Le projet PASARO de Clean Sky 2 cible le cockpit composite OOA à un coup
Le projet PASSARO (caPAbilities for innovant Structural and Functional testing of AeROstructures) vise à développer de nouveaux matériaux multifonctionnels - intégrant une isolation phonique et une résistance aux chocs à haute énergie - et des solutions d'inspection pour un nouveau cockpit composite fabriqué en une seule fois et complété par un out of autoclave (OOA) technologies telles que la consolidation in situ des composites thermoplastiques et l'infusion de résine liquide. Ce cockpit composite a été développé par Airbus Defence and Space (Madrid, Espagne) lors de Clean Sky 1, basé sur l'avion C295. Le projet vise également l'automatisation des processus de fabrication ainsi que de nouvelles approches de test basées sur les concepts de l'Industrie 4.0 et le développement de concepts ergonomiques avancés favorisant le confort du pilote et l'amélioration de l'interface homme-machine.
Le projet PASSARO, qui fait partie de la plate-forme Airframe de Clean Sky 2, a débuté en juillet 2016 pour une durée totale de 48 mois. Il comprend onze partenaires portugais et espagnols travaillant en étroite collaboration avec Airbus Defence and Space.
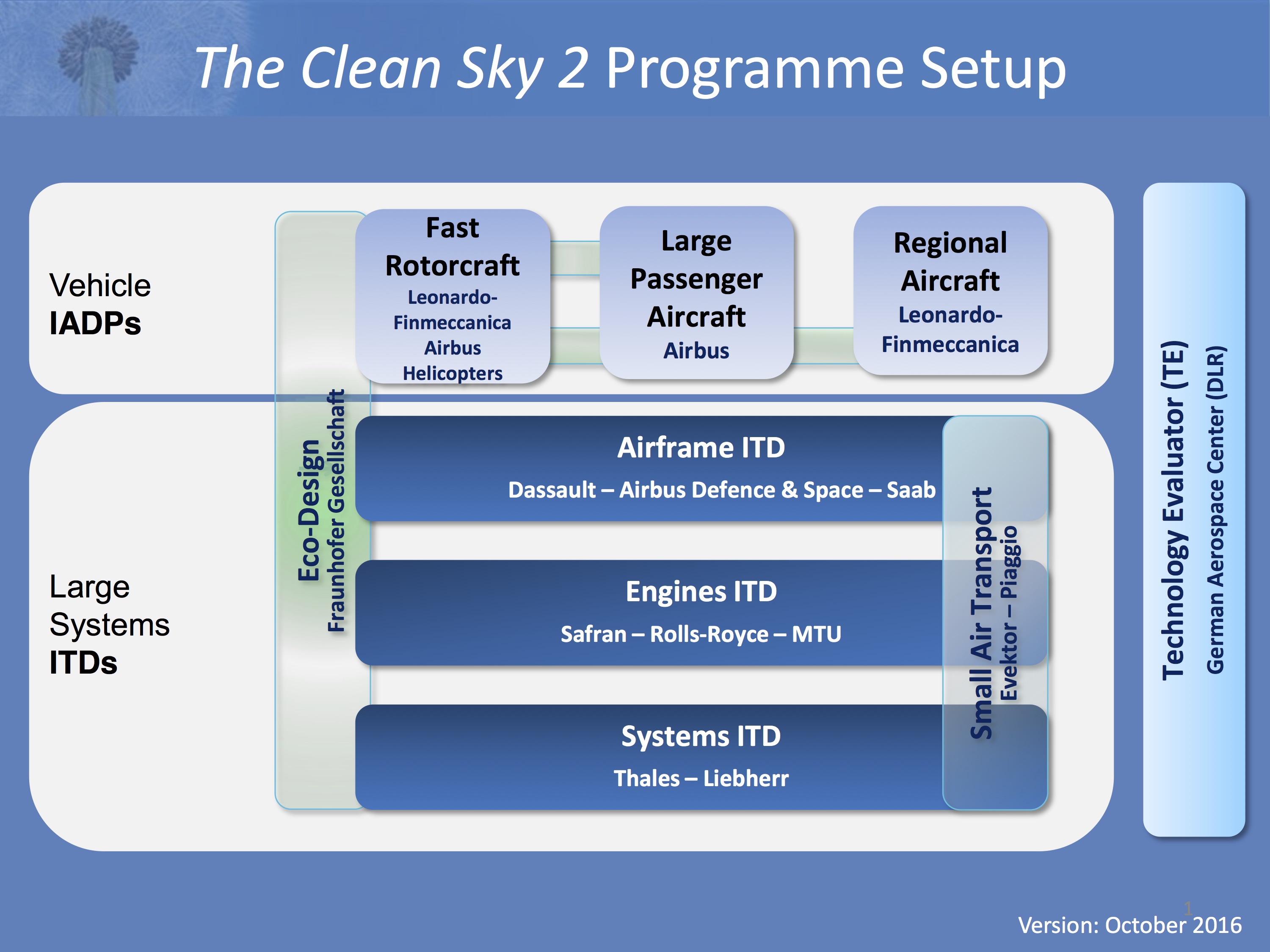
SOURCE :Clean Sky 2
Synergies avec le projet régional MOSHO du Portugal
De nombreux projets Clean Sky 2 (CS2) partagent des synergies avec les initiatives régionales des membres de l'UE (par exemple, le CORAC en France). Le projet PASARO a promu des activités complémentaires avec les initiatives nationales de R&D portugaises. Le projet MOSHO (Solutions avancées pour les matériaux d'impact, la réparation des aérostructures composites et leur surveillance) complète les activités de PASARO dans lesquelles certains partenaires sont impliqués et est soutenu par ADS (Airbus Defence and Space) en tant que coordinateur Clean Sky 2 pour la ITD cellule. Le projet développera et intégrera des solutions avancées pour la réparation d'aérostructures composites.
