Les composites accélèrent la fabrication de façades en béton
Chaque bâtiment à plusieurs étages construit aujourd'hui nécessite une façade. Dérivé du mot français façade , qui à son tour vient de l'italien facciata , cela signifie « visage ». En bref, la façade est la structure extérieure faisant face au public qui donne au bâtiment son caractère, sa couleur et sa forme. Pour les architectes, la façade donne le ton au reste du bâtiment et en dit long sur l'intention architecturale du concepteur.
Une façade est également fonctionnelle. Il fournit la structure qui entoure les fenêtres et les portes, protège le bâtiment des intempéries et des impacts, et affecte l'efficacité énergétique du bâtiment. Une façade peut être construite à partir de divers matériaux, notamment des composites, de la pierre, de l'acier, du verre ou du béton. Le béton dans une façade, en raison de sa formabilité, peut être utilisé pour donner à un bâtiment un aspect très dimensionnel et visuellement impactant, en particulier si les formes du béton sont variées.
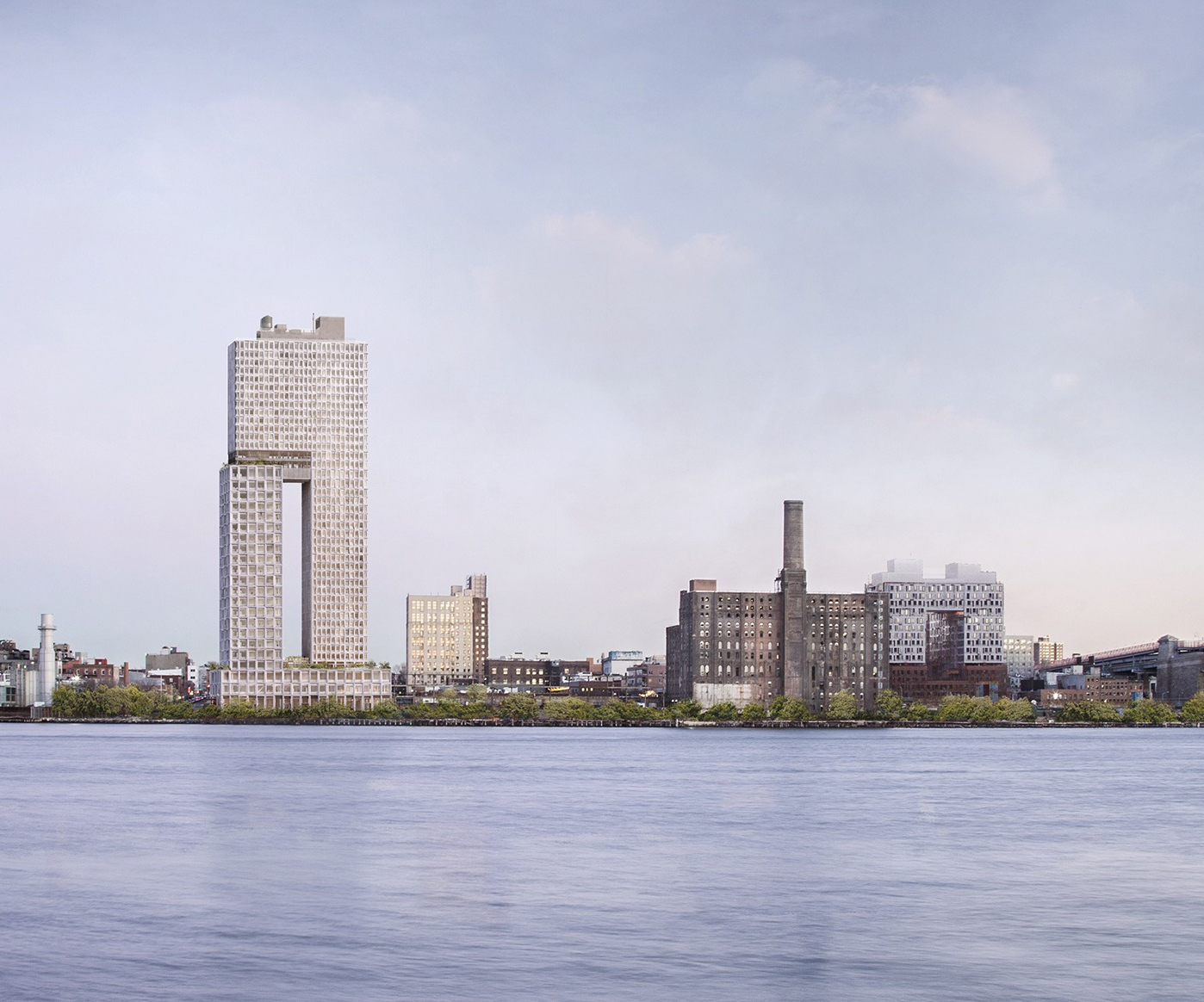
Le sucre est roi
Ce fut le cas à Domino Park, un projet de réaménagement de 11 acres le long du front de mer de Williamsburg à Brooklyn, NY, États-Unis Au cœur de Domino Park se trouve la raffinerie de sucre Domino, vieille de 138 ans, qui a fermé en 2004 et est actuellement en cours de rénovation. comme bureaux et commerces. Une partie de Domino Park comprend plusieurs nouveaux bâtiments, dont le One South First de 45 étages et le 10 Grand siamois. Pour ces bâtiments, l'architecte COOKFOX (New York, NY) a décidé d'utiliser une façade en béton qui présente plusieurs angles de surface, plusieurs formes de châssis de fenêtre et plusieurs largeurs de châssis de fenêtre pour, à distance, transmettre vaguement un sentiment de cristallinité du sucre, dans en gardant l'historique du site.
