Châssis CFRP prototypes WMG pour véhicule de démonstration VLR (Very Light Rail)
Revolution VLR est un consortium au Royaume-Uni - dirigé par Transport Design International Ltd (TDI, Stratford upon Avon) - qui a remporté un financement en 2013 pour développer un bogie ferroviaire auto-alimenté avec un système de propulsion hybride intégré. TDI pense que la conception de véhicules « légers sur rail » plus légers, c'est-à-dire de trains très légers (VLR), est cruciale pour fournir la prochaine génération de transports publics durables. Dans la phase 2 du projet VLR, un véhicule démonstrateur complet de batterie diesel de 18 mètres de long sera disponible pour des tests en 2020.
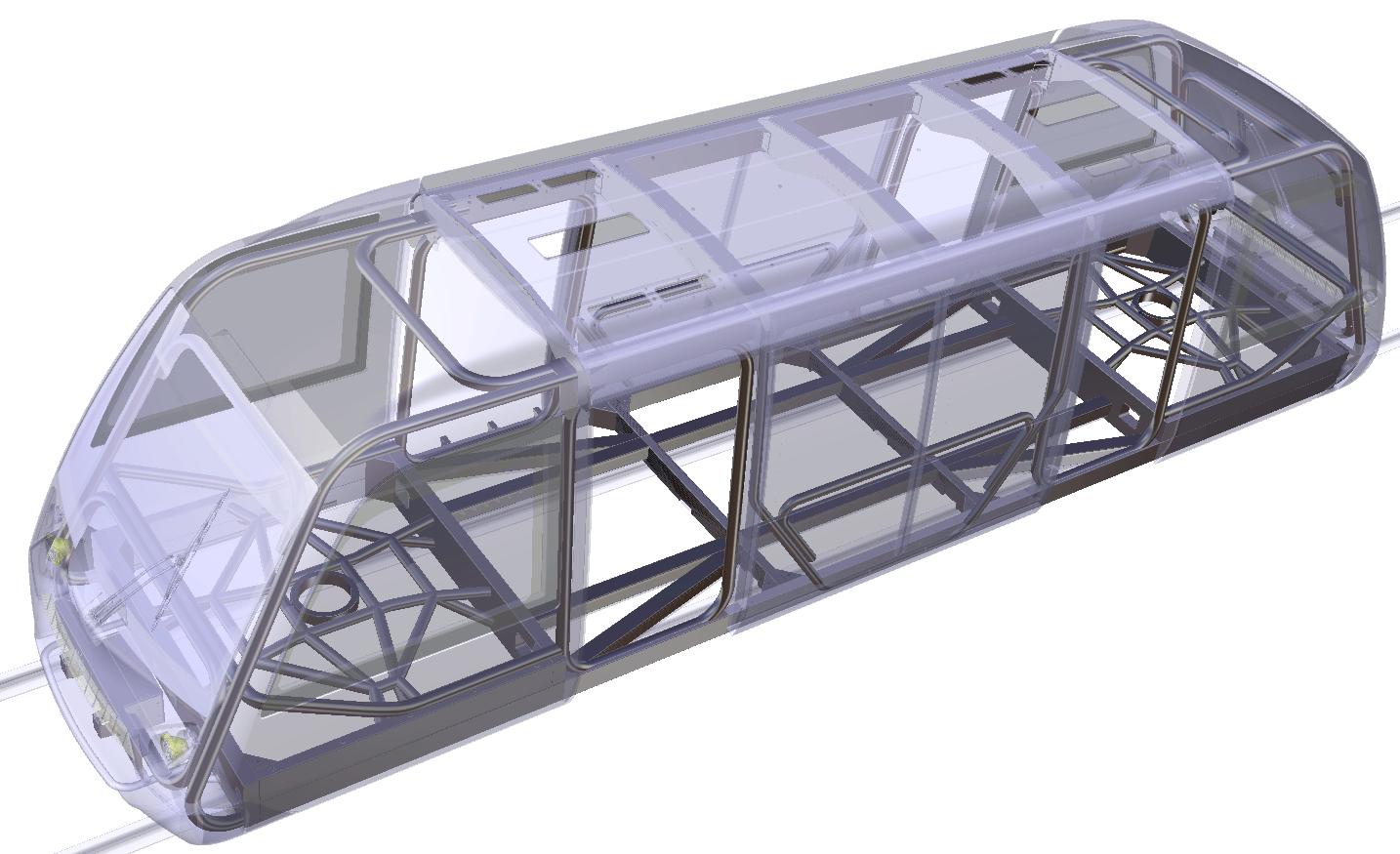
Le démonstrateur Very Light Rail (VLR) est un bogie de 18 mètres de long avec système de propulsion hybride diesel-batterie intégré et un châssis léger en tubes composites tressés. SOURCE | Université de Warwick.
