Visite de l'usine :Holland Composites, Lelystad, Pays-Bas
Catamarans à foils, façades de bâtiments et plus encore. Situé à moins d'une heure de route d'Amsterdam, Holland Composites poursuit une grande variété de projets hautement techniques dans ses 4 500 m 2 facilité. Source, toutes les images | Holland Composites
Situé dans un bâtiment de 4 500 mètres carrés, à moins d'une heure de route d'Amsterdam, Holland Composites (Lelystad, Pays-Bas) se concentre sur quatre marchés :marine/offshore, architecture, énergies renouvelables et projets spéciaux. Holland Composites utilise un mélange de polymère préimprégné renforcé de fibres de carbone (CFRP) et de nid d'abeilles Nomex pour les pièces fortement chargées, et d'infusion de résine et de fibre de verre pour l'industrie du bâtiment et les projets à faible marge. « Nous sommes toujours en mesure d'obtenir des performances élevées même avec ces constructions plus rentables, et nous maintenons de faibles frais généraux pour les pièces utilisant des matériaux de pointe », déclare Sven Erik Janssen, partenaire co-gérant de Holland Composites, avec le fondateur Pieterjan Dwarshuis. "C'est unique."
La société exploite également la marque DNA Performance Sailing, produisant des voiliers multicoques à foils, dont le catamaran F1X de 5,5 mètres, le trimaran TF10 de 11 mètres et le catamaran F4 de 14 mètres. Le catamaran G4 de 12 mètres n'est plus en production, « mais il met en valeur nos capacités en matière de construction de yachts composites avancés et de hautes performances », note Janssen. «Ce bateau est un bateau de course à foils et un croiseur familial à double usage avec couchettes, cuisine et tête, mais atteint une vitesse de plus de 35 nœuds. La capacité de faire du foil avec plus de 4 000 kilogrammes de poids et un équipage de seulement six personnes - il n'y a toujours pas de concurrence dans ce domaine à moins de yachts de plusieurs millions de dollars de l'America's Cups. "
Transport maritime vers routier et aérien
Avant le début de la visite, Janssen donne un historique de l'entreprise et des structures composites qu'elle produit. Holland Composites a été formé en 1992 par Janssen et Dwarshuis, qui étaient, à l'époque, étudiants à l'Université technique de Delft (TU Delft, Pays-Bas). Ils ont construit des mâts en fibre de carbone pour les catamarans à voile Hobie, une annexe de 18 mètres utilisant du CFRP et du nid d'abeilles Nomex en 1993, et un voilier de 100 pieds utilisant le traitement par infusion de résine en 1994. fibre de carbone utilisant un préimprégné ou une infusion », se souvient Janssen. Cependant, ajoute-t-il, parce que l'entreprise était soumise aux hauts et aux bas typiques du marché maritime et à des projets ponctuels, « Nous avons cherché à nous diversifier, mais nous voulions rester dans les composites avancés par rapport au FRP [ce qui signifie moins avancé, plus de fibre de verre de base et résine polyester]. »
L'entreprise a commencé à explorer des solutions légères pour le transport routier, produisant 35 remorques de camions dotées d'un châssis monocoque en composite verre/fibre de carbone, ce qui a permis de réduire le poids de 3 500 kilogrammes. « Les camions transportaient des charges denses, comme des pommes de terre, et pesaient au maximum avant de remplir leur volume », explique Janssen. Holland Composites a également fabriqué des remorques réfrigérées, ajoute-t-il, « Mais nous étions un peu trop tôt ; le marché n'était pas encore prêt :les entreprises n'étaient pas encore en mesure de calculer les gains annuels résultant du transport de plus d'économies de fret et d'entretien des remorques composites par rapport à leur coût initial plus élevé. »
À peu près au même moment, VRR (Rotterdam, Pays-Bas), un fournisseur de solutions de fret aérien personnalisées, a approché l'entreprise. « Ils travaillaient pour Airbus, Boeing et les compagnies aériennes », se souvient Janssen. « Nous avons développé un conteneur poids plume avec une monocoque en composite carbone/fibre d'aramide, qui n'est toujours pas égalé en termes de faible poids aujourd'hui », dit-il. Bien que Holland Composites en ait fabriqué quelques milliers, le marché est rapidement devenu saturé de produits FRP à faible coût.
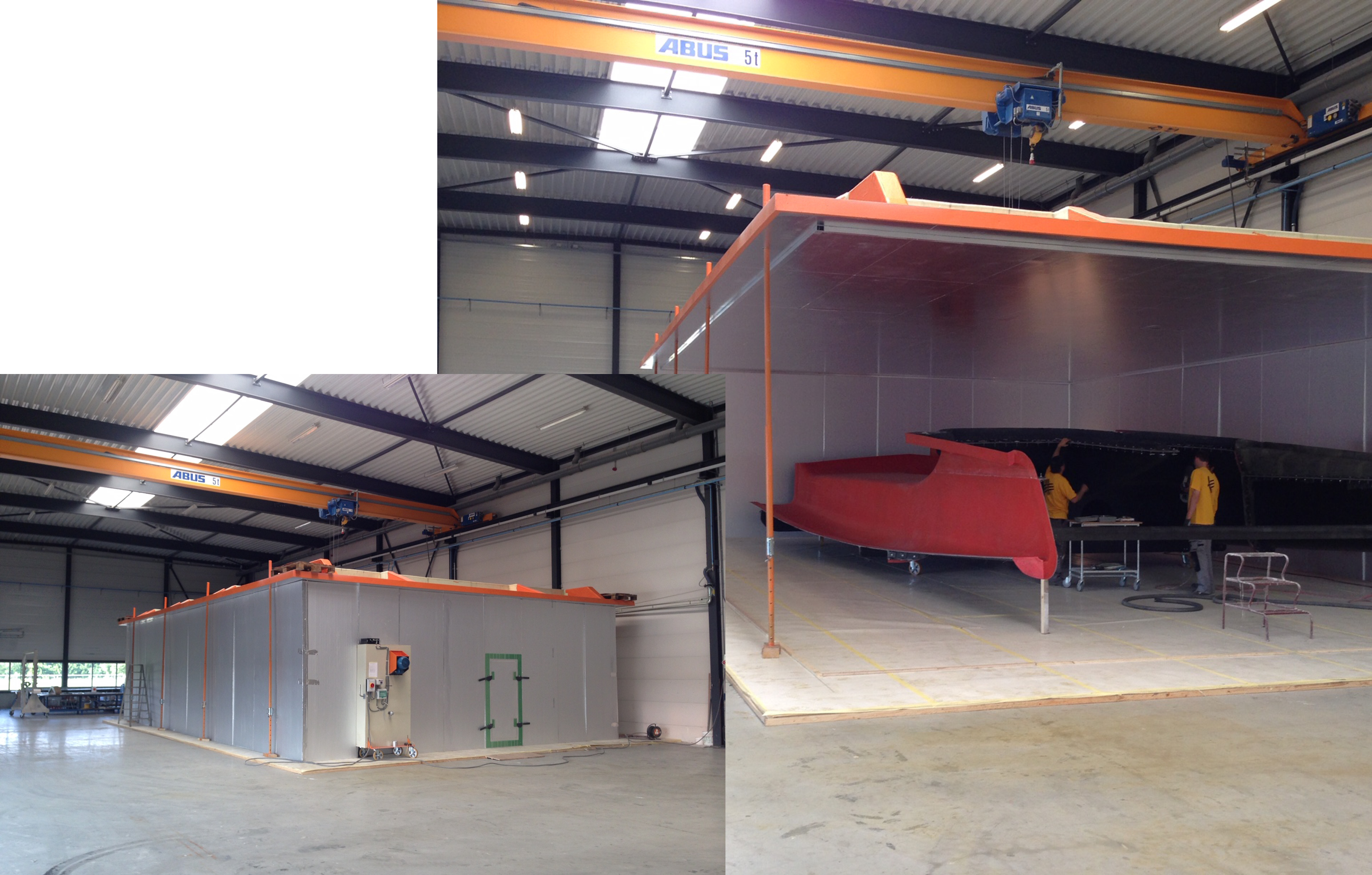
Structures durcies à l'OOA. De grandes structures en composite de carbone pour sa marque DNA Performance Sailing de voiliers multicoques à foils sont durcies dans des fours flexibles (à droite) comprenant des panneaux isolés avec chauffage et circulation d'air commandés par ordinateur depuis une unité extérieure (en médaillon).
