Promotion des composites thermoplastiques et RTM pour Clean Sky 2 en Espagne
L'EURECAT Centro Tecnológico de Catalunya (Centre technologique EURECAT de Catalogne, Barcelone, Espagne) est une organisation de R&D privée à but non lucratif avec 11 installations, 650 employés et 50 millions d'euros de chiffre d'affaires annuel. « C'est le deuxième plus grand centre de R&D d'Espagne », explique Angel Lagraña Hernandez, directeur de programme pour le marché de l'aéronautique et de l'espace chez EURECAT. Il explique qu'une partie des revenus d'EURECAT provient du gouvernement catalan et du reste, la moitié doit provenir d'entreprises privées - principalement des petites et moyennes entreprises (PME) - tandis que l'autre moitié peut être publique, comme l'Union européenne financée par l'Union européenne. Programme Clean Sky 2. « Nous avons maintenant 18 projets Clean Sky », note Lagraña, « qui nous ont été attribués uniquement sur la base de soumissions concurrentielles en réponse à des appels à propositions. »
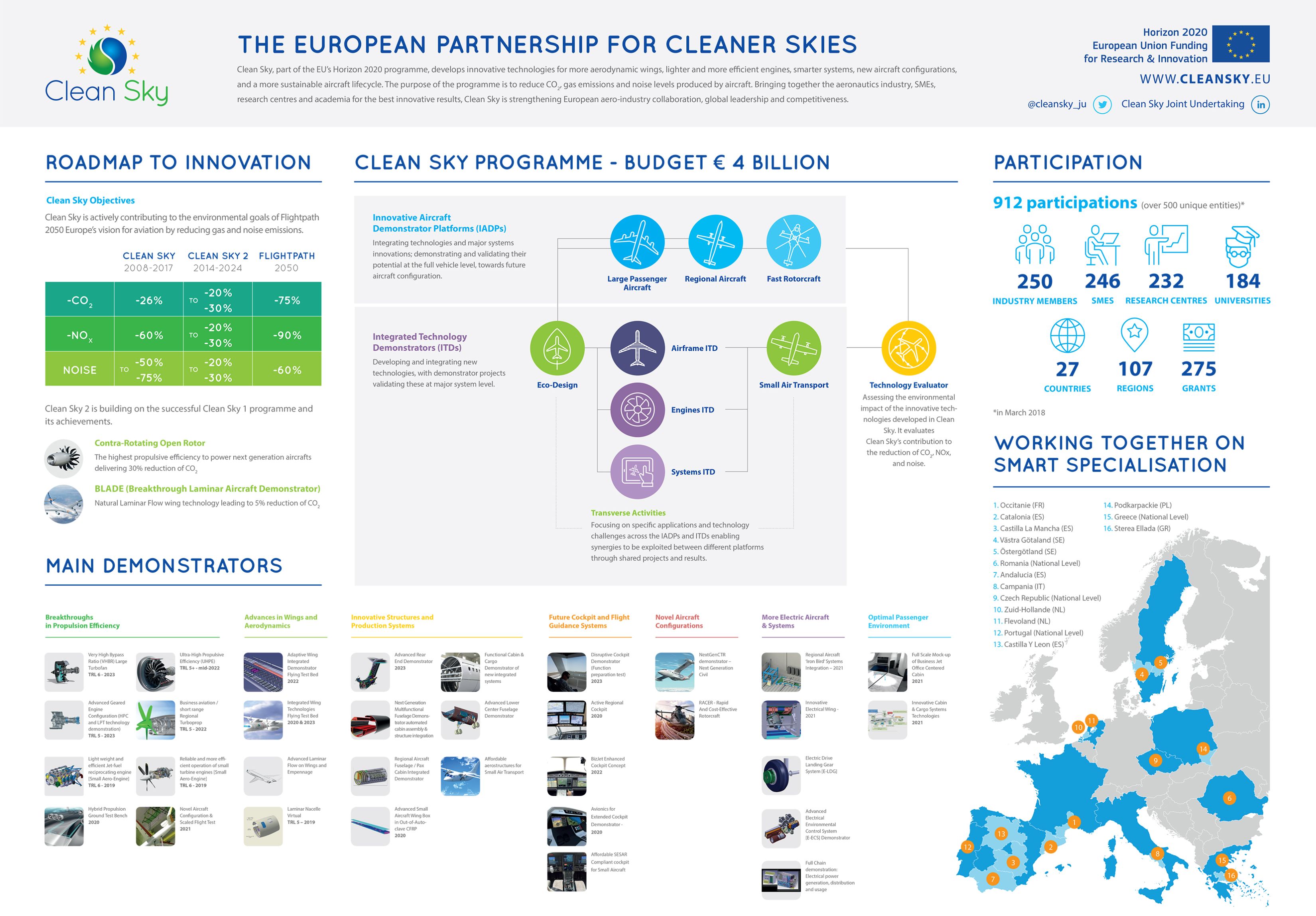
Voici des exemples de la façon dont les composites figurent dans les nombreux objectifs de Clean Sky 2 et les démonstrateurs technologiques prévus :
- Le démonstrateur de fuselage multifonctionnel de nouvelle génération :tirant parti des thermoplastiques pour un ciel plus propre
- Économie circulaire :le fuselage composite pour les avions régionaux prend forme
- Tirer parti de l'expertise en course automobile pour le FastCan de Clean Sky
« EURECAT est très transversal, travaillant dans l'automobile, le rail et d'autres industries en plus de son travail dans l'aérospatiale », explique Lagraña. « Il a également beaucoup d'activités dans l'informatique telles que l'analyse de données et la blockchain, etc. Composites 4.0 est l'un de ses domaines stratégiques. Au sein des composites, il note qu'EURECAT travaille principalement dans des technologies hors autoclave (OOA). « Nous nous concentrons sur les thermoplastiques et le moulage par compression liquide, y compris la surveillance du processus en temps réel, y compris la surveillance de la température de transition vitreuse (Tg) de la résine pendant le traitement. » (Continuez à lire la section sur COFRARE, à la fin de ce blog, pour en savoir plus sur cette surveillance Tg.)
Les projets les plus récents d'EURECAT liés aux composites dans Clean Sky 2 incluent :
- KEELBEMAN pour démontrer une poutre de quille en composite thermoplastique (Ce projet a reçu un financement de l'entreprise commune Clean Sky 2 dans le cadre du programme de recherche et d'innovation Horizon de l'Union européenne sous le GAP n° 785435 KEELBEMAN);
- WINFRAME 4.0 pour construire des cadres de fenêtre en composite thermoplastique (TPC) pour le démonstrateur Green Regional Aircraft (GRA) dans Clean Sky (2008-2017) et étendu à Regional Aircraft IADP (Innovative Aircraft Demonstrator Platform) dans Clean Sky 2 (2014-2024);
(Ce projet a reçu un financement de l'entreprise commune Clean Sky 2 dans le cadre du programme de recherche et d'innovation Horizon de l'Union européenne dans le cadre du GAP n° 821323 WINFRAME 4.0.) - COFRARE 2020 pour les cadres de fuselage thermodurcissables fabriqués à partir de moulage par transfert de résine (RTM) avec des attaches de cisaillement TPC.
(Ce projet a reçu un financement de l'entreprise commune Clean Sky 2 dans le cadre du programme de recherche et d'innovation Horizon de l'Union européenne dans le cadre du GAP n° 821261 COFRARE 2020.)
Poutre de quille composite thermoplastique
Ciel propre 2 - JTI-CS2-2017-CFP06-LPA-02-20. Durée du projet : mars 2018 à décembre 2019
L'objectif du projet KEELBEMAN est de développer une structure de poutre de quille orientée fabrication pour un avion de type A320 qui permet des cadences de production d'avions élevées mais à un coût abordable via des composites thermoplastiques. En plus d'EURECAT en tant que coordinateur du projet, les partenaires comprennent :
- Airbus (Toulouse, France) en tant que topic manager
- CETMA (Centre européen de recherche pour les technologies, la conception et les matériaux, Brindisi, Italie)
- Le groupe d'ingénierie CT (CT Ingenieros, Madrid, Espagne), une entreprise avec de nombreux bureaux mondiaux qui a un contrat pluriannuel avec Airbus pour le développement d'avions tels que la recherche sur le fuselage, les ailes et l'arrière via son bureau de Hambourg, en Allemagne ; recherche sur l'arrière (Espagne); recherche sur les structures liées au fuselage et à la centrale électrique (Toulouse, France) et au développement d'ailes (Bristol, Royaume-Uni)
- Sofitec (Séville, Espagne), spécialiste de la fabrication et de l'assemblage d'aérostructures avec une expertise et une capacité de production dans les composites.
Le CT Engineering Group a réalisé une modélisation complète de la géométrie de la poutre de quille via son bureau de Toulouse, tandis que Sofitec a développé les contrôles non destructifs (CND). « C'est très difficile avec une structure de boîte aussi fermée », souligne Lagraña.
