Optimisation numérique pour la configuration géométrique des céramiques réalisée dans des composites résistants à l'usure HCCI/ZTAP basés sur le modèle de particules réel
Résumé
Afin de réduire la contrainte thermique dans les composites à matrice en fonte à haute teneur en chrome (HCCI) renforcée par des particules de céramique d'alumine durcie à la zircone (ZTA), une simulation par éléments finis est effectuée pour optimiser la configuration géométrique des céramiques. Le modèle précédent simplifie la structure globale de la préforme de particules de céramique et ajoute des conditions aux limites pour simuler les particules, ce qui entraînera une erreur incontrôlable dans les résultats. Dans ce travail, les modèles de grains équivalents sont utilisés pour décrire la préforme réelle, rendant les résultats de simulation plus proches des résultats expérimentaux réels. Le processus de solidification du matériau composite est simulé et l'infiltration entre le fer fondu et les particules de céramique est réalisée. La contrainte thermique dans le processus de solidification et la distribution des contraintes de compression sont obtenues. Les résultats montrent que l'ajout de trous ronds de 10 mm sur la préforme peut améliorer les performances du composite, ce qui est utile pour éviter les fissures et augmente la plasticité du matériau.
Introduction
Avec l'avancement continu du processus d'industrialisation, les matériaux simples traditionnels résistants à l'usure sont progressivement devenus difficiles à répondre aux exigences de performance des pièces résistantes à l'usure dans les domaines de la métallurgie, de l'énergie électrique et des matériaux de construction [1, 2]. Composites à matrice métallique renforcés de particules de céramique, tels que les composites à matrice de fonte à haute teneur en chrome (HCCI) renforcés par des particules de céramique d'alumine durcie à la zircone (ZTA) (appelés HCCI/ZTAP composites ci-après), sont l'un des matériaux résistants à l'usure les plus populaires, qui combine parfaitement la dureté élevée de la céramique ZTA avec la ténacité exceptionnelle du HCCI et tire pleinement parti de la relation complémentaire entre les deux, donnant l'excellente résistance à l'usure à la matrice métallique composites [3, 4].
HCCI/ZTAP les composites ont encore une certaine tendance à la fissuration, ce qui peut affecter l'apparence et la stabilité de la production [5,6,7]. La fissuration des matériaux composites est liée à la plasticité et à la condition de contrainte. Une excellente plasticité et une contrainte thermique plus faible peuvent réduire la possibilité de fissuration des matériaux composites [8]. Si la différence de coefficient de dilatation thermique entre les particules de céramique et le métal est trop grande, la contrainte thermique dans les composites augmentera en conséquence. Lorsque la contrainte thermique est élevée, des fissures peuvent s'amorcer à l'intérieur du composite, notamment à l'interface entre les particules de céramique et le métal. L'extension et la propagation continues des fissures peuvent conduire à terme à la rupture du matériau composite voire à l'écaillage de la totalité de la couche [9, 10]. HCCI/ZTAP les matériaux composites présentent également les problèmes ci-dessus. Lorsque le métal fondu s'infiltre dans les particules agrégées, la température diminue, ce qui entraîne une mauvaise capacité de combinaison du métal avec les particules de céramique. Par conséquent, afin d'améliorer encore les performances de HCCI/ZTAP composites, il est important d'étudier et de réduire leur tendance à la fissuration [11, 12].
En HCCI/ZTAP composites, la couche composite est conçue comme la face de travail et la matrice de repos est en métal, ce qui confère au composite une résistance à l'usure et une plasticité élevées en même temps [13]. La couche composite est préparée par la méthode d'infiltration en HCCI/ZTAP composite. Une des caractéristiques remarquables des matériaux composites est leur aptitude à la conception [14]. Selon la demande réelle, les particules de céramique sont préparées dans une préforme avec une structure et une taille spéciales, puis la préforme est étroitement combinée avec le métal en fusion pour préparer un ZTAP /HCCI composite [15].
Afin de réduire la contrainte thermique, nous choisissons la préforme de particules céramiques d'hexagone. Dans la préforme hexagonale, la distance maximale à laquelle le métal en fusion pénètre dans la préforme est la même quelle que soit la direction, de sorte que l'uniformité de la pénétration du métal est améliorée et la concentration de contrainte dans la préforme est réduite [16, 17]. Bien que la préforme hexagonale soit utilisée pour réduire la tendance du matériau à se fissurer, la contrainte thermique dans le processus de moulage du matériau existe toujours. L'amélioration de la structure de la préforme de particules de céramique peut réduire efficacement la concentration de contraintes.
Dans l'optimisation de la structure de préforme composite, la méthode des éléments finis peut réduire les expériences répétées. Dans les études précédentes, en raison de la complexité du dessin et du calcul des particules de céramique, la préforme de particules de céramique est généralement simplifiée dans son ensemble. Des recherches approfondies ont révélé que le modèle simplifié présente certains défauts et ne peut pas être utilisé dans une gamme plus large. L'établissement d'un modèle de particules équivalent peut en outre combiner le modèle avec la situation réelle et réduire l'erreur causée par le modèle [18]. La méthode du logiciel d'analyse par éléments finis COMSOL Multiphysics est utilisée pour modéliser les champs de contraintes dans le processus de solidification et le processus de compression du HCCI/ZTAP matériau composite [19]. COMSOL Multiphysics est un logiciel de simulation numérique avancé à grande échelle [20, 21].