La marine reste une force essentielle
En 1999, la marine néerlandaise a approché Holland Composites pour produire des dômes sonar composites en fibre de verre solide pour les sous-marins. "Ceux-ci étaient traditionnellement construits en deux moitiés collées ensemble", explique Janssen, "mais la couture provoque une perturbation dans le champ de" vision ". On nous a demandé de les construire en une seule pièce. Ces dômes sonar sont grands — 11,5 mètres sur 3 mètres sur 3 et 45 à 110 millimètres d'épaisseur — et difficiles à infuser, comprenant 5 000 kilogrammes de résine hybride ester vinylique/époxy fournis par Romar-Voss Composites (Roggel, Pays-Bas). La structure finie pèse 6 500 kilogrammes. Ils doivent être rigides et résister aux charges de claquement car ils sont situés à l'avant de la coque. « Nous devons également faire correspondre la densité et la transparence sonar de l'eau », explique Janssen. « Nous faisons cela pour les navires de type destroyer pour un certain nombre de forces navales à travers le monde. »
À l'autre extrémité du spectre des poids se trouvent les multicoques à foils DNA Performance. « Nos petits bateaux ont été les premiers catamarans à foils en compétition », explique Janssen. Holland Composites produit également les hydrofoils composites pour les yachts de course record comme l'équipe ARGO de MOD70 et Beau Geste . "Nous avons une technique en interne qui peut créer des pièces très chargées sans défaillance, et une méthode de production unique pour ces feuilles très performantes", ajoute-t-il. « Nous travaillons avec les meilleurs marins du monde pour atteindre le prochain niveau de performance en foil et produire tous les foils pour les bateaux de la classe olympique NACMA17. »
Le rouf léger en CFRP que Holland Composites produit pour les navires de service/support du parc éolien de Windcat Workboats (voir « Les roufs composites réduisent le poids ») utilise une construction en sandwich de mousse CFRP infusée de résine pour une rigidité permettant d'obtenir une grande portée ouverte sans piliers à l'intérieur de la cabine. « Le rouf monocoque est suffisamment léger pour que nous puissions le mettre sur de bons amortisseurs pour l'isoler des vibrations du moteur et des vagues dans la coque », explique Janssen. « Windcat est connu pour sa conduite très silencieuse et les bateaux sont très appréciés des grands équipementiers d'éoliennes. Tous ces parcs éoliens doivent être entretenus, il y a donc un nouveau marché pour les catamarans à grande vitesse de 50 à 60 pieds de long. »

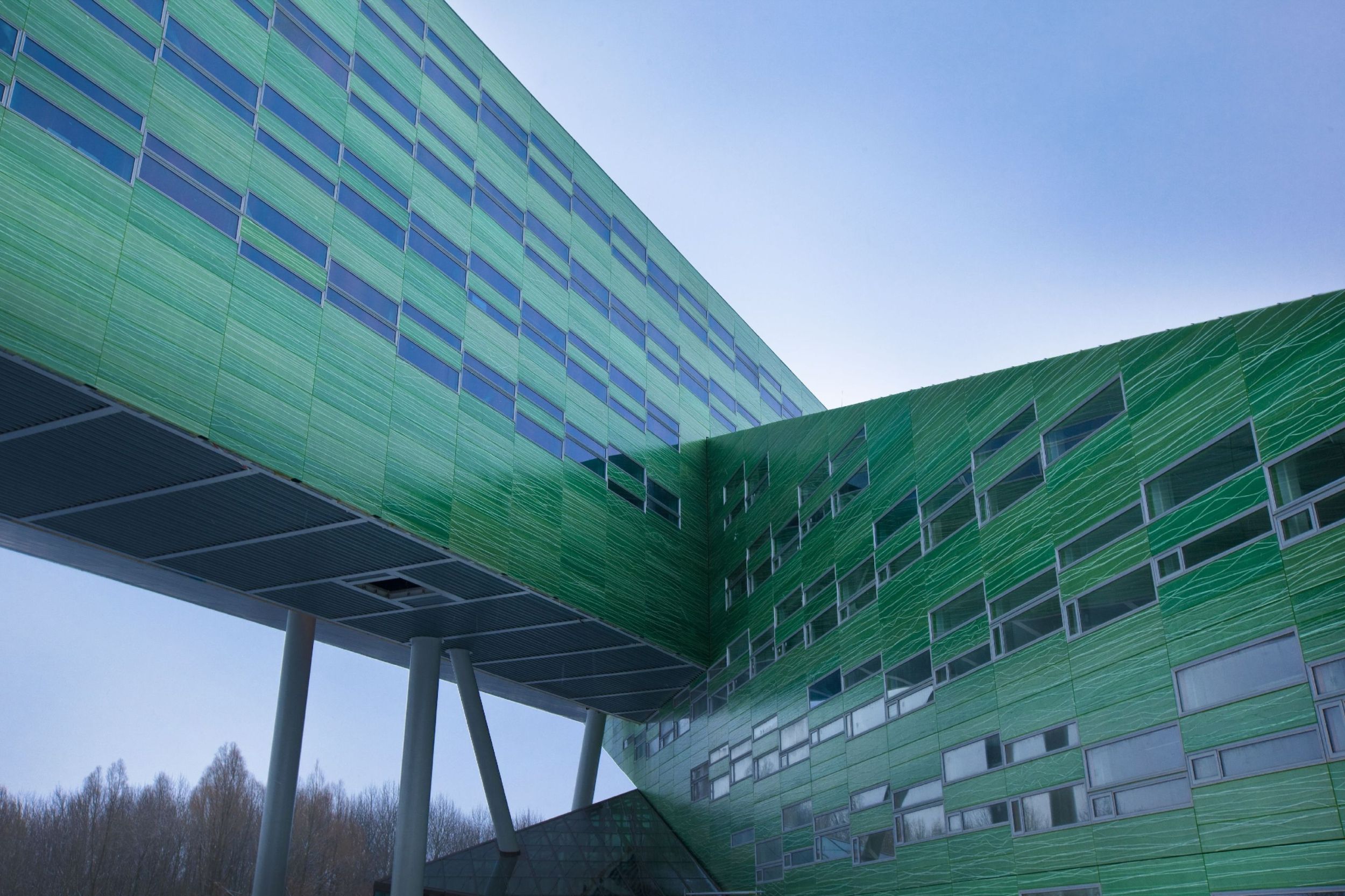
Holland Composites a fourni la façade composite structurelle pour l'Université de Groningen Life Le bâtiment des sciences, utilisant leur système de panneaux translucides RAFICLAD et de grandes tailles de panneaux (3,6 sur 3,3 mètres), permettant des économies de poids et une isolation thermique maximale.
