Préformage automatisé, partie 7 :Fill Gesellschaft
Ceci est le dernier volet d'une série en sept parties sur le préformage. Pour en savoir plus sur cette série, cliquez sur les liens ci-dessous :
SOURCE :remplissage Gesellschaft
Historique des cas d'automatisation
Les premières machines de Fill ont été développées pour automatiser la production de skis pour Fischer. Aujourd'hui, il faut 25 pour cent des travailleurs pour produire 80 pour cent du volume de production annuel d'origine. Notez également que les skis sont de conception hybride, comprenant des couches de composite de verre et/ou de fibre de carbone, des noyaux en bois, des carres en acier et de multiples types de plastique.
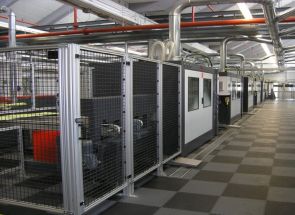
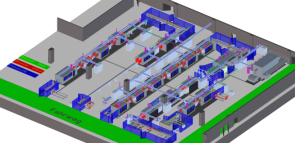
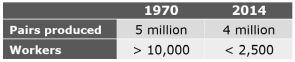
Le remplissage a été fourni plusieurs générations d'équipements automatisés pour la production de skis composites.
SOURCE :Remplissez la présentation CAMX 2017 de la Gesellschaft.
BMW
Alors que BMW développait les modèles i3, i8 et les nouveaux modèles de la série 7, qui utilisent tous des composites en plastique renforcé de fibres de carbone (PRFC), Fill a fourni une gamme de solutions d'automatisation.
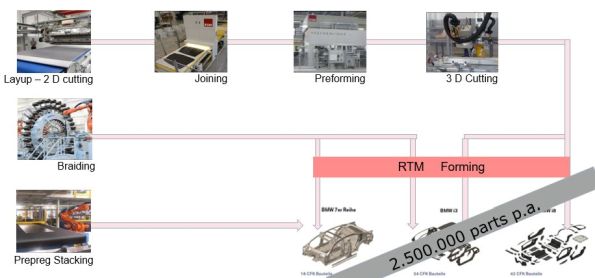
SOURCE :remplissage Présentation Gesellschaft 2017 CAMX
Monocoques composites
Fill a également développé une ligne de production unique pour Mubea CarboTech capable de produire des monocoques CFRP pour deux modèles de voitures différents :la Volkswagen VW XL1 et la Porsche 918 Spyder. Cette ligne automatisée comprenait des outils de moulage actionnés en plusieurs pièces, une presse de moulage par transfert de résine haute pression (HP-RTM), des capacités de post-durcissement et d'usinage.
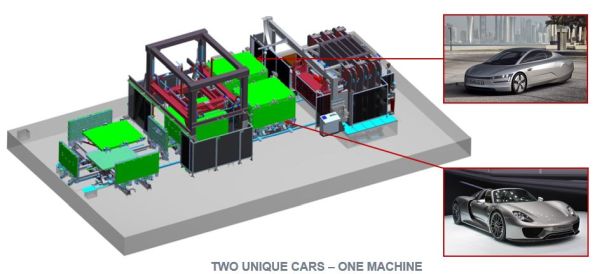
Remplir fourni un ligne de production monocoque composite pour Mubea CarboTech.
SOURCE :Remplissez la présentation CAMX 2017 de la Gesellschaft
Automatisation du layup
Pour le drapage automatisé, Fill a développé des systèmes pour une gamme de matériaux différents, y compris du tissu sec jusqu'à 3 m de largeur (pour une production en plus grand volume chez BMW). Le système de pose automatique de capuchons de longeron SpeedLayer 800 pour pales d'éoliennes applique un préimprégné en fibre de carbone unidirectionnel jusqu'à 800 mm de largeur à une vitesse rapportée de 1,5 m/s et une précision de ±1,5 mm. Il peut gérer des rouleaux préimprégnés de 600 kg et intègre des fonctions de validation de processus et d'assurance qualité.
