Futur fabrication composite - AFP et fabrication additive
« Surimpression » sur des surfaces et des supports préfabriqués en PRFC (en haut à gauche) , hybridant des procédés tels que l'impression 3D et l'enroulement filamentaire (en haut à droite) , impression de noyaux en 3D sur des stratifiés AFP et de peaux AFP sur des noyaux imprimés en 3D (en bas à droite) et impression 3D CEAD AM Flexbot à 45 degrés (en bas à gauche) . Crédit photo :TU Munich, Chaire des composites de carbone
En septembre, j'ai assisté au symposium virtuel "FUTURE COMPOSITE MANUFACTURING – AFP &AM", faisant référence au placement automatisé de fibres (AFP) et à la fabrication additive (AM). Ce symposium a été organisé par la Chaire des Composites Carbone (LCC) à Université technique de Munich (TUM, Munich, Allemagne). L'événement comprenait également le partenaire de recherche de TUM Australian National University (ANU, Canberra). Le symposium a passé en revue les capacités de R&D sur les composites à la fois à la TUM et à l'ANU, ainsi que les projets achevés et en cours avec des partenaires industriels tels que l'AFPT, Airbus, BMW, CEAD, DLR, Fraunhofer, GKN Aerospace, INOMETA, SGL Carbon et Victrex.
La collaboration de TUM avec l'ANU a débuté en 2010 avec le projet AutoCRC visant à développer des réservoirs de stockage de gaz naturel comprimé (GNC) à partir de composites thermoplastiques. La R&D conjointe s'est poursuivie depuis lors, y compris la formation du centre de l'Australian Research Council pour la fabrication automatisée de composites avancés (AMAC) et trois domaines d'intervention majeurs à l'ANU :
- Amélioration des matériaux
- Matériaux et revêtements à l'échelle nanométrique pour l'amélioration des propriétés fonctionnelles des composites de carbone
