L'enroulement filamentaire 3D permet le concept de siège de véhicule
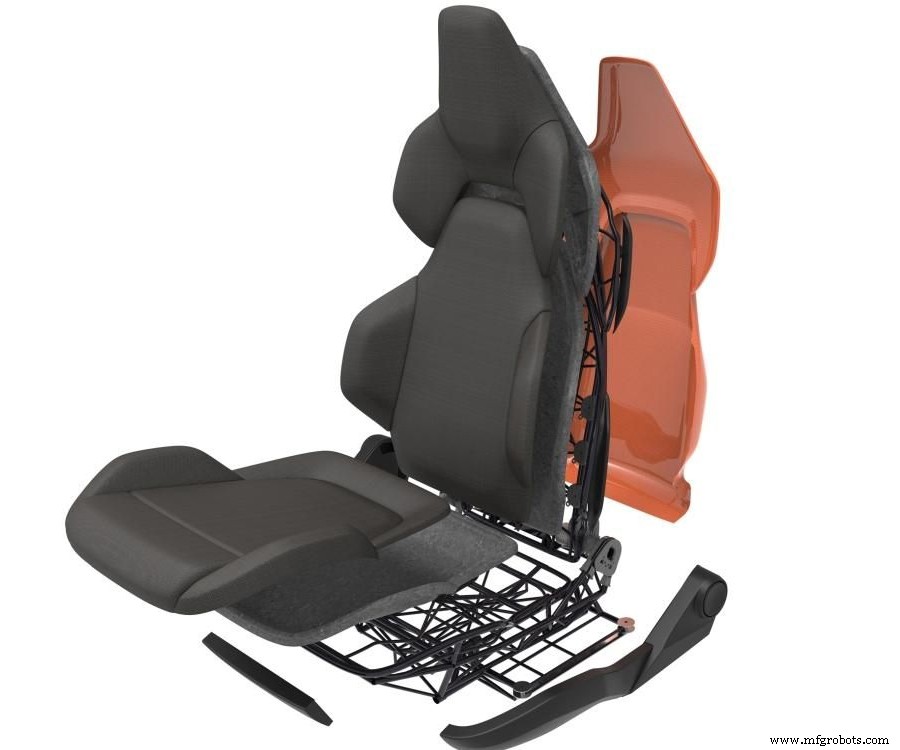
La durabilité et la responsabilité environnementale deviennent des moteurs de plus en plus courants des tendances technologiques dans l'industrie automobile. Les véhicules à faible consommation d'énergie et à faibles émissions sont devenus une priorité pour le secteur automobile international, et les tendances vers des technologies de transport alternatives telles que l'électromobilité et la mobilité aérienne urbaine (UAM) prennent de l'ampleur. Les équipementiers se tournent vers les matériaux et les processus émergents comme catalyseur de ces modes de déplacement potentiels, mais les changements dans le secteur automobile sont souvent lents. Pour que les nouveaux matériaux et procédés soient pleinement adoptés, ils doivent non seulement être qualifiés, ils doivent être rentables et ils doivent permettre une production en grand volume.
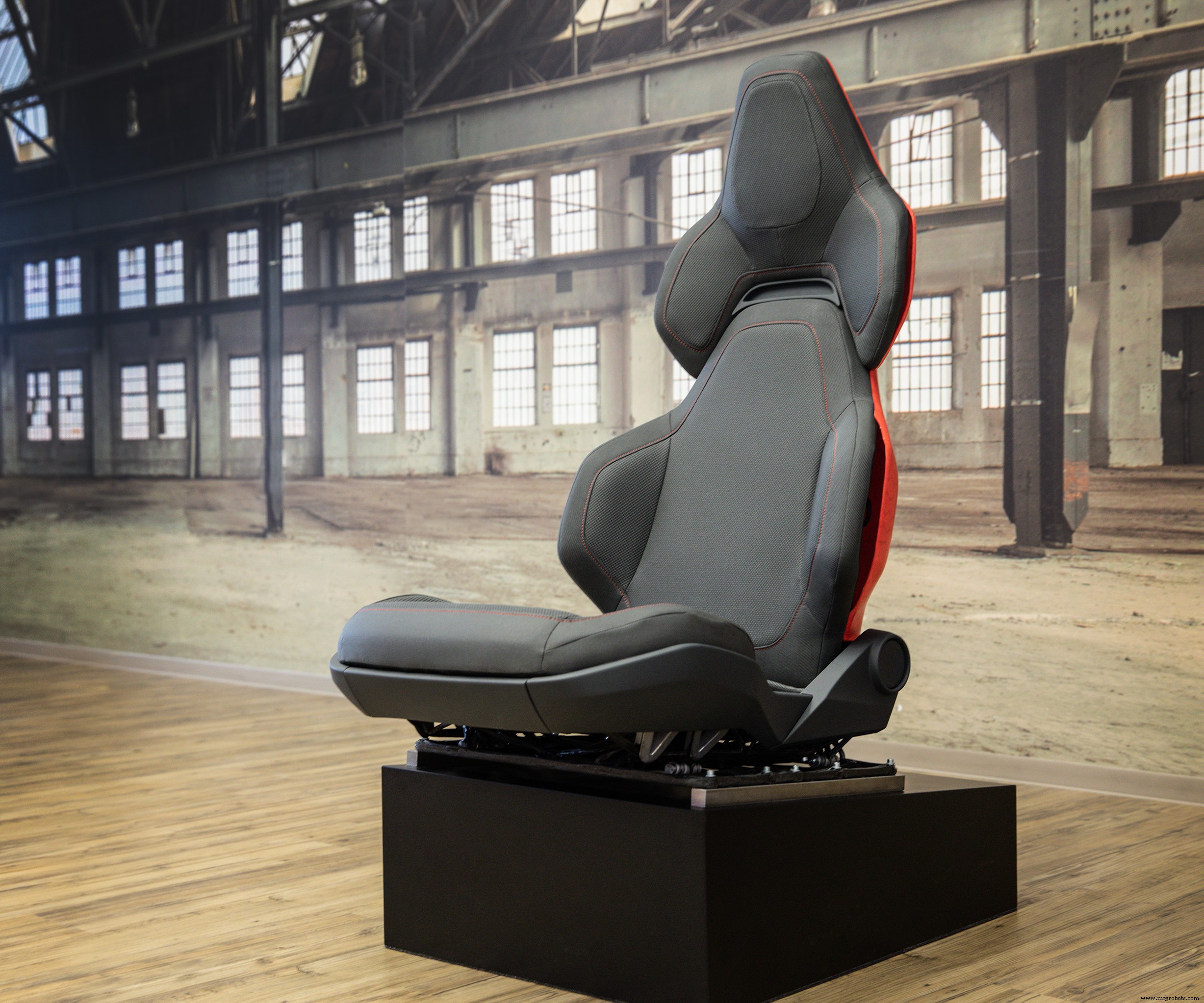
Siège ultra léger. Le concept de siège Ultra Leichtbausitz (ULBS) a été développé grâce à une collaboration entre plusieurs entreprises utilisant une combinaison de technologies. Origine | csi entwicklungstechnik
Récemment, un projet innovant présentant un potentiel pour le secteur automobile, ainsi que pour les marchés émergents tels que les hypercars et les taxis aériens, a démontré comment de nouveaux matériaux, procédés et technologies, ainsi qu'une collaboration étroite entre les entreprises, pourraient permettre des modes de transport de nouvelle génération. L'objectif du projet était de repenser complètement un siège d'auto en utilisant des technologies génératives de pointe, et de le faire en utilisant uniquement autant de bon matériau que nécessaire au bon endroit — et pour donner des résultats rapidement. Le prototype de siège de véhicule hybride ultra-léger et composite métal qui en résulte a été développé, de la conception à la fabrication, en seulement sept mois, grâce à une approche de conception basée sur la simulation, des méthodes de gestion de projet agiles et une coopération et une intégration de système étroites entre les entreprises impliquées.