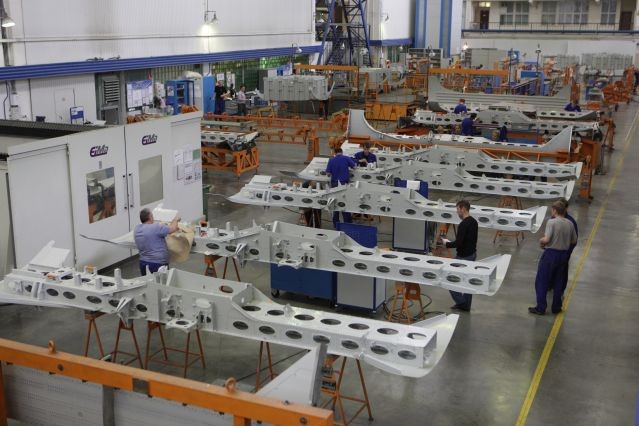
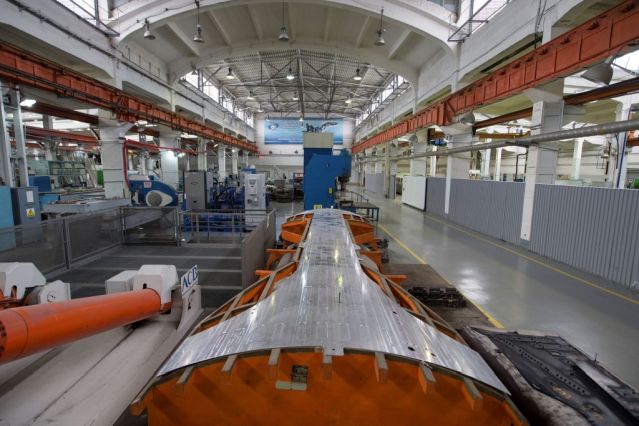
On voit ici l'ensemble poutre de quille de l'A320, fabriqué en métal par Irkut Corporation (Moscou, Russie). Irkut aurait passé un contrat avec Airbus en 2004 pour fournir des composants, notamment la baie du train d'atterrissage avant, la poutre de quille et la piste de volet, qui sont installés, en moyenne, dans un avion sur trois de la famille A320. SOURCE | Irkout
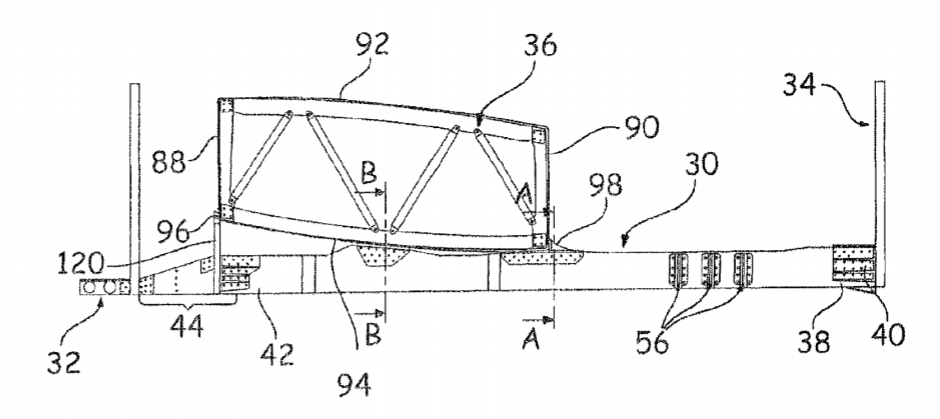
Développement de structures de poutre de quille
"Aujourd'hui, la plupart des poutres de quille d'avion sont en métal, à l'exception de l'Airbus
A350, qui est un composite monolithique en fibre de carbone », explique Lagraña. « Cela nécessite un grand nombre de rivets et un temps d'assemblage important. » Il explique que la poutre de quille est une structure critique dans le fuselage :« Il y a eu des cas où la poutre de quille s'est cassée lors de l'atterrissage, provoquant la fissuration et la rupture de tout le fuselage.
Selon un article de 2011 de Steve Wilhelm, la poutre de quille de l'A350 est composée à 70 % de composite, mesure 54 pieds (16,5 mètres) de long, est assemblée avec 10 000 attaches, pèse 1,2 tonne et constitue l'épine dorsale de l'avion. Wilhelm note que l'avion Boeing 787 concurrent "ne dépend pas d'une structure de quille aussi robuste, car une plus grande partie de la résistance de la coque provient de barils composites qui sont attachés bout à bout". L'article cite ensuite Michel Merluzeau, associé directeur du cabinet de conseil en aérospatiale G2 Solutions LLC (Kirkland, Wash., États-Unis), qui décrit la conception de l'Airbus comme « plus conventionnelle » et « moins risquée » mais souligne que la poutre de quille est « essentielle au l'intégrité structurelle de cet avion. »
Airbus a en fait été le pionnier d'une poutre de quille composite pour l'A340 en 2001. Mais comme décrit ci-dessus, le nombre élevé de rivets requis va à l'encontre des économies de poids possibles grâce à l'utilisation de composites. Ainsi, un objectif clé du projet KEELBEMAN est de minimiser les fixations en utilisant des composants composites thermoplastiques qui sont soudés ensemble.
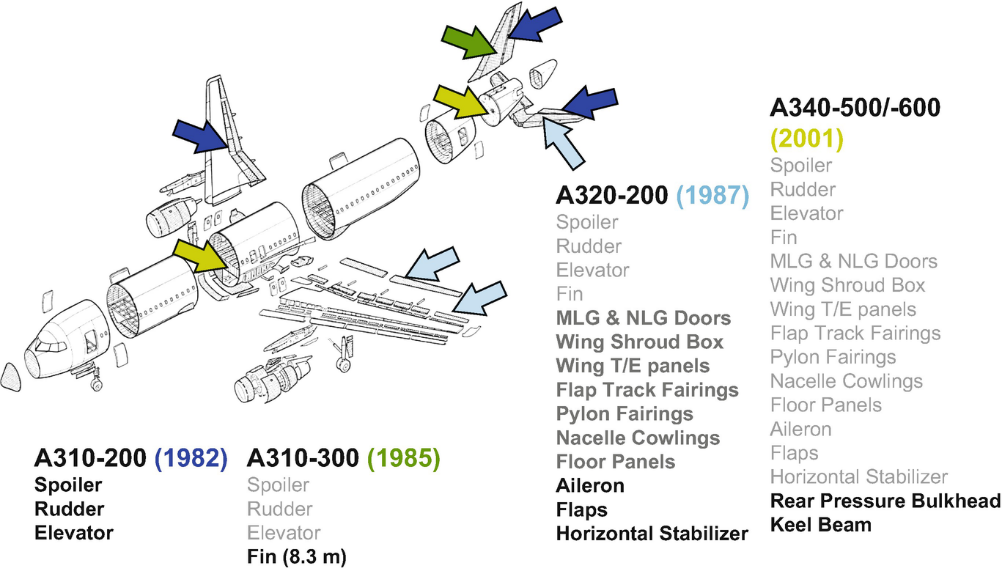
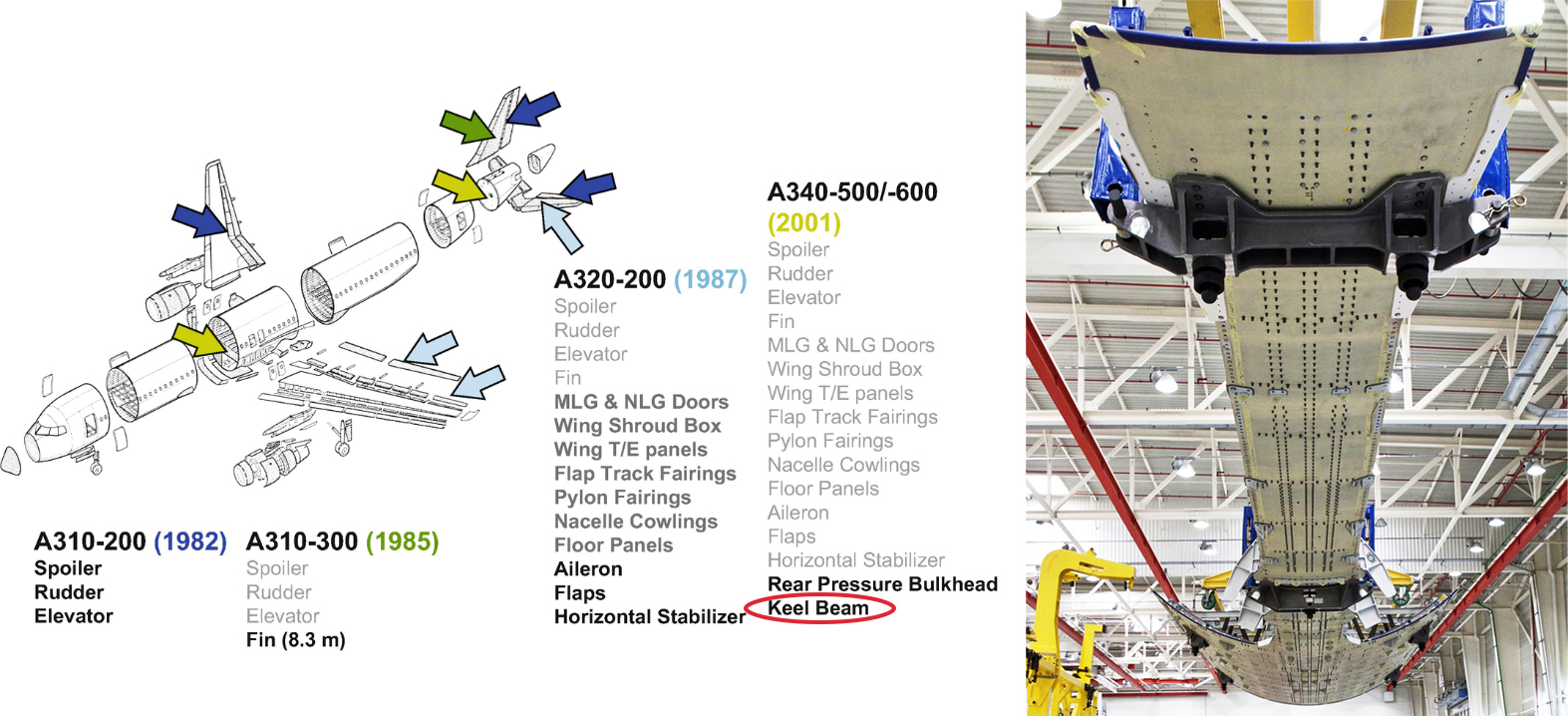
poutre de quille TPC
"Le développement d'une poutre de quille composite thermoplastique utilisant le soudage pour l'assemblage fait partie du développement d'Airbus de l'avion de demain, qui comprend des programmes tels que l'aile de demain et le fuselage de demain", a déclaré Lagraña. « Au sein de KEELBEMAN, nous avons produit une section de démonstration de 250 mm sur 500 millimètres sur 1 mètre de long d'une poutre de quille avec des longerons et avons démontré la faisabilité de souder cette structure avec autant d'automatisation que possible."
