FACC met l'accent sur les préimprégnés à durcissement rapide, les thermoplastiques et les composites biosourcés pour la durabilité des aérostructures de nouvelle génération
FACC (Ried im Innkreis, Autriche) est l'un des principaux fournisseurs aérospatiaux de niveau 1 spécialisé dans la production de systèmes légers pour les intérieurs, les moteurs et les cellules. Dans le numéro de septembre 2021 de son magazine BEyond, FACC présente sa nouvelle usine en Croatie pour les composants de cabine d'avion, le programme COMPETE pour ses fournisseurs qui met l'accent sur les matériaux du futur et trois technologies de R&D axées sur les composites :soudage par induction, moulage par injection hybride et préimprégnés à durcissement rapide.
FACC en Croatie
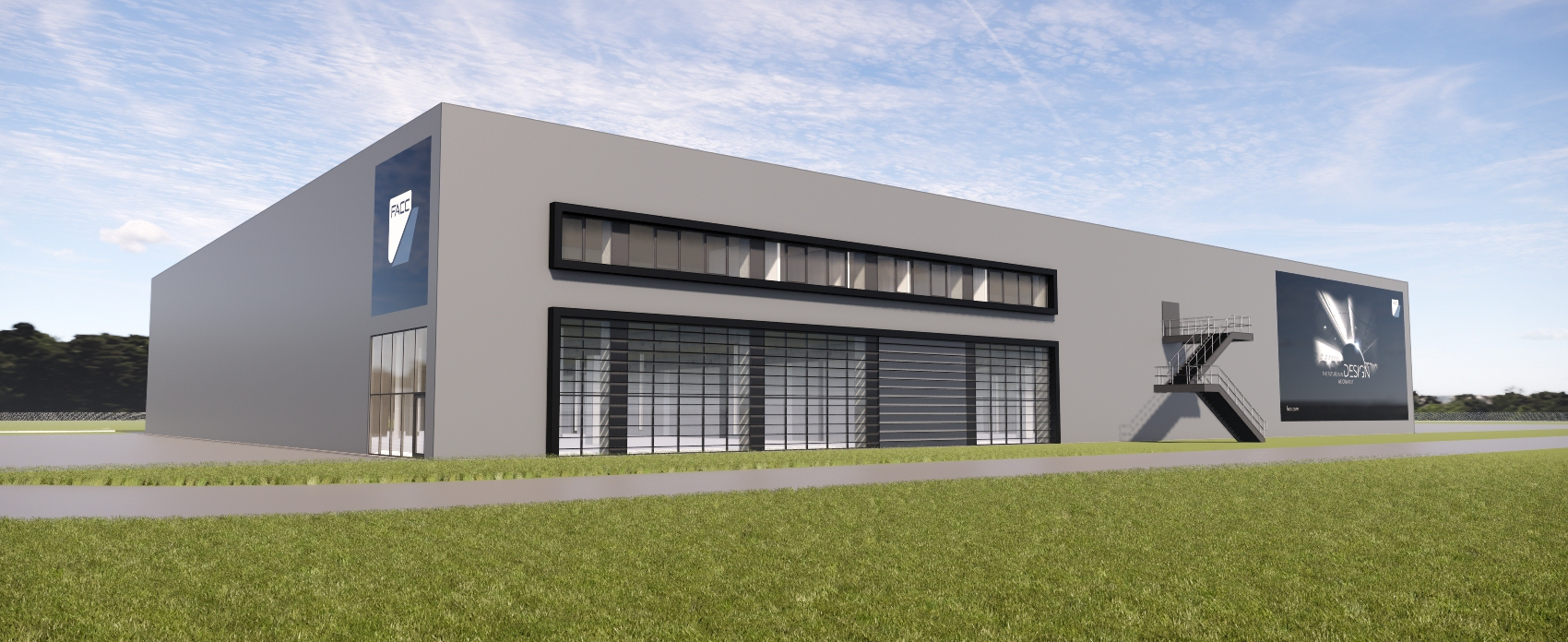
Une usine de haute technologie est actuellement en construction près de Zagreb, en Croatie. Cette installation de 10 000 mètres carrés, dont l'ouverture est prévue en 2022, produira des composants de cabine légers pour les avions commerciaux et les jets d'affaires en utilisant la dernière technologie de composites renforcés de fibres. « Cet investissement entièrement nouveau nous permet de créer une usine de premier ordre qui rassemble une technologie de pointe, une automatisation et des méthodes 4.0 », explique Robert Machtlinger, PDG de FACC. Il note que l'usine est idéalement située à proximité des sites de FACC en Autriche ainsi que du port en eau profonde de Koper. L'usine intègre également d'anciens services tiers dans sa propre chaîne de valeur et jette les bases des futures augmentations de capacité.