Dans cet article, nous utilisons un logiciel d'éléments finis pour simuler la contrainte des matériaux composites dans différentes conditions. La version de COMSOL Multiphysics utilisée dans cet article est la 4.5a. Cette étude analyse systématiquement l'influence du modèle géométrique dans le logiciel d'éléments finis sur les résultats de calcul, ce qui profite à la conception et au développement de poreux perform. La simulation et l'expérience sont comparées entre elles et le modèle est optimisé en permanence.
Méthodes
L'un des problèmes majeurs de la production de composites est la concentration des contraintes, et elle affecte directement la résistance à l'usure et la plasticité des matériaux composites. L'amélioration de la structure de la préforme de particules de céramique peut réduire efficacement la concentration de contraintes. Le but de cette étude est d'étudier l'influence de la structure de la préforme sur la répartition des contraintes et d'améliorer les performances des matériaux composites.
L'établissement et l'optimisation du modèle géométrique
Au cours du processus de solidification, la température du moule et du métal liquide est différente et le métal liquide se solidifie rapidement, de sorte que le transfert de chaleur entre chaque position du processus de coulée est instable et l'équation de transfert de chaleur peut s'écrire [22] :
$$\rho C_{{\text{P}}} \frac{\partial T}{{\partial x}} =\frac{\partial }{\partial x}\left( { \lambda \frac{\ partiel T}{{\partial x}}} \right) + \frac{\partial }{\partial y}\left( { \lambda \frac{\partial T}{{\partial y}}} \right) + \frac{\partial }{\partial z}\left( { \lambda \frac{\partial T}{{\partial z}}} \right) + \rho Q$$ (1)où \(\rho\) est la densité ; \(C_{{\text{P}}}\) correspond aux capacités calorifiques ; \(\lambda\) est la conductivité thermique ; T est la température transitoire ; Q est la chaleur ; les coordonnées x , y , et z sont appelées les coordonnées relatives du sous-système.
Étant donné que la température de chaque point est différente dans le processus de solidification, il existe une contrainte interne variable dans le moulage. Si le moulage peut être considéré comme un corps à élasticité linéaire, lorsque la contrainte interne est inférieure à la limite d'élasticité, avec le processus de déformation élastique, nous pouvons utiliser l'équation de la loi de Hooke pour le décrire.
$$\left\{ {\begin{array}{*{20}l} {\varepsilon_{xx} =\frac{1}{E}\left[ {\sigma_{xx} - v\left( {\ sigma_{yy} + \sigma_{zz} } \right)} \right]} \hfill \\ {\varepsilon_{yy} =\frac{1}{E}\left[ {\sigma_{yy} - v\ left( {\sigma_{xx} + \sigma_{zz} } \right)} \right]} \hfill \\ {\varepsilon_{zz} =\frac{1}{E}\left[ {\sigma_{zz } - v\left( {\sigma_{xx} + \sigma_{yy} } \right)} \right] \to \varepsilon_{ij} =\frac{1 + v}{E}\sigma_{ij} - \frac{v}{E}\delta_{ij} \sigma } \hfill \\ {\varepsilon_{xy} =\frac{1}{2G}\sigma_{x} } \hfill \\ {\varepsilon_{yz } =\frac{1}{2G}\sigma_{yz} } \hfill \\ {\varepsilon_{zx} =\frac{1}{2G}\sigma_{zx} } \hfill \\ \end{array} } \droit.$$ (2)où E est le module de Young ; \(\sigma =\sigma_{{ii + \sigma_{11} }} + \sigma_{22 + } \sigma_{33}\); \(v\) est le coefficient de Poisson; tenseur unitaire \(\varepsilon_{ij} =\frac{1}{2}\gamma_{ij}\); module de cisaillement \(G =\frac{E}{{2\left( {1 + v} \right)}}\).
Ensuite, la contrainte interne est supérieure à la limite d'élasticité et la pièce moulée a plus de déformation. La déformation totale est composée de la déformation élastique et de la déformation plastique, \(\sigma_{ij} =\sigma_{ij}^{e} + \sigma_{ij}^{p}\). Cette équation peut être traitée comme un modèle d'écrouissage linéaire plastique élastique. La déformation élastique et la déformation plastique sont linéaires, et l'équation constitutive peut être écrite comme [23] :
$$\sigma =\left\{ {\begin{array}{*{20}l} {E\varepsilon } \hfill &{\varepsilon \le \varepsilon_{{\text{s}}} } \hfill \ \ {\sigma_{{\text{s}}} + E_{1} \left( {\varepsilon - \varepsilon } \right)} \hfill &{\varepsilon> \varepsilon_{{\text{s}}} } \hfill \\ \end{array} } \right.$$ (3)où \(\sigma\) est la déformation ; E est le module de Young ; \(\varepsilon\) est le stress ; \(\varepsilon_{{\text{s}}}\) est la limite d'élasticité.
