Entretien d'experts :Nanci Hardwick, PDG de MELD Manufacturing, sur la réalisation du potentiel de la fabrication additive métallique
MELD Manufacturing Corporation est le pionnier d'une nouvelle technologie radicale qui permet l'impression 3D de métaux sans fusion. Pendant plus d'une décennie, la technologie était en cours de développement avec la société de technologie Aeroprobe, avant que MELD ne devienne une filiale au printemps 2018.
MELD Manufacturing est entré sur le marché de l'impression 3D métal avec l'introduction de sa machine B8 à grande échelle en avril 2018. Défiant les processus typiques d'impression 3D métal sur lit de poudre, la B8 utilise un processus de fabrication à l'état solide basé sur la friction soudage par brassage. L'utilisation de la friction et de la pression pour lier le métal ensemble sans fondre offre de nombreux avantages uniques à la technologie MELD.
Cette semaine, nous avons le plaisir de nous entretenir avec le PDG de MELD Manufacturing, Nanci Hardwick, pour discuter de ce qui distingue MELD des autres processus de FA métal et du rôle que la technologie jouera dans l'avenir de la fabrication.
Quelle est la vision derrière MELD Manufacturing ?
MELD Manufacturing est une petite entreprise appartenant à une femme lancée l'année dernière et située en Virginie, aux États-Unis.
Nous avons été occupés depuis notre lancement et avons reçu de nombreuses reconnaissances l'année dernière, terminant 2018 avec un R&D 100 Award. Il s'agit d'un concours international qui récompense les nouveaux produits les plus innovants dans toutes les industries et tous les pays, en sélectionnant seulement 100.
Notre mission est de révolutionner la fabrication et de permettre ce qui est actuellement impossible, un exemple étant la réparation de l'irréparable . Chez MELD, notre application de la fabrication additive est un peu plus large qu'avec d'autres sociétés de fabrication additive. Il comprend un plus large éventail d'utilisations et commence par le matériau lui-même, se poursuit par la possibilité de fabriquer des pièces de manière additive, puis continue à offrir une plus grande valeur en étant capable de réparer ce qui a déjà été créé.
Nous pensons qu'aujourd'hui, il existe encore des limites dans les produits et les conceptions de FA, mais MELD peut offrir une opportunité de commencer à la case départ et de créer un produit vraiment conçu pour des performances optimales.
Pouvez-vous expliquer comment fonctionne la technologie MELD ?
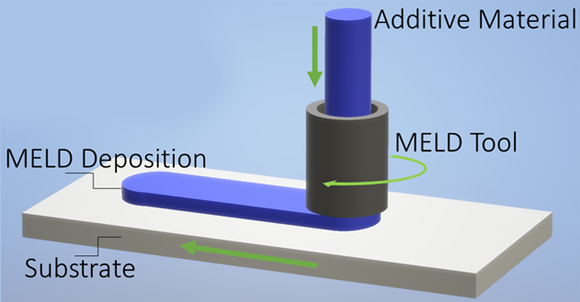
Notre technologie est assez unique. L'attribut fondamental de MELD est qu'il s'agit d'un processus à l'état solide. La plupart des additifs métalliques ou des procédés traditionnels nécessitent la fusion du métal. Cependant, la possibilité de traiter le métal sans le faire fondre crée des avantages intéressants.
La technologie derrière MELD est assez simple, ce qui est l'un de ses plus grands avantages.
Nous avons un outil creux à travers lequel nous passons le matériau. Le processus peut s'adapter à une grande variété de matériaux sous différentes formes, y compris de la poudre, des copeaux de flocons ou des barres solides.
Quel que soit le matériau, il entre dans l'outil rotatif, où des pressions et des frottements extrêmes travaillent pour déformer plastiquement non seulement le matériau que nous ajoutons, mais également le matériau sur lequel nous déposons.
Lorsque les deux sont dans un état de déformation plastique, nous pouvons littéralement mélanger les deux. La façon la plus simple de considérer cette méthodologie est comme un processus d'agitation par friction additif.
