Qu'est-ce que le casting ? explication détaillée | Le Poste Mécanique
Diffusion est un processus de fabrication qui est mis en œuvre depuis l'Antiquité. Jusqu'à présent, le « moulage » est le choix de nombreux fabricants comme méthode de fabrication de diverses pièces. Aujourd'hui, commençons par définir le "casting"
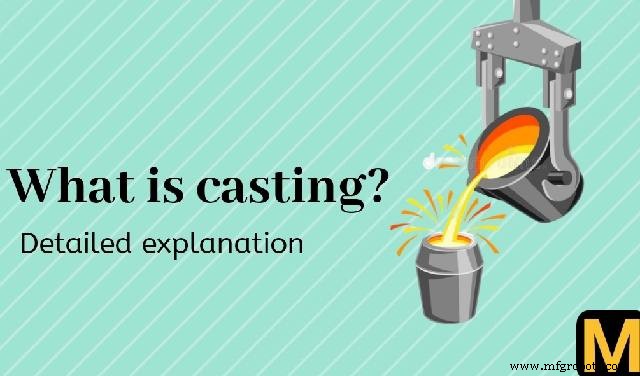
Le processus général de coulée est le suivant :
- Le métal est chauffé jusqu'à ce qu'il soit liquéfié.
- Le métal liquéfié est versé dans des moules afin de donner la forme et la taille souhaitées au métal en fusion.
- Le métal en fusion peut être refroidi et se solidifier à l'intérieur du moule.
- Après la solidification, le composant est retiré du moule, nettoyé et soumis à d'autres processus d'usinage si nécessaire.
La pièce moulée ou le composant qui est retiré lors de la solidification du moule est appelé Coulé . L'usine ou l'atelier qui fabrique des pièces moulées est appelé "Fonderie “.
Dans l'industrie, il existe principalement deux types de fonderie :
- Travail de fonderie
- Fonderie captive
1. Jobbing fonderie : Ce type de fonderie sont des centres de fabrication indépendants. Les fonderies de travail produisent des pièces moulées sur la base de contrats/commandes.
2. Fonderie captive : Ces fonderies sont en propriété exclusive. Étant donné que posséder une fonderie n'est pas bon marché, les fonderies captives appartiennent généralement à de grandes entreprises. C'est comme un département du processus de fabrication de l'entreprise. La fonderie captive produit des pièces moulées selon les besoins de la société mère.
Processus de diffusion :
Organigramme du processus de casting.
- Créez le motif. Le matériau du motif peut être :bois, métal ou plastique.
- A l'aide de patrons, préparez le moule et les noyaux nécessaires.
- Serrez correctement le moule avec les noyaux placés correctement dans la cavité du moule.
- Faire fondre le métal ou l'alliage à couler.
- Versez le métal fondu/la cavité dans la cavité du moule.
- Laissez le métal en fusion refroidir et se solidifier. Retirer le moulage du moule. Cette opération s'appelle « Secouer ».
- Nettoyez et finissez le moulage.
- Testez et inspectez le moulage.
- Supprimer les défauts s'il y en a et si possible (récupération du moulage).
- Soulager le moulage par traitement thermique.
- Inspectez à nouveau le moulage.
- Le casting est prêt à l'emploi.
Création de patrons :
Le processus de moulage commence par la création de modèles. Les modèles sont utilisés pour fabriquer des moules pour la coulée dans lesquels le métal en fusion serait versé. Les modèles sont les répliques du produit destiné à être coulé. Le motif est un peu plus grand car il comprend toutes sortes d'allocations. Certaines des allocations sont Allocation de démarque inconnue : Comme les métaux ont tendance à rétrécir lors de la solidification, le motif doit être un peu plus grand pour compenser le rétrécissement. Allocation d'usinage : L'usinage ou la finition du moulage entraîne l'enlèvement de métal, ainsi les concepteurs conçoivent le modèle de telle manière qu'après tous les processus d'usinage, le produit final ait la forme et la taille souhaitées. De même, il existe de nombreuses autres allocations incluses dans un modèle. ![]() |
Un modèle en bois d'une pièce de machine. |
Les matériaux utilisés pour la réalisation des patrons sont :
- Pour la production à petite échelle :des bois comme le pin blanc, l'acajou, l'érable, le bouleau et le cerisier sont utilisés. Le bois est utilisé dans la production à petite échelle ou lorsque moins de moulages doivent être effectués. Les modèles en bois sont légers, peu coûteux par rapport aux modèles en métal, peuvent être facilement façonnés dans la forme souhaitée. Cela fait des motifs en bois un meilleur choix. Outre le bois, le motif en plastique peut être utilisé comme alternative.
- Pour la production à grande échelle :les métaux sont utilisés pour la fabrication de modèles lorsqu'il s'agit de production à grande échelle. Ils sont plus durables que les motifs en bois et ont une durée de vie plus longue car ils peuvent résister à l'usure. D'autres avantages qui font des métaux une option appropriée sont que les métaux ne se déforment pas facilement, peuvent supporter une manipulation brutale, une résistance à l'usure, une meilleure finition de surface est possible, une résistance à la corrosion (sauf les métaux ferreux), etc. Métaux comme le laiton, l'aluminium, le métal blanc et la fonte sont préférées pour la fabrication de modèles.