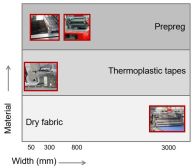
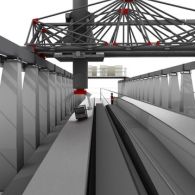
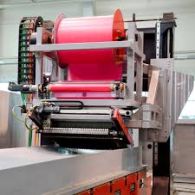
Fill s'est développé une gamme de systèmes de drapage automatisés (à gauche), y compris SpeedLayer 800 pour les chapeaux de longeron de pale de vent utilisant un préimprégné de carbone UD jusqu'à 800 mm de largeur (à droite).
SOURCE :Remplissez la présentation CAMX 2017 de la Gesellschaft
Le projet Low-Cost Flexible Integrated Composite Process (LOWFLIP) était une initiative de 3 ans (octobre 2013-octobre 2016) financée par l'UE qui comprenait Fill et neuf autres partenaires, visant à automatiser la mise en place du préimprégné pour le transport durci hors autoclave (OOA). structure. Il comprenait trois manifestants :
- Paroi avant de 2,5 × 2,9 m pour une remorque de camion
- Longueur de traverse automobile de 1,2 m
- Panneau de cône arrière d'avion à peau raidie de 1,0 x 1,2 m
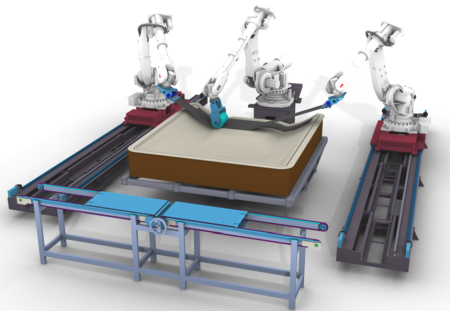
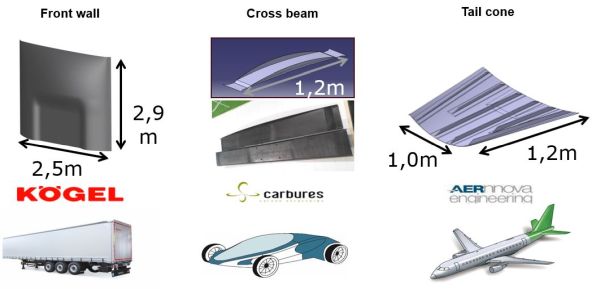
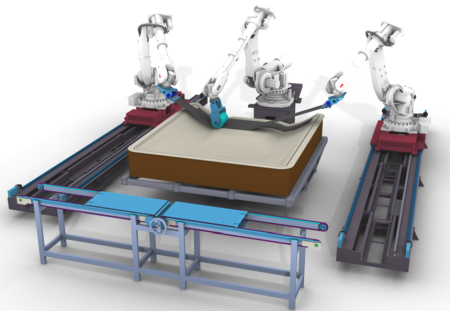
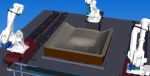
Animation
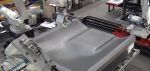
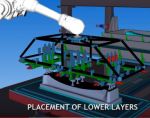
Fill a travaillé avec neuf partenaires de LOWFLIP pour développer une cellule de drapage automatisée pour la production de grandes structures de transport composites sans autoclave.
