Avancement de la boîte à ailes infusée OOA
Alors que l'industrie aérospatiale anticipe sa reprise après la pandémie de COVID-19, la poussée précédente pour une production à haut débit s'est transformée en une action urgente visant à réduire les menaces environnementales pour la planète et les personnes. Cet effort comprend des limites sur les émissions de gaz à effet de serre (GES), la consommation d'énergie et d'eau et la création de déchets qui ne peuvent pas être recyclés. Bien que ces initiatives étaient en cours avant COVID, leur importance est maintenant accrue, tout comme le besoin de coûts beaucoup plus bas pour produire des structures composites. Le programme aéronautique paneuropéen Clean Sky 2 a financé la recherche et le développement dans tous ces domaines et a considérablement fait progresser une variété de technologies composites renforcées de fibres.
Le septième appel à propositions de Clean Sky 2 (CFP07, octobre 2017) comprend la demande d'Airbus Defence and Space (Airbus DS, Cadix, Espagne) pour une usine pilote innovante et flexible pour produire un démonstrateur de vol de caisson de voilure hautement intégré utilisant une fibre automatisée. placement (AFP) et infusion de résine liquide.
Il y a eu d'autres démonstrateurs de caisson d'aile imprégnés de résine et/ou hors autoclave (OOA), y compris un caisson d'aile « mélangé » OOA dévoilé par GKN Aerospace (Redditch, Royaume-Uni) en 2013 ; l'aile d'Airbus A220 produite par Spirit AeroSystems Belfast en Irlande du Nord en utilisant l'infusion de transfert de résine dans un autoclave; et l'aile OOA produite par AeroComposit (Moscou, Russie) pour le MS-21 avion de ligne. Cependant, tous ceux-ci ont assemblé des peaux et des longerons composites renforcés par des lisses et des attaches mécaniques (voir « Le chemin vers les ailes OOA avec un minimum d'attaches »).
Le caisson de voilure demandé par Airbus DS dans Clean Sky 2 devait faire un pas en avant en intégrant la peau inférieure rigidifiée avec des longerons avant et arrière rigidifiés, permettant un module plus complet sans attaches à transmettre pour l'assemblage avec les autres composants de l'aile.
Ce caisson d'aile utiliserait également des rubans en fibre de carbone secs étroits (0,25 ou 0,5 pouce de large) et à haute température (180 °C Tg ) durcissant les résines, mais avec des systèmes de chauffage économes en énergie et à faible coût et un contrôle et une simulation numériques basés sur des capteurs pour prédire et gérer le traitement, raccourcir les boucles d'essais et d'erreurs pendant le développement et permettre une formation rapide du personnel de fabrication. Cette numérisation évoluerait pour inclure une application mobile de réalité augmentée (application) qui fournit également des manuels d'utilisation et de maintenance, une définition de séquence de processus, un processus sans papier et un suivi des pièces et une projection de modèles CATIA sur la pièce pour faciliter le placement précis des préformes de raidisseur, des inserts d'outillage et plaques de calage en polymère renforcé de fibres de carbone (CFRP).
Peut-être le plus exigeant, ce projet exigeait que tous les outils et équipements de fabrication soient portables et flexibles, faciles à déployer sur n'importe quel site de fabrication et adaptables à d'autres conceptions et mises à niveau de pièces à mesure que des technologies plus avancées d'outillage, de chauffage et de contrôle des processus composites 4.0 deviennent disponibles.
Comme l'a expliqué le responsable du sujet Luis Rubio, responsable de l'ingénierie de développement des composites - technologie et processus chez Airbus DS, « l'objectif final du projet est de démontrer qu'une technologie alternative (au préimprégné et à l'autoclave) avec des coûts inférieurs, des délais d'exécution réduits et l'empreinte environnementale peut atteindre des tolérances de conception et des niveaux de qualité similaires. »
MTorres (Torres de Elorz, Espagne) a répondu, postulant sans partenaires. « Nous disposions de toutes les capacités en interne :AFP, infusion, matériaux de bande sèche et automatisation », explique Sebastian Diaz, directeur principal des technologies appliquées aux composites chez MTorres. La société a remporté le projet Innovative Infusion Airframe Manufacturing System (IIAMS), financé par le programme Horizon 2020 de l'Union européenne dans le cadre de l'accord de subvention n° 820845, et a commencé ses travaux en octobre 2018.
Démonstrateur de caisson d'aile extérieure
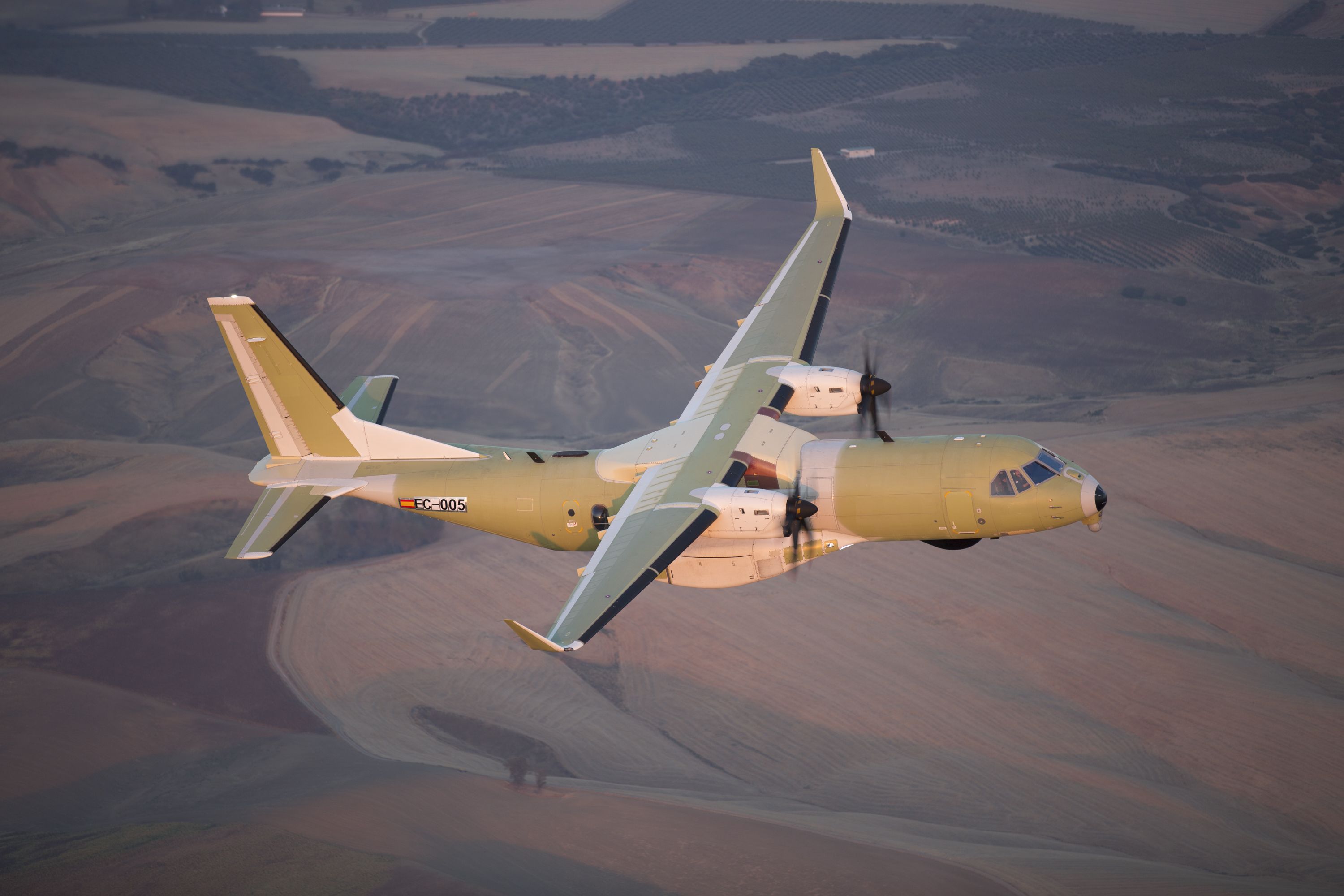
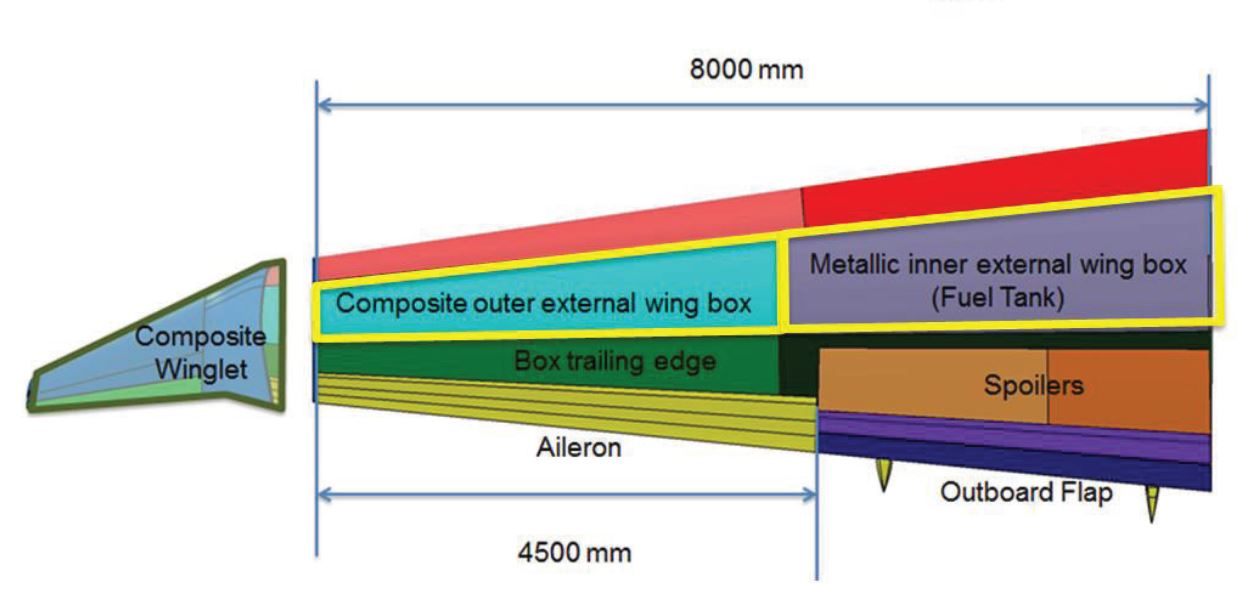
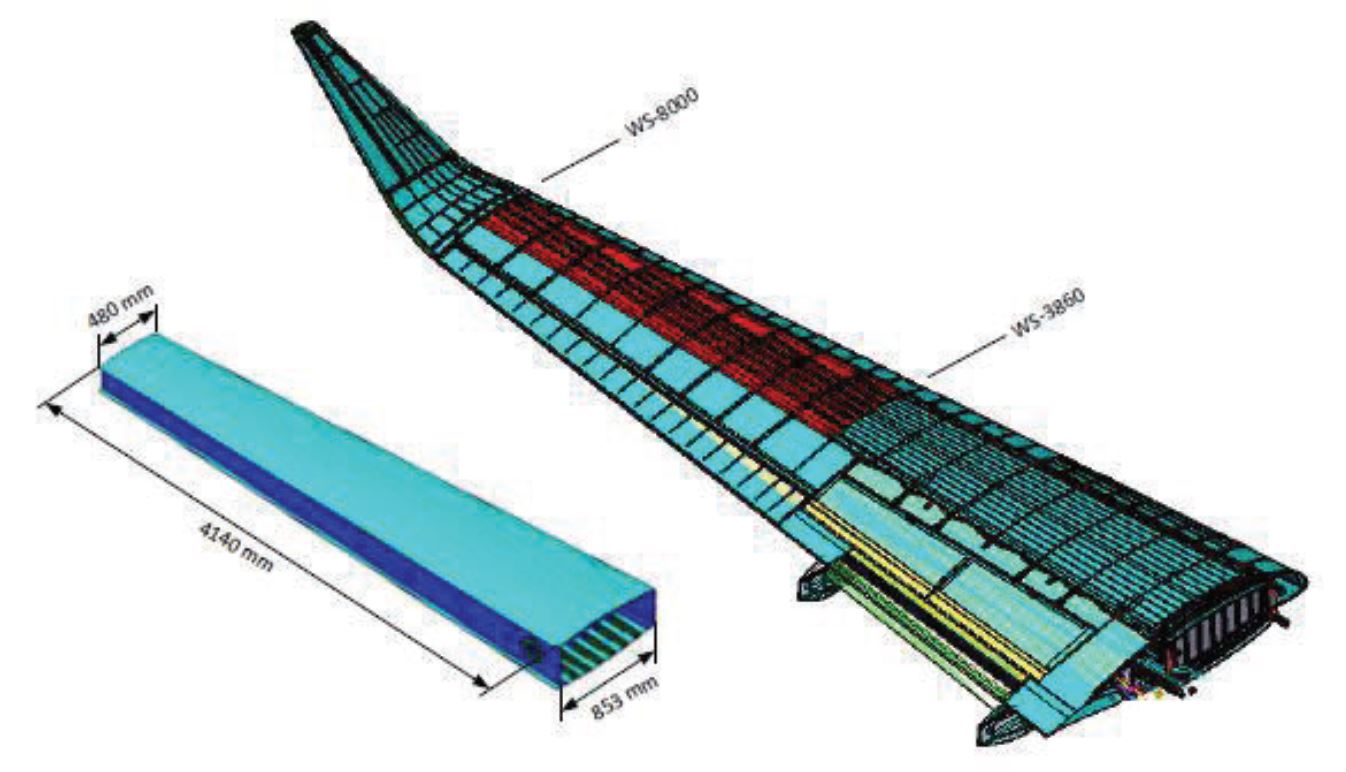
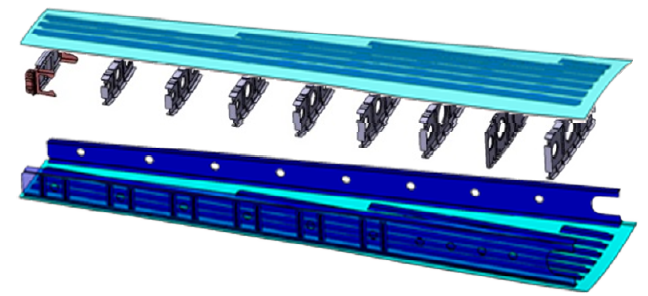
Le démonstrateur choisi par Airbus DS était un caisson de voilure extérieur basé sur son transport militaire bi-turbopropulseur C-295 (Fig. 1), produit à San Pablo, Séville, Espagne. Ce boîtier de couple hors-bord composite de 4,14 mètres de long s'accouple à un métal intérieur boîte de torsion. Le caisson d'aile composite se fixe également à un winglet, un bord d'attaque et un bord de fuite.
