Fabrication additive avec impression 3D industrielle :stratégies de réussite du post-traitement
Les pièces fabriquées de manière additive (AM) sont rarement complètes lorsqu'elles sortent du lit d'impression ou quittent la chambre de fabrication. Voici cinq stratégies pour les rendre fonctionnels, esthétiques et plus précis.
Malgré tous les efforts des fabricants d'imprimantes 3D industrielles, les pièces en plastique ou en métal sortant de leurs machines nécessitent généralement un travail supplémentaire avant d'être considérées comme terminées.
Cette étape de la production de pièces finies est connue sous le nom de post-traitement, et c'est un mal nécessaire dans le monde de la fabrication additive.
Il comprend l'usinage, le traitement thermique, le meulage et d'autres processus abrasifs. Cela implique également des opérations de finition telles que la peinture et le placage, et des technologies plus ésotériques que nous aborderons plus en détail.
Des couches, des supports et de la précision
Il existe de nombreuses raisons de post-traiter des pièces imprimées en 3D.
Pour commencer, la plupart de ces pièces sont construites à partir de fines couches de métal, de plastique ou de matériaux composites. Et à l'instar des bords d'un livre de poche, les surfaces d'une pièce imprimée présentent un aspect nettement en escalier qui, en fonction de son application et des exigences esthétiques, doit être rendu lisse avant utilisation.
L'élimination des surfaces rugueuses aide également à éliminer les élévateurs de contraintes qui peuvent entraîner des fissures, une considération importante pour les pièces porteuses.
La plupart des pièces imprimées en 3D nécessitent des supports temporaires pendant le processus de construction. Ces structures en forme d'échafaudage aident à empêcher les couches et les sections de s'enrouler vers le haut ou de s'affaisser vers le bas (selon le processus AM), et elles réduisent au minimum le gauchissement induit par la chaleur. Une fois la pièce terminée, ces structures de support doivent être retirées, généralement par des moyens mécaniques ou abrasifs. Comme vous le verrez, cependant, un bain chaud suffit parfois.
Le dernier, mais non le moindre, est la précision de la partie. Indépendamment de son immense liberté de conception et des opportunités qu'elle présente pour des pièces solides mais légères, l'impression 3D n'est pas encore très précise, du moins selon les normes de fabrication conventionnelles. Il y a la rugosité de surface déjà décrite, ainsi que la planéité, la rondeur et tout le reste. En conséquence, les trous doivent être alésés ou percés, les tourillons tournés droit, les surfaces de montage fraisées à plat. C'est pourquoi de nombreuses pièces imprimées en 3D, et certainement celles en métal, se rendent à l'atelier d'usinage après l'impression.
Stratégies pour réussir le post-traitement de l'impression 3D
Heureusement, un certain nombre d'équipementiers, ainsi que les fabricants d'imprimantes 3D eux-mêmes, prennent des mesures pour remédier à ces lacunes de la FA.
Ce travail deviendra encore plus important à mesure que les quantités de production augmentent et que l'additif évolue vers un processus courant. Bien que les processus secondaires ne disparaissent jamais (un fait dont les fabricants soustractifs sont également conscients), ces entreprises faciliteront au moins la vie de ceux qui impriment des pièces pour gagner leur vie.
Bernie Kerschbaum est le PDG de l'une de ces sociétés :Rosler Metal Finishing USA, basée à Battle Creek, dans le Michigan. Kerschbaum suggère aux concepteurs et aux fabricants de produits de faire leurs devoirs en ce qui concerne le post-traitement des pièces imprimées en 3D, de préférence bien avant le début de l'impression.
"Personne n'offre une technologie de finition unique, et bien souvent, il ne s'agit pas non plus d'un processus unique", déclare Kerschbaum.
Il donne l'exemple d'un prototype imprimé en 3D d'une bouteille de shampoing avec laquelle il a aidé un grand client de produits de consommation il y a quelques années, qui nécessitait une finition vibratoire approfondie pour obtenir le même aspect et la même sensation que son homologue de production en plastique moulé par injection. D'autres pièces nécessitent un sablage humide ou sec pour niveler les surfaces rugueuses, tandis que certaines nécessitent plusieurs opérations de finition pour atteindre le lissé souhaité. La coloration avec un colorant ou une peinture est également assez courante, tout comme le polissage, le meulage de surface et l'application de revêtements protecteurs.