Lagraña note que les plaques murales et les longerons du démonstrateur ont été fabriqués à l'aide d'un ruban unidirectionnel (UD) en fibre de carbone/polyéthercétonecétone (PEKK) dans un processus de moulage par compression continue (CCM) développé par CETMA (voir « Moulage par compression de qualité aérospatiale » et « PEEK vs. PEKK vs PAEK et moulage par compression continue »). « Il existe également des nervures pour les raidisseurs transversaux qui ont été fabriquées à l'aide d'un moulage par compression traditionnel non isotherme par EURECAT », ajoute Lagraña.
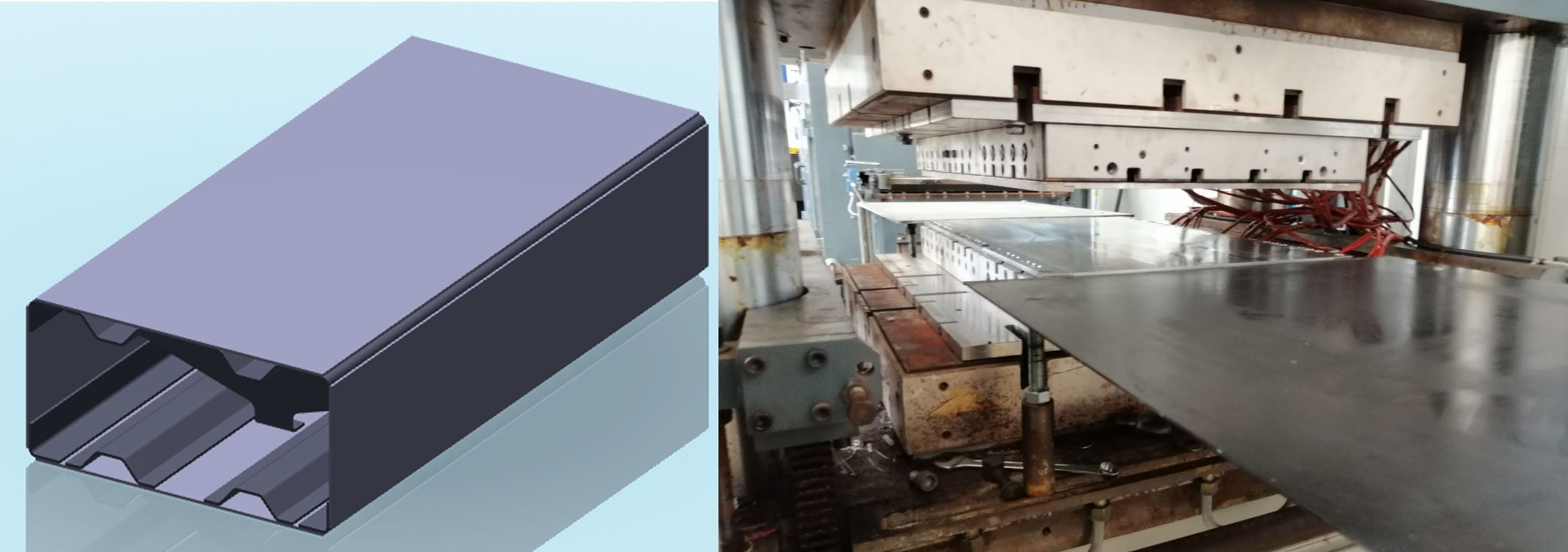
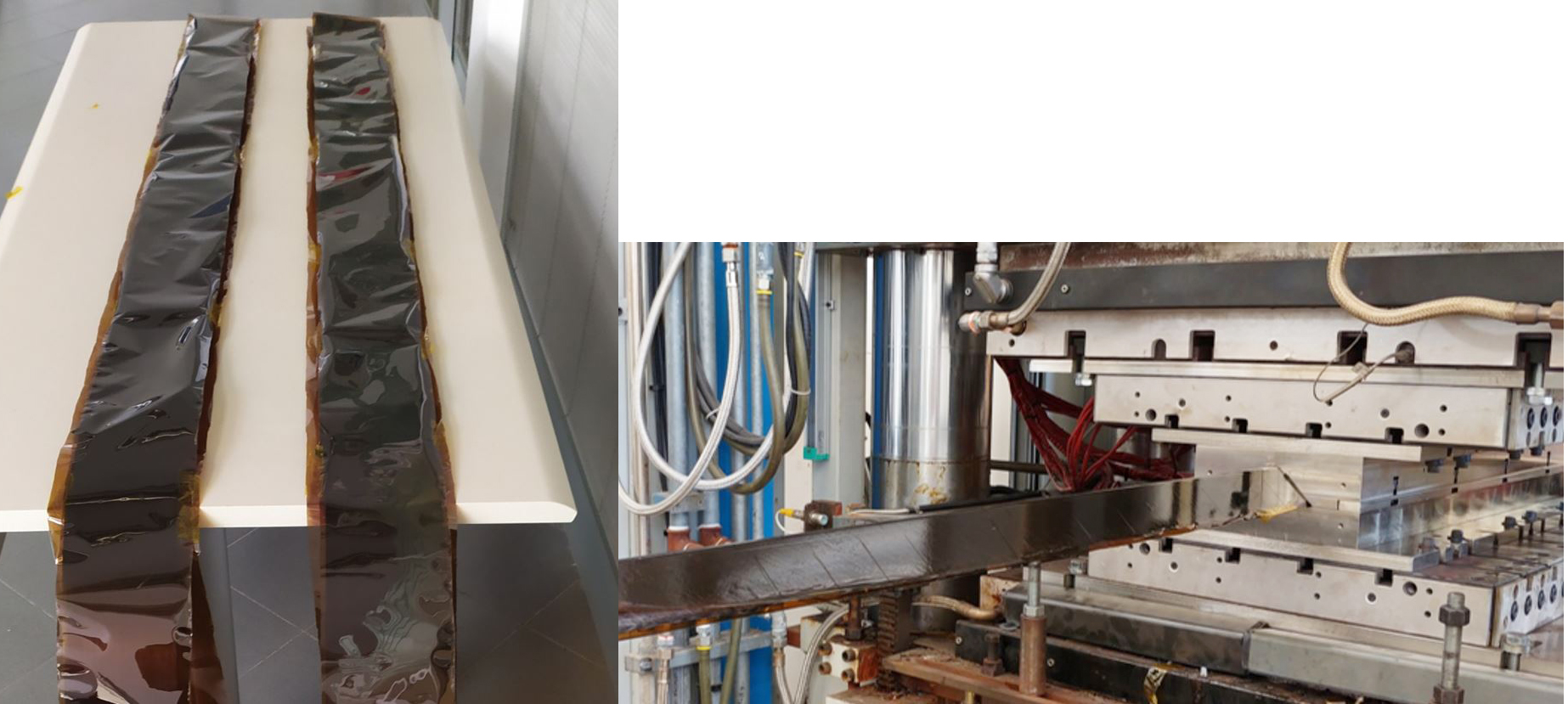
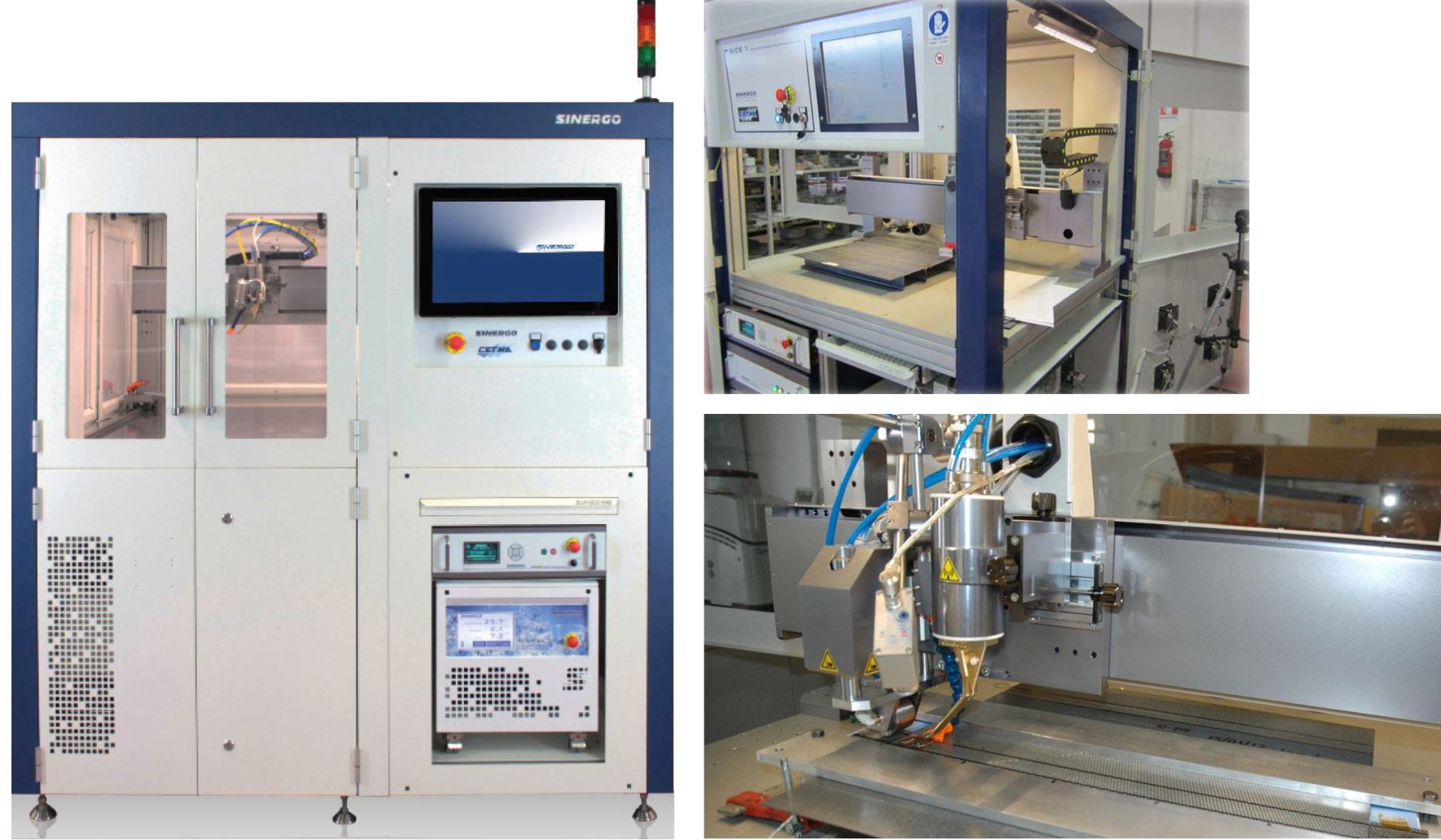
Le soudage par induction comme élément clé
Lagraña note que le CETMA a joué un rôle clé non seulement dans la production de pièces pour KEELBEMAN, mais également dans l'assemblage du démonstrateur à l'aide de sa machine et de sa technologie de soudage par induction brevetées. Ce soudage a été développé à l'origine dans le premier projet ECO FAIRS du programme Clean Sky (2011-2014), ainsi que le moulage par compression isotherme et non isotherme des structures TPC présentées ci-dessus. Dans ECO FAIRS, le CETMA a utilisé toutes ces technologies pour produire un prototype de démonstrateur basé sur le panneau supérieur existant (panneau à peau raidie à longerons) d'un empennage d'hélicoptère Agusta Westland ainsi qu'un démonstrateur de carénage à sponson incurvé. Bien que ceux-ci aient été fabriqués à l'aide de textile en fibre de carbone T300 3K 5HS CETEX (fourni par TenCate, maintenant Toray Advanced Composites) avec un film PPS (sulfure de polyphénylène) double face, CETMA a également prouvé le soudage par induction avec des composites PEEK et PEI.
