Soyez un requin :ramez et fraisez à grande vitesse avec MLCube !
Hudson Boat Works est un fabricant de coques de course d'aviron basé à London, en Ontario. Jack Coughlan et son beau-frère, Hugh Hudson, ont fondé l'entreprise en 1981. Hudson est un fabricant officiel de bateaux pour l'équipe nationale canadienne et leurs bateaux ont remporté 84 médailles mondiales et olympiques depuis 1984.
En mars 2007, Hudson Boat Works a commencé la production de sa gamme de bateaux "Shark". Leurs obus Great White 1x et Hammerhead 8+ sont actuellement conçus par Steve Killing (architecte naval canadien). Ces bateaux élégants sont plus rapides, plus stables et plus confortables pour les rameurs. Depuis 2005, Glen Burston, directeur des opérations, est le moteur de l'innovation d'Hudson. Glen a appliqué ses connaissances de maîtrise en ingénierie et son expérience de l'aviron au niveau national pour transformer l'entreprise en un succès de fabrication de pointe.
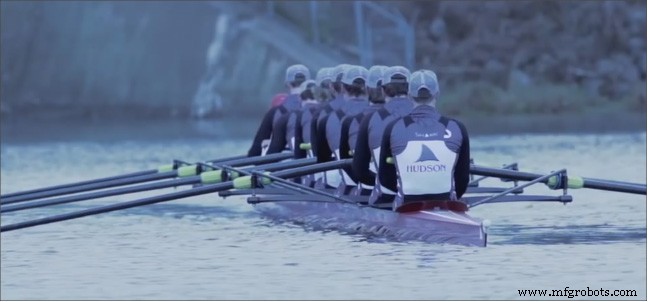
En 2015, des plans ont été établis pour construire une gamme de bateaux plus légers et plus rapides composés de tous les composants en fibre de carbone nommé Ultimate Super Predator (USP). La capacité d'Hudson à mettre rapidement cette gamme sur le marché renforcerait son avantage concurrentiel et sa position de leader de l'industrie. Cependant, leur capacité à le faire était entravée par la lenteur des délais d'exécution et les coûts élevés associés à l'externalisation de 90 % de leurs pièces usinées. En particulier, les moules en aluminium nécessaires à la fabrication de toutes les pièces en fibre de carbone qui composent un godille d'aviron devaient être achevés sur une période de 3 ans - et ce délai ne suffirait tout simplement pas.
Le technologue en génie mécanique d'Hudson, Cam Fisher, se souvient :"Nous avons un assez grand routeur CNC à 3 axes qui fait tout le rognage pour les coques de bateaux et tout le profilage des bords des bateaux, mais il n'a pas la précision nécessaire pour la fabrication de moules."
Ainsi, la recherche d'une nouvelle technologie d'usinage CNC a commencé. Il est vite devenu évident que les routeurs CNC standard n'auraient pas la précision dont ils avaient besoin pour la fabrication de moules, et avec leur plus grande partie étant de l'ordre de 64 pouces d'un bout à l'autre, un VMC conventionnel n'aurait probablement pas la quantité de zone de travail qu'ils avait besoin. Cela a été aggravé par le fait que l'espace qu'ils avaient alloué à la machine était de 20′ x 10′ (200 pieds carrés). Cependant, lorsque Glen Burston a trouvé DATRON, il semblait que tous les «points douloureux» de Hudson Boat Work pouvaient être résolus. Cam Fisher se souvient « En général, vous examinez vos machines Haas parce que ce nom est toujours présent et nous avons examiné d'autres usines plus grandes. Mais, Glen est tombé sur DATRON et quand Jack Coughlan leur a parlé, leur machine MLCube semblait juste avoir atteint tous les points dont nous avions besoin. Footprint était l'un des plus importants car nous n'avons pas beaucoup de place dans notre atelier pour installer un très grand moulin. Le MLCube ne prendrait pas trop de place et ce que nous pourrions faire avec un espace de travail de 60″ x 40″ serait irréel.”
