Le tronçonnage dans un plan facilite la réalisation des patrons ainsi que la réalisation du moule. Les motifs avec des lignes de séparation droites (avec des lignes de séparation dans un plan) peuvent être produits plus facilement et à moindre coût que ceux avec des lignes de séparation irrégulières. Les formes de moulage symétriques suggèrent facilement la ligne de séparation. Une telle conception de moulage simplifie le moulage et le carottage et doit être utilisée dans la mesure du possible. Ils doivent toujours être fabriqués sous forme de "modèles divisés" (chape et traînée séparées) qui nécessitent un minimum de travail manuel dans le moule, améliorent la finition de la coulée et réduisent les coûts.
Cœurs
Un noyau est une pièce séparée (souvent fabriquée à partir de sable de moulage) placée à l'intérieur du moule pour créer des ouvertures et des cavités qui ne peuvent pas être réalisées par le seul motif. Pour réduire le coût final de la coulée, chaque tentative doit être faite par la conception pour éliminer ou réduire le nombre de noyaux nécessaires.
Le diamètre minimum d'un noyau pouvant être utilisé avec succès dans les pièces moulées en acier dépend de trois facteurs :
L'épaisseur de la section métallique entourant l'âme,
La longueur de l'âme, et
Les précautions et procédures particulières utilisées par le fondeur fournisseur.
Les conditions thermiques défavorables auxquelles le noyau est soumis augmentent en sévérité à mesure que l'épaisseur du métal entourant le noyau augmente et que le diamètre du noyau diminue. Ces quantités croissantes de chaleur provenant de la section lourde doivent être dissipées à travers le noyau. À mesure que la sévérité des conditions thermiques augmente, le nettoyage des pièces moulées et le retrait du noyau deviennent beaucoup plus difficiles et coûteux.
L'épaisseur de la section métallique entourant l'âme, et la longueur de l'âme, affectent toutes deux les contraintes de flexion induites dans l'âme par les forces de flottabilité et, par conséquent, la capacité du fondeur fournisseur à obtenir les tolérances requises. Si la taille du noyau est suffisamment grande, des tiges peuvent souvent être utilisées pour renforcer le noyau. Naturellement, à mesure que l'épaisseur du métal et la longueur de l'âme augmentent, la quantité de renforcement nécessaire pour résister aux contraintes de flexion augmente également. Par conséquent, le noyau de diamètre minimum doit également augmenter pour accueillir le renforcement supplémentaire.
Le coût de retrait des noyaux des cavités de coulée peut devenir prohibitif lorsque les zones à nettoyer sont inaccessibles. La conception du moulage doit prévoir des ouvertures suffisamment grandes pour permettre le retrait du noyau.
Les zones moins accessibles dans la coulée rendent plus difficile le retrait des noyaux et affectent la faisabilité économique des projets. Les pièces moulées doivent toujours être conçues avec des ouvertures suffisamment grandes pour permettre le retrait des noyaux.
Les pièces moulées sont normalement expédiées avec des surfaces brutes de coulée non usinées, sauf indication contraire. Pour tirer parti du processus de coulée, le fournisseur de fonderie doit savoir quelles surfaces seront éventuellement usinées (voir "8. Usinage" ci-dessous pour plus de détails) et où se trouvent les points de référence. Les tolérances dimensionnelles acceptables doivent être indiquées lorsqu'un dessin est fourni. Les tolérances sont normalement convenues entre la fonderie du fournisseur et le client.
Une coopération étroite entre les ingénieurs de conception du client et la fonderie du fournisseur est essentielle pour optimiser la conception de la pièce moulée. Toutes les conceptions de moulage doivent être vérifiées par un professionnel de la fonderie avant la production afin de déterminer la faisabilité du projet de moulage.
2. Quantité
Le nombre de pièces moulées à produire, ou la durée du tirage, doit être clairement indiqué. La quantité commandée aura un impact significatif sur le prix, des séries plus longues correspondant à un coût par moulage inférieur.