- Rubans préimprégnés améliorés au graphène pour la conductivité thermique et électrique
- Laser-AFP
- Projet avec Ford pour développer un acier renforcé composite
- Contrôle numérique du biais de chauffage, par ex. stabilité du processus pour les coins/géométries 3D
- Diagnostic avancé avec la tomodensitométrie à rayons X
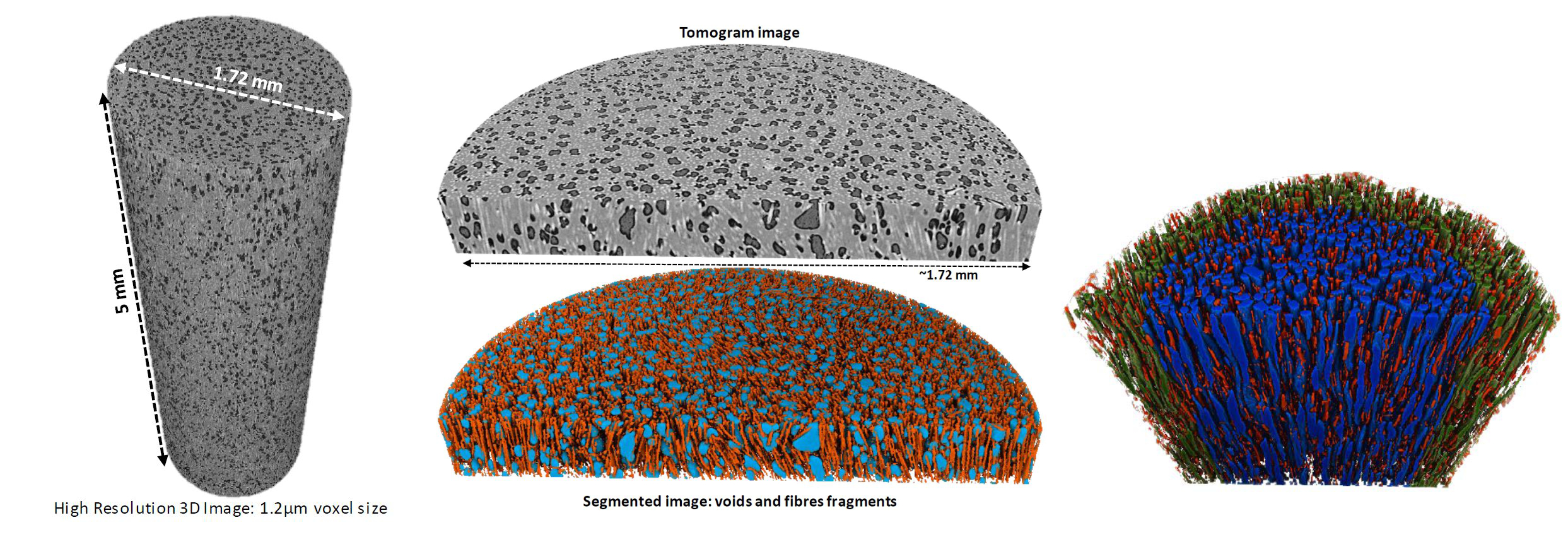
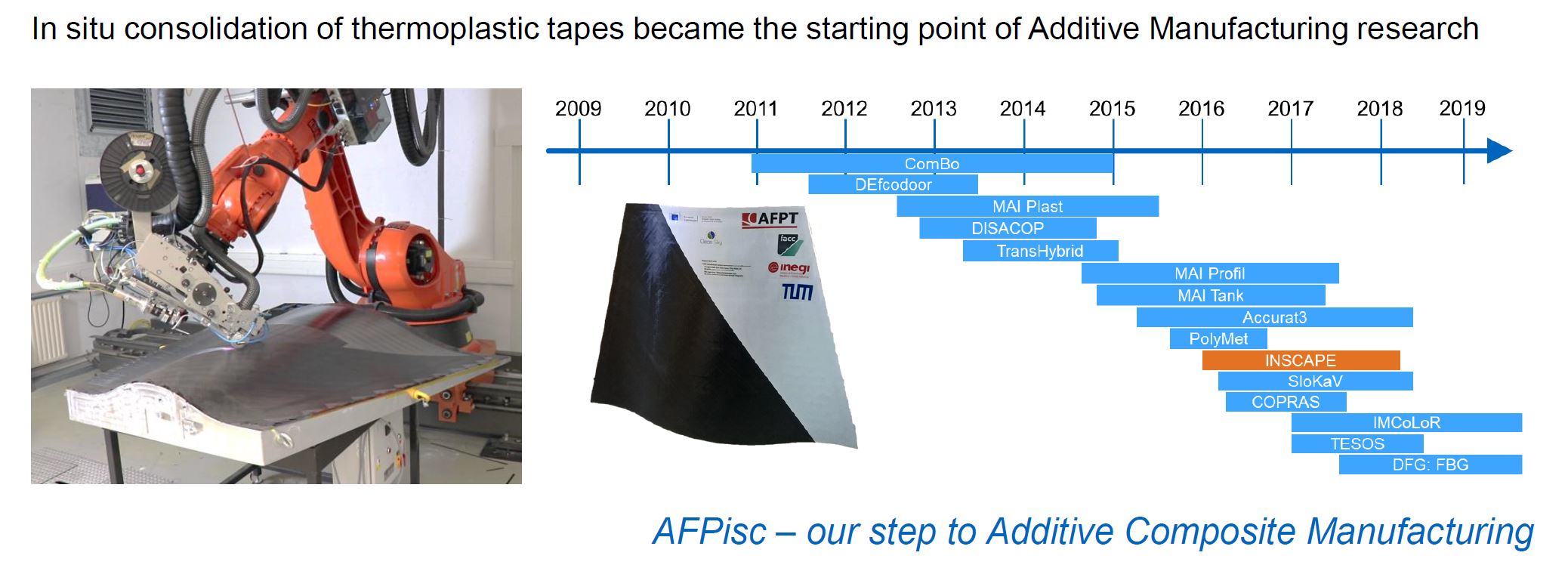
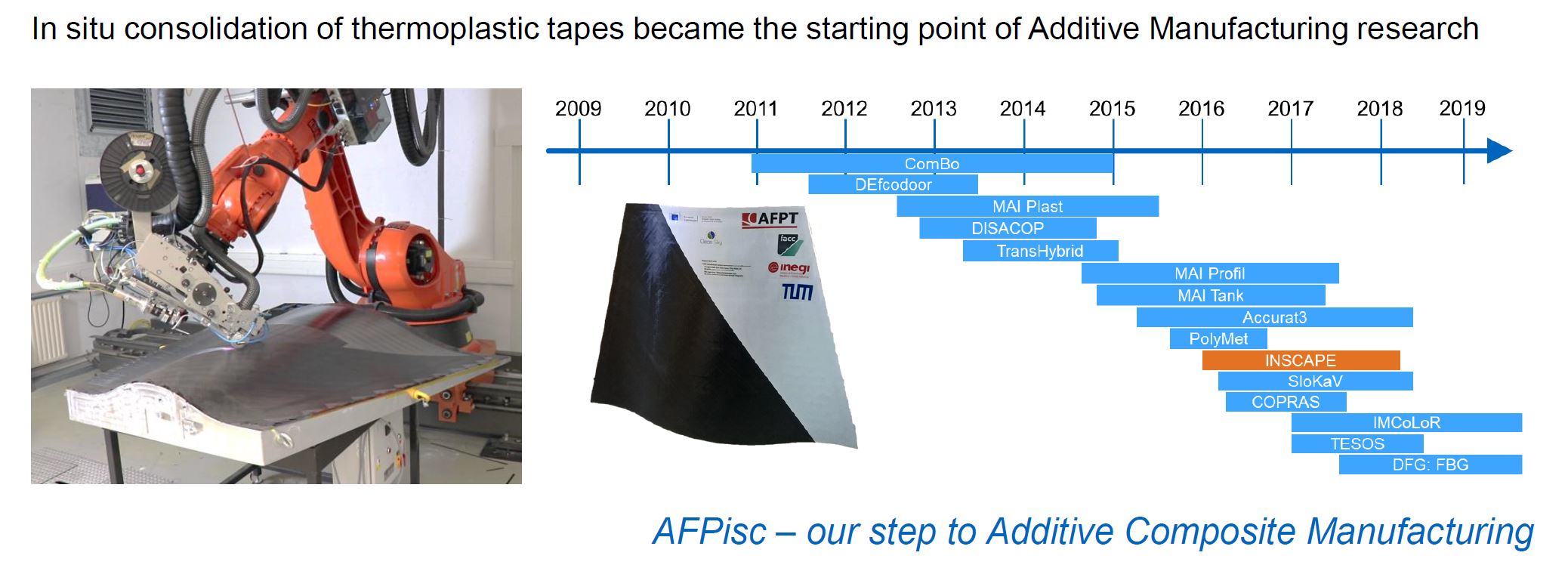
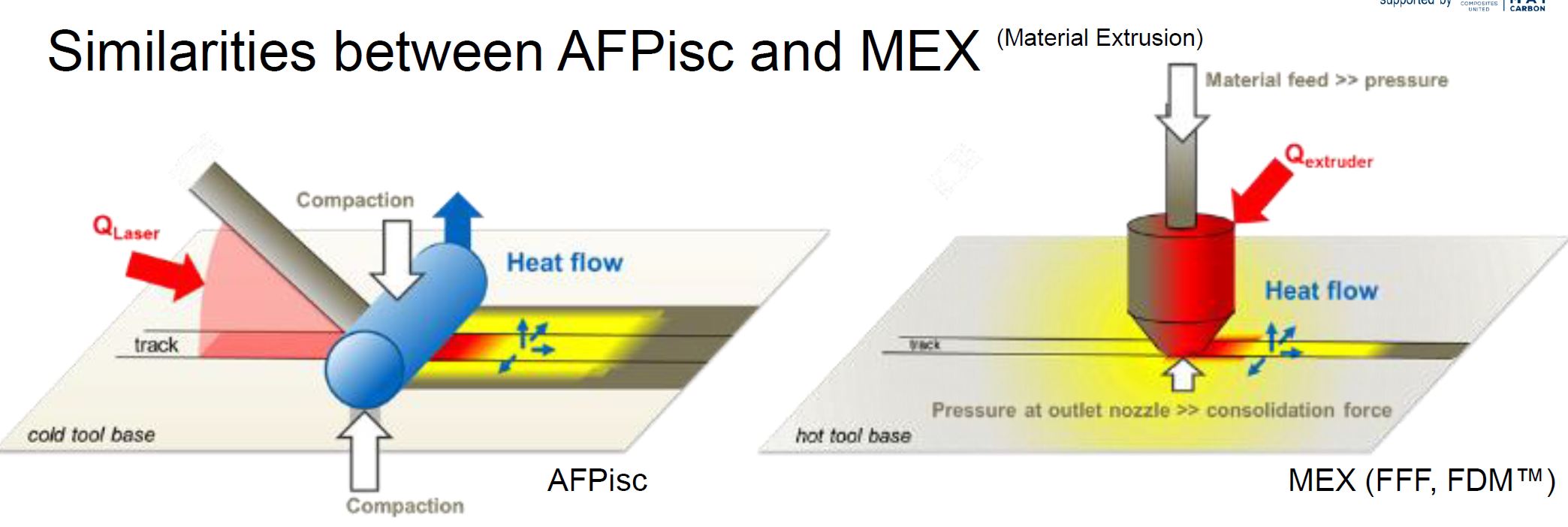
Il a discuté des similitudes entre l'extrusion de matériaux (MEX), le processus le plus couramment utilisé pour l'impression 3D de composites renforcés de fibres, et AFP ISC :
- Traitement thermique local et récurrent
- Conception basée sur des couches et propriétés orthotropes des matériaux
- Placement du matériau le long des chemins programmés 2D et 3D et activation thermique entre les couches.
Drechsler a ensuite discuté des besoins futurs en composites et de la manière dont la combinaison de l'AFP et du MEX pourrait fournir des solutions, y compris à court terme dans l'outillage et à plus long terme dans les structures légères hautes performances qui sont à la fois rentables et écologiquement durables.
En décrivant les capacités de LCC, Drechsler a donné un aperçu de son équipement MEX ainsi que des projets de R&D passés et en cours dans la fabrication additive.
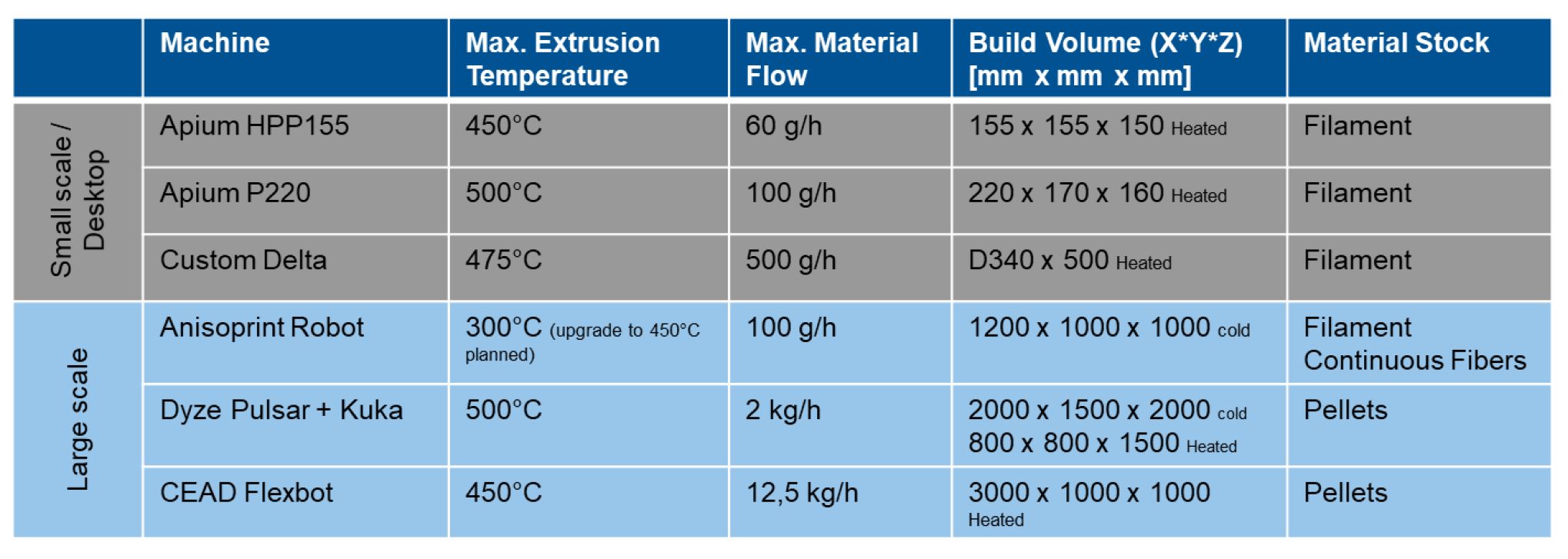
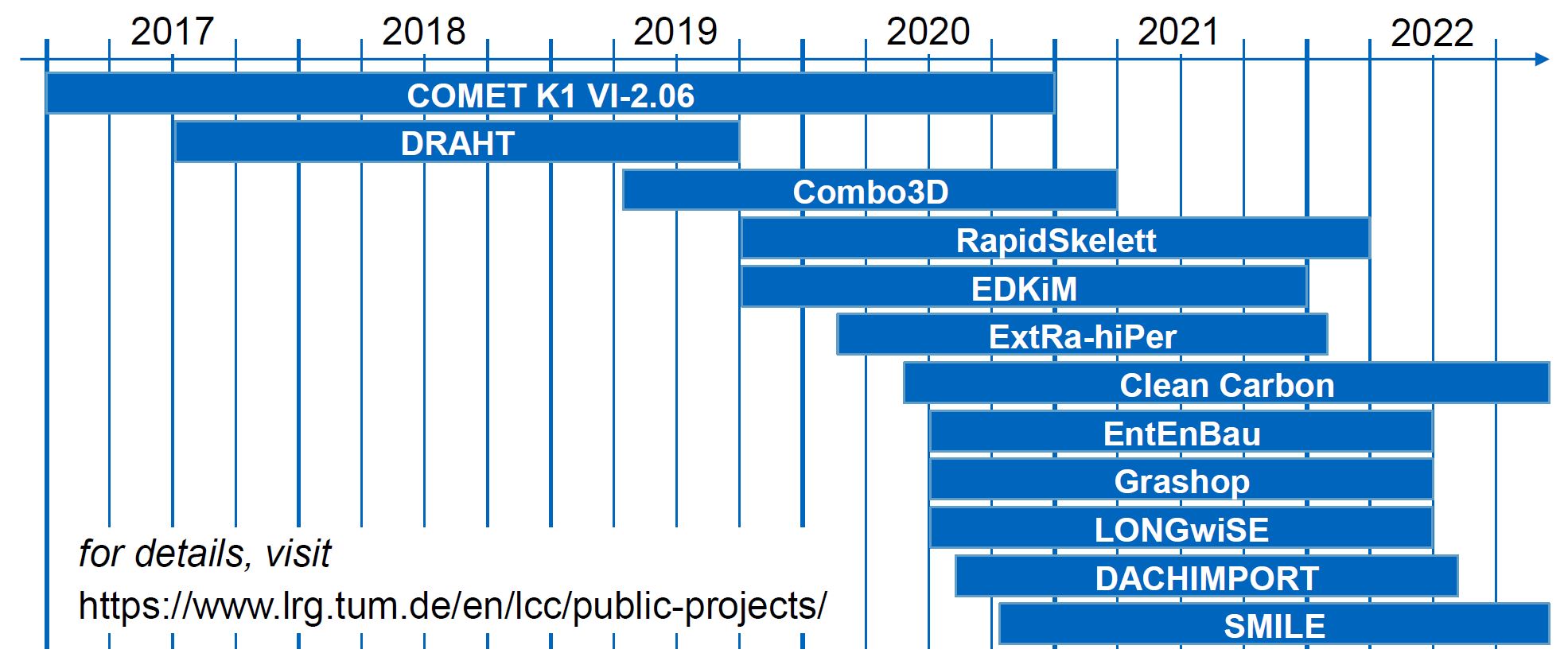
Concernant ISC AFP, les développements récents et en cours au LCC incluent :
- Une tête d'enroulement de navire pour soutenir l'industrialisation de structures telles que les réservoirs sous pression, y compris les réservoirs de stockage d'hydrogène
- Contrôle en boucle fermée du chauffage du faisceau laser
- Utilisation d'un rouleau refroidi par fluide pour la consolidation