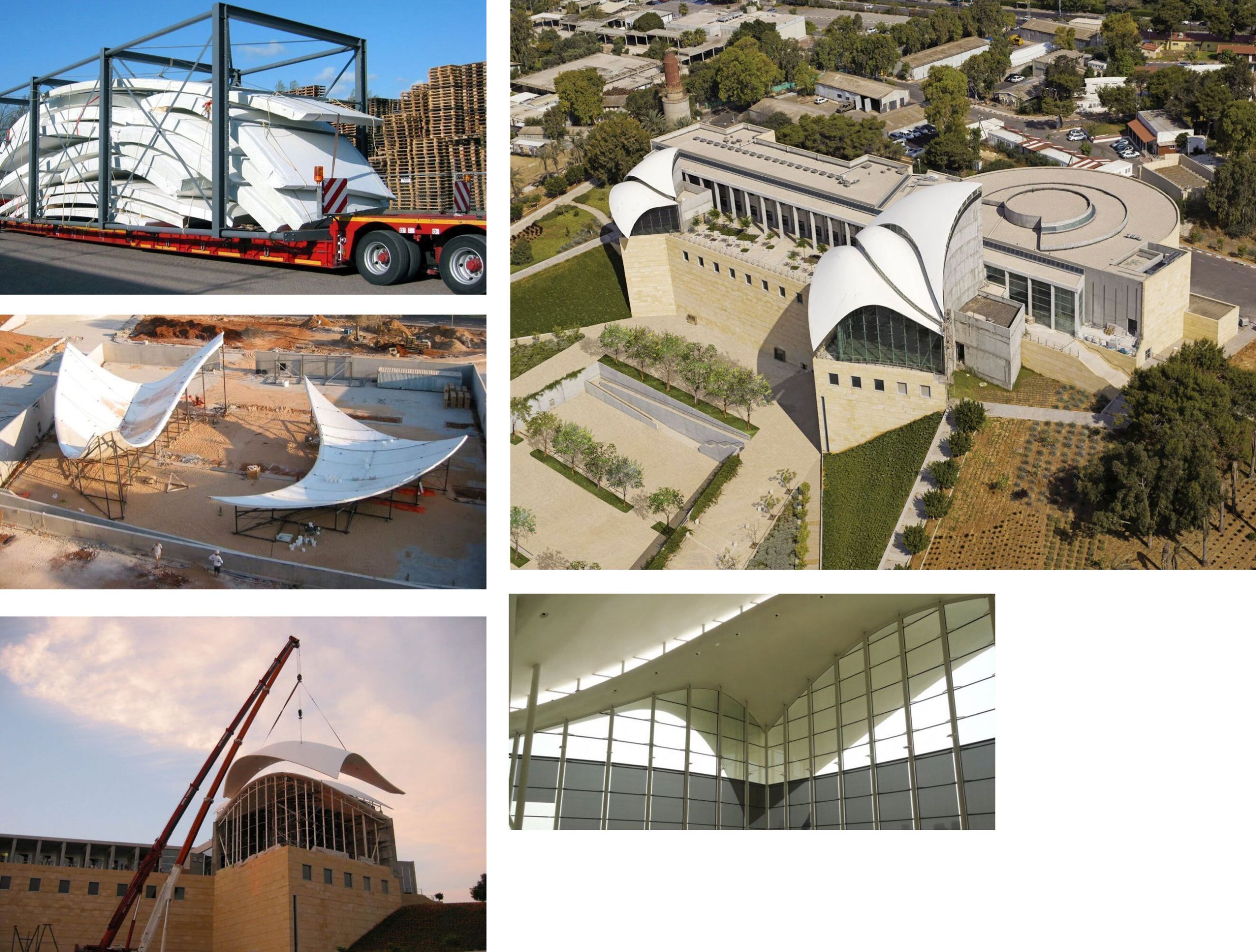
Soixante-quinze sections composites de 40 sur 60 mètres ont été expédiées en Israël, laminées ensemble et hissées en place pour créer les sections de toit en forme d'aile pour le centre Yitzak Rabin à Tel Aviv.
« Tout ce que nous faisons est structurel »
Pour le Centre Yitzak Rabin (Tel Aviv, Israël), l'entreprise a été chargée de construire des structures de toit en forme d'aile qui seraient trop lourdes si elles étaient en béton. « Encore une fois, nous avons créé les sections les plus larges possibles », déclare Janssen. Soixante-quinze sections de 40 mètres sur 60 ont été infusées de résine à l'aide de fibre de verre et de résine d'ester vinylique à base d'époxy, puis expédiées en Israël. Sur place, ceux-ci ont été placés à l'envers dans des gabarits afin de les laminer ensemble en « toits en aile » d'une portée maximale de 31 mètres. Janssen note que le projet était structurellement très difficile. « Ces panneaux ont une épaisseur de 200 à 300 millimètres et maintiennent la façade vitrée ensemble, y compris une section en porte-à-faux de 11 mètres. Le matériau composite peut résister à toutes les forces, vous donnant la possibilité de concevoir de telles travées de toit à suspension libre. »
La tour de l'hôtel Fletcher est un autre de ces projets, achevé en 2012-2013. Il a commencé comme un centre commercial à côté d'une autoroute, mais a nécessité une atténuation acoustique substantielle dans la structure après la décision de convertir le bâtiment en hôtel haut de gamme. « Le squelette en béton ne pouvait pas supporter beaucoup de charges supplémentaires, nous avons donc été appelés pour fournir une solution légère », explique Janssen. Holland Composites a conçu des panneaux composites de 8,5 sur 3 mètres auxquels la façade en verre plat pouvait être fixée. « Le verre s'accroche en fait à nos panneaux, ce qui aide à gérer la charge », souligne-t-il. « Nous avons ensuite fixé nos panneaux à la charpente en béton. Cette combinaison du verre devant les panneaux sandwich composites avec l'entrefer entre les deux crée une énorme barrière acoustique. Chaque panneau composite était prêt à peindre pour les murs intérieurs d'un côté et fini avec des revêtements résistants aux UV sur le côté extérieur faisant face au verre.
