Personnalisation des capteurs à ultrasons pour l'optimisation et le contrôle des processus composites
Ce blog fait suite à mon reportage sur le projet CosiMo (« composites pour une mobilité durable »). Ce projet a été lancé en 2018 par Faurecia Clean Mobility (Nanterre, France) pour démontrer la « fabrication intelligente » d'un couvercle de boîtier de batterie en composite. La partie défi de 1 100 millimètres de long et de 530 millimètres de large comportait des renforts en fibre de verre non tissée et en fibre de carbone unidirectionnelle ainsi que des inserts en métal et en mousse, une géométrie complexe comprenant divers rayons et épaisseurs variant de 2,5 à 10 millimètres. La pièce a été moulée à l'aide d'un moulage par transfert de résine thermoplastique (T-RTM), où le monomère de caprolactame a été injecté puis polymérisé in situ pendant le cycle de pressage chauffé pour former un composite polyamide 6 (PA6). L'objectif principal du projet était d'étudier un processus entièrement automatisé utilisant un contrôle de processus en boucle fermée basé sur des capteurs.
Ce blog explore plus en détail le réseau de 74 capteurs utilisés dans la partie challenge CosiMo, et en particulier les capteurs à ultrasons développés par l'Université d'Augsbourg (UNA, Augsbourg, Allemagne) et comment les données de tous les capteurs ont été utilisées pour construire un modèle numérique du processus (jumeau numérique).
Sur la base du succès de CosiMo et du besoin d'un centre de développement pour le développement de la fabrication basée sur des capteurs et l'IA, UNA a formé le réseau de production d'IA d'Augsbourg, en collaboration avec le partenaire du projet CosiMo German Aerospace Center (DLR) Center of Lightweight Production Technologies ( ZLP, Augsbourg) et l'Institut Fraunhofer pour la technologie de fonderie, de composites et de traitement (Fraunhofer IGCV). "Nous mettons en place une nouvelle installation de 5 000 mètres carrés que nous exploiterons en collaboration", a déclaré le Dr Markus Sause, professeur à l'UNA et directeur du réseau de production d'IA d'Augsbourg. « Nous aurons des cellules de production automatisées, dont beaucoup sont axées sur les technologies des composites, ce qui nous permettra de démontrer ce que l'IA peut faire. »
Réseau de capteurs CosiMo
Pour le projet CosiMo, 74 capteurs ont été intégrés dans l'outillage RTM en acier fourni par Christian Karl Siebenwurst GmbH &Co. KG (Dietfurt, Allemagne) pour le moulage du couvercle du boîtier de batterie T-RTM. Utilisé pour surveiller les paramètres du procédé lors de l'injection de résine, de l'infiltration (surveillance du front d'écoulement) et de la polymérisation in situ, ce réseau comprenait :
- 1 capteur de vide
- 4 capteurs de pression/température de Kistler (Winterthur, Suisse)
- 4 capteurs de température par Kistler
- 8 analyses diélectriques (DEA)/capteurs de température par Netzsch (Selb, Allemagne)
- 57 capteurs à ultrasons développés par l'université d'Augsbourg.
Dans mon rapport initial sur CosiMo, j'ai expliqué en quoi ce réseau de capteurs était destiné à la R&D et non à la production standard :
"Pour la production industrielle en série, personne n'installerait autant de capteurs et ce n'est pas ce à quoi nous nous attendions", déclare Jan Faber, chef de projet de fabrication CosiMo chez DLR ZLP. « Mais pour cette enquête de recherche, ce grand réseau de capteurs était très précis et nous a aidés à avoir une visibilité totale sur le processus et comportement matériel . Nous avons pu voir les effets locaux dans le processus en réponse aux variations d'épaisseur des pièces ou des matériaux intégrés, comme l'âme en mousse. »
Alors, comment ce réseau a-t-il été conçu ? « La plupart étaient des capteurs à ultrasons, car ils ont le coût le plus bas », explique Faber. « Nous les avons utilisés dans une grille à une distance définie les uns des autres. À certains endroits, nous avons retiré les capteurs à ultrasons et mis en place des capteurs de température/pression Kistler ou Netzsch DEA/température. Et pour ces capteurs spécifiques, à la fois le DEA et le Kistler, nous avons juste essayé d'en avoir un près de la carotte, là où la résine est entrée, puis un loin. Ainsi, nous avons pu surveiller les endroits où arrive la résine après avoir vu la température du moule depuis un certain temps déjà. »
Pourquoi utiliser différents types de capteurs ? « Une tâche de recherche consistait à comparer les signaux et à voir comment les différents capteurs fonctionnent », explique Faber. Ceci est important car les différents types de capteurs sont basés sur des principes de mesure différents. Par exemple, les capteurs DEA mesurent l'impédance CA de la résine, qui peut être divisée en différentes fractions, qui à leur tour montrent des effets différents dans le polymère. Kistler, quant à lui, utilise des capteurs piézorésistifs qui reposent sur un pont de Wheatstone à base de silicium - un type de circuit utilisé pour mesurer la résistance électrique dynamique - connecté à une membrane qui forme l'extrémité de détection installée dans la paroi de la cavité de moulage. La membrane s'étend sous pression, ce qui modifie la résistance électrique du pont de Wheatstone en silicium, qui à son tour émet un signal électrique. « Nous avons également utilisé le nouveau capteur 4001a de Kistler qui mesure à la fois la pression et la température », note Faber. "C'était très utile d'avoir les deux valeurs pour certains points locaux dans l'outil."
