Les robots et le personnel d'atelier collaborent, maximisant la synergie et la sécurité
Une fabrication efficace nécessite des systèmes coordonnés de personnel d'atelier, d'équipement et de logiciels. Ces systèmes incluent de plus en plus la technologie robotique, car les fabricants reconnaissent la fiabilité, la répétabilité et la flexibilité qu'offrent les robots. Selon la Fédération internationale de robotique, le nombre de robots industriels utilisés dans le monde passera à environ 2,6 millions d'ici 2019, soit environ un million de plus qu'en 2015. Environ 70 % des robots industriels sont utilisés dans les secteurs de l'automobile, de l'électricité/électronique et de la métallurgie. et industries mécaniques.
La sécurité est la première considération dans toute opération de fabrication; l'utilisation sûre des robots industriels a traditionnellement nécessité le maintien de distances définies entre le personnel de l'atelier et les robots, et le positionnement de protections et de cages autour des robots pour éviter les blessures des travailleurs. Un assortiment croissant de robots, de logiciels et de stratégies de mise en œuvre vise à une interaction plus étroite et plus productive entre les humains et les robots.
Le contrôle de cette relation va de l'interruption du mouvement d'un robot régie par un capteur lorsque les travailleurs se déplacent dans des zones potentiellement dangereuses, à l'application de robots entièrement « collaboratifs », également appelés cobots, conçus pour fonctionner en toute sécurité côte à côte avec des travailleurs humains. Différents modes de collaboration permettent aux fabricants de tirer pleinement parti des capacités des systèmes robotiques et du personnel d'atelier.
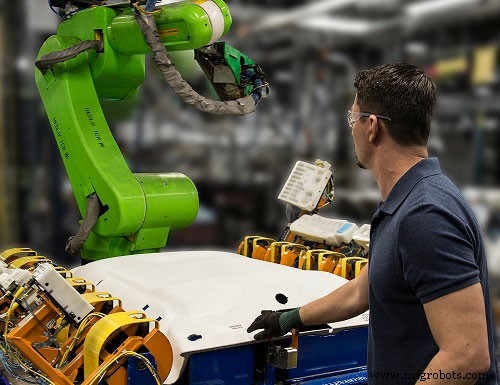
Le terne, dangereux et sale
La pénurie actuelle de travailleurs qualifiés aux États-Unis est à l'origine d'une grande partie de la demande de robots collaboratifs. Le départ à la retraite du personnel d'atelier chevronné et le nombre insuffisant de jeunes travailleurs entrant dans la main-d'œuvre manufacturière ont laissé les propriétaires d'atelier avec des pénuries de personnel.
Pour combler ce déficit de compétences, les fabricants utilisent des robots pour des opérations répétitives et/ou dangereuses et déplacent les travailleurs vers des emplois nécessitant plus de réflexion et de compétences. "Nous constatons que les gens sont réaffectés", a déclaré Craig Tomita, directeur des ventes, région ouest, pour Universal Robots USA Inc. (Ann Arbor, MI), un fabricant de robots entièrement collaboratifs.
Tomita a déclaré que la mise en œuvre des robots collaboratifs est relativement simple car ils fonctionnent dans une enveloppe à échelle humaine et ne nécessitent pas la protection nécessaire avec les robots industriels traditionnels. Il n'est pas nécessaire de réorganiser l'atelier et l'utilisation de l'espace ne change pas. "Vous placez simplement des robots collaboratifs là où des opérateurs humains effectuent actuellement le travail", a-t-il déclaré, ajoutant que même si les robots collaboratifs sont sûrs, l'évaluation des risques - déterminer tous les dangers potentiels dans un système et trouver des moyens de les atténuer - est vitale.
La facilité d'utilisation est un attribut clé des robots entièrement collaboratifs. Bien que les capacités des petits robots collaboratifs soient comparables à celles des petits robots traditionnels, les exigences de formation et de programmation collaboratives sont minimes. "La facilité de programmation dans le système UR change la donne", a déclaré Tomita. « Lorsque, par exemple, un robot doit être intégré dans un système de fabrication plus vaste, les unités d'Universal peuvent être programmées et exécutées à l'aide d'un écran tactile portatif. Si nécessaire, les utilisateurs de niveau supérieur peuvent également programmer le robot à l'aide de son langage de script de type Python."