SOURCE :Remplissez la présentation CAMX 2017 de la Gesellschaft
« Nous avons utilisé un chauffage par résistance électrique pour chauffer le moule jusqu'à 120 °C », se souvient Wilhelm Rupertsberger, responsable du centre de compétence de Fill pour les composites et les plastiques. « Le matériau était toujours sous tension pendant le drapage automatisé », ajoute-t-il, « et nous avons réalisé un drapage sans plis directement sur le moule. Nous avons construit un processus humain, mais utilisant des robots pour améliorer la répétabilité. »
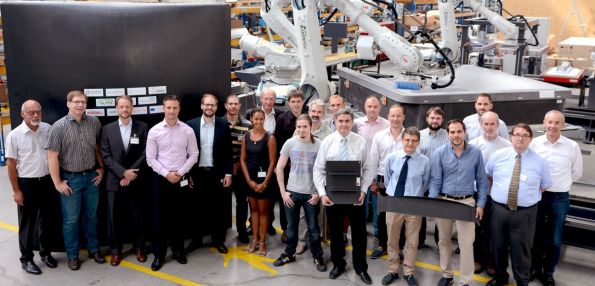
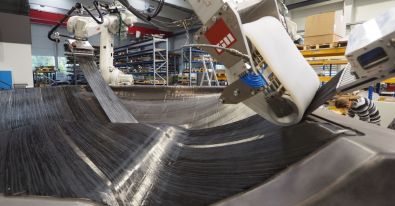
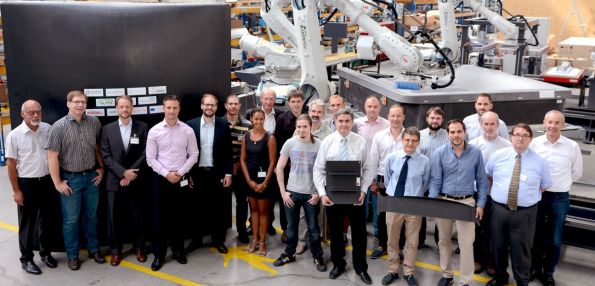
Vous pouvez voir la paroi de la remorque du camion à gauche, ainsi que les démonstrateurs de la poutre transversale de la voiture et du panneau arrière de l'avion sur la photo de l'équipe LOWFLIP ci-dessus .
SOURCE :Remplissez la présentation CAMX 2017 de la Gesellschaft
Système multicouche à multicouche
Le système Multi-Layup de Fill a été développé pour la production de pièces de carrosserie automobile en blanc (BIW) comme les parois arrière et les renforts de pare-chocs inférieurs à l'aide de rubans thermoplastiques. Il était prévu que ces pièces incluraient des nervures surmoulées et d'autres caractéristiques, ainsi le cycle de drapage de la préforme devrait correspondre au cycle de moulage par injection suivant.
Mon article de blog post-spectacle JEC 2017 comprenait une vidéo du système Multi-Layup, qui alimentait les bandes à partir de plusieurs rouleaux, plaçant toutes les bandes nécessaires par couche simultanément, au lieu d'une série, une à la fois. De cette façon, il a atteint un temps de cycle de 10 à 15 secondes par couche.
Fill a maintenant encore modifié le système et l'a renommé Multilayer. Il alimente, coupe et place jusqu'à 16 bandes dans des largeurs allant jusqu'à 50 mm (chacune de 0,01 à 0,04 mm d'épaisseur) sur une table rotative. Le lit de pose de ruban peut produire des pièces jusqu'à 1,6 × 1,6 m. Les bandes sont appliquées à une vitesse de ≈500 m 2 /h :toutes les 12 à 15 secondes, une couche de pièce pleine grandeur est appliquée pendant environ 1 minute de cycle par préforme finie. Les couches ne sont pas entièrement consolidées mais jointes par collage thermique. Au fur et à mesure que chaque bobine manque de bande, elle est automatiquement changée sans arrêter la machine.
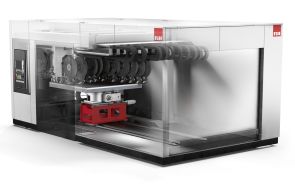
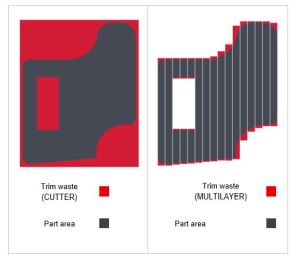
Remplissage multicouche automatisé Le système de préformage permet une réduction significative des déchets de coupe tout en plaçant les rubans uniquement là où cela est nécessaire et en les orientant selon les besoins pour obtenir des stratifiés sur mesure.
SOURCE :Remplissez la présentation CAMX 2017 de la Gesellschaft
Les préformes finies sont ensuite consolidées dans une presse. « Nous avons intégré Multilayer avec une presse de consolidation automatisée et une cellule de moulage par injection Engel qui fonctionnent ensemble pour offrir un temps de cycle d'une minute », explique Rupertsberger. Fill a reçu une commande pour le premier système multicouche de l'Université de technologie de Swinburne (Melbourne, Australie) plus tôt cette année et fera la démonstration de l'équipement en direct pour la première fois au JEC World 2019 (12-14 mars, Paris, France).
