chef-d'œuvre à forte intensité de composites :Corvette 2020, partie 1
Pour la partie 2, lisez « chef-d'œuvre à forte intensité de composites :Corvette 2020, partie 2 ».
La très attendue Corvette de Chevrolet de huitième génération (C8) de General Motors Co. (GM, Detroit, Michigan, États-Unis), qui a suscité des éloges depuis sa révélation officielle le 18 juillet 2019, a commencé la production commerciale plus tôt cette année. La nouvelle Corvette Stingray les cabriolets et les coupés se distinguent non seulement par leur beauté et le fait que GM a produit une fusée à moteur central hautes performances, homologuée pour la rue, à partir de moins de 60 000 $ USD - un tiers du prix d'un moteur central aux performances comparables voitures - mais ils arborent également une gamme impressionnante de contenus composites nouveaux et véritablement innovants, que nous décrirons ici et dans la partie 2 le mois prochain.
La nouvelle configuration du moteur change tout
L'ingénierie de GM est entrée dans la conception préliminaire en sachant qu'elle travaillerait sur un véhicule à moteur central - la première Corvette de production en huit générations pour arborer cette configuration. « Nous avons fait évoluer l'architecture du moteur avant autant que possible pour les performances, donc le passage à une conception de moteur central était la prochaine étape logique pour améliorer une voiture déjà excellente et être le leader du segment », explique Tadge Juechter, ingénieur en chef exécutif de GM. -Global Corvette . Équipée du pack performance Z51, la Corvette Stingray 2020 peut accélérer de 0 à 60 mph (0-97 kmh) en 2,9 secondes et atteindre des vitesses de pointe de 194 mph (312 kmh). Pousser le moteur vers l'arrière du véhicule a affecté de nombreux éléments, notamment le centre de gravité de la voiture, la position relative des occupants, l'emplacement de la transmission et la conception des panneaux de soubassement et du coffre. La conception du moteur central a également introduit des températures de fonctionnement et un bruit plus élevés dans de nouvelles zones de la voiture.