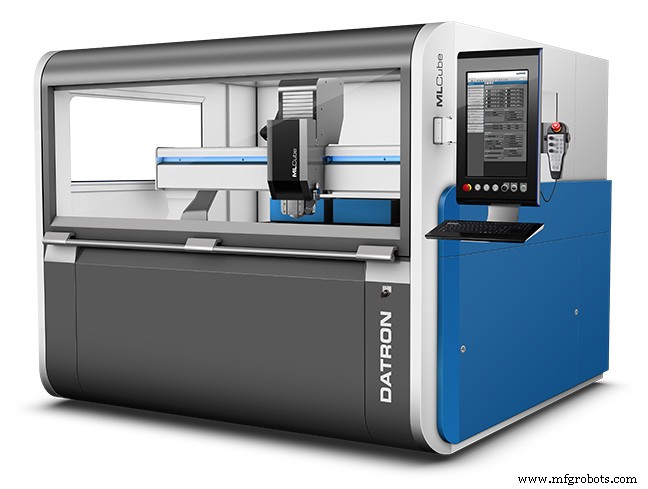
Il a été décidé que Hudson Boat Works enverrait son plus grand modèle à DATRON pour qu'il effectue un test d'ajustement dans son centre de technologie en Nouvelle-Angleterre. Cette partie incurvée ressemblait presque à un énorme boomerang avec une envergure de 64 pouces entre les deux pointes. Cela signifiait que DATRON devait faire preuve d'un peu de « créativité » avec le placement de la pièce et le déplacement d'un magasin d'outils sur le bâti de la machine. Mais, avec cette partie représentant un "scénario du pire", ils étaient convaincus qu'ils avaient la bonne solution pour Hudson.
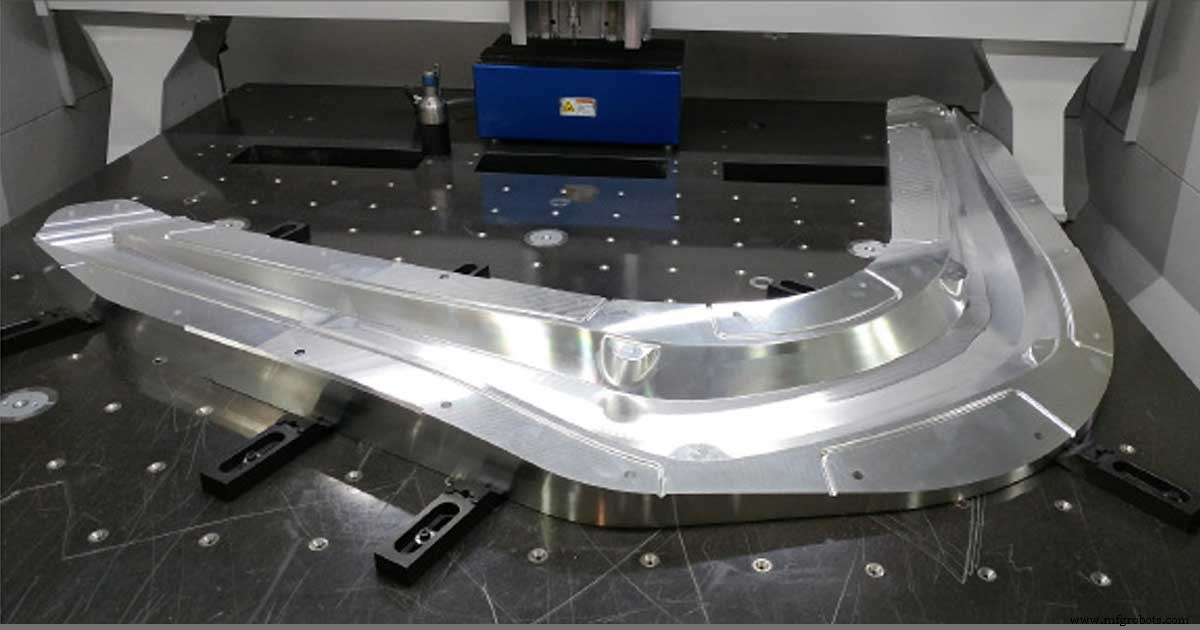
En fin de compte, cela s'est avéré vrai et Hudson était très enthousiaste à l'idée d'acheter le DATRON MLCube. Aujourd'hui, un peu plus d'un an plus tard, rapporte Cam Fisher, "L'introduction de la machine DATRON a été un énorme évitement de coûts dès le départ. À l'origine, nous envisagions la période de 2 à 3 ans pour obtenir tout ce dont nous avions besoin grâce à l'externalisation et le coût de ces très grands moules était astronomique. Avec le DATRON, nous sommes déjà au point où nous sommes prêts à tout offrir. En moins d'un an, nous sommes là où nous n'aurions pas été avant environ 4 ans. La mise sur le marché de cette gamme de bateaux USP nous a donné un énorme avantage concurrentiel.” https://www.youtube.com/embed/-gsNvltcJJQ?feature=oembed&enablejsapi=1&origin=https://www.datron.com
En plus des moules de fraisage qu'ils ont réalisés, Hudson Boat Works fabrique des pièces en aluminium pour le gréement de leurs bateaux et comme prévu, ils sont passés à cette phase de production pour leur nouvelle ligne. Fisher dit, "Maintenant, je sors de la fabrication