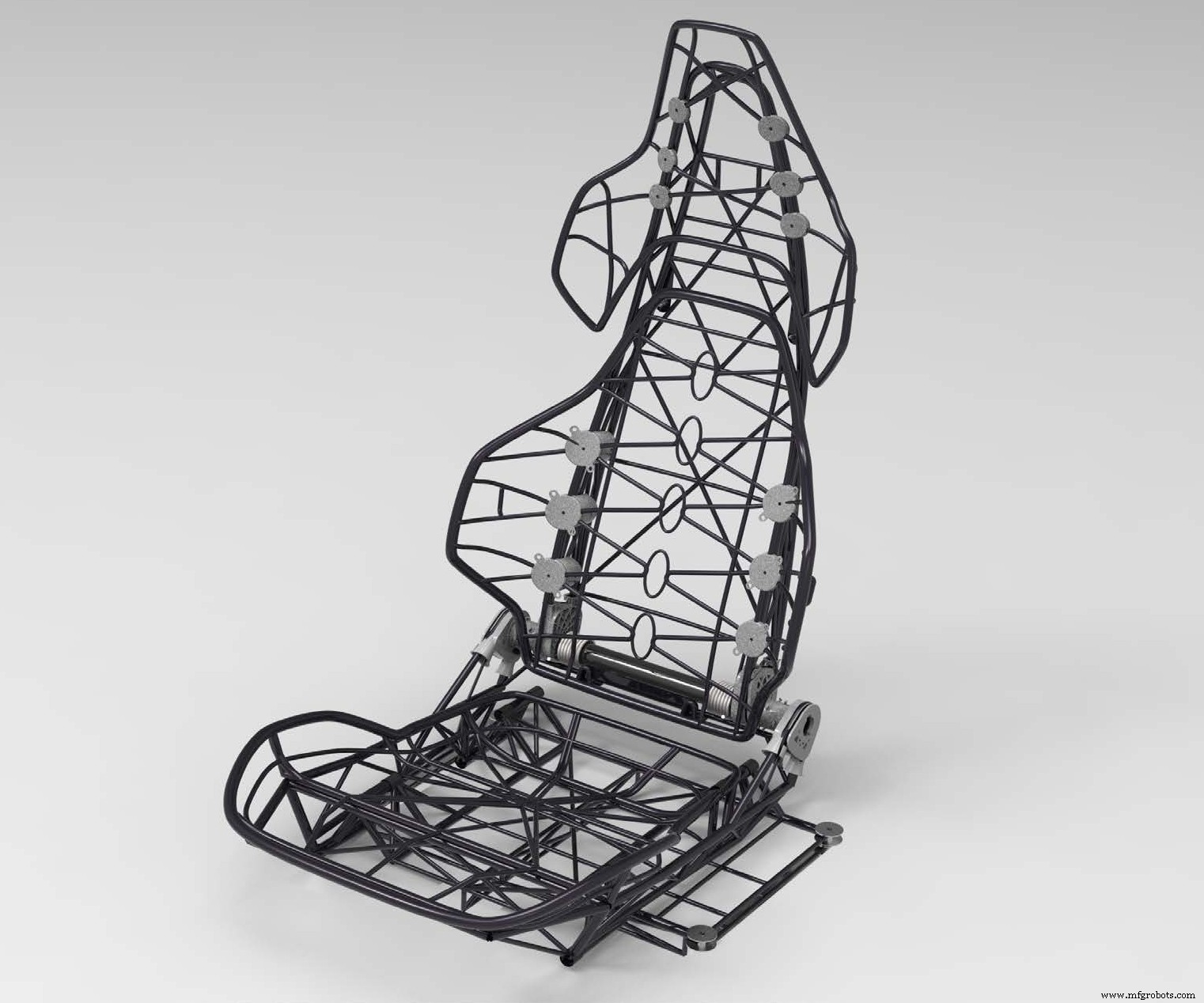
Construire un meilleur siège
L'étude de faisabilité du siège ultraléger Ultraleichtbausitz (ULBS) a été développée grâce à une collaboration entre plusieurs entreprises utilisant une combinaison de technologies. La vision du projet était, selon les termes du groupe, « de créer un concept d'assise ultraléger, exceptionnel sur le marché en termes d'optimisation de son poids ». Les entreprises initiatrices csi entwicklungstechnik GmbH (csi, Neckarsulm, Allemagne), Alba Tooling &Engineering (Forstau, Autriche) et Automotive Management Consulting (AMC, Penzberg, Allemagne) ont développé le prototype de concept de siège en collaboration avec Covestro (Leverkusen, Allemagne), LBK Fertigung (Friedberg, Allemagne), Robert Hofmann (Lichtenfels, Allemagne) et 3D|CORE (Herford, Allemagne).
Le projet collaboratif a abouti à un prototype de siège d'un poids d'un peu plus de 10 kilogrammes, qui comprend le coussin, le cadre structurel, les inserts fonctionnels et la console d'assise qui permet de le monter sur un véhicule. Le siège est 20 % plus léger que les sièges légers comparables sur le marché, dont beaucoup sont des sièges de rechange. Selon Stefan Herrmann, chef de projet de l'ULBS, responsable de la conception légère chez CSI, il n'existe actuellement aucun siège concurrent sur le marché pesant moins de 12 kg.