Gate Precast Co. (Jacksonville, Floride, États-Unis) a remporté le contrat pour la construction de la façade en béton - essentiellement une série de cadres de fenêtres - pour le projet One South First. L'entreprise, comme c'est généralement le cas pour une façade en béton, fabriquerait les cadres dans ses propres installations, puis expédierait les cadres finis sur le chantier où ils seraient hissés en place pour être installés par une grue. Si Gate avait décidé de suivre la tradition, il aurait construit des moules en bois avec lesquels façonner tous les cadres en béton. Gate, cependant, a décidé de ne pas suivre la tradition.
Pour comprendre, remontez à 2017, lorsque Gate s'est associé au Precast/Prestressed Concrete Institute (PCI, Chicago, Illinois, États-Unis) et au Oak Ridge National Laboratory (ORNL, Oak Ridge, Tenn., États-Unis) pour effectuer une évaluation préliminaire de l'utilisation de la fabrication additive grand format pour construire des moules composites pour le formage de béton préfabriqué en usine. Cette évaluation a été réalisée à l'aide d'une machine BAAM (Big Area Additive Manufacturing) à l'ORNL. BAAM est une machine de fabrication additive grand format avec une enveloppe de construction de 25 mètres carrés, co-développée par ORNL et Cincinnati Inc. (Harrison, Ohio, États-Unis) Gate s'est engagée à construire des moules composites pour la façade One South First. Le projet nécessitait 80 moules au total, dont 37 seraient imprimés. Les 43 autres seraient en bois. Au moment où cette décision a été prise, les délais de livraison des moules étaient serrés.
