Types de processus de moulage - Aperçu complet [avec images]
Dans cet article, nous discuterons du processus de moulage, des types de processus de moulage classés sur la base de divers termes tels que le moulage au sable sec, le moulage au sable vert, le moulage sur banc, etc.
Processus de moulage d'usage courant peuvent être classés selon différentes formes. Ils peuvent être classés en gros comme :
- Moulage à la main , et
- Moulage mécanique .
En pièce et en petite série, les moules en sable sont fabriqués à la main; les machines de moulage sont utilisées dans la production de gros lots et de masse.
Types de processus de moulage
Les procédés de moulage sont souvent classés selon :
(A) Le type de matériau dont le moule est fait ou
(1) Moules à sable vert,
(2) Moules à sable sec,
(3) Moules séchés à la peau,
(4) Moules à limon.
(B) Les méthodes utilisées pour fabriquer le moule.
(1) Moulure de banc,
(2) Moulure de plancher,
(3) moulage de fosse,
(4) Moulage par balayage, et
(5) Moulage de plaque.
Processus de moulage basé sur le sable utilisé
1. Moulure Sable Vert
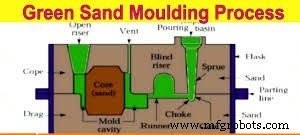
Moulure au sable vert est une méthode polyvalente, rapide et peu coûteuse de création de moules pour des pièces moulées ferreuses et non ferreuses de haute qualité. Le sable vert est composé de sable de silice, d'eau, de bentonite et d'autres additifs, tels que la poussière de charbon pour les applications de fer.
Les moules en sable vert sont préparés avec des sables de moulage naturels ou avec des mélanges de sable de silice, d'argile liante et d'eau. Ces matériaux sont soigneusement mélangés dans des proportions qui donneront les propriétés souhaitées pour la classe de travail en cours.
2. Moule à Sable Sec
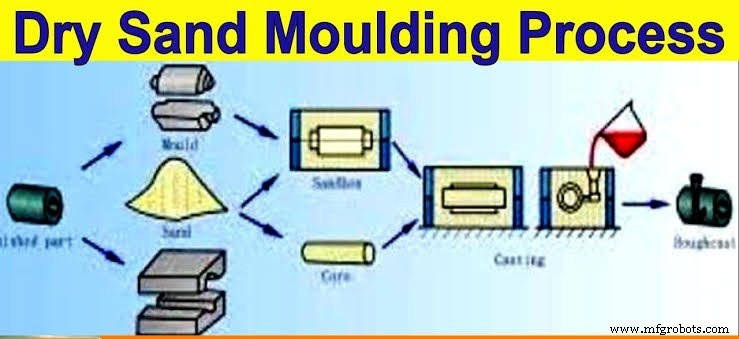
Le processus de moulage impliqué dans la fabrication de moules en sable sec sont similaires à ceux utilisés dans le moulage au sable vert, sauf qu'un mélange de sable différent est utilisé et que toutes les parties du moule sont séchées dans un four avant d'être réassemblées pour le moulage.
Le moule de sable vert dépend de l'humidité et du liant d'argile naturelle dans le sable pour conserver sa forme. Mais le sable utilisé pour les moules en sable sec dépend de l'ajout de liants tels que la farine, la résine, la mélasse ou l'argile. Les matériaux sont soigneusement mélangés et trempés avec une fine eau argileuse. La quantité de liant est déterminé par la taille du casting en cours de fabrication.
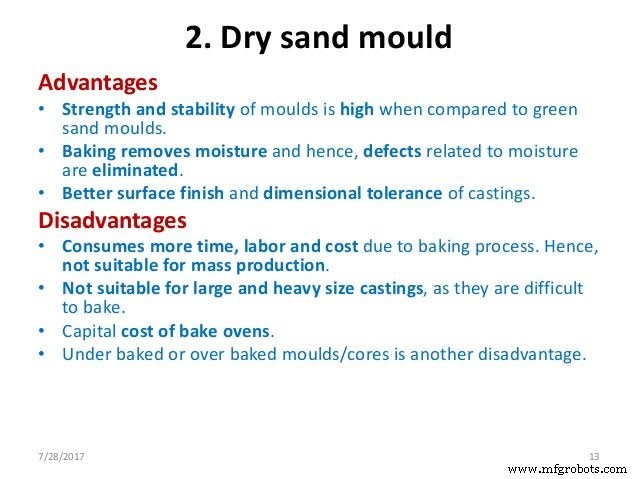
3. Moulage séché à la peau
Le processus de moulage séché à la peau est un processus qui sèche l'humidité de la couche de surface du sable damé à une profondeur d'environ 25 mm ou plus en utilisant des chalumeaux à gaz ou des appareils de chauffage. Il présente dans une certaine mesure les avantages du moulage au sable vert et au sable sec. Comme le temps nécessaire au séchage est moindre que dans le cas du sable sec, la méthode est moins coûteuse. Le skin-drying est particulièrement adapté aux moules de très grandes dimensions, ou aux travaux nécessitant des détails précis.
