Noyautage en fonderie
Les noyaux supportent la complexité du moulage au sable
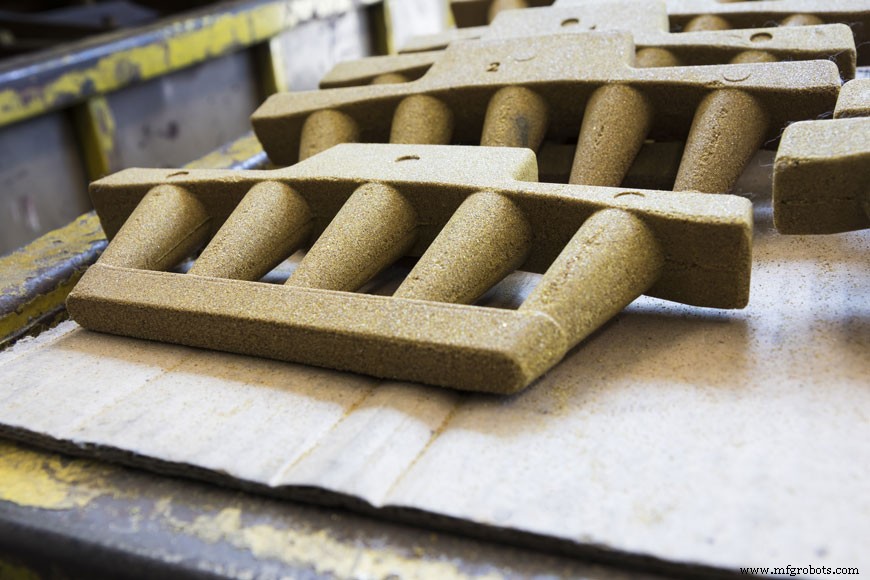
Qu'est-ce qu'un noyau dans la coulée de métal ?
Un noyau est un insert en sable ou en métal utilisé pour façonner toute partie d'une pièce moulée qui ne peut pas être façonnée par le modèle amovible principal. Lorsqu'un motif est pressé dans du sable puis extrait, il laisse une impression concave. Le métal liquide remplit ce vide et se refroidit. Des noyaux sont créés pour permettre plus de complexité dans la conception. Des noyaux bien construits créent des trous ou des chambres dans un moulage. Les moules de moteurs automobiles peuvent contenir jusqu'à cinq noyaux pour créer les chambres nécessaires au fonctionnement d'un moteur à combustion.
Les noyaux peuvent également aider à créer des angles qui seraient impossibles avec un motif. Tout surplomb au-dessus d'un espace vide rendrait impossible le retrait du motif sans casser le surplomb. Dans ces cas, un noyau peut être utilisé.
Les moulages utilisant des noyaux internes ont généralement une ouverture dans l'enveloppe extérieure du moulage pour extraire le noyau après le moulage, bien que cette ouverture puisse être bouchée mécaniquement pendant la finition.
Les noyaux faits de sable sont conçus pour se décomposer; les noyaux internes sont littéralement secoués hors du moulage à la fin du processus. L'ouverture de « décochage » est également utile pour le placement du noyau. Tout endroit où le noyau touche le moule est un endroit où le métal en fusion ne peut pas s'écouler, donc pour obtenir une épaisseur de métal constante, un noyau doit « combler » l'espace à remplir sans toucher aucun côté. Pour ce faire, le noyau est normalement plus long que le moulage et maintenu en place par des divots dans le sable à l'extérieur du modèle de moulage.
Chapelets pour le support de base
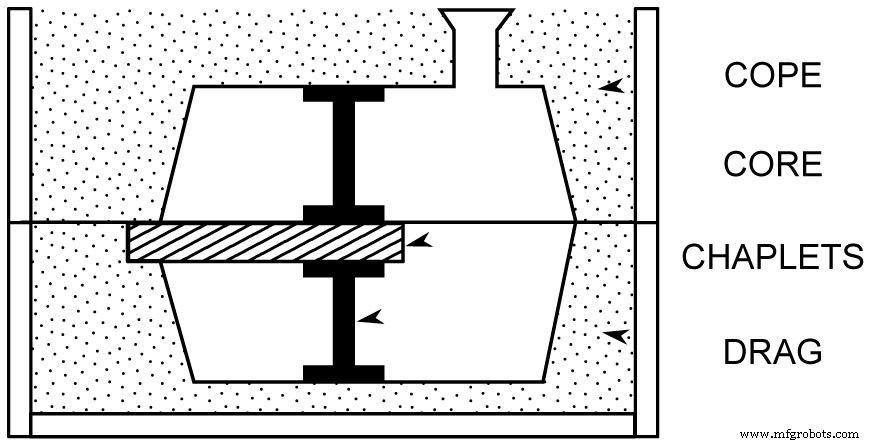
Si le noyau est très long ou si un seul bord peut dépasser du moule, alors les chapelets sont utilisés pour aider à ancrer le noyau en place. Les chapelets sont souvent faits du même métal que le moulage, car une partie du métal du chapelet sera incorporée dans le moulage lui-même. Pour se lier solidement avec le reste du moulage, la surface du chapelet doit fondre, mais d'abord, il doit faire le travail de soutien du noyau. La conception des chapelets est donc un processus métallurgique délicat à éviter dans la mesure du possible, car il y a toujours la possibilité d'introduire une faiblesse ou un défaut de moulage lors de l'utilisation d'un chapelet.