« Nous devions fabriquer deux démonstrateurs de 4 mètres de long, les ailes droite et gauche, qui seront installés pour des essais en vol », explique Diaz. « La fabrication devait être un processus unique, sans liaison secondaire. Nous n'avons fait que le « U », comprenant la peau inférieure avec six longerons intégrés et les longerons de chaque côté. La peau, les longerons et les longerons varient tous en épaisseur. La forme en J des longerons et l'intégration de leurs raidisseurs étaient assez difficiles à fabriquer. Nous avons également été confrontés au défi de maintenir des tolérances serrées et une géométrie précise avec ce processus de fabrication. Cette précision est critique, en particulier au niveau de l'emplanture pour l'assemblage au caisson de voilure intérieur, puis également au niveau de l'ailette. »
La conception de la fabrication industrielle innovante a été développée chez MTorres, tandis qu'Airbus DS a fourni les spécifications de conception des pièces. "Nous avons travaillé facilement ensemble pour concevoir le meilleur processus de fabrication, en vérifiant que cette conception pouvait être produite par notre processus et vice versa", explique Diaz.
Centre automatisé de thermo infusion (ACTI)
Selon la spécification Airbus DS, tous les outillages et équipements de fabrication utilisés pour produire le caisson de voilure doivent être portables, capables d'être transportés vers d'autres installations avec des véhicules standard et mis en place rapidement sans mesures spéciales. Cela a conduit au développement du centre automatisé de thermo infusion (ACTI), qui réalise le drapage à chaud des longerons et des longerons; infusion des longerons, des espars et de la peau; et des cycles de cure. Le formage par drapage à chaud (HDF) - développé sous forme de réduction chauffée dans les aérostructures et en tant que préformage chauffé en dehors de l'aérospatiale - supprime les vides dans les drapages et convertit les ébauches 2D pour les longerons et les longerons en préformes façonnées (voir « Formage par drapage à chaud »).
L'ACTI a une surface intérieure utile d'environ 5,5 x 2,2 mètres et ressemble à un système HDF traditionnel, avec un cadre en acier et une moitié supérieure qui est relevée et abaissée électroniquement, avec verrouillage et autres dispositifs de sécurité. L'outil de durcissement et plusieurs outils de formage de drap chaud sont positionnés à l'intérieur de l'ACTI. « Aucune pression n'est appliquée, seulement du vide », note Diaz. "ACTI utilise de l'air chauffé avec un flux d'air qui a été défini pour fournir un transfert de chaleur rapide à la fois dans les processus de formation de draps chauds et d'infusion."
Il note également que le système est auto-nivelant. "La rigidité de la structure ACTI (et de l'outil de durcissement) a été conçue pour se conformer aux tolérances sous les charges opérationnelles dans une condition simplement supportée sur seulement deux sections de support", explique Diaz. « Cela signifie que la précision dimensionnelle est conservée lorsqu'elle repose sur le sol, sans aucun nivellement supplémentaire ou autre réglage géométrique requis. ACTI se caractérise également par une faible consommation d'énergie et de faibles coûts de fabrication. »
Ce dernier est dû, en grande partie, au remplacement de l'assemblage de plusieurs pièces durcies par l'assemblage de plusieurs préformes, qui sont ensuite infusées et durcies en une seule structure intégrée. « L'outil de durcissement est également l'outil d'assemblage », explique Diaz. "Tous les éléments sont des préformes sèches assemblées dans l'outil de durcissement, puis co-infusées ensemble en un seul processus." Aucun gabarit d'assemblage n'est nécessaire et des tolérances strictes sont obtenues grâce à des éléments innovants dans l'outillage.
Un autre aspect clé de cette approche consiste à supprimer les tests destructifs et non destructifs (END), en s'appuyant plutôt sur les données de processus collectées au cours des différentes étapes de fabrication pour vérifier la qualité du processus et signaler les paramètres hors spécifications. Les capteurs utilisés avec l'ACTI collectent la température, le vide, le débit de résine et l'état de durcissement. « La température de l'air et la température des pièces sont surveillées », explique Diaz. "L'outillage a intégré des thermocouples qui suivent la température des moules et des surfaces des pièces." Toutes les données sont enregistrées, analysées et utilisées pour imprimer des graphiques et aider à guider les décisions de fabrication.
« Tant dans l'IIAMS que dans les projets futurs, les données aident à améliorer la configuration du processus dès les premières étapes », explique Diaz. Le flux de résine et l'état de durcissement sont surveillés à l'aide de capteurs diélectriques Netzsch (Selb, Allemagne), installés directement dans les outils de durcissement CFRP. « Nous avions besoin de capteurs sans contact pour la peau, car il n'y a pas de contact direct entre la résine et la moisissure », explique Diaz. « Les capteurs surveillent le changement du champ diélectrique à mesure que la résine arrive et devient solide pendant le durcissement. Nous avons utilisé ces données pour raccourcir le cycle de guérison. »
Plus tard dans le projet, les capteurs et l'ACTI ont été combinés à une interface homme-machine (IHM) développée par MTorres, qui permet un véritable contrôle du processus à partir d'un ordinateur, y compris le vide et la température, ainsi que le flux de résine via une vanne d'alimentation. L'objectif, selon Airbus DS, est de faire progresser la production de masse de structures primaires composites intégrées en rendant le processus plus rationalisé et intelligent.
