25 jalons clés de la fabrication additive en 2019
2019 marque une nouvelle année positive pour l'industrie de la fabrication additive (FA). Cette année, l'industrie a continué de mûrir pour devenir un processus prêt pour la production, avec de plus en plus d'entreprises adoptant la technologie ou intensifiant leur implication dans l'industrie.
Pour mettre en évidence l'évolution de la FA, nous avons compilé une liste des étapes clés qui ont façonné l'industrie en 2019.
Matériel
1. Desktop Metal livre son premier système de production
En mars, Desktop Metal a livré son premier système de production à une société Fortune 500 dont l'identité n'a pas encore été divulguée. Dévoilé pour la première fois en 2017, le système de production de Desktop Metal est alimenté par sa technologie Single Pass Jetting, qui, selon lui, le rend plus de 100 fois plus rapide que les imprimantes métalliques quadri-laser, 4 fois plus rapide que l'alternative de jet de liant la plus proche et jusqu'à 20 fois coût par pièce inférieur à celui des imprimantes 3D métal d'aujourd'hui.
Avec la machine officiellement sur le terrain, l'industrie est impatiente de voir si le système de production peut vraiment fournir ce que son nom suggère.
En plus de cette annonce, Desktop Metal a également récemment lancé le système de boutique de Formnext. La nouvelle imprimante 3D est conçue pour combler le fossé entre les systèmes Studio et Production.
Ces 2 jalons sont particulièrement cruciaux pour l'avancement de la technologie de projection de liant métallique, qui pourrait bientôt devenir une nouvelle méthode de production à haut volume.
2. HP lance une nouvelle gamme d'imprimantes 3D Jet Fusion
Dans le segment des polymères, HP continue d'innover sa technologie Multi Jet Fusion (MJF). En mai, la société a dévoilé la série 5200 de ses imprimantes 3D MJF.
La nouvelle série 5200 s'inscrit dans une évolution naturelle de l'entreprise. Alors que la série 500/300 d'imprimantes 3D visait le prototypage fonctionnel et la série 4200 visait les petites séries et la production, la dernière série vise la production en volume, avec une précision et une répétabilité comparables au moulage par injection.
L'une des caractéristiques les plus notables de la série 5200 est la puissance améliorée des lampes à l'intérieur des imprimantes 3D 5200. Cela permet au nouveau système de fusionner la poudre en un seul passage, par opposition à un mode à deux passages dans les systèmes précédents. En conséquence, le système a une amélioration de 40 pour cent de la productivité et ouvre des possibilités pour l'impression 3D de matériaux à haute température.
Les premiers utilisateurs rapportent de bons résultats jusqu'à présent. Le producteur d'éoliennes, Vestas, par exemple, utilise la technologie et le matériau TPU pour produire des composants de protection pour ses pales d'éoliennes. HP lui-même tire également parti de sa technologie pour produire des composants pour ses autres machines d'impression.
De toute évidence, cette annonce élargit considérablement les opérations de FA de l'entreprise et permet aux clients HP d'exploiter véritablement la fabrication numérique.
3. Impression 3D multi-matériaux alimentée par l'IA à partir d'Inkbit
Plus tôt cette année, Inkbit, une start-up du Laboratoire d'informatique et d'intelligence artificielle (CSAIL) du MIT, a dévoilé une imprimante 3D industrielle dotée des technologies de vision industrielle et d'apprentissage automatique.
Bien que le procédé PolyJet de Stratasys, capable de fournir une grande variété de textures et de couleurs de plastiques durcissables aux UV, soit sur le marché depuis un certain temps, cette technologie est principalement utilisée pour le prototypage.
Inkbit, quant à lui, envisage des applications de production pour sa nouvelle technologie. Pour rendre cela possible, l'entreprise équipe sa machine de systèmes de vision artificielle et d'apprentissage automatique.
Le système de vision scanne de manière exhaustive chaque couche de l'objet au fur et à mesure de son impression, pour corriger les erreurs en temps réel, tandis que le système d'apprentissage automatique utilise ces informations pour prédire le comportement de déformation des matériaux et rendre plus précis produits finaux. Cette combinaison ouvre également la technologie à une plus grande variété de matériaux que ceux que l'on trouve dans les imprimantes 3D à jet d'encre traditionnelles.
Ce développement marque des jalons importants :l'un concerne l'impression 3D multi-matériaux, qui pourrait bientôt être utilisée pour fabriquer des produits finis, et l'autre est l'utilisation de l'IA, qui permet une plus grande précision de processus et automatisation.
Les deux combinés pourraient à terme conduire à une percée majeure dans l'impression 3D polymère. L'imprimante d'Inkbit est actuellement disponible pour certains clients, dont Johnson &Johnson, dans le cadre d'un programme de lancement anticipé. Les premiers systèmes seront expédiés à certains clients en 2021.