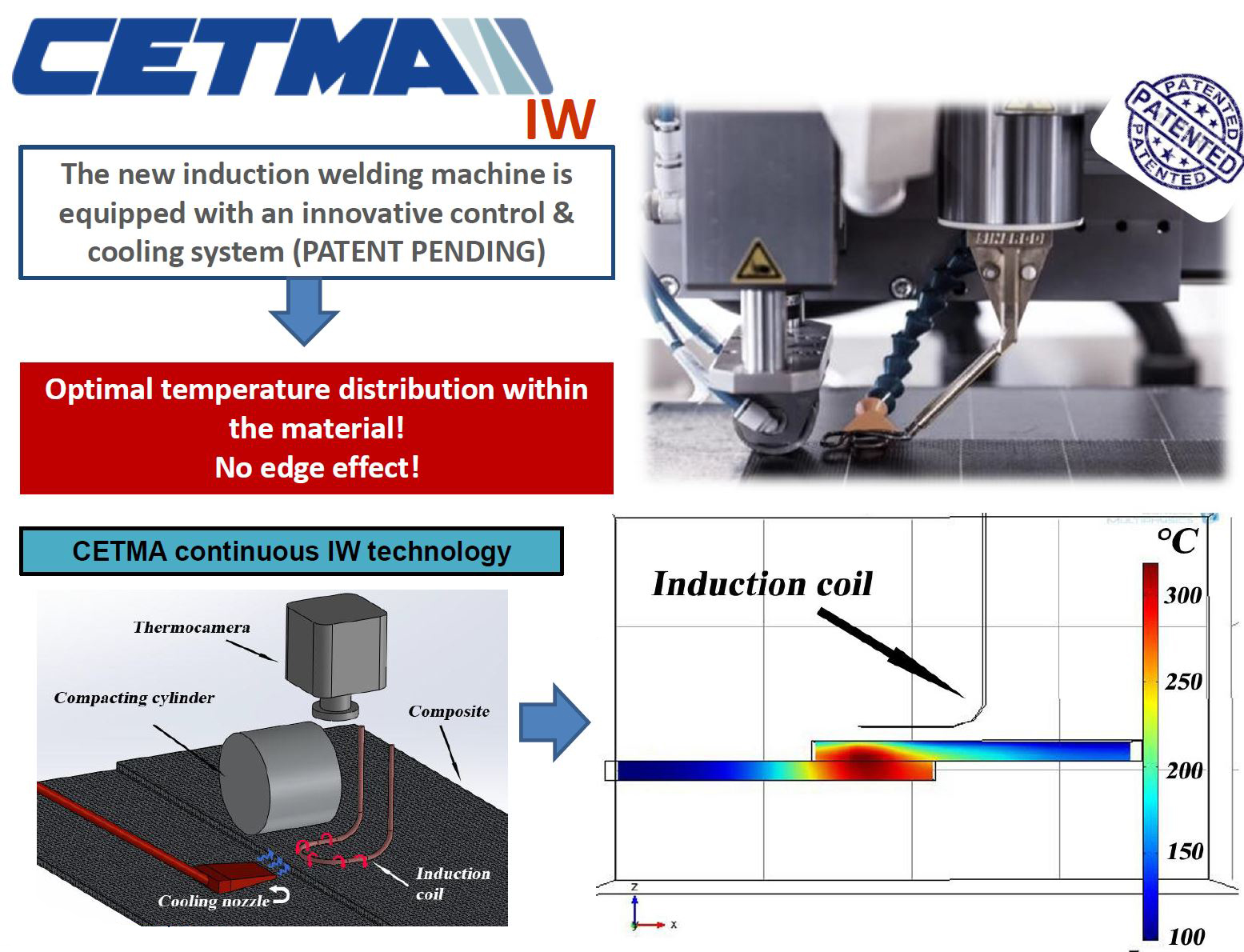
Le CETMA a sélectionné le soudage par induction (IW) comme la plus prometteuse des techniques de soudage des composites thermoplastiques et a travaillé avec le spécialiste du soudage et de l'ingénierie électronique SINERGO srl (Valdobbiadene, Trévise, Italie) pour développer une nouvelle machine de soudage par induction. La machine SICE 1 WIDE à portique proposée par SINERGO (voir image ci-dessous) est capable de souder en continu des pièces de qualité aérospatiale jusqu'à 1 mètre sur 1 mètre. Il comprend un système de contrôle robuste pour garantir des distributions de température optimisées dans les matériaux à souder. La machine est équipée d'un cylindre refroidi pour appliquer une pression de consolidation et d'un système de refroidissement par air pour évacuer la chaleur là où cela est nécessaire, comme dans les bords, où le flux des courants de Foucault électriques induits est limité, ce qui entraîne une densité de courant élevée et une surchauffe. . Il est également possible d'installer la tête de soudage par induction CETMA sur un bras robotisé 6 axes pour le soudage de formes géométriquement complexes.
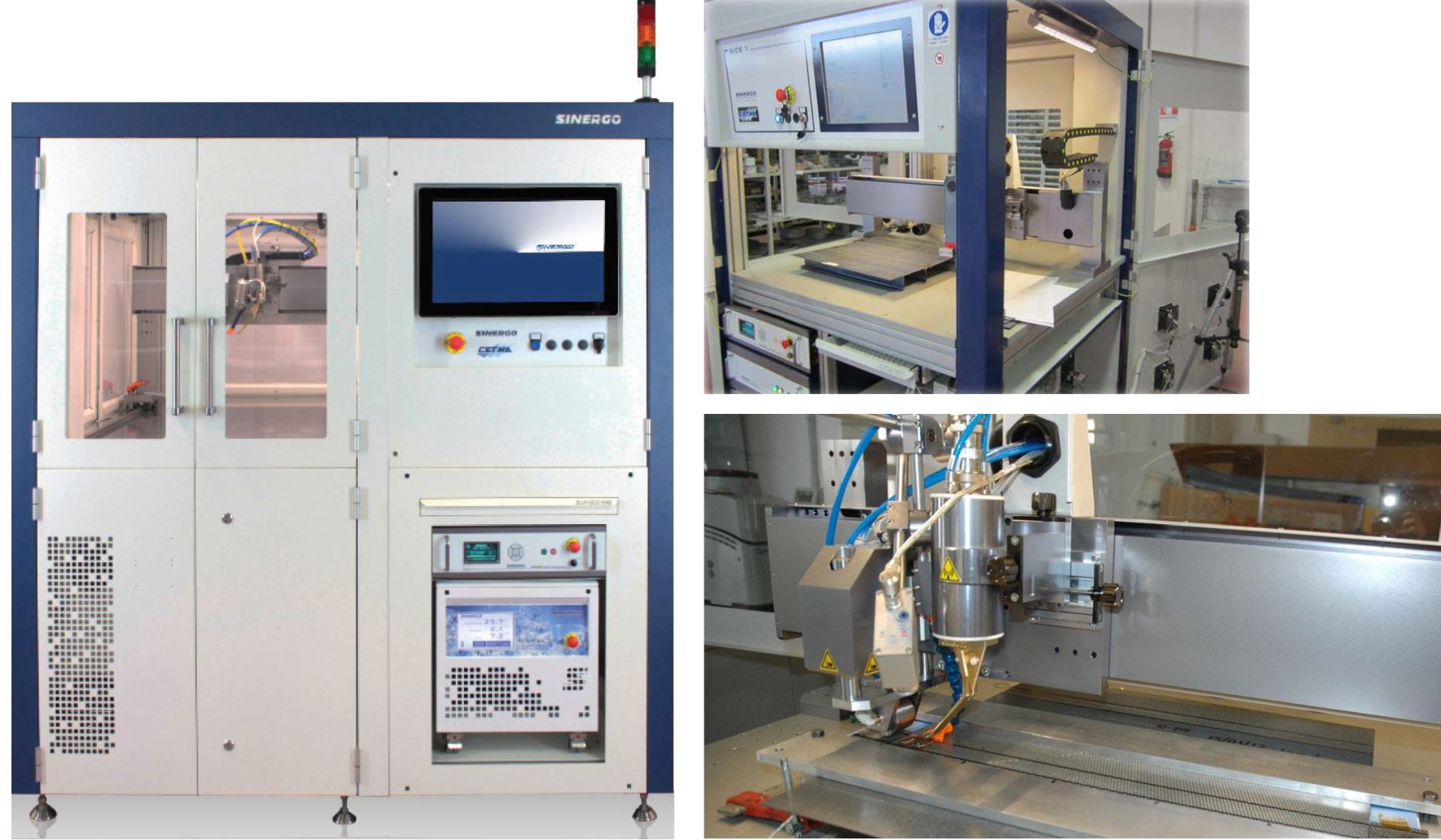
CETMA a également développé la capacité d'optimiser son procédé de soudage par induction en utilisant des outils de simulation, en effectuant une analyse numérique à l'aide du logiciel de modélisation par éléments finis (FEM) COMSOL Multiphysics (COMSOL Inc., Burlington, Mass, U.S.). Il a vérifié ces modèles à travers un grand nombre de tests physiques. Le CETMA a confirmé ses paramètres de processus optimisés par des tests à un tour sur des coupons soudés, dans lesquels les valeurs de résistance au cisaillement étaient très proches du maximum rapporté dans la littérature. Notamment, celles-ci étaient également beaucoup plus élevées que les valeurs maximales lors de l'utilisation d'adhésifs structuraux, explique le CETMA.