Types de motifs :
- Patron une pièce
- Modèle divisé ou modèle en deux parties
- Modèle fermé
- Modèle de copie et de glissement
- Modèle de balayage
- Motif squelette
Lire aussi :
- Qu'est-ce qu'un tour
- Outils d'atelier de base que vous devez connaître
- Qu'est-ce que le soudage GTAW ou TIG ?
- L'automatisation industrielle et ses types
Moulure :
Maintenant que le patron est fait, le patron est utilisé pour en faire un moule. Comment ? Voyons voir. De tous les processus de moulage, le moulage au sable est le plus largement utilisé pour le moulage. Les moules à sable sont des moules « jetables » ou « à usage unique ». Après la coulée, le moule en sable est complètement détruit pour retirer la coulée du moule. Le sable est mélangé avec des liants et des additifs avec de l'eau pour augmenter la moulabilité du sable. Pour la préparation du moule, le matériau de moulage est contenu autour du modèle. Comme le montre la figure, la partie supérieure du moule est appelée chape et la partie inférieure est appelée traînée. Le moule est autorisé à durcir et le modèle est retiré du moule uniquement pour exposer la cavité ainsi créée pour y verser le métal en fusion. Les types de moules en sable sont :- Moule à sable vert
- Moule à sable sec
- Moules à sable limoneux
- Moules CO2, etc.
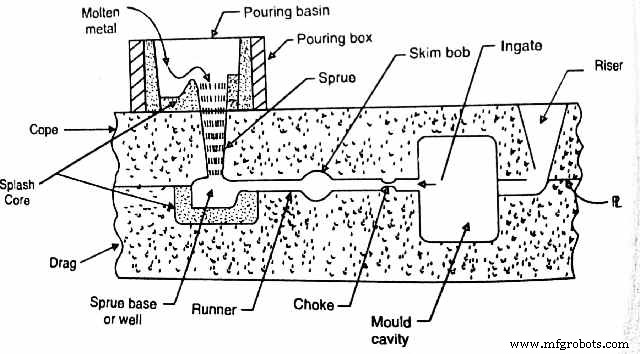
Le moule contient les éléments suivants pour une coulée réussie :
Core : Généralement fabriqué à partir de sable, de bois ou de métal, le noyau est utilisé pour faire des trous dans le moulage. Le noyau est un corps qui est placé dans la cavité du moule avant de fermer le moule et de couler le métal en fusion. Le noyau contribue ainsi à former une cavité à l'intérieur de la coulée. Bassin verseur : C'est le réservoir au sommet de la carotte (dans la chape) qui reçoit la vapeur de métal en fusion coulée de la poche. Grappe : Une carotte ou une porte vers le bas est un canal vertical qui relie le bassin de coulée aux glissières et aux portes. Il est quelque peu effilé vers le bas pour faciliter le moulage et, plus important encore, pour avoir une section transversale décroissante correspondant à l'augmentation de la vitesse du métal en fusion lorsqu'il s'écoule dans le trou de coulée. Cela empêche l'écoulement turbulent et donc l'aspiration d'air avec le liquide dans la cavité du moule. Base de carotte ou puits : C'est le réservoir à l'extrémité inférieure de la carotte. Il empêche l'érosion excessive du sable lorsque le métal en fusion frappe la glissière à la base en épicéa. De plus, il y a une perte considérable de vitesse dans le puits. Coureur : Le canal d'alimentation est généralement le canal horizontal dont les fonctions sont de piéger les scories et de relier le fond de cheminée aux portes, permettant ainsi au métal en fusion de pénétrer dans la cavité du moule. Portes : Les portes sont les canaux par lesquels le métal entrant entre directement dans la cavité du moule. Élévateurs : La colonne montante ou les têtes d'alimentation font partie du système d'alimentation. Ce sont des réservoirs de métal en fusion qui alimentent le métal dans la pièce moulée au fur et à mesure qu'elle se solidifie, pour éviter les cavités de retrait dans la pièce moulée.Si vous aimez cet article, faites-le nous savoir dans les commentaires et partagez-le avec vos amis et votre famille grâce aux liens sociaux indiqués ci-dessous.
Technologie industrielle
- Coulée en mousse perdue ou coulée en moule complet :quelle est la différence ?
- Les bases de la coulée centrifuge :ce que vous devez savoir
- Qu'est-ce que le soudage GMAW ou MIG ? – expliqué | Le Poste Mécanique
- Quels sont les principaux types de systèmes de transmission de puissance mécanique ?
- Qu'est-ce que le 5S ? Une explication des éléments des 5S pour une culture Lean
- En quoi consiste le processus de fabrication ?
- Moulage de précision et moulage sous pression :quelles sont les différences ?
- Moulage au sable et moulage sous pression :quelles sont les différences ?
- Qu'est-ce que le moulage au sable ?