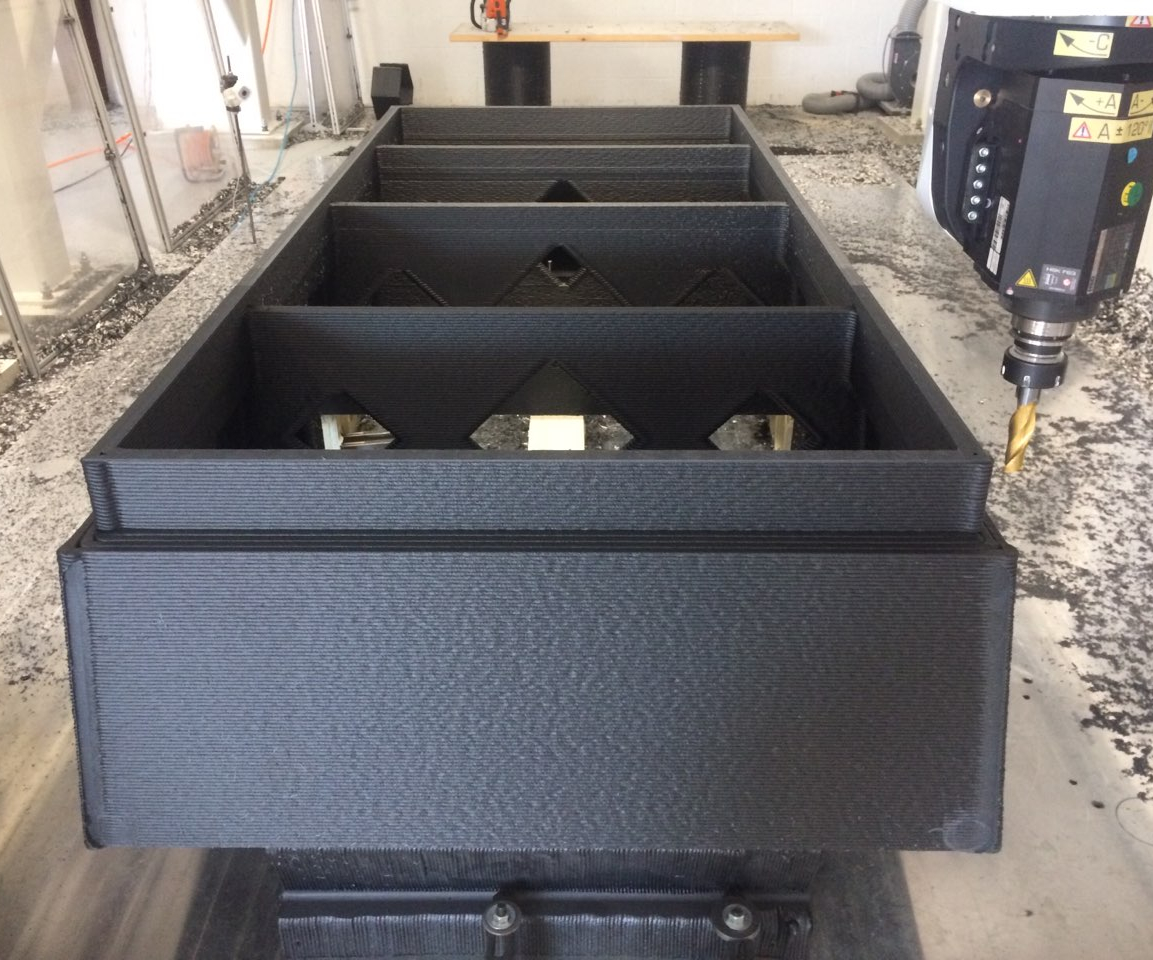
En 2016, Additive Engineering Solutions (AES, Akron, OH) avait acquis sa première machine BAAM auprès de Cincinnati Inc. Pour cette raison, ORNL et Gate Precast se sont tournés vers AES pour obtenir de l'aide. Andrew Bader, vice-président et co-fondateur d'AES, déclare que son entreprise et ORNL ont divisé le lot de travail, AES produisant 18 des 37 moules. Bader dit que chaque moule de cadre de fenêtre mesure environ 5 à 6 pieds de large, 9 à 10 pieds de haut et 16 pouces de profondeur et pèse environ 500 lb.