L'action d'agitation brise les grains de matériau individuels, créant une structure de grain raffinée, qui offre des propriétés de résistance et de performance améliorées, y compris la corrosion et résistance à la fatigue par impact.
Ce processus permet un lien supérieur entre ce qui est ajouté et ce qui est ajouté. Cela permet aux utilisateurs non seulement de fabriquer une nouvelle pièce, mais également de réparer, de revêtir ou d'ajouter des fonctionnalités à une pièce existante.
Ce processus est très flexible car il se produit en dessous de la température de fusion des matériaux avec lesquels nous travaillons. En conséquence, nous pouvons traiter la plus large gamme de matériaux, y compris des métaux non soudables ou des matériaux qui ne sont pas disponibles pour les processus basés sur la fusion.
Nous pouvons traiter une plus grande variété de formes de matériaux comme des poudres, des copeaux et tige ou fil solide. Il n'y a pas de spécifications ou d'exigences pour la machine MELD en termes d'entrée de matière, ce qui est tout à fait unique dans le monde des additifs. En fait, certains autres fabricants d'équipements de FA ont des tolérances si strictes sur leurs exigences en matière de matières premières qu'ils exigent que leurs utilisateurs leur achètent le matériel.
MELD est un processus de fabrication additive en atmosphère ouverte. La plupart des équipements d'additifs métalliques sont entourés d'un conteneur. Ce conteneur est utilisé soit pour faire le vide, soit pour évacuer l'oxygène et faire entrer un gaz non oxygène comme l'Argon. Avec des procédés comme MELD, lorsque vous ne faites pas fondre de métal, vous n'avez pas nécessairement à vous soucier de l'absorption d'oxygène, comme le font d'autres procédés. Cela se traduit également par un processus d'additifs plus économique, plus sûr et plus écologique.
De plus, une atmosphère ouverte permet un processus extrêmement évolutif. Avec les imprimantes 3D à atmosphère fermée, si vous voulez faire une plus grosse pièce, vous devez trouver un conteneur plus grand pour faire fonctionner vos processus. Mais avec MELD, ce n'est pas le cas. Certaines des applications envisagées pour l'additif maintenant sont des choses à très grande échelle comme les navires, les engins spatiaux, les ponts à réparer en particulier. MELD, étant un processus à atmosphère ouverte, vous donne beaucoup de liberté dans de telles applications.
Poursuivant la liste des avantages, notre technologie est de très faible consommation car elle n'utilise pas de laser. Les taux de dépôt de matériau sont assez élevés et la pièce finie nécessite peu de post-traitement car le matériau déposé est déjà entièrement dense. Cela signifie que vous n'avez pas besoin de deuxièmes étapes pour arriver à une pièce finale, comme le pressage isostatique à chaud (HIP) ou le frittage.
Comment la technologie se compare-t-elle à d'autres méthodes de FA en métal ?
Il existe des opportunités et les meilleurs cas d'utilisation pour tous les processus. Un seul processus ne peut pas répondre à tous les besoins. C'est pourquoi il est important de comprendre les attributs uniques de chaque processus. Pour MELD, l'attribut unique par rapport aux autres technologies 3D métalliques est qu'il est à semi-conducteurs.
Nous sommes la seule technologie capable de faire évoluer et de construire ou de réparer de très grandes pièces. Une autre capacité unique est que vous pouvez prendre une pièce existante et la placer dans la machine, puis ajouter du matériau supplémentaire, que vous souhaitiez un revêtement résistant à l'usure sur un matériau très léger ou que vous souhaitiez ajouter le matériau pour réparer une pièce usée. surface.
Le fait qu'il s'agisse d'un processus thermique plus faible signifie que nous créons moins de contraintes résiduelles, qui se manifestent par une distorsion réduite. MELD peut mettre pas mal de matériau sur une plaque très fine sans distorsion. Cela rend MELD d'un intérêt extrême pour les industries automobile et aérospatiale.
