Visite de l'usine :Veelo Technologies, Woodlawn, Ohio, États-Unis
Que faites-vous lorsque la fibre de nanotubes de carbone (CNT) que votre entreprise essayait de commercialiser ne fournit pas le performances requises par vos clients potentiels, dont l'US Air Force et Boeing (Chicago, Ill., US) ? Vous pivotez, revenez à la planche à dessin et utilisez votre expertise avancée en matière de traitement des matériaux et des composites pour développer d'autres solutions. « Nous utilisons souvent des nanomatériaux, mais nous ne sommes en aucun cas une entreprise de nanomatériaux », déclare Joe Sprengard, PDG de Veelo Technologies. « Nous sommes une entreprise de matériaux de pointe spécialisée dans les matériaux conducteurs d'électricité et les solutions de chauffage non métalliques. Le fil conducteur entre notre concentration initiale sur le développement de fibres et de feuilles CNT continues et notre portefeuille actuel de produits — protection contre la foudre (LSP) et blindage électromagnétique, couvertures chauffantes pour un traitement efficace des composites et systèmes de dégivrage électrothermique non métalliques — est notre capacité pour développer de nouveaux matériaux qui non seulement offrent de nouveaux niveaux de performance, mais répondent également aux exigences de poids et de coût. »
L'entreprise est passée de quatre à 24 employés et a emménagé dans une nouvelle usine de fabrication de 20 000 pieds carrés à Woodlawn, une banlieue de Cincinnati située à un mile du siège de GE Aviation à Evendale et à une heure au sud de l'Air Force Research Laboratory (AFRL) à la base aérienne de Wright-Patterson à Dayton, Ohio. Sprengard dirige la CW visite du nouveau site de production de Veelo Technologies, en parcourant l'évolution de l'entreprise, de fournisseur de nanomatériaux à spécialiste avancé de produits étendus à partenaire d'innovation pour les futurs composites.
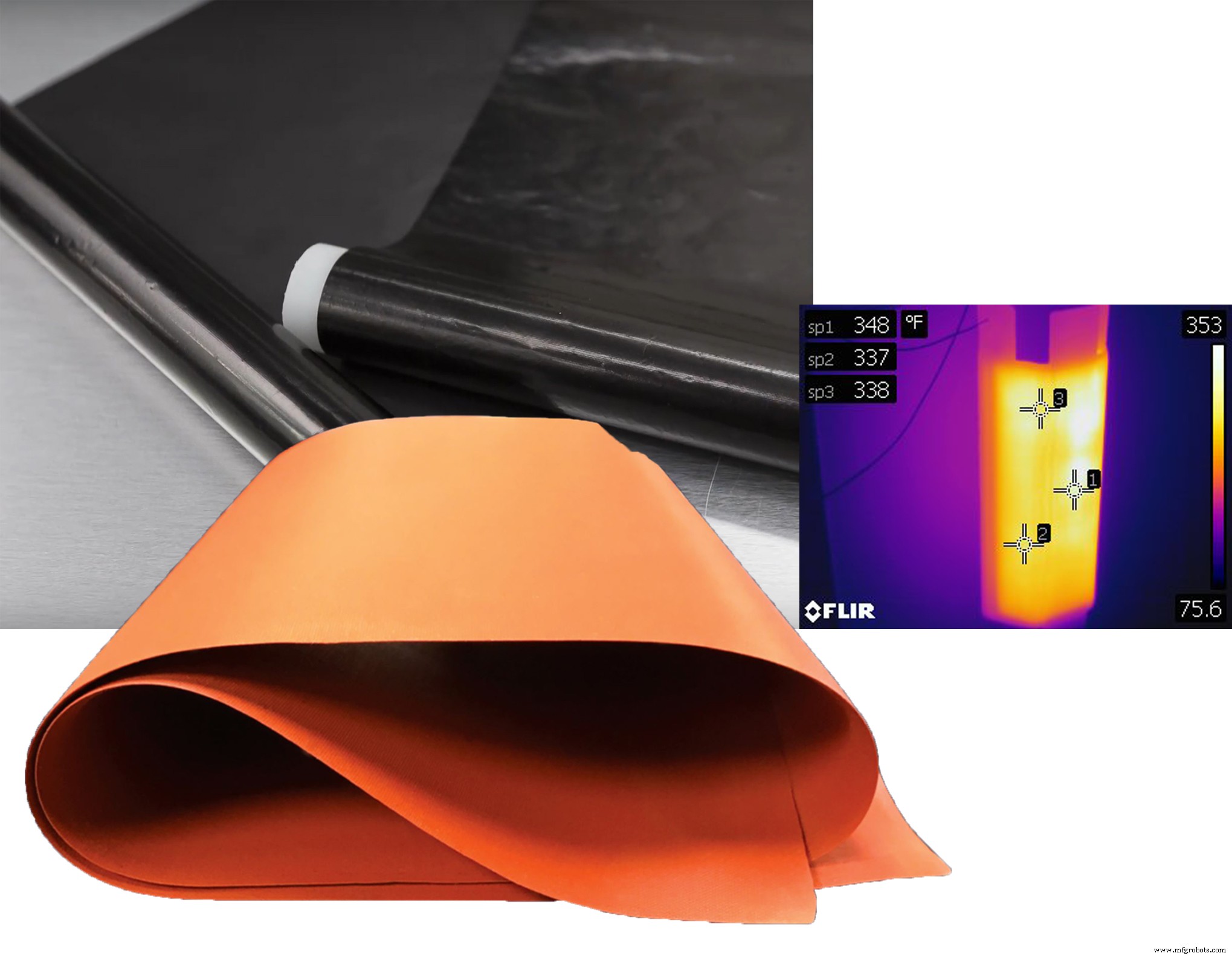
Du nano aux composites multifonctionnels et au traitement
Veelo Technologies a commencé par développer des feuilles de fibres CNT continues (en haut à gauche) mais a maintenant évolué pour utiliser une gamme de matériaux dans ses produits pour la protection contre la foudre et des couvertures chauffantes non métalliques pour le traitement des composites et les systèmes de dégivrage pour les aérostructures (en bas et à droite) .