Presses RTM et injection adaptative
Fill a fourni plusieurs presses RTM, y compris des presses HP-RTM à SGL Composites.
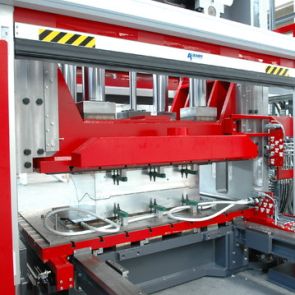
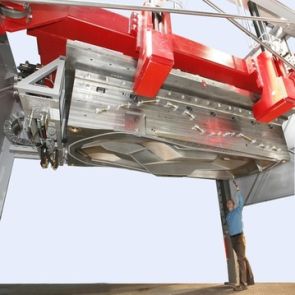
Le remplissage a fourni une grande variété de presses pour la production de composites, y compris les presses HP-RTM pour SGL Composites (à droite).
SOURCE : Remplir Gesellschaft
Avec Airbus Operations (Stade, Allemagne) et l'Institute of Plastics Processing (IKV) de l'Université RWTH d'Aix-la-Chapelle, Fill a développé une unité d'injection adaptative innovante pour RTM initialement pour les structures aérocomposites. Avant que les pièces fabriquées avec RTM puissent voler sur un avion, elles doivent passer un processus d'assurance qualité (AQ) long et coûteux. Pour raccourcir ce processus, les outils de formage RTM ont été équipés de capteurs, permettant de déployer l'AQ en ligne pendant la production. IKV, Airbus et Fill ont désormais intégré ces capteurs dans le système d'injection, éliminant ainsi le besoin d'équiper chaque outil de formage. Utilisant des cartouches jetables de la même manière que les systèmes d'injection à piston sont utilisés dans les systèmes RTM typiques, l'unité d'injection adaptative est équipée d'un boîtier de capteur permettant de mesurer et d'enregistrer les données suivantes in situ :
- Température
- Pression
- Viscosité de la résine
- Densité de réticulation du système de résine
- Température de transition vitreuse (Tg).
Tout en garantissant la qualité des pièces moulées, ces données peuvent également être utilisées pour gérer et contrôler le processus d'injection. Ce système d'injection adaptatif Industrie 4.0 est développé pour les aérocomposites, et également étendu à d'autres industries telles que l'automobile.
Formation du drapé à chaud
Dans les récents articles de tournée que Sara Black et moi avons écrits sur les composites haute performance en Israël, nous avons noté que la plupart des entreprises utilisaient le formage par drapage à chaud. En fait, à Elbit Cyclone, notre guide touristique Jonathan Hulaty a déclaré :« Je ne sais pas comment vous faites ce type de production de pièces préimprégnées à haut débit sans formage à chaud », se référant aux poutres et aux chandeliers pour les assemblages Boeing 787. Les formeurs de draps à chaud (HDF) sont également considérés comme indispensables par FBM et Israel Aerospace Industries. Fill fournit des systèmes HDF depuis des années, dont plusieurs unités en production chez FACC. Ce sont essentiellement des systèmes de formage sous vide, équipés d'éléments chauffants infrarouges ou d'autres types et d'une membrane en caoutchouc de silicone réutilisable pour chauffer et comprimer - réduire en vrac - les couches de préimprégné sur leurs outils avant le durcissement. HDF devient un élément clé de la chaîne de production complète d'aérocomposites illustrée ci-dessous.