de moules et j'apporte des pièces de production. J'avais encore un appareil de moulage sur la machine la semaine dernière et une autre pièce est arrivée et je n'ai jamais retiré l'autre appareil de la machine. Grâce aux coniques, j'ai positionné la nouvelle pièce où je le voulais et c'était parti et en marche. »
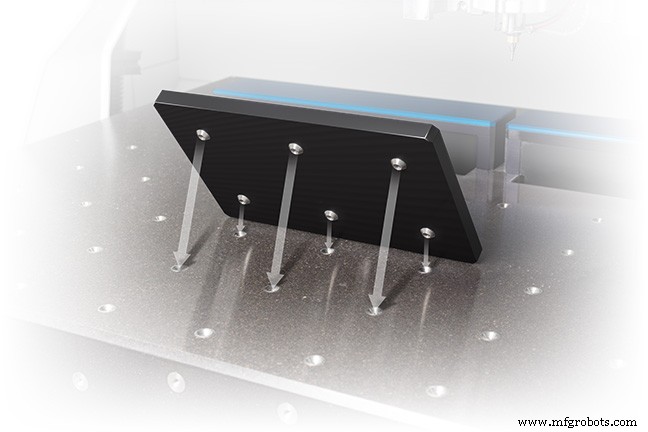
Fisher fait référence à un système de coniques intégré dans le lit du MLCube. Ces coniques sont utilisées pour positionner les pièces de serrage telles que les pinces, les palettes et les mandrins à vide. Les cavités coniques sont fraisées par la machine elle-même sur la surface de la table d'usinage. Il en résulte un système «boss-in-cavity» qui assure la répétabilité de la localisation. Ainsi, s'il est au milieu d'un lot de pièces et qu'un projet urgent inattendu se présente, il peut retirer un appareil et le remplacer par celui du nouveau travail. Lorsque le travail urgent est terminé, il remet le premier appareil à sa place et reprend là où il s'était arrêté. Parce que le MLCube a une si grande enveloppe de travail, il peut accueillir plus d'un
luminaire ou configuration et dans le cas mentionné par Fisher, il vient de trouver un espace vide sur le lit pour la nouvelle pièce.
Les pièces de gréement en aluminium que Fisher fabrique maintenant seront soudées sur les stabilisateurs du bateau et il a été impressionné par la façon dont les pièces se détachent de la machine "En utilisant de l'éthanol comme liquide de refroidissement pour ces pièces en aluminium, elles se détachent de la machine et allez directement à nos soudures – parce que l'éthanol s'évapore, il n'y a pas de post-travail à leur faire. Ils sont juste propres et prêts à être soudés. C'est un énorme gain de temps."