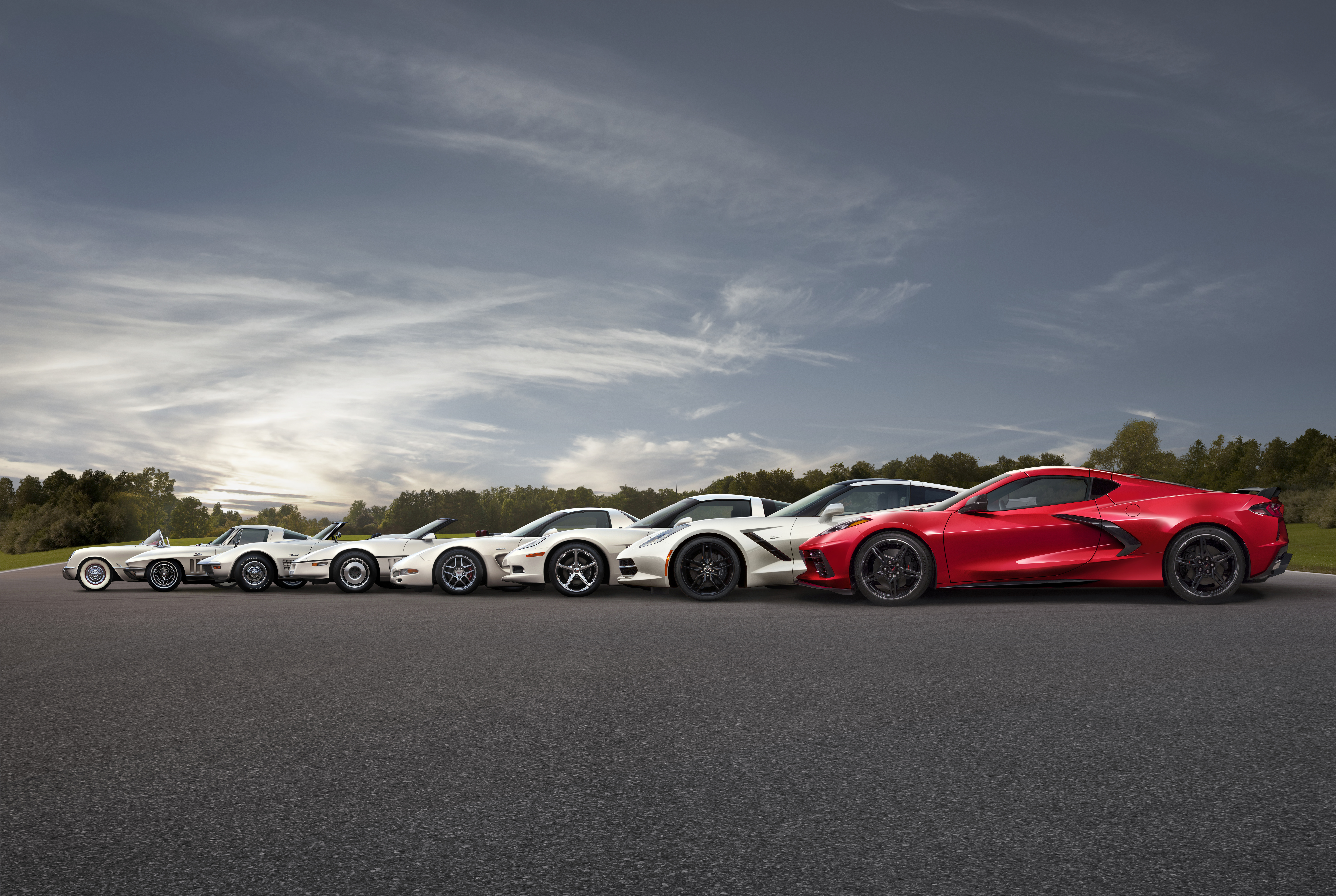
« En raison du moteur central, nous avons dû faire les choses différemment », explique Ed Moss, Corvette responsable du groupe d'ingénierie de la structure de la carrosserie. « Dès le début, nous avons eu tellement de discussions sur la façon d'agencer la structure du corps. À un moment donné, tout était sur la table alors que nous discutions de la meilleure façon de concevoir et de construire chaque système. Par exemple, nous avons débattu du métal par rapport au composite pour les timoneries. Si nous avions conservé les timoneries composites du C7, nous aurions dû nous lier au pilier de charnière [un pilier], qui est immédiatement adjacent à la roue avant d'un véhicule à moteur central, laissant très peu d'espace pour l'emballage. Nous y sommes allés avec du métal. Nous avons même brièvement discuté des panneaux de carrosserie en métal par rapport aux panneaux de carrosserie composites. Cependant, il aurait été économiquement impossible de créer les lignes de style de la C8 en métallisé. »
« Un vrai défi auquel nous avons été confrontés était de savoir comment gérer l'induction d'air », se souvient Chris Basela, Corvette ingénieur en chef de la structure de la carrosserie, expliquant la nécessité d'une méthode différente pour acheminer l'air de refroidissement dans et à travers le moteur V8 de 6,2 litres à aspiration naturelle de 495 chevaux, qui génère un couple de 470 livres-pied (637 Newton-mètres). «Nous avons essayé toutes sortes de conceptions qui forçaient l'air à emprunter des chemins vraiment tortueux, créant des tourbillons et des flux dont nous ne voulions pas. Il a fallu beaucoup de travail itératif avec l'équipe du groupe motopropulseur pour développer le meilleur chemin pour le flux d'air, car la voiture doit respirer librement sans restriction. Nous avions également besoin d'accéder à la boîte à air et avons dû contourner l'espace du coffre arrière. Un autre problème était la chaleur et le bruit du