Simulation de dynamique moléculaire sur le mécanisme de coupe dans le processus d'usinage hybride du silicium monocristallin
Résumé
Dans cet article, des simulations de dynamique moléculaire sont effectuées pour étudier le mécanisme de coupe au cours du processus d'usinage hybride combiné aux assistants thermiques et vibratoires. Un modèle de coupe modifié est appliqué pour étudier le comportement d'enlèvement de matière et la formation de dommages sous la surface au cours d'un cycle de vibration. Les résultats indiquent que pendant le processus d'usinage hybride, le mécanisme d'enlèvement de matière dominant pourrait passer de l'extrusion au cisaillement en un seul cycle de vibration. Avec une augmentation de la température de coupe, la génération et la propagation de fissures sont efficacement supprimées tandis que le gonflement apparaît lorsque le mécanisme d'enlèvement de matière dominant devient le cisaillement. Le mécanisme de formation des dommages souterrains dans un cycle de vibration peut être distinct selon la distribution des contraintes. De plus, la génération des lacunes dans la pièce devient apparente avec l'augmentation de la température, ce qui est un phénomène important dans le processus d'usinage hybride.
Introduction
Le silicium monocristallin est un matériau semi-conducteur important, qui a été largement utilisé dans les systèmes optiques infrarouges, microélectroniques et optoélectroniques en raison de ses excellentes propriétés optiques et mécaniques [1, 2]. Cependant, en raison de la nature de la dureté et de la fragilité du silicium monocristallin, une rupture fragile microscopique et des dommages souterrains peuvent être générés pendant l'usinage mécanique. Au cours du processus de micro-fraisage, des défauts d'écaillage des bords de type intérieur induits par l'usinage peuvent être générés dans la pièce [3]. Dans l'usinage de coupe au diamant monocristallin (SPDT), une couche endommagée allant de 200 à 600 nm peut être formée en fonction des paramètres de traitement [4, 5]. Bien que la couche de dommages sous la surface puisse être réduite à environ 50 nm par meulage et polissage. L'efficacité d'usinage et la capacité à fabriquer des structures complexes sont limitées. Pour surmonter ces problèmes, diverses technologies d'usinage d'assistance ont été proposées et testées. En particulier, la découpe assistée thermiquement (TAC) [6] et la découpe assistée par vibration (VAC) [7] ont attiré une large attention en raison de leurs performances de découpe extraordinaires.
Pour les matériaux fragiles comme le silicium monocristallin, la transition fragile à ductile peut être favorisée lorsque la température d'usinage est augmentée. Au cours du processus TAC, la pièce de silicium est ramollie thermiquement, ce qui entraîne la diminution des forces de coupe [8] et de l'énergie de coupe spécifique [9, 10]. Pendant ce temps, le recuit des phases à haute pression en phase de silicium cubique devient apparent lorsque la température d'usinage est augmentée [11]. Avec une sélection appropriée des paramètres d'usinage, la surface usinée souhaitée avec une pureté de phase élevée et un faible endommagement de la sous-surface peut être obtenue par TAC [12,13,14]. En plus du TAC, la découpe assistée par vibration (VAC) est une autre méthode de promotion pour obtenir une surface de haute qualité sur du silicium monocristallin. Cette technique est appliquée dans l'industrie manufacturière depuis les années 1960 [15]. Au début du développement de cette technologie, seul un mouvement de vibration linéaire dans la direction de coupe nominale est pratiqué dans l'usinage, qui est appelé coupe à vibration linéaire (LVC). En 1994, le découpage vibratoire elliptique (EVC) a été proposé par Shamoto et Moriwaki [16]. Comme suit, les faisabilités d'usinage de l'EVC sur de nombreux matériaux fragiles comme le silicium [17, 18], le carbure de silicium lié par réaction [7], le carbure de tungstène [19, 20] et l'acier durci [21] ont été vérifiées. Pendant le processus EVC, les dommages souterrains peuvent être efficacement supprimés puisque la profondeur de coupe transitoire (DOC) est beaucoup plus petite que la DOC nominale [22]. En outre, en raison de la séparation dans chaque cycle de vibration, les surfaces de contact entre l'outil de coupe et la pièce sont exposées au gaz ou au fluide environnant, ce qui dissipe la chaleur de coupe générée. Par conséquent, l'usure de l'outil de coupe comme l'adhérence et la réaction thermochimique [23] peut être efficacement supprimée.
Pour améliorer encore l'usinabilité des matériaux fragiles, des expériences d'usinage hybride (HM) combinant l'assistant thermique et vibratoire ont été menées [24, 25]. Il a été constaté que lors de la coupe de l'Inconel 718 par la méthode HM, la rugosité de la surface usinée peut être efficacement réduite [26]. Grâce à des expériences et des simulations par la méthode des éléments finis (FEM), une baisse substantielle des forces de coupe et une qualité de surface supérieure des alliages de titane peuvent être obtenues pendant le processus HM [27]. Ces résultats démontrent la faisabilité de la méthode HM dans l'usinage de précision des matériaux fragiles. Cependant, il est difficile d'observer et de mesurer directement les variables physiques pendant le processus d'usinage car l'outil de coupe vibre à haute fréquence et la zone de déformation est à haute température. De plus, dans la fabrication de surfaces nanométriques, l'épaisseur transitoire d'enlèvement de matière varie généralement de quelques sous-nanomètres à quelques nanomètres. Par conséquent, la représentation continue traditionnelle du problème telle que FEM est discutable puisque les effets de la mécanique quantique deviennent apparents.