Capteurs à ultrasons UNA
La majorité des capteurs utilisés dans le réseau de pièces CosiMo étaient des capteurs à ultrasons développés par UNA. Sause note que ceux-ci ont été privilégiés non seulement en raison de leur faible coût (<10 euros) mais aussi parce qu'ils peuvent fournir un large éventail d'informations.
Les capteurs à ultrasons sont utilisés depuis des décennies pour inspecter les pièces composites finies, mais ont également une longue histoire dans le moulage par injection. Des capteurs à ultrasons envoient une onde sonore à haute fréquence dans un milieu et mesurent sa réflexion (écho d'impulsion) et/ou sa transmission. Dans le projet CosiMo, la fréquence nominale était de 2 000 kilohertz. Sur les 57 capteurs à ultrasons installés dans le moule — à une distance de 20 millimètres de la surface de la cavité — 10 fonctionnaient en mode transmission et le reste en mode impulsion-écho. Des capteurs à ultrasons mesurent la vitesse de l'onde et sa diminution d'amplitude (atténuation) ; les deux sont sensibles aux propriétés du polymère. De plus, la vitesse des ondes peut être calculée en fonction de la pression et de la température, mais les données ultrasonores doivent être calibrées en fonction du polymère étudié.
« Le capteur à ultrasons que nous avons développé n'est en fait pas très différent de ce qui est disponible dans le commerce », explique Sause. « Il est basé sur un matériau piézoélectrique, qui est assez sensible pour convertir un mouvement élastique en un signal électrique. Mais là où les capteurs typiques peuvent fonctionner à des températures allant jusqu'à 150 °C, nous devions égaler les températures élevées du moulage thermoplastique à plus de 200 °C, ce qui était un peu difficile pour l'électronique du capteur. »
« Nous avons également dû concevoir le système mécanique permettant d'intégrer correctement le capteur dans le moule », explique-t-il, « ce qui nécessitait une sollicitation du ressort avec une bonne étanchéité pour fournir un bon couplage. Le capteur devait répondre à un large éventail d'exigences ; nous avons donc dû le concevoir à partir de zéro. Nous avons également réalisé une conception acoustique appropriée de l'ensemble du système. »
Polymérisation et surveillance du front d'écoulement
« L'acoustique se concentre sur les propriétés élastiques des matériaux dans le moule », poursuit Sause. « Fondamentalement, la rigidité dans un liquide n'est pas la même que lorsque la polymérisation est terminée. Nous surveillons efficacement cette transition. Nous examinons l'intensité acoustique de la réflexion des ondes à l'interface du moule au matériau polymère à chaque emplacement du capteur, et suivons ainsi en continu le durcissement au fil du temps. »
La mécanique de cette mesure est expliquée par Sause et Faber, et. al., dans le document de conférence SAMPE Europe 2021, « Sensor-based process monitoring of in-situ polymerization in T-RTM manufacturing with caprolactame ». Le rapport de l'amplitude de l'écho du signal acoustique avant et après l'imprégnation de la préforme dépend de l'indice de réflexion à l'interface moule-pièce, R. Il se rapproche d'une valeur constante au fur et à mesure que la polymérisation progresse. Idéalement, une fois la polymérisation presque terminée, le changement de R sera nul.
Il est également possible, à partir du signal de transmission acoustique, d'extraire le temps de parcours des ondes ultrasonores pour traverser la préforme imprégnée. Ceci est utile car la vitesse du son à travers la préforme est liée au degré de polymérisation. Pour l'expérimentation achevée au moment de l'article SAMPE Europe 2021, le temps entre le mouillage complet de la préforme à l'emplacement du capteur et la fin de la polymérisation était de 240 secondes.
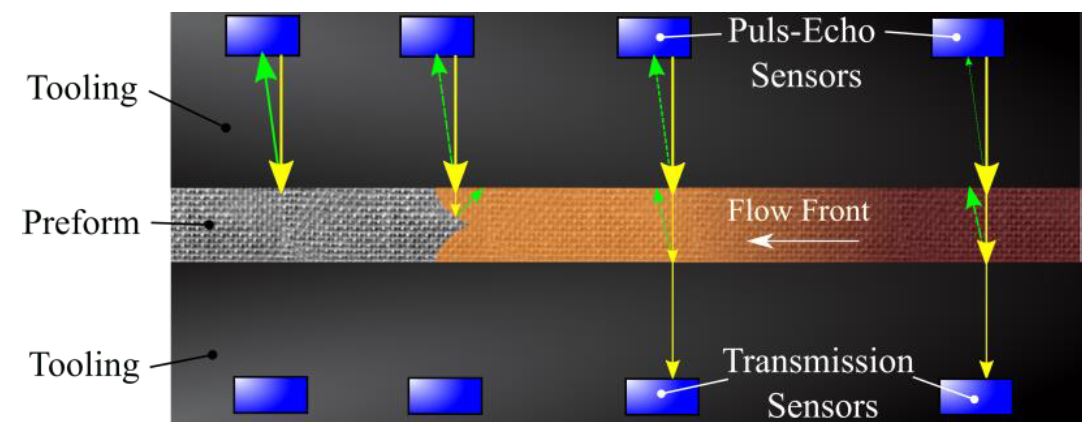
« Nous pouvons également surveiller le débit pendant l'injection », explique Sause, « car les informations du signal acoustique changent lorsque le front d'écoulement du polymère passe devant le capteur ». Également vérifié dans l'article SAMPE Europe 2021, le signal acoustique a chuté brusquement d'une valeur normalisée initiale de 1 à entre 0,85 et 0,9 à l'arrivée du front d'écoulement du caprolactame pour le capteur sélectionné 15 secondes après le début de l'injection.