La durée de vie des pièces en fonte à haute teneur en chrome est plus courte en raison d'une faible résistance à l'usure. Les matériaux composites présentent de nombreux avantages par rapport au HCCI simple. Dans le processus de fabrication de HCCI/ZTAP composites, les particules de céramique ZTA sont préparées à l'avance dans une préforme poreuse. La préforme rend les particules de céramique ZTA et le HCCI plus étroitement combinées, et les particules de céramique ne tombent pas facilement lorsqu'elles sont soumises à un impact. Afin d'améliorer encore les performances du HCCI/ZTAP composites, il est nécessaire d'optimiser la structure des préformes.
Pendant le processus de coulée, le métal en fusion peut remplir les trous circulaires et augmenter la proportion de métal. Dans le processus de candidature de HCCI/ZTAP composites, il s'avère que la position d'agrégation des particules est plus sujette aux fissures, de sorte que le trou circulaire est ajouté dans cette position.
La forme des particules de céramique ZTA est un polygone arbitraire et il existe de nombreuses particules dans la préforme. Si toutes les particules sont dessinées, la charge de travail est importante. Dans les simulations précédentes de composites céramiques à matrice métallique, la plupart des préformes de particules céramiques étaient considérées comme un tout. Comme le montre la figure 1, l'article établit des modèles à l'échelle macro et micro, respectivement. L'établissement d'un modèle raisonnable nécessite une vérification mutuelle répétée avec des expériences. Dans le modèle d'optimisation, les résultats calculés sont en bon accord avec les résultats expérimentaux. Les résultats de la simulation comprenaient la contrainte thermique, le champ de température, le champ de transition de phase pendant la solidification et la contrainte de contrainte de la coulée sous charge. Apportez des ajustements raisonnables et efficaces au modèle d'éléments finis établi afin que le modèle d'éléments finis optimisé puisse être utilisé dans une gamme plus large.
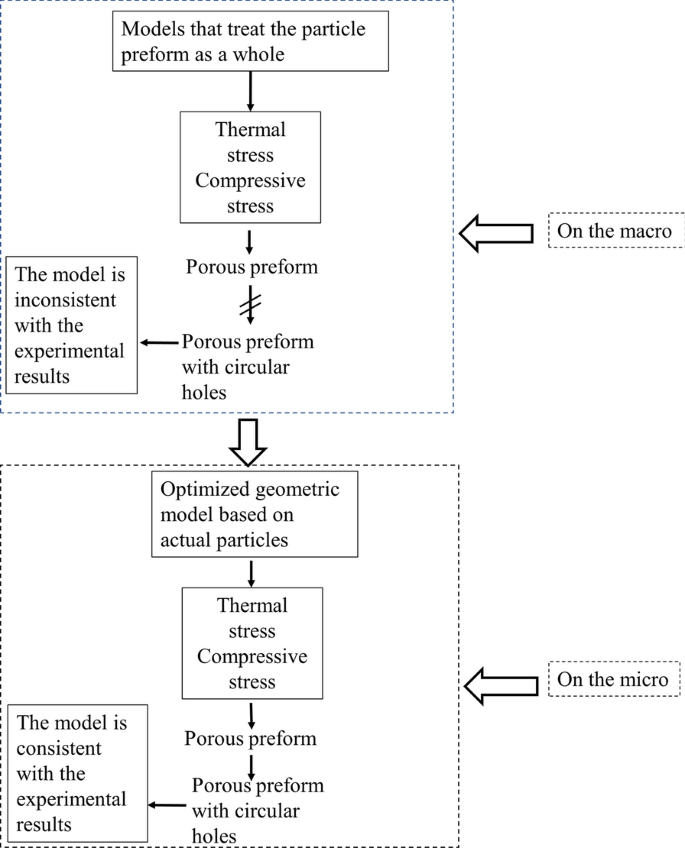
L'organigramme de l'optimisation du modèle géométrique pour HCCI/ZTAP matériaux
Dans l'établissement du modèle géométrique à l'aide du logiciel éléments finis, afin de réduire le temps de calcul et la charge de travail de modélisation, le modèle géométrique simplifié est souvent utilisé. Comme le montre la figure 2, il existe des espaces entre les particules car la préforme poreuse hexagonale tridimensionnelle est simplifiée en un modèle bidimensionnel, et une seule couche de particules est sélectionnée pour projeter le modèle bidimensionnel. De cette façon, l'empilement de particules dans l'espace tridimensionnel peut efficacement éviter l'influence sur le modèle géométrique bidimensionnel et simplifier raisonnablement le modèle et améliorer l'efficacité du calcul.