Bader dit que l'intérieur de la géométrie des moules, parce qu'ils sont conçus pour produire des cadres qui entourent les fenêtres rectangulaires, était relativement simple. Cependant, la conception des surfaces extérieures des cadres, comme indiqué, était plus complexe, avec des profondeurs et des angles variés intégrés dans chaque moule. Une forme imprimée a remplacé une forme en bois composée de nombreuses pièces coupées individuellement et clouées ensemble. « La géométrie était simple, mais compliquée », dit Bader. « Le projet nécessitait plusieurs conceptions de cadre uniques, en fonction de l'emplacement du cadre. »
Pour une partie de sa production, AES a choisi un composé LNP THERMOCOMP AM, un matériau à haut module et à faible gauchissement à base d'ABS avec un renfort en fibres de carbone haché à 20 % fourni par SABIC (Houston, Texas, États-Unis). Bader dit qu'il a fallu 8 à 10 heures à la machine BAAM pour construire chaque moule monolithique, suivies de 4 à 8 heures d'usinage et de finition dans une machine CNC Quintax (Stow, Ohio, États-Unis). Il rapporte que les moules ont été poncés aux dimensions requises, mais pas scellés.
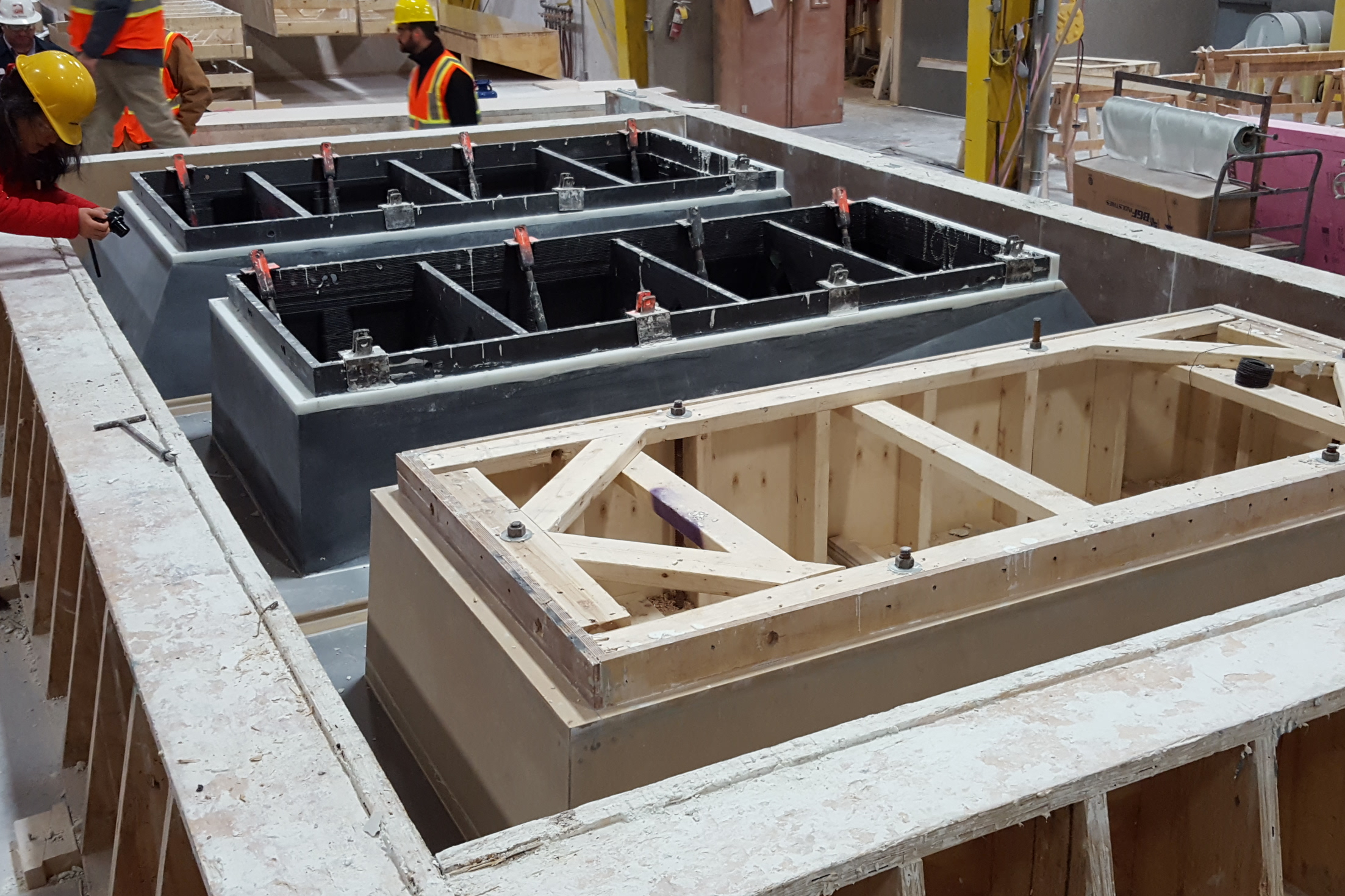
Fabrication de cadres de fenêtres