Membre original de Revolution VLR, WMG de l'Université de Warwick a développé un cadre en plastique renforcé de fibres de carbone (CFRP) pour ce véhicule de démonstration VLR. WMG est un partisan de longue date des composites, avec des initiatives telles que le National Automotive Innovation Centre, le Materials Engineering Center et l'International Institute for Nanocomposites Manufacturing. Les partenaires de WMG pour ce projet « BRAINSTORM VLR » comprennent TDI, Innovate UK du gouvernement britannique (qui finance les composites), le développeur de composants composites structuraux légers Far Composites et Composite Braiding. Le cadre est composé d'une série de tubes composites thermoplastiques tressés qui s'assemblent facilement par collage et soudure simple.
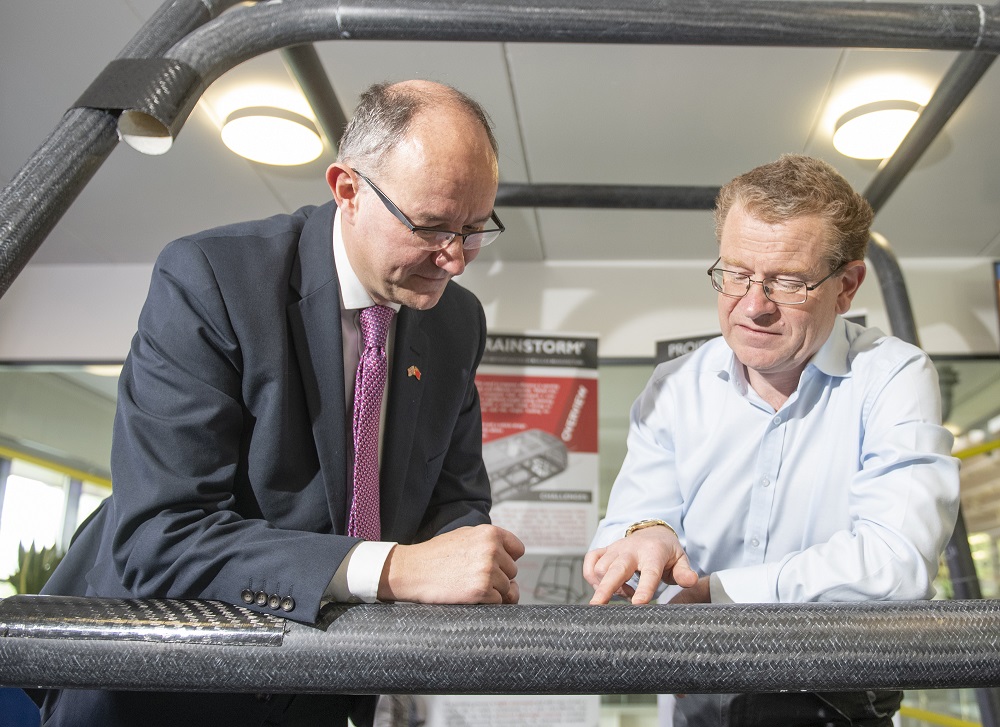
Le véhicule prototype/démonstrateur VLR utilisera un châssis spatial composé de tubes composites thermoplastiques renforcés de fibres de carbone tressés qui s'assemblent facilement par collage et simple soudage. SOURCE | Université de Warwick.