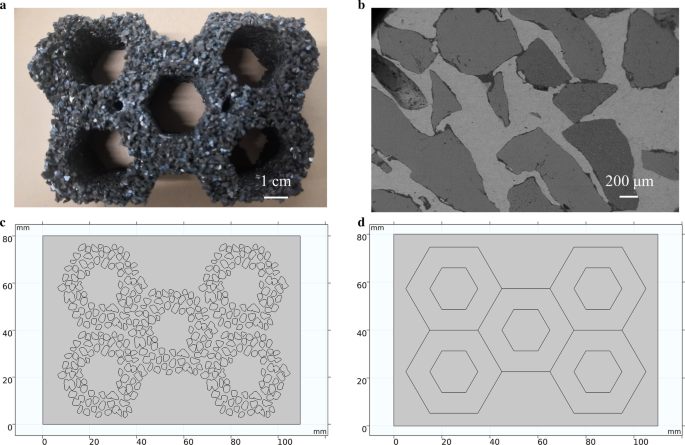
Particules de céramique ZTA et modèle géométrique de HCCI/ZTAP matériaux composites. un Performance poreuse, b la zone composite de HCCI/ZTAP composites, c modèle géométrique optimisé basé sur des particules réelles, d modèle géométrique initial
Dans cet article, les particules de céramique ZTA sont sélectionnées comme phase de renforcement du composite. Les particules de céramique ZTA sont une céramique structurelle multiphasée préparée en ajoutant de la zircone à de l'alumine, puis en frittant, où la fraction massique de zircone est de 18 % et la fraction massique d'alumine est de 82 %. La fonte à haute teneur en chrome est la matrice du matériau composite, qui contient plus de 12% de chrome, et est un excellent matériau résistant à l'usure.
Les paramètres du matériau ont une grande influence sur le résultat du calcul par éléments finis. Les paramètres de matériau requis pour le calcul de simulation dans cet article sont obtenus par des expériences et la littérature. Les paramètres de matériau des particules de céramique ZTA et du HCCI sont indiqués dans le tableau 1.
Expériences
Pour tester la plasticité et la résistance à l'usure du HCCI/ZTAP matériau composite, un test systématique a été effectué sur le composite pour mieux déterminer l'influence de la structure de la préforme. La machine d'essai universelle SHT4305 a été utilisée pour mesurer les propriétés de compression de HCCI/ZTAP matériaux composites. La taille de l'échantillon d'essai de compression est de 10 × 10 × 25 mm, la charge appliquée est de 30 tonnes et la vitesse de compression est de 0,5 mm/min.
Le test de résistance à l'usure du HCCI/ZTAP composite est nécessaire. Une excellente résistance à l'abrasion est le critère le plus important pour tester les performances des matériaux composites résistants à l'usure. HCCI/ZTAP les composites sont principalement utilisés dans les industries du traitement des minéraux, de la fabrication du ciment et de la fabrication du papier, et la plupart des conditions de travail sont une usure abrasive à trois corps. Afin de simuler les performances de service de HCCI/ZTAP composites dans des conditions de travail réelles autant que possible, testé le HCCI/ZTAP composites à l'aide du testeur d'usure abrasive à trois corps MMH-5. Le matériau de la piste du testeur est en acier à outils M2, dureté 820-860 Hv, diamètre extérieur 380 mm, largeur 20 mm. Le type et la taille des abrasifs sont sélectionnés en fonction des différentes conditions de travail. Dans cet article, le sable de quartz est utilisé pour les abrasifs, la dureté est de 1 000 à 1 200 Hv, la charge d'essai est de 40 N et la vitesse de rotation de l'échantillon est de 30 r/min.
Un nanoindenteur est utilisé pour effectuer un test de module d'Young à 100 points dans les 100 × 100 m 2 sélectionnés. microrégion. Le modèle du nanoindenteur est iMicro.
La résistance à l'usure des matériaux peut être mesurée avec une réduction de masse, une réduction de volume, etc. La perte de volume mesurée par un cylindre de mesure avec de petits changements peut facilement provoquer des erreurs dans les lectures humaines. Par conséquent, dans les mêmes conditions d'usure, la perte de masse m est utilisée pour évaluer les performances d'usure du matériau. La formule de calcul des pertes matérielles est la suivante :
$$\Delta m =m_{1} - m_{2}$$ (4)où m 1 et m 2 , respectivement, représentent la masse des échantillons avant et après usure.