Les moules ont été livrés aux installations de Gate à Winchester, dans le Ky., aux États-Unis, où ils ont été utilisés avec les 43 moules en bois traditionnels que Gate a construits pour le projet. Les moules en bois ont été assemblés à la main par les employés de Gate, puis un tapis de fibre de verre et une couche de résine ont été appliqués, avec de l'huile de coffrage pulvérisée pour faciliter la libération du cadre en béton formé. De l'huile de forme a également été pulvérisée sur les moules composites pour faciliter le démoulage.
Pour effectuer une coulée de béton, plusieurs moules ont été placés sur une table de coulée en bois de 40 à 50 pieds de long. Les moules ont été regroupés pour produire un cadre simple, un cadre double ou un cadre triple. Des barres d'armature en acier ont été placées à l'intérieur de chaque moule et du béton a été coulé autour des barres d'armature. La table de coulée a ensuite été vibrée pour consolider le béton. Après 14 à 20 heures de durcissement, les cadres de fenêtres ont été démoulés, lavés à l'acide et polis. Ensuite, les fenêtres ont été installées et l'ensemble du colis a été expédié par camion jusqu'au chantier de construction à Brooklyn.
Bader dit que les moules composites AES, en collaboration avec les moules en bois traditionnels, ont rapidement révélé leurs avantages. Premièrement, dit-il, un moule en bois ne permet que 15 à 20 coulées de béton avant de devoir être retiré du service et remis à neuf ou remplacé. Les moules AES, à l'inverse, ont permis 200 coulées de béton avec une remise à neuf minimale ou un temps hors service. Et les 200 coulées, dit Bader, représentaient la