« Cependant, une comparaison directe n'est souvent pas comparable à la pomme, car les sièges du marché secondaire n'incluent souvent pas la console d'assise dans la définition du poids », déclare Herrmann, « De plus, le confort d'assise de l'ULBS est beaucoup plus élevé que celui des sièges avec poids similaire. Les sièges existants sont souvent des sièges baquets, qui sont encore plus légers mais pas aussi confortables, ou des sièges supersports traditionnels, qui ont un poids beaucoup plus élevé. »
L'ULBS dispose de plusieurs technologies innovantes, parmi lesquelles la structure de squelette de mèches de fibres basée sur la technologie de processus xFK en 3D joue le rôle le plus important. (Voir « Enroulement de filament, réinventé » pour en savoir plus sur xFK en 3D et d'autres technologies d'enroulement de filament.) L'importance fondamentale de la technologie primée pour le dépôt de mèches de fibres sans fin réside dans sa liberté de conception, dans la simulation et le matériau placement optimisé des fibres exactement dans le sens de la charge ainsi que dans l'application simple, économique et sans déchets du matériau fibreux. Pour le transfert de charge dans cette structure de charpente, des pièces imprimées en 3D ont été utilisées. Dans les zones les plus sollicitées, telles que les fixations du dossier, le siège utilise des structures imprimées en 3D en acier inoxydable à haute résistance et à module élevé. Dans les zones moins chargées, l'impression 3D en aluminium est utilisée.
csi entwicklungstechnik, une société d'ingénierie spécialisée dans les structures de carrosserie de véhicule en blanc (BIW), ainsi que dans les intérieurs et extérieurs d'automobiles avec des domaines d'activité tels que les polymères renforcés de fibres de carbone (CFRP) et la fabrication additive, a supervisé et coordonné le projet sur la base de la idée initiée par AMC. csi a fourni le style, le surfaçage, le concept, la simulation, l'ingénierie de conception et la gestion de projet pour le projet.