Programme partenaire COMPETE
La FACC a lancé le programme de partenariat COMPETE en février 2021 pour renforcer ses liens avec des partenaires sélectionnés et intensifier durablement la coopération. Les fournisseurs de FACC auront la possibilité de générer de nouvelles commandes malgré les hauts et les bas du marché de l'aviation, mais ils doivent d'abord concurrencer avec succès les autres fournisseurs. FACC évalue ses fournisseurs selon les critères suivants :
- Rapport coût-efficacité
- Excellence opérationnelle
- Matériaux du futur :des matériaux innovants pour un changement radical dans les produits et les processus de production
- Partenariat et passion
- Efficacité dans tous les processus, y compris la numérisation ciblée
- Transparence des citations
- Responsabilité environnementale et sociale.
« COMPETE, c'est avant tout une concurrence loyale et des partenariats solides avec des fournisseurs aux performances constantes et au potentiel particulièrement élevé », déclare Andreas Ockel, COO de FACC. « Nous concentrons notre futur volume d'achats sur nos partenaires du programme COMPETE. Au cours des trois prochaines années, FACC redistribuera 75 millions d'euros d'achats, avec pour objectif de passer de 440 à moins de 400 fournisseurs.
En donnant plus de détails sur les matériaux du futur, Ockel explique qu'il est essentiel d'offrir de l'innovation dans les matériaux :« Nouveaux composites renforcés de fibres les matériaux façonnent notre avenir ! Les systèmes de résine à durcissement instantané et à durcissement rapide qui réduisent considérablement les temps de cycle de production sont une innovation qui introduit de véritables changements d'étape dans les processus de fabrication. Nous cherchons donc à travailler en étroite collaboration avec des fournisseurs qui offrent cet avantage concurrentiel technologique. »
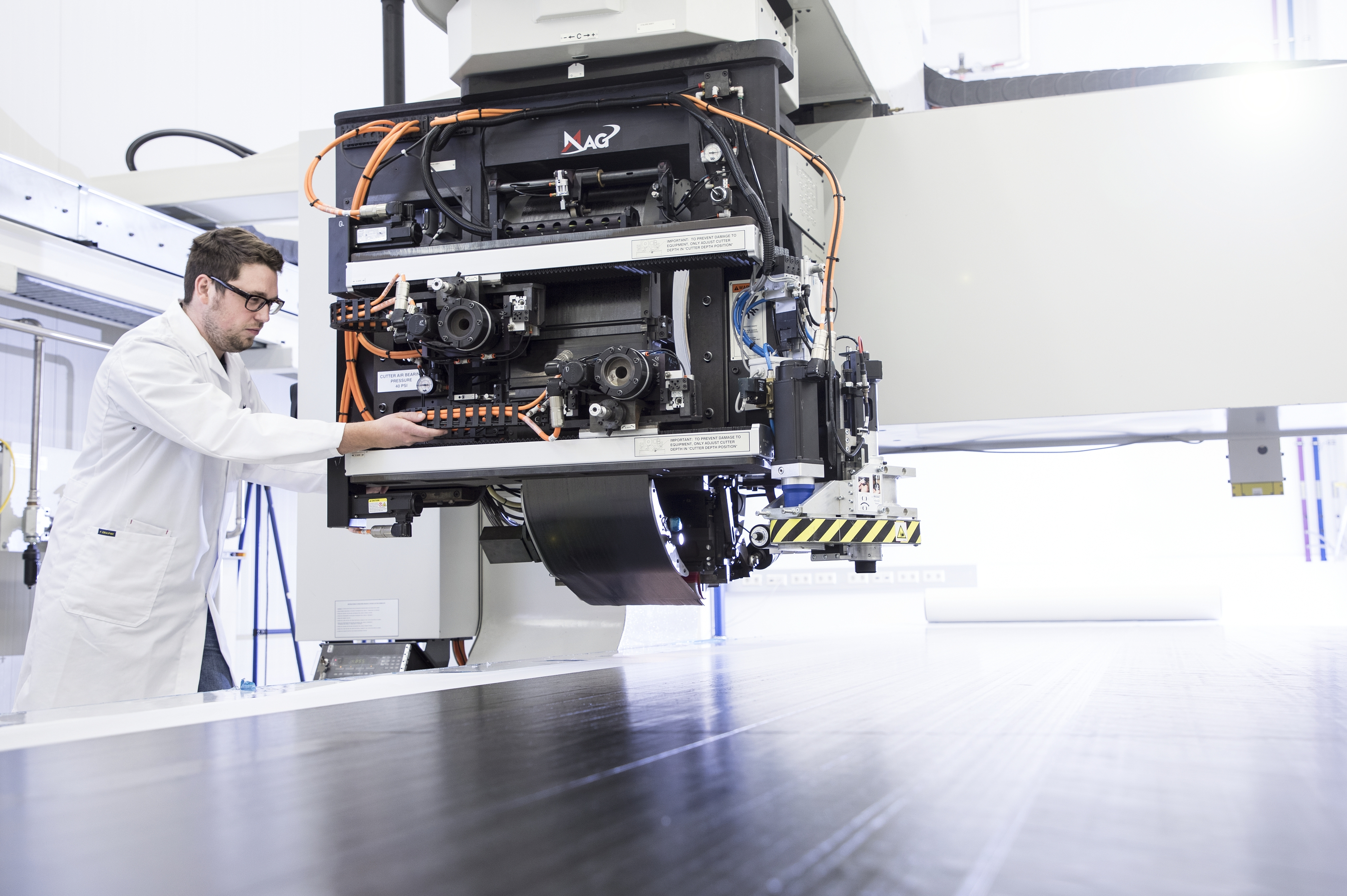
Durabilité, investissement et innovation
La FACC affirme qu'elle a contribué à accroître la durabilité dans l'industrie aéronautique grâce aux pièces d'avion qu'elle fabrique à l'aide de composites légers et de nouvelles formes aérodynamiques. Pour réduire davantage le CO2 global à l'avenir, l'entreprise travaille dur pour développer des technologies qui rendent les avions encore plus légers, plus silencieux et plus efficaces.