Développer un jumeau numérique du processus
Sause dit que le développement du capteur à ultrasons était en fait une très petite partie de ce que UNA a fait dans le projet CosiMo, "et même pas la partie la plus fascinante". La véritable réussite, note-t-il, réside dans l'analyse des données et le développement d'un modèle numérique du processus pour permettre un contrôle en boucle fermée pendant la fabrication des pièces.
"Ce que nous essayons de faire, c'est de fournir des informations sur ce qui se passe réellement dans le moule", ajoute-t-il. « Nous avons établi des itinéraires pour adapter le processus à la température et à la pression, plus ou moins, mais ce que nous faisons maintenant, c'est exploiter les informations du signal acoustique en effectuant une impulsion active à chaque emplacement de capteur. Et cela nous permet de déterminer diverses choses telles que la forme du front d'écoulement, le temps nécessaire pour qu'il atteigne chaque partie de la préforme et le degré de polymérisation à chaque emplacement du capteur. »
« Idéalement, vous pouvez définir des paramètres pour activer le contrôle en boucle fermée et les ajuster au cours du processus », explique Sause. « Ceux-ci incluraient des paramètres tels que la pression d'injection et la pression et la température du moule. Vous pouvez également utiliser ces informations pour optimiser vos matériaux. »
Le développement du jumeau numérique a été un effort en plusieurs étapes et en plusieurs partenaires. Tout a commencé avec l'un des lots de travaux affectés au DLR ZLP. « Nous avons mis en place une simulation basée sur une plaque 2D, où nous voulions simuler le remplissage et la polymérisation à l'aide du logiciel de simulation PAM-RTM d'ESI Group (Rungis, France) », explique Faber. « Nous avons obtenu les données de perméabilité des préformes des partenaires du projet ITA (Institute for Textile Technology, RWTH Aachen, Allemagne) et SGL Carbon (Wiesbaden, Allemagne) ainsi qu'un modèle réactif de la réaction du polymère thermoplastique de l'Université d'Augsbourg. Nous avons ensuite tout intégré à la simulation et essayé de voir à quel point nous pouvions nous rapprocher des données réelles des capteurs. »
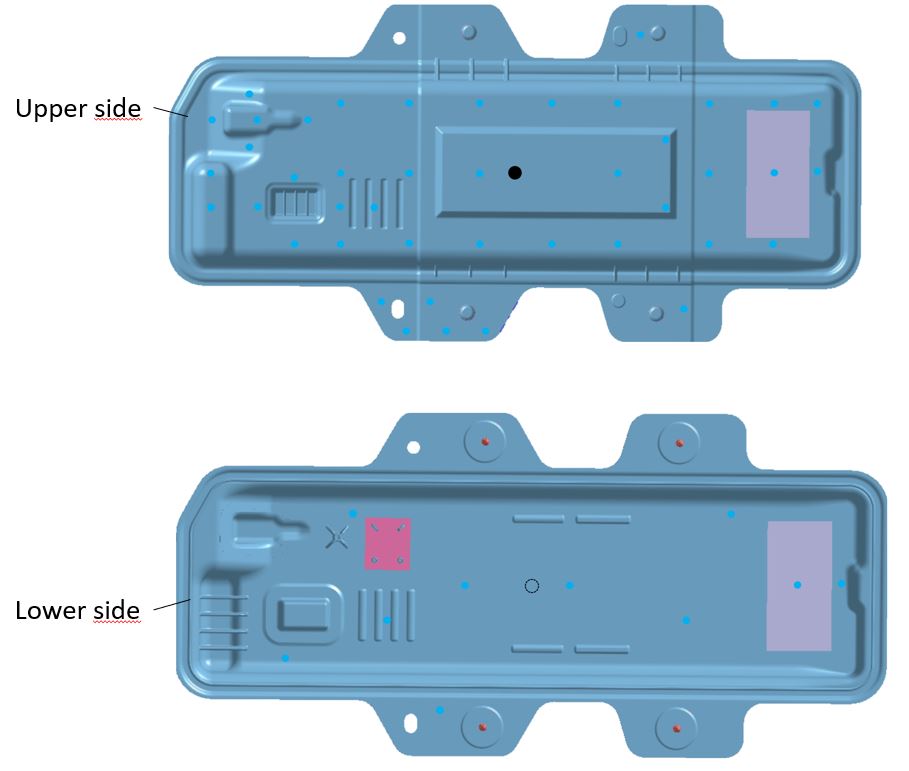
Les points bleu clair dans les moules supérieur et inférieur de la partie démonstratrice du projet CosiMo ont fourni des données à des points spécifiques tout au long du processus. Cela a ensuite été utilisé dans la simulation de jumeaux numériques pour interpoler entre les emplacements des capteurs et modéliser le processus à travers la pièce. Crédit photo :projet CosiMo, DLR ZLP Augsburg, Université d'Augsbourg
« Nous avons découvert, sur la base du modèle de plaque 2D, que nous sommes en fait très proches en ce qui concerne le remplissage », poursuit Faber. « Mais nous avons eu des effets de température pendant la polymérisation que nous n'avons pas pu décrire dans la simulation. Par exemple, cette réaction de polymérisation est exothermique, et vous voyez une légère augmentation au niveau des capteurs de température dans les données réelles, mais l'augmentation dans la simulation était beaucoup plus élevée. C'est donc un domaine dans lequel nous avons continué à travailler. »
L'une des choses que l'équipe voulait découvrir à partir de la simulation était le temps nécessaire pour que la polymérisation soit complète. « Ce que nous voulions vraiment, c'était le temps minimum dont nous avions besoin dans le moule », note Faber. Ces informations étaient dérivées du modèle de simulation et reposaient, comme toute la simulation, sur plusieurs types de capteurs et d'algorithmes d'IA. Par exemple, Netzsch a fourni les capteurs diélectriques utilisés pour l'analyse diélectrique, mais a également aidé avec certaines parties du jumeau numérique du processus. "Ils ont mis en place des modèles d'IA prédictifs pour étudier les mécanismes à l'intérieur de l'injection et pour prédire à quel moment la polymérisation devrait être terminée et quel serait l'état de polymérisation", explique Faber.