Herrmann explique :« csi était responsable des lots de travaux dans le domaine de la chaîne de processus numérique — stylisme, conception technique, conception de surfaçage, simulation CAE, simulation de topologie, simulation de validation et confirmation virtuelle du projet. »
Il souligne que ce qui rend le projet ULBS remarquable n'est pas seulement l'utilisation de matériaux et de méthodes de fabrication innovants, mais le développement d'une pièce complexe qui comprend de nouvelles conceptions de composants dans un court laps de temps de sept mois en utilisant une étroite collaboration entre les partenaires.
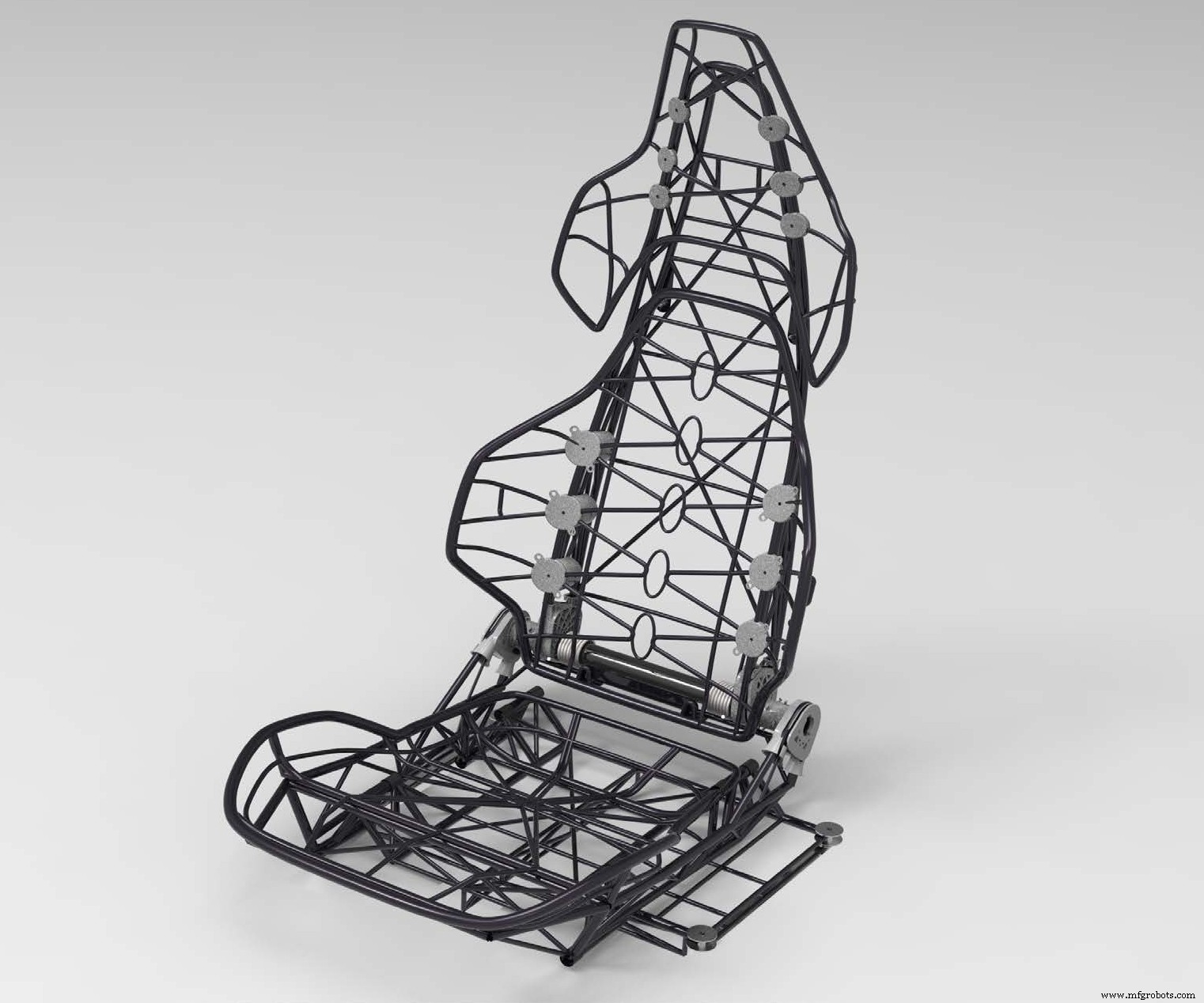
Cadre de siège enroulé par filament. Une grande partie de la réduction de poids dans le projet ULBS résulte de la technologie de processus d'enroulement de fibres d'AMC xFK en 3D. Origine | csi entwicklungstechnik
Enrouler un cadre
Une grande partie de la réduction de poids dans le projet ULBS résulte du xFK d'AMC en 3D, une technologie de fibre composite hautement flexible, configurable, rentable et durable pour les composants d'enroulement.
xFK en 3D a déjà été utilisé pour une variété de produits et d'applications pour divers secteurs et segments de marché. SGL Group Wiesbaden, Allemagne) a présenté plusieurs pièces automobiles et de bicyclettes fabriquées grâce à cette technologie au salon international des composites JEC World 2018. L'une des pièces exposées, un anneau de chaîne de bicyclette en fibre de carbone développé par AMC, est censée réduire le poids jusqu'à 70 %. par rapport à une version en aluminium.
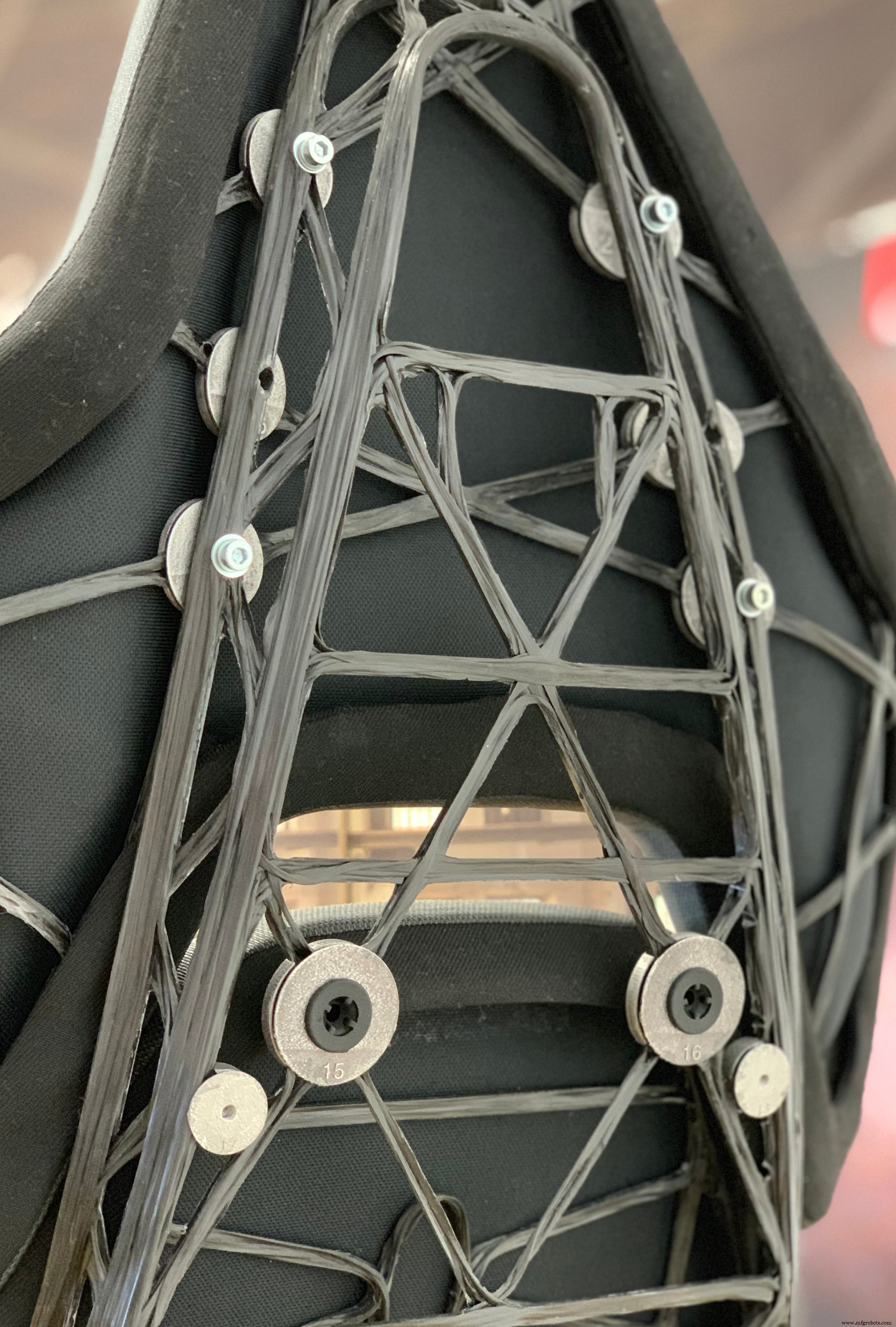
Douilles d'enroulement. Une mèche de fibres thermodurcissable imprégnée de résine est enroulée autour d'un dispositif de positionnement, permettant aux fibres d'être arrangées pour correspondre aux charges de chaque pièce et aux fonctions souhaitées. Origine | csi entwicklungstechnik