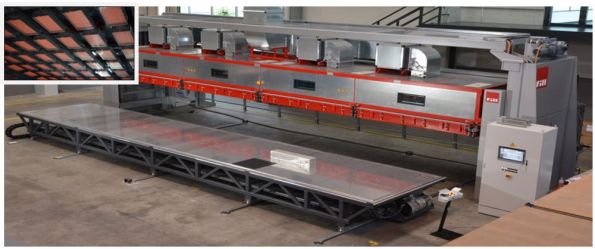
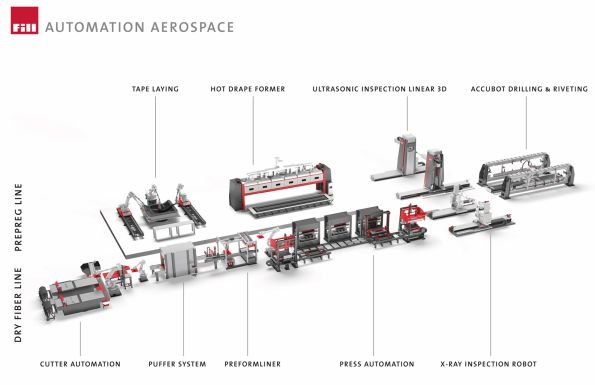
Formation à chaud est devenu un catalyseur important pour la production en grand volume d'aérostructures composites préimprégnées et est automatisé par Fill dans le cadre de ses solutions de chaîne de processus complète. SOURCE : Remplir Gesellschaft
Cellules de production de l'industrie 4.0 pour CFRP
Fin 2013, Fill a commencé à développer un système de production pour la fabrication de longerons CFRP, utilisés pour rigidifier les coques des volets d'atterrissage de l'Airbus A320, en collaboration avec le fournisseur Tier. Lors de l'installation, ce système a réussi à réduire le nombre de stations, améliorant ainsi le flux de production et améliorant également la convivialité. Il comprend :
- Stockage automatique des outils de formage
- Gare HDF
- Station de levage presse-tournage où les stratifiés sont transformés en limons.
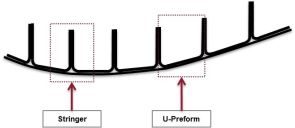
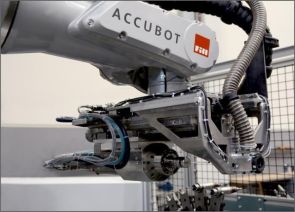
Fill s'est développé trois générations de cellules de production automatisées (à droite) pour les longerons de volets de train d'atterrissage en préimprégné (à gauche).
SOURCE : Remplir Gesellschaft
Un système de deuxième génération pour produire le même type de pièces a été mis en service en 2017. Là où le premier système se concentrait sur l'optimisation des postes individuels, ce dernier système visait à minimiser les tâches manuelles et à intégrer toute la logistique des outils. Trois domaines de développement clés permettent à ce système de deuxième génération d'atteindre une reproductibilité élevée et une productivité considérablement accrue :
- La récupération et le stockage manuels des outils de formage sont remplacés par un retour d'outils entièrement automatique, ce qui raccourcit les temps de processus logistiques. Cela a également réduit l'espace requis de plus de 50 %.
- La poursuite de l'automatisation des sous-processus a réduit les temps improductifs.
- Industry 4.0 numérisation de tous les enregistrements et rapports. Le logiciel développé par Fill permet de visualiser le processus à tout moment et d'enregistrer l'historique de chaque composant tout au long de la chaîne de processus. Des capteurs détectent la disponibilité des outils et des matériaux pour éviter les goulots d'étranglement et améliorer le réapprovisionnement.
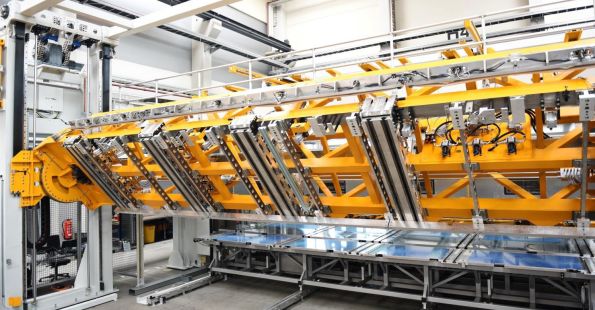
Appuyez-tournez -station de levage utilisée dans les cellules de production automatisées des longerons de volets de trains d'atterrissage A320 et A350.