moteur dans l'habitacle, car les occupants ne sont plus assis derrière le moteur mais sont placés directement devant celui-ci. Et nous étions particulièrement soucieux de la qualité de l'air dans les cabines, car les lois avaient changé en Europe et ailleurs depuis le C7, nous avons donc travaillé très dur pour réduire les COV [composés organiques volatils]. »
« Même en cherchant comment assembler la voiture était un défi », ajoute Moss. « Avec une conception à moteur avant, vous disposez d'un long capot et d'un grand compartiment moteur, offrant aux opérateurs beaucoup d'espace pour construire la voiture depuis l'intérieur du compartiment, même avec la poutre de pare-chocs avant déjà soudée. Sur la Corvette à moteur central , avec son clip avant très court, nous gardons l'avant de la voiture ouvert au fur et à mesure de la construction du véhicule, puis boulonnons le pare-chocs avant. »
« C'était tout un exercice d'équilibre pour obtenir les formes appropriées, tout en veillant à ce que nos fournisseurs puissent produire les pièces et notre équipe à Bowling Green [la Corvette de GM basée au Kentucky usine d'assemblage] pourrait les assembler », poursuit Basela. "En fin de compte, il n'y avait qu'un seul composite de transfert de la carrosserie de la C7 à la C8." Il s'agissait d'un composé de moulage en feuille (SMC) à densité spécifique (SG) de classe A robuste de 1,2 développé pour la Corvette 2016 et utilisé dans une variété de fermetures extérieures sur le nouveau véhicule.
Architecture du véhicule
Depuis quatre générations (C5-C8), Corvettes ont présenté une structure de corps multi-matériaux à trois couches :le cadre , généralement un mélange d'aluminium ou d'acier - cette fois avec une pièce en composite renforcé de fibres de carbone (CFRP) ; la structure du corps , qui est en grande partie un composite lié pour capitaliser sur la flexibilité de conception et de fabrication ; plus des clôtures (panneaux de carrosserie), qui sont composites depuis Covette Débuts en juin 1953. Cette structure hybride en couches