fin du projet, pas la fin de la durée de vie du moule. "C'est juste là qu'ils se sont arrêtés", dit-il. « Si nos moules sont bien entretenus, nous pensons qu'ils peuvent être utilisés des centaines et des centaines de fois. »
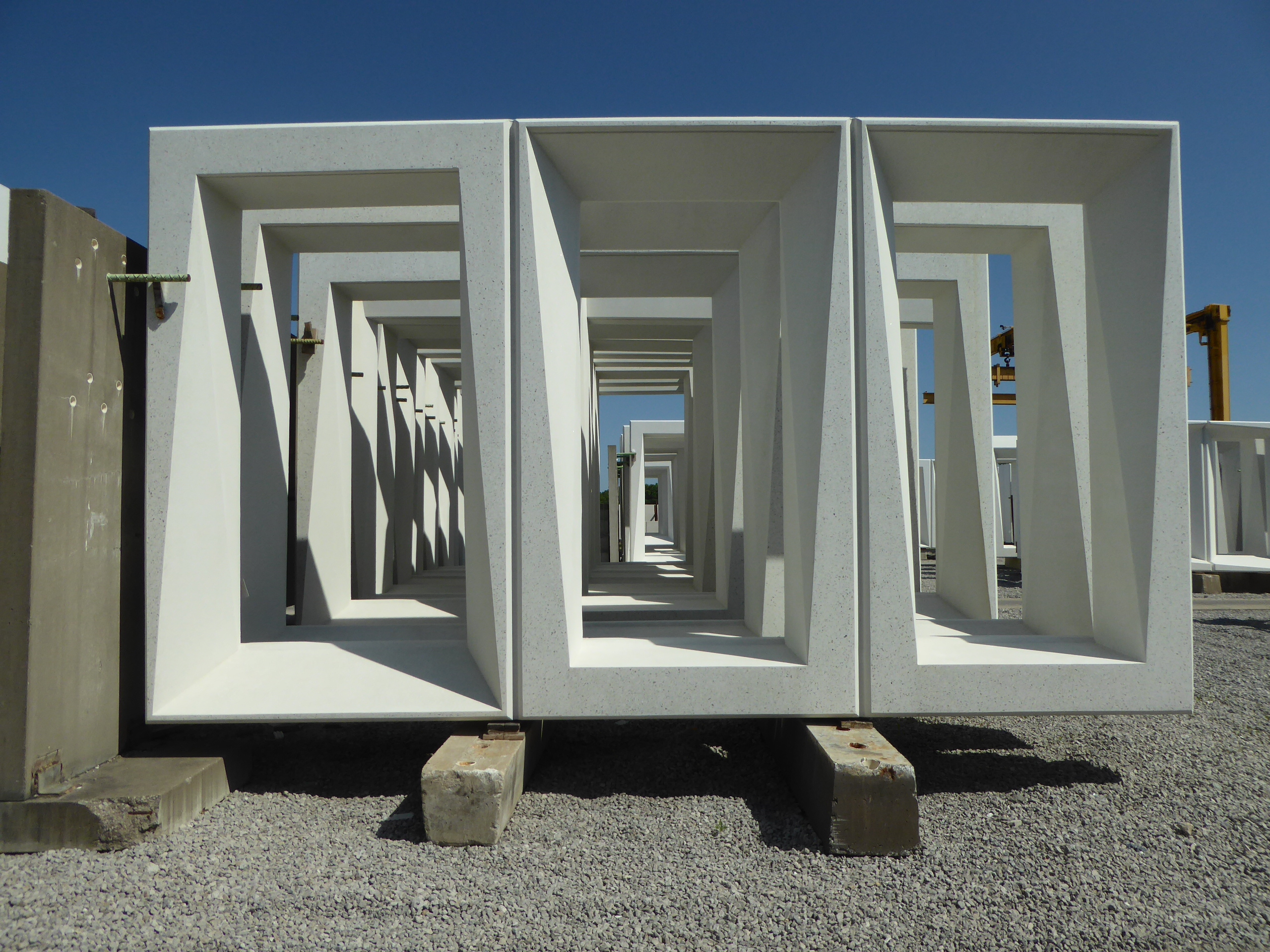
De plus, pour une utilisation de 150 coulées ou plus, Gate calcule qu'il aurait fallu jusqu'à 10 moules en bois pour atteindre les performances d'un moule AES. De plus, étant donné qu'il faut 40 heures-personnes à Gate pour produire un moule en bois, sans les 37 moules composites, l'entreprise n'aurait pas respecté les exigences de calendrier du projet One South First.
Bader admet qu'un moule composite AES coûte quatre fois plus cher qu'un moule en bois, mais qu'il est au moins 10 fois plus durable. « La façon dont les formes préfabriquées ont été construites est restée relativement inchangée pendant des décennies », affirme Bader. "Tout d'un coup, un jour, nous créons des formulaires 3D de 500 livres et tout le monde a été choqué." Cela dit, il reconnaît que la fabrication additive de tels moules est la plupart rentable dans les applications où les coffrages à béton ont une géométrie compliquée ou une répétition élevée — même forme plusieurs fois.
AES, rapporte Bader, possède et exploite maintenant quatre machines BAAM et peut produire des pièces jusqu'à 8 pieds de haut. Des pièces beaucoup plus grandes ont été construites en joignant plusieurs pièces.