« C'était également un moyen très rapide de monter un revêtement sur un bâtiment de forme ronde », explique Janssen. « Nous avons monté la façade complète en une seule étape et obtenu une valeur d'isolation R de 8, ce qui est le double de la cote des matériaux extérieurs de construction normaux. Développant cette idée, Janssen dit qu'il pense que la neutralité énergétique est essentielle à la construction future de bâtiments. « Peu d'énergie est nécessaire pour chauffer les bâtiments qui utilisent notre revêtement composite structurel, notre approche est donc très efficace pour atteindre une empreinte nette zéro. BREEAM est la certification néerlandaise pour l'efficacité énergétique, et les deux premiers bâtiments qui y sont parvenus utilisent nos composites. »
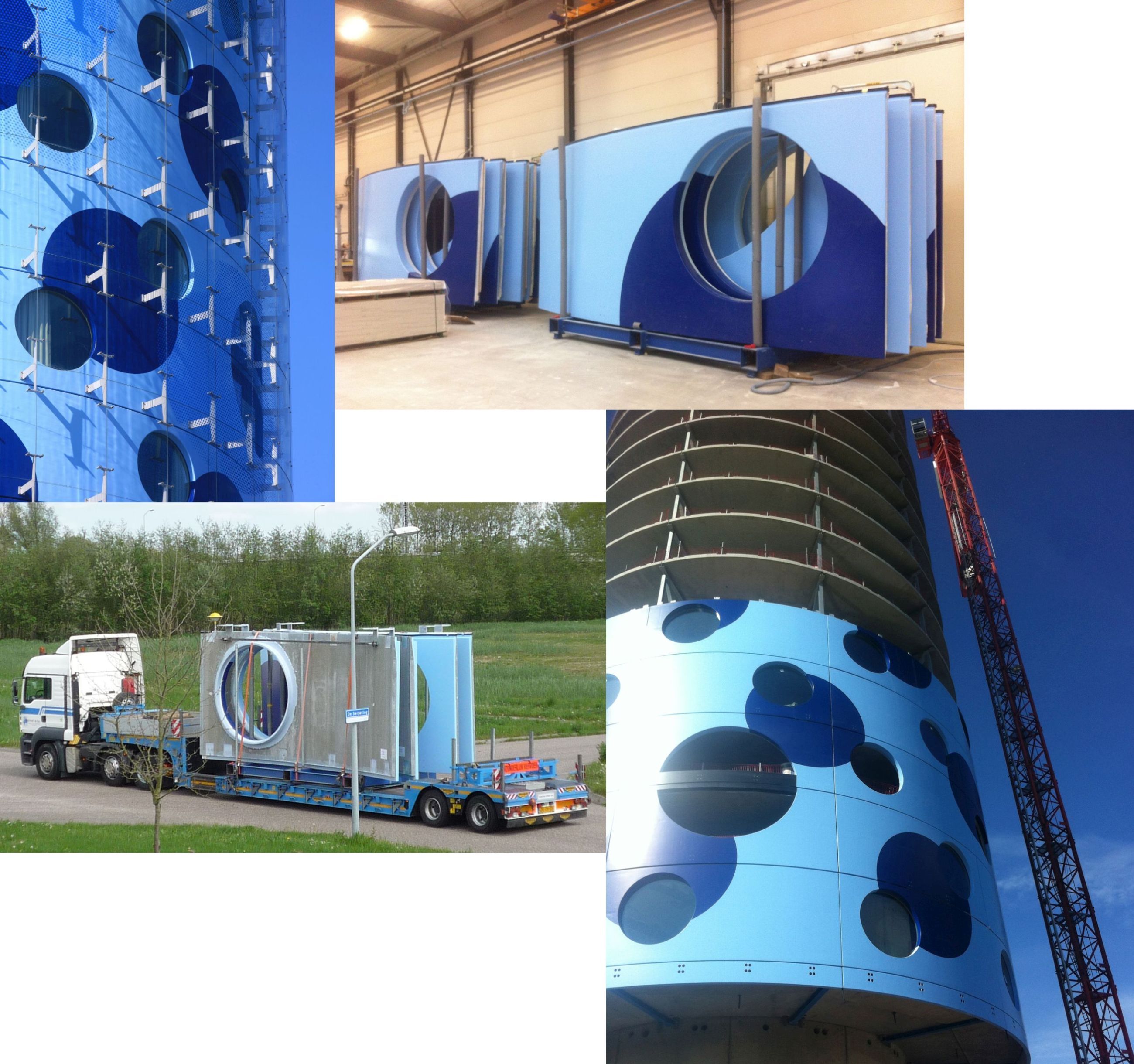
Pour l'hôtel Fletcher, Holland Composites a réalisé un extérieur esthétique et insonorisant en fixant des panneaux composites incurvés au squelette en béton du bâtiment, auquel la façade en verre pouvait être fixée sans ajouter de charge permanente excessive.
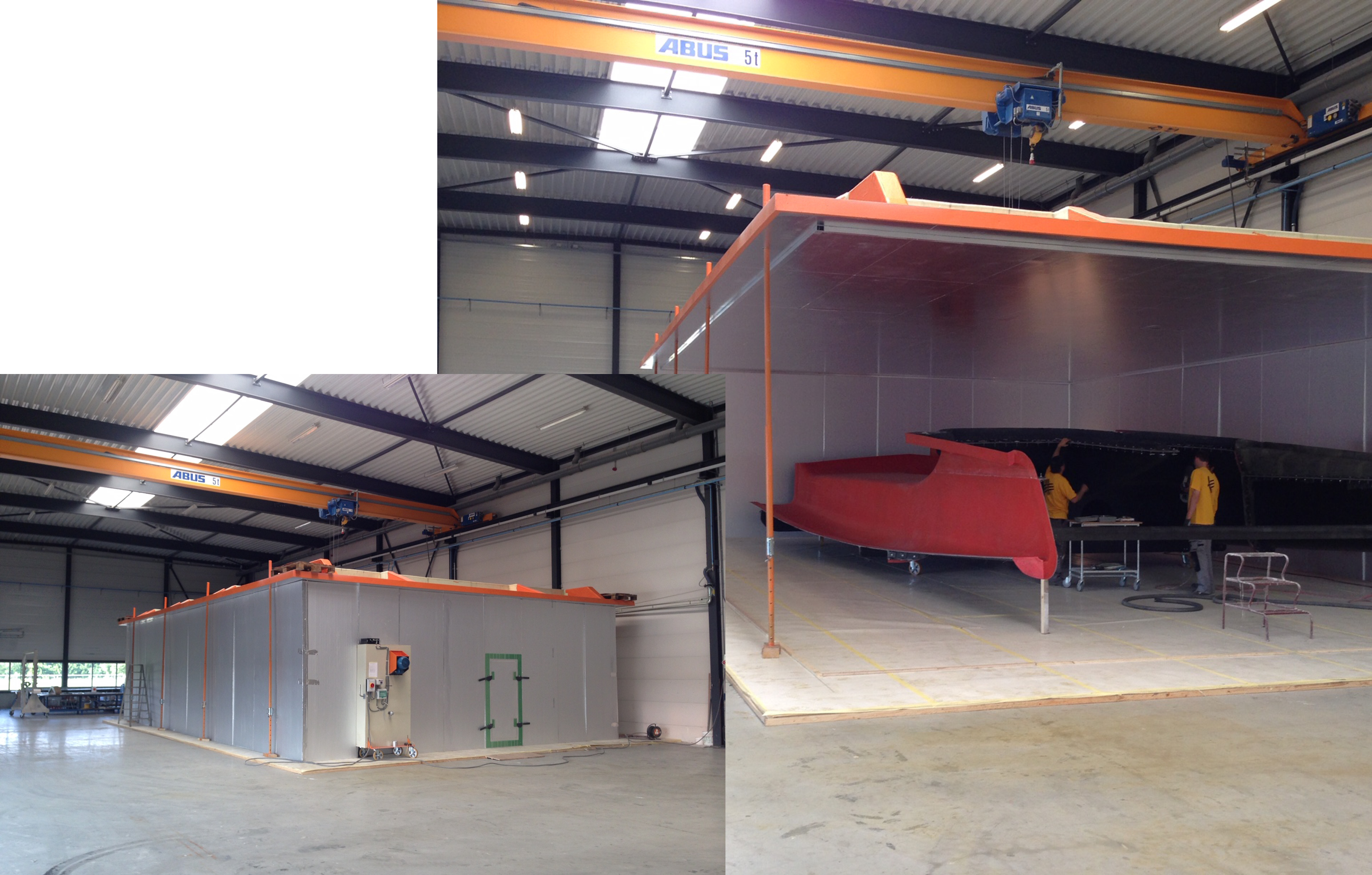
Janssen désigne le Stedelijk Museum of Contemporary Art au centre-ville d'Amsterdam comme le summum des projets de construction technique de Holland Composites (voir « Grand musée, grandes structures »). « Ce fut un exercice extrême de gestion de la dilatation thermique et illustre ce que nous faisons. » Holland Composites a également été le pionnier des façades structurelles antisismiques, qui sont désormais requises dans certaines parties des Pays-Bas, explique Janssen, car le sol a été déstabilisé en raison de la fracturation hydraulique (fracking). Le bâtiment Wiebenga à Groningue présente une façade antisismique qui peut se déplacer de 30 centimètres sans défaillance. « L'acier et le béton typiques ne peuvent pas gérer ce type de mouvement », ajoute-t-il.