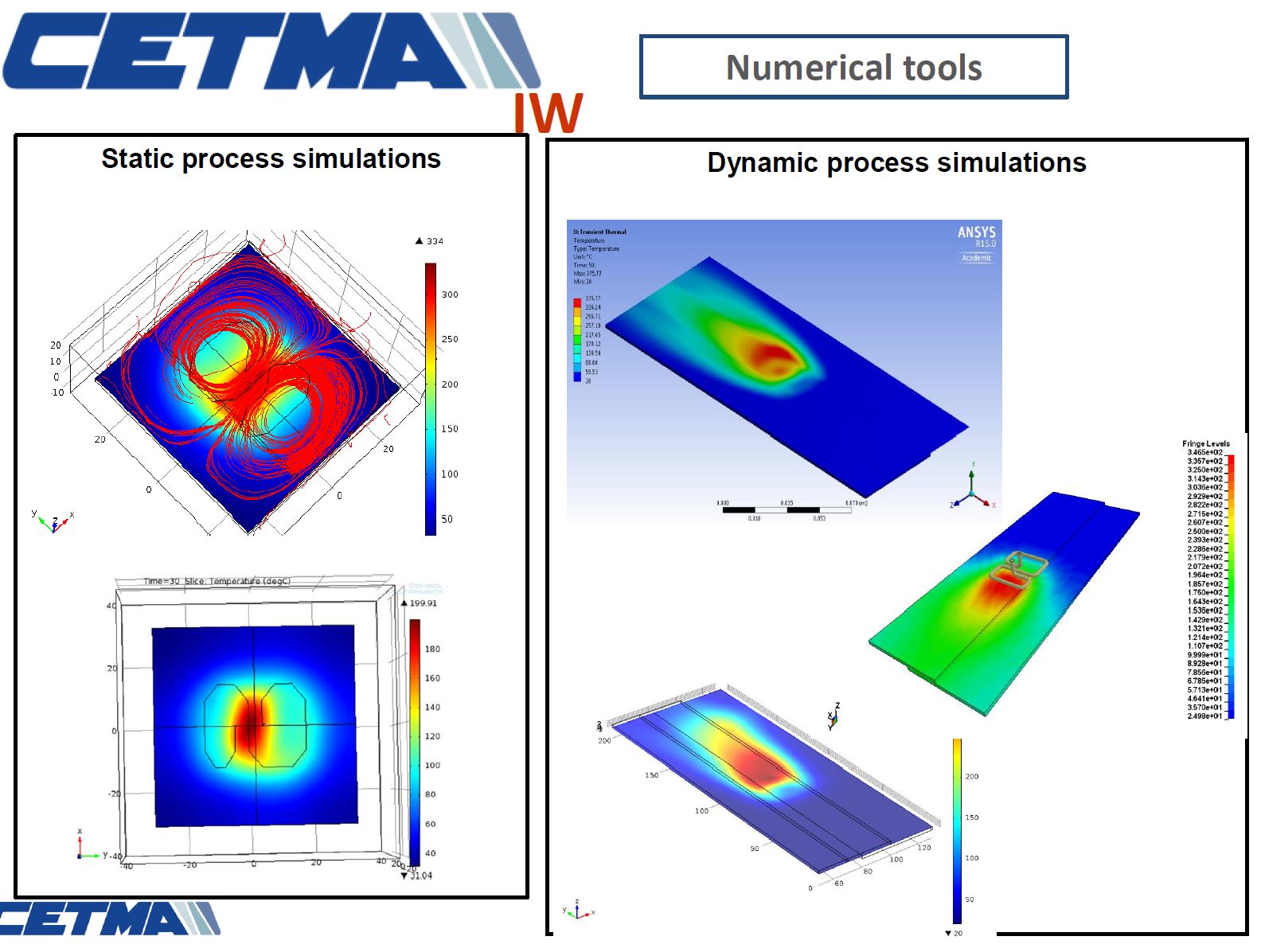
CETMA a prouvé sa capacité de soudage pour une grande variété de matériaux, y compris la fibre de carbone tissée et UD, ainsi que PEEK, PEI, PEKK, PP, PA6, PA12 et même le soudage à CF/époxy à l'aide d'un hybride thermoplastique PVB (polyvinylbutyral) couche de transition du substrat thermodurcissable à la face thermoplastique à souder. (La plupart des détails de cette section ont été tirés de la présentation des compétences du CETMA et du Rapport final de CORDIS pour les FOIRES ÉCO.) Le CETMA a déposé une demande de brevet européen en 2014 et les inventeurs Silvio Pappada et Andrea Salomi ont obtenu le brevet EP2801472A1 en 2016. Le CETMA a publié de nombreux articles et présentations sur cette technologie, notamment :
- « Simulations par éléments finis pour soutenir le développement de technologies hors autoclave », A&D, 11-12 octobre 2012
- « Simulations par éléments finis pour prendre en charge le soudage par induction en continu de composites PPS-carbone », SEICO 13, 11-13 mars 2013 « Paris »
- "Développement d'une nouvelle machine de soudage par induction pour les composites thermoplastiques dans le secteur aérospatial", XXIIe conférence de l'Association italienne d'aéronautique et d'astronautique à Naples, 9-12 septembre 2013
- « Soudage par induction dans le secteur aérospatial », TPRC, Thermoplastic Composites European Consortium, réunion Web, décembre 2013.
- « Tests à grande échelle sur des composants thermoplastiques pour le secteur aérospatial », SEICO 14, 10-11 mars 2014 « Paris »
- « Nouveaux équipements de soudage par induction pour le secteur aérospatial », magazine JEC, n° 87, mars 2014, pp. 89-91.
Statut de KEELBEMAN et voie à suivre
Airbus a visité le CETMA en décembre pour voir le soudage final de la section de démonstration de 1 mètre, et l'équipe KEELBEMAN a également procédé à un examen final du niveau de préparation technologique (TRL). « Nous obtenons de bons résultats et faisons évoluer la technologie de TRL 3 à TRL 4 », déclare Lagraña. Les prochaines étapes pourraient inclure la poursuite du développement du TRL 6 et la production d'une poutre de quille à grande échelle à installer dans l'un des démonstrateurs de Clean Sky 2, comme le fuselage central inférieur pleine grandeur WP 2.3.2, mais cela n'a pas encore été décidé.