4. Moule à limon
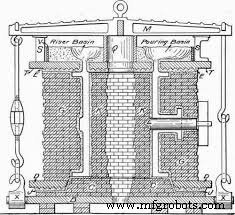
Limon est de l'argile et du sable mélangés à de l'eau pour former un mélange de plastique fin à partir duquel des moules sont fabriqués. Le sable limoneux contient également de l'argile réfractaire ou des ganisters. Le terreau doit être suffisamment adhérent pour pouvoir adhérer aux surfaces verticales. Les moules en limon nécessitent toujours des dispositions spéciales pour assurer une ventilation adéquate. Le but est d'ouvrir des pores dans la masse autrement compacte et étroitement liée, par des moyens artificiels. Ainsi diverses sortes de matières organiques telles que la paille hachée, et en particulier le fumier de cheval , est mélangé avec le sable. Un mélange typique de sable limoneux est donné ci-dessous :
Celui-ci est appliqué sous forme de plâtre sur la structure rugueuse du moule généralement en brique et la forme exacte est donnée par un balayage rotatif autour d'un axe central, comme indiqué sur la figure. Des plaques et des barres en fonte sont utilisées pour renforcer la maçonnerie qui retient le matériau de moulage. Les moules en limon peuvent également être préparés en utilisant un modèle de squelette en bois. Les surfaces des limons sont noircies et séchées avant d'être assemblées.
Les moules en limon sont principalement utilisés dans la fabrication de grandes pièces moulées pour lesquelles il serait trop coûteux d'utiliser des modèles complets et un équipement de flacon ordinaire. Des objets tels que de grands cylindres, des bouilloires à fond rond, des casseroles chimiques, de grands engrenages et d'autres pièces de machine sont produits dans des moules en limon.
Types de processus de moulage en fonction des méthodes utilisées
1. Banc et Moulure de Plancher
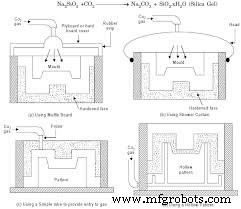
Moulure de banc s'applique principalement aux moules suffisamment petits pour être réalisés sur un établi d'une hauteur convenable au mouleur.
Les moulages très lourds ou les moulages d'une profondeur ou d'une surface considérables peuvent être moulés dans le sable du sol de la fonderie de la même manière que le moulage au sable vert ou au sable sec. Dans de tels cas, le sol lui-même agit comme une traînée, et celui-ci peut être recouvert d'une chape ou le moule peut être ouvert.
2. Moulage de la fosse
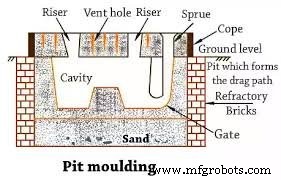
Moulage de la fosse Processus :Les moules des gros travaux sont généralement préparés dans une fosse creusée dans le sol de la fonderie, ce qui facilite le levage du modèle et la coulée du moule facilement. Étant donné qu'une fosse qui fonctionne comme une traînée ne peut pas être renversée, le sable sous le motif peut être enfoncé par rodage. Le motif peut être suspendu au bon endroit lorsque le sable est enfoncé en dessous. Dans d'autres cas, si la surface inférieure d'un motif est plate, le motif peut être placé sur une surface plane et éperonnée pour cela.
Un lit de coke est déposé au fond de la fosse, recouvert de paille puis d'une couche de sable, qui est damée et nivelée. Le lit de coke est relié à l'atmosphère par des tuyaux d'évent verticaux dans les coins de la fosse pour fournir une sortie pour les gaz générés. Si le sol est légèrement humide, les surfaces intérieures de la fosse sont tapissées de papier goudronné, de briques ou de planches de bois. Généralement, une boîte est nécessaire pour terminer le processus de moulage. Coulisses, bassins verseurs, mangeoires, y sont taillés.