Les diamètres extérieurs des tubes sont conservés les mêmes, avec différentes exigences de charge et de fixation gérées en faisant varier les épaisseurs de paroi. Cela permet de réduire les coûts d'outillage et de standardiser les assemblages. Le tressage permet un processus de fabrication hautement automatisé - les taux pour le renforcement seul peuvent dépasser 1 mile/jour - ainsi qu'un ensemble de matériaux sur mesure, y compris d'autres fibres (par exemple, verre, aramide, thermoplastique) et des matériaux de matrice thermoplastique à partir de polypropylène à faible coût au polyétheréthercétone (PEEK) haut de gamme. Pendant ce temps, WMG a démontré un cycle de moulage complet qui peut être réduit à moins de cinq minutes, soulignant le potentiel de ce processus abordable pour les applications à grand volume.
Les thermoplastiques assurent également la recyclabilité, selon David Goodwin, directeur de l'ingénierie chez Far-UK. « Avec les composites, vous pouvez gagner beaucoup de poids, ce qui est évidemment attrayant pour le fonctionnement du wagon [rail]", commence-t-il, "mais avec les composites traditionnels, en fin de vie du wagon, il est simplement mis en décharge, ce qui n'est pas idéal. Avec cette [conception], il existe une voie pour recycler la carrosserie de la voiture lorsqu'elle est finalement hors service, ou, alternativement, si elle subit un impact et qu'une partie doit être réparée et remplacée.
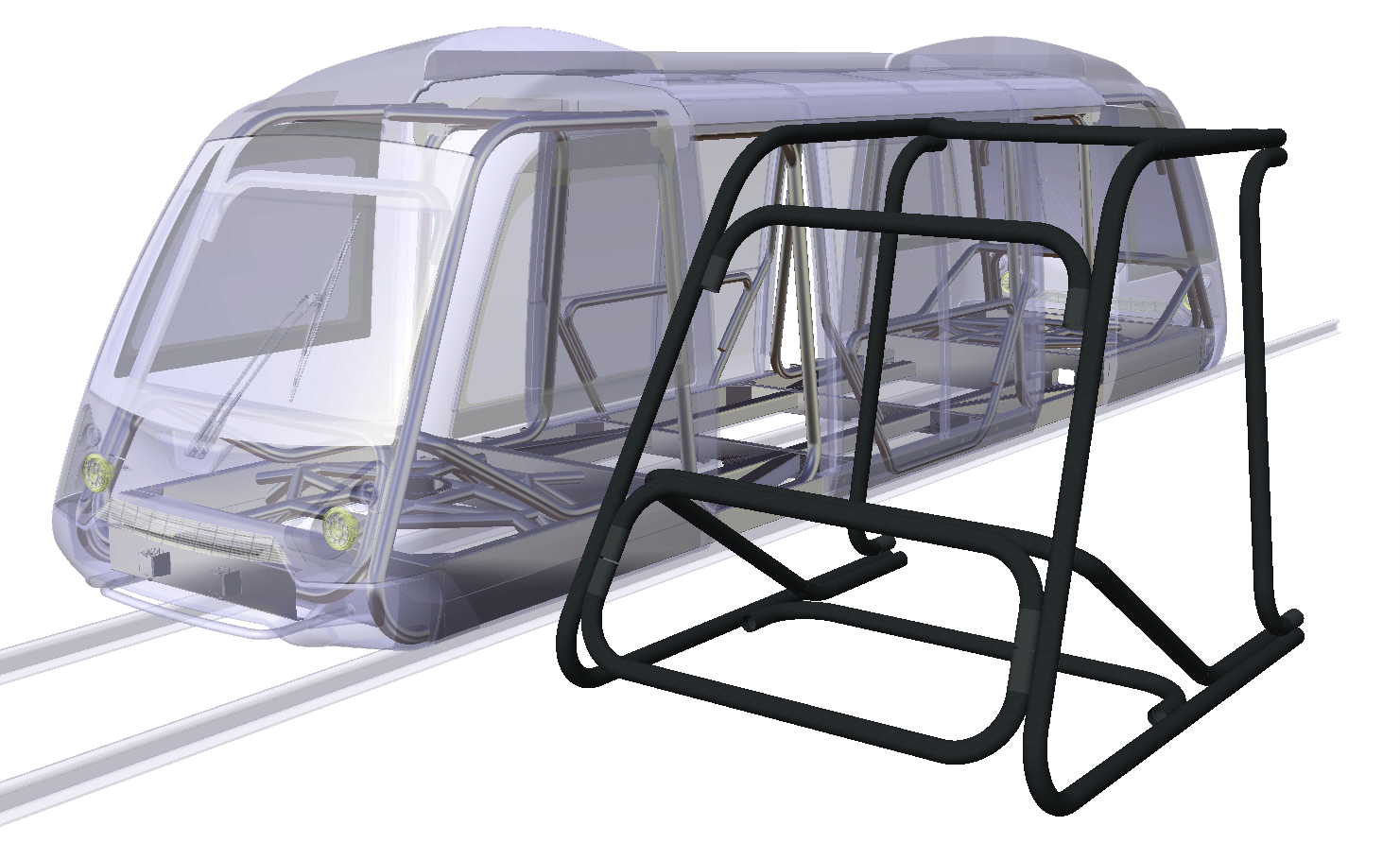
Université de Warwick
La conception tubulaire du châssis spatial facilite également cette approche, permettant à tout tube endommagé d'être simplement retiré et remplacé par un nouveau ou réparé. « Notre partenariat de recherche BRAINSTORM VLR a permis de réduire considérablement le poids, permettant aux services VLR d'accueillir plus de passagers