Fibres et feuilles NTC
Veelo Technologies a été créée à l'origine par l'Université de Cincinnati (UC) sous le nom de General Nano. L'université avait produit les matrices CNT les plus longues au monde - 18 millimètres de long - en 2007. années, nous essayions de comprendre comment convertir ces longs NTC en fibres à haute résistance et à grande échelle, ce qui intéresse l'AFRL. Mais les propriétés ne se sont jamais matérialisées. »
Ainsi, l'entreprise a pivoté, développant un moyen de convertir les CNT en une feuille continue. Boeing s'est intéressé, considérant la technologie comme une solution potentielle à ses besoins en LSP et en blindage contre les interférences électromagnétiques (EMI) pour ses structures composites d'avions. "En moyenne, les avions commerciaux sont touchés par la foudre toutes les 1 000 heures", explique Sprengard. Bien que la fibre de carbone soit conductrice, les résines matricielles des composites ne le sont pas. Ainsi, les aérostructures en polymère renforcé de fibres de carbone (CFRP) que Boeing produisait en nombre record pour ses avions commerciaux 777 et 787 reposaient sur des feuilles de métal déployé et d'autres solutions métalliques pour conduire rapidement le courant électrique vers une connexion mise à la terre afin d'éviter les dommages causés par la chaleur. . "Mais le treillis métallique est lourd, produit beaucoup de poids parasite et peut être difficile à traiter dans les pièces composites", explique Larry Christy, ingénieur en développement de produits de Veelo Technologies.
En 2015, Boeing a lancé une poussée à l'échelle de l'entreprise pour développer une solution LSP de nouvelle génération, et General Nano était un partenaire clé. CW a visité General Nano peu de temps après, en 2016, à son emplacement d'origine dans un incubateur d'entreprises basé à Cincinnati qui abritait plusieurs start-ups. Christy a dirigé cette visite des laboratoires de l'entreprise et a discuté de l'évolution de la technologie alors en cours. "L'efficacité du LSP métallique et du blindage diminue avec la fréquence", a-t-il expliqué. « Vous devez améliorer la conductivité et réduire l'impédance mais avoir une épaisseur inférieure à 25 microns. Cependant, les jonctions CNT à CNT ajoutent de la résistance à l'intérieur de la feuille. De 2014 à 2016, nous avons multiplié par 12 la conductivité et prouvé une solution intégrée pour le blindage à une fréquence de 200 [mégahertz] MHz avec une économie de poids de 25 % par rapport au métal. Mais nous devons encore réduire l'épaisseur. »
À ce stade, la société avait développé la capacité de produire des NTC alignés sur un substrat de 5 pieds de large dans des longueurs mesurant des centaines de pieds. Elle fabriquait également du papier CNT de 20 grammes par mètre carré, 2 millimètres d'épaisseur et des matériaux non tissés - une sorte de non tissé continu CNT - en utilisant un réseau de partenaires de fabrication à façon avec une capacité excédentaire sur leur équipement de fabrication de papier. « Cette approche nous donne de la flexibilité », a expliqué Christy, « et nous permet de nous concentrer sur le travail avec nos clients pour ajouter des fonctionnalités et adapter les propriétés et le format de nos produits. » L'entreprise avait également été invitée à réaliser des bandes en continu, qu'elle a de nouveau réalisées à l'aide de son réseau à péage.