Les robots collaboratifs peuvent être facilement utilisés par les petits magasins, où les coûts d'intégration ont été un obstacle à l'entrée. "Si vous le regardez comme un iceberg, la partie robot apparaît au-dessus de l'eau", a déclaré Tomita. "Le processus d'intégration est ce qui est ci-dessous. Vous prenez cet iceberg dans son ensemble et cela coûte vraiment cher. Un robot collaboratif coûte à peu près le même prix qu'un robot industriel standard, mais le coût d'intégration est bien inférieur », a-t-il déclaré.
L'utilisation de robots peut également aider à réduire les coûts de main-d'œuvre, a déclaré Tomita :"Les entreprises qui utilisent des robots collaboratifs peuvent souvent proposer des offres qu'elles ne pouvaient pas proposer auparavant, car leurs coûts de main-d'œuvre étaient hors de prix."
Les applications potentielles sont largement ouvertes. "Le nombre et les types d'applications pour nos robots collaboratifs n'ont pas encore été pensés", a déclaré Tomita. "Les gens sont tellement habitués à penser que le robot est derrière une cage là-bas, que les gens sont là-bas et que les deux ne se rencontreront jamais. Cela est en train de changer."
Universal Robots propose trois modèles de robots collaboratifs à six axes, des unités UR3 qui gèrent des charges utiles jusqu'à 3,3 kg (7,26 lb) et ont un rayon de travail de 500 mm (19,7″), aux robots UR10 avec un 10 kg (22- lb) charge utile et rayon de travail de 1300 mm (51,2″).
Un client typique des robots Universal est CleanLogix LLC (Santa Clarita, CA), qui développe des produits qui utilisent le CO2 pour le nettoyage, le refroidissement et d'autres applications. Le président de CleanLogix, David Jackson, a déclaré :« Nous pouvons diffuser une pulvérisation dans une zone de coupe et fournir un moyen très propre et écologique pour refroidir un outil de coupe dans un processus. Il a noté qu'un seul robot est capable d'effectuer différentes tâches; par exemple, placer une pièce dans un centre d'usinage puis changer l'outillage de l'effecteur final pour fournir du liquide de refroidissement. « Vous disposez donc d'un robot multitâche et d'une solution totalement verte et allégée. Nous sommes très enthousiasmés par ces robots à petit facteur de forme. »
La capacité des robots collaboratifs à travailler en toute sécurité avec les humains permet d'organiser les opérations pour maximiser la synergie; par exemple, un robot peut assembler une série de composants tandis qu'un travailleur humain effectue l'insertion de minuscules fils qui nécessitent de la dextérité et une perception cognitive. Les robots sont idéaux pour les opérations qui nécessitent répétition, fiabilité et précision, y compris les opérations d'emballage, de palettisation, d'assemblage et de pick-and-place.
La répétabilité et la précision sont des mesures distinctes mais liées des performances du robot. La répétabilité est une mesure de la capacité d'un robot à revenir à une position donnée à chaque fois. La répétabilité revendiquée de divers robots collaboratifs est de l'ordre d'environ ± 0,02 à ± 0,1 mm (0,0008 à 0,004″) ou moins.
La précision, d'autre part, mesure à quelle distance d'une position ou d'un chemin souhaité un robot peut se déplacer, et peut être classée comme précision de position et précision de chemin. Des tâches telles que le forage, où le robot se déplace vers une position et s'arrête pendant que le trou est foré, nécessitent une précision de positionnement. La précision de la trajectoire est requise pour les processus tels que la découpe au laser ou la peinture où le processus a lieu pendant que le robot se déplace entre les points.