Bien qu'il soit difficile d'équilibrer la myriade d'exigences avec les coûts et le calendrier lors de la construction de structures, Janssen note que le plus gros problème actuellement est la résistance au feu. « De mauvaises implémentations de composites ont valu à l'industrie des composites une mauvaise réputation à cet égard », explique-t-il. « Nous n'utilisons désormais que des matériaux résistants au feu sur ces projets de construction et effectuons des tests d'incendie conformément aux réglementations approuvées. »
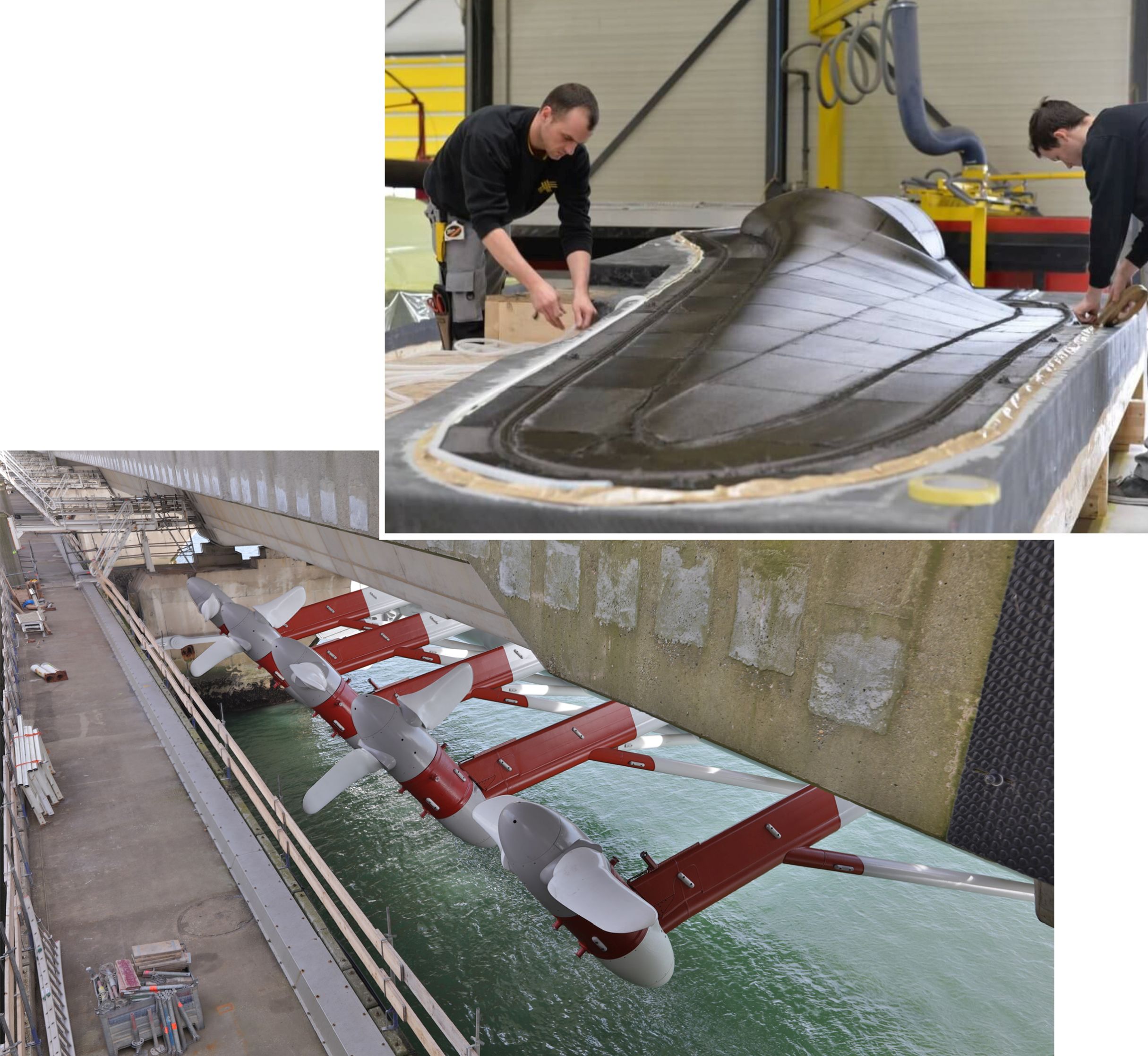
Holland Composites construit des aubes pour les générateurs de turbine marémotrice en utilisant un préimprégné en fibre de carbone, durci dans un autoclave, pour gérer les charges importantes placées sur ces structures à faible vitesse et à couple élevé.
Énergies offshore et renouvelables
Holland Composites a également des contrats à long terme dans l'industrie pétrolière et gazière offshore. « Les composites ici offrent non seulement un poids léger et une résistance à la corrosion, mais également une réparation facile », explique Janssen. « Les plates-formes et les navires offshore ne sont pas autorisés à s'arrêter. Cependant, la réparation des structures métalliques nécessite des soudures et des étincelles, la production doit donc être arrêtée en raison du risque d'incendie. Nous pouvons réparer les composites sans cette interruption. La société a de nouveaux clients qui demandent de tels produits pour une variété de constructions offshore.