Le procédé xFK en 3D enroule les structures porteuses sans déchets à l'aide de fibres continues imprégnées de résine thermodurcissable. Une mèche de fibres saturée de résine époxy est enroulée autour d'un dispositif de positionnement ou de bagues d'enroulement, permettant aux fibres d'être arrangées spécifiquement pour correspondre aux charges de chaque pièce et aux fonctions souhaitées.
« L'un des principaux avantages de xFK en 3D est l'élimination des points faibles concernant le transfert de charge et l'introduction de charge dans les structures », explique Herrmann. Il explique que les points faibles ne se trouvent souvent pas dans le continuum de la structure, mais dans les zones où des charges sont introduites dans la structure, en particulier là où les composants voisins sont connectés à la structure. La technologie xFK en 3D permet des transferts de charge à travers les connexions et permet d'aligner les fibres en fonction des fonctions des composants et des cas de charge souhaités, et de les fabriquer en trois dimensions.
Le processus d'enroulement filamentaire offre également des avantages supplémentaires. Le processus aide à minimiser les déchets de matériaux :moins de 1 % de la mèche de fibres est gaspillée.
csi a reconnu xFK dans les points forts de 3D et a conçu le cadre du siège ULBS à construire sous les conseils du Dr Clause Georg Bayreuther, responsable de la technologie d'AMC.
"En collaboration avec les ingénieurs csi, les consultants AMC et les experts en outillage d'Alba ont développé ce concept et cette structure pour que le cadre du siège soit fabriqué à l'aide du processus xFK en 3D", explique Peter Fassbaender, consultant en technologie et initiateur de xFK en technologie 3D.
Alba a fabriqué l'outillage pour le cadre du siège en PRFC et a fourni une assistance technique. De plus, bien que le cadre du siège ait été enroulé à partir de fibre de carbone, les fibres naturelles ou les fibres de basalte sont également de bons candidats.