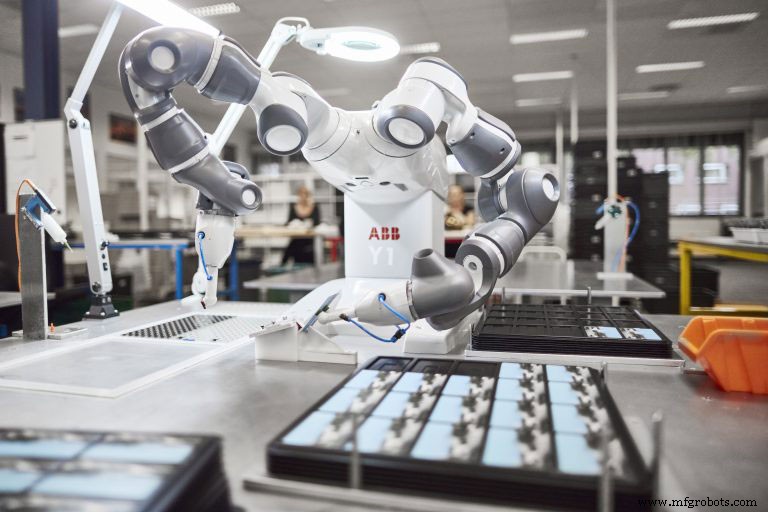
L'application détermine la collaboration
En général, l'activité côte à côte du personnel de l'atelier et des robots est réalisée avec des robots collaboratifs qui manipulent de petites charges utiles à des vitesses lentes - généralement aux alentours de 1 m/s (39,4 ips). Cependant, a déclaré Nicolas De Keijser, responsable de la ligne d'activité assemblage et test pour la division Robotique et mouvement d'ABB Inc. (Cary, Caroline du Nord), la charge qu'un robot porte ou la vitesse à laquelle il se déplace ne garantissent pas en elles-mêmes un fonctionnement sûr et collaboratif. . Une charge utile très légère mais dangereuse pourrait être une lame de rasoir ou une aiguille hypodermique. Une charge utile lente mais lourde pourrait présenter un risque d'écrasement pour le personnel de l'atelier. De même, une défaillance du préhenseur lors du déplacement d'une charge utile de taille moyenne à vitesse modérée pourrait projeter la charge utile à travers l'atelier.
Un système robotique n'est collaboratif que par rapport à son application. "Si l'opération est dangereuse, vous ne voulez pas être à proximité du robot, peu importe à quel point le robot est collaboratif", a déclaré De Keijser, ajoutant qu'une évaluation complète de la sécurité de la solution est requise dans toute application. "Si vous lisez les normes, elles dictent toujours que nous parlons d'un fonctionnement collaboratif, pas d'un robot collaboratif."
ABB adopte deux approches pour assurer une coexistence sûre des travailleurs et des robots. Les applications véritablement collaboratives, telles que l'assemblage de petites pièces, peuvent généralement être remplies par le robot YuMi à double bras monté sur table de l'entreprise. La portée du robot de 38 kg (84 lb) est de 599 mm (24″) et la charge utile de 500 kg (1,1 lb) par bras. Il occupe un espace à taille humaine tout en fonctionnant en toute sécurité aux côtés du personnel de l'atelier.
D'autre part, ABB facilite le fonctionnement en toute sécurité de grands robots industriels standard via des systèmes redondants qui combinent une programmation minutieuse et un logiciel de surveillance de la sécurité. Une fois qu'un robot est programmé pour une plage de fonctionnement sûre, le logiciel de surveillance de robot certifié SafeMove2 d'ABB fournit une protection de sécurité redondante en surveillant l'activité du robot, y compris les limites de vitesse de sécurité, la surveillance de l'arrêt et les plages d'axes, ainsi que la supervision de la position et de l'orientation. Selon De Keijser, le logiciel est intégré au contrôleur du robot et permet de gagner du temps de configuration et d'augmenter la productivité tout en réduisant le coût total de l'investissement.
Le système Kinetiq Teach de Yaskawa Motoman est un exemple de mode de guidage manuel de l'interaction homme/robot décrit dans les normes ISO 10218-1 et 10218-2.
Contrôle adaptatif intégré
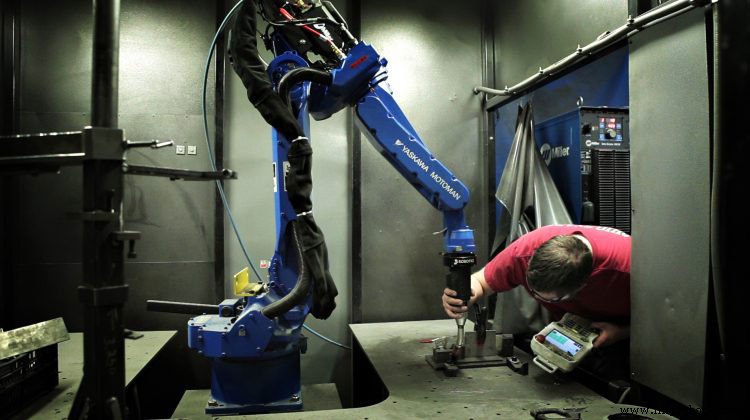
Une autre forme de collaboration robotique combine les compétences et l'expérience d'un artisan avec la capacité d'un robot à opérer dans des zones dangereuses. Le soudage n'est généralement pas une opération conviviale. Selon Zane Michael, directeur du développement commercial thermique pour Yaskawa America Inc., Motoman Robotics Division (Miamisburg, OH), « Dans le marché actuel, le mot collaboratif signifie que vous avez un robot et une zone d'opérateur qui se chevauchent. Ils travaillent en étroite collaboration. Je n'ai pas vu le mot collaboratif dans ce sens appliqué à l'environnement de soudage. »
Bien que le soudage robotisé ne puisse pas être qualifié de collaboratif à proprement parler, une forme de collaboration entre un soudeur qualifié et un robot prend en charge des performances constantes. Ce n'est pas que faire fonctionner un robot de soudage soit trop difficile. "Programmer et faire fonctionner le robot est facile", a déclaré Michael. "Chez Motoman, nous avons un système appelé Kinetiq Teach, où vous pouvez saisir la torche et déplacer le robot sur le chemin que vous voulez qu'il suive, enregistrer ce chemin et vous êtes prêt à partir." Cependant, a-t-il ajouté, faire fonctionner un robot de soudage sans connaissances en soudage est "une bataille difficile" si des défauts de soudure épisodiques tels que des contre-dépouilles ou des brûlures se produisent.
