Moulage par injection robotisé pour composites fonctionnalisés
Anybrid GmbH (Dresde, Allemagne) est une entreprise dérivée de l'Institute for Lightweight Engineering and Polymer Technology (ILK) de la TU Dresden. ILK travaille avec l'industrie pour développer de nouvelles technologies légères, en mettant l'accent sur les composites polymères renforcés. « Nous avons développé cette machine de moulage par injection robotisée il y a deux ans pour produire des composants hybrides », explique Michael Stegelmann, directeur commercial d'Anybrid. Les composants hybrides font référence à la fonctionnalisation d'une structure - par exemple, un tube composite ou un châssis de véhicule électrique en métal - avec du plastique moulé par injection pour créer des points d'attache locaux, des nervures de renforcement, etc.
Ce processus, appelé surmoulage ou moulage par injection hybride, a attiré beaucoup d'attention au cours des 5 à 6 dernières années, mais sous une forme plus traditionnelle - des moules en acier dans une presse à mouler avec une unité d'injection attachée. Anybrid a essentiellement miniaturisé cette configuration dans l'effecteur terminal en forme de C rouge et noir montré sur le robot Kuka dans l'image ci-dessus et la vidéo ci-dessous. Le résultat est révolutionnaire, permettant de surmouler des pultrusions ou des extrusions à leur sortie de la matrice de moulage ou de fonctionnaliser de grandes structures au fur et à mesure qu'elles descendent une ligne d'assemblage.
ROBIN
ROBIN, abréviation de « moulage par injection robotisé », a été présenté pour la première fois en 2019 au salon K à Düsseldorf, en Allemagne. « Nous avons ensuite fondé l'entreprise l'année dernière et travaillons maintenant avec des clients pour établir des lignes de production pilotes utilisant l'équipement », explique Stegelmann. Le concept, explique-t-il, est de réduire la masse de la machine de moulage par injection en utilisant de petites unités d'injection et des outils de moulage compacts et peu coûteux qui peuvent être rapidement remplacés.
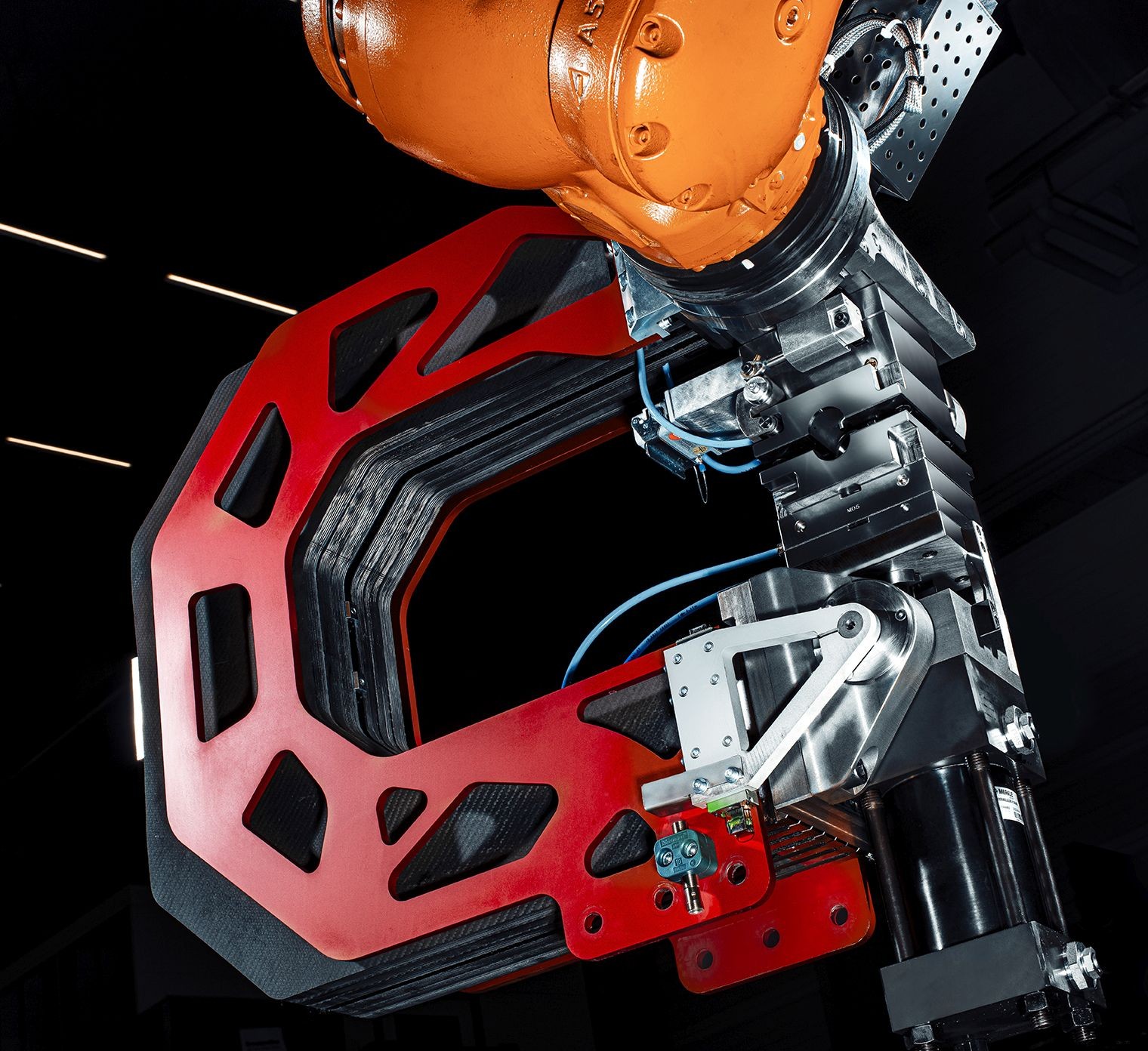
« L'effecteur terminal ROBIN comprend un cadre en C en composite de fibre de carbone et à l'extérieur, vous voyez un cadre en aluminium », explique Stegelmann. "Le cadre contient le système de verrouillage léger, qui gère jusqu'à 12 tonnes de forces de chargement pendant le moulage par injection, amenées du côté supérieur vers le côté inférieur du moule." ROBIN peut également atteindre un porte-à-faux de 1 mètre à travers de grandes structures. « C'est notre savoir-faire au sein d'ILK :comment utiliser la fibre de carbone et les matériaux légers de la bonne manière. »