Pivoter vers des produits larges hautes performances
Cette adaptabilité et cette volonté de modifier ses produits en fonction des besoins des clients étaient essentielles, car environ une décennie après son existence, l'entreprise a compris que son avenir pourrait être très différent de son passé. Christy a expliqué qu'il y avait de multiples besoins, non seulement pour le LSP mais aussi pour le blindage EMI. « Il faut adapter les performances électriques de chacun. Les propriétés du treillis métallique dépendent de la fréquence et diminuent à mesure que la fréquence augmente en raison des fuites des trous dans la feuille. Nos performances augmentent avec la fréquence car nos produits sont continus, sans trous ni fuites. Les NTC surpassent les métaux à hautes fréquences, ils sont donc parfaits pour les applications de radiofréquence à haute intensité (HIRF) et de communications par satellite à haute puissance. Les NTC n'ont pas non plus d'effet cutané , ce qui est un problème avec les métaux. L'effet de peau est la tendance du courant alternatif à éviter de traverser le centre d'un conducteur, limité à sa surface ou à sa peau, ce qui réduit efficacement la section transversale disponible pour transporter le courant et augmente la résistance. Christy poursuit : « Mais les CNT ne peuvent pas rivaliser avec les basses fréquences. Leur conductivité n'est tout simplement pas assez élevée et il y a trop de perte de signal. Donc, nous cherchons des hybrides. »
"Cela a conduit à d'autres matériaux en feuille qui ne sont pas basés sur des nanomatériaux", explique Sprengard. « Nous avons développé VeeloVEIL, une solution en fibre de carbone métallisée pour LSP qui est 70 % plus légère que la feuille de cuivre expansée (ECF) et répond aux exigences de protection contre la foudre de la zone 1A. » La zone 1A comprend le radôme/le nez, les extrémités des ailes, les nacelles et les extrémités de l'empennage d'un avion et doit supporter 200 000 ampères de courant électrique, tel que défini par les exigences de la Federal Aviation Administration (FAA) des États-Unis (voir « Stratégies LSP pour les avions composites » et « LSP pour structures composites »). « VeeloVEIL est quatre fois plus conducteur et pourtant moitié moins lourd que les autres non-tissés métallisés », poursuit-il. « Cela est possible grâce à la chimie et au traitement des matériaux que nous avons développés. »
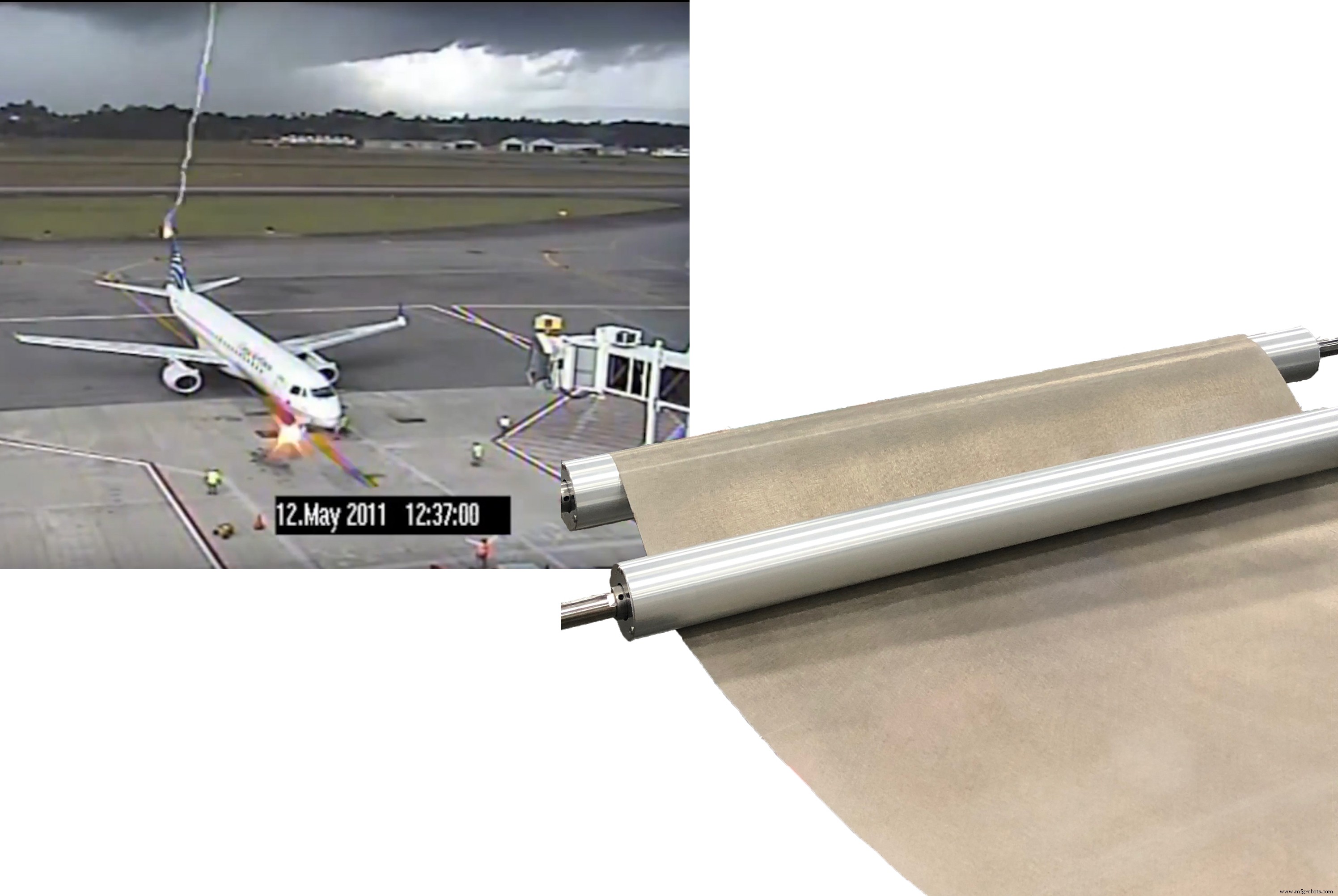
LSP de nouvelle génération pour les aérostructures
Les avions commerciaux sont touchés par la foudre, en moyenne, toutes les 1 000 heures. Le non-tissé en fibre de carbone métallisé VeeloVEIL répond aux exigences de protection contre la foudre (LSP) de la zone 1A pour les avions composites avec un poids inférieur de 70 % par rapport à une feuille de cuivre expansée. Conçu pour être traité par des machines automatisées de placement de fibres/pose de ruban (AFP/ATL), VeeloVEIL offre une conductivité perturbatrice dans un seul pli de 80 microns d'épaisseur et réduit le total des matériaux LSP et le temps de traitement de plus de 75 %.