Ces dernières années, la simulation de la dynamique moléculaire (MD) a été largement appliquée dans les enquêtes sur le processus d'usinage assisté en raison de ses avantages dans l'étude du processus de coupe nanométrique [28,29,30]. Sur la base de simulations précédentes de TAC [31], lorsque la température de coupe augmente, l'anisotropie de la force de coupe, de l'énergie de coupe spécifique et de la contrainte élastique devient plus évidente. Pendant ce temps, la force de cisaillement dans la pièce est plus faible à une température de coupe plus élevée, ce qui conduit à des zones de cisaillement plus étroites et à des amplitudes plus élevées de l'angle du plan de cisaillement [32]. De plus, le taux d'enlèvement de matière peut être amélioré avec l'augmentation de la température de coupe car plus de copeaux se forment [33]. Pour le processus EVC, il a été découvert par simulation MD que la contrainte de compression et la contrainte de cisaillement dans la région de déformation peuvent être considérablement réduites par rapport à la coupe ordinaire [34], ce qui est avantageux pour la suppression des dommages souterrains. En outre, le processus EVC montre un amincissement évident des copeaux de coupe, entraînant une augmentation du rapport entre l'épaisseur des copeaux non coupés et l'épaisseur des copeaux coupés [35]. De plus, il a été découvert que les paramètres de vibration, y compris les rapports d'amplitude, les fréquences de vibration et les différences de phase, ont une grande influence sur les performances d'enlèvement de matière [34, 36].
Ces réalisations remarquables ont amélioré la compréhension du mécanisme d'usinage pour le processus d'usinage d'assistance. Cependant, afin d'économiser le temps de calcul et la mémoire, les systèmes de simulation sont généralement assez petits. Dans les simulations précédentes du processus EVC, les amplitudes de vibration et le DOC nominal sont inférieurs à 5 nm [22, 36]. Par conséquent, l'épaisseur d'enlèvement de matière transitoire est généralement inférieure à 1 nm, ce qui ne décrit pas avec précision le processus d'enlèvement de matière réel. De plus, les simulations MD du procédé HM n'ont pas été rapportées. Le mécanisme du processus d'enlèvement de matière et de la formation de dommages souterrains au cours du processus HM n'est toujours pas clair. Par conséquent, dans cet article, une simulation MD est effectuée pour révéler le mécanisme de coupe du processus HM. Le modèle de coupe classique est modifié pour que les paramètres de vibration soient beaucoup plus proches des valeurs expérimentales, par exemple, l'amplitude de vibration est agrandie à 40 nm avec une vitesse de coupe nominale de 3,125 m/s. Le mécanisme d'enlèvement de matière dans un cycle de vibration et l'influence de l'augmentation de la température de coupe sont étudiés. La simulation MD est réalisée par le célèbre Large-scale Atomic/Molecular Massively Parallel Simulator (LAMMPS) [37]. Le logiciel de post-traitement OVITO [38] est utilisé pour analyser les résultats de la simulation.
Méthode de simulation
Détails du modèle de coupe
La figure 1 montre le diagramme schématique du processus EVC, qui est initialement présenté par Shamoto et al. [39]. La trajectoire de l'outil peut être exprimée sous la forme :
$$x\left( t \right) =A_{{\text{c}}} \sin \left( {2\pi ft} \right) - vt$$ (1) $$z\left( t \ right) =A_{{\text{d}}} \sin \left( {2\pi ft + \varphi } \right)$$ (2)où x (t ) et z (t ) représentent le déplacement de l'outil de coupe dans le x et z directions. Un c et A d sont l'amplitude de vibration dans le sens de coupe nominal (x direction) et la direction nominale du DOC (z négatif direction). Paramètres f , v , φ , et t représentent respectivement la fréquence de vibration, la vitesse de coupe nominale, la différence de phase et le temps de simulation. Le temps de simulation t i représente l'heure du point P i sur la trajectoire de l'outil de la Fig. 1.
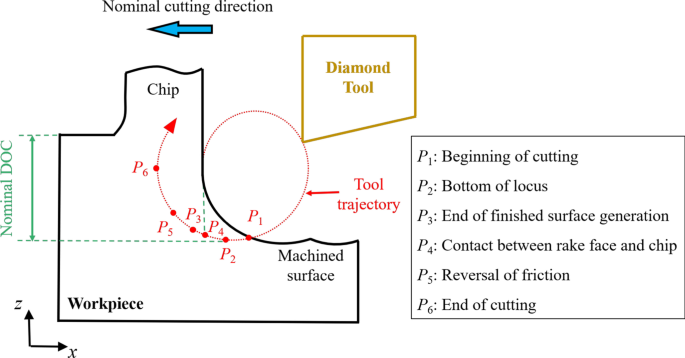
Le schéma de principe du processus EVC
D'après la relation géométrique [40], la valeur de t 1 et t 3 peut être déterminé par :
$$x\left( {t_{1} } \right){-}x\left( {t_{3} } \right) =2\pi v/\omega$$ (3) $$z\left( {t_{1} } \right){-}z\left( {t_{3} } \right) =0$$ (4)Ensuite, t 6 peut être obtenu lorsque la direction du mouvement transitoire de l'outil diamanté est parallèle à la face de coupe de l'outil :
$$\frac{{A_{{\text{c}}} \sin (2\pi ft_{6} ) + v}}{{A_{{\text{d}}} \sin (2\pi ft_ {6} + \varphi ) }} =\tan \gamma$$ (5)où γ est l'angle de coupe de l'outil de coupe diamanté.