- Caractérisation des bandes pour optimiser l'ISC.
Les développements de LCC en matière de MEX et d'impression 3D ont été approfondis lors de plusieurs présentations au cours des deux jours suivants.
CEAD et impression 3D à grande échelle
La présentation suivante après le discours de Drechsler a été donnée par Maarten Logtenberg, directeur exécutif de CEAD (Delft, Pays-Bas). Fondée en 2014, CEAD a vendu des systèmes commerciaux basés sur sa technologie de fabrication additive continue de fibres (CFAM), à la fois sous forme de cellule fermée à portique (CFAM Prime) et de système basé sur robot (AM Flexbot). LCC est propriétaire de ce dernier (voir tableau ci-dessus) et travaille avec LCC sur plusieurs projets (voir CW articles sur CEAD et son travail avec TUM LCC).
Les points saillants de la présentation de Logtenberg comprenaient le développement par CEAD de solutions hybrides qui intègrent le fraisage CNC, de grands lits d'impression chauffants (1,2 m x 3 m et 1,2 m x 2 m) et des lits d'impression rotatifs chauffants. Il vise également des cellules encore plus grandes et une impression à 45 degrés, ainsi que l'impression d'outils renforcés de fibres pour la production en série d'autoclaves de pièces d'avions commerciaux.
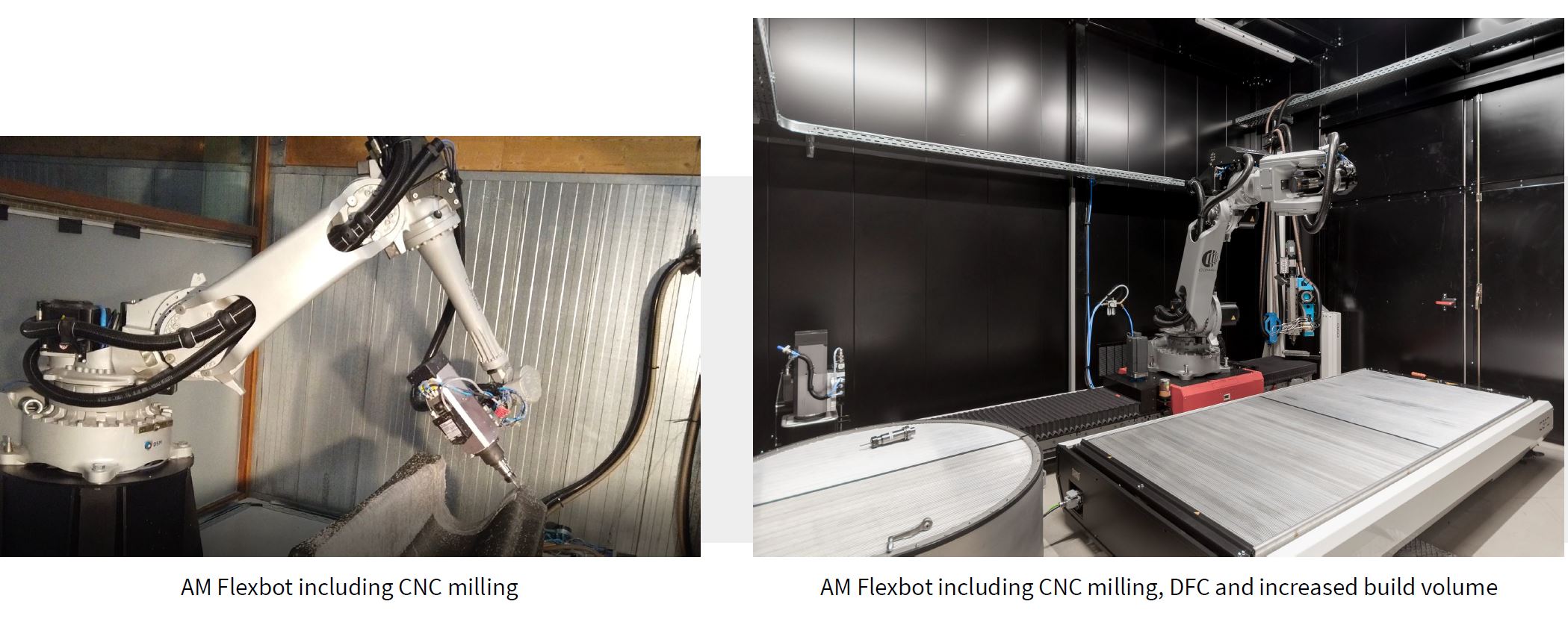
Logtenberg a noté que l'un des principaux défis pour les outils d'autoclave imprimés en 3D est la dilatation thermique et que les outils beaucoup plus grands que 4 mètres ont tendance à trop se dilater (voir « Outillage additif hybride grand format »), ce qui rend difficile une compensation suffisante via la conception de l'outil. . La solution qu'il propose est de remplacer le renfort en fibres coupées utilisé majoritairement à ce jour par des fibres continues déposées par des systèmes comme AM Flexbot.