Imaginez que vous fabriquiez un panneau de fuselage d'avion. Avec une approche conventionnelle, vous prendriez une plaque d'aluminium de quatre pouces d'épaisseur et usineriez 80% du matériau pour obtenir une plaque mince avec une bande de raidisseurs à nervures, qui a le poids minimal mais la résistance structurelle et les performances maximales. Avec le procédé MELD, nous pouvons commencer avec une plaque très fine et ajouter ces raidisseurs de nervures sans créer de contrainte résiduelle qui peut détruire cette plaque.
Un autre différenciateur de la technologie MELD est qu'elle prend en charge la plus large gamme de matériaux, alors qu'il existe des machines AM qui n'acceptent qu'un ou peut-être deux ou trois matériaux.
Revenir en arrière là où nous nous dirigeons vraiment, nous offrons également la possibilité de créer réellement le matériel. Avec une machine MELD, vous pouvez créer vos propres alliages et composites à matrice métallique in situ.
Si vous pensez à la proposition de valeur de la fabrication additive en général, en termes de prototypage, cela donne aux entreprises l'opportunité d'évaluer très rapidement une nouvelle géométrie d'une pièce. MELD offrira cette même proposition de valeur pour l'évaluation de nouveaux matériaux. Les utilisateurs de notre technologie peuvent adapter leurs recettes d'alliage, puis effectuer des tests pour soutenir l'effort d'optimisation d'un nouvel alliage. Pour moi, c'est l'une des opportunités les plus intéressantes qu'offre la technologie.
De plus, MELD est la seule technologie démontrée pour recycler les matériaux. Par exemple, vous pouvez prendre des copeaux de machine dans un atelier d'usinage et fabriquer une pièce avec la machine MELD. C'est un énorme facteur de différenciation en termes de respect de l'environnement et de l'environnement de ce processus.
Enfin, lorsque vous associez certains de ces avantages :il est peu énergivore, n'émet pas de gaz et est assez facile à utiliser - ces attributs réunis rendent le processus MELD très attrayant en termes de portabilité. Cela intéresse des organisations comme l'armée américaine qui souhaitent apporter des capacités supplémentaires sur le champ de bataille. Les sociétés de production d'électricité qui ont de très gros équipements sur le terrain bénéficieraient également de l'utilisation d'additifs pour minimiser les temps d'arrêt et effectuer la réparation au point de besoin.
Qu'est-ce qui rend l'impression 3D métal si attrayante pour les industries que vous avez mentionnées ?
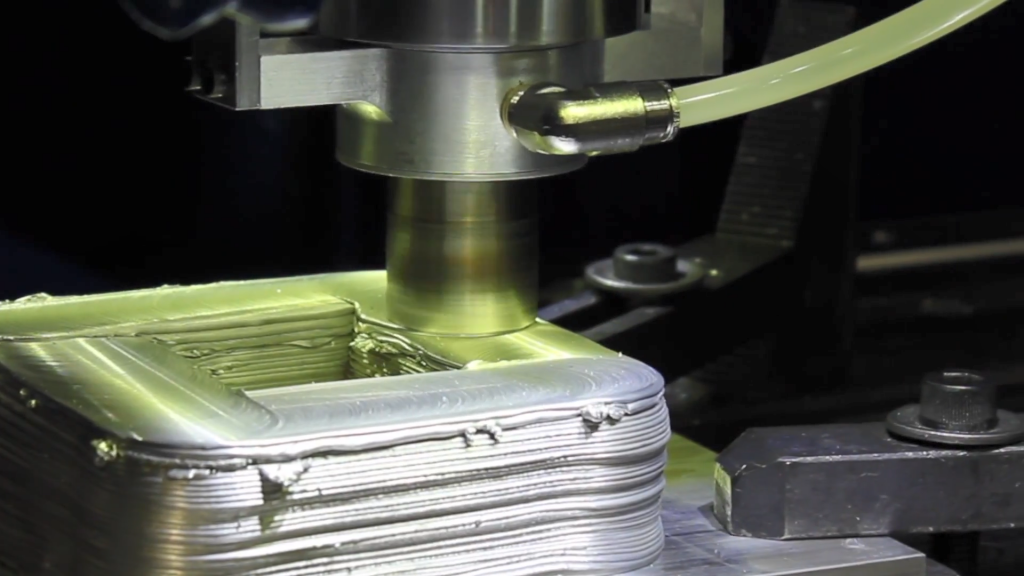
Jusqu'à présent, je n'ai pas encore trouvé d'industrie qui ne puisse bénéficier de la fabrication additive et de la technologie MELD en particulier. L'additif a beaucoup à offrir en termes de matériaux et d'applications industrielles. Les métaux ne sont qu'une petite étape dans le cheminement global vers une véritable personnalisation.