Le modèle MD est présent sur la Fig. 2. La pièce en silicium monocristallin est définie comme un corps déformable. Alors que l'outil diamanté est considéré comme un corps rigide puisque l'usure de l'outil peut être négligée dans cette simulation. La morphologie de la pièce dans le modèle de coupe classique est remodelée en fonction de la trajectoire de l'outil dans le cycle de vibration précédent en tenant compte du rayon de l'arête de l'outil. La trajectoire de l'outil peut être déterminée comme illustré sur la Fig. 2b. P o et P b sont le centre et le point inférieur du cercle de bord de l'outil. Lorsque l'effet de bord de l'outil est pris en compte, le point de génération de surface transitoire P c varie le long du bord de l'outil pendant le mouvement de l'outil. La surface finie réelle est générée par la ligne d'enveloppe de l'arête de l'outil de coupe. Si la trajectoire de P b est exprimé par les équations. (1) et (2), la trajectoire de P c peut être calculé par [41] :
$$x_{{\text{c}}} \left( t \right) =A_{{\text{c}}} \sin \left( {2\pi ft} \right) - vt - r\sin \theta \left( t \right)$$ (6) $$z_{{\text{c}}} \left( t \right) =A_{{\text{d}}} \sin \left( { 2\pi ft + \varphi } \right) + r(1{-}\cos \theta \left( t \right))$$ (7)où
$$\sin \theta \left( t \right) =\frac{{z^{{\prime }} (t)}}{{\sqrt {x^{{\prime }} (t)^{2 } + z^{{\prime }} (t)^{2} } }}$$ (8) $$\cos \theta \left( t \right) =\frac{{ - x^{{\prime }} (t)}}{{\sqrt {x^{{\prime }} (t)^{2} + z^{{\prime }} (t)^{2} } }}$$ (9 )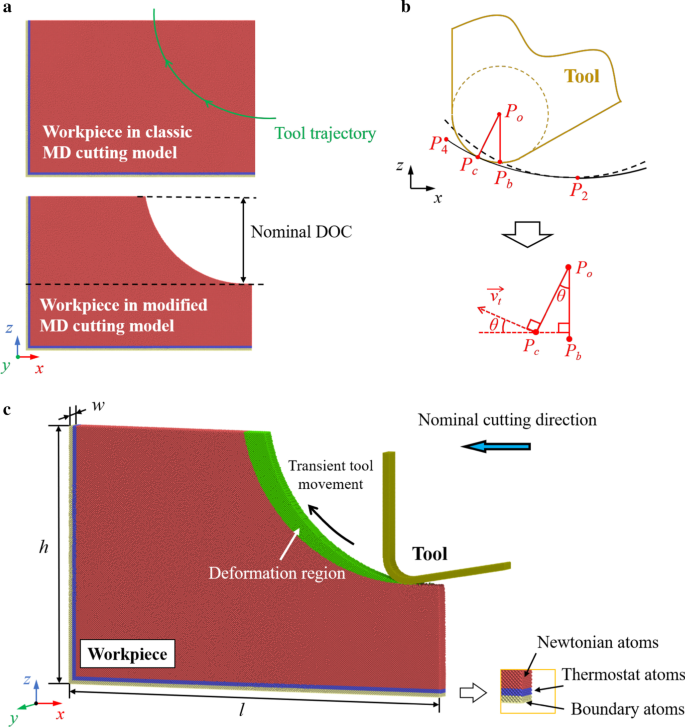
Schéma du modèle de coupe MD. un Modification de la pièce. b Détermination de la trajectoire de l'outil. c La morphologie du modèle MD modifié. Les atomes verts représentent la région de déformation dans un cycle de vibration
Les atomes de silicium sont divisés en trois groupes :les atomes limites, les atomes thermostatiques et les atomes newtoniens. Les atomes limites sont fixés dans leurs positions équilibrées pour maintenir la pièce pendant la simulation. Les atomes du thermostat sont maintenus à la température ambiante pour dissiper la chaleur de coupe générée tandis que les atomes newtoniens suivent la deuxième loi de Newton.
Les détails des paramètres de simulation sont répertoriés dans le tableau 1. La longueur l et hauteur h ont été déterminés à garder une distance suffisante entre la zone de coupe et les limites fixes. La condition aux limites périodique est appliquée le long du y direction pour imiter le silicium en vrac. La direction de coupe nominale, l'angle de dépouille/dépouille de l'outil et la différence de phase ont été déterminés en se référant au montage expérimental [42]. L'amplitude de vibration et le COD nominal sont agrandis pour se rapprocher de l'échelle expérimentale avec un coût de simulation acceptable. Pendant ce temps, afin de garantir l'épaisseur du matériau retiré (atomes verts sur la figure 2c), le rapport de vitesse et la fréquence de vibration ont été fixés à 40 et 500 MHz, respectivement. Par conséquent, la vitesse de coupe nominale a été déterminée à 3,125 m/s. De plus, des simulations avec différentes températures de coupe sont effectuées pour révéler l'effet de l'assistant thermique sur le mécanisme de coupe. La température de coupe est augmentée de 300 à 1 200 K, ce qui est réalisable lors de TAC comme l'usinage assisté par laser [4, 11].
Dans ce modèle modifié, seule l'étape de coupe pendant le cycle de vibration est simulée et les pas de temps lorsque la pièce est séparée avec l'outil de coupe sont enregistrés. Par conséquent, la puissance de calcul peut être concentrée sur le processus de coupe transitoire. Plus important encore, le processus d'enlèvement de matière transitoire peut être décrit avec précision. Une comparaison entre le modèle modifié et le modèle MD classique est présentée dans le tableau 2.
Fonction potentielle
Dans la simulation MD, il est important d'adopter un potentiel robuste pour décrire l'interaction entre les atomes. Pour le silicium monocristallin, les chercheurs ont développé de nombreux potentiels tels que la méthode des atomes intégrés modifiés (MEAM) [45], Stillinger-Weber (SW) [46], Tersoff [47] et la charge optimisée à plusieurs corps (COMB) [ 48] potentiels. Parmi ces potentiels, le potentiel d'ordre de liaison analytique (ABOP) proposé par Erhart et Albe [49] a attiré une attention croissante. C'est une fonction de potentiel à trois corps qui permet la formation et la rupture de liaisons lors de la simulation d'usinage. Selon des recherches antérieures [50], l'ABOP peut décrire avec précision à la fois les propriétés de dimère et de masse du silicium. Pendant ce temps, les propriétés mécaniques du silicium fabriqué par l'ABOP sont bien cohérentes avec les expériences [31], ce qui est important dans les simulations MD de l'usinage à l'échelle nanométrique. Par conséquent, dans cet article, le potentiel ABOP est appliqué pour décrire les interactions silicium-silicium et carbone-carbone. Pendant ce temps, l'interaction silicium-carbone est décrite par le potentiel Morse, qui s'est avéré être un potentiel efficace dans la simulation de coupe à l'échelle nanométrique [51, 52]. La fonction potentielle de Morse peut être exprimée par :
$$E_{{\text{Si - C}}} \left( {r_{ij} } \right) \, =D_{{\text{M}}} \left[ {{\text{e}} ^{{ - 2a(r_{ij} - R_{{\text{M}}} )}} - 2{\text{e}}^{{ - a(r_{ij} - R_{{\text{ M}}} )}} } \right]$$ (10)où D M , un, et R M représente l'énergie de cohésion, le module d'élasticité et la distance d'équilibre entre les atomes, respectivement. Le paramètre du potentiel Morse est [53] :D M = 0,435 eV, a = 46.487 nm −1 , R M = 0.19475 nm.