Outillage léger et portabilité
MTorres a produit deux ensembles de moules - un pour l'aile droite et un pour l'aile gauche. « Les pièces à géométrie identique, comme les raidisseurs, n'avaient qu'un seul jeu », note Diaz. « D'autres outils ont été partagés, lorsque cela était possible. »
Un seul outil de durcissement monobloc a été utilisé pour former la forme 3D de la peau, sur laquelle toutes les autres préformes étaient situées. Mesurant environ 4,5 mètres de long, les versions droite et gauche de cet outil ont été fabriquées à l'aide de CFRP, explique Diaz. « Cela facilite le maintien des tolérances car nous avons conçu l'outillage avec le même drapage et le même traitement que les pièces, de sorte que le CTE est très proche de celui de la pièce finale. Ces outils de durcissement CFRP sont également légers, environ 200 kilogrammes, et donc mobiles avec un petit chariot élévateur électrique. Ce serait impossible si nous utilisions du métal pour un outil de 4,5 mètres de long. »
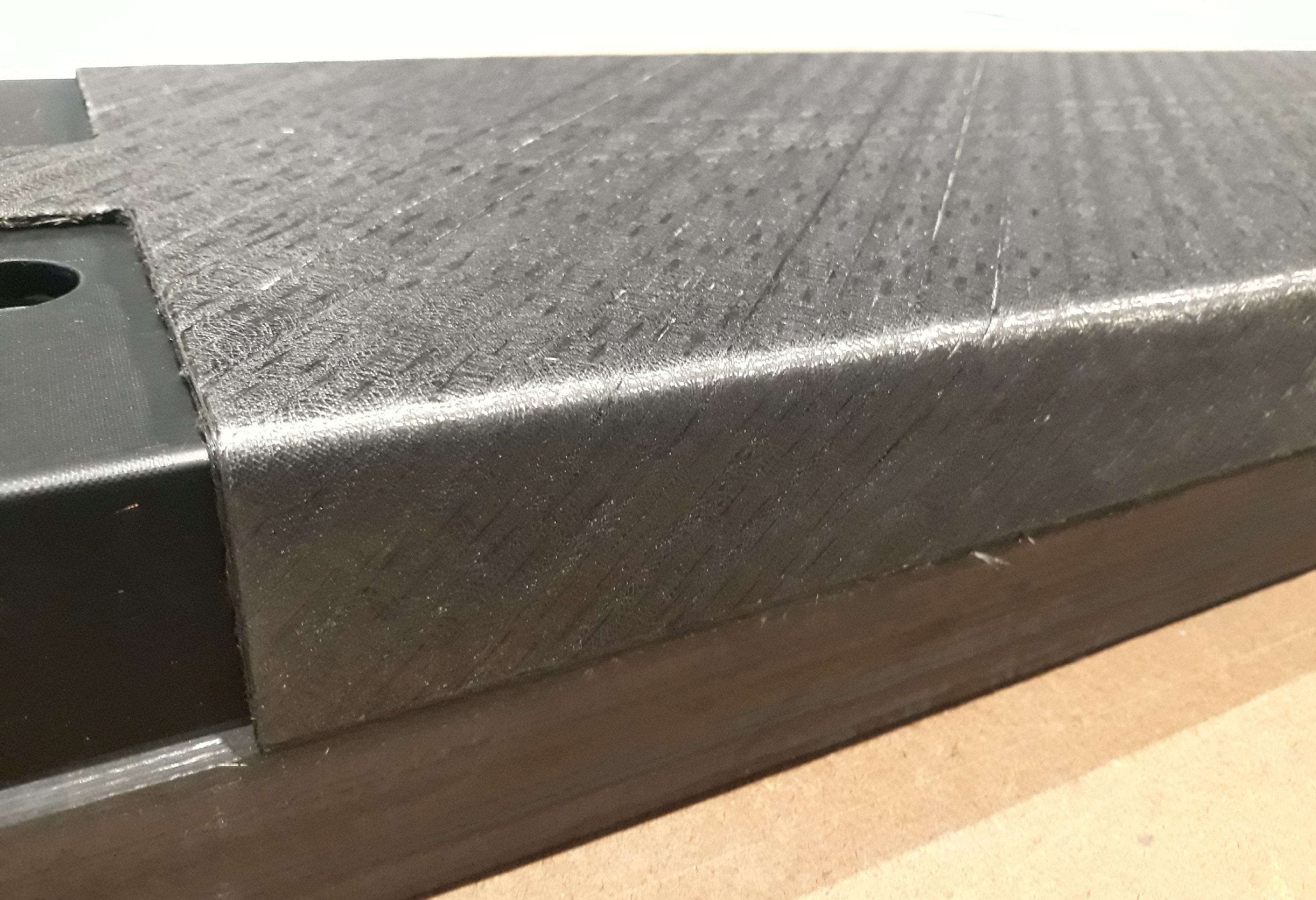
Le reste de l'outillage - cales, positionneurs et outils HDF - était facilement géré à la main. Le HDF des longerons, des longerons et des préformes de raidisseur de longeron utilisait des outils mâles (IML), également fabriqués à partir de CFRP. Pendant l'utilisation, ceux-ci ont été montés sur une table en aluminium et placés dans l'ACTI.
AFP utilisant un nouveau ruban de fibres sèches
Tous les éléments structurels du caisson de voilure - peau, longerons, longerons, raidisseurs de longerons - ont été produits à l'aide de la technologie AFP de MTorres pour les rubans en fibres sèches. "L'appel de propositions a dit d'utiliser des matériaux rapides et bon marché", explique Diaz. « Mais les rubans en fibres sèches disponibles dans le commerce, en particulier auprès des plus gros fournisseurs, n'étaient pas si faciles à acheter et nous avions l'expertise pour fabriquer notre propre matériau (voir « Nouveau ruban sec pour les composites moulés liquides »). Nous avons donc utilisé notre ruban en fibre de carbone sec de 300 grammes par mètre carré (g/m²) de 0,5 pouce de large, fabriqué à partir de la fibre haute résistance (HS) 50K de Mitsubishi Rayon (Tokyo, Japon). Notre ruban a été conçu pour faciliter et bien fonctionner pendant l'infusion, mais aussi pendant le drapage à l'aide de nos têtes AFP. Nous connaissons tous les paramètres du drapage AFP, du drapage à chaud et de l'infusion de résine, et si nous devions apporter de petits changements, nous le pouvions parce que nous disposions de la ligne de fabrication de rubans. »
MTorres a également testé son procédé de fabrication de caisson de voilure avec du ruban 200 g/m² d'Hexcel (Les Avenières, France) fabriqué à partir de sa fibre à module intermédiaire (IM). « Bien que notre processus puisse bien fonctionner avec les deux types de rubans », explique Diaz, « au cours de la phase de développement, il était plus facile et moins coûteux de poser avec notre matériau par rapport au matériau disponible dans le commerce - la largeur et la rigidité ont été conçues pour que son comportement à partir de bobines à table était lisse et rapide. Il était également facilement disponible. »

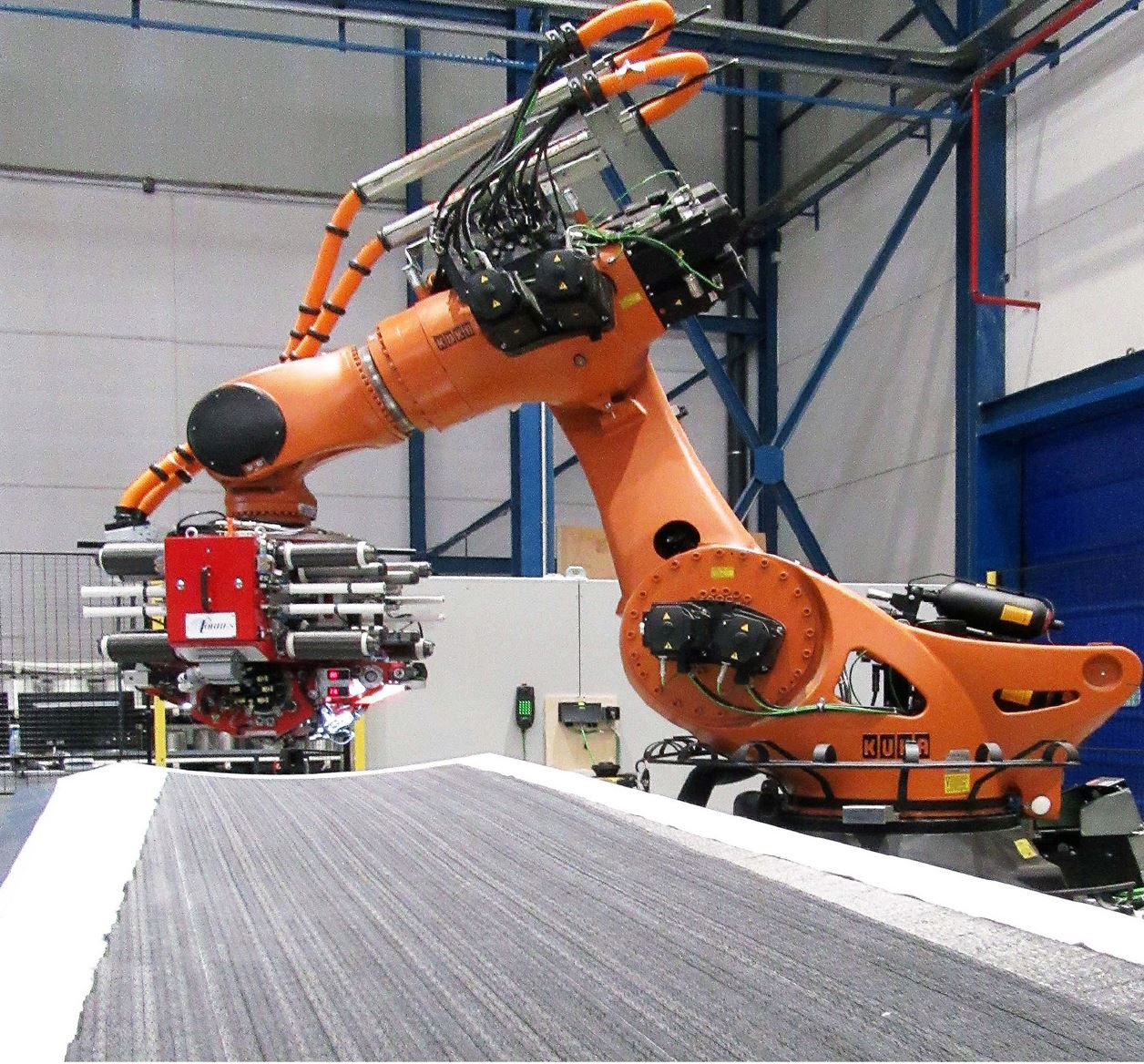
Étape 1. L'AFP a été utilisée pour déposer des peaux de caisson de voilure (illustrées ici) ainsi que des ébauches 2D pour les longerons, les longerons et les raidisseurs de longerons. Crédit photo, toutes les étapes : Projet IIAMS, Airbus Defence and Space, MTorres.