Efficacité, économies de coûts, amélioration des performances, capacité à réparer, réduire l'investissement global et effectuer des remplacements, en minimisant la queue logistique — tout cela les avantages offerts par la FA sont disponibles pour toutes les industries que j'ai rencontrées.
Le métal, en particulier, est utilisé dans toutes les industries. Nous avons tendance à penser aux produits finis qui sont en métal. Mais la vérité est qu'il n'y a pas de fabricant qui n'utilise pas de métal dans la production de ses produits. Cela signifie que les fabricants de tout produit peuvent potentiellement bénéficier de la FA.
Comment décririez-vous l'état actuel de la fabrication additive et comment voyez-vous le paysage évoluer au cours des cinq prochaines années ?
Nous sommes encore à l'aube d'une nouvelle ère. En ce moment, les gens parlent d'Industrie 4.0. Je pense que nous nous dirigeons vers 5.0.
À court terme, nous nous concentrons principalement sur les étapes finales de fabrication du produit. Nous pensons à un produit existant et à la façon dont nous pouvons le fabriquer avec moins de temps, de coût, de poids et avec moins d'étapes.
Dans une moindre mesure, l'accent est mis sur l'étape précédente, qui consiste à examiner et à définir les différentes exigences de performance d'une pièce à l'autre. Je crois que la véritable évolution se situe au stade où nous considérons la sélection des matériaux, la conception et les exigences de performance. Par exemple, nous pouvons exiger une pièce résistante dans un domaine mais ayant une plus grande ductilité dans un autre domaine.
Lorsque toutes ces exigences et variables sont prises en compte dès la conception d'un produit, lorsqu'il ne s'agit que de cet effort synergique d'évaluation et d'optimisation simultanées de chaque aspect d'un produit, alors nous aurons réalisé tous les potentiels de fabrication additive.
Quel est selon vous le plus grand défi que l'industrie de la FA doit relever pour accélérer l'adoption de la technologie ?
Un défi commun que je vois est le manque d'expertise et de capacité internes. En discutant avec un très large éventail d'entreprises, la responsabilité de créer une stratégie additive incombe souvent à une personne pour laquelle il s'agit d'une responsabilité supplémentaire plutôt que d'une responsabilité principale.
Pour accélérer l'adoption de la fabrication additive , les entreprises doivent allouer des ressources aux champions internes.
Y a-t-il une corrélation entre la taille d'une entreprise et le niveau d'expertise de l'entreprise en matière de FA ?
Non, cela varie beaucoup. Parfois, les petites entreprises sont capables d'aller beaucoup plus vite et de prendre des décisions beaucoup plus rapidement et décident donc qu'elles vont poursuivre l'avantage concurrentiel que les additifs peuvent apporter avec une vitesse maximale.
Parfois, il ne s'agit pas nécessairement autant de ressources que d'un capacité à maximiser le taux de changement. Et le changement est difficile, surtout si vous avez déjà une façon bien définie de faire les choses. Devoir le changer ou l'adapter est toujours un défi.
Quels conseils donneriez-vous à une entreprise souhaitant adopter l'impression 3D métal mais ne sachant pas par où commencer ?
Il existe quelques critères simples permettant de construire un cadre pour évaluer les technologies d'impression 3D. Ceux-ci incluent la taille du produit, les matériaux du produit et les critères de performance pour les pièces potentielles.
Tous les processus additifs ont leurs avantages et leurs inconvénients pour une tâche donnée. La partie délicate consiste alors à examiner une pièce existante avec certaines spécifications matérielles et exigences de performance et à réfléchir à la manière dont nous pouvons améliorer cette pièce, la rendre plus rapide ou moins chère.