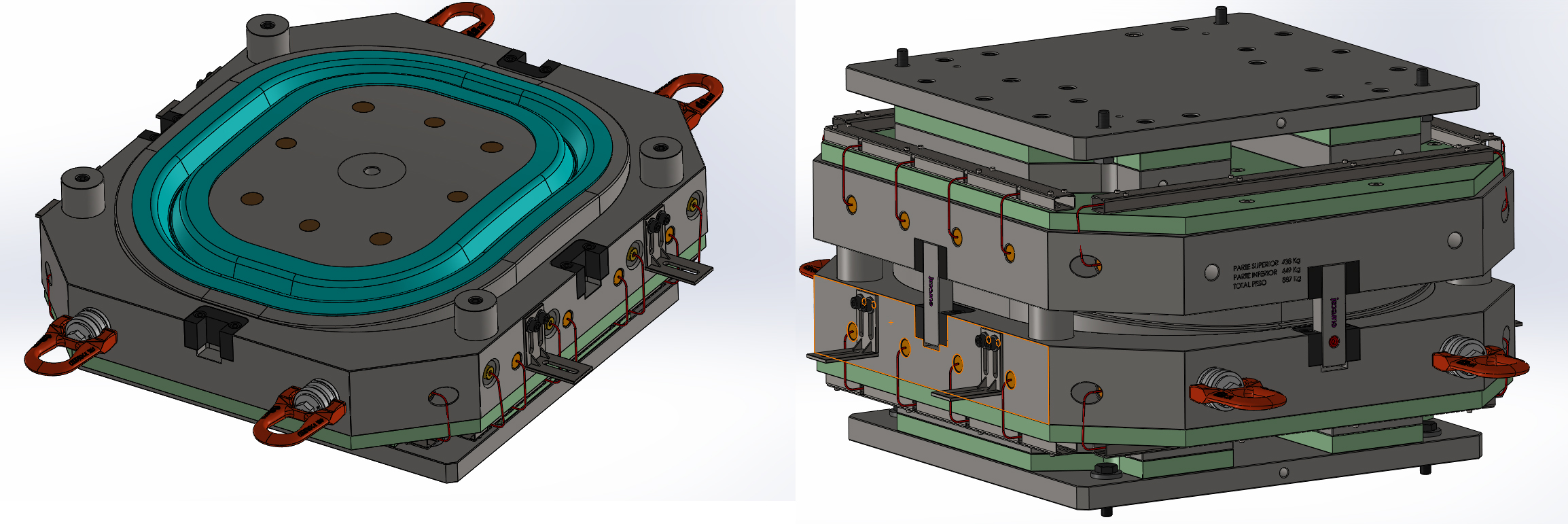
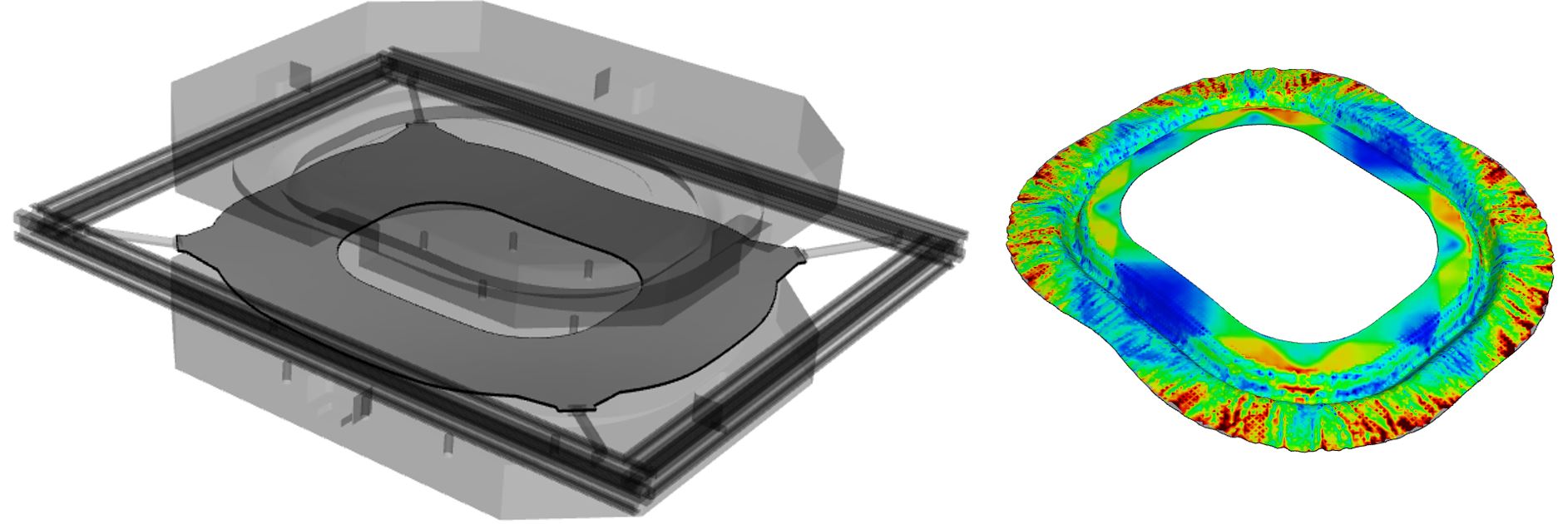
Projet WINFRAME 4.0 pour châssis de fenêtres TPC
Un autre programme de composite thermoplastique (TPC) pour EURECAT est WINFRAME 4.0, dont l'objectif est de développer et de fabriquer 24 cadres de fenêtre pour un démonstrateur au sol intégré fuselage/cabine d'avion régional (voir l'explication des développements de Clean Sky 2 pour les avions régionaux et le Full -Démonstrateur innovant de fuselage et de cabine passagers au dessous de). Les partenaires WINFRAME 4.0 incluent :
- Entreprise aérospatiale multinationale Leonardo (Rome, Italie) en tant que responsable de sujet
- EURECAT
- Sofitec.
« La méthode que nous utilisons peut produire un cadre de fenêtre toutes les 10 minutes », explique Lagraña. Les étapes de production incluent :chauffer les ébauches de stratifié TPC dans un four, les transformer en moule, fermer le moule dans une presse, appliquer de la chaleur et de la pression pendant 10 à 20 minutes et démouler la ou les pièces finies. « Cette approche permet non seulement d'obtenir des cycles plus courts que le moulage liquide, mais également un outillage beaucoup moins coûteux », ajoute-t-il. « Le procédé est bien connu dans l'industrie automobile, c'est le moulage par compression dans une configuration hautement automatisée qui augmente la qualité de la pièce, mais les matériaux aérospatiaux utilisés sont différents, en l'occurrence un PPS renforcé de fibre de carbone et de la fibre de carbone de Toray. Composites avancés (anciennement TenCate). À la fin de ce projet, nous aurons atteint un TRL 6 pour ces technologies », déclare Lagraña.
Projet COFRARE :Châssis RTM et tirants thermoplastiques de cisaillement
Le projet COFRARE 2020 est une extension du projet initial COFRARE 2.0 :
Clean Sky 2 - JTI-CS2-2015-CFP02-AIR-02-16. « Développement de procédés pour la fabrication de cadres composites à cadence de production élevée et à faible coût »Durée du projet : 2016 à 2018.
L'objectif du projet Clean Sky 2 COFRARE 2.0 était de développer un processus de fabrication compétitif et réalisable pour les cadres composites en fibre de carbone à utiliser dans un fuselage à base de panneaux composites pour les avions régionaux. Partenaires inclus :
- Fournisseur aérospatial de niveau 1 basé à Naples et société d'ingénierie/d'industrialisation DEMA (Design Manufacturing SpA, Somma Vesuviana, Italie)
- EURECAT
- LGAI Technological Center S.A., une division des Laboratoires Applus+ à Barcelone, en Espagne, a effectué des tests.
L'objectif du projet COFRARE 2020 de prochaine génération est de fabriquer des cadres composites à grande échelle et des attaches de cisaillement à utiliser dans le démonstrateur au sol intégré fuselage/cabine Clean Sky 2. Ce démonstrateur est organisé au sein de la plate-forme de démonstration d'avions régionaux (IADP) de Clean Sky 2 et détaillé dans la section 5.2.2 du document du programme technique conjoint de mars 2015 :
"Les avions régionaux sont un élément clé de Clean Sky via un ITD (Démonstrateur Technologique Intégré) dédié - Avions Régionaux Verts (GRA) , fournissant les éléments essentiels d'un système de transport aérien qui respecte l'environnement, assure une mobilité sûre et transparente et renforce le leadership industriel en Europe. Dans Clean Sky 2 , … Les objectifs de démonstration du Regional Aircraft IADP sont beaucoup plus complexes, complets et stimulants que ceux de l'actuel Clean Sky Projet GRA , qui a été contraint de travailler dans les limites de son budget et de son temps. …"