Résultats et discussion
Performances de coupe
En coupe ordinaire, le mécanisme d'enlèvement de matière dominant peut être fortement influencé par l'épaisseur des copeaux non déformés [54]. Avec une faible épaisseur de copeaux non déformés, le mécanisme d'enlèvement de matière dominant est l'extrusion. La phase métallique stable (Si-II) peut être générée par la transition de phase haute pression (HPPT), qui facilite la déformation ductile du silicium. Lorsque l'épaisseur des copeaux non déformés est augmentée, le matériau peut être principalement éliminé via un processus de cisaillement. Pendant le processus EVC, étant donné que l'épaisseur des copeaux non déformés varie constamment, le mécanisme d'enlèvement de matière peut passer de l'extrusion au cisaillement en un cycle de vibration. La figure 3 montre les instantanés de la simulation de coupe à 300 K. La structure cristalline de la pièce est déterminée par l'analyse du voisin commun (CNA) [55]. Cette analyse trouve des atomes qui sont disposés dans un réseau de diamants cubique ou hexagonal. La structure non diamantée de la figure 3c, e contient principalement la phase amorphe (a-Si), Si-II et d'autres atomes défectueux [56]. Ces structures sont instables et se transformeront en a-Si après découpe. Il peut être observé à partir de la Fig. 3b, c que le matériau est principalement éliminé par extrusion au cours de l'étape de découpe initiale. Un point de stagnation transitoire peut être observé près du bord de l'outil de coupe. Semblable à la coupe ordinaire, les matériaux dans la zone de déformation sont divisés par le point de stagnation en copeaux et en matériau comprimé. Au fur et à mesure que l'outil de coupe avance, l'épaisseur des copeaux non déformés augmente. Des plans de cisaillement et des grains de polycristaux sont générés dans la pièce, indiquant que le cisaillement devient le mécanisme d'enlèvement de matière dominant.
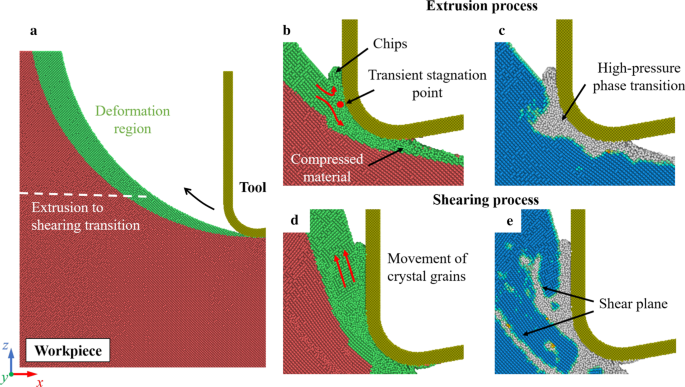
Transition du mécanisme d'enlèvement de matière. un Illustration de la zone de déformation. b , d Processus d'extrusion et de cisaillement. c , e Identification de la structure cristalline dans la pièce. Les atomes bleus représentent la structure en diamant cubique tandis que les atomes gris sont dans la structure non diamantée
La figure 4 montre la morphologie de la pièce à différentes températures de coupe. À 300 K, des fissures et des fractures évidentes peuvent être observées dans la pièce pendant le mouvement ascendant de l'outil. Pour les matériaux fragiles comme le silicium monocristallin, le mouvement ascendant de l'outil conduirait à l'arrachement des matériaux et laisserait des défauts dans la pièce, ce qui est considéré comme un problème spécifique dans EVC [42]. Bien que ces fissures puissent être éliminées par d'autres cycles de vibration, la stabilité de l'usinage sera affectée en raison de l'irrégularité de la surface de la pièce. Lorsque la température de coupe est augmentée, la génération et la propagation de fissures sont efficacement supprimées. D'après la Fig. 4d, aucune fracture évidente n'est détectée lorsque la température de coupe s'élève à 1200 K. Cependant, on observe qu'à 900 K et 1200 K, le gonflement de la surface usinée devient évident lorsque le mécanisme d'enlèvement de matière se transforme en cisaillement. On peut conclure qu'à mesure que davantage de grains cristallins sont générés au stade de cisaillement, le gonflement peut être causé par la rotation de ces grains cristallins à haute température.