La quantité de pièces requises n'est pas une considération mineure; non seulement la consommation de projet de la pièce déterminera les types d'outillage requis, mais elle définira également la capacité de fonderies spécifiques à répondre aux besoins de volume de production.
De nombreuses fonderies se spécialisent dans la production de travaux de courte durée et de courte durée, tandis que d'autres se concentrent sur la production à grand volume. Définir vos besoins dès le début vous aidera à vous assurer que vous communiquez avec les bonnes installations de production.
3. Spécifications
Les spécifications standard de l'industrie fournissent au client de moulage les outils nécessaires pour établir des critères pour presque toutes les applications de moulage. Ces spécifications n'excluent pas les exigences particulières que peuvent exiger les membres du personnel technique du client. Les écarts par rapport aux spécifications standard peuvent entraîner des malentendus, des coûts plus élevés et la disqualification des fonderies de fournisseurs potentiels. Si une exception est faite à une disposition dans le corps principal d'une exigence de spécification (par opposition à une exception à une exigence supplémentaire d'une spécification), le moulage résultant ne peut pas être tenu pour conforme à ces spécifications.
L'alliage métallique exact à couler doit être spécifié à l'aide d'une norme internationalement reconnue telle que l'ASTM. Les pièces moulées sont produites à partir de deux catégories de métaux :ferreux (à base de fer) et non ferreux (à base de fer).
L'acier moulé est le métal de coulée ferreux le plus courant, cependant, d'autres métaux peuvent être utilisés en fonction des propriétés physiques souhaitées, notamment l'acier inoxydable, la fonte malléable et la fonte ductile. L'aluminium et le cuivre sont les métaux non ferreux les plus couramment utilisés dans la coulée.

Les propriétés mécaniques peuvent être vérifiées à l'aide d'éprouvettes, soit coulées séparément, soit fixées aux pièces moulées. Les propriétés mécaniques obtenues représentent la qualité du métal, mais ne représentent pas nécessairement les propriétés des pièces moulées elles-mêmes, qui sont affectées par les conditions de solidification et la vitesse de refroidissement pendant le traitement thermique, qui à leur tour sont influencées par l'épaisseur, la taille et la forme de la pièce coulée. . La capacité de durcissement de certaines nuances peut limiter la taille maximale à laquelle les propriétés mécaniques requises peuvent être obtenues.
Traitement thermique
Le traitement thermique est utilisé pour normaliser, homogénéiser et améliorer les propriétés d'alliages spécifiques. Pour de nombreux alliages, le traitement thermique est un processus de routine utilisé pour garantir que les propriétés physiques minimales spécifiées sont atteintes dans les produits coulés finaux. Des dispositifs de contrôle de la température et même des équipements d'enregistrement de température avancés se trouvent couramment sur les fours de traitement thermique modernes pour assurer la cohérence et la qualité des étapes de traitement thermique.
Dans certains cas, un traitement thermique spécialisé (tel que la trempe à la flamme, la cémentation, etc.) peut être spécifié comme un processus supplémentaire devant être effectué par la fonderie du fournisseur.