Le programme technique conjoint de 2015 décrit le développement d'avions régionaux pour inclure deux bancs d'essai volants et cinq grands démonstrateurs au sol intégrés. Ce dernier comprend le Démonstrateur de fuselage et de cabine passagers innovant à grande échelle :« Le fuselage sera une démonstration à grande échelle des technologies pour les matériaux composites, les structures et la fabrication visant à [atteindre] la réduction du poids et des coûts et à minimiser l'impact environnemental grâce à l'éco-conception et à l'optimisation de la consommation d'énergie tout au long du cycle de vie (vers un impact zéro). »
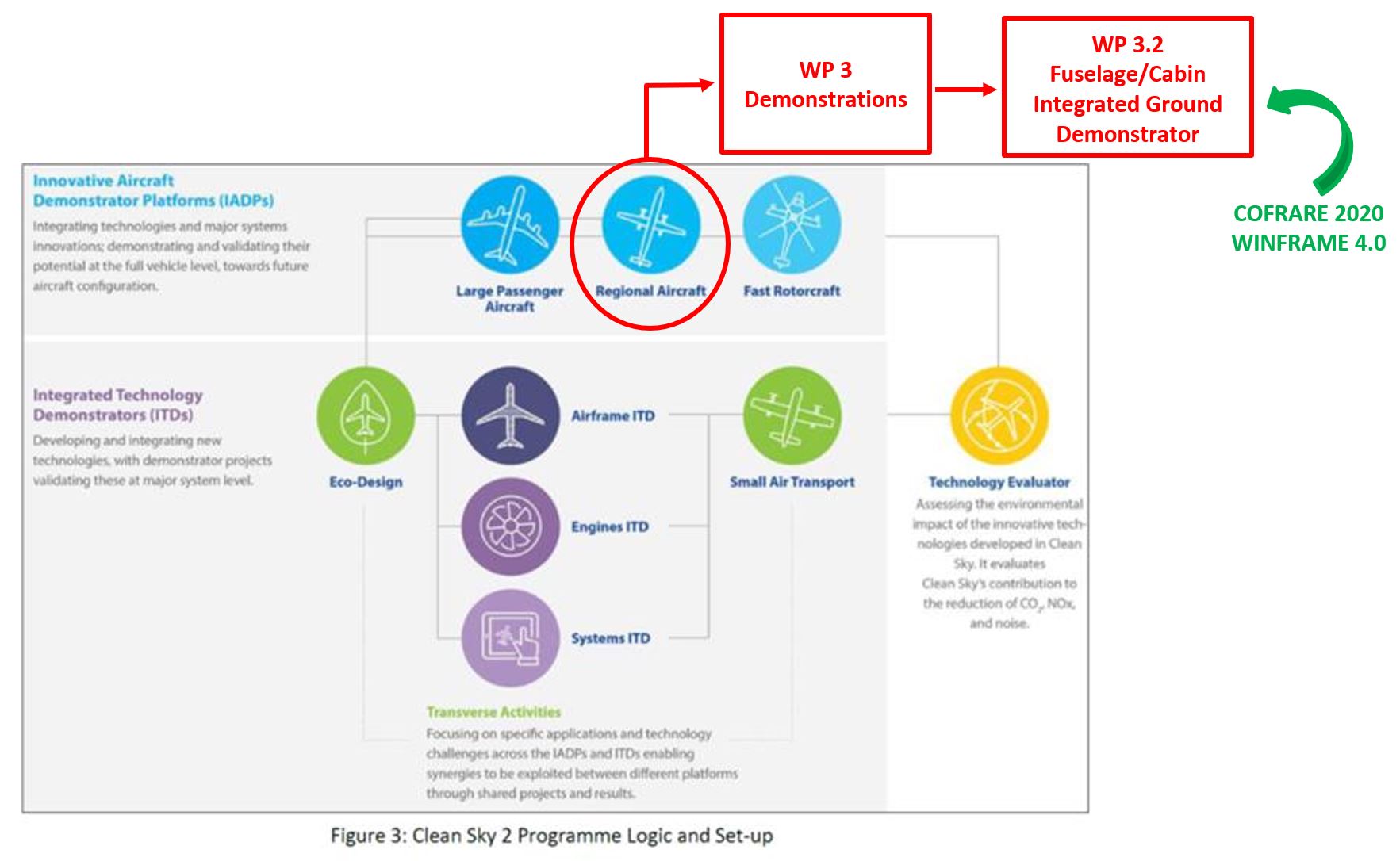
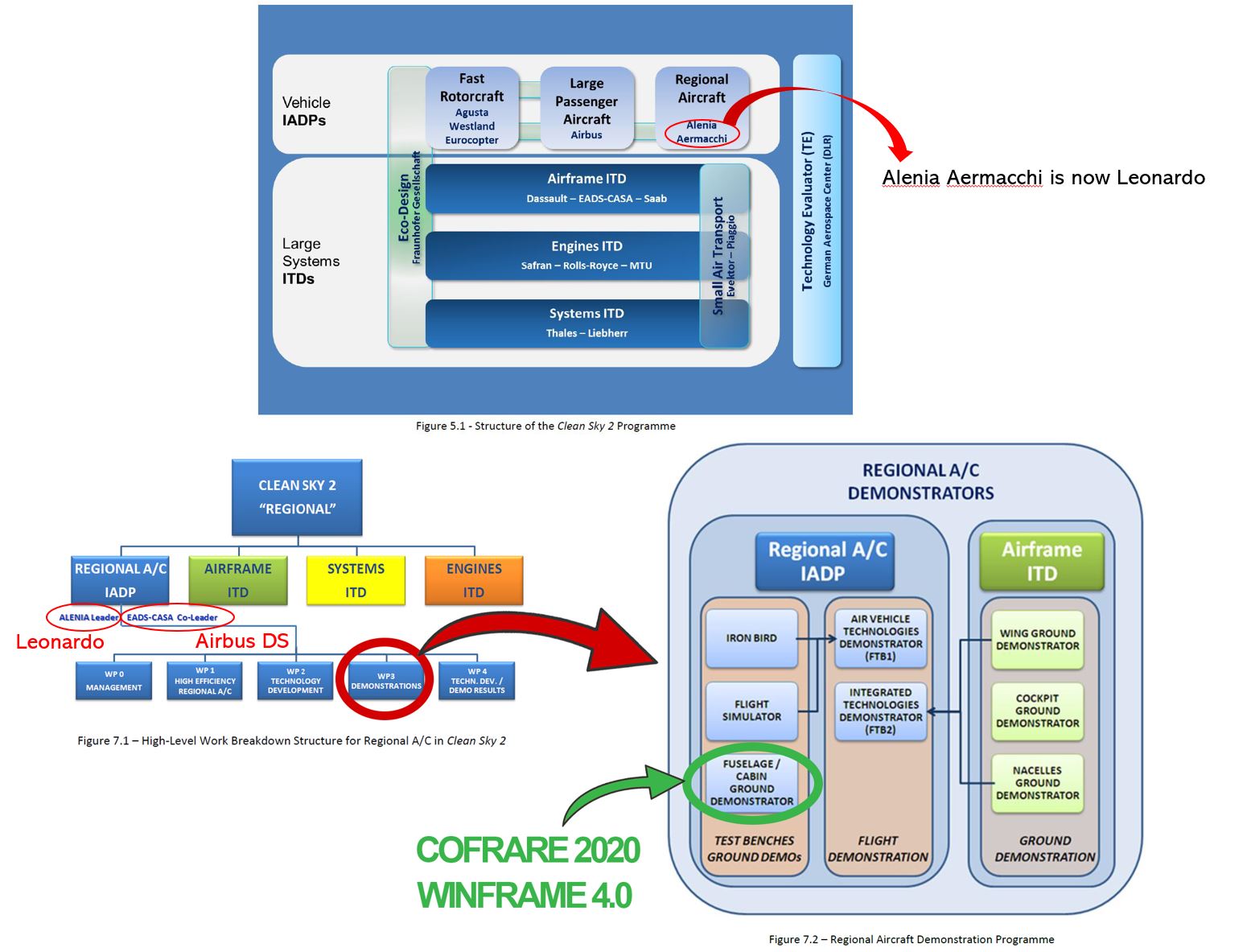
Les partenaires du projet COFRARE 2020 incluent :
- Léonard en tant que gestionnaire de sujets
- EURECAT
- DEMA
- La fabrication de composants et d'assemblages d'aéronefs A. Abete (Nola/Marigliano, Italie).
« En COFRARE 2020, nous réalisons des cadres de fuselage en RTM (moulage par transfert de résine), qui seront intégrés au démonstrateur de fuselage », explique Lagraña. « Nous utilisons la technologie Ziplus de Shikibo (Osaka, Japon) qui produit des préformes bien adaptées à l'injection de résine. Shikibo Ltd. fait partie de Composite Alliance Corp. (Dallas, Texas, États-Unis) et propose une variété de technologies de préformage textile.
Un aspect intéressant de ce programme est l'utilisation de capteurs de Synthesites (Uccle, Belgique) pour le suivi en temps réel de l'arrivée de la résine, de la température, de la pression, de la Tg et du durcissement. « Les capteurs sont situés dans des zones spécifiques de la pièce composite et de l'outil RTM pour optimiser la stratégie d'injection de résine », note Lagraña. L'injection est réalisée à l'aide d'un système hautement automatisé fourni par ISOJET (Corba, France), qui fait également partie de Composite Alliance Corp. Les capteurs Synthesites sont des capteurs diélectriques, mais contrairement à la plupart des analyses diélectriques (DEA), qui sont basées sur le courant alternatif (AC) , Synthesites utilise du courant continu (DC). "Nos capteurs fonctionnent bien avec des matériaux à haute résistivité comme les résines et parce que nous appliquons une seule tension, nous n'avons pas à analyser plusieurs fréquences, mais nous obtenons une grande précision, même à la fin du durcissement", explique le directeur de Synthesites, le Dr. Nikos Pantellis.
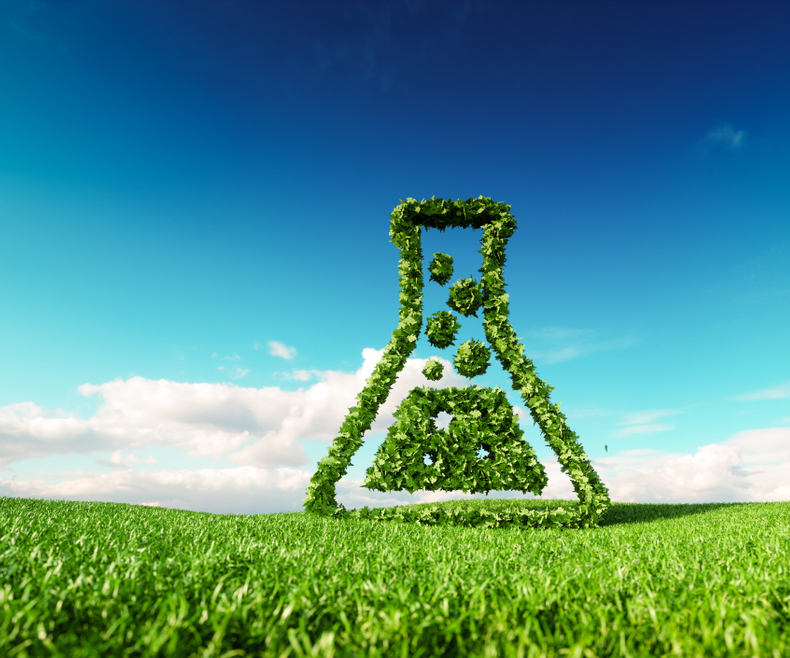
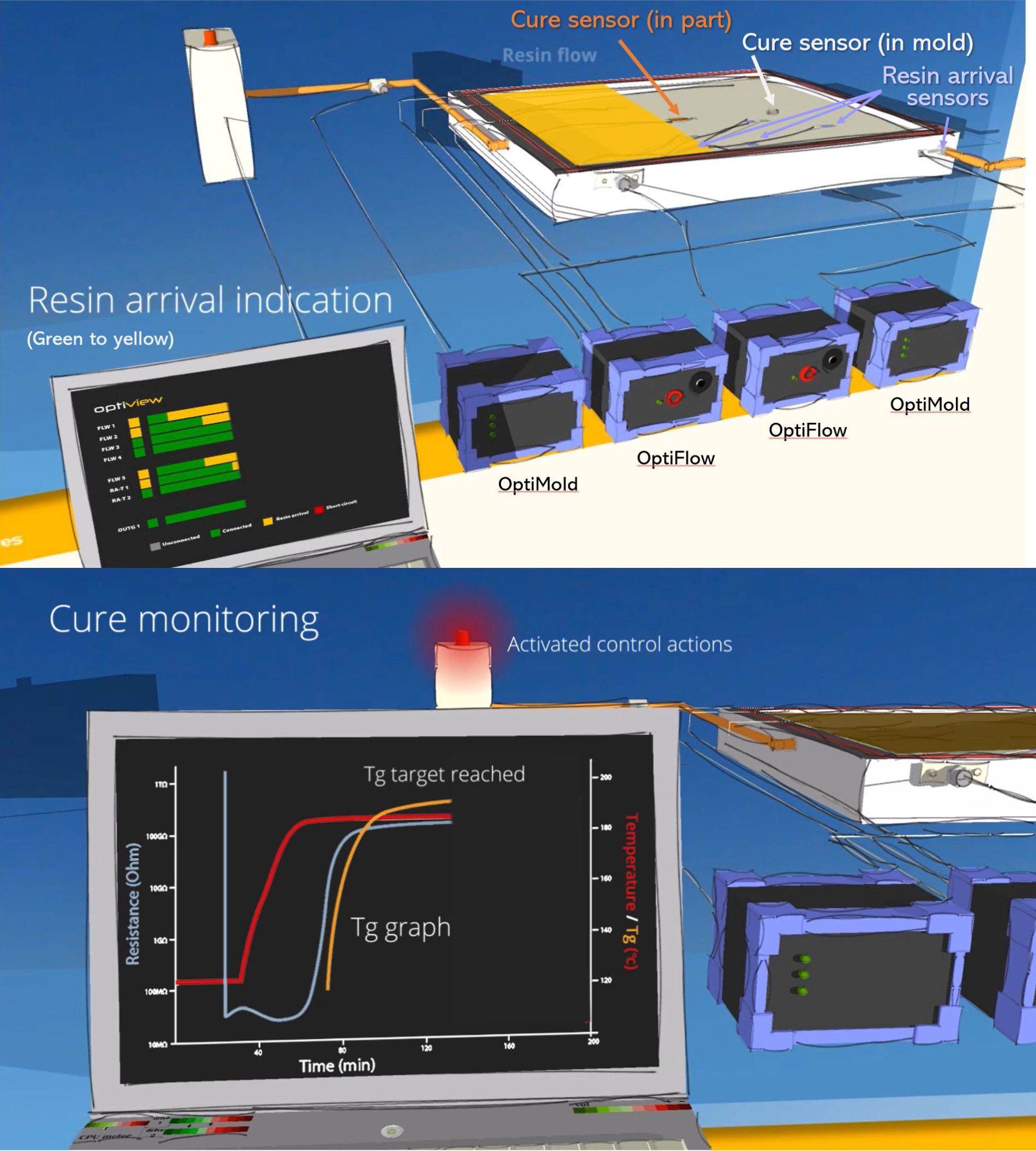
« Nous avons rencontré Synthesites lors d'une conférence SAMPE en 2011 », se souvient Lagraña. « Ils ont parlé de capteurs pour raccourcir le cycle de durcissement. Nous explorons comment automatiser les préformes pour les cadres de fuselage et même utiliser un traitement plus rapide avec HP-RTM (RTM haute pression), mais vous êtes toujours à 3-4 heures de temps de traitement. Cependant, avec Synthesites, nous avons réduit le cycle de durcissement de 50 % en surveillant la Tg. Nous testons maintenant les propriétés. Ces capteurs peuvent fonctionner à haute pression, mais dans notre traitement RTM, nous n'utilisons que 8 bars de pression. »