Résultats et discussion
Simulation basée sur un modèle complet simplifié
Dans la simulation de contrainte thermique dans le processus de solidification de HCCI/ZTAP composites dans cette étude, la distribution de la contrainte thermique à 10 s est sélectionnée pour tous les résultats de simulation, car la contrainte thermique change de manière significative avant et après 10 s. Par rapport à l'échelle à droite de la figure 3, la couleur rouge indique un stress plus élevé et la couleur bleue indique un stress plus faible. Sur la figure 3a, une concentration de contraintes est apparue sur le bord de la préforme, en particulier dans la position médiane, la face supérieure et la face inférieure de la préforme sont apparues en rouge. Par rapport à l'échelle de droite de la figure 3a, cela montre que la contrainte est énorme ici. La couleur bleue apparaît à l'endroit où les particules se rassemblent, c'est-à-dire à l'intersection des parois des trous hexagonaux, indiquant que la contrainte est faible ici. Dans le modèle géométrique de la figure 3c, des trous circulaires sont ajoutés aux agrégats de particules de la préforme. La distribution des contraintes sur la figure 3c est similaire à celle de la figure 3a, sauf qu'il y a une concentration de contraintes plus évidente autour des trous circulaires. La répartition des contraintes autour du trou circulaire de la performance de la figure 4 est similaire à celle de la figure 3
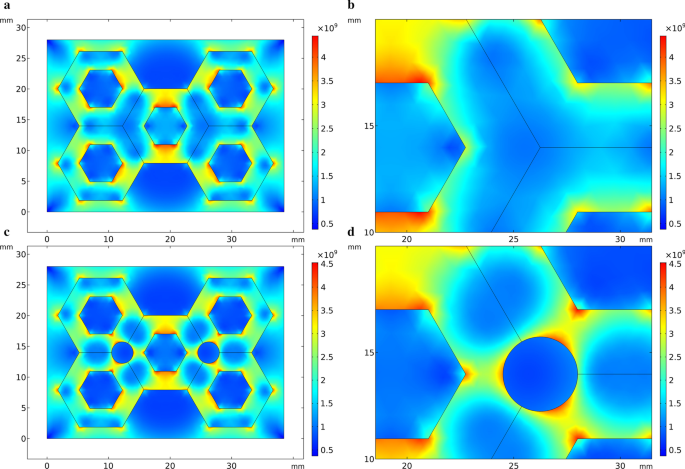
Distribution des contraintes thermiques lors de la solidification dans le modèle simplifié. un Performance initiale, b vue agrandie partielle de la performance initiale, b préforme avec trous circulaires ajoutés, d vue partielle agrandie de la scène avec trous circulaires ajoutés
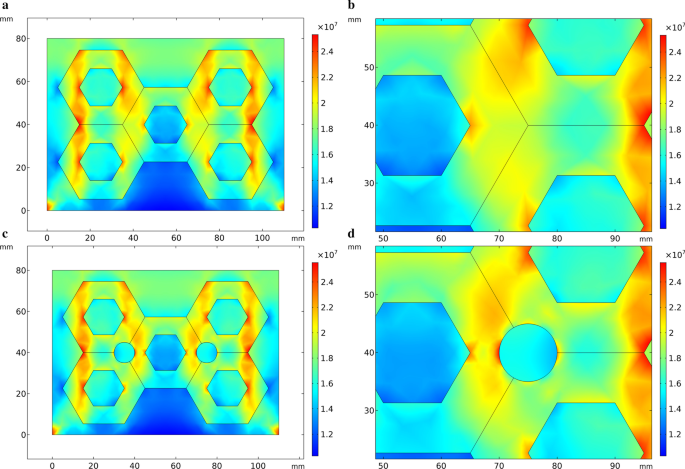
Contrainte de compression dans le modèle simplifié. un Performance initiale, b vue agrandie partielle de la performance initiale, b préforme avec trous circulaires ajoutés, d vue partielle agrandie de la scène avec trous circulaires ajoutés
Les résultats du calcul final doivent être intuitifs, les résultats ont donc été post-traités et un tableau de comparaison transversale des contraintes a été établi. Tracez d'abord une transversale 2D dans le modèle géométrique, car la partie principale d'observation se situe autour du trou circulaire, c'est-à-dire là où les particules se rassemblent, de sorte que la transversale 2D passe par le trou circulaire. L'ordonnée du graphique de contrainte est la valeur de contrainte sur la ligne de coupe et l'abscisse est le x -coordonnée de l'axe du modèle, comme illustré à la Fig. 5. Dans le modèle simplifié, les coordonnées du trou circulaire sont (12, 14), (27, 14). La figure 5c est un graphique linéaire de la contrainte de solidification. Sur la figure 5c, la préforme avec des trous circulaires a une augmentation significative de la contrainte aux abscisses 12 et 27, par rapport à la préforme sans trous circulaires. La figure 5d est un tableau de comparaison des contraintes de compression. La tendance générale de la courbe est la même que celle de la figure 5c, et la contrainte de localisation du trou circulaire augmentera considérablement.