Cependant, les chapelets sont parfois le seul moyen de créer certaines structures à l'intérieur d'un moulage. Les noyaux de sable ont tendance à flotter sur le métal liquide, s'élevant parfois suffisamment pour se casser. Les chapelets placés au-dessus et en dessous peuvent aider à maintenir le noyau dans la bonne position. Le chapelet supérieur doit être le plus solide, pour contrecarrer la pression du métal et du gaz qui remontent dans le moule.
Créer du sable avec force
La tendance du noyau à flotter est l'une des raisons pour lesquelles une compréhension précise de la résistance mécanique du sable du noyau est importante. Les tests de résistance au cisaillement et à la traction effectués sur les sables à noyau sont similaires aux tests explorés dans notre article sur le sable de fonderie. Si la résistance au cisaillement du sable est inférieure à la pression créée par le métal liquide remplissant le moule, le noyau peut se fendre et créer une distorsion dans le corps de coulée.
Les liants sont une grande partie du processus de fabrication du noyau de sable. Noyaux de sable vert sont fabriqués à partir de mélanges de sable de moulage humide standard et d'un liant, comme la dextrine. Les noyaux de ce type sont très fragiles et peuvent être réalisés avec un arbre ou des fils intérieurs pour faciliter la manipulation. Noyaux de sable sec ne contiennent pas d'eau. Ils sont fabriqués à partir de sable de silice et d'un liant pour durcir la surface.
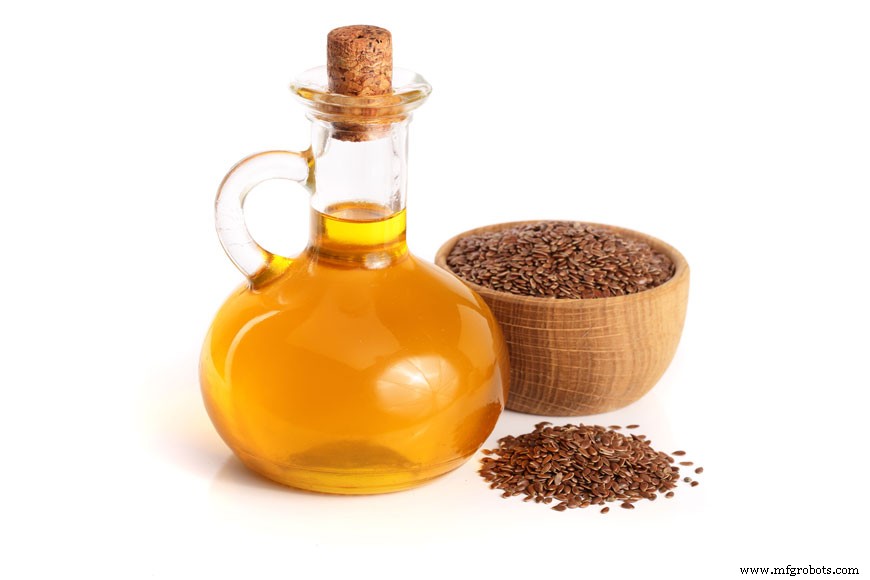
Une transition dans la technologie des liants de base s'est produite à partir des années 1980. Pendant des centaines d'années, le pétrole de base était le liant de base traditionnel - et est encore utilisé de temps en temps. De l'huile de lin mélangée à de plus petites quantités de résine et à un diluant, tel que du kérosène de haute qualité, serait ajoutée au sable de fonderie sec pour créer du sable à noyau. Des additifs comme la farine de maïs, la dextrine, les sous-produits de papeterie ou les liants protéiques peuvent être ajoutés pour renforcer le noyau. Ceux-ci brûlaient généralement à la chaleur élevée de la coulée, permettant au noyau de s'effondrer et d'être facilement secoué. D'autres liants traditionnels comprenaient le braix de goudron de houille et le brai de pétrole, particulièrement stable pour les gros noyaux. Bois et colophane était également traditionnellement utilisé pour améliorer la capacité d'écrasement du noyau, bien que ces colophanes aient tendance à durcir sous l'effet de la chaleur et de l'humidité. Beaucoup de ces composés traditionnels ont été remplacés par des options synthétiques, de sorte que les caractéristiques souhaitables sont conservées mais les défis supprimés.