L'approche traditionnelle du moulage par injection nécessite de grandes presses et des outils de moulage coûteux. Ainsi, elle s'est limitée à la production en grande série/en grand volume. En revanche, ROBIN permet la fabrication de petites séries ou de multiples moulages différents sur des composants plus grands. « Le principe est que nous avons une telle flexibilité dans les machines que nous pouvons fonctionnaliser presque n'importe quel matériau ou structure composite », note Stegelmann.
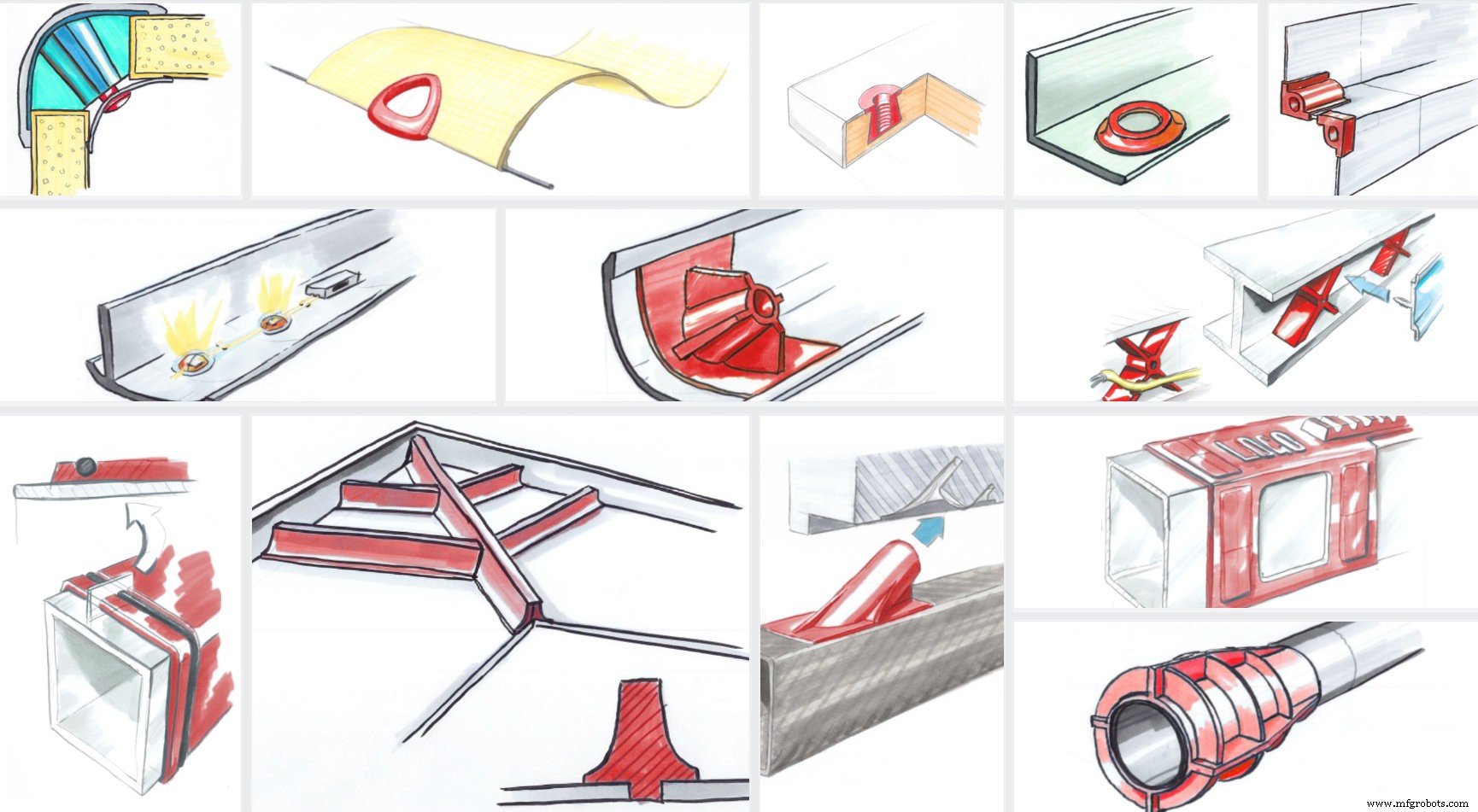
« Nous essayons de minimiser la taille des moules pour réduire les coûts, vous n'avez donc besoin que de quelques milliers d'euros pour construire le moule », explique Stegelmann. « Cela permet un système de changement rapide intégré car seule une petite zone de moule doit être changée. L'idée, par exemple, est que vous ayez une chaîne de montage avec la possibilité de changer rapidement de moule et de faire une pièce différente sur deux côtés différents de la ligne. Vous pouvez utiliser deux systèmes Robin ou un système Robin et changer rapidement de moule. Vous disposez donc d'une grande flexibilité."