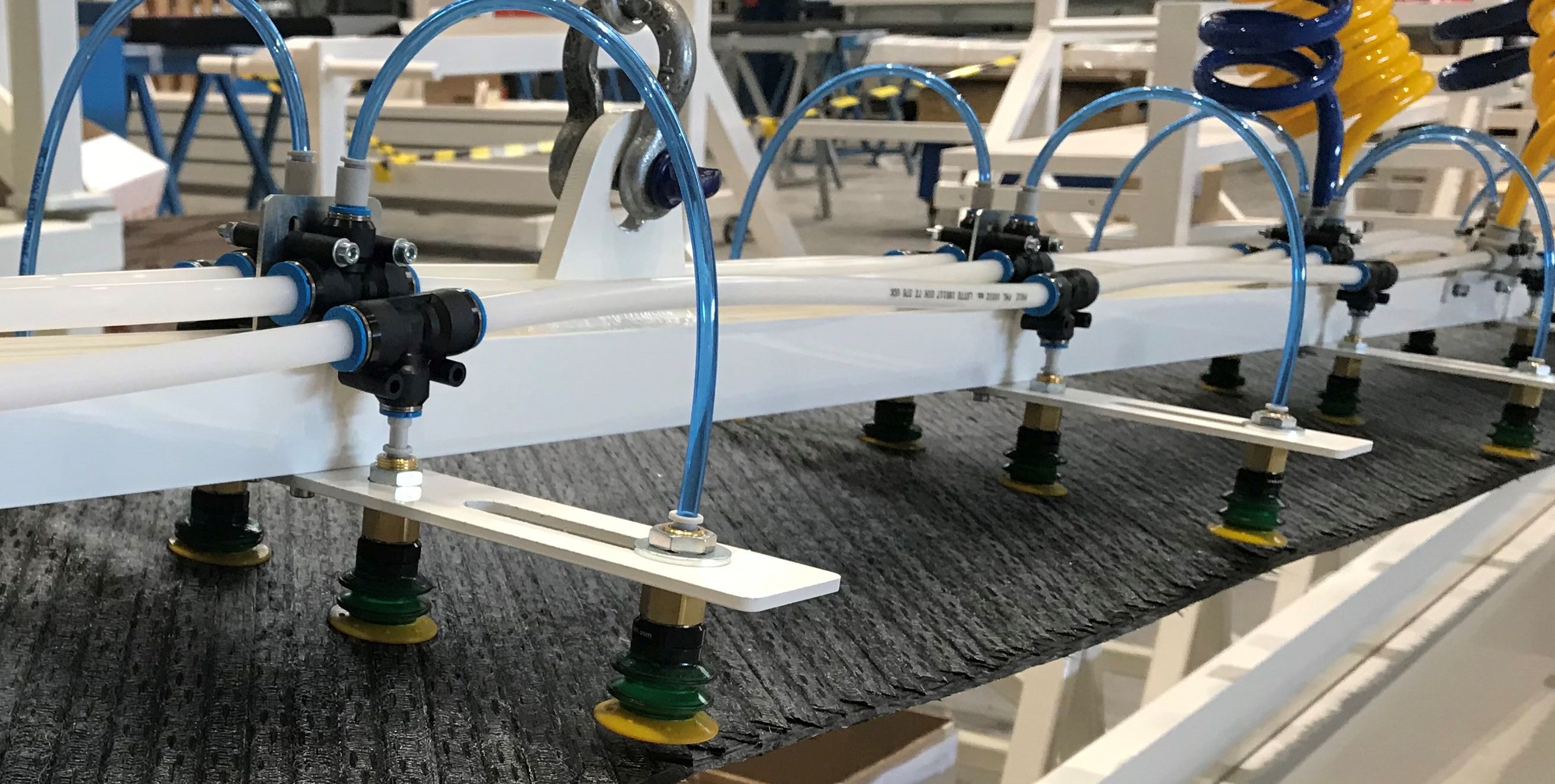
Étape 2. Les ébauches de ruban plat ont été transportées de la table de drapage aux outils de formage à chaud.
Il note que deux stratégies ont été suivies pour l'AFP :une pour la peau inférieure et une autre pour les longerons, les longerons et les raidisseurs de longerons. La peau (3-6 millimètres d'épaisseur) a été appliquée à la forme 3D finale sur le dessus de l'outil de durcissement (étape 1), en utilisant une membrane semi-perméable — brevetée par Airbus dans son infusion de procédé assisté par vide (VAP). Les longerons, les longerons et les raidisseurs de longerons ont été posés sous forme de flans plats (2D) sur une table à vide, puis déplacés sur les outils HDF pour obtenir leur forme 3D finale (étape 2).
Préformage chauffé
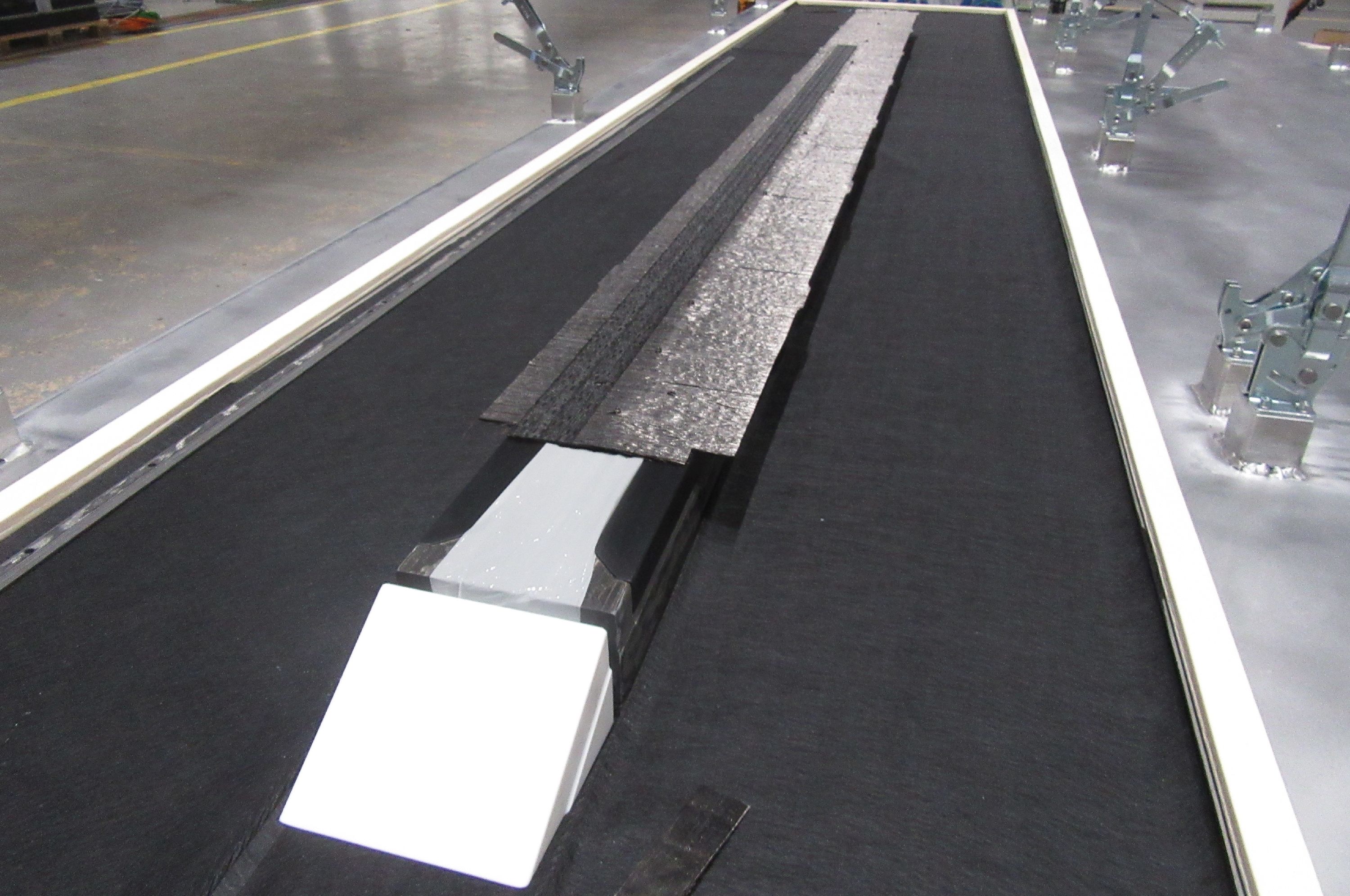
Étape 3. L'ébauche de limon est placée sur l'outil HDF mâle.