Cette voie à suivre a été appuyée par la présentation « Introduction d'intensificateurs de chenilles imprimés en 3D pour la production de volets composites » donnée par Thomas Herkner chez GKN Aerospace à Munich, en Allemagne. Ces renforçateurs CFRP imprimés en 3D sont utilisés comme outillage dans la production de volets d'atterrissage CFRP pour les Airbus A350 et A330. Bien que ce programme réussi chez GKN ait utilisé un renforcement en fibres coupées, Herkner a montré une feuille de route pour un développement ultérieur qui comprenait l'utilisation de fibres continues dans les outils imprimés en 3D ainsi que, éventuellement, dans les pièces d'avion elles-mêmes.
Cette voie à suivre a été bien expliquée par Patrick Consul, chercheur au LCC, dans un récent blog CW :
Consul a également présenté au symposium TUM, examinant la conception de processus pour la FA à grande échelle basée sur l'extrusion. Il a expliqué comment les transitions de verre et de phase illustrées ci-dessous représentent le plus grand changement dans les propriétés des matériaux des granulés renforcés de fibres hachées qui sont fondus et extrudés dans des systèmes d'impression 3D comme CFAM et AM Flexbot.
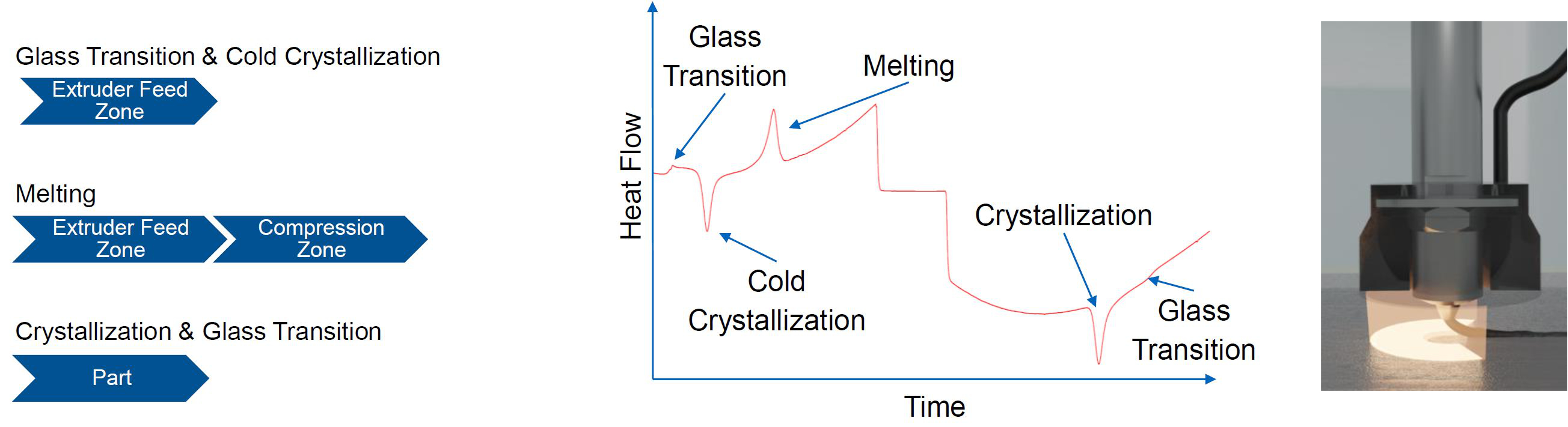
Le travail de Consul a analysé comment les paramètres MEX tels que la viscosité du polymère et la température et le couple d'extrusion affectent la cristallinité dans le composite imprimé, qui à son tour influence la capacité à souder les couches ensemble pendant l'impression 3D. En plus de cette liaison couche à couche, Consul a également exploré l'alignement des fibres et les contraintes résiduelles dans les couches imprimées. Une solution présentée consistait à utiliser un laser pour préchauffer le substrat pendant l'impression - largement utilisé aujourd'hui dans l'ISC AFP des composites thermoplastiques - transférant ainsi les connaissances de l'AFP à la FA. Les premières expériences ont utilisé un anneau de diodes laser contrôlables.
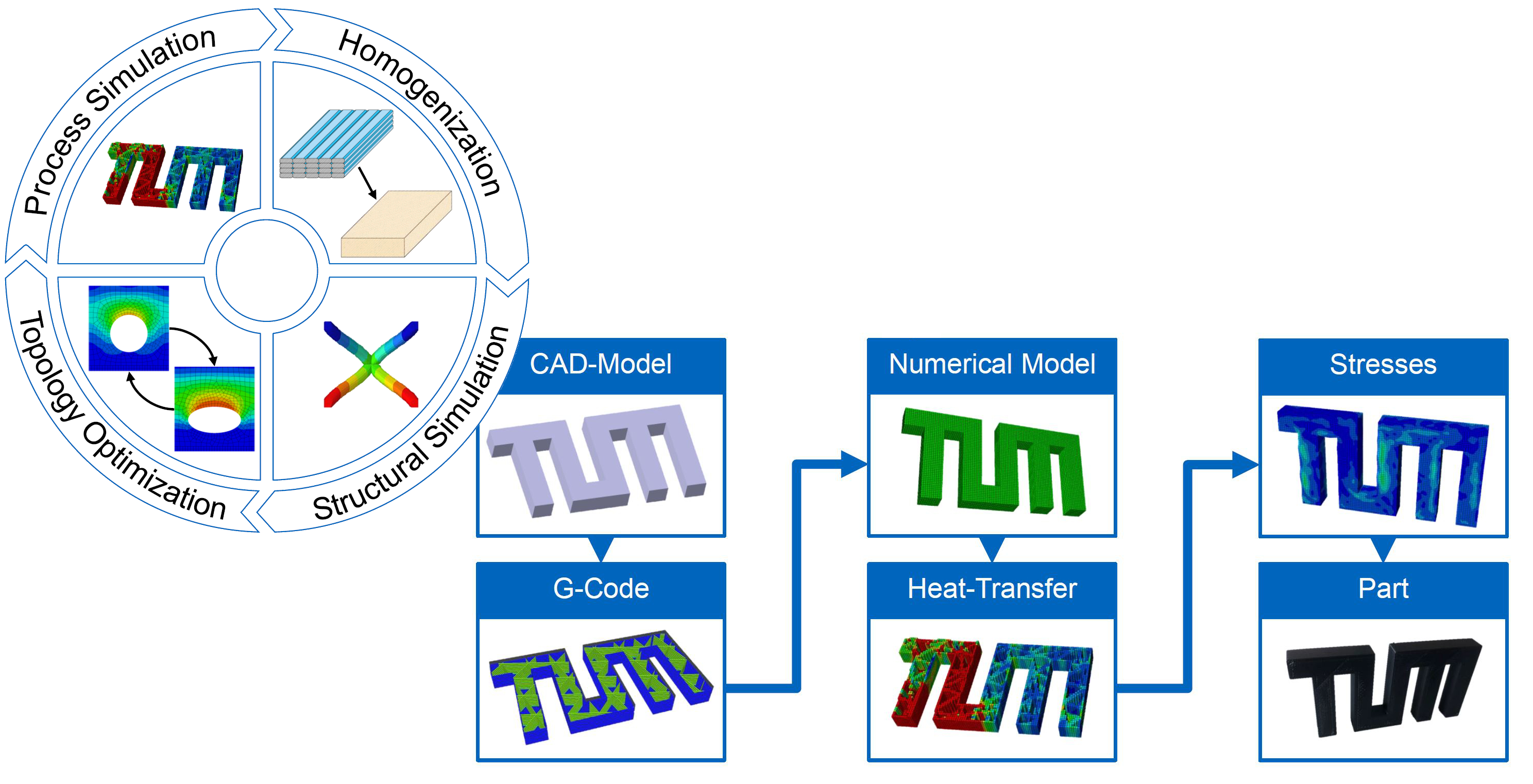
Le collègue du consul, Matthias Feuchtgruber, a présenté plus tard dans la journée, passant de la conception de processus et de la caractérisation des matériaux au développement d'une chaîne de processus virtuelle pour les composites AM.
Alexander Matschinski a ensuite présenté l'intégration des fibres sans fin dans les composites AM, présentant le graphique ci-dessous, qui est devenu la base du graphique modifié que j'ai utilisé dans CW Article du supplément Next-Gen sur l'impression 3D en fibre continue. Matschinski a également discuté des travaux de conception de structures FA à fibre continue et du développement futur de la « surimpression » sur des pièces et des surfaces préfabriquées en PRFC.