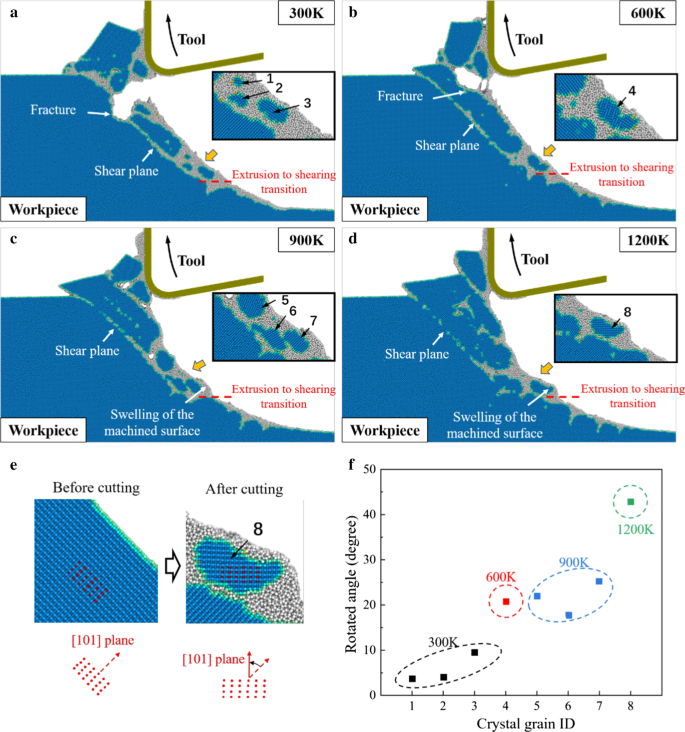
Morphologie de la pièce du procédé HM à a 300 K. b 600 K. c 900 K. d 1200 K. Les atomes bleus représentent la structure en diamant cubique tandis que les atomes gris sont en structure non diamantée. e Détermination de l'angle de rotation des grains cristallins. f L'angle de rotation avec l'augmentation de la température de coupe
Pour une description claire de cette rotation, les coordonnées de 24 atomes marqués (atomes rouges) dans les grains de cristal sont utilisées pour calculer l'angle de rotation moyen, comme illustré sur la figure 4e. L'angle de rotation de 8 grains de cristal (numérotés sur la figure 4a–d) est résumé sur la figure 4f. On peut observer que l'angle de rotation est évidemment augmenté à température élevée. Au cours du processus HM, la viscosité de l'a-Si peut être considérablement diminuée à haute température et le mouvement de traction des atomes de la pièce est favorisé par le mouvement ascendant de l'outil. Par conséquent, le flux atomique dans la pièce est amélioré et la rotation des grains de cristal peut être facilitée, entraînant un gonflement de la surface usinée. Pour restreindre la rotation des grains de cristal, la puissance de chauffage doit être contrôlée pour éviter une surchauffe de la pièce. En outre, les paramètres de vibration doivent être choisis avec soin, par exemple, une vitesse de coupe nominale plus petite et une fréquence de vibration plus élevée doivent être appliquées pour supprimer la génération de grains de cristal et éliminer le gonflement par d'autres cycles de vibration. Comme illustré sur la Fig. 5, avec les paramètres de vibration appropriés, P 1 pourrait se localiser dans l'étape d'extrusion et la surface usinée finale est générée par extrusion sans gonflement.
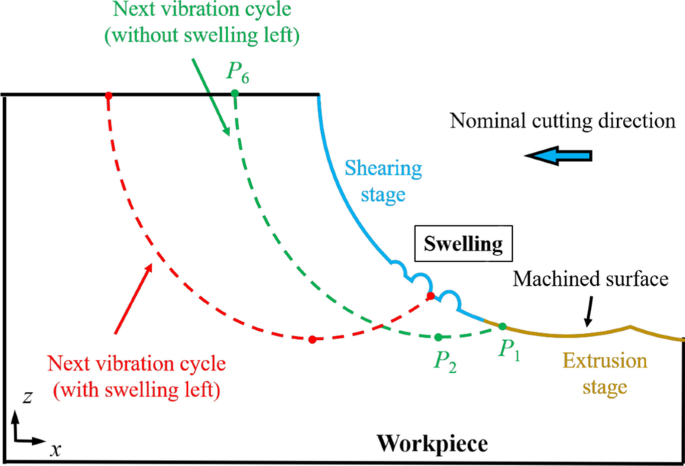
Élimination du gonflement dans le processus HM
Champ de contrainte dans la pièce
Pour étudier davantage le mécanisme de coupe au cours du processus HM, la distribution des contraintes dans la pièce a été calculée. Dans la simulation MD, la contrainte hydrostatique peut être exprimée sous la forme :
$$\sigma_{{{\text{hydrostatique}}}} =\, (\sigma_{x} + \sigma_{y} + \sigma_{z} )/3$$ (11)où σ x , σ y , et σ z , sont des tenseurs de contraintes provenant des données de sortie de LAMMPS.
La distribution des contraintes hydrostatiques pendant les étapes d'extrusion et de cisaillement est illustrée à la figure 6. Et les valeurs maximales des contraintes dans les régions de compression et de traction ont été marquées. Avec le mouvement de l'outil, le point de contact entre l'outil et la pièce varie le long du cycle de l'arête de l'outil, ce qui entraîne le mouvement de la zone de compression depuis l'arête de l'outil jusqu'à la face de coupe. À la suite de rapports précédents, le HPPT de la phase de silicium monocristallin (Si-I) à Si-II pourrait se produire à des pressions commençant à 10-12 GPa [57, 58]. Dans la simulation de coupe à 300 K, la contrainte de compression maximale au stade de l'extrusion et du cisaillement a atteint respectivement 18,1 GPa et 17,6 GPa. Ce résultat indique que la phase Si-II ductile peut être générée pendant la coupe et que le HPPT existe toujours dans l'étape de cisaillement. De plus, au stade de l'extrusion, la contrainte de traction se concentre principalement près de la zone de contact entre la face de flanc de l'outil et la surface usinée en raison de l'adhérence des atomes de silicium et de la surface de l'outil. Au fur et à mesure que l'outil passe à l'étape de cisaillement, la région de traction est agrandie et la concentration de contrainte de traction dans la pièce souterraine est considérablement augmentée, ce qui est provoqué par le mouvement de traction. Lorsque la température de coupe est augmentée, la déformabilité plastique du silicium monocristallin est améliorée et la contrainte interne dans la pièce est diminuée. À mesure que la température augmente de 300 à 1 200 K, la contrainte de compression maximale a diminué de 16,6 % et de 25 % au stade de l'extrusion et du cisaillement. Pendant ce temps, bien que la concentration de contrainte de traction dans la pièce souterraine soit toujours évidente, la valeur maximale de la contrainte de traction est apparemment diminuée de plus de 30 %. Il a été rapporté que la ténacité à la rupture du silicium monocristallin peut être efficacement augmentée à une température plus élevée [59]. Par conséquent, les fissures et les fractures causées par l'effet d'arrachement dû au mouvement vers le haut de l'outil peuvent être efficacement supprimées.