Les fonderies modernes ont donc des processus de fabrication de noyaux plus propres qui favorisent une meilleure qualité de l'air et sont plus faciles à mettre en œuvre sur le sol de la fonderie. Ces noyaux synthétiques "à prise chimique" offrent plusieurs avantages, notamment une cuisson à basse température, un effondrement facile pendant le décochage et moins de dégagement gazeux pendant le processus de fabrication du noyau.
Aujourd'hui, les liants de base les plus couramment utilisés sont les plastiques de l'urée - et phénol-formaldéhyde groupes et résines de furane . Il existe trois catégories de processus de liant résine : la prise à froid , boîte froide/durci au gaz , et durcissement à chaud méthodes.
Mise à froid les processus commencent à durcir après que le dernier additif a été mélangé au sable, comme le fait le ciment. Ce sont des processus chimiquement auto-durcissants. Des exemples courants sont les résines de furane et les résines de phénol-formaldéhyde qui sont catalysées par un acide. Ils commencent à durcir après avoir mélangé de l'acide sulfonique dans le sable. Le timing est important pour ces processus - le sable ne peut pas durcir si lentement qu'il interfère avec la production, ni si rapidement qu'il est difficile de gérer la réaction.
Procédés en boîte froide ou durcis au gaz introduire dans la boîte à noyau un gaz qui réagit chimiquement pour durcir le liant du noyau. Par exemple, les sables enrichis en résines furaniques ou en époxy peuvent être durcis en introduisant du SO2 . Le verre soluble, ou silicate de sodium, peut être durci à l'aide du CO2 processus.
Durcissement à chaud les méthodes reposent sur l'introduction de chaleur pour fixer les sables à noyau. Huile de graines de lin , le liant à noyau traditionnel, est fixé avec un processus de durcissement à chaud. Dans le processus shell , la fonderie n'a pas besoin de faire de la chimie :le sable est prémélangé ou enrobé par le distributeur et les produits chimiques contenus dans le sable créent une coque dure lors de la cuisson. Habituellement, ceux-ci n'ont pas besoin de guérir complètement. Boîte chaude et boîte chauffante les méthodes utilisent des résines furanniques ou phénoliques et un catalyseur acide-sel qui durcit lorsque la boîte à noyau est chauffée. (Ils ne diffèrent que par le type de résine et la température nécessaires à la prise.)
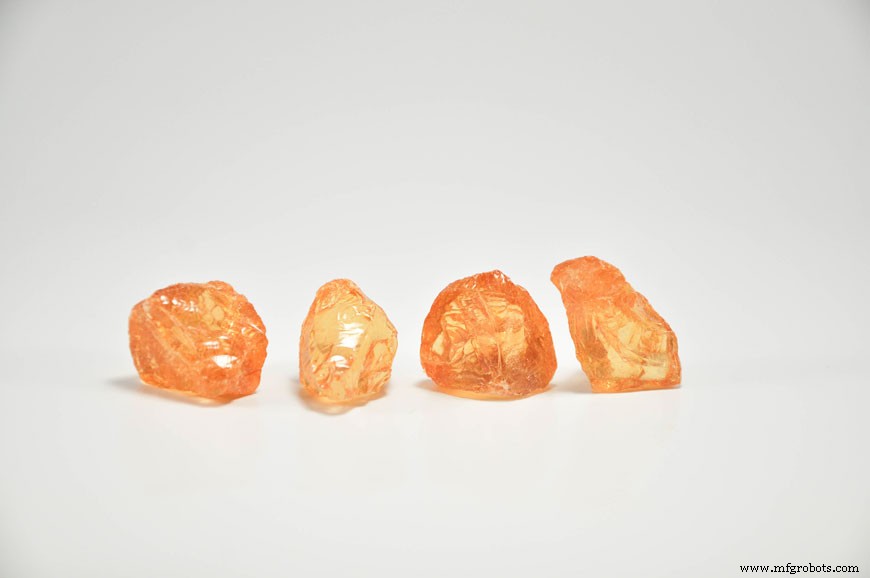
Méthodes de fabrication de noyaux
Les noyaux sont fabriqués par bon nombre des mêmes méthodes que celles utilisées pour les moules en sable. De plus, les soufflantes de base et machines d'alimentation à vis sont utilisés.
Souffleurs de carottes forcer le sable dans la boîte à carottes avec de l'air comprimé à environ 100 lb/in 2 . Ils peuvent être utilisés pour fabriquer tous types de noyaux de petites et moyennes dimensions. Les noyaux produits sont très uniformes et des taux de production élevés sont atteints.