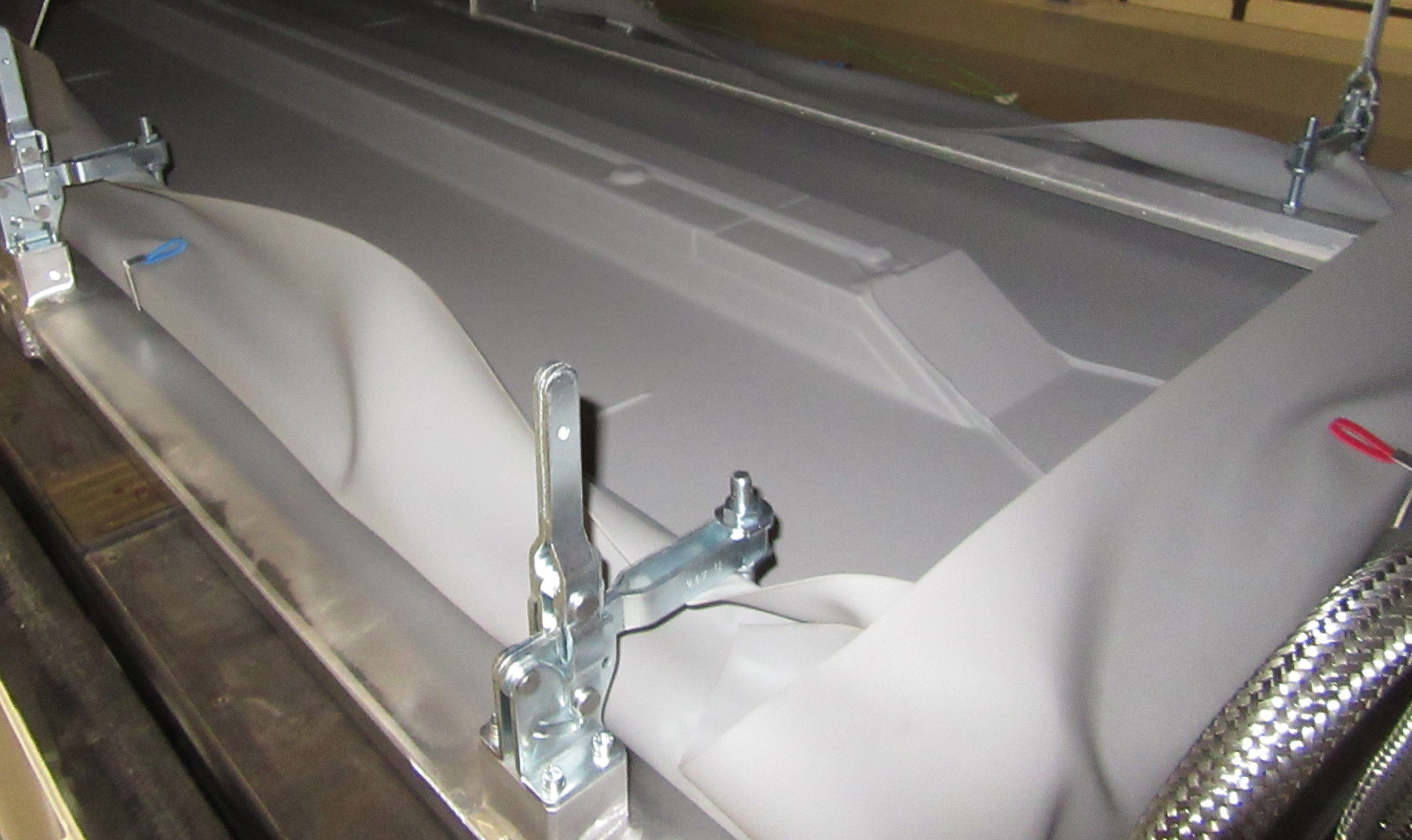
« Nous avons déplacé les ébauches plates pour les longerons, les longerons et les raidisseurs de longerons de la table de drapage à la station de formage à chaud à l'aide d'un portique avec des pinces à vide », explique Diaz. « Le système automatisé peut déplacer les flans à plat et les placer sur les outils de formage mâles [étape 3] sans créer de plis. » Les outils de formage ont été installés sur une table de formage en aluminium, qui a été placée dans l'ACTI. Un sac sous vide en silicone réutilisable (Mosites Rubber Co., Fort Worth, Texas, États-Unis) a été placé sur les ébauches, qui ont ensuite été chauffées dans l'ACTI à 130 °C et façonnées à l'aide d'une pression sous vide (étape 4). « Le vide a été appliqué en douceur suivant une rampe prédéfinie au moyen d'une vanne de régulation lorsque le point de consigne de température était atteint », explique Diaz.
Il note que les rubans secs sont plus faciles à préformer/former à chaud, « car la liaison entre les couches est plus douce que dans les préimprégnés. Bien qu'il s'agisse d'un matériau sec, il est un dégonflage HDF/chauffé dans lequel la préforme obtenue garde sa forme grâce aux liants inclus dans les rubans. »
Pour les longerons et les raidisseurs de longeron, des ébauches ont été formées en deux L, qui ont ensuite été placés dos à dos sur l'outil de durcissement pour former des longerons/raidisseurs en T. Chacun des six longerons de peau est différent et nécessite des ébauches de formes différentes pour créer les préformes. Chacun des 24 raidisseurs de longeron est également d'une longueur différente.
Les longerons en J avant et arrière comprennent une ébauche en forme de C tournée vers l'intérieur du caisson de voilure et une autre ébauche en forme de Z tournée vers l'extérieur — les deux sont placés dos à dos. Les longerons ont également des pieds de forme sinusoïdale à l'extérieur du caisson de voilure (flèche à l'étape 7). « Nous avons découpé la forme des pieds de longeron sur la table de drapage à plat avant de déplacer le flan vers la station de formage », explique Diaz. « Rien n'a pu être taillé ou fraisé par la suite dans cette zone. Les ébauches ont été placées directement sur l'outil de formage mâle avec les pieds de longeron sur le côté gauche de l'outil et la bride supérieure sur son côté droit. »
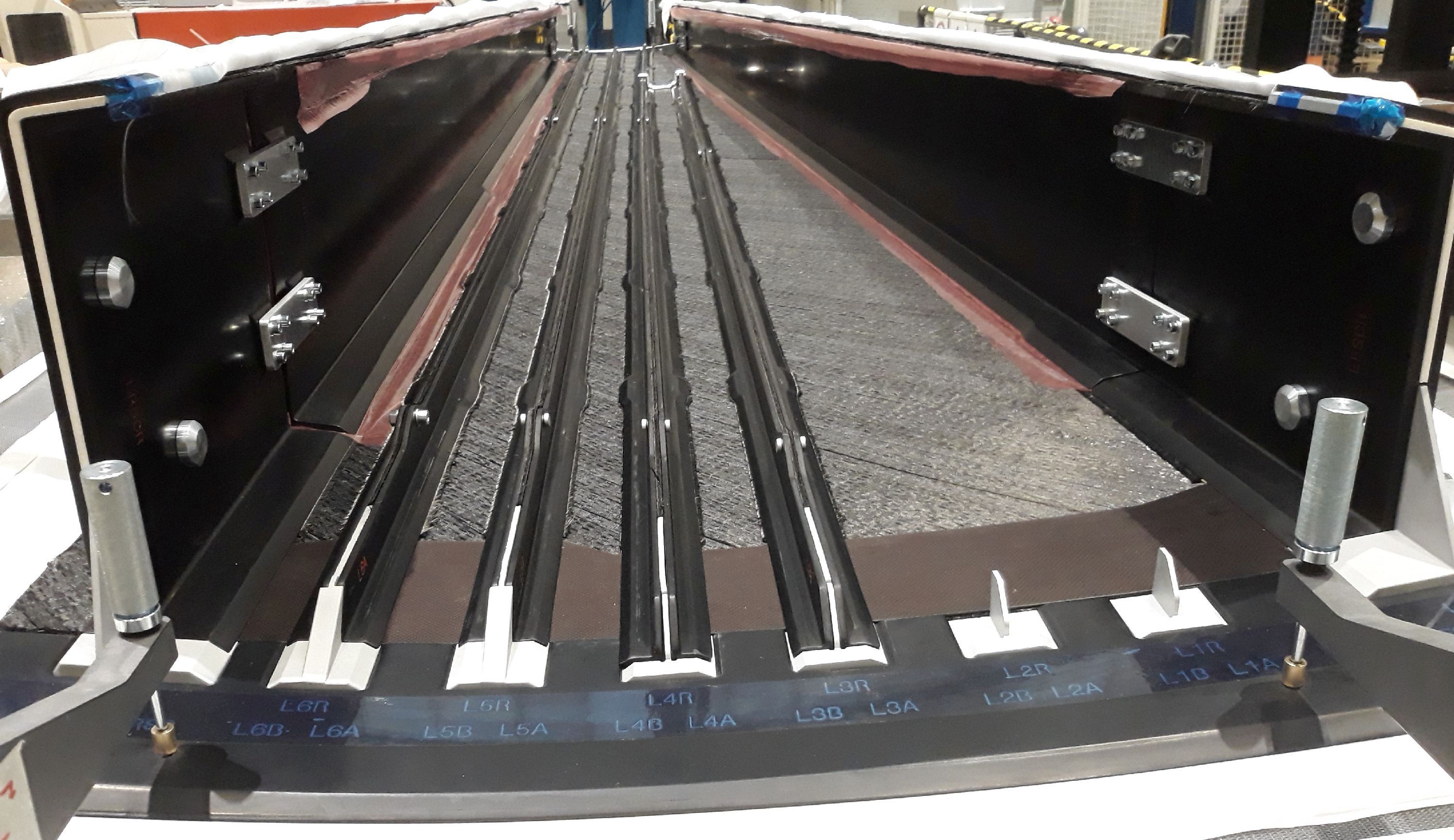
Fig. 3. Placement précis de la préforme. Les préformes pour les longerons en J et les longerons ont été positionnées à l'aide de cylindres métalliques jumeaux (vus à l'extrême gauche et à droite), des positionneurs blancs et un caul CFRP avec des découpes pour les longerons/positionneurs. Crédit photo : Projet IIAMS, Airbus Defence and Space, MTorres.
