Spécialiste des applications :supports imprimés en 3D
Les supports, bien que des pièces assez simples, sont un choix populaire pour l'impression 3D. D'une part, l'impression 3D permet d'optimiser le support, en aidant à améliorer les performances d'une pièce ainsi qu'une structure dans laquelle un support est utilisé.
Dans la rubrique Application Spotlight d'aujourd'hui, nous explorons les principaux avantages de l'utilisation de l'impression 3D pour les supports, ainsi que des applications passionnantes dans les secteurs de l'aérospatiale et de l'automobile.
Regardez les autres applications couvertes dans cette série :
Impression 3D pour échangeurs de chaleur
Impression 3D pour roulements
Impression 3D pour la fabrication de vélos
Impression 3D pour la dentisterie numérique et la fabrication d'aligneurs transparents
Impression 3D pour implants médicaux
Les fusées imprimées en 3D et l'avenir de la fabrication d'engins spatiaux
Impression 3D pour la fabrication de chaussures
Impression 3D pour composants électroniques
Impression 3D dans l'industrie ferroviaire
Lunettes imprimées en 3D
Impression 3D pour la production de pièces finies
Impression 3D pour pièces de turbine
Comment l'impression 3D permet des composants hydrauliques plus performants
Comment l'impression 3D soutient l'innovation dans l'industrie de l'énergie nucléaire
Qu'est-ce qu'un support ?
Une équerre est une attache, destinée à maintenir ensemble deux pièces perpendiculaires dans un assemblage et à renforcer l'angle.
Les supports maintiennent ensemble les structures tout autour de nous (pensez aux bâtiments, aux avions et aux voitures), déterminant en grande partie la force, la résilience et l'intégrité de ces structures.
Pourquoi utiliser l'impression 3D pour les brackets ?
Les supports sont des composants assez simples à fabriquer selon des méthodes traditionnelles. Cependant, avec l'avènement de l'impression 3D, les ingénieurs peuvent désormais explorer de nouvelles façons d'optimiser la conception des brackets.
Cela est largement possible, grâce à la capacité de l'impression 3D à créer des formes géométriques complexes qui seraient soit impossibles, soit d'un coût et d'un temps prohibitifs avec les moyens de fabrication traditionnels.
Les principaux avantages des brackets imprimés en 3D sont :
Production plus rapide
La production de supports métalliques complexes nécessite généralement plusieurs configurations de machine et peut prendre plusieurs heures. L'impression 3D, en revanche, peut offrir une solution plus rapide. L'une des raisons est qu'il est possible d'imbriquer plusieurs pièces à l'intérieur d'une imprimante 3D, permettant la production de plusieurs supports simultanément dans la même machine.
Pour un support préalablement moulé par injection, le gain de temps est encore plus important car l'impression 3D supprime le délai de réalisation d'un outillage de moule.
Assemblage supprimé
Certains supports sont fabriqués à partir de plusieurs pièces, ce qui peut augmenter le temps nécessaire pour assembler le support. L'impression 3D permet de concevoir et de produire un support en une seule pièce consolidée, ce qui nécessite moins de travail et de temps pour assembler le support. L'impression 3D d'un support en une seule pièce augmentera également probablement la résistance globale d'une pièce.
Dans un exemple, Philips a utilisé l'impression 3D pour produire un support repensé qui maintient les lampes en place sur la ligne de production. La pièce tombait fréquemment en panne, avec une ou deux défaillances chaque semaine, en grande partie en raison d'une exposition répétée à des températures élevées, associée à une structure comportant des lignes de soudure à partir d'un support en quatre pièces.
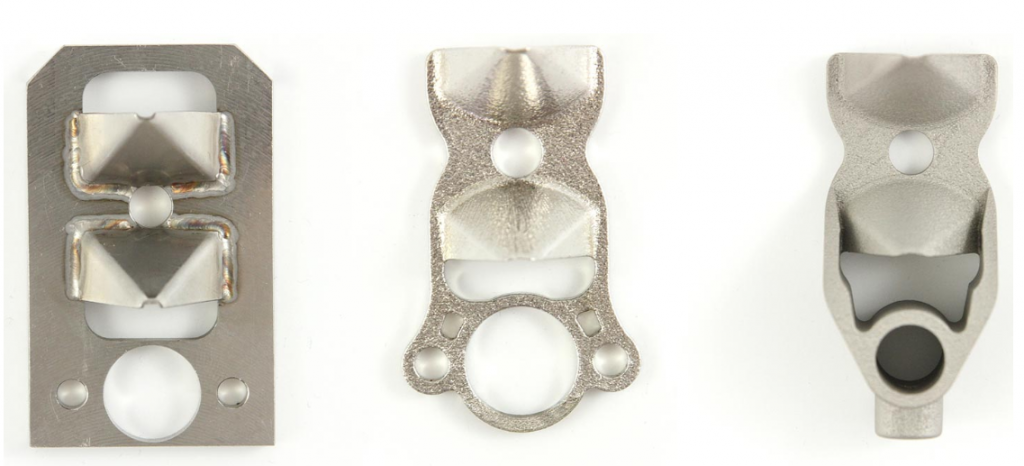
Philips a pu reconcevoir une pièce métallique en tant que support à structure unique, réduisant ainsi le temps d'assemblage des pièces et supprimant complètement les points de pression de la ligne de soudure. Au cours de ses trois premiers mois d'utilisation, le support réinventé ne s'est pas cassé une seule fois.