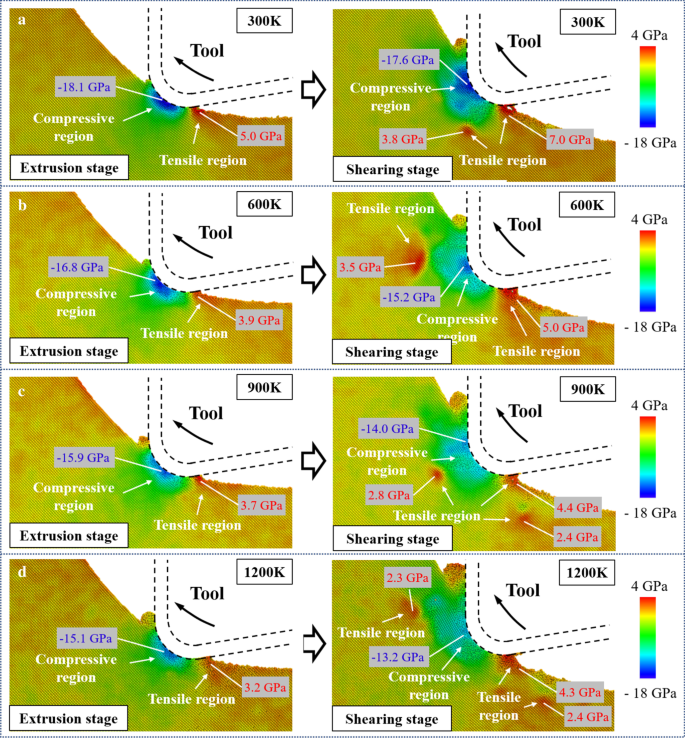
La distribution des contraintes hydrostatiques à :a 300 K. b 600 K. c 900 K. d 1200 K
Le silicium monocristallin a une structure cristalline Face Center Cubic (FCC) avec 12 systèmes de glissement. Sur la base du mouvement de l'outil, les principaux systèmes de glissement pour la déformation par cisaillement sont les (111)/[\(\stackrel{\mathrm{-}}{1}\)01] et (1\(\stackrel{\mathrm{- }}{1}\)1)/[\(\stackrel{\mathrm{-}}{1}\)01]. Par conséquent, la composante de contrainte de cisaillement résolue τ s dans le système de glissement (111)/[\(\stackrel{\mathrm{-}}{1}\)01] est calculé. Comme illustré sur la Fig. 7, la composante de contrainte de cisaillement résolue τ s dans le sens M du plan de glissement N peut être calculé à l'aide de tenseurs de contraintes par :
$$\tau_{{\text{s}}} =a_{1} a_{2} \sigma_{x} + b_{1} b_{2} \sigma_{y} + c_{1} c_{2} \sigma_{z} + \left( {a_{1} b_{2} + a_{2} b_{1} } \right)\tau_{xy} + \left( {a_{1} c_{2} + a_{2} c_{1} } \right)\tau_{xz} + \left( {b_{1} c_{2} + b_{2} c_{1} } \right)\tau_{yz}$$ (12)où un 1 , b 1 , c 1 sont les cosinus directeurs de la direction normale du plan N tandis que a 2 , b 2 , c 2 sont les cosinus directeurs de la direction de glissement M . Tandis que τ xy , τ xz , et τ yz sont les tenseurs de contrainte de cisaillement des données de sortie LAMMPS.
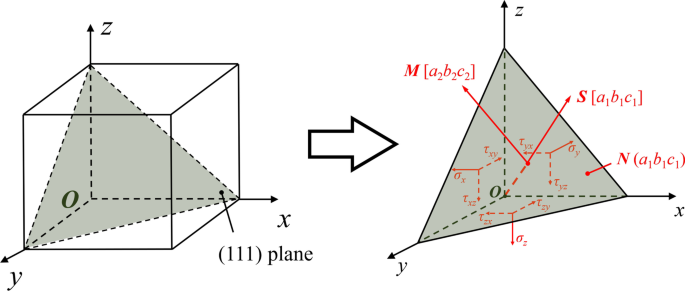
Illustration des tenseurs de contraintes
La distribution de la contrainte de cisaillement résolue τ s est illustré à la Fig. 8. La région avec τ positif s est définie comme la région de cisaillement puisque le mouvement de glissement le long de la direction [\(\stackrel{\mathrm{-}}{1}\)01] est favorisé, ce qui facilite l'enlèvement de matière par cisaillement. Alors que la région avec un τ négatif s est considérée comme la région endommagée car le mouvement de glissement est préférable dans la direction opposée, conduisant à la formation de dommages souterrains dans la pièce. Au stade de l'extrusion, la contrainte dans la zone de cisaillement est inférieure à celle dans la zone endommagée. Les dommages souterrains causés par la déformation par cisaillement peuvent être générés sous la surface usinée [60]. Au fur et à mesure du mouvement de l'outil de coupe, la contrainte de cisaillement le long de la direction [\(\stackrel{\mathrm{-}}{1}\)01] augmente progressivement, provoquant la transition d'enlèvement de matière de l'extrusion au cisaillement. En outre, étant donné que la position de la zone endommagée se déplace vers le haut le long du mouvement de l'outil, les dommages générés peuvent être supprimés par un cycle de vibration supplémentaire et ne seront pas laissés dans la pièce. Lorsque la température est augmentée de 300 K à 1 200 K, la contrainte de cisaillement dans la région endommagée a diminué de 36,1 % et 42,4 % au stade de l'extrusion et du cisaillement, respectivement. En revanche, en raison du mouvement ascendant de l'outil, la diminution de la contrainte de cisaillement le long de la direction [\(\stackrel{\mathrm{-}}{1}\)01] au stade de cisaillement est beaucoup moins apparente. La contrainte de cisaillement critique résolue (CRSS) pour le mouvement de glissement peut être exprimée comme [61] :
$$\tau_{{\text{c}}} \left( T \right) =C\varepsilon^{1/n} \exp \left( \frac{U}{nkT} \right)$$ (13 )où U et représente l'énergie d'activation du mouvement de glissement et la vitesse de déformation. Paramètres n et C sont des constantes matérielles. On peut conclure que le CRSS peut être diminué évidemment avec l'augmentation de la température. Par conséquent, la déformation par cisaillement dans la direction [\({\overline{\text{1}}}\)01] peut être facilitée à température élevée.