(Remarque, Netzsch a combiné ses compétences dans la caractérisation des matériaux, la simulation cinétique et la technologie des capteurs pour établir de nouvelles offres dans les solutions d'IA et de cloud. Ce type de solution intégrée a été démontré avec succès dans CosiMo pour fournir une évaluation en temps réel du degré de polymérisation et sera commercialisé sous la marque sensXPERT.)
A partir du réseau complet de capteurs et de simulation, il a été constaté que 96% était la polymérisation maximale atteinte et cela a nécessité 4,5 minutes. « C'est donc beaucoup plus rapide que les processus d'infusion, mais beaucoup plus lent que l'injection à grande vitesse utilisant des thermodurcissables, par exemple. »
« Les données du capteur s'intègrent dans le modèle de jumeau numérique », explique Sause. « L'idée était d'avoir un modèle fonctionnant en même temps que le processus qui est numériquement stabilisé par les informations du capteur. Les points bleus fournissent une grille grossière de capteurs à ultrasons, puis nous avons pu interpoler entre ces points. Par exemple, nous avons pu fournir une vidéo de l'évolution du front d'écoulement dans la partie CosiMo en fonction du temps sur la base des données de mesure de nos capteurs. »
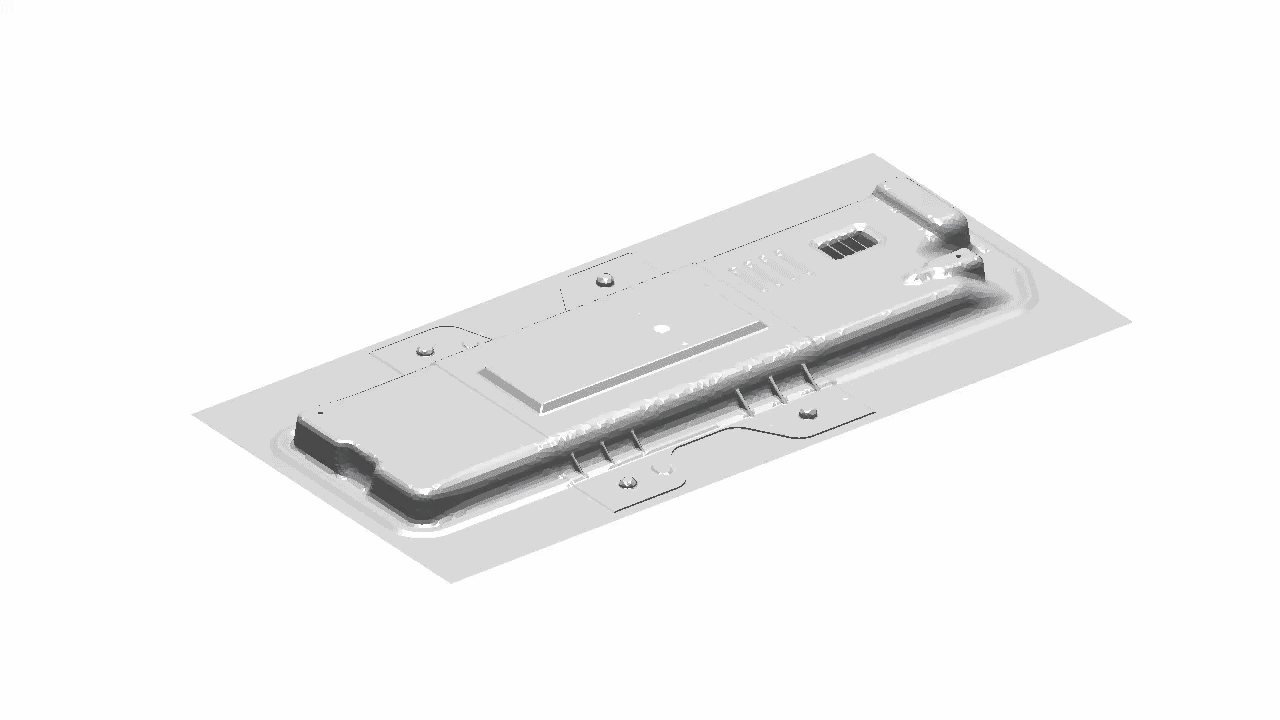
Comment les prédictions de vitesse de polymérisation ont-elles été validées ? «Nous avons eu plusieurs approches», explique Sause. « Tout d'abord, un étudiant en doctorat ici à l'UNA effectuait un ensemble complet de modélisation de la cinétique de réaction du système de matériaux caprolactame-to-PA6. Ainsi, il étudiait simultanément la spectroscopie infrarouge avec les données rhéométriques et les données des capteurs d'analyse diélectrique pour fournir un modèle de matériau très précis pour la cinétique de durcissement de ce système et pour valider ce modèle. Nous avons donc utilisé le même modèle pour valider croisées nos capteurs. »
Architecture du jumeau numérique
L'architecture du fonctionnement du jumeau numérique est décrite par Stieber, et. Al. dans le document technique de 2020, « Vers une surveillance des processus en temps réel et un apprentissage automatique pour la fabrication de structures composites » :
Il se compose de trois parties :la machinerie T-RTM, les capteurs in-situ dans l'outillage du moule et le jumeau numérique. Cette structure et le jumeau numérique, en particulier, ont été développés avec les objectifs O1 à O4 suivants :
- O1 :Surveillez le processus de fabrication de chaque pièce composite avec les capteurs in-situ de l'outillage.