3. Moulage par balayage
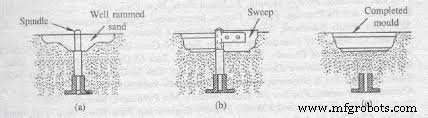
Moulures de balayage sont employés pour mouler des pièces dont la forme est celle d'une surface de révolution. Dans le processus préliminaire, une base 1 et une broche 2 sont bien placées dans le sol de la fonderie. Le sable est rempli et enfoncé jusqu'à ce que l'excavation ait approximativement la forme et la taille de la coulée requise. Ceci est illustré dans la figure a.
Un support de balai 5 est ensuite placé dans la broche et le balai 6 est fixé par des boulons et des écrous. La surface du moule est produite par le profil du balayage lors de sa rotation autour de la broche, comme illustré à la figure (b). Après le balayage, la broche est retirée et le moule rapiécé au centre. La porte est ensuite découpée et le moule est prêt à être coulé. Ceci est illustré à la figure (c).
4. Moulage de plaque
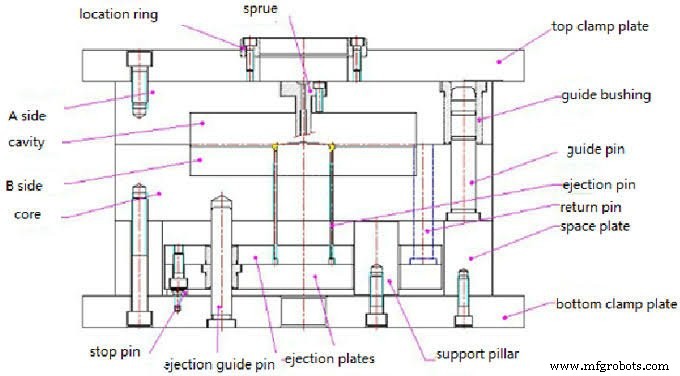
Moulage de plaque Processus :Dans ce processus de séparation monté, le motif est divisé en deux sur la séparation et en deux sur des plaques à côtés parallèles de la même forme que la figure. L'utilisation de plaques offre les avantages suivants :
- Les motifs peuvent être maniés facilement et rapidement.
- La tâche de faire le joint entre les deux parties du moule est soulagée car la plaque fournit son propre joint lorsque le flacon est enfoncé.
- Le motif peut être dessiné rapidement , car la plaque chevauche le côté de la boîte et les goupilles qui la maintiennent en position servent de guides pendant l'opération de tirage.
Quelques processus de moulage spéciaux
Ces dernières années, des procédés de moulage spéciaux ont été développés pour réaliser une économie de temps et d'argent, pour produire des moules et des noyaux de meilleure qualité et pour augmenter la productivité avec moins d'effort et de compétence. Généralement, ces procédés ne nécessitent pas dans tous les cas le séchage ou la cuisson des moules ou des noyaux, et une action de durcissement rapide se produit en raison de réactions chimiques dans ceux-ci. L'utilisation des procédés de moulage spéciaux suivants a considérablement augmenté ces dernières années.
1. Moulage au dioxyde de carbone
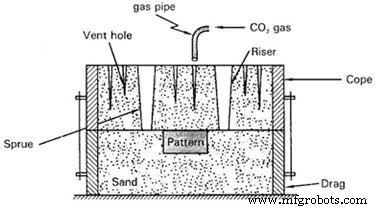
Moulage au dioxyde de carbone Processus : Le processus est essentiellement un processus de durcissement pour les moules et les noyaux. Le principe de travail du processus CO2 est basé sur le fait que si le gaz CO2 est transmis un mélange de sable contenant du silicate de sodium (verre soluble), le sable devient immédiatement extrêmement fortement lié car le silicate de sodium devient un gel rigide. Ce gel est chargé de donner la force nécessaire au moule.
2. Moulage de ferro-silicium
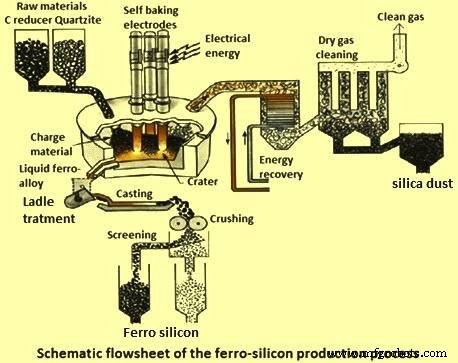
Moulage de ferro-silicium :Ce procédé de moulage est basé sur le principe que si le silicate de sodium et ferro-silicium en poudre sont mixtes dans le rapport de 2,25 :1 en poids, une action moussante a lieu et la température s'élève par réaction exothermique entre eux. A température ambiante, cette réaction se déroule lentement mais une fois la température augmentée, la réaction s'accélère. Enfin, le sable de silice forme une masse spongieuse dure. Aucune cuisson du moule ou du noyau n'est nécessaire comme dans le procédé au CO2.