Une fois que nous maîtriserons toutes les capacités de la technologie additive, nous découvrirons rapidement des idées sur la façon dont nous pouvons nous améliorer. Cette liste de critères originale est utile comme point de départ. En outre, il est utile de réaliser que quel que soit l'intérêt pour l'additif, il grandira avec l'éducation et la familiarité avec ce que l'additif rend possible.
À quoi ressemble l'avenir de MELD Manufacturing ?
Nous allons nous diriger vers ce que je crois être l'Industrie 5.0 :la synthèse des fonctions qui sont encore séparées aujourd'hui. Nous continuerons à démontrer ce qui est possible lorsque vous intégrez la conception de matériaux à la conception de produits et autorisez la variation et la personnalisation à travers une pièce.
Cette idée de personnalisation et de variation dans la pièce elle-même est le prochain endroit où nous irons et cela nécessite de réunir la science des matériaux, la conception des matériaux, l'ingénierie mécanique et électrique. MELD en particulier peut aider à les rassembler. Nous continuerons à pousser la fabrication additive au-delà de l'idée de la simple fabrication de pièces à la capacité d'ajouter des revêtements résistants à l'usure ou à la résistance balistique ou d'ajouter des fonctionnalités pour personnaliser, renforcer ou réparer une pièce. Il y a encore tellement d'opportunités devant nous.
Cette année, nous lancerons une autre plate-forme de machine d'équipement à ajouter à notre gamme qui a un espace de construction beaucoup plus grand, mesuré en pieds cubes plutôt qu'en pouces.
En outre, 2019 apportera un cours de certification pour les opérateurs. Nous lancerons un consortium de recherche, puis participerons évidemment à de nombreux événements, parlerons et exposerons.
Enfin, voyez-vous des développements concernant l'arrivée de plus de femmes dans l'espace d'impression 3D ?
C'est une excellente question. J'ai récemment pris la parole lors de l'événement Women in Manufacturing organisé par Volvo Trucks. C'était un grand événement auquel ont participé à la fois des hommes et des femmes. L'une des choses que j'ai adorées a été de participer à un panel où nous avons parlé de notre voyage et du chemin tortueux que tout le monde prend dans la vie pour finir là où ils en sont.
L'une des choses que j'en ai retenues, c'est que les femmes sont courageuses, capables et courageuses. Ils peuvent se soulever l'un l'autre et n'ont pas à prendre une ligne droite ou à faire des sacrifices pour arriver là où ils vont.
Pour moi, c'est extrêmement excitant de faire partie d'une toute nouvelle technologie. C'est vraiment une révolution dans notre vie et nous verrons le changement que les gens d'aujourd'hui ne peuvent pas vraiment exprimer. Je pense que c'est merveilleux d'en faire partie et j'espère que cela montrera que n'importe qui peut faire n'importe quoi. Ils doivent juste être prêts à tenter leur chance.
Pour en savoir plus sur MELD Manufacturing, visitez :meldmanufacturing.com
impression en 3D
- Repenser le processus d'intégration logicielle pour les opérations de fabrication additive
- Entretien d'experts :Duncan McCallum, PDG de Digital Alloys, sur l'impression Joule et l'avenir de l'impression 3D sur métal
- Entretien :Global Head of Metals de HP sur l'impact de HP Metal Jet
- Entretien d'experts :Guillaume de Calan, PDG de Nanoe, sur l'avenir de l'impression 3D céramique
- Entretien d'experts :PDG de PostProcess Technologies sur la résolution du goulot d'étranglement du post-traitement pour la fabrication additive
- Entretien d'experts :Doug Hedges, président de Sintavia, sur la réalisation de la production en série avec l'impression 3D en métal
- Entretien d'experts :Rush LaSelle de Jabil sur l'avenir de la fabrication additive
- Entretien d'experts :Carl Fruth, PDG de FIT AG, sur la réalisation d'une innovation radicale avec la fabrication additive
- Comment tirer pleinement parti de la CAO dans le processus de fabrication additive