4. Solidité
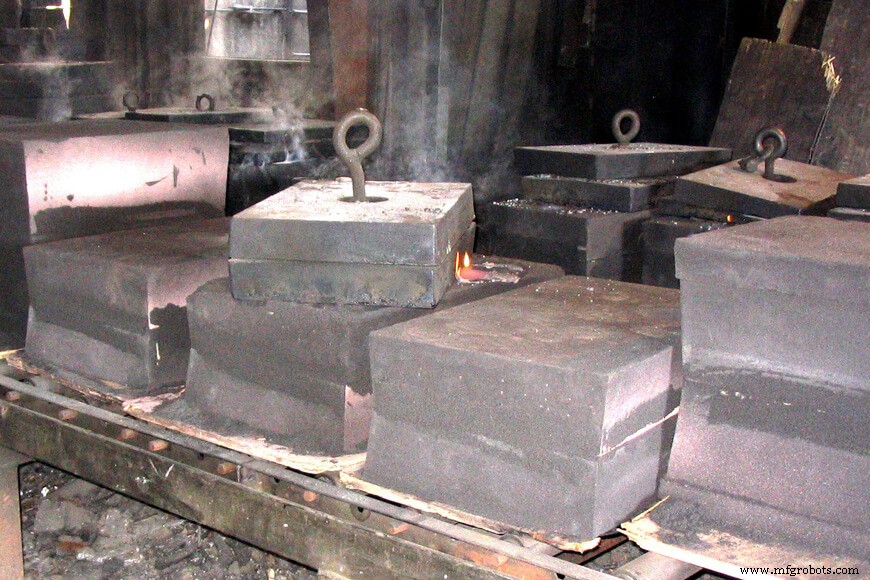
La solidité des composants métalliques fait référence au niveau d'absence d'impuretés et/ou de discontinuités, telles que les inclusions de sable, les inclusions de laitier, la macroporosité et le retrait. Il est impossible de produire une pièce moulée sans défaut, uniquement des pièces moulées présentant des défauts à des degrés divers. L'acceptation ou le rejet des pièces moulées est déterminé par l'examen des pièces (conformément aux normes internationalement reconnues telles que l'ASTM) en fonction des exigences techniques formelles des clients ; les critères d'acceptation et de rejet sont définis par un accord entre le fournisseur fondeur et le client avant la production. Ces critères affectent à la fois le coût de la fonderie et les processus de production utilisés.
5. Essais et inspection
Après la production, toutes les pièces moulées doivent être testées pour s'assurer qu'elles répondent aux exigences des spécifications. Les pièces moulées sont également inspectées pour la précision dimensionnelle, l'état de la finition de surface, les propriétés physiques, la solidité interne et les fissures. Dans de nombreuses applications, les tests sont obligatoires; des tests supplémentaires pourraient être nécessaires pour s'assurer que les spécifications des matériaux ou d'autres exigences générales sont respectées.
Les critères de test et d'acceptation doivent être clairement communiqués et convenus avant la production. Des conditions de test plus rigoureuses augmenteront le coût global. Pour rester rentables, les conditions de test et d'acceptation doivent être basées sur les exigences précises de chaque application.
Il existe deux types de tests utilisés pour inspecter les pièces moulées :les tests destructifs et les tests non destructifs.
Tests destructifs
Les essais destructifs nécessitent un moulage d'essai séparé à couler en plus de la pièce requise. Le moulage d'essai est ensuite soumis à une destruction pour déterminer visuellement la solidité interne (volume d'inclusions, retrait ou présence de gaz). Les tests destructifs indiquent uniquement l'état de la pièce testée et ne garantissent pas que les autres pièces non testées seront saines, mais ils sont largement utilisés dans la pratique. Si le moulage d'essai est acceptable, la production peut se poursuivre en supposant que les moulages produits de la même manière présenteront le même niveau de solidité.
Tests non destructifs
Des méthodes de test non destructives sont utilisées sur le moulage lui-même pour vérifier la solidité interne et externe sans endommager le produit. Les méthodes comprennent l'inspection visuelle, l'inspection dimensionnelle, l'inspection par ressuage liquide (LPI), l'inspection par particules magnétiques (MPI), les tests par ultrasons (UT) et l'inspection radiographique (rayons X).