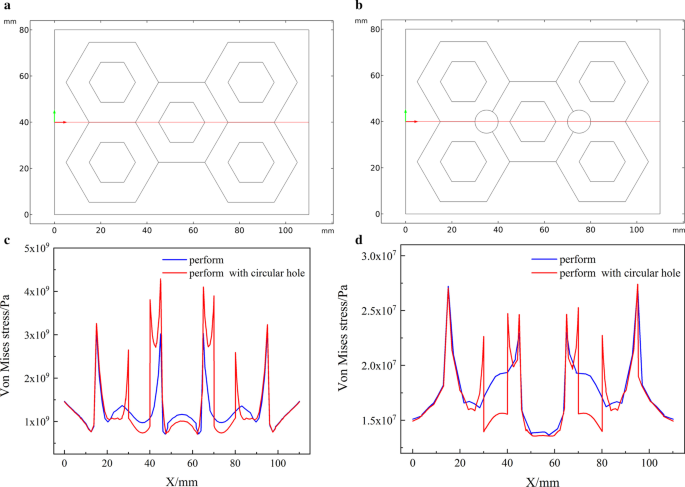
La position de la transversale 2D du modèle simplifié et la comparaison transversale des contraintes. un Performance initiale, b vue agrandie partielle de la performance initiale, c préforme avec trous circulaires ajoutés, d vue partielle agrandie de la scène avec trous circulaires ajoutés
Simulation basée sur un modèle de grain équivalent
La figure 6 montre la distribution des contraintes thermiques de HCCI/ZTAP modèle de composites basé sur des particules réelles, qui est similaire à la Fig. 3. Cependant, sur la Fig. 6, les particules de céramique ZTA ne sont plus simplifiées comme une préforme entière, mais établies comme des particules individuelles, et on peut observer que la plupart des les particules autour apparaissent de couleur rouge. La forme des particules de céramique ZTA n'est pas uniforme et la contrainte est supérieure à la valeur environnante, en particulier à la pointe des particules. Les distributions des contraintes thermiques sur les Fig. 3b et 6b sont évidemment différents. Le trou circulaire de la préforme sur la figure 6b apparaît en bleu, indiquant que la contrainte est faible ici. Les résultats du calcul de la concentration des contraintes autour du trou circulaire sont opposés. Le degré de simplification et les méthodes de dessin des modèles géométriques conduisent à des résultats de calcul différents.
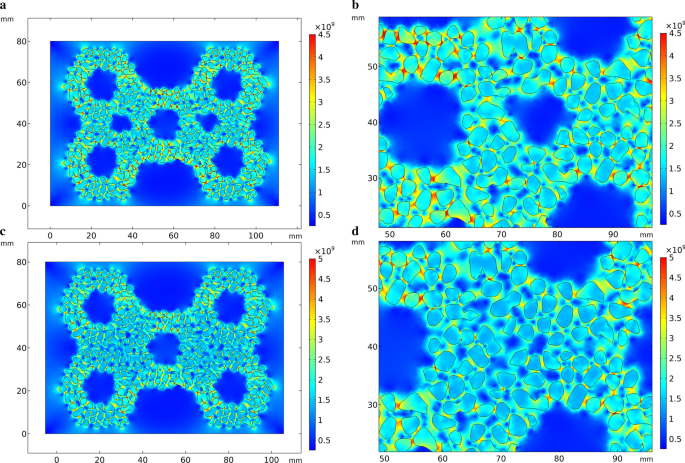
Distribution des contraintes thermiques lors de la solidification dans le modèle optimisé. un Performance initiale, b vue agrandie partielle de la performance initiale, c préforme avec trous circulaires ajoutés, d vue partielle agrandie de la scène avec trous circulaires ajoutés
Le modèle géométrique utilisé pour simuler la contrainte de compression sur la figure 7 est le même que sur la figure 6. Sur la figure 7, en comparant avec l'échelle de droite, la contrainte est concentrée sur la partie supérieure du modèle et la préforme, en particulier les bords des deux côtés de la préforme en céramique, qui sont jaune-vert. Dans la partie d'agrégation des particules de la préforme, cette zone est représentée en vert sur la figure 7a, indiquant que la contrainte est faible ici. Sur la figure 7b, des trous circulaires sont ajoutés au niveau des agrégats de la préforme. La couleur de la zone des trous circulaires est verte et jaune, indiquant qu'il n'y a pas de concentration de contrainte évidente.
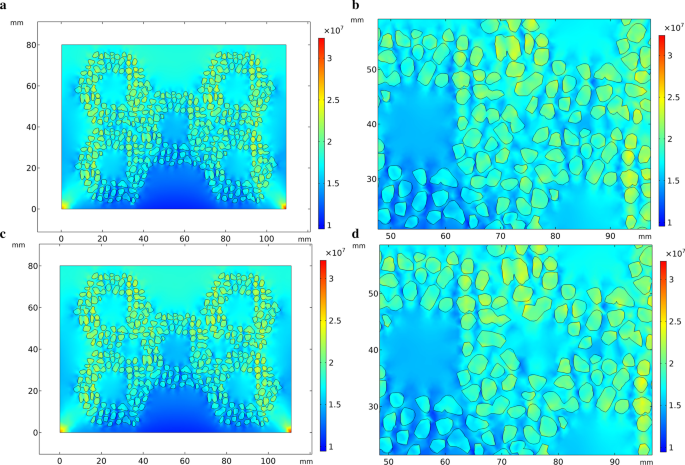
Contrainte de compression dans le modèle optimisé. un Performance initiale, b vue agrandie partielle de la performance optimisée, c préforme avec trous circulaires ajoutés, d vue partielle agrandie de la scène avec trous circulaires ajoutés
Dans le modèle basé sur des particules réelles, les coordonnées du trou circulaire sont (12, 14) (27, 14). La figure 8 est un diagramme de comparaison de la contrainte de solidification, comparant l'effet de la présence ou de l'absence de trous circulaires sur la contrainte. La contrainte de la préforme à trous circulaires a montré une diminution significative aux abscisses 12 et 27, et sa position coïncidait fondamentalement avec la position des trous circulaires. La contrainte des coordonnées restantes de la préforme avec des trous circulaires a une petite augmentation. Sur la figure 8a, b, les deux courbes sont fondamentalement coïncidentes, sauf dans la préforme avec des trous circulaires ; la contrainte près des coordonnées du trou circulaire diminue considérablement.