FACC étudie actuellement des composites utilisant des matériaux biosourcés et/ou biosourcés qui, selon lui, devraient permettre prochainement un recyclage complet des composants d'avions. "Il s'agit de développer des matériaux biologiques et de nouveaux procédés qui consomment moins d'énergie et offrent de meilleures performances tout en restant abordables", explique Machtlinger.
L'entreprise elle-même devient également plus durable, visant à ce que ses usines soient autosuffisantes en termes d'énergie et que ses processus de production soient neutres en carbone d'ici 2040. Pour la décennie en cours, la feuille de route 2030 de FACC comprend des investissements dans de nouvelles installations comme Zagreb, ainsi que de nouvelles méthodes de production, mises en évidence ensuite.
Trois initiatives de R&D
FACC développe le soudage par induction de composites thermoplastiques pour remplacer les vis et les rivets dans les composants et assemblages d'avions. Une bobine d'induction induit un courant de Foucault dans les fibres de carbone, générant de la chaleur (voir « Soudage des composites thermoplastiques »). Le thermoplastique haute performance est ensuite fondu et consolidé dans la zone de soudure. Des joints soudés homogènes de composites thermoplastiques renforcés de fibres sont utilisés dans les gouvernails, les gouvernes de profondeur et les volets. Ils peuvent être assemblés plus rapidement et plus efficacement par rapport à la fixation mécanique ou au collage et peuvent être entièrement automatisés.
Moulage par injection hybride est décrit comme un moyen efficace de fonctionnaliser les composites renforcés de fibres. Le processus consolide un matériau semi-fini en un stratifié, qui est ensuite chauffé, remodelé et surmoulé à l'aide d'un composé de moulage par injection. Un avantage majeur de ce procédé est qu'il permet le recyclage; les déchets peuvent être retraités et utilisés dans le composé de moulage par injection. Il est également possible d'intégrer des éléments de rigidification et de réaliser des composants complexes tels que des intérieurs d'avions ou des carénages.