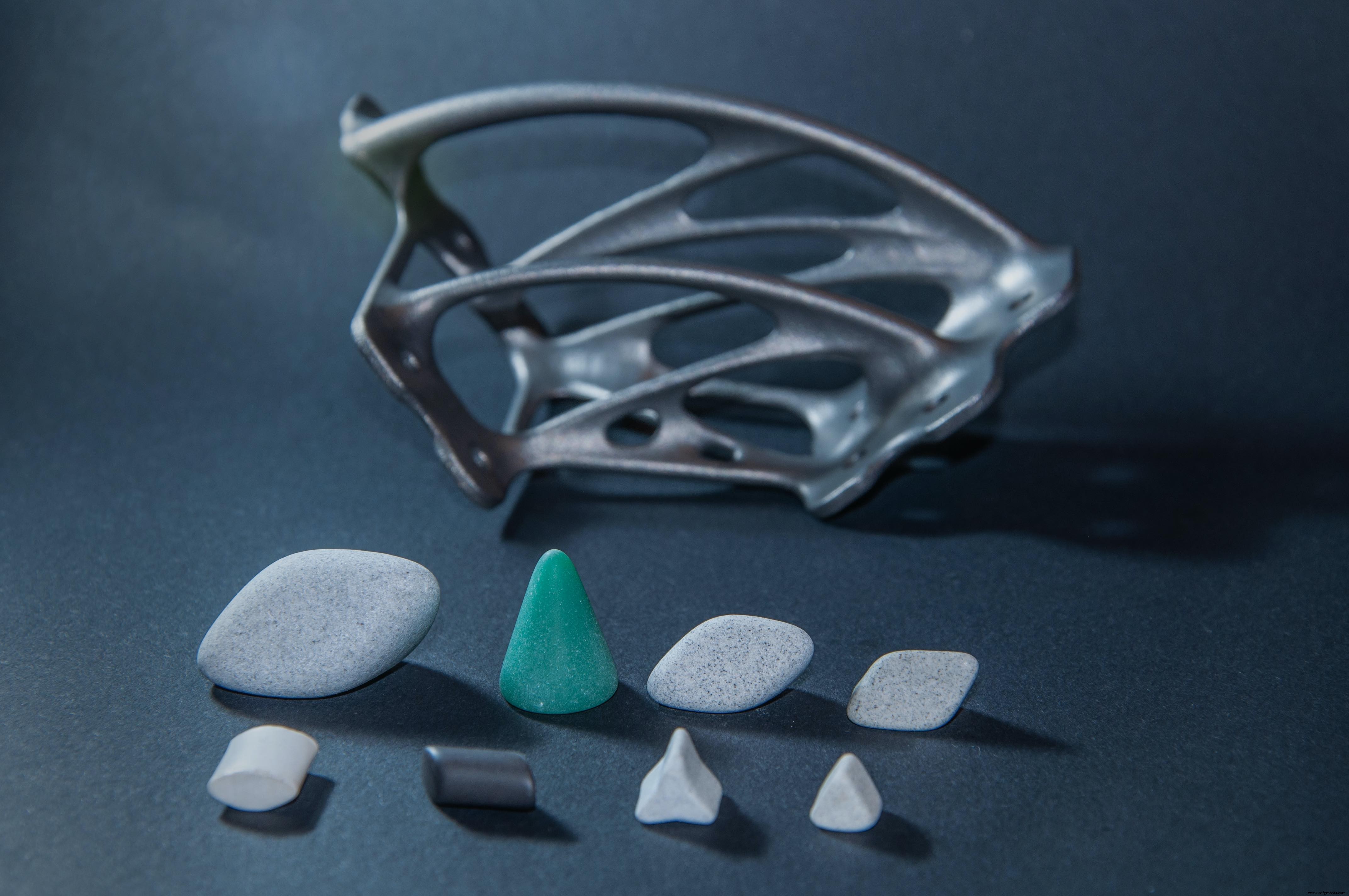
Kerschbaum poursuit en énumérant les différentes étapes nécessaires avant que ces opérations et d'autres opérations de post-traitement puissent être effectuées.
Celles-ci incluent le déballage des pièces du « gâteau » dans le cas des imprimantes à jet de liant et à lit de poudre. Il y a l'élimination des structures de support et de la poudre libre ou frittée des surfaces des composants, ainsi que le lissage et le nettoyage des passages internes. Si les quantités le justifient, chacune de ces opérations peut être réalisée de manière automatisée à l'aide d'un des différents systèmes de production de la marque AM Solutions de l'entreprise, ou à l'ancienne :ponçage fastidieux, lissage et polissage à la main.