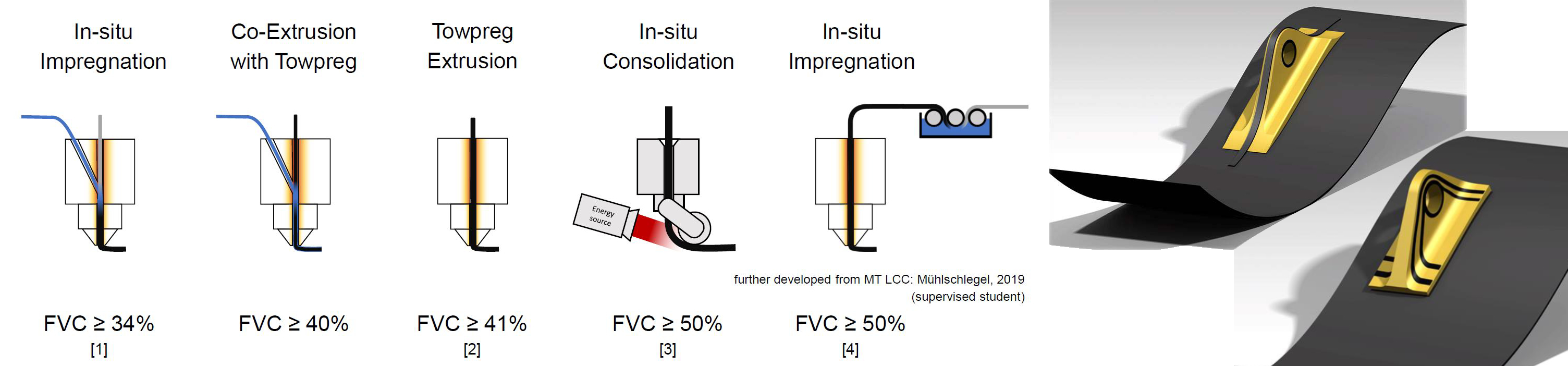
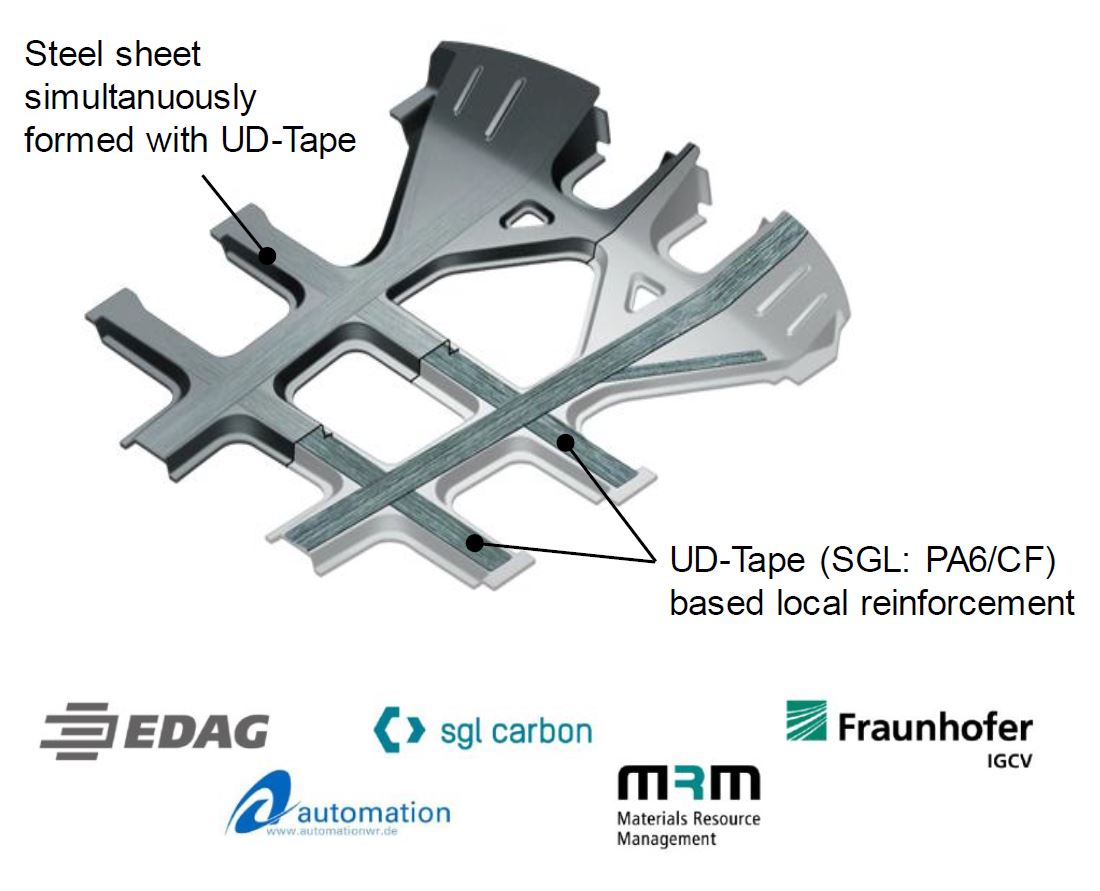
D'autres applications intéressantes des fibres continues ont été présentées par le Dr.Christopher Ebel chez SGL Carbon, notamment pour renforcer les structures de soubassement en acier pour l'automobile, en réduisant le nombre de pièces de 37 à 9 et en réduisant le poids de 41 %. Un autre concept était le bobinage 3D à l'aide de towpreg imprégné de résine époxy à durcissement instantané pour des structures à charge optimisée. Cette approche numérique commence par la simplification des charges complexes et l'optimisation de la topologie, suivies de la fabrication automatisée. Les pièces résultantes peuvent exploiter le verrouillage de forme des inserts dans les structures, permettant l'introduction de la charge sans perte de rigidité. Les derniers procédés d'impression 3D métal peuvent être utilisés pour de tels inserts, optimisant davantage l'efficacité de la gestion des charges et la réduction des coûts.
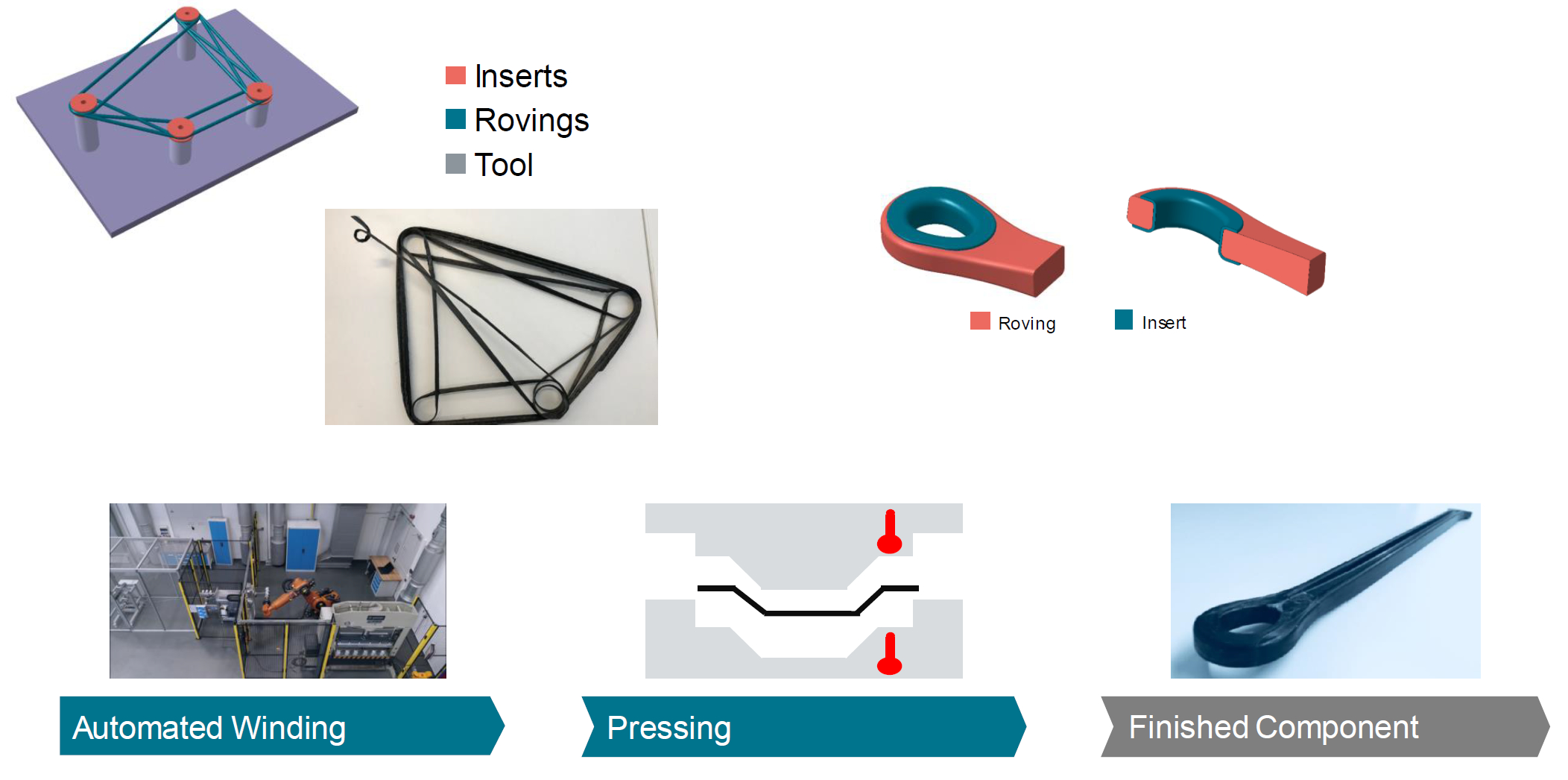
Sebastian Nowotny du DLR a discuté de la combinaison de l'impression 3D avec ISC AFP de composites thermoplastiques, y compris l'impression 3D sur des stratifiés AFP et AFP sur des structures imprimées en 3D partiellement ouvertes. Les premières expériences incluent l'impression 3D d'un noyau sur une peau de CFRP préfabriquée, puis l'AFP/le ruban adhésif posé sur le noyau imprimé en 3D. Des spécimens ont été créés puis soumis à un test de traction et de cisaillement pour évaluer la liaison peau-âme.