- O2 :visualisez chaque processus de fabrication en temps réel pour obtenir des informations supplémentaires sur les processus.
- O3 :entraîner des modèles de ML sur des données simulées et réelles pour prédire le résultat du processus de fabrication.
- O4 :Utilisez des modèles de ML entraînés pour réduire les rejets de production.
Les capteurs alimentent ensuite les données d'analyse de bord du jumeau numérique, qui peuvent ensuite être utilisées pour prédire la future dynamique du front d'écoulement, déterminer le contenu en volume de fibres de chaque préforme textile, prédire les points secs et détecter les anomalies qui peuvent réduire les pièces rejetées.
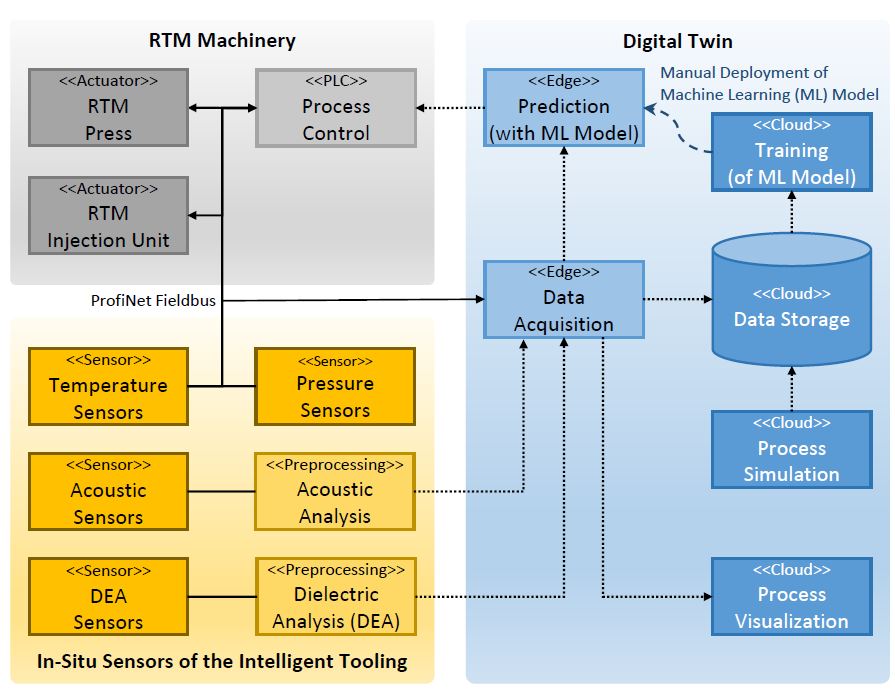
La machinerie T-RTM comprend deux composants standard :une presse à chaud Wickert (Landau in der Pfalz, Allemagne) de 440 kilonewtons et une unité d'injection T-RTM de KrausMaffei (Munich, Allemagne). Ces deux machines ainsi que l'ensemble du réseau de capteurs sont connectés à un API (contrôleur logique programmé) qui est chargé de contrôler l'ensemble du processus de fabrication.
Étant donné que les capteurs ont besoin d'un prétraitement en temps réel pour transformer les données brutes en informations de niveau supérieur sur le front d'écoulement ou le durcissement de la résine, les données prétraitées sont enregistrées directement au bord à l'aide d'une unité d'acquisition de données ibaPDA d'iba AG ( Fürth, Allemagne). Ainsi, les données du capteur sont enregistrées et fusionnées avec un horodatage cohérent lié aux données de processus et aux informations sur les pièces avec les données du capteur par objectifs O1 et O2.
Pour optimiser automatiquement le processus de fabrication, les données stockées sont utilisées pour former des modèles d'apprentissage automatique (ML) pour répondre à l'objectif O3. Ces modèles sont chargés, par exemple, de reconstruire le front d'écoulement de la résine à partir du réseau de capteurs, de prédire la progression du front d'écoulement et, idéalement, d'adapter les paramètres du procédé pour optimiser le résultat soit au cours d'une instance de procédé, soit pour les exécutions suivantes. . Étant donné que les données réelles ne sont généralement pas suffisantes pour former des modèles fiables, l'équipe des jumeaux numériques a utilisé des simulations PAM-RTM pour augmenter les données mesurées. Après une pré-formation à l'aide de données simulées, le jumeau numérique a été affiné avec des données du monde réel. Cette stratégie est connue sous le nom d'apprentissage par transfert et a été adoptée avec succès dans les applications de vision par ordinateur et de traitement du langage naturel. Les analyses avancées possibles avec le ML permettent des capacités de prédiction et une visualisation des processus accrues ainsi qu'un contrôle en boucle fermée.
Intégration de capteurs pour la production de composites industriels
Alors, comment les fabricants de pièces composites appliquent-ils cette technologie pour développer un contrôle en boucle fermée dans leurs propres processus de production ? Sause dit qu'il est logique d'utiliser plusieurs types de capteurs pour valider le flux et la surveillance du durcissement/polymérisation et pour fournir des informations complémentaires. Ensuite, il s'agit de définir l'emplacement des capteurs, y compris les types qui sont placés à chaque emplacement. "Par exemple", note-t-il, "vous n'avez pas besoin de capteurs de pression et de température partout, mais juste là où vous avez besoin de ces points de données clés, tels que l'entrée de la résine, les points de géométrie complexe, etc."
