Ingénierie simultanée et séquentielle - Développement de nouveaux produits
Ingénierie simultanée et séquentielle
Concurrent et ingénierie séquentielle sont deux principales approches de flux de travail de conception de produits que les entreprises doivent suivre sur l'interaction entre les équipes fonctionnelles pour partager des informations au cours des 8 étapes du développement d'un nouveau produit.
Tout développement de produit prend du temps et la technologie impliquée pour créer des produits modernes est très complexe. Les entreprises ne peuvent plus compter sur quelques ingénieurs pour les concevoir, les développer puis les lancer. La révolution industrielle et les progrès technologiques continus qui ont suivi dans de nombreux domaines ont forcé les gens à se spécialiser dans un domaine, ce qui a obligé les entreprises à embaucher des employés spécialisés. Le développement de nouveaux produits modernes est un processus multidisciplinaire et repose sur des équipes fonctionnelles telles que des concepteurs industriels, des concepteurs de produits (ingénieurs en mécanique, électricité et logiciel), du personnel de fabrication, de marketing, etc., pour mettre le produit sur le marché. Les défis auxquels est confronté le NPD sont nombreux. Par conséquent, le NPD échoue plus souvent qu'il ne réussit.
La façon dont les différentes équipes fonctionnelles interagissent entre elles quand (à quelles étapes du développement) elles communiquent et la façon dont elles partagent les informations ferait une énorme différence dans leur quête d'un produit performant. En effet, ces facteurs affectent à leur tour le temps de développement, le coût du produit et la qualité du produit.
Qu'est-ce que l'ingénierie séquentielle (SE) ?
Ingénierie séquentielle traditionnelle est le terme utilisé pour décrire les processus de développement de produits linéaires, où les étapes de conception et de développement sont effectuées les unes après les autres en se concentrant sur un domaine d'expertise à la fois. Pendant la révolution industrielle, cela a obligé les entreprises à embaucher des personnes et des départements spécialisés en raison de la complexité croissante des produits. Ceci, à son tour, a ouvert la voie à une mentalité « par-dessus le mur » où chaque membre de l'équipe ou service se concentrait uniquement sur ses tâches et transmettait le travail terminé au suivant (Figure 1).
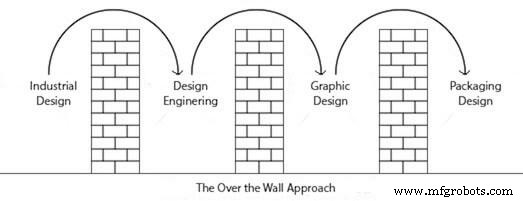
Ce processus traditionnel de développement de nouveaux produits basé sur la « cheminée » décrit une grande structure verticale qui n'interagit qu'en aval, avec les avantages et les inconvénients suivants.
Avantages et inconvénients de l'ingénierie séquentielle
Avantages de l'ingénierie séquentielle
- Facile à suivre les progrès et à comprendre les exigences du projet et des processus
- Il est bien défini pour chaque membre de l'équipe ou service
- Simple à comprendre et évite les erreurs d'interprétation
- Il s'agit d'une approche disciplinée imposée qui élimine tout malentendu
Inconvénients de l'ingénierie séquentielle
- Augmentation du temps de cycle du produit en raison de la reprise au cours des dernières étapes du NPD
- Les demandes de modification des autres dans les dernières étapes sont souvent très coûteuses et difficiles à gérer
- Sans retour d'information échelonné et sans grilles d'évaluation des spécifications, le produit peut s'éloigner ou ne pas répondre aux attentes
- Les coûts de fabrication et de production peuvent être trop difficiles et coûteux, ce qui rend le coût unitaire final non économiquement viable
Qu'est-ce que l'ingénierie simultanée (CE) ?
L'ingénierie simultanée est une approche développée dans les années 1980 pour éliminer certains des problèmes liés à la méthode « par-dessus le mur ». Il existe de nombreux avantages à l'ingénierie simultanée où différents départements travaillent simultanément sur les différentes étapes du développement de produits d'ingénierie tout en concevant et en développant de nouveaux produits d'ingénierie. Plus d'informations sur le développement de nouveaux produits d'ingénierie simultanée ici, y compris certains avantages clés.
Ingénierie simultanée vs ingénierie séquentielle
Examinons un parcours typique de développement de nouveaux produits suivi par une entreprise et explorons les différences entre l'ingénierie simultanée et l'ingénierie séquentielle.
Développement séquentiel de nouveaux produits
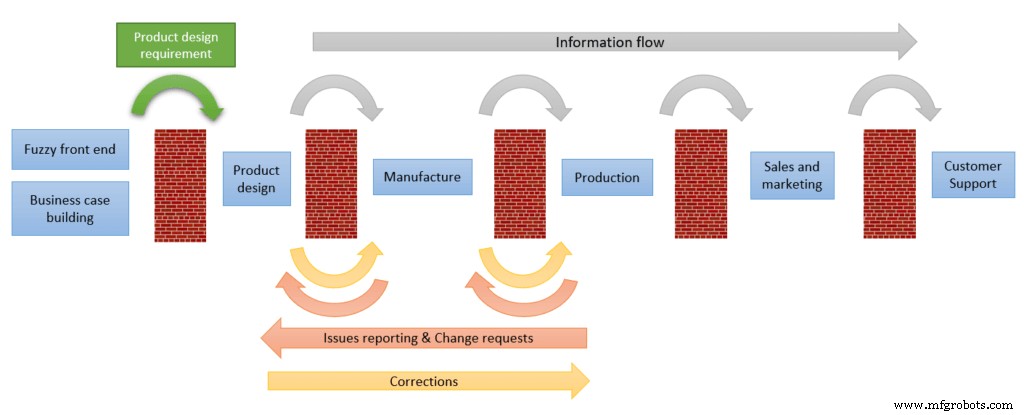
La figure 2 montre une équipe de développement de produits typique et ses fonctionnalités dans un flux de travail linéaire traditionnel.