Elle a également fabriqué des pales pour hydroliennes. La récupération de l'énergie marémotrice est encore nouvelle, dit Janssen, mais les premiers projets ont été achevés et les résultats sont impressionnants. « Les turbines marémotrices offrent une source d'énergie fiable », explique-t-il. « Les marées sont toujours là, par rapport à l'éolien et au solaire, vous pouvez donc prévoir de manière fiable la puissance de sortie, ce qui est essentiel pour les compagnies d'électricité. » Holland Composites utilise un préimprégné en fibre de carbone durci à l'autoclave pour ces lames car les charges sont énormes. « Les lames se déplacent à basse vitesse mais avec un couple élevé », explique Janssen. "Vous voulez que la conversion maximale de la vitesse du rotor dans le moteur produise de l'énergie, les fabricants de turbines ont donc besoin de structures solides mais efficaces qui sont conçues pour tirer le plus d'énergie possible des mouvements de marée."
Chaque turbine a deux pales de 3 mètres de long et 18 millimètres d'épaisseur. Il y a cinq turbines par générateur de marée. « La charge sur ces aubes de turbine est décrite comme égale à celle d'un remorqueur de 13 600 chevaux qui avance à pleine puissance », explique Janssen, « mais le client a également besoin d'aubes rigides, légères et nécessitant peu d'entretien avec une bonne résistance à la fatigue pour la durabilité. L'acier aurait été trop lourd, rendant les générateurs moins efficaces. Holland Composites fabrique uniquement les lames; les carénages, le cône de nez et le revêtement non structurel sont fabriqués par des fabricants de FRP.
Installation tournée vers l'avenir
La visite commence dans la zone de layup, qui comprend une grande table de layup, des pièces pour les voiliers de performance DNA et une variété de foils CFRP en cours de préparation pour l'installation. Le plafond est bas ici à cause d'une mezzanine pour le stockage des matériaux. Celui-ci s'ouvre sur un étage de production à haut plafond, doté d'une machine de découpe automatisée Zünd (Altstätten, Suisse) juste au-delà de la zone de drapage. Le cutter a une plage de coupe de 5,7 x 2,8 x 0,3 mètre pour traiter des matériaux préimprégnés, des fibres sèches et des mousses jusqu'à 25 millimètres d'épaisseur.
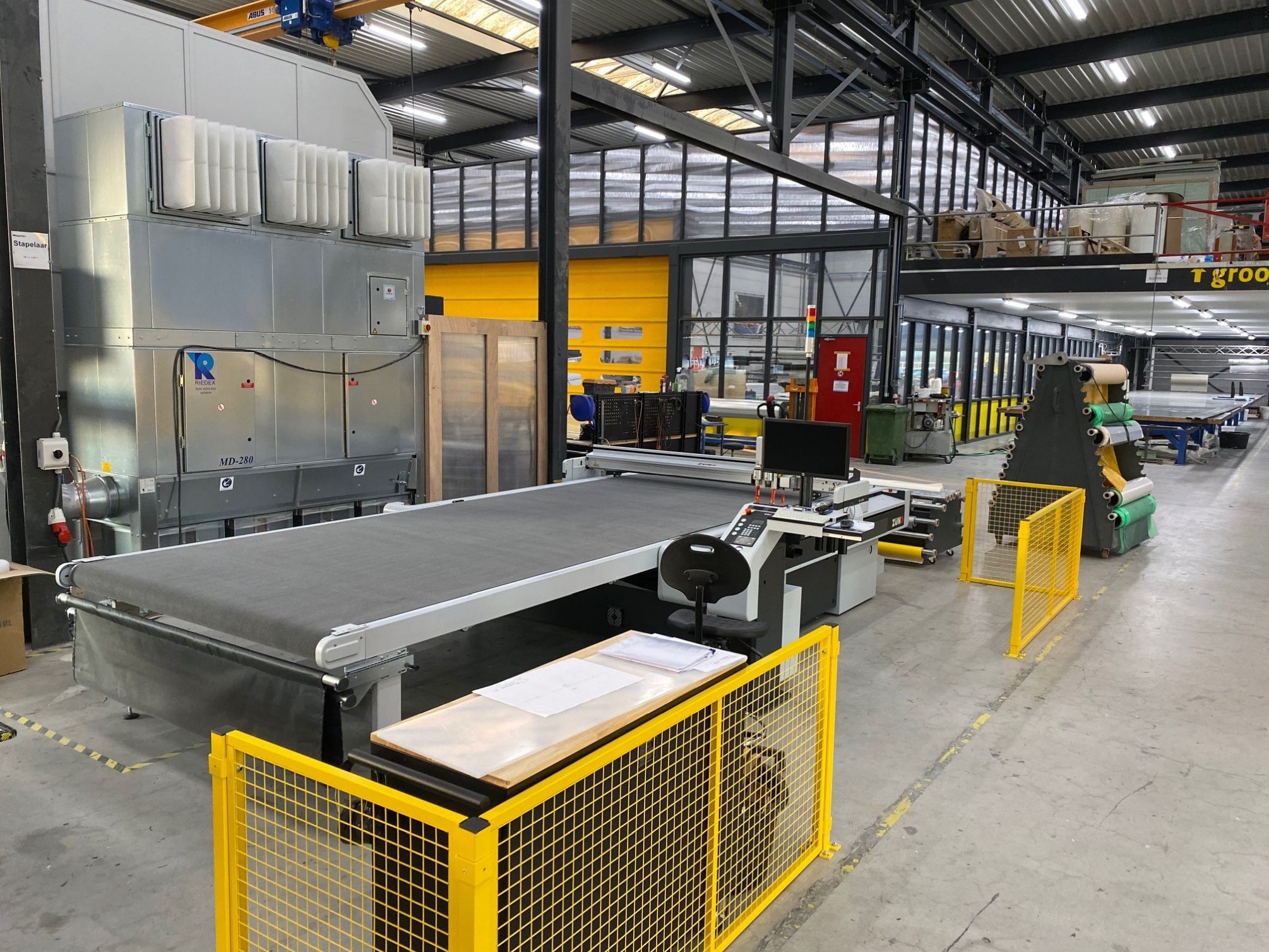
Le découpeur automatisé Zünd au premier plan fournit des renforts découpés et de la mousse à la zone de drapage, qui peut être vue à l'arrière, à droite, avec la mezzanine de stockage des matériaux au-dessus. La zone d'outillage fermée se trouve derrière la porte à enroulement jaune, vue ici derrière le côté du centre d'usinage CMS, qui est à côté de la table de coupe Zünd.
En nous détournant de la fraise Zünd, nous marchons jusqu'à une salle d'outillage vitrée qui jouxte la zone de drapage. En entrant par une porte à enroulement jaune, plusieurs outils sont en cours et les pièces sont durcies sous des sacs sous vide. « Nous fabriquons nos propres moules », explique Janssen. "Pour les pièces en CFRP, nous utilisons du CFRP ou de l'aluminium pour l'outillage, ainsi que des trous de ventilation pour la circulation de l'air dans les outils, ce qui permet d'assurer un durcissement uniforme sur toute la pièce."