offre non seulement un allégement abordable dans des volumes de production élevés - en particulier pour les voitures de cette classe de performances - mais permet également de produire plusieurs variantes de véhicules avec un faible investissement en outillage. En fait, pour la C8 actuelle, GM a réussi à produire tous les panneaux de carrosserie composites de classe A (intérieurs et extérieurs collés) à la fois sur le modèle de base coupé et cabriolet en utilisant seulement 20 outils.
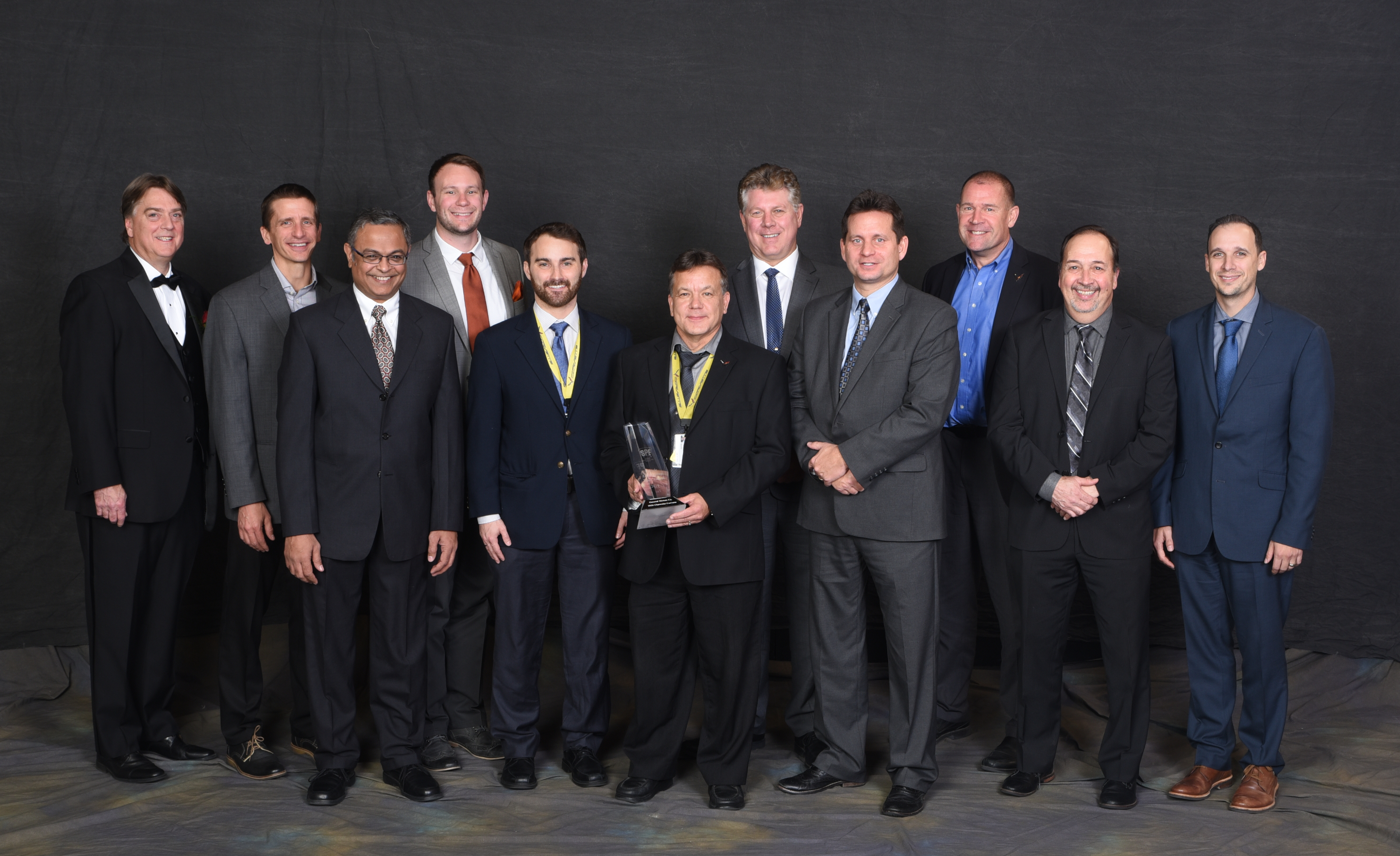
De plus, les Corvettes ont toujours été conçus avec une architecture à toit ouvert, qu'il s'agisse de cabriolets ou de coupés à panneaux de toit fixes ou amovibles. Parce que les véhicules à toit ouvrant sont généralement moins rigides que ceux à toit fixe, un objectif important pour chaque Corvette' L'ingénierie de S est toujours de créer la base la plus rigide possible pour améliorer la suspension et la direction. Historiquement, les tunnels (boîtiers de transmission et arbres de transmission sur les véhicules à moteur avant) ont dominé les Corvette structures de carrosserie et ont été des catalyseurs clés pour atteindre une rigidité en torsion élevée. Dans le cas de la nouvelle Corvette , GM a atteint une rigidité encore plus élevée. Avec le toit retiré, la carrosserie de la C8 est 53,78 % plus rigide qu'un concurrent de référence à moteur central hautes performances, 29,27 % plus rigide qu'un deuxième concurrent à moteur central hautes performances et 13,79 % plus rigide que la C7. Deux pièces composites ont contribué de manière importante à la rigidité du véhicule :l'une directement fixée à la structure du châssis (poutre de pare-chocs arrière) et l'autre fixée au soubassement (fermeture du tunnel inférieur).
Structure du cadre
Le cadre du C8 est en grande partie en alliage d'aluminium avec une pièce en PRFC développée pour répondre aux objectifs stricts de GM en matière de dollar par kilogramme. En revanche, le cadre du C7 était tout en aluminium et le C6 était principalement en acier.