Infusion unique
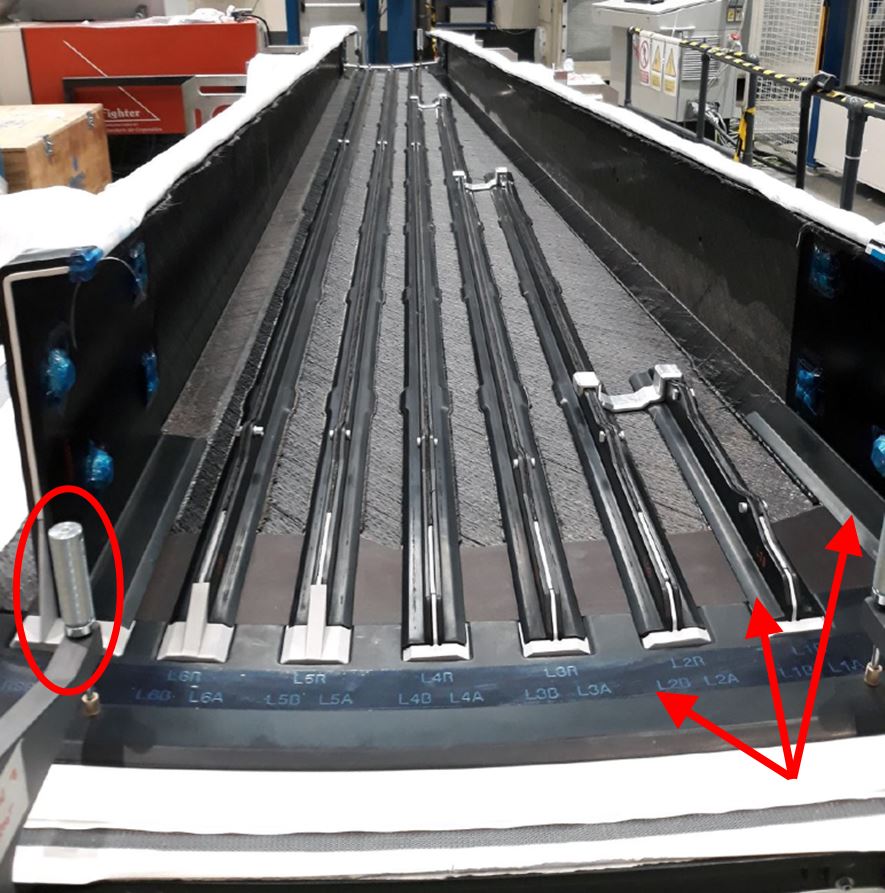
Étape 5. Des préformes de longeron et de longeron ont été placées sur la peau inférieure, à l'aide de cylindres (entourés ) et des éléments de positionnement blancs. Cauls CFRP noirs (flèches ) ont également été utilisés pour aider à positionner les limons et placé sur les longerons et les longerons en J.
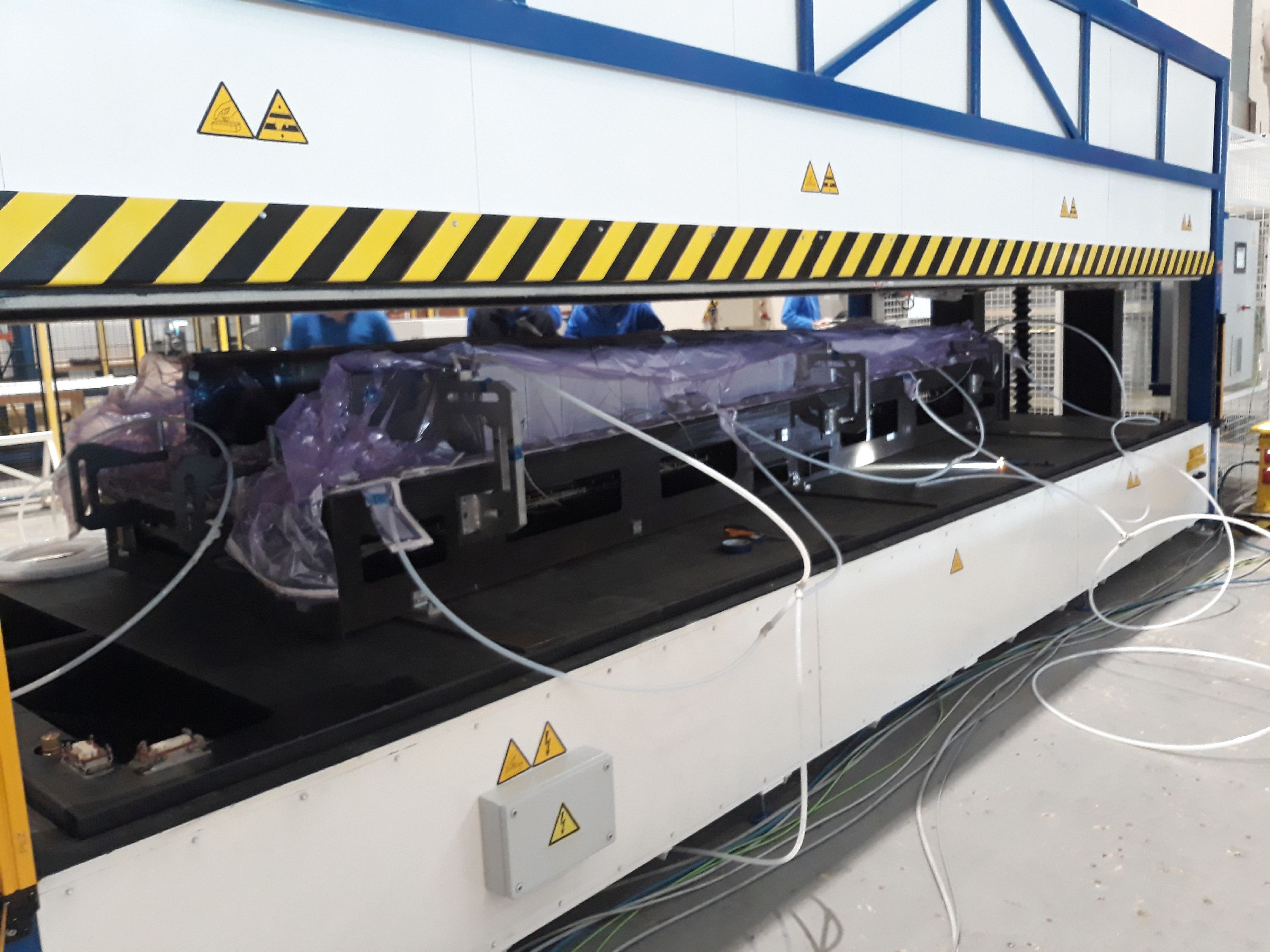
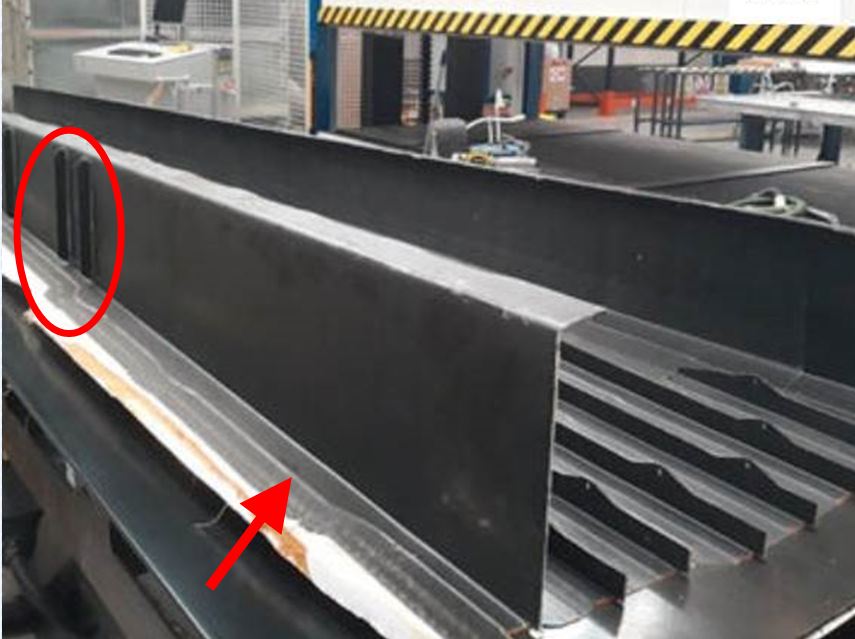
Étape 7. Le démonstrateur initial achevé à MTorres montre le longeron en J avec deux raidisseurs de nervures (encerclé ) et ses pieds sinusoïdaux (flèche ).
L'étape suivante consistait à placer les préformes de longeron, de longeron et de raidisseur de longeron sur le revêtement inférieur de l'aile déjà posé (étape 5). « Nous indexions chaque préforme au fur et à mesure que nous la placions sur la peau et l'outil de durcissement », explique Diaz. Les cylindres qui agissent comme éléments de localisation peuvent être vus à l'extrémité du longeron à gauche de l'étape 5 et à l'extrémité des deux longerons de la figure 3. Ces images montrent également des dispositifs de positionnement blancs pour les longerons et les longerons en J. Il y avait 13 de ces positionneurs dans l'assemblage final de la préforme, et chacun était différent.