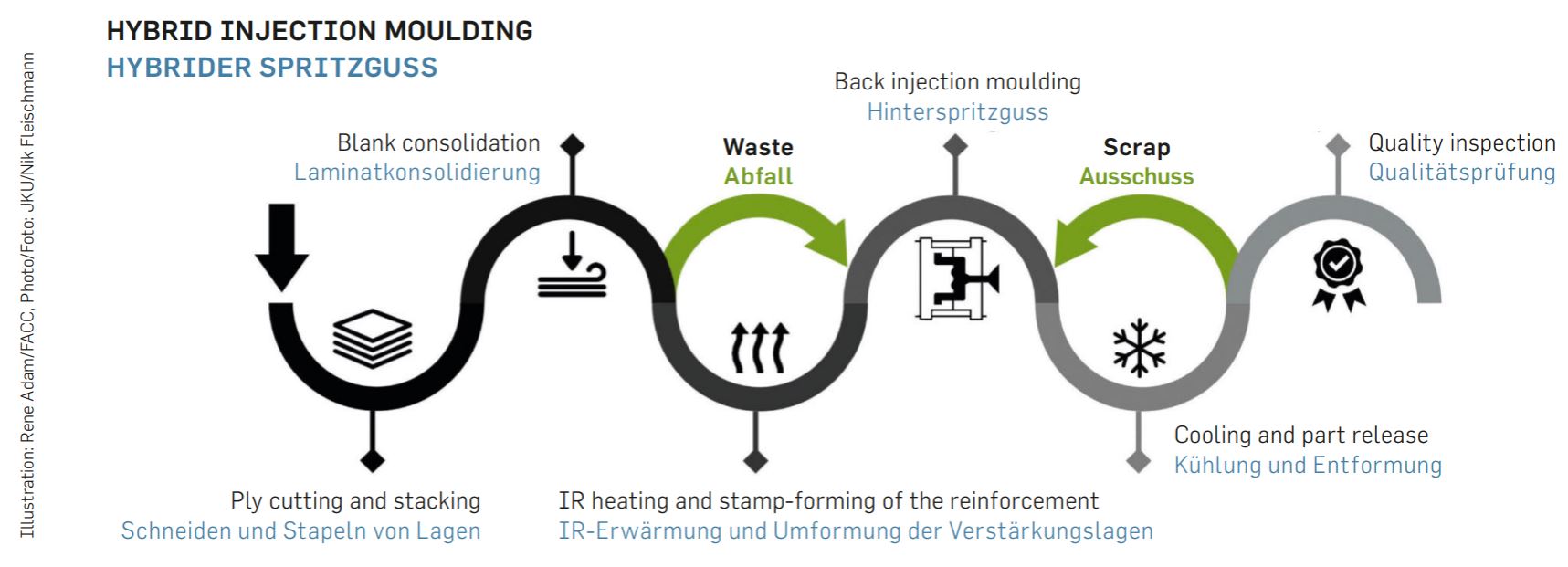
Préimprégnés à durcissement rapide offrent un potentiel énorme pour réduire jusqu'à 90 % le temps de durcissement des composites pendant la production. Cela permet même des pièces fabriquées avec thermoset résines à produire en quelques minutes, en utilisant un processus robuste et économe en énergie. FACC rapporte que les préimprégnés à durcissement rapide sont plus simples à travailler que les matériaux composites thermoplastiques. L'entreprise considère également ces matériaux comme une voie vers une meilleure durabilité, car les résines nécessaires pour les produits d'intérieur, par exemple, peuvent être fabriquées à partir de matières premières renouvelables à base de canne à sucre, de bambou ou d'algues.
Résine
- Composites TPE ultra-légers pour chaussures
- RS Electric Boats sélectionne Norco pour la fabrication de composites
- Thermocouple haute température PEEKSense pour le durcissement des composites PEEK
- Film à base d'époxy Solvay pour préimprégnés
- Hexion reçoit l'approbation pour le financement DIP
- Solvay composites sélectionnés pour catamaran de course
- Teijin fournira des thermoplastiques renforcés de fibres de carbone pour Boeing
- Porte thermoplastique une première pour les composites automobiles
- Aperçu CAMX 2018 :PolyOne Advanced Composites