La seule pièce composite directement montée sur le cadre qui se déplace avec la carrosserie en blanc (BIW) à travers le processus de revêtement de rouille électrophorétique (que GM appelle ELPO), est une poutre de pare-chocs arrière unique en CFRP. Cette partie aide à rigidifier le cadre et contribue aux performances en cas de choc arrière. Sa forme incurvée - possible grâce à un nouveau procédé appelé pultrusion de rayon développé par Thomas GmbH + Co. Technik + Innovation KG (TTI, Bremervörde, Allemagne) - lui permet de s'adapter aux repères de style arrière et de s'adapter à un espace limité tout en maintenant l'intégrité dimensionnelle proche à la chaleur du compartiment moteur. En tant que première pièce pultrudée incurvée de l'industrie automobile (voir notre article complet sur cette pièce dans le numéro de CW de mai 2020), la poutre creuse à deux chambres a été produite par Shape Corp. (Grand Haven, Michigan, États-Unis) sur des équipements développés et construit par TTI. La poutre ne pèse que 1,3 kilogramme et est dotée d'un œillet de remorquage collé/boulonné capable d'une force de traction de 25 kilonewtons.
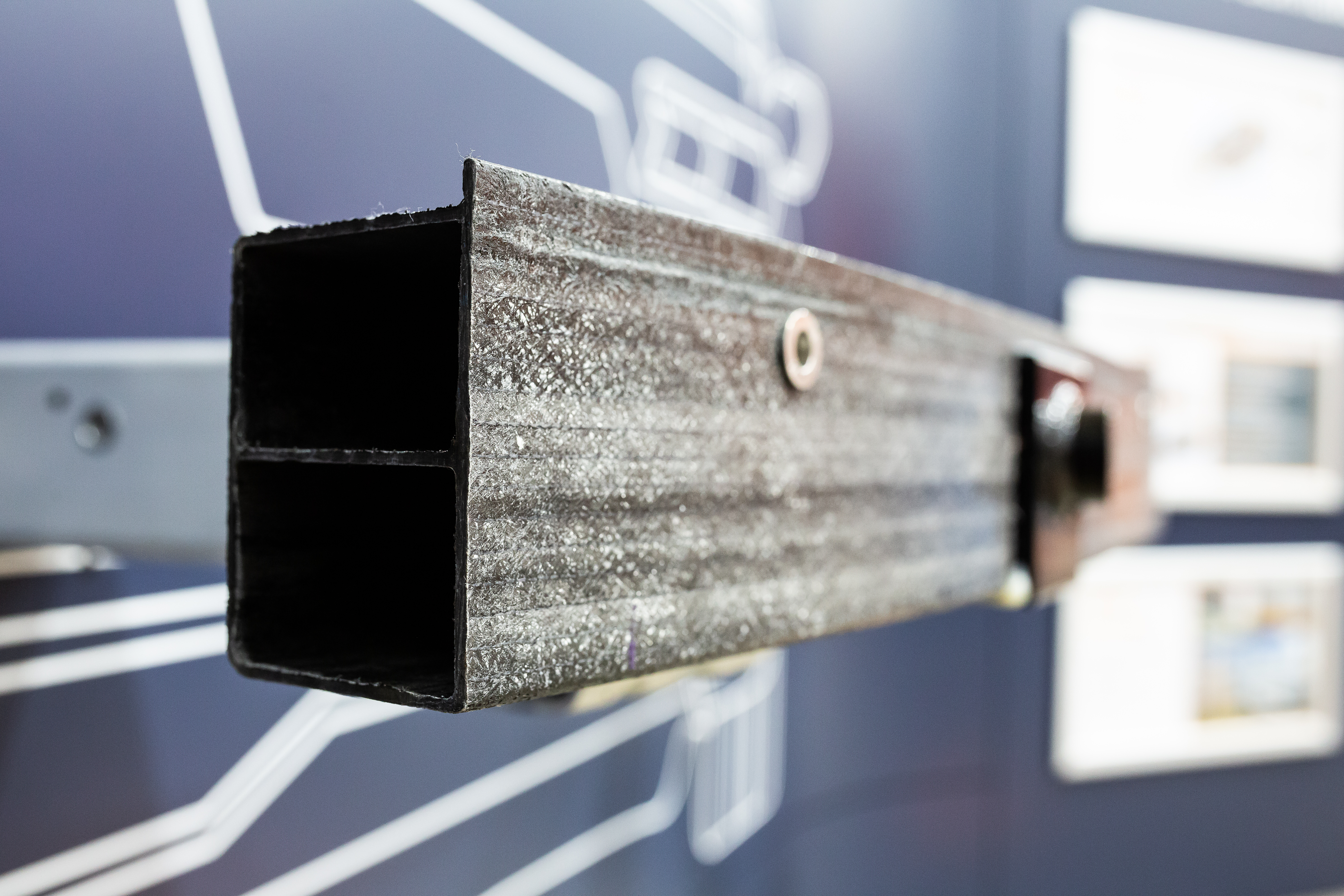
Structure du corps :partie A