Les plaques de calage étaient également un élément clé du système de localisation et de placement des préformes. Ils ont servi l'objectif traditionnel de maintenir une pression et une température uniformes dans les régions de couches complexes et/ou de géométrie, mais seraient également essentiels pour l'infusion, comme indiqué ci-dessous. Une plaque de calage en PRFC noire avec des découpes pour les préformes de longerons est visible à l'extrémité des longerons et des longerons à l'étape 5 et à la figure 3.
"L'emplacement des préformes de limon dépend de l'emplacement de ce caul", explique Diaz. « La technologie numérique que nous avons développée pour surveiller et contrôler le processus de fabrication comprenait une application de réalité augmentée qui projetait les modèles CATIA sur le layup. Cela a été utilisé pour aider à guider le placement des plaques de calage, des éléments de positionnement, puis des préformes. Il a également montré les prochaines étapes à effectuer. L'application permet l'auto-assistance sur les tablettes afin que tous les travailleurs aient un accès facile à toutes les informations."
Un ensemble final de plaques de calage en PRFC noir a ensuite été placé sur le dessus des préformes en L pour les longerons en T et également le long de l'intérieur et de l'extérieur de chaque longeron en J, s'étendant vers le haut sur la bride et vers le bas sur le pied à l'extérieur du caisson d'aile, comme illustré à l'étape 5 et à la figure 3. « Les longerons utilisent également une sorte de plaque de calage sur le côté intérieur aux extrémités, afin d'obtenir une précision accrue dans les zones de jonction », explique Diaz. « Toutes ces plaques de calage ont été utilisées pendant le processus HDF et sont restées attachées aux préformes grâce au drapage. »
L'assemblage de préforme sèche terminé avec des plaques de calage a ensuite été recouvert d'une couche pelable et d'un film de sac sous vide. L'ensemble complet de la peau, des longerons et des longerons a ensuite été placé dans l'ACTI et l'outillage a été chauffé à 120°C. La résine époxy Hexcel RTM6 a été chauffée à 70°C et dégazée avant l'infusion via un seul point d'alimentation en résine. « L'ACTI était prêt à alimenter en résine à partir de quatre emplacements », note Diaz, « mais après une simulation et des tests approfondis, nous avons décidé qu'il était plus facile et moins cher d'avoir une seule entrée de résine. »
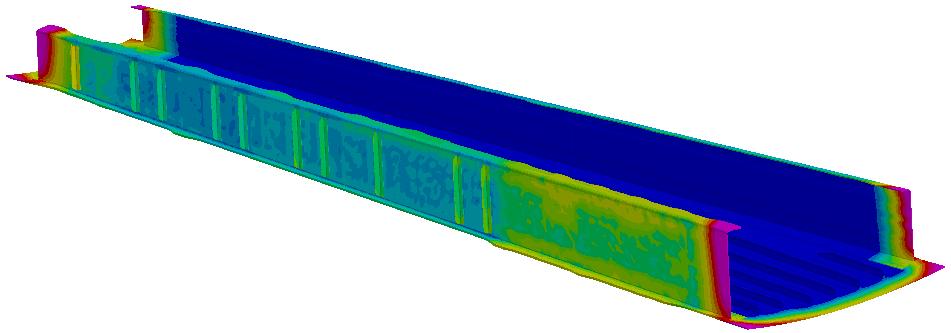
Même avec une seule entrée, le processus d'infusion était très complexe, comprenant trois modes différents. « Nous avons d'abord effectué une simulation d'écoulement à l'aide du logiciel PAM-RTM [ESI Group, Paris, France] », explique Diaz. « Il y avait un mélange si complexe de fronts d'écoulement et de paramètres nécessaires pour un mouillage complet. Par exemple, l'écoulement de la résine était plus rapide au centre du caisson de voilure, mais c'était un défi de mouiller tous les raidisseurs. »
Le VAP, avec une membrane semi-perméable, a bien fonctionné pour la peau inférieure, mais il a été remplacé par un filet d'écoulement à haute température le long des longerons et à l'intérieur des longerons. « Les coins étaient les zones les plus difficiles à mouiller », note Diaz, « mais ils étaient également les plus critiques pour maintenir les tolérances d'assemblage, ainsi que le long des bords. » Cela peut être vu dans les zones rouges de la simulation d'écoulement sur la figure 4. « Dans ces zones, une approche personnalisée a été développée pour atteindre les dimensions précises requises », explique-t-il. Nous avons également utilisé des orifices d'aspiration le long du périmètre et au-dessus des longerons. »
L'infusion a été relativement rapide, comme prédit par les simulations, suivie d'un durcissement de deux heures à 180°C, en utilisant uniquement de l'air chaud, et non des outils chauffés. Après avoir été démoulé, chaque démonstrateur de caisson de voilure a ensuite été inspecté à l'aide d'un contrôle par ultrasons (UT). Cela a été fait dans le cadre des livrables du projet IIAMS, pour analyser la qualité des démonstrateurs. L'application industrielle de ce processus, cependant, réduira les END traditionnels au profit de capteurs numériques et d'outils d'inspection en ligne plus rapides tels que les systèmes de vision.
Selon Diaz, bien que le cycle de durcissement par infusion soit similaire à celui d'un caisson d'aile préimprégné durci à l'autoclave, le temps de cycle global devrait être inférieur. « Nous avons éliminé la majeure partie de l'assemblage par la suite et nous n'avons pas non plus besoin de caler quelque chose comme avec du préimprégné, mais notre qualité est la même. Par exemple, le collage entre la dernière couche de la peau et la première couche d'un limon ne nécessite aucun film adhésif au milieu pour améliorer les propriétés mécaniques et tenir compte des tolérances. C'est évidemment plus efficace, mais il note que la cadence de production des pièces n'était pas au départ le facteur déterminant. "Cette méthode n'est pas en concurrence avec la fabrication de pièces individuelles mais avec un assemblage de caisson de voilure terminé."
Démonstrateurs complets, cheminement vers la certification
« Nous n'avions que 18 mois pour mener à bien ce projet, qui comprenait la conception du processus et de l'outillage et la fabrication de l'outillage et des démonstrateurs », explique Diaz. «Au 14e mois, nous avions le premier démonstrateur prêt à être exposé au JEC fin février 2020 [étape 3], mais le JEC a ensuite été annulé en raison de la pandémie. Bien que le projet se soit terminé fin septembre 2020, si vous soustrayez les mois pendant lesquels nous n'avons pas pu travailler en raison de COVID-19, nous avons en fait terminé au 16e mois. Nous avons pu respecter ce calendrier très serré grâce à notre capacité et capacité de conception internes. pour fabriquer les prototypes d'outillage à l'aide de nos fraiseuses AFP et CNC.
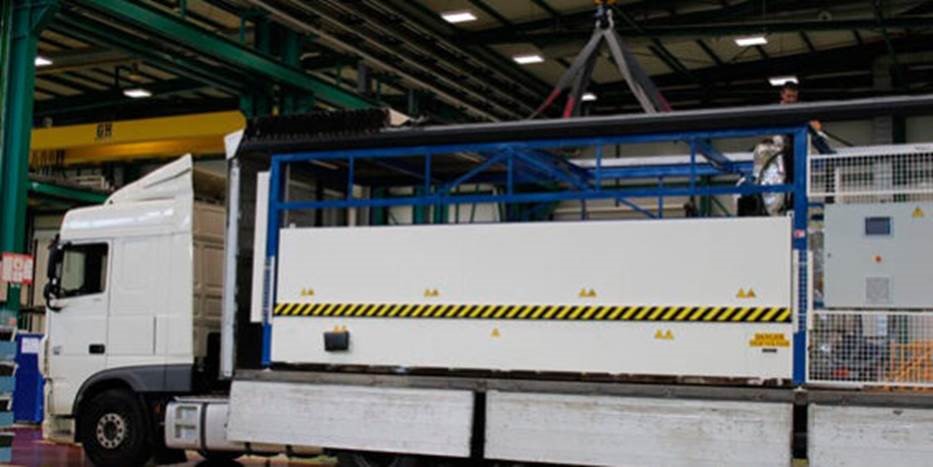
Étape 8. L'équipement de formage/durcissement ACTI et l'outillage du caisson de voilure ont été montés sur un camion de déménagement standard et transférés à Airbus DS à Cadix, en Espagne.