Avance par vis les machines sont utilisées pour extruder des noyaux lisses, généralement cylindriques. Le sable de noyau est poussé à travers une matrice sur une plaque de noyau. L'utilisation de ces machines est limitée à la production de noyaux de stock :le long cylindre extrudé créé par la machine est cuit puis coupé aux longueurs souhaitées.
Séchoirs à noyau sont comme des moules à gâteaux en ce sens qu'ils supportent la forme d'un cœur lorsqu'il est dans le four à cœur pâtisserie. Il s'agit généralement de boîtes légères en fer ou en aluminium, dont la forme interne épouse étroitement la partie de chape du noyau. Les noyaux qui s'effriteraient ou dont des parties se détacheraient lorsqu'ils seraient placés sur une assiette plate passeraient au four dans un séchoir à noyaux.
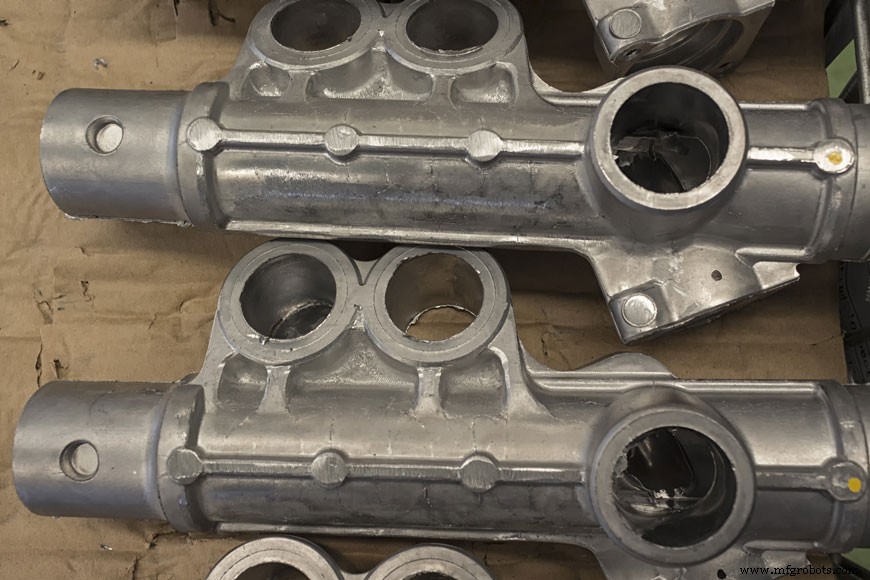
Placer le noyau
Une fois qu'un noyau a fini de durcir, il sera souvent fini à la main. Le long des lignes de séparation de la boîte à noyaux, il peut y avoir des "ailettes" à limer. Parfois, les noyaux sont fabriqués en plusieurs parties, si la forme nécessaire est plus grande que les boîtes à noyaux et les fours à portée de main. Un noyau segmenté est assemblé après l'étape de durcissement. Lorsque les noyaux sont lisses et joints, ils sont placés dans des racks en attendant d'être utilisés dans le moule.
Les noyaux sont presque toujours placés avec soin par les fondeurs plutôt qu'insérés par une machine. Les chapelets, s'il y en a, descendent d'abord dans la traînée, puis le noyau est placé. L'ouvrier fondeur s'assure que le noyau repose correctement dans le moule et qu'il est exempt de défauts. Tous les chapelets nécessaires sont placés sur la chape, et quand tout semble bon, la chape est placée sur la traînée et serrée.
Les noyaux créent de la flexibilité dans le moulage au sable
La capacité de fabriquer et de placer des noyaux de sable est un élément essentiel du processus de coulée.
Dans certains cas, le noyau est nécessaire à l'utilité de la pièce finale :les tubes, les moteurs et autres dispositifs mécaniques doivent souvent être creux pour fonctionner. Pour les articles de décoration, les noyaux peuvent également réduire le coût total du métal. Surtout lors de la coulée en fonte, les noyaux peuvent réduire considérablement le poids d'un produit final. Lorsque la résistance mécanique de l'acier massif est nécessaire, cela peut être inapproprié. Dans d'autres circonstances, cependant, un noyau est une bonne considération de conception, même s'il n'est pas nécessaire au fonctionnement du produit.
Post précédent :Sable de fonderieProcédé de coulée de métalProchain post :Fusion et coulée
Processus de fabrication
- L'importance des compétences de base
- Les bases de la stratification du noyau de stator dans votre équipement
- Systèmes cyber-physiques :le cœur de l'industrie 4.0
- Quels sont les différents types de sable de sablage ?
- Applications de moulage au sable pour le marché de l'équipement lourd
- Moulage au sable et moulage sous pression :quelles sont les différences ?
- Applications de moulage au sable pour le marché automobile
- Quand choisir le processus de moulage au sable de résine
- Comprendre le fonctionnement d'un radiateur de chauffage