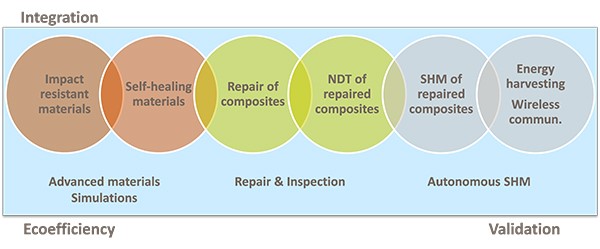
Figure 3 :Portée technique du projet MOSHO SOURCE : https://www.cleansky.eu/commissioner-moedas-meets-passaro-at-isq
Les robots collaboratifs PASSARO réduisent le temps de cycle de préparation des mains jusqu'à 70 %
Dans le cadre des objectifs du projet PASSARO de rechercher et de développer comment utiliser des robots collaboratifs dans la fabrication de composites, le projet OPTIMAL a développé une solution automatisée pratique et rentable pour remplacer la pose manuelle traditionnelle, en utilisant des matériaux qualifiés.
Traditionnellement, la fabrication de composants composites à l'aide de préimprégnés est essentiellement une activité artisanale, mais des mesures sont prises vers l'automatisation. Au cours de la dernière décennie, plusieurs solutions de superposition automatisées ont vu le jour pour des pièces à géométrie relativement simple. Ces solutions sont souvent assez coûteuses et exigent généralement que les usines soient conçues à partir de zéro pour leur installation. Ils nécessitent généralement des environnements spéciaux sous la forme de cellules isolées avec des systèmes de sécurité dédiés. Comme alternative, des robots collaboratifs (cobots) pourraient être intégrés aux workflows de fabrication existants pour automatiser certaines tâches et améliorer la productivité sans changer radicalement l'environnement environnant.
Les robots industriels sont rapides, solides et ont une précision et une répétabilité exceptionnelles, mais ils sont développés dans le seul but d'optimiser le résultat final. En comparaison, les cobots sont plus lents, moins précis et gèrent des charges utiles plus petites, mais ont ce qu'il faut pour automatiser des tâches simples, en particulier avec des humains, à un coût considérablement moindre. Les cobots sont équipés de capteurs de charge qui détectent les plus petits impacts et s'arrêtent en toute sécurité.