Combien de capteurs ? "Pour CosiMo, nous avons utilisé 74 capteurs, mais pour une pièce d'un demi-mètre, vous en utiliseriez moins, peut-être 35-40 selon votre géométrie et vos points d'intérêt clés", explique Sause. « Cela dépend aussi du processus de production. Il existe des procédés dans l'aérospatiale, par exemple, qui sont utilisés depuis des décennies et qui sont bien établis. Pour ceux-ci, vous n'aurez peut-être pas besoin de beaucoup de capteurs et il pourrait être possible de les intégrer sans trop de travail de développement au début. Mais d'autres processus sont plus inconnus et nécessiteront plus de travail en amont. Pour CosiMo, nous cherchions à utiliser le T-RTM avec une polymérisation in-situ au PA6, et ce n'était pas aussi bien documenté que le RTM avec de l'époxy, par exemple. »
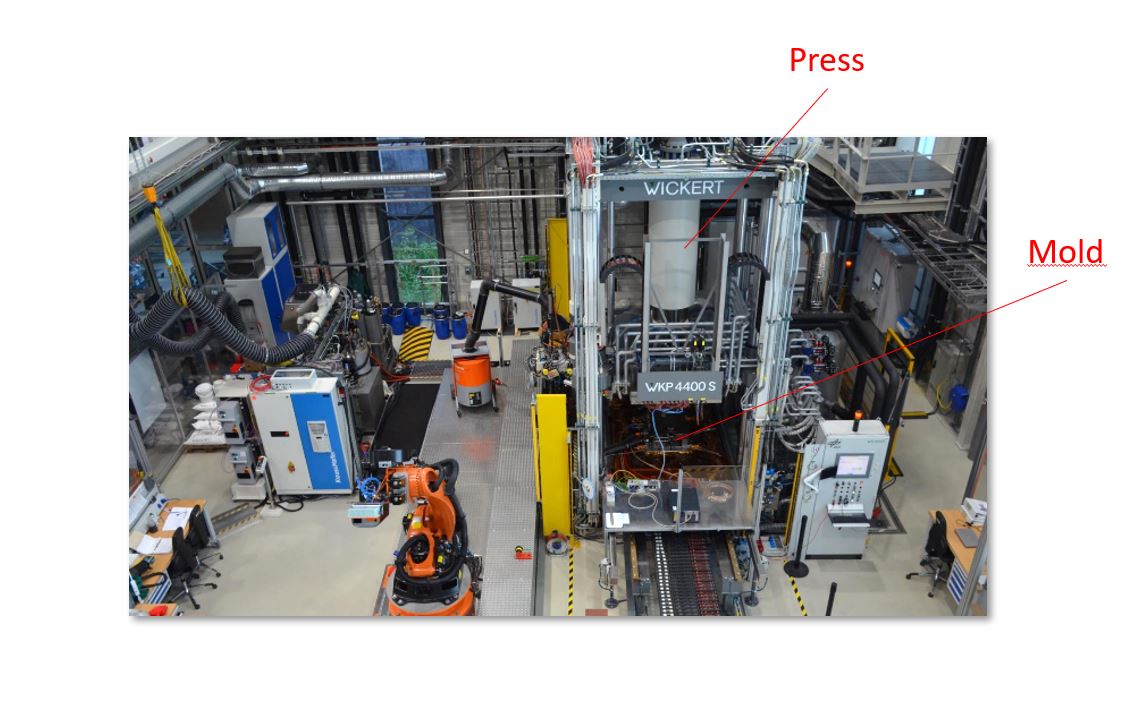
L'équipement de fabrication du projet CosiMo comprenait une presse Wickert de 440 kN et une machine d'injection KraussMaffei. Crédit photo pour cette série :projet CosiMo, DLR ZLP Augsburg, University of Augsburg
Combien de temps prend la construction d'un modèle numérique ? Et est-ce toujours nécessaire pour obtenir un contrôle en boucle fermée ? «Encore une fois, cela dépend de votre processus et du niveau que vous souhaitez atteindre», explique Sause. « Tout d'abord, l'intégration des informations du capteur vous permet de visualiser ce qui se passe à l'intérieur de votre boîte noire de traitement et les paramètres à utiliser.