Normalement, pour la fonte ferreuse propre et sable sec de 65 mesh , tandis que pour la fonte non ferreuse , sable de 100 mesh est adapté. Les moules doivent être enduits d'un badigeon adapté avant d'être fermés.
3. Moulage au silicate dicalcique
Moulage au silicate dicalcique :Ce procédé de moulage est basé sur le principe que si environ 2-3 % de silicate dicalcique , connu pour être un agent de durcissement très efficace, et 5 % de silicate de sodium sont mixtes avec du sable avec des produits chimiques moussants appropriés, la fluidité de la masse de sable augmente. En conséquence, le mélange de sable peut facilement s'écouler dans le moule, et il n'est pas nécessaire d'enfoncer comme requis dans le processus de moulage conventionnel. Enfin, le sable forme une masse dure ayant une capacité d'écrasement suffisante
Le principal avantage de ce processus de moulage est la grande économie de main-d'œuvre et équipement de moulage puisqu'aucun séchage ou support n'est nécessaire. D'autre part, des moulages de haute qualité sans défauts sont produits. Cela trouve une large application dans les pièces moulées moyennes et lourdes, à la fois dans les pièces moulées en fonte grise et en acier.
4. Moulage Ciment-Sable
Moulage Ciment-Sable :Le ciment Portland peut être utilisé comme liant pour lier les grains de sable ensemble. On a constaté qu'une bonne combinaison de résistance, de perméabilité et de fluidité est obtenue en utilisant du ciment avec du silicate de sodium. Le coulis de ciment fluide peut également être produit en utilisant des produits chimiques moussants dans le mélange de sable. L'enfoncement du sable est ainsi considérablement réduit. Cependant, une bonne liaison peut être développée dans le sable avec l'ajout d'environ 2 pour cent 2 de ciment, 4 à 5 pour cent de silicate de sodium et 1 pour cent de brai ou de mélasse.
Ces moules produisent une surface lisse et précise, mais le principal inconvénient des moules en sable lié au ciment est qu'ils sont difficiles à faire sortir du flacon.
5. Moulure de coque
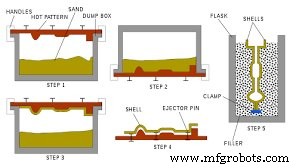
Moulure de coque :D'après le nom de son inventeur, le coquillage est aussi appelé procédé Croning ou processus C . Il s'agit d'une variante de la technique du sable lié à la résine pour la coulée d'acier, de fer ou d'alliages non ferreux.
Le moule est formé d'un mélange de sable fin (100-150 mesh) et d'un liant en résine thermodurcissable qui est placé contre un modèle métallique chauffé, de préférence en fonte grise. Lorsque le mélange est chauffé de cette manière, la résine durcit, faisant adhérer les grains de sable les uns aux autres, formant une coque solide qui se conforme exactement aux dimensions et à la forme du motif et constitue la moitié d'un moule.
Une fois que la coque a été durcie et retirée du modèle, tous les noyaux nécessaires sont fixés, les deux moitiés du moule sont fixées ensemble, placées dans un flacon et un matériau de sauvegarde est ajouté ; alors le moule est prêt à être coulé.
6. Moulage de boîtes chaudes et froides
Le processus hot-box , particulièrement adapté au noyautage, utilise essentiellement les mêmes matériaux que celui utilisé en carapace, mais ici la résine est appliquée pour enrober les grains de sable. Le mélange résine-sable est ensuite soufflé sur le modèle métallique ou la boîte à noyau chauffé à environ 200 ° à 300 °C et autorisé à former une masse solide au lieu de permettre la formation de coquille.
Des machines spéciales à boîte chaude sont maintenant disponibles où le mélange de sable est soufflé sur le modèle chauffé, le sable soufflé durci et le moule ou le noyau ensuite retiré du modèle ou de la boîte à noyau.
Une plus grande précision des dimensions et des taux de production plus élevés que dans le cas du moulage en coquille sont obtenus. Il s'agit d'un processus de moulage et de fabrication de noyaux essentiellement pour la production mécanisée de petites pièces requises en grandes quantités.