"Souvent, vous commencez avec une finition de surface assez rugueuse, mais selon les besoins du client, nous sommes en mesure de réduire cela à un Ra dans les adolescents bas ou même à un chiffre sans trop de difficulté", déclare Kerschbaum. "Le grenaillage et la finition de masse se sont avérés être des processus très efficaces et économiques pour les pièces fabriquées de manière additive."
Pour le post-traitement des pièces en polymère, Luis Folgar, vice-président exécutif d'Additive Manufacturing Technologies (AMT) Inc. de Cedar Park, Texas, propose une alternative :l'un des systèmes automatisés PostPro 3D et PostPro SF50 de sa société.
Les deux utilisent une vapeur chimique exclusive qui est "sûre à utiliser, relativement peu coûteuse et surtout durable" pour lisser la surface des pièces imprimées avec des technologies à base de lit de poudre, de fusion à jets multiples et d'extrusion.
Les polymères candidats comprennent le nylon, l'ABS (acrylonitrile butadiène styrène), le PC (polycarbonate), le polypropylène, le TPU (polyuréthane thermoplastique) et le TPE (élastomère thermoplastique), l'Ultem et les matériaux chargés de verre ou de carbone, "avec PEEK (polyéther éther cétone) et PAEK (polyaryléthercétone) bientôt en ligne », déclare Folgar.
Des finitions de surface de pièces jusqu'à 1 μm Ra (40 μin Ra) sont possibles, ajoute-t-il, avec une dégradation dimensionnelle ne dépassant pas 0,4 %, une porosité et des fissures de surface réduites et des caractéristiques de couleur améliorées dans la pièce finie. Comme Rosler et d'autres fournisseurs, AMT propose également des systèmes automatisés de dépoudrage et de grenaillage.
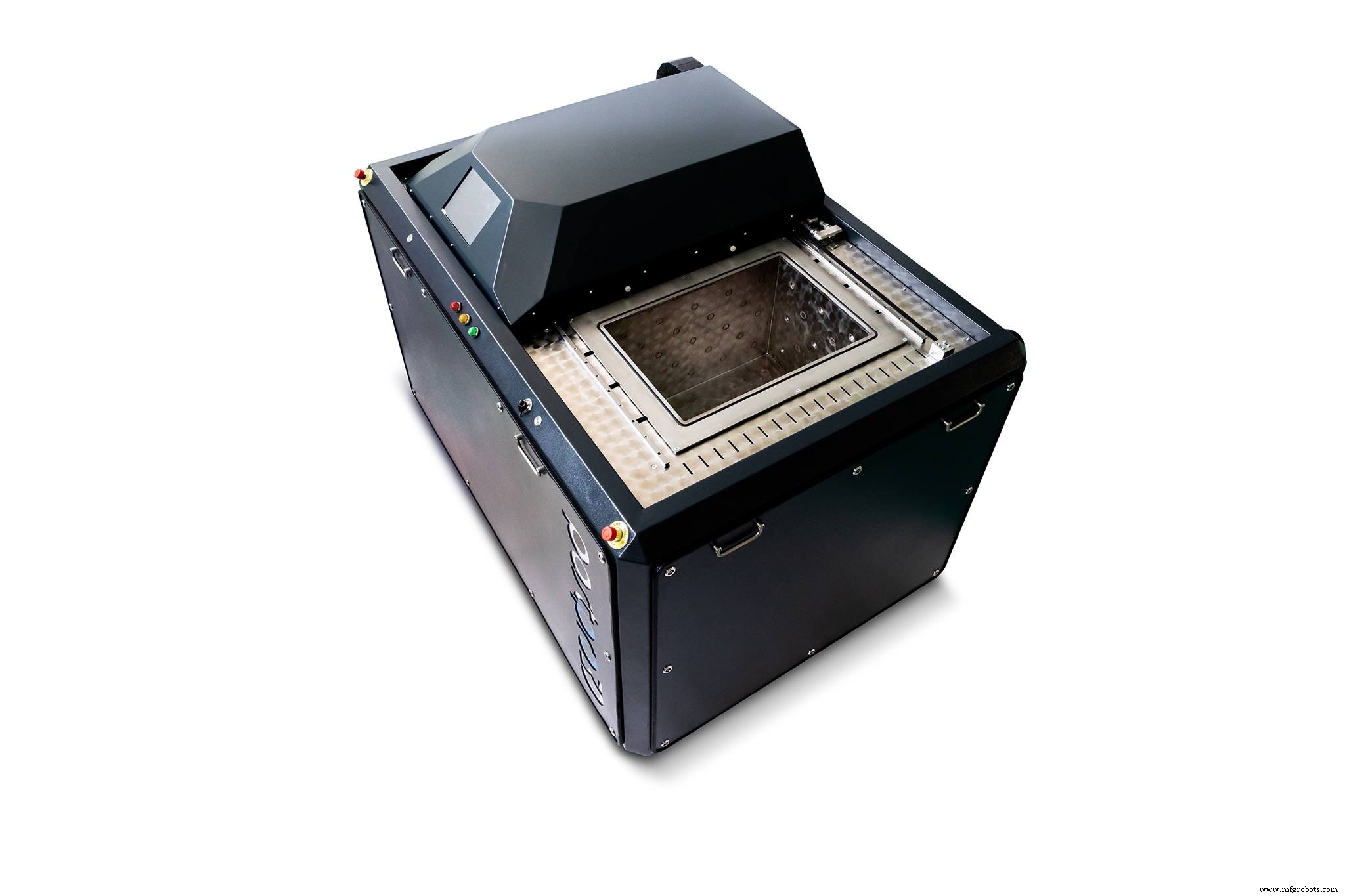