Réduction des déchets de matériaux
Le processus d'impression 3D d'un support en tant que composant utilise souvent moins de matériau, créant ainsi un support plus léger.
Cette économie de poids se traduit par une utilisation réduite du matériel et, dans certains cas, peut améliorer les performances d'un système où un support est utilisé.
Prenez l'exemple des moteurs GEnx de GE. Les moteurs utilisaient des supports fabriqués avec des méthodes traditionnelles telles que le fraisage. Cela signifie que les pièces ont été fraisées à partir d'un gros bloc de métal, dont plus de la moitié s'est retrouvée sous forme de déchets.
L'équipe travaillant sur les supports s'est rendu compte qu'en imprimant la pièce en 3D, elle serait en mesure de réduire jusqu'à 90 % des déchets.
L'équipe a également mis en œuvre de petites améliorations de conception qui ont réduit le poids du support de 10 %. Selon l'équipe, « lorsqu'il s'agit de voler, chaque once compte ». Cela signifie que la réduction du poids du composant peut avoir un impact sur le taux de consommation de carburant de l'avion, la réduisant et donc conduisant à un avion plus efficace.
Dans un autre exemple, les ingénieurs de Ford ont récemment imprimé en 3D un support de frein de stationnement électrique en plastique pour la Ford Mustang Shelby GT500 qui est 60 % plus léger qu'une version en acier estampée auparavant.
La possibilité de remplacer le métal par du plastique ou du composite
Pour certaines applications, l'impression 3D peut être utilisée pour produire des supports en plastique au lieu du métal. Les supports en plastique peuvent être mieux adaptés aux applications telles que les produits de consommation à durée de vie limitée ou les produits comportant des composants électroniques sensibles pour lesquels les supports métalliques ne fonctionneront pas.
Un exemple vient d'un fabricant d'appareils de communication, Boyce Les technologies. L'entreprise a utilisé l'impression 3D pour fabriquer des pièces en plastique pour les totems de NYC Transit. Chacun de ces systèmes comporte un capuchon en acrylique vert sur le dessus qui abrite une bande LED pour l'éclairage ainsi qu'un instrument d'antenne sensible.
Pour éviter la perturbation du signal d'antenne, il ne devrait pas y en avoir matériau métallique devant lui. Cela signifie que l'entreprise a dû fabriquer les supports pour la bande LED et le boîtier pour l'antenne en plastique. L'équipe Boyce n'avait que peu de temps pour la conception, l'ingénierie et la production, faisant de l'impression 3D une solution appropriée.
À l'aide du système BigRep Studio, Boyce a pu prototyper des supports de montage incurvés pour les lumières LED afin d'éclairer le capuchon, puis passer directement à la fabrication de ces pièces sur cette même plate-forme.
L'impression 3D de ces supports a permis de les fabriquer rapidement et de manière plus rentable que le moulage par injection ou l'usinage, tout en répondant à l'exigence sans métal au-dessus de l'antenne.
Plus d'exemples de supports imprimés en 3D
Aérospatiale
Supports en titane imprimés en 3D pour Boeing 787
Les supports aérospatiaux imprimés en 3D, fabriqués à partir d'alliages de titane, sont de plus en plus courants dans la conception des avions. Un exemple est un support pour un loquet de porte d'accès pour le Boeing 787, installé par Spirit AeroSystems.
La ferrure du loquet de porte, qui était auparavant usinée, est maintenant imprimée en 3D par Norsk Titanium, à l'aide de sa technologie brevetée Rapid Plasma Deposition (RPD). Le nom décrit le processus :un arc plasma permet un dépôt contrôlé de titane à des vitesses de fabrication rapides. La technologie serait 50 à 100 fois plus rapide que les systèmes à base de poudre et utiliserait 25 à 50 % moins de titane que les procédés de forgeage.
La principale raison du passage à l'impression 3D en titane est la possibilité de réduire la fabrication. Coût. Le titane est cher, et lors de l'usinage d'une pièce à partir d'un bloc de titane, une grande partie de ce matériau coûteux est gaspillée. Le deuxième problème est la grande quantité de temps machine et les frais d'outils de coupe nécessaires à l'usinage du métal, ce qui augmente le coût de production.