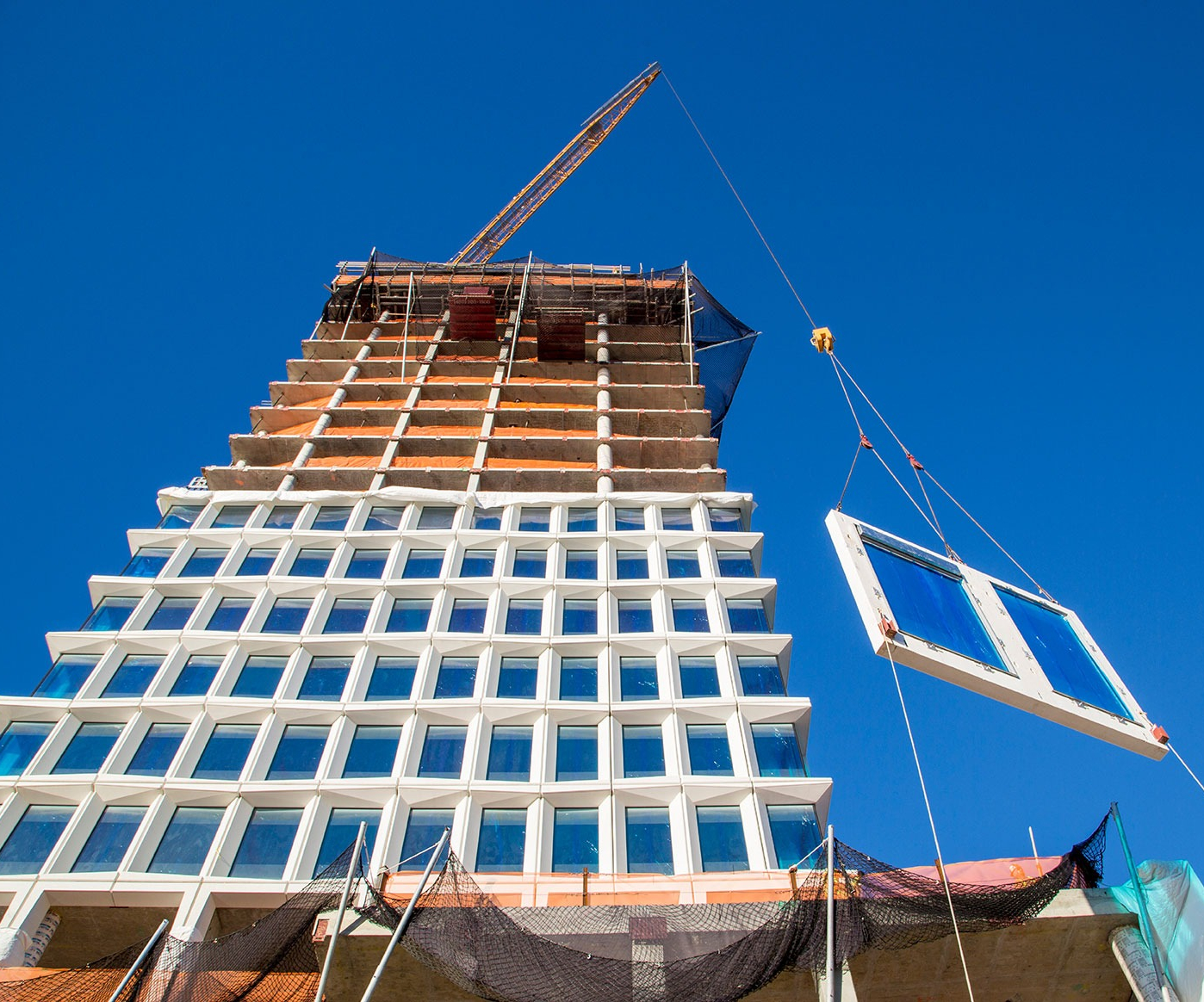
Résine
- Compteur de vitesse
- Béton
- CompositesWorld SourceBook 2022
- Dépannage du thermoformage des composites thermoplastiques
- L'évolution des composites additifs
- ATL Composites contribue au projet de réhabilitation des piliers en béton
- RS Electric Boats sélectionne Norco pour la fabrication de composites
- Soudage de composites thermoplastiques
- Composites hautes performances en Israël