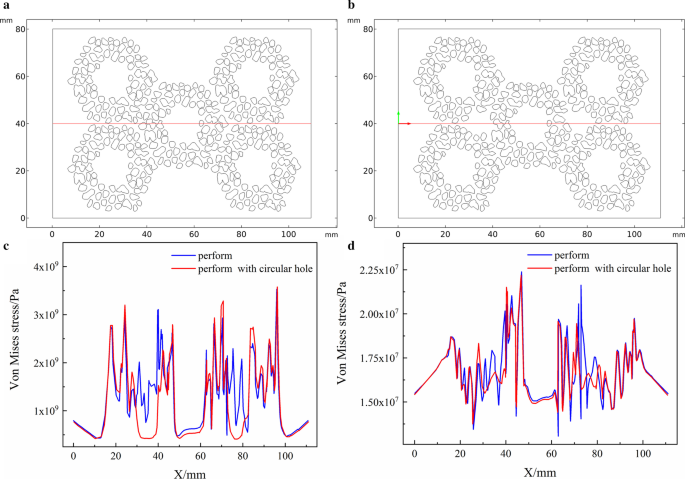
La position de la transversale 2D du modèle optimisé et la comparaison transversale des contraintes. un Performance initiale, b préforme avec trous circulaires ajoutés, c contrainte de solidification, d contrainte de compression
Validations expérimentales
On peut voir sur la Fig. 9, dans le test d'usure, la perte de masse des composites utilisant la préforme optimisée et les composites avec la préforme d'origine n'est pas très différente, indiquant que la résistance à l'usure n'est pas significativement sacrifiée et peut également améliorer la plasticité globale du HCCI/ZTAP composites.
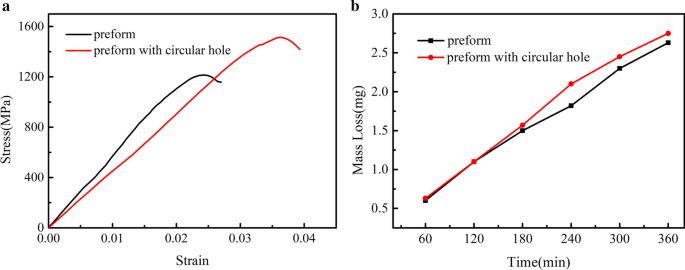
Courbe contrainte-déformation de compression de HCCI/ZTAP matériau composite et perte de masse d'abrasif à trois corps à la jonction des parois en nid d'abeille composites
La préforme poreuse a été optimisée en ajoutant des trous cylindriques de petite taille au niveau des zones d'agrégation des particules, ce qui a modifié la fraction volumique des particules de céramique dans le HCCI/ZTAP matériaux composites. La teneur en particules de céramique ZTA dans le matériau composite est un facteur important affectant ses propriétés mécaniques. Comme le montre la Fig. 9, la résistance à la compression et la déformation par compression de l'échantillon qui a des préformes avec des trous circulaires augmentent de manière significative par rapport à celle de l'échantillon avec la préforme initiale, indiquant que les petits trous circulaires dans les zones d'agrégation des particules de céramique ZTA sont propices à l'amélioration la résistance et la plasticité du HCCI/ZTAP matériaux composites. L'ajout de petits trous cylindriques au niveau des zones d'agglomération de la préforme poreuse augmentera le contenu de la matrice métallique, augmentant ainsi la déformation en compression du HCCI/ZTAP composites sous contrainte de compression et affectant également sa résistance à la compression. Lorsque la contrainte atteint la valeur de crête, on peut considérer que l'endommagement s'est déjà produit dans l'éprouvette. Avec l'augmentation continue de la déformation, les dommages internes du matériau s'accumulent également, la résistance à la déformation diminue progressivement et finalement la rupture par cisaillement se produit.
Les microanalyses de la dureté de tous les échantillons sont présentées sur la figure 10. Comme indiqué sur les figures 10a, b, la zone de test est sélectionnée autour des particules arrondies et des particules aux angles vifs, respectivement, afin de mieux correspondre aux résultats de la simulation. La figure 10c, d est comparée à la vue partielle agrandie de la contrainte. Dans la simulation, la concentration de contraintes a tendance à se produire autour des angles vifs des particules. Dans les résultats des tests, le module près des particules aux angles vifs est supérieur à la matrice métallique à proximité des angles arrondis, ce qui vérifie davantage la rationalité du modèle basé sur la particule réelle.