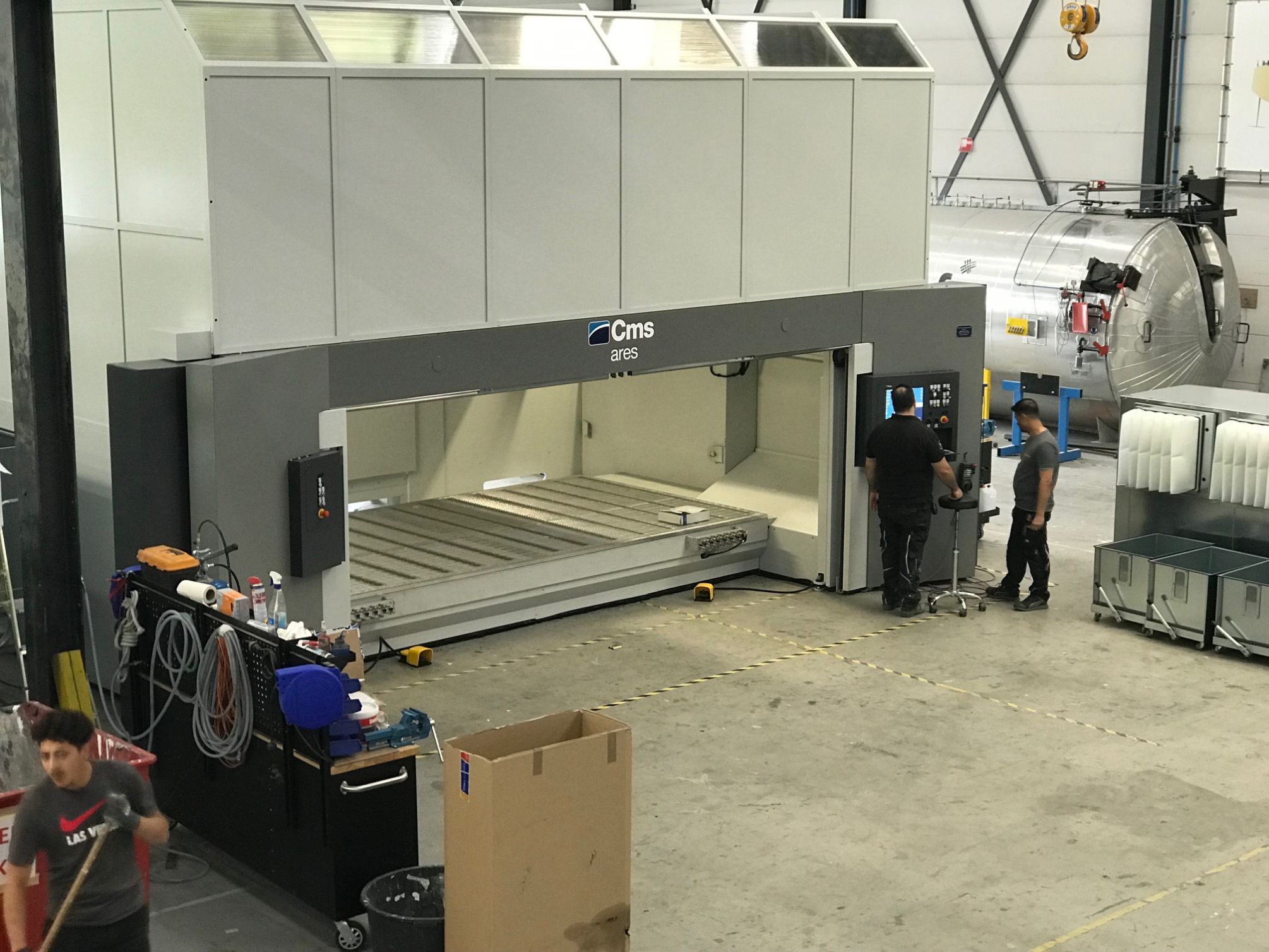
Le centre d'usinage CMS est situé entre la table de découpe à sa gauche (hors de vue) et l'autoclave (à l'extrême droite, contre le mur).
En revenant de la salle d'outillage, nous passons devant le centre de fraisage CNC 5 axes de 5 x 2 x 1,8 mètres (CMS SpA, Zogno, Italie) et pouvons voir l'autoclave de 6,5 x 2,2 mètres (Tankbouw Rootselaar, Nijkerk, Pays-Bas). « Nous polymérisons généralement à 125° C avec une pression de 6 bars », note Janssen.
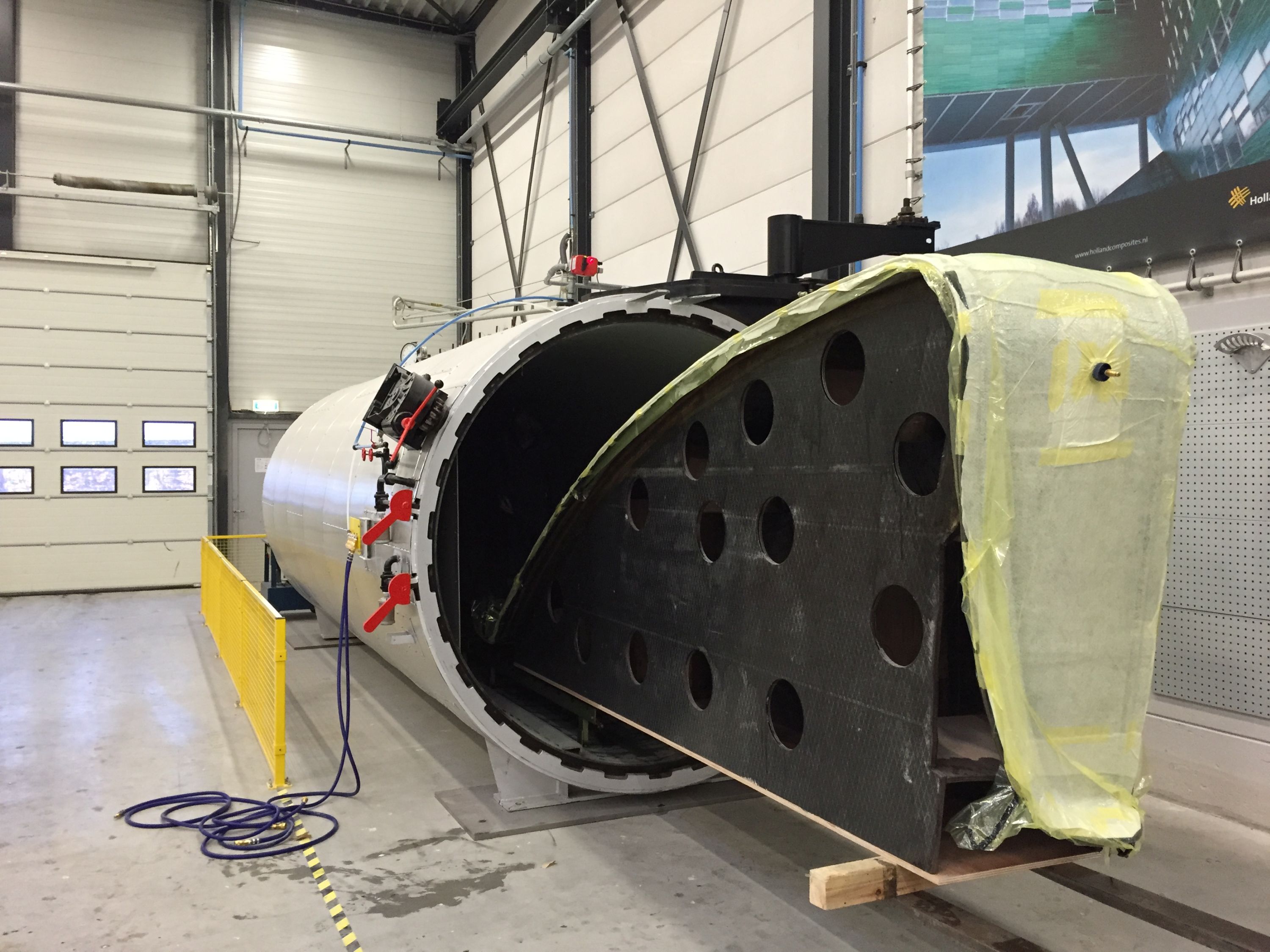
L'autoclave est également vu ci-dessous avec un outil CFRP (notez les trous pour la ventilation de l'air) et une grande feuille de CFRP durcie sous un sac sous vide pour un voilier multicoque performant.