Titre du diaporama
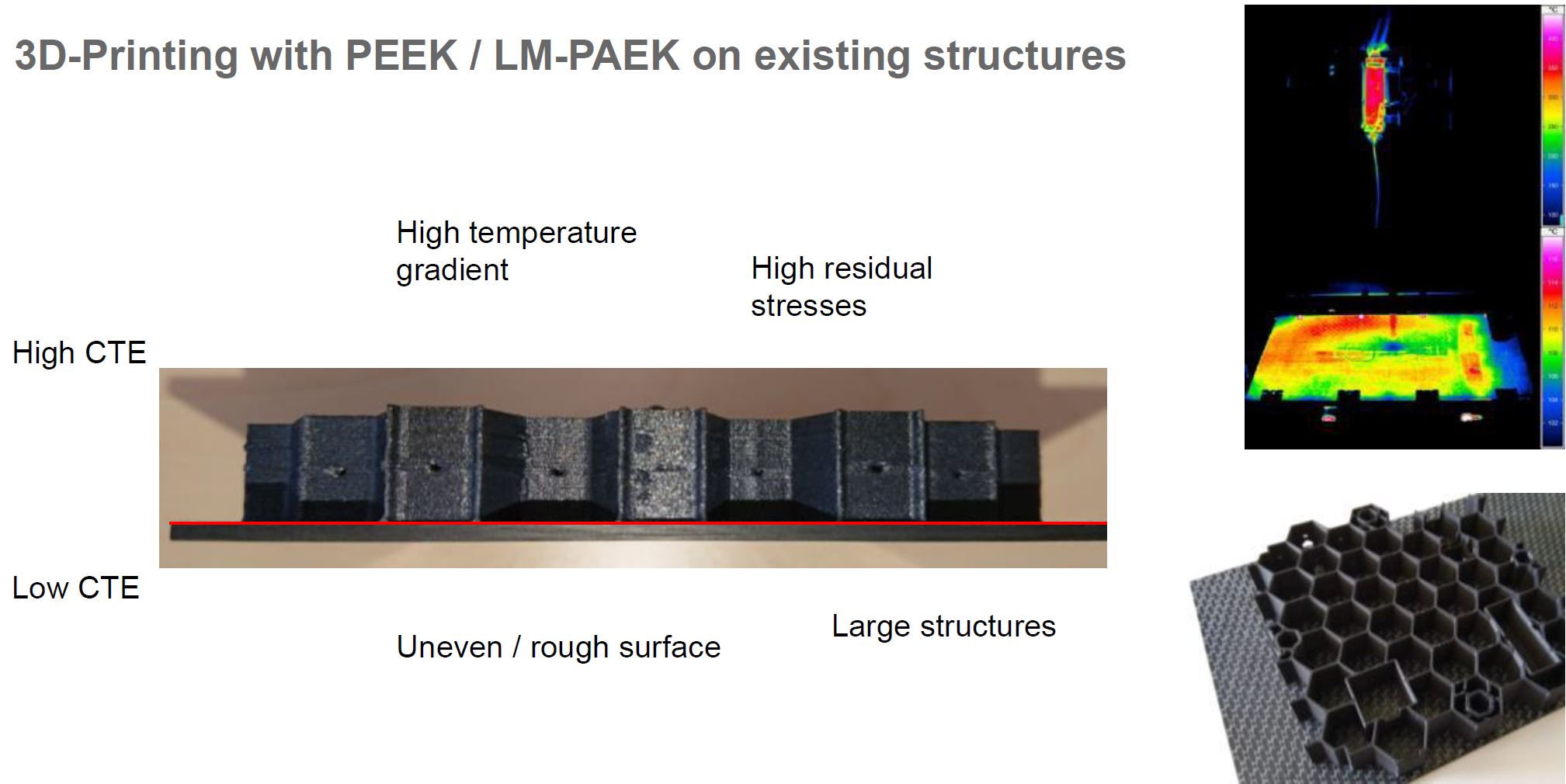
Crédit photo :Sebastian Nowotny, DLR, Symposium TUM septembre 2020
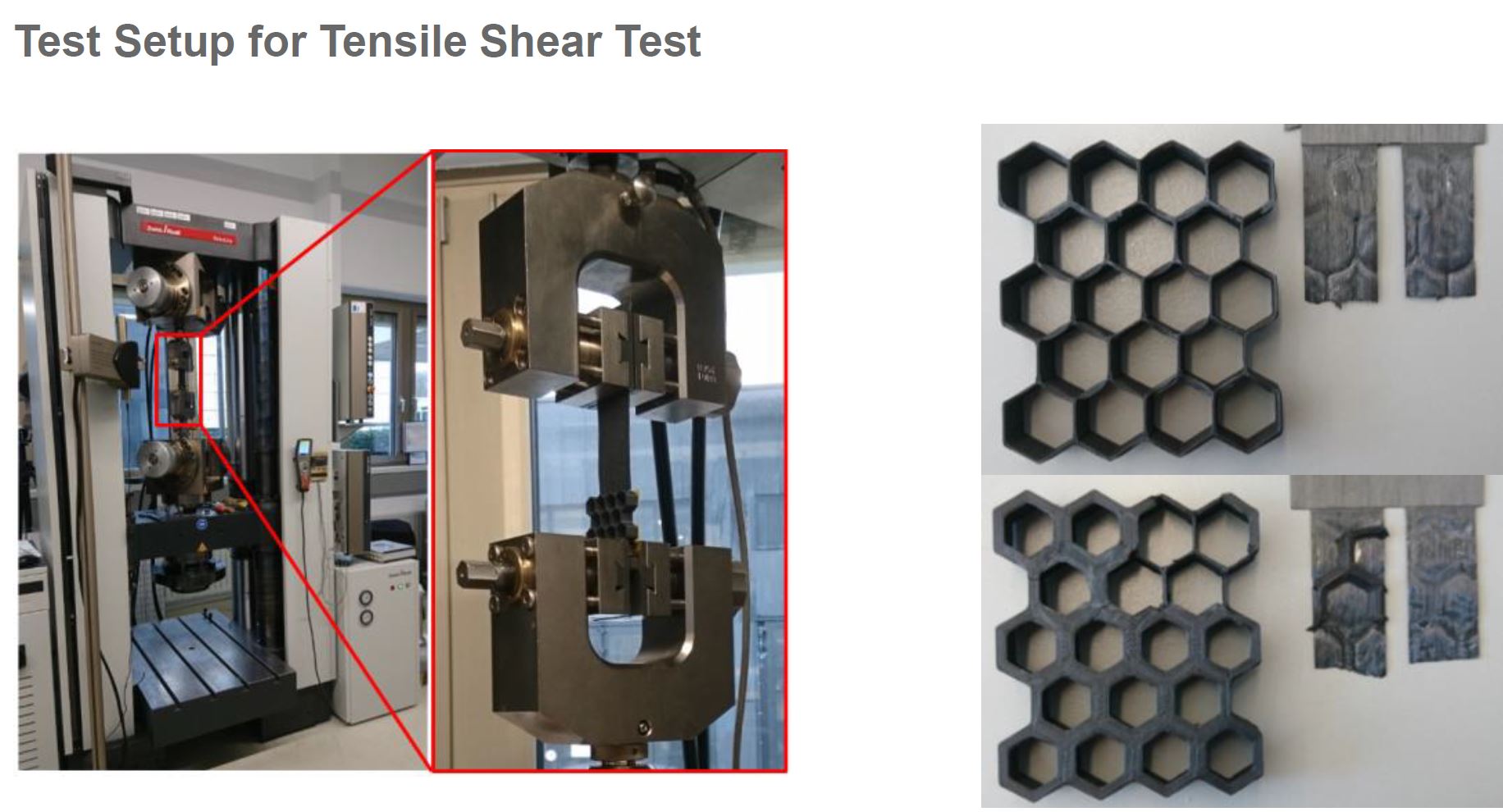
Essais de traction et de cisaillement de coupons fabriqués à l'aide de l'impression 3D hybride et de l'AFP. Crédit photo :Sebastian Nowotny, DLR, Symposium TUM septembre 2020
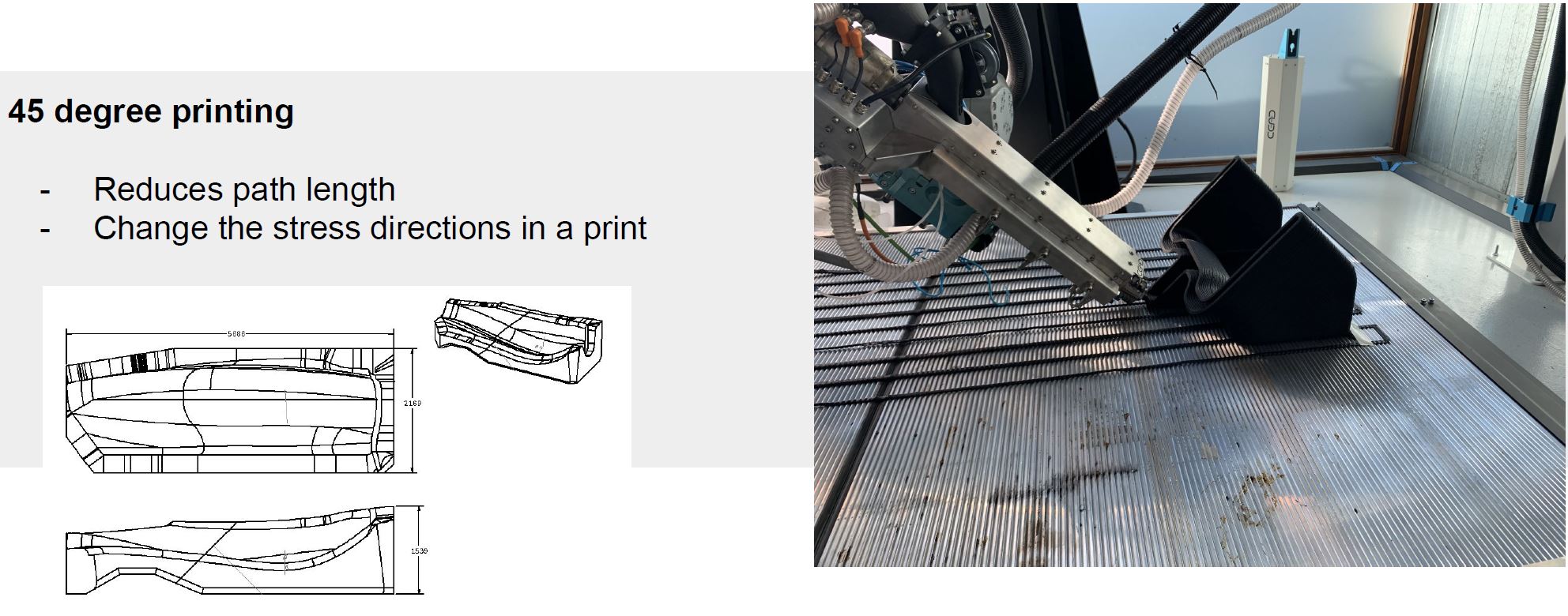
Crédit photo :CEAD, Symposium TUM septembre 2020
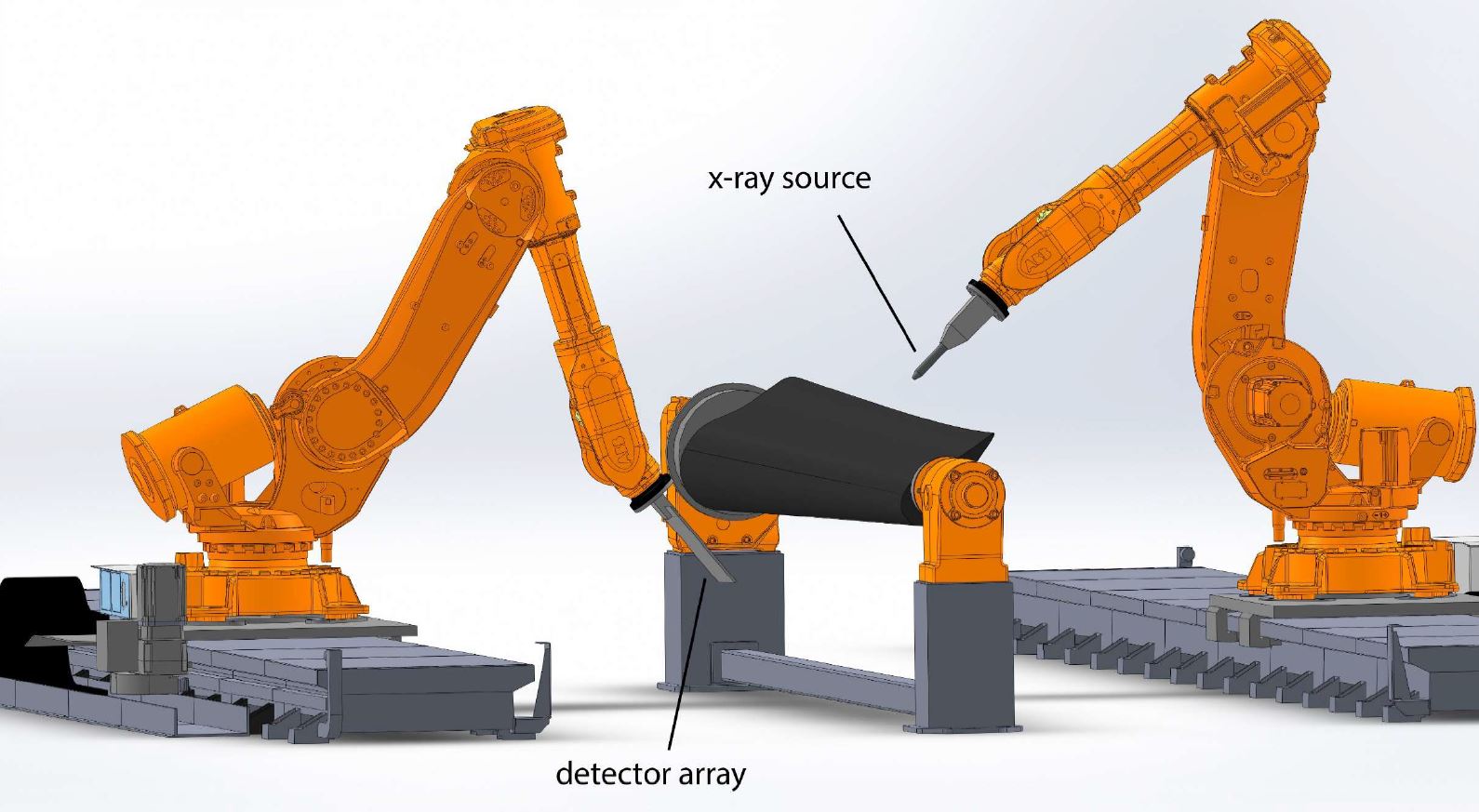
Application future de la tomodensitométrie lors de la production de composites. Crédit photo :Université nationale australienne, Symposium TUM, septembre 2020
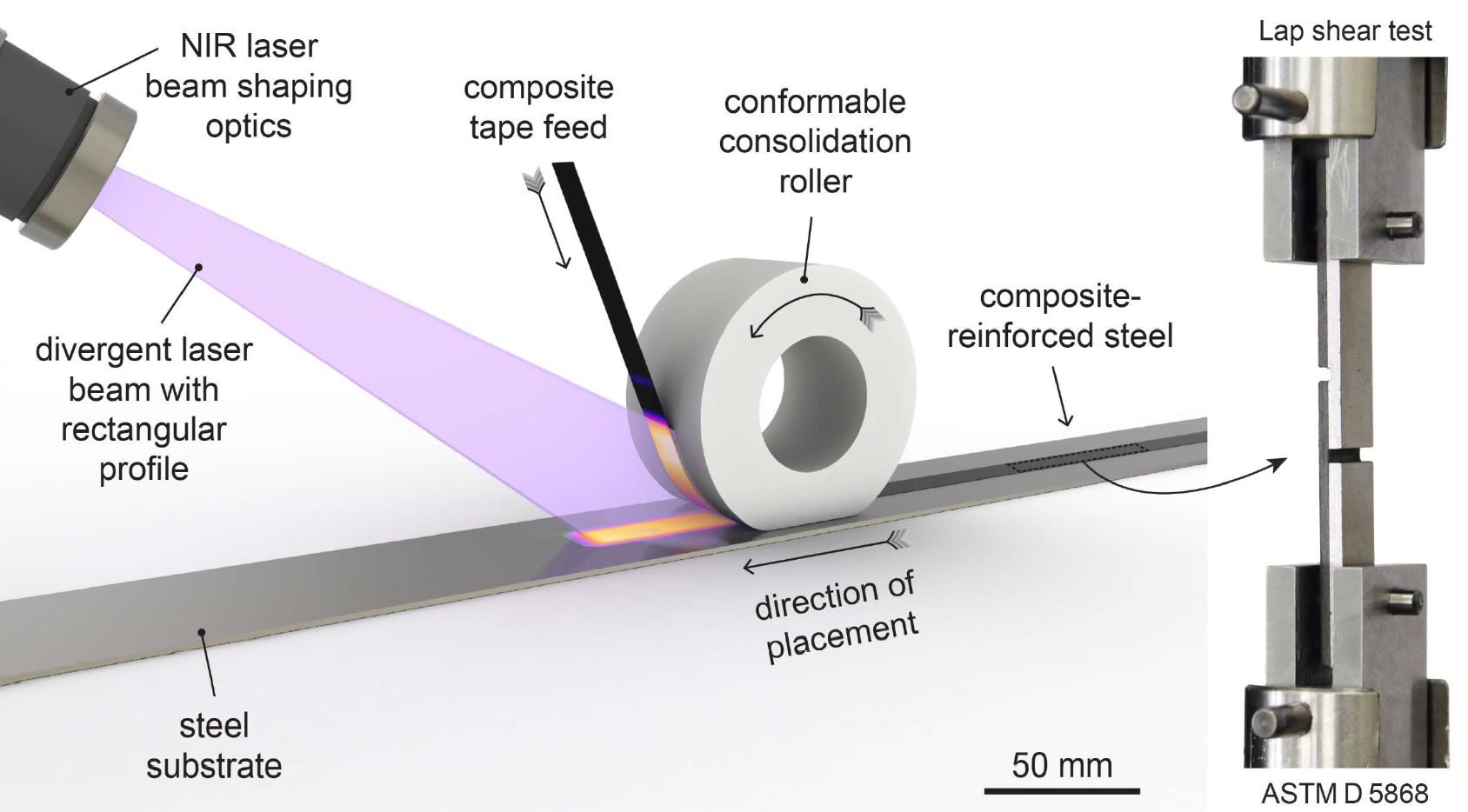
Travail de développement utilisant le laser AFP pour créer des structures hybrides CFRP-métal. Crédit photo :Université nationale australienne, Symposium TUM, septembre 2020
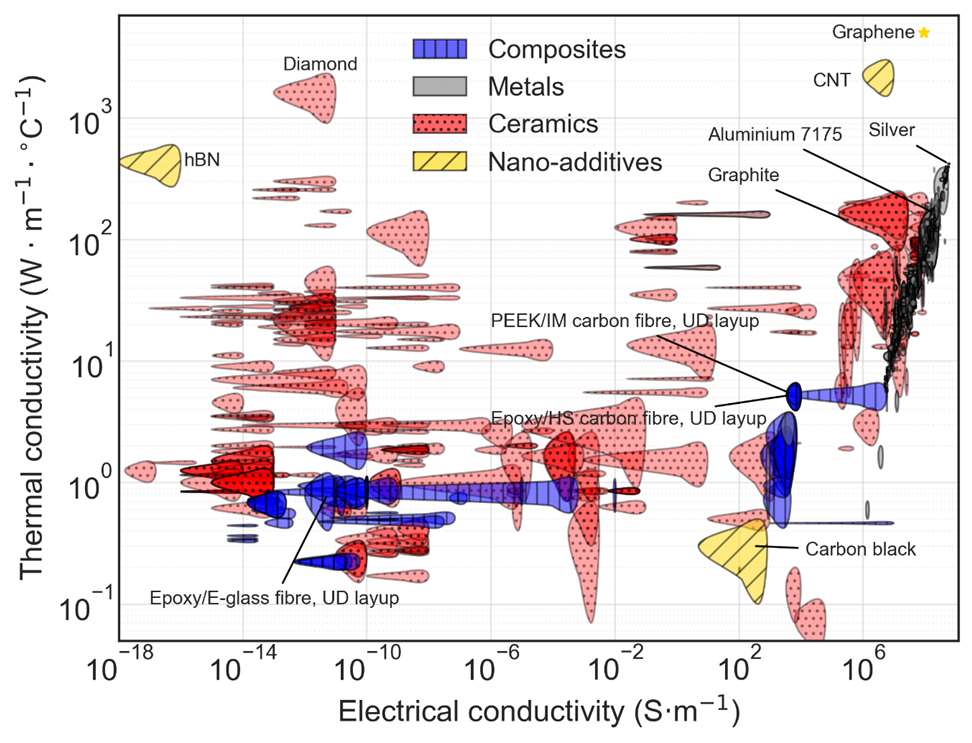
Rubans préimprégnés au graphène pour la conductivité thermique et électrique. Crédit photo :Université nationale australienne, Symposium TUM, septembre 2020