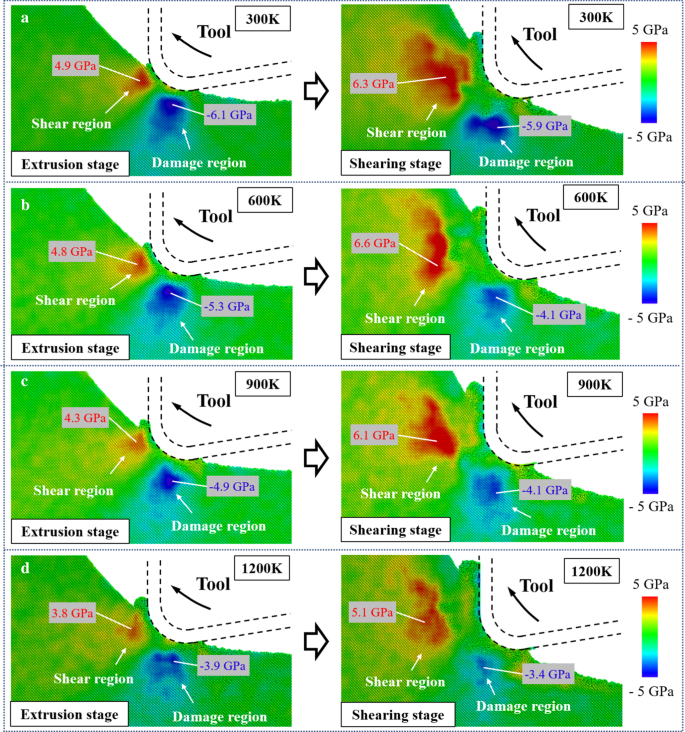
La distribution de contrainte de cisaillement résolue à :a 300 K. b 600 K. c 900 K. d 1200 K
Transition de phase
Lorsque la température de coupe est augmentée, la transition de phase du silicium peut être fortement influencée. La relaxation du a-Si et la transition vers Si-I peuvent être favorisées à une température appropriée [62]. Sur la figure 4, le motif d'endommagement des pièces devient plus étroit à haute température. Une observation détaillée de la configuration des dommages lors de la coupe à 1200 K est présente sur la figure 9a. On observe que les dommages générés dans la région de déformation sont partiellement récupérés après la coupe, indiquant que la transition de la structure non diamantée à Si-I s'est produite. Et plus d'atomes de Si-I sont générés lorsque la température de coupe augmente, comme le montre la figure 9b. De plus, le maillage de surface construit (couleur rouge) [63] de la pièce usinée à 1200 K est présent sur la figure 9c. On observe que des lacunes se forment dans la pièce souterraine. Étant donné que les atomes sont plus étroitement emballés dans la phase Si-I, la transition vers Si-I pourrait provoquer un rétrécissement du matériau, ce qui induit des lacunes dans la pièce. Le volume des lacunes à différentes températures est calculé et présent sur la figure 9d. On observe qu'il n'y a pratiquement pas de lacunes générées à température ambiante. Alors qu'une augmentation évidente des lacunes peut être détectée lorsque la température de coupe augmente à 900 K et 1200 K.
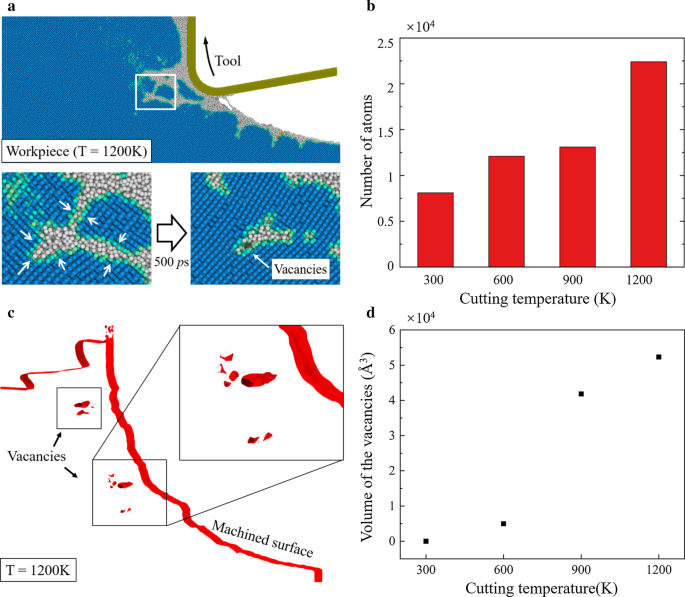
Processus de relaxation et lacunes dans la pièce. un Instantané de l'endommagement de la pièce à 1 200 K. b Nombre d'atomes transformés de la structure non-diamant en phase Si-I. c Maillage de surface construit de la pièce à 1 200 K. d Le volume des vides à différentes températures
Une analyse plus approfondie des lacunes est présente sur la figure 10. Un élément de matériau sous la surface usinée est choisi pour surveiller la génération des lacunes. Le nombre d'atomes dans la structure non diamantée et l'évolution des contraintes de l'élément matériel sont présents. Il est conclu que pendant le processus de coupe, l'élément de matériau est d'abord comprimé puis subit une contrainte de traction due au mouvement ascendant de l'outil. Pendant ce temps, deux pics de contrainte de cisaillement peuvent être observés à 300 K car la contrainte de cisaillement dans la région endommagée augmente au fur et à mesure que l'outil de coupe passe. Lorsque la température de coupe est augmentée, la diminution de la contrainte de cisaillement est plus évidente que la contrainte de traction. À 1 200 K, le deuxième pic de la contrainte de cisaillement a presque disparu tandis que la contrainte de traction devient dominante dans l'élément matériel pendant le processus de relaxation.