Le mur à côté de l'autoclave coupe la zone de production en deux moitiés, sur toute la longueur du bâtiment le long de la salle d'outillage. Nous faisons demi-tour et passons par une porte menant à la seconde moitié de l'usine de Holland Composites, qui contient une machine de découpe au jet d'eau (plage de coupe de 8 x 2 x 0,5 mètre), plusieurs fours dimensionnés jusqu'à 15 x 10 -par-3,5 mètres, et la cabine de peinture de l'entreprise de 19-par-12-par-3,5 mètres. "Actuellement, nous produisons de grands panneaux pour un projet au Qatar et une série de roufs CFRP pour les bateaux Windcat", explique Janssen.
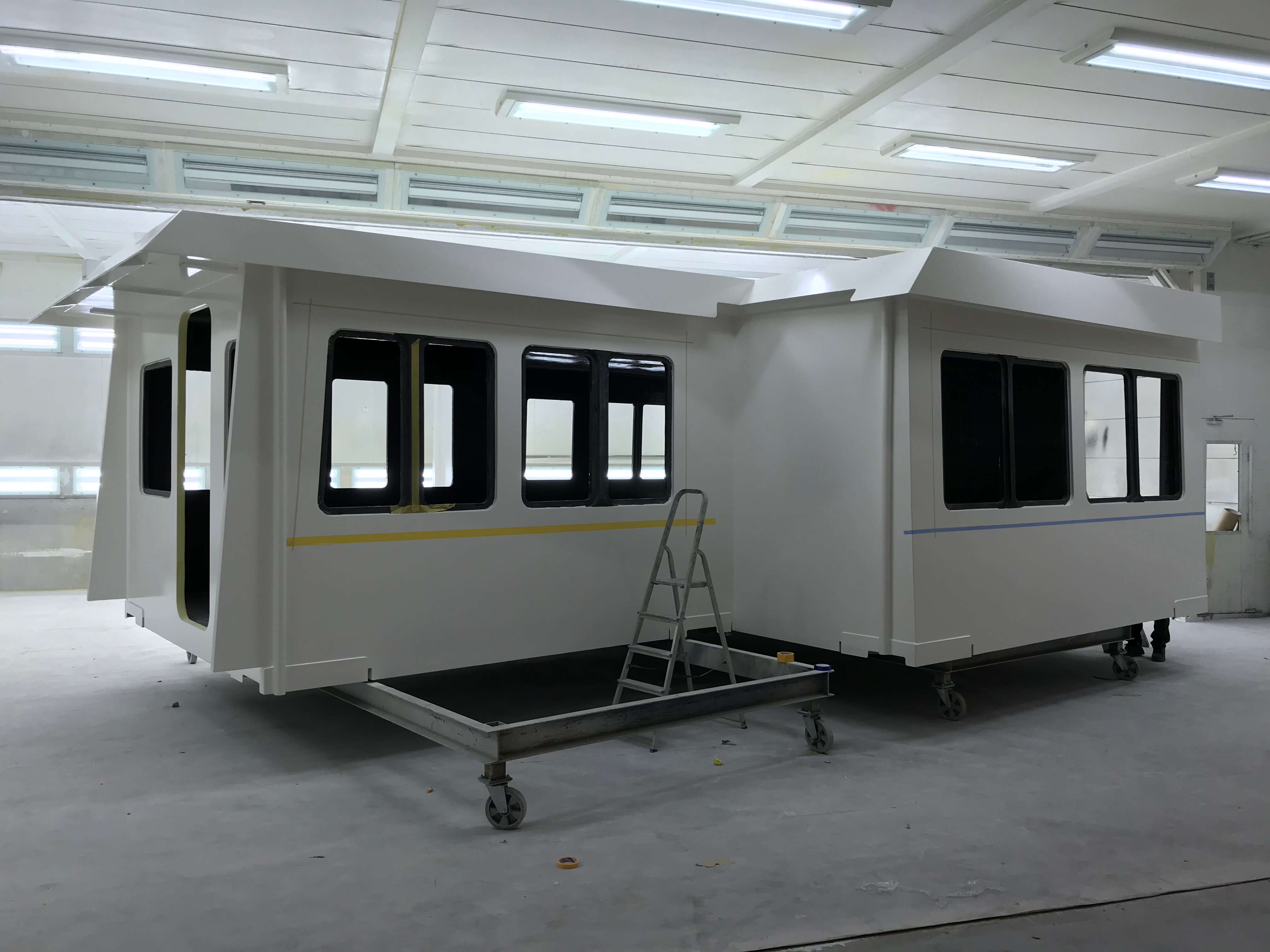
Les roufs CFRP que Holland Composites produit pour les catamarans Windcat Workboats sont peints dans la cabine de peinture de 19 x 12 x 3,5 mètres.
La dernière installation de Holland Composites est une imprimante Massivit 3D (Lod, Israël) 1800 Pro avec un volume de construction de 145 par 111 par 180 centimètres. « Nous sommes des partenaires qui innovent dans l'impression 3D de moules à l'aide de trois têtes d'impression, où deux impriment les peaux d'un sandwich et la buse centrale imprime la structure de remplissage ou de réseau entre les deux », explique Janssen. « Nous utiliserons des matériaux renforcés de fibres dans les développements futurs, mais pour l'instant, nous pouvons imprimer un outillage précis avec un minimum de fraisage. Nous utilisons beaucoup moins de matière et voyons des temps de production de moules très rapides. Nous avons maintenant une chaîne de processus complète, avec la possibilité de passer de la conception aux moules et aux pièces peintes dans un court laps de temps. »
Il note que la société explore toujours comment augmenter son utilisation de l'automatisation pour faire progresser ses produits, mais sans augmenter les coûts. « C'est une question d'ingéniosité. Nous sommes attirés par des problèmes très complexes que peu d'autres osent aborder, mais en tant que constructeurs de bateaux, nous avons toujours dû être très créatifs avec des ressources limitées. Pour ce que nous faisons dans les composites, nous voyons de nombreuses opportunités à l'avenir. »
Résine
- Les fabricants visitent United Safety for Plant Tour, discussion sur les meilleures pratiques
- CompositesWorld SourceBook 2022
- Dépannage du thermoformage des composites thermoplastiques
- L'évolution des composites additifs
- Composites thermoplastiques :support de pare-chocs structurel
- Les Pays-Bas présenteront l'expertise du pays en matière de composites au JEC World 2019
- TPAC et TPRC développent un procédé de recyclage des composites thermoplastiques
- Soudage de composites thermoplastiques
- Composites hautes performances en Israël