En imprimant un support en 3D, Spirit peut réduire considérablement ces coûts, tout en accélérant le délai de mise sur le marché des nouvelles pièces d'au moins 60 %.
Liebherr-Aerospace imprime en 3D des supports pour Airbus
Dans un autre exemple dans l'industrie aérospatiale, Liebherr-Aerospace a commencé à imprimer en 3D des supports de train avant pour l'Airbus A350 XWB.
Ces supports seront les tout premiers qualifiés Des pièces en titane imprimées en 3D introduites dans le système Airbus.
Contrairement à Spirit AeroSystems, Liebherr a pu redessiner une pièce pour obtenir une réduction de poids de 29 %. L'utilisation de l'impression 3D a également permis d'augmenter la rigidité du composant de 100 %.
En 2019, Liebherr-Aerospace a franchi une étape clé :l'Office fédéral allemand de l'aviation a donné son feu vert à l'entreprise pour produire des composants en utilisant la FA. Depuis, Liebherr imprime en 3D des pièces de série en titane, y compris des supports.
Automobile
Un support de toit optimisé et imprimé en 3D par BMW
En 2018, BMW a sorti son emblématique voiture i8 Roadster, dotée d'un support de toit en métal imprimé en 3D.
Le support de toit, un petit composant qui aide à se plier et déplier le toit de la voiture, nécessitait une nouvelle conception pour maximiser les performances du mécanisme de pliage du toit. Pour atteindre cet objectif, les ingénieurs de BMW ont combiné l'impression 3D avec un logiciel d'optimisation de la topologie.
En utilisant le logiciel, les ingénieurs ont pu saisir des paramètres tels que le poids, la taille du composant et la charge qu'il supportera. Le logiciel a ensuite généré une conception qui a optimisé la répartition des matériaux de la pièce.
La conception réalisée par l'équipe d'ingénierie était impossible à couler. L'équipe a découvert que la seule façon de rendre cette conception possible était l'impression 3D en métal.
Grâce à la technologie de fusion sélective au laser (SLM), les ingénieurs ont créé un support de toit en métal qui est 10 fois plus rigide et 44 % plus léger que l'alternative conventionnelle.
Les supports légers de Bugatti
Les véhicules Bugatti comportent également un certain nombre de supports imprimés en 3D. L'un est un support de spoiler en titane fabriqué en collaboration avec Fraunhofer IAPT. On dit que ce becquet améliore la conception aérodynamique des véhicules Bugatti.
Un autre partenaire dans le projet de support de spoiler était Siemens, qui a aidé à optimiser le support pour la production. Au final, la pièce finale présentait une résistance à la traction de 1 250 MPa, une densité de matériau de plus de 99,7 % et une réduction de poids de 53 %.
L'impression 3D a également été utilisée pour réinventer un petit support moteur avec refroidissement par eau intégré pour la supercar Bugatti Chiron. La pièce sert de bouclier thermique actif, réduisant considérablement la chaleur transférée du moteur. Le composant innovant, imprimé en AlSi10Mg sur une imprimante 3D SLM280 Twin par SLM Solutions, a été installé dans tous les véhicules de série depuis la sortie de la première Bugatti Chiron.
Supports imprimés en 3D :petits composants offrant une énorme opportunité
Les supports sont des pièces petites et plutôt banales, qui étaient difficiles à optimiser dans le passé, lorsque les ingénieurs étaient contraints par les méthodes de fabrication traditionnelles. Aujourd'hui, les ingénieurs peuvent concevoir des supports optimisés et donner vie à ces conceptions à l'aide de l'impression 3D.
Grâce à la technologie, les supports peuvent être rendus plus légers, mais plus rigides et durables. Les exemples ci-dessus démontrent également qu'en tirant parti de l'impression 3D, la durée de vie du composant et les performances globales peuvent être améliorées.
Clairement, on est encore loin des brackets imprimés en 3D. Cela dit, les applications spécialisées, comme les supports d'avions et les supports produits en petits volumes, resteront un bon créneau pour la technologie à l'avenir.
impression en 3D
- Soudage et collage de pièces en plastique imprimées en 3D
- Exploration de l'impression 3D Polyjet
- Qu'est-ce que la bioimpression ?
- L'application en vedette :l'impression 3D pour les implants médicaux
- Spécialiste de l'application :impression 3D pour la dentisterie numérique et la fabrication d'aligneurs transparents
- Spécialiste de l'application :Impression 3D pour la fabrication de vélos
- L'application en vedette :l'impression 3D pour les roulements
- COVID-19 a mis l'impression 3D sous les projecteurs
- Application de l'impression 3D dans l'industrie automobile