L'industrie aérospatiale n'utilise actuellement pas de voile de fibre de carbone pour le LSP, explique Sprengard, "car il n'y a pas de produits suffisamment conducteurs pour répondre aux exigences de la zone 1A". VeeloVEIL a été conçu pour fournir 5 à 10 milliohms de résistivité électrique (une résistivité plus faible signifie un matériau plus conducteur) à un poids surfacique de 40 à 50 grammes par mètre carré, et répond aux exigences LSP des avions en utilisant un seul pli de 80 microns d'épaisseur. « Cela rend le matériau très drapable, ce qui donne une finition de surface lisse sans le post-traitement de remplissage de porosité souvent requis avec les produits ECF », note-t-il. « Ceci, à son tour, permet aux fabricants d'utiliser moins de résine de surfaçage, ce qui permet d'économiser des matériaux et des coûts de fabrication. Les trois principaux équipementiers d'aérostructures nous ont dit que VeeloVEIL leur permet de réduire le total des matériaux LSP et le temps de traitement de plus de vingt heures à moins de trois heures. »
VeeloVEIL est fourni sous la même forme de produit que l'ECF, ce qui permet aux fabricants de l'utiliser sans modifier leurs processus de fabrication existants. « Tous nos matériaux conducteurs d'électricité pour composites aérospatiaux sont conçus pour être traités par des machines AFP [de placement automatisé de fibres] », explique Sprengard. Veelo Technologies est également en train d'intégrer VeeloVEIL dans un produit de couche de surface standard, en travaillant avec des préimprégnés aérospatiaux de niveau 1.
Adapter la conductivité au chauffage
Au cours du développement de VeeloVEIL, l'équipe de Sprengard s'est rendu compte que la capacité d'adapter la conductivité électrique de ses produits pourrait également être utilisée pour des applications de chauffage électrothermique. Cela a ouvert la porte à une autre de ses familles de produits, VeeloHEAT.
« VeeloHEAT est un matériau non métallique à base de carbone qui est intégré aux aérostructures pour le dégivrage », explique Sprengard. Notez que ce n'est pas fibre de carbone. « Aujourd'hui, les systèmes de dégivrage des avions utilisent souvent des fils métalliques, qui ont des problèmes de durabilité, en particulier dans les environnements à haute fatigue tels que les giravions. Si l'un des fils casse, le système ne fonctionne plus. Ces systèmes de dégivrage métalliques conventionnels tombent généralement en panne et doivent être réparés, ce qui prend beaucoup de temps et d'argent. Nous avons démontré que nos produits sont beaucoup plus durables, ce qui réduit considérablement les temps d'arrêt de l'avion. » Il note que ces produits sont en effet utilisés sur des pales de rotor pour hélicoptères et ont un potentiel important pour les avions EVTOL (décollage et atterrissage de véhicules électriques) qui sont actuellement développés pour la mobilité aérienne urbaine et la prochaine génération de transport.
À plus court terme, Sprengard indique que les produits VeeloHEAT devraient voler sur un avion commercial à voilure fixe au premier trimestre 2020 pour une qualification initiale. « L'attrait de cette technologie n'est pas un secret », dit-il, notant que Collins Aerospace (anciennement UTC, qui fera désormais partie de Raytheon) a annoncé une licence exclusive pour les systèmes de dégivrage à base de CNT en janvier 2017. « Ils connaissent le bien marché et se positionnent pour l'avenir. Leur investissement est une bonne indication de la direction que prend cette technologie », ajoute Sprengard.
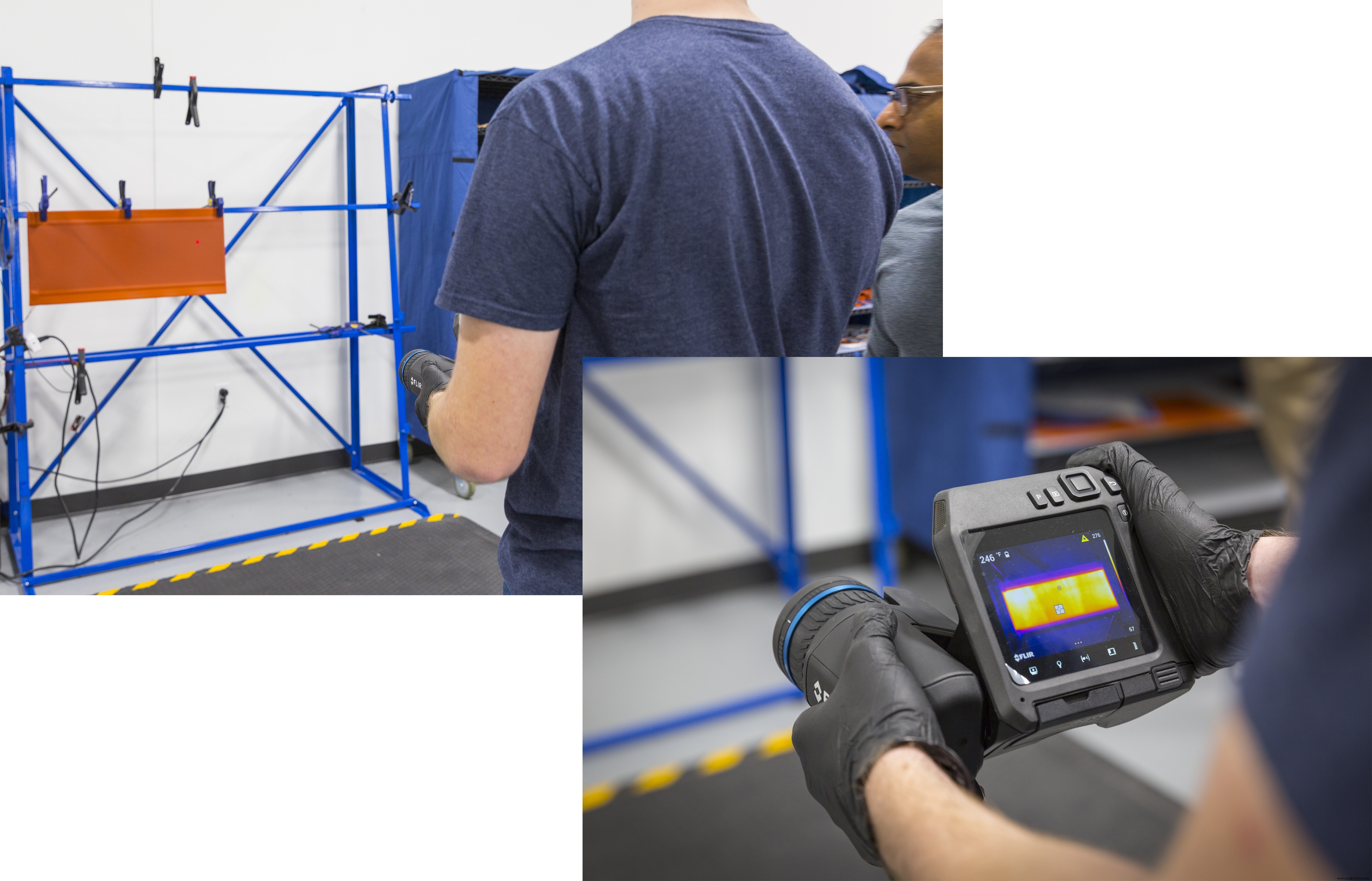
Veelo Technologies teste chaque couverture VeeloHEAT pour la sortie de température et l'uniformité.