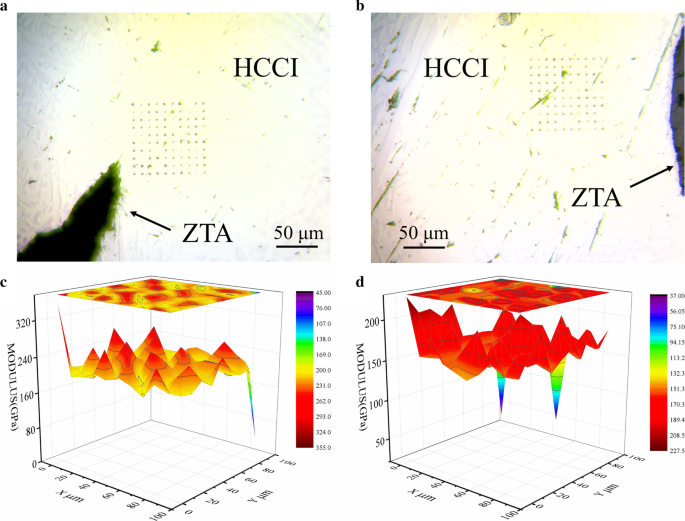
Distribution d'indentation des matériaux composites et distribution du module d'Young autour des particules de matériaux composites. un La forme des particules est nette, b la forme des particules est arrondie, c la forme des particules est pointue, d la forme des particules est arrondie
Un trou circulaire est ajouté aux zones d'agrégation des particules des préformes, qui a trois fonctions. La première fonction est de réduire la fraction volumique de particules de céramique dans le HCCI/ZTAP matériau composite et réduire la contrainte résiduelle ; la deuxième fonction est de réduire l'agglomération des particules céramiques de la préforme; la troisième fonction est d'augmenter la fraction volumique de la matrice métallique avec une meilleure plasticité pour empêcher la propagation des fissures. La plasticité du HCCI/ZTAP composites diminue avec l'augmentation de la contrainte résiduelle. La fraction volumique des particules de céramique diminue et la contrainte résiduelle devient relativement faible. L'ajout de trous circulaires dans la préforme de particules de céramique ZTA peut réduire les fissures car l'instabilité des fissures a tendance à s'étendre le long d'une ligne droite. Lorsque des fissures sont générées dans la zone composite de HCCI/ZTAP matériau composite, les fissures s'étendent facilement le long de la paroi du trou hexagonal dans la préforme pour générer une propagation des fissures. Le trou circulaire augmente le contenu de la matrice HCCI à la jonction de la paroi du trou hexagonal, entrave la propagation des fissures et joue ainsi un rôle dans le durcissement de la structure.
Conclusion
La grande différence de coefficient de dilatation thermique entre HCCI et ZTAP provoque des fissures dans le matériau composite. Le processus de solidification et de compression de HCCI/ZTAP les matériaux composites sont simulés à l'aide du logiciel d'éléments finis, et les valeurs numériques et les distributions des contraintes analysées sur la base d'un modèle complet simplifié et d'un modèle de grain équivalent pour la préforme. D'après les résultats du calcul, la structure de la préforme est optimisée. En analysant la simulation et les résultats expérimentaux, on peut conclure que l'ajout de trous circulaires à la préforme poreuse hexagonale entraînera une diminution de la contrainte thermique et de la contrainte de compression lors de la solidification. Après l'optimisation et l'ajustement du modèle, les résultats de la simulation tendent à être cohérents avec les résultats expérimentaux. Les méthodes décrites dans cet article peuvent fournir une référence importante pour la simulation et l'optimisation des paramètres de traitement dans les systèmes de coulée des divers composites à matrice métallique.
Disponibilité des données et des matériaux
Les ensembles de données soutenant les conclusions de cet article sont inclus dans l'article.
Abréviations
- HCCI :
-
Fonte à haute teneur en chrome
- ZTA :
-
Alumine durcie à la zircone
- HCCI/ZTAP :
-
Composites à matrice en fonte à haute teneur en chrome renforcés par des composites de particules de céramique d'alumine durcie à la zircone
Nanomatériaux
- Les pompes AODD peuvent être la meilleure solution pour améliorer la production de céramique
- Conseils pour l'utilisation de composites thermodurcissables dans l'industrie CVC
- Comment monter dans le modèle de maturité IIoT pour l'industrie manufacturière
- Les scientifiques d'IBM inventent un thermomètre pour l'échelle nanométrique
- 3 façons dont les entreprises utilisent les composites dans l'aérospatiale pour l'avenir
- La valeur du découpage en nuage et de la gestion de fichiers pour l'impression 3D
- Optimisation des couches minces hautement réfléchissantes pour les micro-LED plein angle
- La conception de la couche d'émission pour les multiplicateurs d'électrons
- La pandémie est à l'origine d'un nouveau modèle de prise de décision dans la chaîne d'approvisionnement