tout en réduisant l'énergie nécessaire pour propulser le véhicule et le poids qu'il exercera sur ses rails et la surface de la route », explique le Dr Darren Hughes, professeur agrégé en matériaux et fabrication à l'Université WMG de Warwick. "La technologie garantit également que le véhicule est robuste pour une longue durée de vie, facilement réparable en cas d'accident et suffisamment solide pour protéger les passagers à bord."
« Le projet BRAINSTORM est un véritable pas en avant pour l'équipe de Far Composites », déclare Lyndon Sanders, directeur et directeur général de Far-UK. « Pouvoir tirer parti de l'expérience industrielle de TDI pour perfectionner le principe d'un nouveau type de structure de carrosserie pour les applications de transport en commun était formidable. Ajoutez à cela le travail collaboratif avec Composites Braiding et WMG pour transformer cette réflexion en un démonstrateur physique pour montrer à quoi cela ressemblerait dans la pratique était vraiment puissant. Maintenant, c'est plus qu'une bonne idée, c'est une révélation pour les acteurs de l'industrie qui peuvent la voir, la toucher et même la ramasser. »
Résine
- Composites TPE ultra-légers pour chaussures
- Conception pour la fabrication automatisée de composites d'aérostructures de faible volume
- Résines époxy retransformables, réparables et recyclables pour composites
- Combinaison de mesures diélectriques CA et CC pour la surveillance du durcissement des composites
- RS Electric Boats sélectionne Norco pour la fabrication de composites
- Thermocouple haute température PEEKSense pour le durcissement des composites PEEK
- Solvay composites sélectionnés pour catamaran de course
- Porte thermoplastique une première pour les composites automobiles
- Ashland s'associe à Velox pour la distribution de composites en France