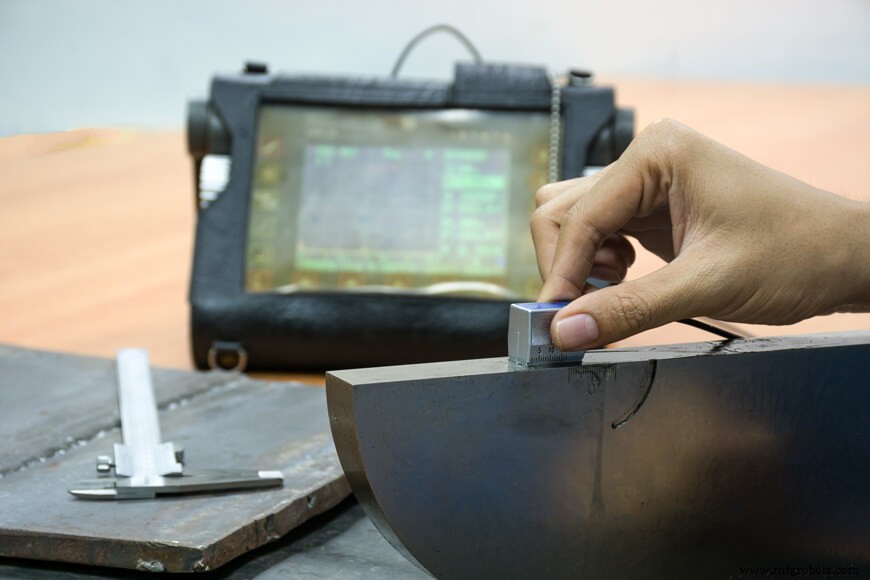
Une fois les inspections terminées, les pièces moulées inspectées et acceptées sont parfois utilisées telles quelles et expédiées aux clients, mais le plus souvent, elles sont soumises à un traitement ultérieur. Cela peut inclure le traitement thermique spécialisé, la peinture, les huiles antirouille, d'autres traitements de surface (tels que la galvanisation à chaud) et l'usinage.
6. Poids
Un élément de coût important pour tout moulage est le matériau. Plus le poids de la pièce moulée est élevé, plus le coût du matériau sera élevé pour ladite pièce moulée. Plus les données de poids fournies à une fonderie concernant les pièces en question sont détaillées, plus les calculs de prix peuvent être précis et fiables.
Les fonderies ne sont pas seulement préoccupées par le poids net (résultant) d'une pièce coulée; ils sont surtout préoccupés par le poids brut de la coulée. Le poids brut est mesuré par le poids de métal en fusion nécessaire pour remplir un moule composé de la coulée résultante et de tous les matériaux d'alimentation (portes, colonnes montantes, etc.) nécessaires pour garantir une coulée solide résultant du processus de coulée. Le prix de coulée d'une fonderie sera considérablement affecté par le rendement de coulée (l'efficacité du processus de coulée et le poids de la coulée résultante divisé par le poids du métal d'alimentation versé dans le moule) qu'ils obtiennent.
7. Motifs
Les modèles sont nécessaires pour fabriquer des moules, et la fabrication de modèles est le processus et le métier pour produire des modèles. Étant donné que les modèles sont les formes des moulages, le moulage ne peut être meilleur que les modèles à partir desquels il est fabriqué. Lorsque des tolérances étroites ou des finitions de moulage lisses sont souhaitées, il est particulièrement important que les modèles soient soigneusement conçus, construits et finis.
La conception des équipements de modèle et les coûts qui en résultent peuvent constituer une source majeure d'incompréhension entre le client et le fournisseur fondeur. La nécessité de construire un nouvel équipement de modèle pour s'adapter aux machines de production d'une fonderie même si un équipement existant/ancien est disponible, une exigence pour une boîte à noyau divisé complète à la place d'une boîte à demi-noyau, un besoin de produire des modèles en métal au lieu de modèles en bois , et/ou les besoins de modèles montés plutôt que l'utilisation de modèles lâches ne sont que quelques-uns des nombreux domaines de discussion qui affectent le coût de l'équipement. Invariablement, le coût de moulage le plus bas et la qualité de moulage la plus élevée découlent de l'équipement de modèle plus sophistiqué, qui génère le coût de modèle le plus élevé.