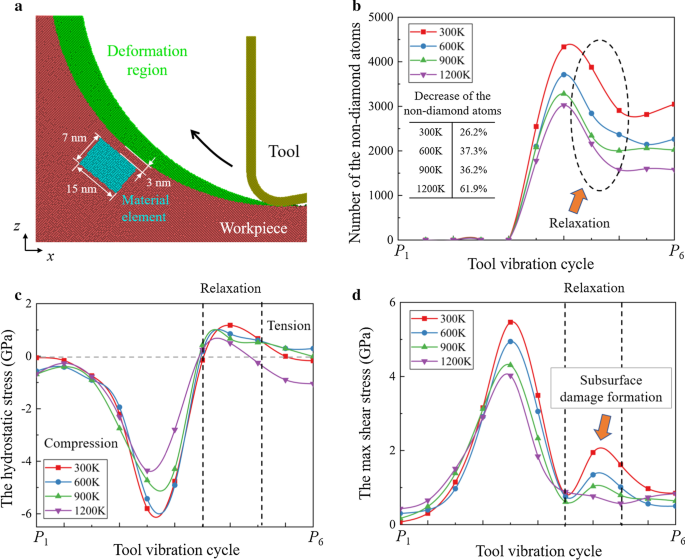
Relaxation pendant le processus HM. un Illustration de l'élément matériel. b Statistiques des atomes dans la structure non-diamant dans l'élément matériel. c , d Evolution des contraintes de l'élément matériel
Pour explorer l'effet de la contrainte de traction sur le processus de formation des lacunes, des simulations de relaxation d'échantillons de silicium en vrac ont été menées. Comme le montre la figure 11a, le modèle initial se compose de 40 % d'atomes de Si-I et de 60 % d'atomes de a-Si, qui sont générés par la méthode de fusion-extinction [64]. La taille du modèle est de 21,7 nm × 8,1 nm × 26,1 nm en x , y , et z direction, qui contient 230 400 atomes. The initial interface between crystal and non-crystal region is set as (001) crystal plane. Periodic boundary condition is applied in three dimensions to mimic bulk materials. The constructed surface mesh of the relaxed model is present in Fig. 11b. Furthermore, to quantify the vacancies, the solid volume fraction is calculated as the ratio of the solid material volume and the total volume of the simulation sample, as shown in Fig. 11c. It is observed that when temperature is increased, the solid volume fraction decreased obviously under tensile stress. Therefore, to suppress the vacancies, the desired cutting temperature in HM process should be lower than that in ordinary TAC. Meanwhile, the vibration parameters should be optimized to reduce the tensile stress in subsurface workpiece.
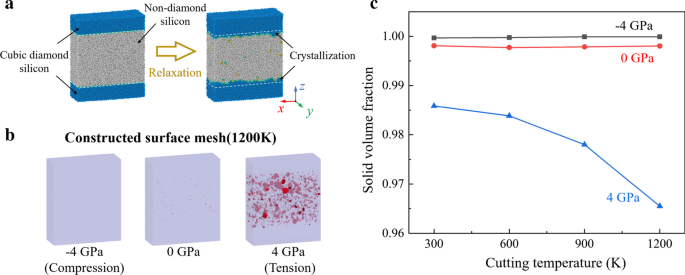
Relaxation simulation of silicon. un Scheme of MD relaxation simulation. b The surface mesh of the relaxed model at 1200 K. c The solid volume fraction curves
Conclusions
In this paper, MD simulation is carried out to investigate the cutting mechanism of hybrid machining (HM) process. A modified cutting model is applied to reveal the material removal behavior and subsurface damage formation in one vibration cycle. The main conclusions were as follows:
- (1)
During HM process, the dominant material removal mechanism could transform from extrusion to shear in a single vibration cycle. With an increase of the cutting temperature, the generation and propagation of cracks can be effectively suppressed. However, the swelling appears when the dominant material removal mechanism becomes shearing, which is caused by the rotation of the crystal grains in workpiece.
- (2)
Based on the stress analysis, the dominant formation mechanism of the subsurface damage in one vibration cycle can be distinct. In the extrusion stage, the subsurface damage can be generated by the shear stress in the damage region. While in the shearing stage, tensile stress becomes dominant in subsurface damage formation. When the cutting temperature is increased, although the tensile stress concentration in the subsurface workpiece is still obvious, the peak value of the stresses is apparently decreased, which effectively suppress the cracks and fractures in workpiece.
- (3)
When the cutting temperature is increased, less subsurface damage is generated in the workpiece. However, due to the tensile stress, some vacancies can be generated in the workpiece when the cutting temperature is increased. Therefore, the desired cutting temperature during HM process should be lower than that in ordinary TAC and the vibration parameters should be set carefully to suppress the vacancies in the subsurface workpiece.
Disponibilité des données et des matériaux
The datasets used and analyzed in the current study can be obtained from the corresponding authors upon reasonable request.
Abréviations
- TAC:
-
Thermal assisted cutting
- VAC:
-
Vibration assisted cutting
- LVC:
-
Linear vibration cutting
- EVC:
-
Elliptical vibration cutting
- DOC:
-
Depth of cut
- HM:
-
Hybrid machining
- FEM :
-
Méthode des éléments finis
- MD :
-
Dynamique moléculaire
- LAMMPS:
-
Large-scale Atomic/Molecular Massively Parallel Simulator
- MEAM:
-
Modified embedded-atom method
- SW:
-
Stillinger–Weber
- COMB:
-
Charge optimized many-body
- ABOP:
-
Analytical bond-order potential
- Si-II:
-
Metallic stable phase
- HPPT:
-
High-pressure phase transition
- AIIC :
-
Analyse des voisins communs
- a-Si:
-
Amorphous phase
- Si-I:
-
Single-crystal silicon phase
- FCC :
-
Face Center Cubic
- CRSS:
-
Critical resolved shear stress
Nanomatériaux
- Types et classification des processus d'usinage | Sciences de la fabrication
- Quelles sont les principales étapes du processus d'usinage ?
- L'importance de la lubrification dans l'usinage de pièces mécaniques
- Comprendre la précision et le processus de la technologie de découpe laser
- Vitesse d'avance et vitesse de coupe :comprendre la différence
- La différence entre le processus d'usinage conventionnel et non conventionnel
- Comprendre le processus de tournage dans l'usinage CNC
- Un aperçu du processus d'usinage du plastique
- Préparation du processus de fabrication des prototypes à la production