Felipe Castañeda est designer industriel et directeur créatif pour MakerBot à Brooklyn, New York, une filiale de Stratasys. Il note que, pour les pièces fabriquées avec FFF (fabrication de filaments fondus), l'un des moyens les plus efficaces d'éliminer les structures de support après l'impression consiste à utiliser des matériaux solubles.
Le premier d'entre eux est le PVA (alcool polyvinylique), un polymère doux et biodégradable qui fond lorsqu'il est exposé à l'eau chaude du robinet. Il suffit de déposer les pièces finies dedans, de les remuer pendant quelques minutes et d'obtenir une pièce sans support. Cela fonctionne bien pour les matériaux plus souples tels que le PLA (acide polylactique) et le PETG (polyéthylène téréphtalate glycol), mais pour les "polymères plus complexes" comme l'ABS, MakerBot prend en charge l'utilisation du SR-30 de Stratasys.
Comme pour le PVA, il se dissout dans l'eau, mais nécessite une petite quantité de NaOH (soude caustique ou lessive) et des températures légèrement plus élevées. Chacun de ces éléments est appliqué pendant le processus d'impression, la tête de dépôt basculant automatiquement entre la pièce et le matériau de support selon les besoins.
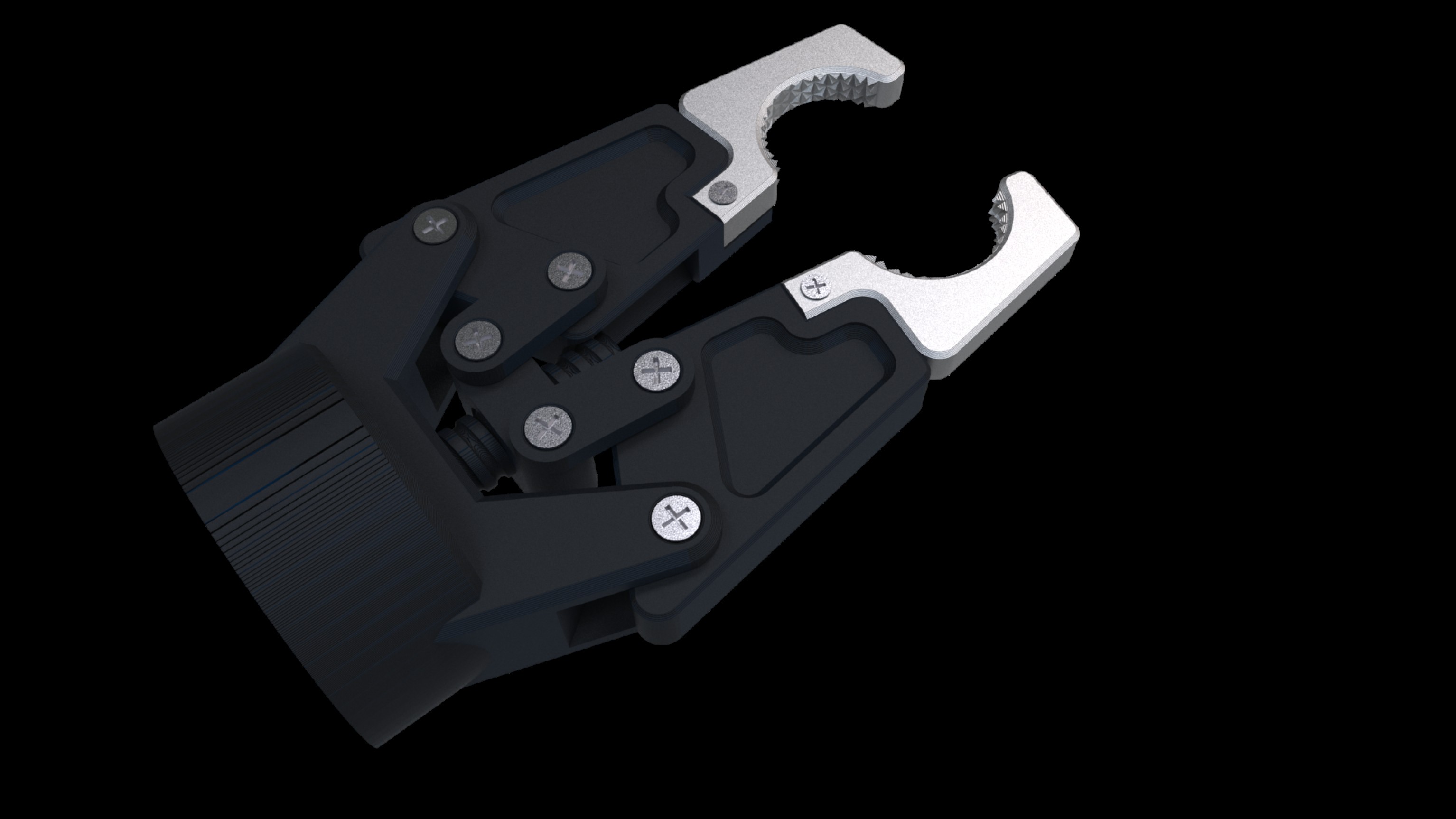
La beauté de ces matériaux solubles et d'autres est la capacité de créer des structures de support pour des pièces complexes et en particulier des géométries internes qui seraient autrement assez difficiles à enlever par des moyens mécaniques.
Une autre option est l'impression de supports dits détachables. Ici, la part du lion du support est imprimée à partir du même matériau que la pièce, le PVA ou le SR-30 n'étant appliqué que là où la pièce et ses supports se rejoignent. Le processus de retrait est le même, mais comme la tête d'impression n'a pas besoin de basculer entre les matériaux aussi souvent, cela accélère le processus de construction.