Cette réduction de taille limite la zone qui peut être surmoulée. "Pour le moment, nous sommes limités à 50-60 grammes pour le tir d'injection", explique Stegelmann. « Nous avons développé ROBIN pour un poids de 140 kg seulement, ce qui permet d'utiliser une automatisation plus petite et plus abordable. Nous nous concentrons actuellement sur la fonctionnalisation des tuyaux et des profilés et sur l'ajout d'éléments plus petits à des structures plus grandes. »
Réussir une bonne adhérence en surmoulage
"C'est en fait notre parcours", déclare Stegelmann, faisant référence aux quatre co-fondateurs d'Anybrid. « Nous avons fait cela dans de nombreux projets au cours des 10 ou 15 dernières années, en combinant différents matériaux et en trouvant le bon collage, j'ai fait mon doctorat sur les procédés d'extrusion, et c'est toujours un défi lorsque vous combinez différents matériaux. Vous avez toujours besoin d'une préparation supplémentaire pour le collage, comme un traitement plasma ou un traitement laser, pour modifier la structure de la surface, en particulier lors du collage de plastique ou de plastique renforcé sur du métal. Les composites sont un peu plus faciles, car vous pouvez faire correspondre la matrice polymère dans le matériau de moulage par injection et le substrat. »
Par exemple, dans le tube surmoulé illustré ci-dessous, Mitsui Chemicals Europe (Düsseldorf, Allemagne) a fourni les rubans unidirectionnels (UD) en polypropylène (PP) renforcé de fibres de carbone et INOMETA (Herford, Allemagne) les a utilisés pour produire des tubes composites, qu'Anybrid a ensuite surmoulé. « La fonctionnalisation était faite du même matériau que les tuyaux », explique Stegelmann. « Nous l'avons surmoulé avec du PP non renforcé et renforcé de fibres de carbone, mais aussi avec des renforts en fibre de verre. Avec ROBIN, vous pouvez fabriquer avec n'importe quel matériau thermoplastique du marché. »
C'est pourquoi Anybrid accompagne ses clients dans les tests. « Nous avons des clients qui ne sont pas sûrs que leurs matériaux se lieront les uns aux autres », note Stegelmann. « Nous leur demandons de nous envoyer une partie du matériel et nous fabriquons ensuite de petites structures simples à tester. Nous avons un petit moule pour une nervure de raidissement que nous pouvons mouler par injection sur différentes plaques. Par exemple, si le client nous envoie des échantillons de certaines plaques composites, nous pouvons les surmouler avec leurs matériaux de moulage par injection. C'est la première étape, que nous avons une étude de faisabilité du comportement de collage des différents matériaux. Après cela, nous pouvons faire des analyses et proposer des suggestions d'optimisation. »
Applications potentielles
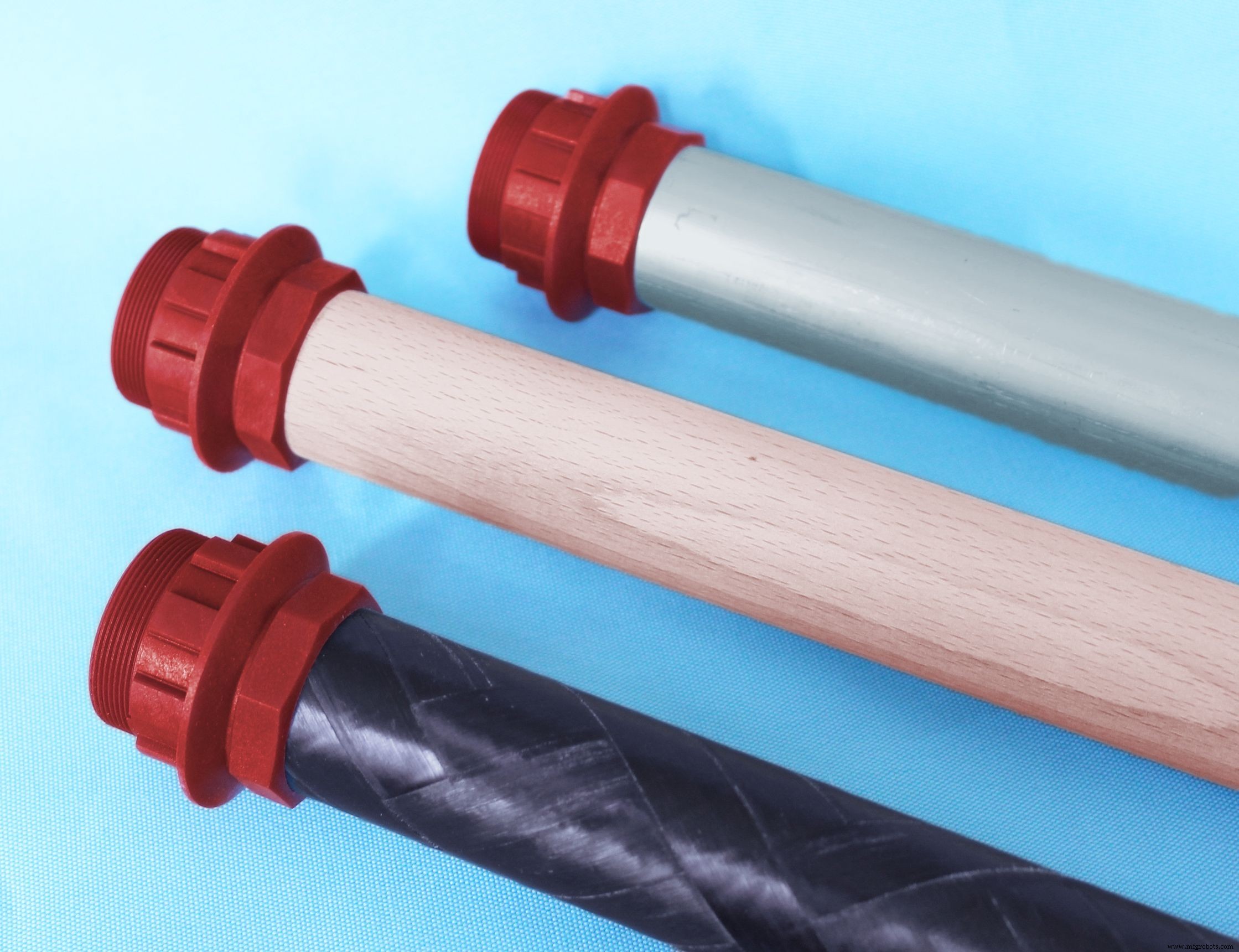