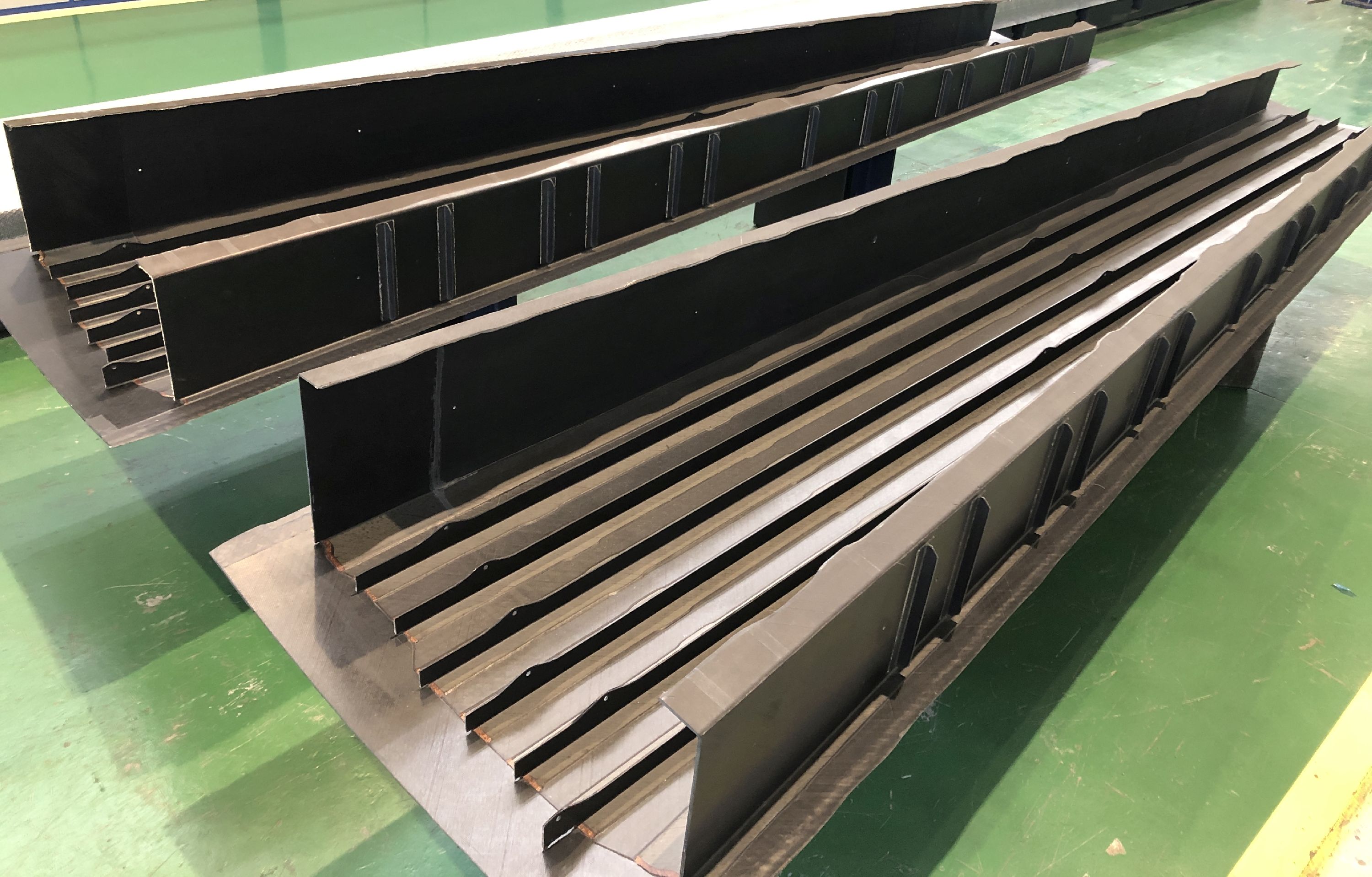
Un démonstrateur simplifié de 1 mètre de long a été réalisé à MTorres pour vérifier l'ensemble des paramètres du procédé. Ensuite, le premier démonstrateur grandeur nature a été produit. L'outillage et les équipements de fabrication ont ensuite été transférés chez Airbus DS à Cadix (étape 8), où le démonstrateur final a été produit. Cela faisait également partie des livrables du projet, prouvant que l'équipement pouvait être facilement transporté et installé à plusieurs endroits.
Comme expliqué dans l'encadré, « Feuille de route du caisson de voilure de l'IIAMS vers la certification », Airbus DS a joué un rôle clé dans le programme Clean Sky, passant de co-leader du démonstrateur de technologie intégrée (ITD) Green Regional Aircraft (GRA) dans Clean Sky, co-leader de l'ITD AIRFRAME, ainsi que leader pour le banc d'essai en vol 2 (FTB#2) dans la plate-forme de démonstration d'avions intégrés REGIONAL (IADP) au sein de Clean Sky 2. Le FTB#2 comprendra d'autres composites et cellule développements, y compris dans le cockpit et d'autres composants de l'aile.
Tous les projets de préparation du FTB#2 s'inscrivent en effet dans une stratégie plus large et à long terme chez Airbus. L'objectif est de développer une future cellule de turbopropulseur plus légère et plus efficace, ainsi que des processus de production moins chers et utilisant moins d'énergie, de fabrication de liquides et de matériaux auxiliaires, tout en générant moins de déchets et en offrant une recyclabilité accrue.
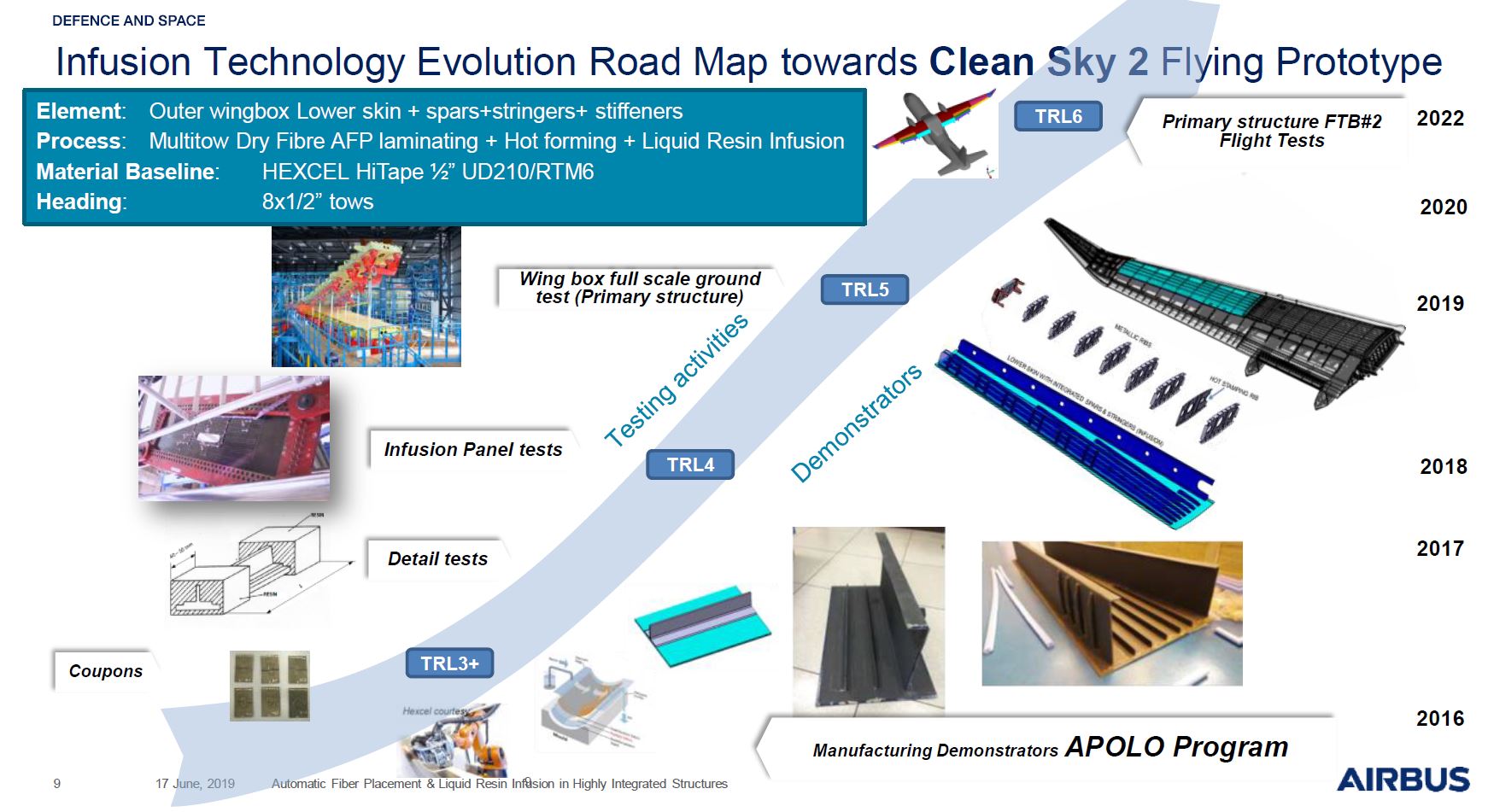
« Pas à pas, nous [Airbus DS] parcourons l'ensemble de la pyramide des tests des structures de la cellule, des coupons aux tests structurels à grande échelle de l'aile extérieure", explique A.E. Jiménez Gahete dans un Materiales Compuestos de septembre 2020 article intitulé « section de caisson de voilure hautement intégrée d'Airbus Defence and Space fabriquée par placement de fibres sèches et infusion de résine liquide ». Les tests de caractérisation des matériaux, une matrice de test des détails de conception et des tests de sous-composants pour les autorisations de conception ont tous été réalisés avec des résultats positifs. MTorres a aidé dans ces tests, y compris des coupons et des pièces de test de fabrication, ainsi que des démonstrateurs pour valider le processus de fabrication du caisson de voilure et les détails de conception. Seuls les derniers tests statiques et fonctionnels à grande échelle de l'aile extérieure restent, dit Gahete, pour obtenir la qualification FTB#2 pour le vol.
« La perfusion en une seule fois réduit les articulations, diminue le poids et augmente la robustesse », explique Diaz. "Le nouveau ruban sec développé par MTorres a produit d'excellents résultats, à la fois dans le traitement - AFP, drapage à chaud et infusion - et dans les propriétés structurelles de la pièce." Il note que, historiquement, il y a eu des doutes sur le fait que les composites infusés de résine pourraient correspondre aux mêmes performances structurelles et tolérances que le préimprégné durci à l'autoclave.
« Obtenir les mêmes tolérances en une seule opération avec un outillage souple [non métallique] était notre plus grand défi », concède-t-il. « Mais nous avons prouvé que cette technologie fonctionne et qu'elle peut produire les grandes structures primaires nécessaires aux futurs avions. Notre prochaine étape est de continuer à faire progresser les technologies numériques et la portabilité du système de production. »
Résine
- Les poudres pigmentaires ont infusé de la brillance dans l'industrie du plastique
- BLB Industries The BOX SMALL
- Airbus présente l'usine du futur
- Le développement des plastiques modernes
- Histoire de la vis
- Vespel® :le matériau aérospatial
- Qu'est-ce que l'économie circulaire ?
- Faire progresser la technologie dans le nouveau scénario de travail
- Le meilleur choix :un tour CNC Box Way