Dans ces cas, un soudeur expérimenté peut ajuster les actions du robot pour surmonter les problèmes. Des systèmes de contrôle adaptatifs utilisant des lasers ou d'autres capteurs sont disponibles pour le suivi de couture de base, mais la majorité des systèmes de soudage sont expédiés sans ces systèmes. "Le soudeur humain a ce que j'appelle un contrôle adaptatif intégré", a déclaré Michael.
En fonction de la complexité opérationnelle et des capacités de volume, les cellules robotisées possèdent différentes formes de systèmes d'automatisation et de sécurité. La cellule C30 à station unique ArcWorld de Motoman est destinée au traitement monobloc à faible volume de pièces plus petites. Lorsque la porte de la cellule s'ouvre pour permettre à un opérateur de charger une soudure sur le positionneur dans la cellule, le robot est en mode d'arrêt d'urgence. Une fois que l'opérateur a quitté la cellule, la porte descend et le soudage a lieu. D'autre part, les machines de la série 6000 à grand volume et à grandes pièces de Motoman sont équipées d'un positionneur qui indexe les fixations de pièces comme une grande roue et peut être chargé de l'extérieur de la cellule tandis que plusieurs robots soudent un assemblage à l'intérieur.
Les entreprises de soudage font face à des pénuries de main-d'œuvre similaires à celles des autres segments de la fabrication. Sur la base des statistiques du Bureau of Labor des États-Unis, l'American Welding Society estime une pénurie de soudeurs de 290 000 aux États-Unis d'ici 2020. Michael a déclaré que les fournisseurs de soudage avant-gardistes travaillent avec des écoles de métiers et des centres de carrière pour créer un programme pour les soudeurs. Par exemple, Motoman a créé un programme STEM de soudage et un programme d'études correspondant pour la formation en soudage des lycées et des adultes.
Robots, l'IdO
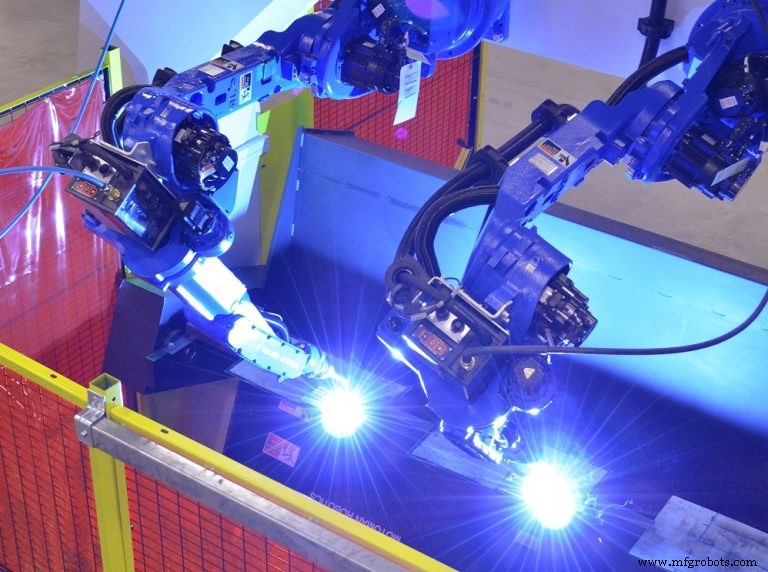
Le cloud computing et l'Internet des objets facilitent la collaboration entre les robots, les utilisateurs et les fabricants de robots. Les fabricants surveillent régulièrement la disponibilité des robots pour documenter la productivité, a déclaré Mark Scherler, directeur général, segment d'assemblage des matériaux, pour le fournisseur de robots FANUC America Corp. (Rochester Hills, MI), « Mais il y a plus que cela. Nous utilisons Internet pour collecter les données des robots et aider les fabricants à améliorer leur disponibilité."