Du dégivrage au traitement et à la réparation des composites
Les couvertures chauffantes conventionnelles sont utilisées depuis des décennies pour durcir des zones relativement petites - généralement moins d'un mètre carré - de structures composites lors de réparations de foulards collés. Ces couvertures chauffantes utilisent des fils métalliques traditionnels noyés dans du caoutchouc de silicone ou d'autres matériaux (selon la température de durcissement requise). « Comme pour les systèmes de dégivrage à base de métal, si un fil se brise, les couvertures thermiques se raccourcissent et ne fonctionnent plus », explique Sprengard. « Nous avons utilisé notre produit de dégivrage à base de carbone dans une couverture chauffante non métallique qui a une durabilité et une drapabilité inégalées, ainsi que des performances. » La norme de l'industrie pour ce dernier est un coefficient de variance (COV) de 3 %, qui est une mesure de l'uniformité des produits de chauffage, d'un couvercle à l'autre et d'un bord à l'autre. La couverture VeeloHEAT dépasse cette norme avec une puissance énergétique typique de 5 watts par pouce carré.
Les couvertures chauffantes de Veelo peuvent produire des températures allant jusqu'à 550 °F (288 °C) et peuvent être façonnées en filet pour s'adapter aux pièces et aux outils. « Cette capacité est possible grâce à notre capacité à formuler des chimies et à fabriquer des matériaux avancés uniques avec des résistivités adaptées », note Sprengard. Veelo Technologies a commercialisé cette technologie en 15 mois et est maintenant en pleine production. « Nous constatons une très bonne croissance de cette gamme de produits », ajoute-t-il, « et nous fabriquons maintenant de grands volumes de couvertures VeeloHeat qui sont utilisées pour coller de grandes structures composites hors de l'autoclave et four, en utilisant plusieurs zones de température et d'autres fonctionnalités de traitement demandées par nos clients. »
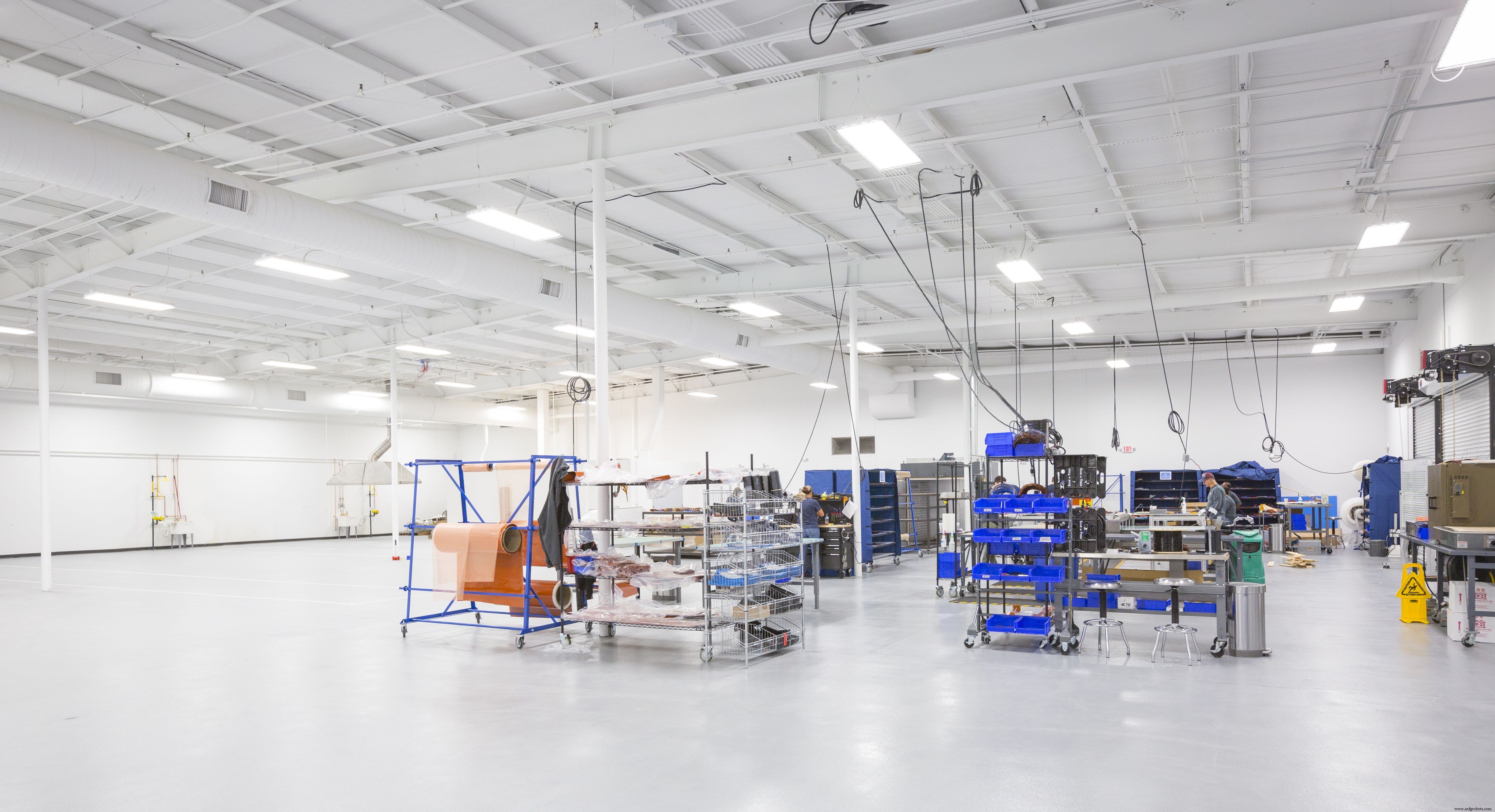
Relocalisation et montée en puissance de la production
Le nouveau hall de production de 20 000 pieds carrés de Veelo Technologies offre beaucoup d'espace pour augmenter la production de couvertures VeeloHEAT, qui a été déplacée et accélérée à pleine vitesse lors de la première phase de la transition de fabrication. La phase deux sera achevée d'ici le 3e trimestre 2019.