Pratiquement tous les composants de la structure de la carrosserie de la C8 sont en composite et sont collés et/ou boulonnés au cadre après que ce dernier a subi l'ELPO. Les pièces composites notables à ce niveau comprennent les fermetures structurelles du soubassement et le plancher - que nous couvrirons dans ce numéro - et les coffres avant et arrière, les conduits d'induction et l'entourage arrière et la cloison - que nous couvrirons, ainsi que les panneaux de carrosserie et les garnitures , le mois prochain.
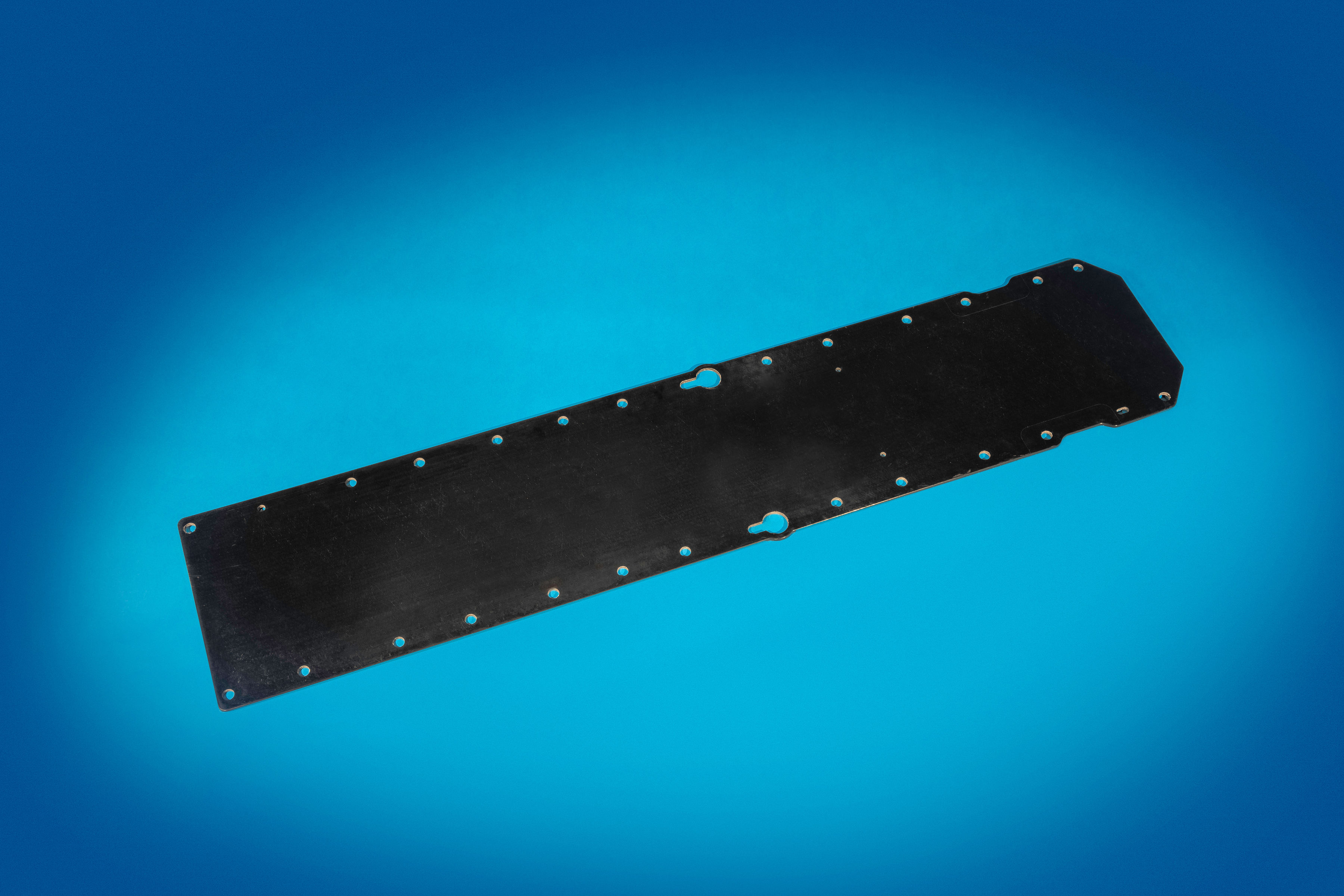
La fermeture structurelle amovible du tunnel inférieur du C8, qui agit comme une porte d'accès, contribue à plus de 10 % de la rigidité en torsion du véhicule et agit comme un chemin de charge principal lors d'un accident. Ce panneau hybride-composite se compose de trois couches de préforme en fibre de verre. Ceux-ci se composent de fibres continues/tissées et hachées/aléatoires à 38 % de fraction volumique de fibres (FVF), avec des voiles ajoutés aux couches de face supérieure et inférieure sur chaque pile pour une finition de surface améliorée. Les préformes en verre sont intercalées avec deux couches de préformes fabriquées à partir de fibre de carbone à module standard Toray (Tokyo, Japon) T700 12K sous forme de tissu biaxial NCF à 21% FVF et d'une matrice d'ester vinylique (VE). La fermeture est produite par Molded Fiber Glass Co. (MFG, Ashtabula, Ohio, États-Unis) à l'aide de son processus exclusif PRIME (Prepositioned Reinforcement assurant l'excellence de la fabrication), un type de moulage par compression liquide (LCM).
Mis à part une seule fermeture en aluminium près des roues arrière qui fait partie du berceau du moteur, les panneaux de soubassement restants sont constitués de SMC moulés par compression ou de thermoplastiques moulés par injection. Entre autres avantages, ces panneaux réduisent les turbulences et la traînée du soubassement, améliorent le rendement énergétique et empêchent l'humidité, la poussière et les pierres d'entrer dans le moteur et la transmission du véhicule. De plus, ils fournissent la base dimensionnelle pour de multiples interfaces extérieures et intérieures.
La faible densité mais structurelle Les panneaux SMC présentent de nouvelles formulations (dans ce cas, 40 % de fibre de verre coupée FVF/résine de polyester insaturé (UP)) développées par MFG. Le matériau est appelé SMC « flottant » car la densité de chaque panneau est inférieure à 1,0 (SG moyen =0,97) et peut donc flotter dans l'eau. MFG a produit toutes les pièces structurelles SMC et LCM de la voiture.