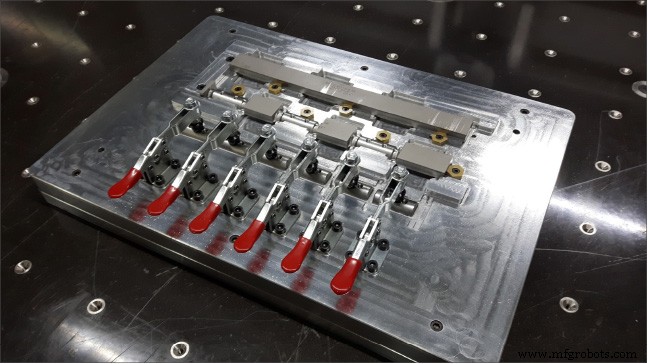
Mais l'aluminium n'est pas le seul métal que Hudson découpera sur la machine DATRON et Fisher commente des plans supplémentaires, "Nous apporterons également du titane. Avec toutes les pièces en fibre de carbone, tous les composants métalliques qui les composent sont en titane. Le titane n'est pas un métal amusant à couper, mais pour une partie que j'ai faite jusqu'à présent sur le DATRON, je tournais à 200-220 ipm qui est
incroyablement rapide et je compose toujours les flux et les vitesses."
Afin d'optimiser le programme pour la pièce en titane, Fisher a consulté le technicien d'application DATRON, Dann Demazure, et rappelle :"Les techniciens d'application de DATRON ont été formidables et m'ont envoyé de nombreuses informations pour m'aider dans mes efforts pour me connecter. les pièces en titane. Dann a fait une tonne de recherches pour moi. Comme je n'avais pas beaucoup d'expérience avec cela, il aurait été difficile de comprendre sans beaucoup d'essais et d'erreurs, mais les gars de DATRON réussissent toujours."
Ce type de relation entre les opérateurs et les techniciens d'applications DATRON est courant et est généralement initié au cours du processus de vente et renforcé lors de l'installation de la machine et de la formation. C'est le cas de Fisher et Demazure et Fisher dit :"Nous avons eu 3 jours de formation avec Dann Demazure, ici dans notre établissement et c'est vraiment tout ce qu'il a fallu, quelques jours et nous étions prêts à partir. C'était assez époustouflant de faire atterrir la machine et le lendemain, nous étions en train de couper des pièces. »
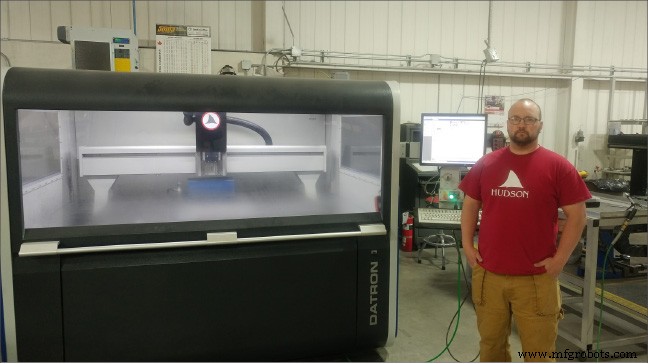
L'installation initiale comprenait l'intégration de HSMWORKS que Hudson Boat Works avait acheté en même temps que la machine DATRON. Fisher commente la facilité d'intégration, "En plus d'apporter le DATRON, nous avons également apporté un logiciel de FAO 3D que nous n'avions jamais utilisé auparavant. Nous externalisions tout, donc même si nous faisions un moule en interne, nous externalisions toujours toute la programmation. Nous avons opté pour HSMWORKS car nous sommes fortement basés sur SolidWorks ici. Le message fourni avec HSMWORKS pour DATRON ne pourrait pas être meilleur. J'étais un peu vert avec juste une certaine expérience avec les pièces plates 2D, mais après l'avoir fait fonctionner un peu, je pense que je pourrais former quelqu'un d'autre en 2 jours à utiliser cette machine même s'il n'avait jamais vu de DATRON auparavant… ou même jamais vu une machine CNC auparavant. C'est SI facile !"
commande numérique par ordinateur
- vos connaissances sur la fabrication avec les fraiseuses verticales
- Impression 3D haute vitesse avec AFPM
- Impression 3D haute vitesse avec AION500MK3
- Même les entreprises avec une maturité élevée de la chaîne d'approvisionnement ne se sentaient pas préparées au virus
- Comment accélérer la durabilité ? Avec un accélérateur, bien sûr
- Tour CNC à grande vitesse
- Machine de métal déployé à grande vitesse
- Broches à grande vitesse avec une grande force de couple
- Un aperçu complet des machines à grande vitesse