Fabriquer pour répondre aux besoins des clients
En octobre 2018, Veelo Technologies a reçu la confirmation qu'elle avait remporté un important programme de défense nécessitant une montée en puissance immédiate. « Heureusement, nous avons trouvé une installation presque parfaite et prête à emménager qui était déjà équipée de l'infrastructure dont nous avions besoin pour démarrer rapidement », se souvient Sprengard. L'installation de Woodlawn est dotée d'un contrôle environnemental, d'un éclairage et d'un revêtement de sol en époxy mur à mur à la pointe de la technologie. « Nous n'avons pris aucun raccourci — notre investissement dans des matériaux et des finitions de la plus haute qualité reflète notre stratégie à long terme et notre vision pour l'avenir », explique-t-il. Cet investissement se traduit également par le contrôle d'accès et le personnel de sécurité de l'installation, nécessaires à ses contrats de défense.
La construction requise de l'installation a été achevée au deuxième trimestre 2019, après quoi Veelo a commencé la relocalisation de ses lignes de production. « Tous nos équipements fonctionnent presque à pleine capacité, ce qui a rendu difficile l'arrêt de la planification pour le déplacement de toutes les lignes vers la nouvelle installation », concède-t-il. L'entreprise a achevé la première phase de sa transition de fabrication en juillet 2019, en déplaçant la ligne de couvertures VeeloHEAT et en la ramenant à la pleine production.
Le grand hall de production ouvert de la nouvelle installation est accessible depuis le hall avant. À droite se trouve la zone de fabrication des couvertures VeeloHEAT. Quatre tables de superposition de 4 pieds sur 10 pieds sont utilisées pour superposer le film VeeloHEAT avec d'autres matériaux sur des outils de moulage en métal façonnés. Ces couches sont ensuite durcies dans un four de 10 pieds sur 10 pieds fourni par JPW Industrial Furnaces (Trout Run, Pennsylvanie, États-Unis). Les couvertures finies sont démoulées et connectées à des fils d'alimentation électrique, qui permettent une utilisation avec des unités de contrôle informatisées (hot bonders) pour durcir les stratifiés composites et les réparations. Chaque couverture VeeloHEAT est testée pour la sortie de température et l'uniformité.