- Après avoir identifié une opportunité de développement de produit et analysé l'analyse de rentabilisation lors de la phase initiale floue d'un NPD, la direction transmet une spécification de conception de produit (PDS) au service de conception et de développement.
- Si l'équipe de conception du produit n'a eu aucune contribution au cours du PDS, elle commencera le parcours de développement du produit avec du papier vierge. Les données de génération d'idées, d'évaluation et d'évaluation des clients ne sont pas transmises.
- La conception du produit est terminée conformément au PDS jusqu'à ce que les conceptions détaillées soient en place. Les dessins détaillés sont ensuite remis à l'ingénieur de fabrication. C'est à ce stade que de nombreux problèmes sont signalés par le service de fabrication qui demandera des modifications et signalera les problèmes avec les fournisseurs. Tout problème soulevé par les fournisseurs lors de la phase d'approvisionnement sera signalé au service de conception.
- Après la phase de demande et de modification, les pièces seront prêtes à être livrées au service de production pour assemblage et test, où d'autres problèmes sont signalés lors de l'assemblage
Développement simultané de nouveaux produits

Le même développement de produit peut être réorganisé avec très peu de ressources supplémentaires pour avoir un flux de travail d'ingénierie simultané. Comme le montre la figure 3 ci-dessous, les départements se consultent ou consultent le personnel concerné avant de finaliser leur tâche. Laissez-nous plonger dans le processus pour explorer les avantages.
- L'entreprise définit conjointement une spécification de conception de produit (PDS).
- La fabrication et la production sont consultées pour évaluer la fabricabilité de la conception. Des outils tels que DFM, QFD et DFMA peuvent être utilisés pour l'évaluation.
- Des outils tels que la conception pour l'assemblage (DFA) sont utilisés pour évaluer la conception conjointement avec la production
- Des informations de conception détaillées sont partagées avec la production, ce qui leur permet de préparer les outils et les gabarits de production.
- Enfin, l'équipe de conception partage des informations telles que les spécifications finales avec les équipes commerciales et marketing, ce qui leur permet de préparer des fiches techniques, des brochures, la conception d'emballages, des événements promotionnels, etc.
Comparaison des coûts entre CE et SE
Dans le développement de produits d'ingénierie séquentielle, les coûts augmentent lentement car les activités sont exécutées séquentiellement par les départements au fur et à mesure qu'ils s'impliquent dans le processus. Mais, lors de la phase de conception-fabrication, les coûts augmentent rapidement en raison des demandes de changement et des boucles d'itération où il y a un processus de gestion des changements dans les deux sens.
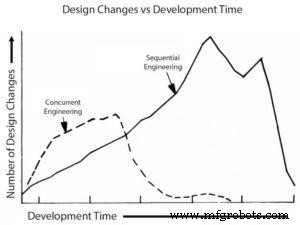
Dans le développement de produits d'ingénierie simultanée, les coûts augmentent rapidement au début du développement en raison de l'implication d'une équipe plus importante et d'activités intensives. Cependant, à mesure que le développement du produit progresse vers la fabrication et la production, il s'accélère et les coûts diminuent en raison du nombre moins élevé de problèmes à trier et de boucles itératives plus courtes.
Ici, les coûts de conception ou de développement du produit varient entre 5 et 15 % du coût total du produit. Mais, la décision prise lors de la phase de conception affecte 60 à 95% du coût. Cela montre à quel point il est crucial de prendre les bonnes décisions dès les premières étapes de conception pour réduire le coût global d'un produit.
Il existe de nombreuses données pratiques réelles disponibles sur l'épargne, telles que,
- Comment l'entreprise automobile Ford a considérablement réduit ses délais de mise sur le marché tout en améliorant la qualité de certaines de ses voitures.
- DFM, QFD, des équipes interfonctionnelles soutenues par la direction ont été la clé du succès du multimètre HPs 34401A
Résumé
L'introduction de la pratique simultanée dans le développement de produits présente de nombreux avantages. Il n'a pas besoin d'être complet. Certaines des critiques portent sur le fait qu'il a besoin de plus de ressources au début. Mais fait correctement, il peut être minimisé. Tous les départements n'auront pas à s'impliquer dès le départ ou à toutes les réunions d'étapes clés.
Pour les entreprises qui développent régulièrement des produits, il vaut la peine de mettre en place des processus de développement de produits avec des étapes définies.
Processus de fabrication
- Défis du développement de nouveaux produits
- Comment embaucher la meilleure entreprise de conception et de développement de produits industriels ?
- Conception de produits médicaux :trucs et astuces
- Silicon Valley Product Development 2018
- 5 clés pour le développement de produits IoT
- NEW RASPBERRY PI 3 MODEL B + CARACTÉRISTIQUES ET ACHAT
- Conception et développement d'un robot d'inspection à faible coût
- GE présente un nouveau produit pour les applications de contrôle et de surveillance
- Les machines CNC et leurs avantages dans l'ingénierie industrielle