FANUC fournit des robots industriels collaboratifs et standards. Pour exploiter pleinement les données collectées par les robots, la société a développé une application de diagnostic sans temps d'arrêt (ZDT) qui détecte et analyse les informations critiques concernant le fonctionnement mécanique et l'état de maintenance d'un robot. Par exemple, le ZDT installé sur des robots dans l'usine d'un fabricant peut détecter un robot subissant des niveaux de couple croissants qui peuvent indiquer un problème avec un axe particulier. Via la technologie cloud, l'application ZDT envoie les informations opérationnelles au centre de données FANUC pour analyse. Les problèmes critiques déclenchent la transmission d'avis aux appareils intelligents désignés chez l'utilisateur du robot.
Dans le même temps, FANUC confirme la disponibilité des pièces qui peuvent être nécessaires pour résoudre le problème. Les données peuvent également être utilisées pour optimiser les systèmes robotiques en termes d'amélioration du temps de cycle, de réduction de la consommation d'énergie et de prolongation de la durée de vie du robot grâce à une meilleure maintenance.
Flexibilité de l'automatisation
Jeff Estes, directeur régional des ventes pour l'Est de la division Morris-Sud du groupe Morris (Charlotte, Caroline du Nord) et ancien directeur, partenaires de THINC pour Okuma America Corp., a déclaré que l'industrie automobile à volume élevé a mené l'adoption de l'automatisation pendant des décennies. Aujourd'hui, les fabricants de petits volumes recherchent la fiabilité et la prévisibilité fournies par l'automatisation, mais veulent également la flexibilité nécessaire pour permettre des changements rapides d'un lot de production à un autre. À cette fin, la technologie robotique permet à un atelier de modifier rapidement les détails de programmation et les effecteurs finaux.
Estes a souligné que l'automatisation robotisée d'une machine-outil n'implique pas simplement le chargement et le déchargement des pièces. "La clé est de savoir comment parvenir à un fonctionnement avec peu ou pas de présence", a-t-il déclaré. Dans une cellule entièrement automatisée, de nombreux éléments, dont une machine-outil, un robot, une jauge, un système de vision et un équipement de manutention, sont réunis pour créer une « opération en boucle fermée qui peut continuer à fonctionner et prendre des décisions de base sans interaction humaine, », a déclaré Estès. Les multiples éléments d'une cellule génèrent des informations sur les opérations individuelles mais, "jusqu'à ce qu'ils commencent à travailler les uns avec les autres, ce ne sont que des éléments d'information". Un intégrateur choisit et organise les éléments de la cellule et coordonne leurs fonctions.
Certains fournisseurs de machines-outils maintiennent des capacités d'intégration internes afin de fournir des systèmes clés en main. Methods Machine Tools Inc. (Sudbury, MA) compte plus de 30 ingénieurs en automatisation aux États-Unis, ainsi que du personnel de conception, de contrôle, d'électricité/mécanique, d'intégration de systèmes et de service sur le terrain/d'installation. En complément de ses activités de fournisseur de machines-outils et d'intégrateur de systèmes, Methods a récemment ajouté un centre d'automatisation et d'intégration à son usine de Charlotte, en Caroline du Nord. Les spécialistes de l'automatisation et les ingénieurs en intégration de systèmes fournissent des conseils aux clients concernant les équipements et les capacités allant de la définition et de la construction de cellules à l'exécution des écoulements. L'objectif de la nouvelle installation de 10 000 pi2 (929 m2) "est de fournir une solution complète et sur mesure à nos clients", a déclaré John Lucier, responsable de l'automatisation des méthodes.
Automatisation holistique
Des technologies comme les robots collaboratifs changent la façon dont les fabricants envisagent l'automatisation. Estes encourage les fabricants à tirer parti de la puissance des données générées et collectées par un système d'automatisation.
L'analyse des données peut contribuer à d'autres aspects de la production, notamment la qualité des produits, la gestion des outils, le flux de matériaux et la logistique. Lors de la mise en œuvre de la technologie robotique, les fabricants devraient adopter "une approche plus holistique", a déclaré Estes. "Au lieu de simplement éviter à une personne de charger et de décharger une machine, un fabricant devrait demander :" Puis-je faire quelque chose de plus avec ce robot pour le rendre également plus lié à l'IOT ou à l'industrie 4.0 ?" capacités, a-t-il déclaré :"Même nous, en tant que fournisseurs OEM, apprenons chaque jour à quel point nous pouvons les rendre plus performants."