"Cela raccourcit également le temps nécessaire à la dissolution, donc pour de nombreuses pièces, cela offre une approche du meilleur des deux mondes", explique Castañeda.
Comme mentionné au début, il y a aussi l'usinage, le meulage et, dans le cas des pièces métalliques, le traitement thermique à envisager, utilisé pour soulager les contraintes internes de la pièce et durcir la pièce si désiré.
Parce que les métaux utilisés dans la plupart des processus d'impression 3D sont en grande partie identiques à leurs homologues forgés ou coulés, il n'y a pas de magie impliquée ici - il suffit de scier ou de câbler la pièce sans la plaque de construction, de la serrer et de la couper.
Quelles techniques utilisez-vous pour le post-traitement des pièces fabriquées avec la fabrication additive ? Partagez vos pensées et vos idées dans les commentaires ci-dessous.
Technologie industrielle
- 8 façons dont l'impression 3D industrielle transforme la fabrication
- Post-traitement pour l'impression 3D industrielle :la voie vers l'automatisation
- Entretien d'experts :Jonathan Warbrick de Graphite Additive Manufacturing sur la réussite de l'impression 3D
- Impression du fusible 1 avec le fusible 1
- Le travail traditionnel des métaux brille toujours dans la fabrication
- La fabrication additive commence à mûrir au-delà de l'impression 3D de bureau
- Le cas de l'impression 3D dans le secteur manufacturier
- L'impact de la fabrication additive sur la production industrielle
- Stratasys :être plus durable avec l'impression 3D