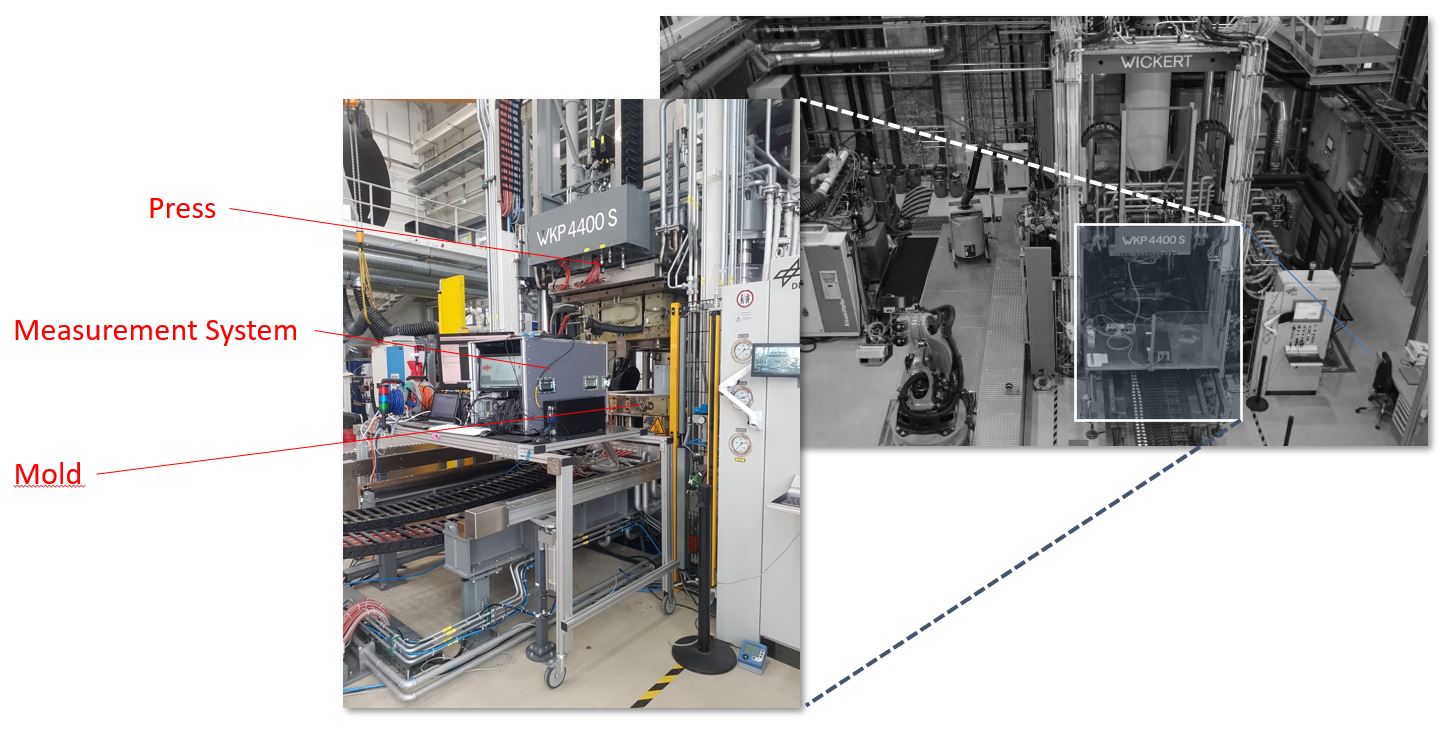
Le système de contrôle en boucle fermée développé dans CosiMo a également intégré des capteurs dans le moule et un système d'acquisition de données (système de mesure illustré ici) par iba AG.
Une fois ce premier objectif atteint, il ne reste plus que quelques étapes pour parvenir à un contrôle de processus en boucle fermée. À mi-chemin, peut-être, est d'avoir la visualisation et vous pouvez appuyer sur le bouton d'arrêt par vous-même afin d'adapter le processus et d'éviter le rejet de pièces. C'est donc aussi un début. Et puis vous pouvez développer le jumeau numérique, mais il a besoin de données d'entraînement. Donc, vous devez fournir cela d'une manière ou d'une autre, ce qui signifie que vous pouvez produire quelques pièces à utiliser comme données d'entrée. Mais alors, il faut aussi produire des pièces de mauvaise qualité. Il s'agit donc de votre volonté d'investir dans la formation de votre approche d'apprentissage automatique. »
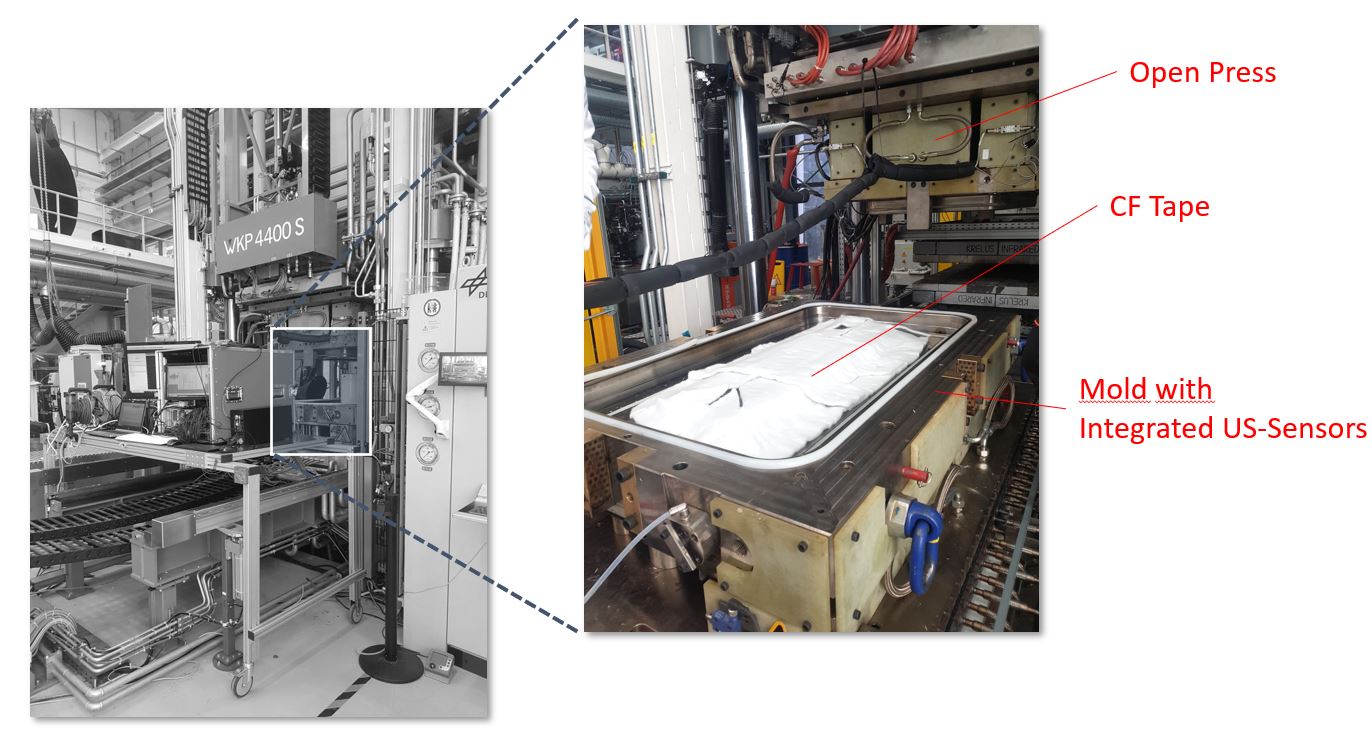
Une fois entraîné, le jumeau numérique peut optimiser les paramètres de processus et fournir un contrôle de processus en boucle fermée.