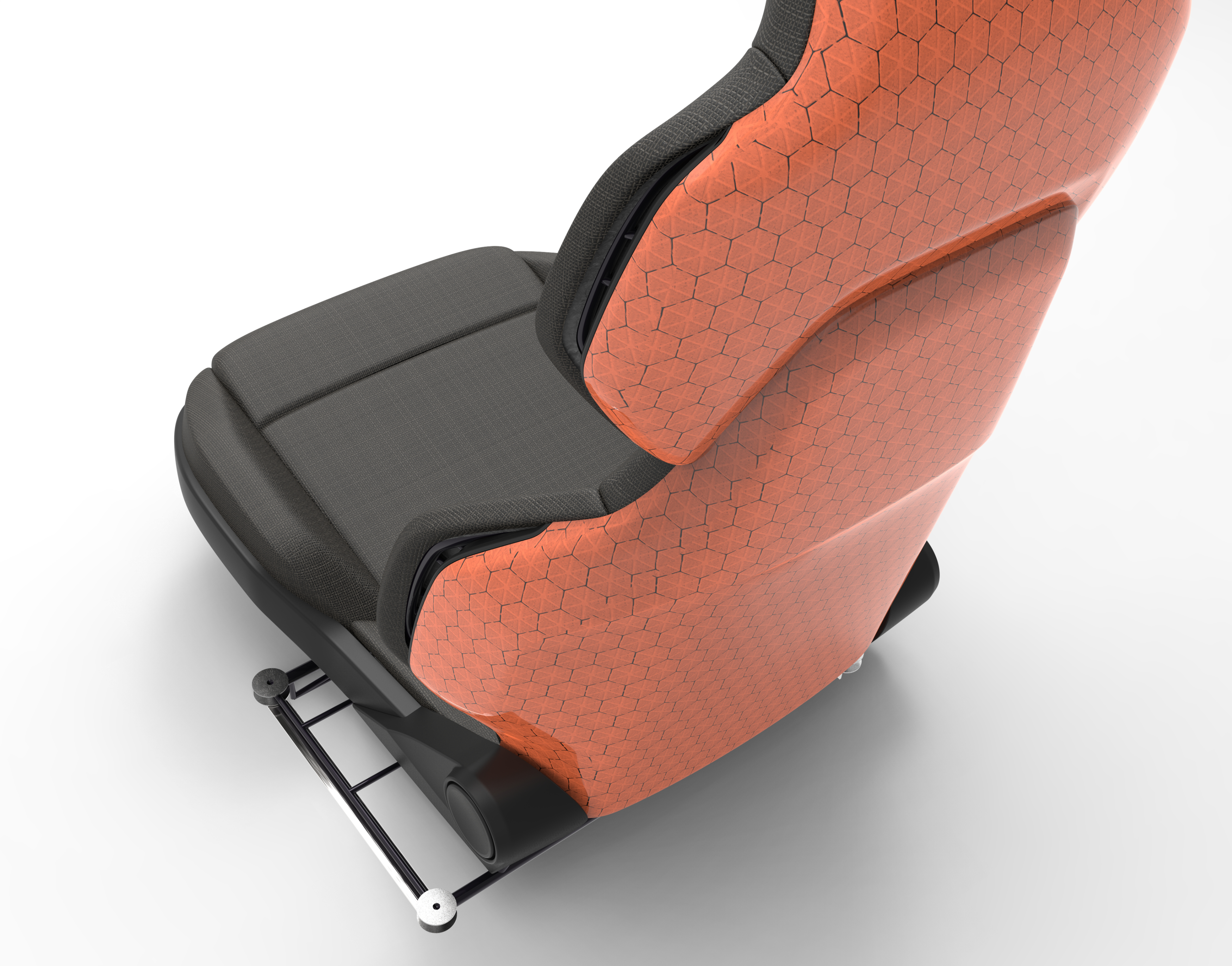
Nouvelles technologies. Le prototype ULBS utilise une combinaison de nouvelles technologies, notamment une coque de panneau arrière en matériau de noyau de renforcement intralaminaire (IRC) et des coussins de dossier de siège imprimés en 3D en polyuréthane thermoplastique (TPU). Origine | csi entwicklungstechnik
Une structure matérielle hybride
En plus du cadre, le prototype ULBS comprend plusieurs autres nouveautés. Alba, qui a fourni l'outillage, a également fourni l'outillage, l'ingénierie et la fabrication du corps en mousse du siège et a exécuté l'assemblage du siège. Un tapis en fibre polaire recouvre le cadre en PRFC du siège qui est ensuite recouvert d'une housse en mousse PUR imprimée en 3D. La zone du coussin d'assise est en mousse traditionnelle.