Le processus de la boîte froide consiste à mélanger du sable sec fin soit de la résine polyisocyanate classeur et résine phénolique alkyde , en soufflant le mélange dans une boîte à noyau scellée et en injectant une vapeur de triéthylamine de catalyseur en suspension dans l'air à travers la boîte à noyau. Le groupe hydroxyle de la résine phénolique liquide se combine avec le groupe isocyanate pour former une résine uréthane rigide. Les deux composants du liant sont généralement utilisés dans un rapport de 1:1 avec de 1 à 2 % en poids du mélange de résine ajouté au sable. un
Le processus présente l'avantage qu'aucun chauffage du modèle n'est nécessaire et que le durcissement a lieu en seulement 20 à 30 secondes. Il s'agit donc d'un processus de fabrication de noyaux simple et à haute production, et extrêmement adapté aux pièces moulées de petite taille requises en grandes quantités.
7. Invest Moulage
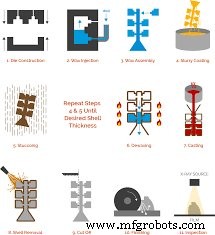
Moulage d'investissement :Ce processus de fabrication de moulage est souvent appelé "processus de cire perdue " et " processus de moulage de précision ”. Le moulage peut être réalisé avec des tolérances très étroites dans ce processus et ne nécessite pas d'usinage ultérieur.
Il se compose principalement de deux étapes qui sont représentés sur la figure. Tout d'abord, un modèle maître est fait de bois ou de métal autour duquel un moule est formé. Il n'est pas constitué de sable de moules mais de gélatine ou d'un alliage à bas point de fusion qui est coulé sur le patron. Ce moule maître se compose des deux sections habituelles et peut être ouvert. Il est utilisé pour créer le "motif perdu ".
8. Moulage en plâtre
Moulage en plâtre :Dans cette méthode, le moule est préparé en gypse ou plâtre de paris. En pratique, le plâtre de paris est mélangé avec du talc, de l'amiante, des fibres, de la farine de silice et une quantité contrôlée d'eau pour former une bouillie. Cette pâte de plâtre est coulée sur le motif métallique confiné dans un flacon.
Le moule est vibré et la bouillie est laissée durcir. Le motif est retiré après environ 30 minutes lorsque la prise est terminée et le moule est séché et renforcé en le chauffant lentement à environ 200°C dans un four à convoyeur. Les inserts et les noyaux sont placés, font face et traînent en correspondance avec des broches de guidage. Le métal en fusion est ensuite versé dans le moule. Enfin, la coulée est refroidie dans le moule, secouée et le moule est détruit. Les moulages sont ensuite débarrassés des portes, des carottes et du flash.
9. Moulage en céramique
En moulage céramique processus, une suspension épaisse, composée d'agrégats céramiques spécialement développés et d'un liant chimique liquide (ester de silicium à base d'alcool) est purée sur le modèle métallique fendu et fermé réutilisable qui est généralement monté sur une plaque d'allumette. La boue remplit toutes les cavités et les cavités par elle-même et aucun pilonnage ou vibration du moule n'est nécessaire. Le motif est retiré après avoir pris environ 3 à 5 minutes. La masse céramique est ensuite retirée du flacon, traitée avec un durcisseur pour favoriser la stabilisation chimique et chauffée à environ 980°C dans un four pour éliminer le liant liquide. Le moule est alors prêt à couler le métal en fusion.
10. Moulage par succion
Moulage par succion Processus : Dans cette méthode, un vide est créé en retirant de l'air de l'espace du moule. Ensuite, le sable de moulage est aspiré et la cavité est remplie. Le sable peut ensuite être enfoncé dans le motif. Le procédé est utilisé pour couler le fer, l'acier et l'aluminium.
Nous avons essayé de couvrir tous les points importants relatifs au processus de moulage et à ses types et classifications. J'espère que vous avez apprécié cet article. Veuillez fournir vos commentaires dans le commentaire ci-dessous.
Technologie industrielle
- MTBF :un aperçu complet
- 5 types de centres de données différents [avec exemples]
- Sable de moulage :types et constituants | Coulée | Métallurgie
- Propriétés du sable de moulage | Matériaux | Coulée | Métallurgie
- Qu'est-ce que le sable de moulage ? - Types et propriétés
- Types de sable utilisés dans le processus de moulage
- Définition, processus et types de fraiseuses
- Signification et types de processus de fabrication
- Types d'équipement de moulage au sable