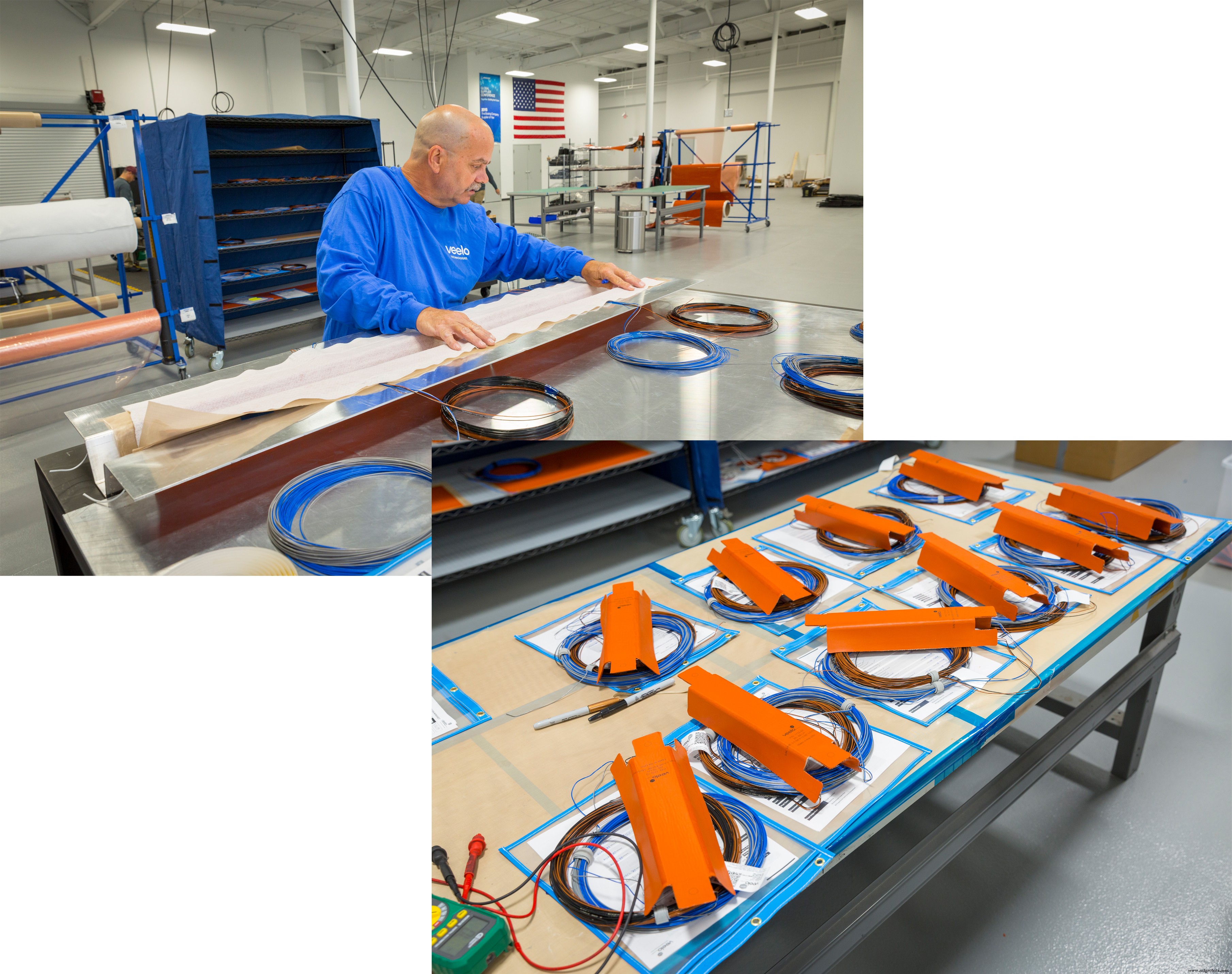
Couvertures chauffantes non métalliques plus durables et plus conformables
Bien que les fils soient utilisés pour chauffer l'outillage métallique dans la production des couvertures VeeloHEAT (ci-dessus) et pour fournir le courant électrique des unités de contrôle informatisées (hot bonders) aux couvertures pendant le durcissement et la réparation des composites, les fils métalliques ne sont pas utilisés à l'intérieur. Cela permet à ces couvertures chauffantes non métalliques d'être produites dans des formes 3D sans fils cassés, court-circuit et problèmes d'uniformité de la température (points chauds et froids). Le film VeeloHEAT à base de carbone à l'intérieur produit des températures jusqu'à 550°F (288°C) avec 3% de COV à 5 W/in2.
Juste au-delà de la zone de production de la couverture chauffante se trouve la salle de production de chimie humide. Ici, des équipements industriels provenant de Silverson Machine (East Longmeadow, Mass., États-Unis) et Netzsch (Burlington, Mass., États-Unis) sont utilisés pour mélanger les formulations chimiques avancées utilisées dans les produits de Veelo. Vient ensuite la salle de fabrication du film, qui abrite un système exclusif de fabrication du film VeeloHEAT à base de carbone de Veelo, la technologie clé à l'intérieur de la couverture VeeloHEAT. A nouveau vers la gauche se trouve la zone de production VeeloVEIL. Bien que vides au moment de cette tournée, les lignes de fabrication roll-to-roll de 15 pouces et 36 pouces de large pour la production de VeeloVEIL ont été déplacées dans la nouvelle usine en août. L'entreprise est également en train de concevoir une ligne de 60 pouces de large pour répondre à la demande future. D'ici octobre, Veelo Technologies aura toutes ses gammes de produits exploitées sous un même toit et s'orientera vers une production accrue.
Solutions de nouvelle génération
La route vers le succès actuel de Veelo Technologies a été longue et pas toujours simple. « Oui, nous avons commencé dans les nanomatériaux et nous maintenons toujours une expertise importante dans ce domaine, mais aucun de nos clients ne se soucie de savoir si nous utilisons ou non des nanomatériaux », explique Sprengard. « Ils ne se soucient que si nous fournissons une solution convaincante qui répond à leurs objectifs de performances et de retour sur investissement. Par exemple, des produits qui permettent à la prochaine génération de systèmes de dégivrage d'utiliser moins d'énergie sur l'avion, ce qui ouvre de nouvelles opportunités pour la conception des véhicules aériens et l'efficacité opérationnelle. »
Sprengard dit que les trois familles de produits Veelo vont de l'avant, soit en train d'être finalisées dans des listes de produits qualifiés OEM et fournisseurs (QPL) "ou d'être ajoutées en tant que numéro de pièce dans la base d'approvisionnement de nos clients". Bien que la grande majorité de ce que l'entreprise fasse actuellement concerne les composites thermodurcissables, il note qu'elle commence également à s'intéresser aux composites thermoplastiques et à la fabrication additive.