8. Usinage
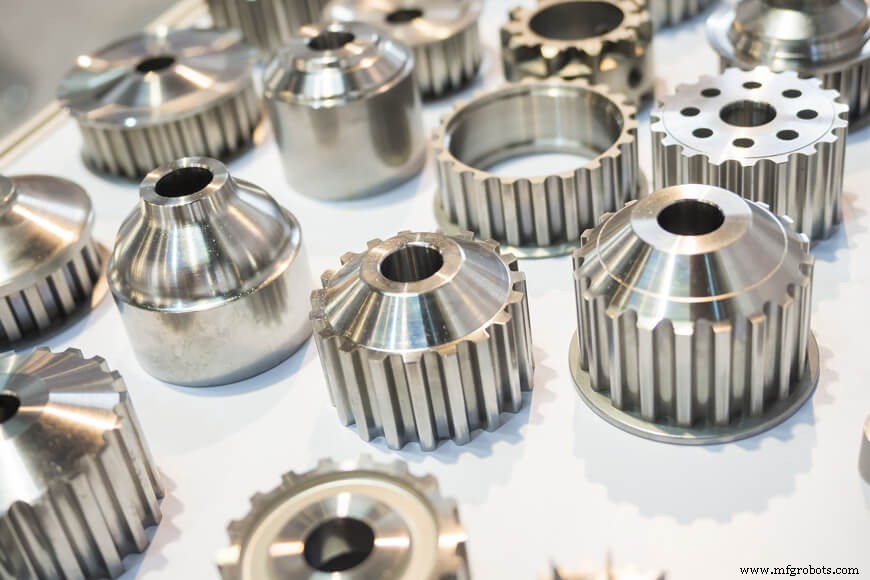
Le processus d'élimination mécanique du matériau supplémentaire inutile est appelé usinage et est un processus vital lorsqu'un niveau élevé de précision dimensionnelle est nécessaire. En tant que tel, une certaine quantité de matériau supplémentaire doit être allouée pour l'usinage en cas de besoin, en particulier lorsque la pièce ou le produit coulé a une tolérance serrée.
La tolérance fait référence à la précision dimensionnelle réalisable pour une méthode de production donnée. L'expansion du moule, le retrait de solidification et la contraction thermique influencent tous la tolérance de la pièce finie dans le processus de moulage au sable vert. Par conséquent, il existe des limites aux tolérances dans une pièce brute de coulée. L'usinage ultérieur est couramment utilisé lorsqu'une tolérance plus serrée est requise.
Toutes les fonderies de fournisseurs ne proposent pas d'usinage en interne, mais elles sont chargées de produire un produit coulé susceptible d'être transformé par usinage pour répondre aux exigences spécifiques de la pièce. Pour atteindre cet objectif, une relation étroite doit être maintenue entre le personnel d'ingénierie et d'achat du client et le producteur de moulage. Avec une approche coopérative, les points suivants doivent être pris en compte :
- Le processus de casting, ainsi que ses avantages et ses limites
- Allocation de stock d'usinage (quantité de matière restante pour la finition après l'ébauche) pour assurer le nettoyage de toutes les surfaces usinées,
- Conception du produit en relation avec l'application des dispositifs de serrage et de fixation qui fixent la pièce pendant l'usinage,
- Sélection de la spécification des matériaux et du traitement thermique, et
- Quantité de pièces à produire.
Chaque conception de fonderie lors de sa première production doit être vérifiée pour déterminer si toutes les exigences d'usinage sont réalisables. Une méthode pour y parvenir consiste à créer une disposition complète de l'échantillon coulé et à vérifier s'il existe une tolérance de stock d'usinage adéquate sur toutes les surfaces nécessitant la procédure d'usinage.
Pour les conceptions plus simples, une disposition complète du moulage peut ne pas être nécessaire. Mais dans d'autres cas où les dimensions d'usinage sont plus compliquées, il est conseillé de vérifier soigneusement la fonte. Cela peut être fait en concevant des points cibles et en traçant des lignes pour indiquer toutes les surfaces usinées, assurant la cohérence à toutes les étapes de la production.