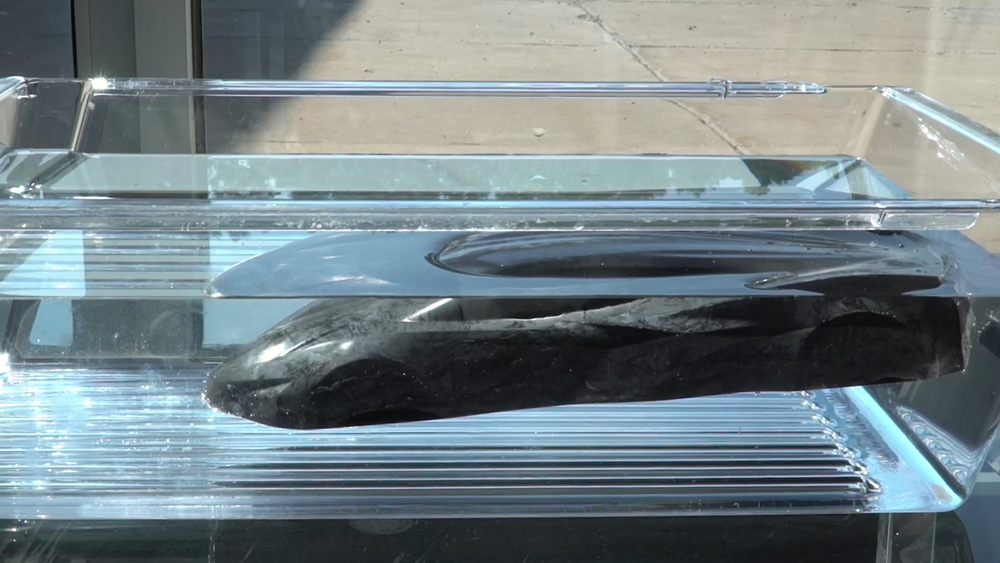
Le véhicule arbore également un plancher hybride optimisé pour la flexion en torsion et la protection contre les chocs latéraux (en engageant les bas de caisse et le tunnel, auxquels il est joint). Les panneaux de plancher comportent de l'aluminium estampé faisant face à la cabine et collé à des feuilles de composite 1,5-SG faisant face à la route (60 % en poids de fibre de verre continue et tissée/VE) produites via le processus PRIME. Avant de thermocoller les deux couches avec l'adhésif structurel polyuréthane Pliogrip 9100 d'Ashland Global Holdings Inc. (Wilmington, Del., États-Unis), MFG nettoie et prépare les matériaux.
Toutes les pièces composites directement liées au cadre C8 sont d'abord soumises à une ablation laser, un processus développé par GM, MFG et Adapt Laser Systems LLC (Kansas City, Mo., États-Unis) pour la Corvette 2016 et adapté d'une méthode de l'industrie des composites pour le nettoyage des moules. L'ablation au laser remplace le ponçage manuel et réduit la main-d'œuvre, le temps et les coûts, élimine la poussière et améliore la répétabilité. La trajectoire laser, l'angle d'attaque et le niveau d'énergie sont personnalisables pour le matériau et la géométrie de chaque pièce. Pour maximiser la flexibilité de fabrication, l'ensemble du soubassement, y compris le plancher, est relié au cadre et à lui-même par collage et vis.
Dans le numéro d'août de CW, nous continuerons à couvrir l'innovation des composites sur la nouvelle Corvette , reprenant avec des composants supplémentaires au niveau des structures de carrosserie et se terminant par des fermetures extérieures (panneaux de carrosserie), ainsi que des garnitures et des améliorations supplémentaires. Voir la partie 2.
Résine
- 10 avantages du cloud computing en 2020
- Direction de la maintenance, partie 3
- Introduction aux harmoniques :Partie 1
- Durabilité dans le secteur manufacturier - Partie 3
- Tendances et défis 2020 impactés par le Covid-19 : 1ère partie
- Le virage est facultatif
- Qu'est-ce qu'un numéro de pièce ?
- Usinage de petites pièces
- Cylindricité en GD&T