Une réduction supplémentaire du poids a été obtenue grâce à l'utilisation de 3D|CORE, un matériau de noyau de renforcement intralaminaire (IRC), dans la structure de coque du panneau arrière du dossier du siège. Le matériau est un matériau de noyau de renforcement intra-laminaire (IRC) - un noyau sandwich structurel qui comprend des corps en mousse de polystyrène extrudé (XPS) et de polyéthylène téréphtalate (PET) dans un motif en nid d'abeille intégré. Lors de la production de pièces composites, la structure en nid d'abeille est remplie de résine, ce qui entraîne une résistance intra-laminaire élevée. Le 3D|Core est assemblé entre deux couches de fibre de verre pour créer une préforme, qui est infusée de résine époxy thermoplastique à l'aide d'un moulage par transfert de résine sous vide (VA-RTM).
Covestro a fourni son adhésif Dispercoll comme liant pour les tapis en fibre polaire, ainsi que le coussin de dossier imprimé en 3D. Selon Herrmann, les propriétés mécaniques de Dispercoll offrent une bonne résistance à l'abrasion, ce qui est important car le contact de surface entre le coussin et le cadre peut soumettre le molleton à l'usure au fil du temps.
« Si vous avez une seule mèche de fibres, lorsque vous la placez dans un textile, vous obtenez des micro-mouvements entre les parties dures en PRFC et les tapis en polaire. Les composants du cadre du siège peuvent frotter contre le textile et le détruire », explique Herrmann.
Les sièges traditionnels ont généralement une plus grande surface supportant le rembourrage, et n'ont pas ce problème. Avec xFK en 3D, cependant, il y a une plus petite surface de contact en raison de la structure du cadre.
« Lorsque xFK dans les structures 3D poussent contre le tissu polaire, vous devez disposer d'un liant spécifique et durable; c'est ce que Dispercoll propose dans ce contexte », ajoute Herrmann.
Covestro a également fourni ce qui serait le premier coussin imprimé en 3D au monde. Alors que la mousse conventionnelle et intensive en outillage est généralement utilisée dans les dossiers de siège, l'utilisation des coussins de dossier de siège imprimés en 3D, qui sont fabriqués à partir de TPU (polyuréthane thermoplastique), augmente encore la flexibilité et l'adaptabilité du siège ULBS en ce qui concerne son esthétique, options d'intégration fonctionnelle et confort.
Un siège pour l'avenir
Le projet ULBS atteint plusieurs objectifs. Le concept résultant, bien qu'il ne soit pas encore sur le marché, a le potentiel de servir de nombreux marchés de niche tels que les hypercars, les taxis aériens, les véhicules ultra-légers, la micromobilité, les hélicoptères, les multicoptères et aéronautique. Bien qu'il soit certes plus cher que les sièges d'auto de production, l'ULBS démontre plusieurs technologies qui minimisent les déchets, réduisant ainsi les coûts des matériaux. En comparaison avec d'autres technologies de fibre de carbone, xFK en 3D génère une très faible quantité de déchets. En fait, tout le projet vise à utiliser un minimum de ressources et seulement le minimum nécessaire de matériel. L'ULBS offre également la possibilité d'utiliser des ressources renouvelables et durables telles que les fibres naturelles dans la structure du cadre, les coussins et les textiles.
Mais plus important encore, le projet démontre comment les entreprises peuvent minimiser les délais de mise sur le marché en travaillant ensemble grâce à des procédures de coordination courtes et agiles. C'est également un bon exemple d'utilisation du design thinking pour réussir à faire passer un produit de l'idée au prototype matériel en se concentrant sur les exigences fonctionnelles et en anticipant les applications futures et les objectifs de durabilité.
fibre
- Configurations d'enroulement
- Siège de vélo
- Monocycle
- Siège de sécurité pour enfants
- La puce à bande ultra-large permet l'accès aux véhicules depuis un smartphone
- La plate-forme informatique de pointe permet un accès approfondi aux données automobiles
- Caractéristiques de performance du fil de fibre de verre
- Les nouvelles technologies et les marchés à World of Filament événement Winding
- Enrouleur de filament Roth pour faciliter les grandes réductions de poids/coût d'Ariane 6