« Nous explorons toujours des applications, mais nous travaillons initialement avec des tuyaux et des profilés », explique Stegelmann. « L'une de nos idées est d'amener séquentiellement différentes structures sur ces formes continues et potentiellement très longues », explique Stegelmann. « Ainsi, les éléments peuvent être appliqués directement sur les tuyaux. De tels concepts sont déjà utilisés par INOMETA et Herone (Dresde, Allemagne) pour intégrer des systèmes de connexion axiale et des engrenages de forme. Cela peut également être intéressant dans l'industrie aéronautique, où vous avez besoin de diverses améliorations de la rigidité et souhaitez peut-être ajouter des fonctions telles que des accessoires. De plus, vous pouvez avoir un limon ou un cadre, par exemple, mais de nombreuses variations de longueur. Avec notre technologie, il y a la possibilité de maintenir un haut niveau d'automatisation et de simplement varier les éléments que vous fonctionnalisez d'une pièce à l'autre. »
« Il existe également un potentiel avec les composants de grande taille », déclare Stegelmann. « En travaillant chez ILK ces dernières années, nous avons développé de nombreux composants hybrides différents utilisant de l'acier, du plastique et des composites. Nous avons pu voir que les clips surmoulés sur les cadres structurels et le châssis ont du sens pour l'assemblage. Et avec le passage aux véhicules électriques et aux systèmes à hydrogène, nous constatons qu'il est important de rendre les chaînes de montage et les processus aussi flexibles que possible, pour se préparer à une variété de composants différents qui pourraient être nécessaires à l'avenir. Avec ROBIN, vous pouvez facilement ajuster les améliorations locales pour l'assemblage mais aussi pour la rigidité de la structure par exemple. Cependant, nous voulons étendre cette capacité au-delà de l'automobile et de l'aérospatiale. Notre idée était de rendre cela plus abordable pour les petites entreprises et de permettre cette technologie hybride pour de plus petites quantités dans d'autres domaines et d'autres applications. »
fibre
- PEEK à haute viscosité pour le moulage par injection et l'extrusion
- Matériaux en mousse pour moulage par injection ou compression
- Matériaux pour le moulage par injection-réaction (RIM)
- Moulage par injection :qu'est-ce que c'est, comment ça marche, à qui s'adresse-t-il ?
- Outillage souple ou dur pour le moulage par injection
- Moulage par injection plastique :une technologie pour les besoins actuels
- Top 10 des résines plastiques pour le moulage par injection
- Top 10 des résines plastiques pour le moulage par injection
- Présentation du moulage par injection médicale :moulage par injection de plastique pour l'industrie des dispositifs médicaux