SOURCE : Remplir Gesellschaft
Fill travaille désormais sur un système de production de troisième génération de coques de volets d'atterrissage destinées à l'Airbus A350-900. Il comprend également un stockage d'outils, une station de formation de membranes (HDF), une station de levage de presse-tour et un retour automatique d'outils, mais a été amélioré avec un système de transport pour les outils d'autoclave, remplaçant les anciens camions de transport manuel et tracteurs électriques par des véhicules à guidage automatique (AGV ). Fill travaille déjà sur de futurs systèmes, cherchant comment améliorer encore la collaboration homme-machine.
Accubot
Avant même que l'industrie des composites ne commence à verbaliser son besoin futur envisagé d'une cellule de travail multi-opérations, Fill développait déjà les premiers prototypes, ce qu'elle appelle Accubot. L'idée était de développer un robot précis utilisant un laser tracker pour la compensation spatiale ainsi que des systèmes de mesure externes directs. Ce robot serait capable d'alterner les fonctions avec les effecteurs finaux, devenant non seulement une cellule de contrôle non destructif (CND) mais également une cellule d'usinage. Les applications Accubot incluent :
- Forage
- Rivetage
- NDT – Échographie avec un gicleur
- NDT – Rayon X
- NDT – Tomodensitométrie
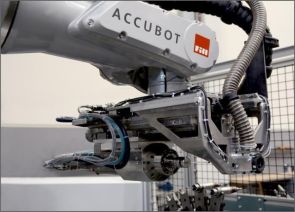
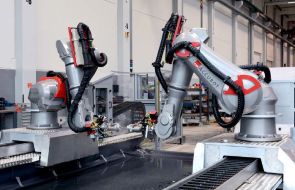
Accubot pour le forage (à gauche) et le CND à l'aide d'un balayage à ultrasons à grande vitesse (à droite).
SOURCE :Remplissez Gesellschaft.
FlexHyJoin
Fill est membre du projet Flexible Production Cell for Hybrid Joining (FlexHyJoin) financé par l'UE. Ce programme de 3 ans vise à développer un processus pilote entièrement automatisé pour l'assemblage de supports/raccords métalliques avec des composites thermoplastiques dans des applications automobiles en combinant les technologies d'assemblage laser et d'assemblage par induction. Fill a conçu et construit la cellule automatisée, y compris le logiciel et l'intégration des différentes technologies.
La recherche et le développement de Fill se poursuivent. Il comprend que des systèmes de production innovants et intelligents sont nécessaires pour rendre la fabrication de pièces composites plus économique et adaptée à des volumes plus élevés. Et il s'engage à développer ces systèmes en fonction de l'échelle et des besoins spécifiques de ses clients.
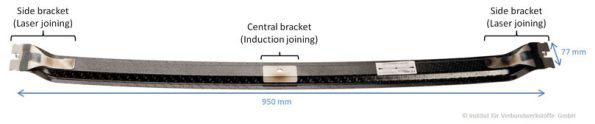
SOURCE :FlexHyJoin.
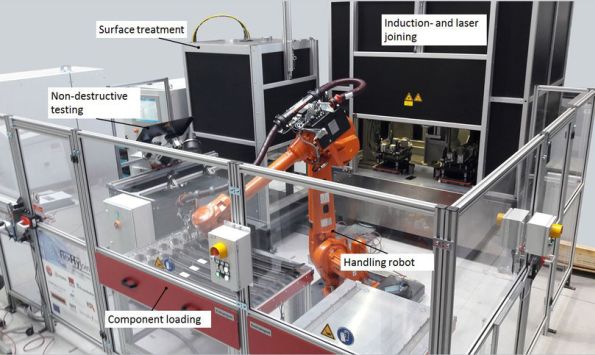
Résine
- Remplir le barrage
- Directives du préprocesseur C#
- Python strftime()
- Python strptime()
- Introduction aux harmoniques :Partie 1
- Durabilité dans le secteur manufacturier - Partie 3
- Le virage est facultatif
- Inspection en ligne et automatisée des données de tomodensitométrie des connecteurs électroniques
- Cylindricité en GD&T