L'objectif d'OPTIMAL lors du développement de technologies de cobot est d'améliorer sa propre capacité et celle d'autres entreprises, pour offrir des produits plus reproductibles et de meilleure qualité en grandes quantités et à des prix inférieurs.
Au sein du Work Package 10 du projet PASSARO, trois étapes principales ont été développées à l'aide de robots collaboratifs :
- Ramassage et tri des plis, directement depuis le coupe-plis automatisé ;
- Épluchage des plis à l'aide d'une cellule dédiée ;
- Positionnement et empilage des plis dans un outil.
Pour mettre en œuvre ces activités, une cellule a été développée qui reçoit les plis préimprégnés du coupe-plis et les épluche et les empile automatiquement sur un moule.
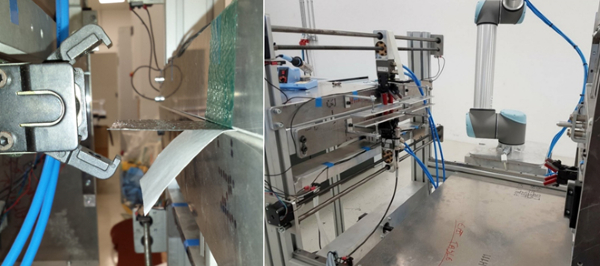
Robots collaboratifs utilisés pour la fabrication de composites dans le projet PASSARO. SOURCE : Groupe ISQ
Les tâches de positionnement et d'empilage sont effectuées par le bras du robot à l'aide de ventouses spéciales pour la manipulation du préimprégné. L'éplucheur est une machine plus complexe, utilisant de l'air comprimé pour éplucher le préimprégné, qui est protégé par deux revêtements - généralement un plastique et un papier, ou simplement par deux plastiques. Le concept de pelage est basé sur le fait que différents matériaux ont tendance à vibrer à des fréquences différentes lorsque le même stimulus est appliqué. Les différentes fréquences de vibration produisent des poches d'air entre le préimprégné et les couches de revêtement. Le résonateur à plaques ajuste l'amplitude de vibration pour différents matériaux. Ce prototype pourrait atteindre des taux de pelage avec près de 100% de réussite pour des matériaux spécifiques et une précision d'empilement de ± 0,5 mm, dans chacun des deux degrés de liberté dans le plan du moule, et ± 0,1° en rotation.
L'approche modulaire adoptée pour ce système le rend indépendant des dimensions des plis. La largeur est couverte en ajoutant plus de modules d'épluchage parallèles et la longueur en ajustant la plage d'ouverture de l'éplucheur. Cette technologie, par rapport à un opérateur humain, offre une nette amélioration de la précision du processus, de la répétabilité et surtout du temps de cycle, avec des réductions allant jusqu'à 70 %.
Auteurs :António Reis, Nicole Cruz, Marco Neves (OPTIMAL) et Rúben Buelga Sanchez (ADS). Pour plus d'informations, contactez:
INEGI
Campus de la FEUP
Rua Dr Roberto Frias, 400
4200-465, Porto, Portugal
Tél. :(+351) 229 578 710
Courriel :[email protected]
Résine
- Solvay augmente la capacité des composites thermoplastiques
- Toray in Dutch Project for Aircraft Liquid-Hydrogen Tanks
- Le projet Clean Sky 2 FUSINBUL développe des cloisons étanches à pression en fibre de carbone à grande échelle
- L'importance de la sélection de résine
- Le projet Clean Sky 2 FRAMES fait progresser la simulation de chauffage du composite thermoplastique AFP avec une lampe flash au xénon
- Clean Sky 2 publie les résultats du projet
- Le spécialiste allemand des composites INVENT collabore avec SUSTAINair pour une circularité accrue des avions
- Le consortium cible des solutions pour les structures composites thermoplastiques en fibre de carbone
- Fabrication rapide d'ébauches composites sur mesure