Qu'est-ce qui rend un robot collaboratif ?
Le terme « robotique collaborative » est fréquemment utilisé pour décrire toute situation où l'action du robot est contrôlée pour s'adapter aux travailleurs humains. En réalité, les relations possibles entre les travailleurs et les robots varient considérablement selon le robot et l'application.
Les normes ISO 10218-1 et 10218-2, « Normes de sécurité pour les applications des robots industriels », ont été publiées en 2011. Elles énumèrent les exigences pour une conception sûre, les mesures de protection et l'application des robots industriels. Les normes définissent quatre modes différents d'interaction liée à la sécurité entre le personnel de l'atelier et les robots.
Un mode est la possibilité d'effectuer un arrêt surveillé de sécurité. Des capteurs surveillent une zone prédéterminée autour d'un robot et le mouvement du robot s'arrête lorsqu'un humain pénètre dans cette zone. Ce niveau de surveillance de la sécurité est satisfaisant lorsque l'intervention humaine est minimale, même si des interruptions fréquentes peuvent diminuer la productivité. Un deuxième mode implique un guidage manuel, dans lequel un opérateur apprend à un robot à suivre un chemin souhaité en saisissant le bras du robot et en le déplaçant vers les points souhaités sur le chemin tout en enregistrant les points avec un pendentif d'apprentissage. Un capteur de couple de force dans le robot reconnaît le guidage manuel de l'opérateur. Le capteur n'agit pas comme un système de sécurité et, en dehors du mode d'apprentissage, le robot doit avoir d'autres dispositifs ou systèmes en place pour assurer une interaction sûre avec les humains.
En mode de surveillance de la vitesse et de la séparation, un système de vision détecte les humains dans une zone de sécurité désignée autour du robot. Au fur et à mesure que la séparation entre le robot et l'humain diminue, le robot ralentit progressivement; à une certaine distance, le mouvement du robot s'arrête. Puis, lorsque l'humain sort de la zone de sécurité, le robot reprend son travail à vitesse normale. Ce mode de sécurité gradué aide à maintenir la productivité même avec les interventions des travailleurs.
Le quatrième mode de collaboration permet une activité côte à côte des robots et des humains et élimine le besoin de gardes et de cages de protection. Les robots décrits sont appelés robots limiteurs de puissance et de force. Lorsque des capteurs détectent des forces anormales sur le robot, telles que celles générées par le contact avec un travailleur, le robot ralentit, s'arrête ou recule immédiatement. Ces robots décrits sont appelés robots limiteurs de puissance et d'effort. Lorsque des capteurs détectent des forces anormales sur le robot, telles que celles actionnées en contactant un travailleur, le robot ralentit, s'arrête ou recule immédiatement. Ces robots sont généralement plus petits et moins puissants que les robots industriels traditionnels, et ont également des formes arrondies et des articulations fermées pour éviter les blessures par pincement.
En 2016, l'ISO a publié la spécification technique ISO/TS 15066 qui ajoute des détails et des éclaircissements aux normes ISO 10281-1 et 2. La TS 15066 définit les robots collaboratifs comme ceux conçus pour une interaction directe avec un humain dans un espace de travail collaboratif où l'humain et le robot peuvent effectuer tâches simultanément. La spécification détaille la quantité de force qu'un robot peut infliger à un humain sans causer de douleur ni de blessure. Les niveaux de force ont été déterminés par des tests d'impact sur des zones spécifiques du corps humain. Néanmoins, il est essentiel d'effectuer des évaluations des risques de l'opération en cours et des pièces et outils impliqués dans une application spécifique pour assurer une sécurité absolue.
Système de contrôle d'automatisation
- Robots collaboratifs :devenir grand public ?
- Nouveaux robots :économiques et haut de gamme
- Les robots collaboratifs et leur impact sur la fabrication
- Arrêt d'urgence et contrôleurs d'arrêt
- Pourquoi utiliser un robot collaboratif ?
- Cobots et fabrication :3 façons dont l'automatisation collaborative peut aider votre boutique
- Les cobots et l'avenir de la robotique avancée dans la fabrication
- L'avenir des tests :automatisation et robots collaboratifs
- Que sont les cobots (robots collaboratifs) ?