9. Calendriers de production et de livraison
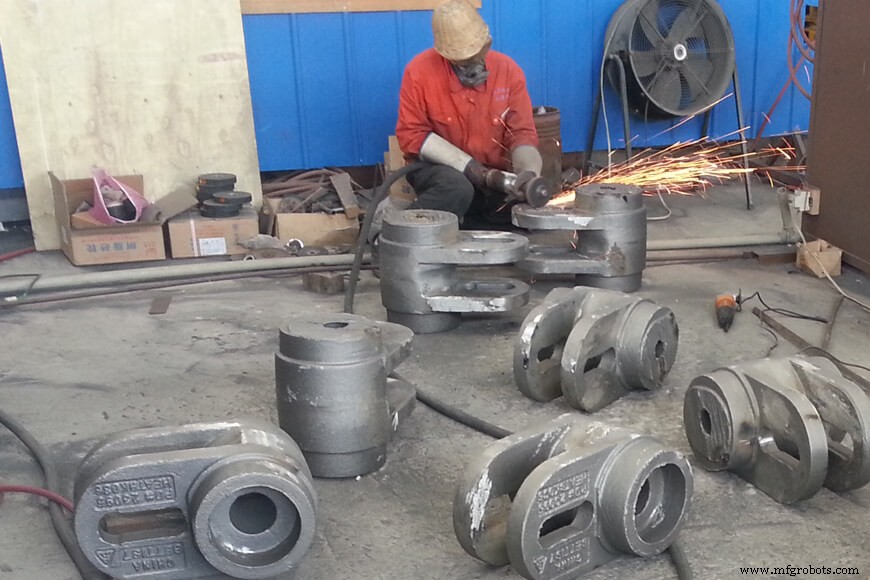
La communication des exigences de livraison et de la demande est essentielle pour trouver le bon magasin pour répondre aux besoins à court et à long terme.
En plus de toutes les autres considérations ci-dessus, il est impératif que les clients et les fournisseurs soient conscients des besoins du calendrier de production. Par exemple, si un client exige la livraison de pièces de production en six semaines, cela limiterait considérablement le nombre de fonderies désireuses ou capables de proposer un devis pour un tel travail, sans parler d'une production fiable dans un délai aussi serré. À l'inverse, si un client recherche des fonderies intéressées pour revoir leurs besoins détaillés à long terme (par exemple, 600 pièces par an de la pièce "x", produites en lots de 150 pièces par commande, avec des cycles de production initiaux nécessaires au plus tôt dans six mois), ils trouveront alors de nombreuses autres parties intéressées et capables de répondre à leurs besoins.
Une demande de devis doit être faite bien avant la date de livraison souhaitée. En raison de la complexité du processus de coulée de métal, les délais de réalisation des projets peuvent facilement atteindre 24 semaines avant la production complète et la livraison une fois les pièces moulées commandées. Ce temps peut inclure des considérations commerciales (administration financière), la construction de modèles et d'outils, l'échantillonnage, les inspections, les modifications de modèles, la configuration (complète) de la production, la production, les processus de post-production, etc.
Commander des moulages
Un effort de coopération est essentiel à la réussite de l'externalisation d'un projet de fonderie de métal :la fonderie du fournisseur doit être impliquée dès les premières étapes de la conception jusqu'à la fabrication et la livraison du produit.
Une fois que la fonderie du fournisseur a examiné une demande de devis, elle travaille avec les clients pour évaluer tous les coûts et déterminer les objectifs du produit. Une bonne planification est payante à la fois pour la fonderie et pour le client, car les experts en fonderie évaluent le projet avant la production et recommanderont les meilleurs matériaux et méthodes pour obtenir la solution la plus économique.
En fournissant aux fonderies les informations les plus précises et les plus détaillées possibles sur leurs besoins en matière de moulage, les clients peuvent s'attendre à recevoir de nombreux commentaires, questions et, une fois les détails confirmés, les prix des parties intéressées. Une bonne préparation rationalise le processus de commande, ce qui permet de gagner du temps et de réduire la probabilité d'erreurs de produit.
Processus de fabrication
- Coulage au sable :processus et caractéristiques | Secteurs | Métallurgie
- Qu'est-ce que la coulée de métal ? - Définition, types et processus
- Définition, types et procédés de coulée de métal
- Coule rapide des métaux :avantages et applications
- Guide de moulage de précision
- Guide des jauges et des conversions de tôle
- Création d'alliages personnalisés à partir de rebuts et de restes
- Scie à ruban et productivité
- Qu'est-ce que la coulée de métal à la cire perdue?