Cependant, Sause reconnaît que l'approche d'apprentissage par transfert adoptée dans CosiMo « est transférable dans une certaine mesure à des géométries ou des systèmes matériels similaires et à d'autres variations qui ne changent pas complètement la situation. Ainsi, vous pouvez constituer votre base de données de cette manière, avec la possibilité d'identifier les tendances d'efficacité à partir des données déjà acquises. Vous pouvez ensuite l'utiliser pour d'autres questions que vous pourriez avoir à côté. »
Donc, la façon de commencer semble être la suivante :commencez à utiliser des capteurs et à créer des modèles numériques pour accompagner les capteurs afin que vous puissiez comprendre votre processus ? "Absolument", dit Sause. « Et je peux vous assurer que la plupart des machines utilisées dans la production aujourd'hui sont encore très stupides. De nombreuses machines n'ont pas de capteurs qui peuvent vous donner les bases de données pour fournir des informations sur ce qui se passe. Alors, oui, l'intégration de systèmes de capteurs serait la toute première étape. Mais vous devez faire un systématique acquisition de données, et également fournir une architecture de stockage de données, pour pouvoir faire quelque chose avec les données . En fait, de nombreuses entreprises ont intégré des capteurs, mais elles ne font rien avec les données. »
Réseau de production d'IA
En répondant aux questions ci-dessus, Sause n'a cessé de revenir vers divers groupes au sein de l'UNA ainsi que des entreprises dérivées qui peuvent fournir des services d'intégration de capteurs et de jumeaux numériques. À cette fin, le réseau de production d'IA d'Augsbourg a été lancé en janvier 2021 par UNA, DLR ZLP et Fraunhofer IGCV. « Le cadre de collaboration provient de projets que nous avons eus avec DLR et Fraunhofer dans le passé », explique Sause. « Nous prenons le modèle de développement de la production basé sur l'IA de CosiMo et l'étendons maintenant à une très large échelle. Ainsi, par exemple, le budget de notre travail dans CosiMo était de 10 millions d'euros, mais pour l'AI Production Network c'est 92 millions d'euros comme financement initial. Cela nous donnera la possibilité de lancer de nombreux nouveaux projets de recherche comme CosiMo dans l'exploitation de l'IA dans la fabrication. Et nous ne travaillons pas uniquement sur les composites, mais nous nous concentrons fortement sur eux. »
L'utilisation de capteurs à ultrasons pour améliorer l'usinage CNC est un projet déjà lancé en 2021. « Un projet est sur le point de démarrer sur le recyclage des composites à matrice céramique (CMC) », déclare Sause, « et nous aurons plusieurs projets avec un lien étroit entre la fabrication additive et la réutilisation de matériaux renforcés de fibres spécifiquement recyclés. »
Quant aux rôles que chaque organisation jouera, Sause explique qu'il n'y a pas de concurrence, car chaque institution dispose d'un budget alloué. « Nous avons tous notre part et sommes donc libres de collaborer comme nous l'avons fait par le passé. De plus, nous nous connaissons assez bien ainsi que nos compétences, nos forces et nos faiblesses. C'est amusant de travailler ensemble parce que nous savons ce que nous pouvons et ne pouvons pas faire. Nous avons été approchés par de nombreuses entreprises qui souhaitent travailler avec nous et nous discutons maintenant de la manière de trouver la correspondance idéale de notre côté des compétences. »
Concernant le site de production de 5 000 mètres carrés, « nous allons tous gérer cela ensemble », déclare Sause. « Nous prévoyons d'ouvrir d'ici début 2023 et de commencer à installer des machines. Et nous fournirons des paramètres de production automatisés qui relient les cellules individuelles. Beaucoup d'entre eux se concentreront sur les technologies de production de composites. Et nous le ferons également pour présenter et démontrer aux partenaires de l'industrie ce que l'IA peut faire dans un tel cadre de production. Nous souhaitons également que des partenaires de l'industrie viennent et placent également des machines dans nos installations afin que nous puissions exécuter des projets ensemble pour voir comment lier et intégrer de nouvelles solutions pour leurs sites. »
Résine
- Vannes pour fermeture et contrôle difficiles
- Capteurs et systèmes pour CBM
- Ingénierie des procédés de revêtement par immersion et optimisation des performances pour les appareils électrochromes à trois états
- OTOMcomposite développe un logiciel pour la production de Composites 4.0 utilisant le placement et le bobinage de bandes assistés par laser
- TPAC et TPRC développent un procédé de recyclage des composites thermoplastiques
- Conseils pour la configuration et le câblage des boîtiers du panneau de commande
- Qu'est-ce que l'usinage par ultrasons ? - Travail et processus
- Connexions pour le contrôle :interfaces de communication pour les capteurs de position et de mouvement
- Collecte des données de terrain pour l'optimisation des processus