Les capteurs diélectriques DC Synthesites, le système de surveillance du débit de résine liquide OptiFlow et le système de surveillance du durcissement OptiMold ont été démontrés en production par divers fabricants de pales d'éoliennes. Ils sont également utilisés par Bombardier Aéronautique (Belfast, Royaume-Uni) pour produire l'aile moulée en composite liquide de la Série C, désormais Airbus 220. Le Centre aérospatial allemand (DLR, Stade, Allemagne) a démontré une réduction du cycle de durcissement jusqu'à 50 % avec les deux préimprégné autoclave et RTM, tandis que le National Composites Center (NCC, Bristol, Royaume-Uni) a démontré que même pour les résines hautement réactives, les calculs de Tg en temps réel effectués à partir des mesures de capteur de température et de résistivité de la résine sont aussi précis que la Tg mesurée à partir de panneaux durcis utilisant la calorimétrie différentielle à balayage (DSC).
Joindre des cadres avec des attaches de cisaillement TPC
Un autre élément clé de COFRARE 2020 est une méthode de production à plus grand volume pour produire les centaines d'attaches de cisaillement et de supports qui sont nécessaires pour joindre les cadres en C du fuselage RTM aux panneaux de fuselage composites. « Nous développons 255 géométries différentes pour les brackets composites thermoplastiques produits par moulage par compression », explique Lagraña. (Remarque, GKN Fokker a plusieurs projets Clean Sky 2 où il produira des supports TPC pour le démonstrateur de fuselage multifonctionnel dans l'IADP des grands avions de passagers ; ce travail dans COFRARE 2020 est destiné aux avions régionaux plus petits.) La méthode de base est illustrée ci-dessous, en utilisant des outils en acier assortis et une presse chauffée. « Le coût de tels outils de moulage par compression n'est que de 2 000 euros, ce qui est très abordable par rapport aux outillages RTM », ajoute-t-il. « L'emboutissage permet également d'obtenir des temps de cycle très courts. »
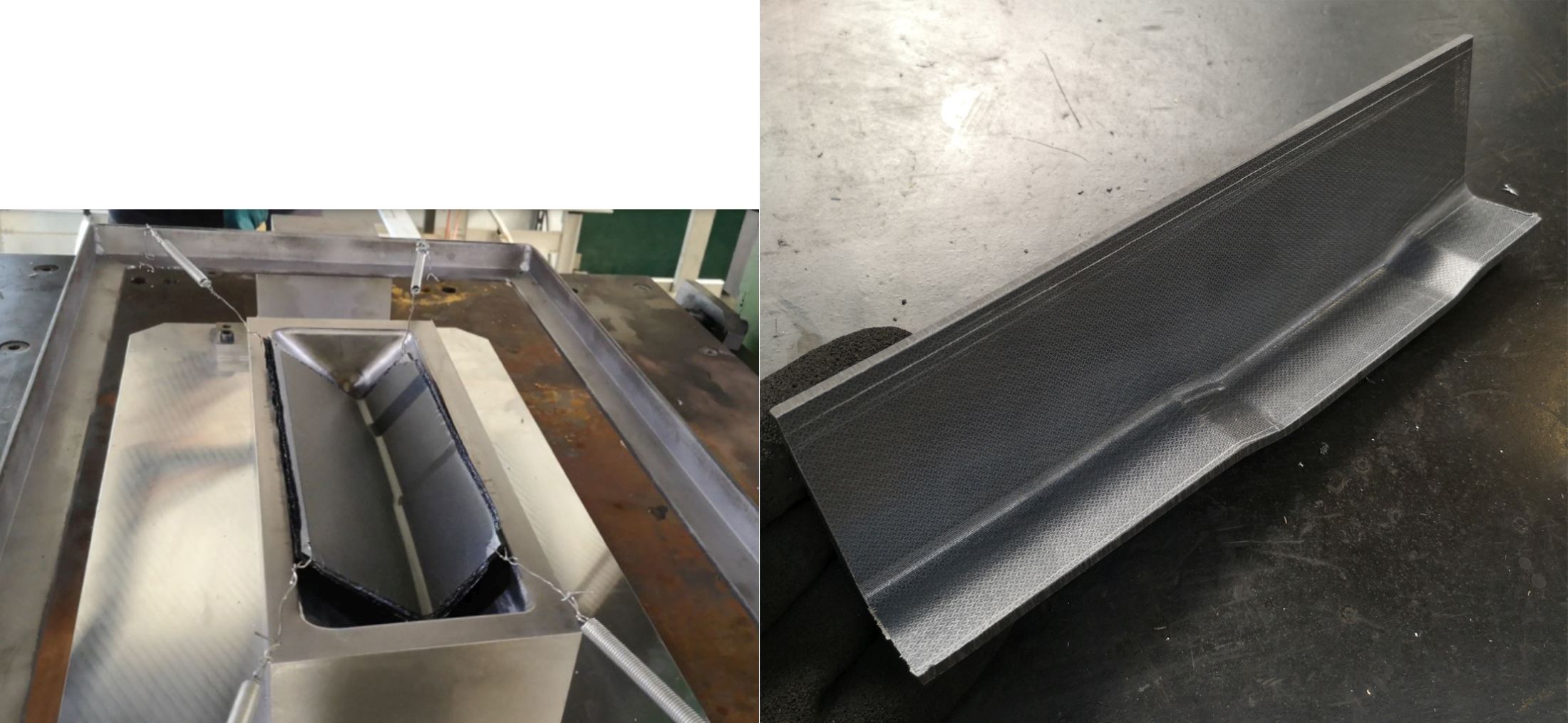
EURECAT s'efforce de rester à la pointe du développement de la technologie des composites, déclare Lagraña. « Nous pensons que la pression pour un environnement propre augmentera considérablement l'utilisation des composites dans tous les transports, et que l'abordabilité et la performance iront de pair. C'est pourquoi nous nous concentrons sur les technologies automatisées hors autoclave à offrir à nos clients. »
Restez à l'écoute pour mon prochain blog sur les projets Clean Sky 2 STUNNING et MECATESTERS, qui discutera du développement de supports TPC soudés pour le démonstrateur de fuselage multifonctionnel et d'une caractérisation complète du PAEK pour ce projet. Je bloguerai également plus en détail sur Synthesites ainsi que sur les développements du CETMA dans les composites. 2020 va être une année très intéressante pour les composites !
Résine
- Sandwich en nid d'abeille thermoplastique pour surmoulage dans des composites légers plus minces
- Personnalisation des capteurs à ultrasons pour l'optimisation et le contrôle des processus composites
- Résines époxy retransformables, réparables et recyclables pour composites
- Combinaison de mesures diélectriques CA et CC pour la surveillance du durcissement des composites
- Porte thermoplastique une première pour les composites automobiles
- LANXESS étend sa capacité de production de composites thermoplastiques renforcés de fibres continues
- TPAC et TPRC développent un procédé de recyclage des composites thermoplastiques
- Soudage de composites thermoplastiques
- Le consortium des composites thermoplastiques vise une production à haut volume pour l'automobile et l'aérospatiale