Précédent SuivantChristian Weimer, responsable des matériaux pour Airbus Central Research &Technology, a évoqué l'impression à fibre continue dans le cadre du paysage technologique en évolution, visant à réduire le poids avec des coûts réduits et une durabilité accrue qui doit être atteinte pour que les composites s'assurent une place sur les futurs avions. Il a souligné que les composites 3D vraiment efficaces doivent utiliser :
- Les bonnes matières premières et intermédiaires - fibres, semi-finis
- Processus et interfaces efficaces – thermoplastiques AM, moulage par injection
- Conception et dimensionnement adaptés – intégrés, entièrement optimisés pour la charge 3D)
- Surface et fonctionnalité – ESN (numéro de série électronique), SHM (surveillance de la santé structurelle)
Il a également discuté du besoin de fibres et de résines bio-dérivées afin d'atteindre les objectifs urgents de durabilité climatique et environnementale.
Le symposium TUM comprenait de nombreuses autres présentations, y compris des résumés des travaux à l'ANU, et toutes étaient très intéressantes pour montrer comment les composites progressent et comment le LCC, en collaboration avec des partenaires du monde entier, continue d'envisager ce que les composites peuvent réaliser et faire avancer notre industrie.
Résine
- Présentation des vendredis AM et du podcast additif
- Fabrication additive avec des composites dans l'aérospatiale et la défense
- Essentium et Lehvoss s'associent pour développer des matériaux pour la fabrication additive
- La robotique et l'avenir de la production et du travail
- AMRC et Prodrive s'associent pour faire progresser la fabrication de composants composites recyclables
- L'additif PES augmente la résistance à la rupture et aux microfissures dans les composites époxy
- Les thermoplastiques durables et la fabrication additive forment une alliance au Colorado
- Qu'est-ce que la fabrication additive ? - Types et fonctionnement
- L'automatisation et l'avenir de la fabrication numérique ?