Sur quoi Veelo Technologies se concentre-t-elle pour l'avenir ? « Notre première priorité est de continuer à honorer nos commandes existantes et nos opportunités stratégiques », a déclaré Sprengard. « Le marché nous pousse à répondre à de nouveaux niveaux de demande, ce qui est formidable et stimulant. Rester concentré est notre priorité absolue. »
Les objectifs que Veelo s'est fixés maintenant sont tout aussi impressionnants que sa ténacité et sa patience à travers 12 années de développement pour atteindre ce point. « Si vous regardez les meilleurs fournisseurs de composites aérospatiaux, tels que Airtech et A&P Technologies », déclare Sprengard, « ils ont une place à la table au début des cycles de développement de leurs clients. Être un tel partenaire d'innovation prend du temps. Il ajoute « et engagement ».
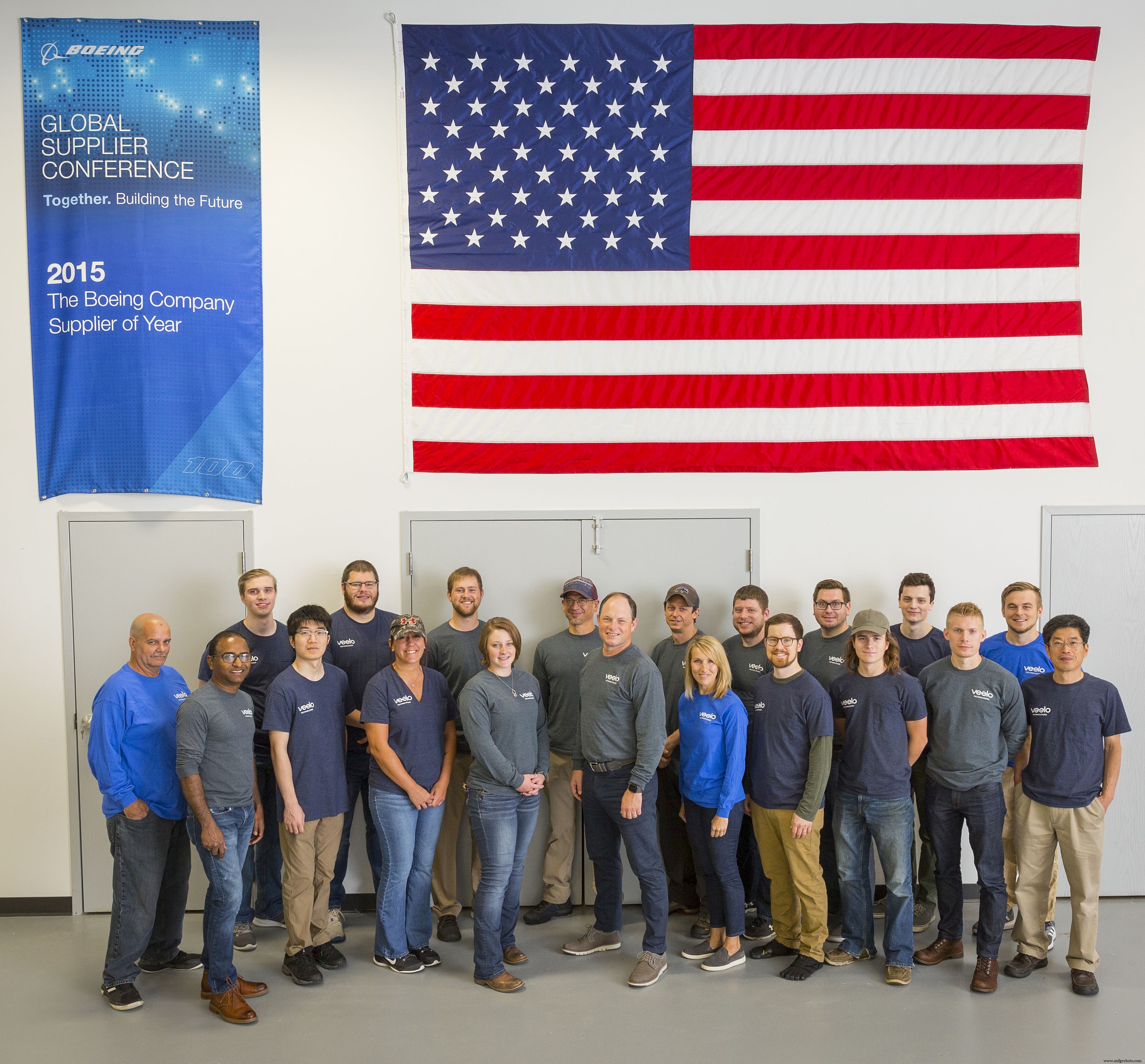
Veelo Technologies est passé de quatre à 24 employés et est passé d'un fournisseur de nanomatériaux à un spécialiste des produits étendus avancés à un partenaire d'innovation pour les futurs composites, reconnu par Boeing comme fournisseur de l'année en 2015.
Matériau composite
- Emerson fournira des technologies d'automatisation avancées pour une usine révolutionnaire de recyclage des plastiques
- Présentation d'une usine fiable
- Société saoudienne d'électricité pour améliorer la fiabilité de la centrale électrique
- Technologies faisant basculer l'industrie 4.0
- Les fabricants visitent Southco pour une visite de l'usine, une discussion sur les meilleures pratiques d'amélioration continue
- Qu'est-ce que l'entretien des plantes ?
- Tour d'outillage
- Tour CNC
- Plate-forme pour les technologies quantiques utilisant l'or