4. Imprimante 3D à résolution fine des détails (FDR) d'EOS
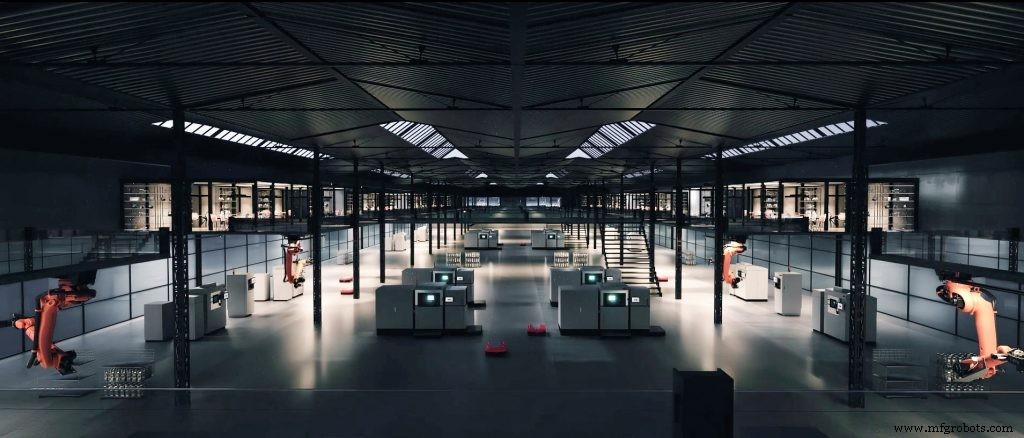
Au Formnext de cette année, EOS a présenté sa technologie d'impression 3D à base de polymère Fine Detail Resolution (FDR). Le nouveau processus utilise un laser CO pour imprimer en 3D des composants polymères délicats mais robustes avec des surfaces de résolution fine des détails et une épaisseur de paroi minimale de 0,22 mm.
EOS affirme être le premier fabricant à développer une solution laser CO pour l'impression 3D industrielle à base de poudre. La majorité des machines SLS actuelles utilisent un ou plusieurs lasers CO₂.
Le type de laser CO crée un faisceau laser ultra-fin dont le diamètre de focalisation serait la moitié de la taille des technologies SLS actuelles. Une conséquence importante de cette précision accrue est de nouveaux paramètres d'exposition qui peuvent entraîner des pièces avec des surfaces extrêmement fines.
En plus de la nouvelle technologie, EOS a également lancé une configuration de modules partagés, qui est une série de périphériques pour aider à automatiser et accélérer la FA en production.
Le matériel modulaire permet aux utilisateurs de mettre en œuvre des activités d'équipement, de déballage, de transport et de tamisage parallèlement au processus de fabrication AM.
Les développements d'EOS indiquent la demande croissante de solutions professionnelles prêtes pour la production, suggérant que la technologie arrive rapidement à maturité.
Logiciel
5. Markforged dévoile le logiciel d'IA Blacksmith
Les logiciels d'impression 3D deviennent de plus en plus intelligents, car de plus en plus d'entreprises commencent à intégrer l'intelligence artificielle (IA) dans la technologie. Le logiciel Blacksmith de Markforged en est un exemple, marquant l'évolution continue des logiciels de FA avancés.
« Premier exemple de fabrication adaptative », comme l'appelle l'entreprise, Blacksmith est un logiciel qui rend les machines de fabrication « conscientes », afin qu'elles puissent ajuster automatiquement la programmation pour s'assurer que chaque pièce est produite comme prévu.
Essentiellement, cela signifie un contrôle en boucle fermée, où les conceptions sont analysées puis comparées aux scans de la pièce, et le processus est automatiquement modifié pour construire les pièces comme elles ont été conçues.
Markforged pense que son outil d'IA Blacksmith sera « particulièrement puissant » à mesure que l'adoption de la FA métal se développe, garantissant que le processus de production est reproductible et précis.
Plus de données Blacksmith est donnée, plus les tolérances seront serrées lors de la production de pièces. En impression 3D, Markforged produit actuellement des tolérances comparables au moulage. L'objectif de la plate-forme Blacksmith est de se rapprocher le plus possible du fichier CAO numérique.
En fin de compte, un logiciel comme Blacksmith est un tremplin pour la fabrication numérique. Selon Markforged, l'impression 3D n'est qu'un début. L'entreprise envisage que son Blacksmith AI puisse connecter toutes les machines d'une usine. Cela permettra à terme à une génération de machines qui savent ce qu'elles sont censées faire et peuvent s'adapter pour produire la bonne pièce à chaque fois.
6. nTopology lance nTop Platform
Alors que les capacités des imprimantes 3D progressent régulièrement, les progiciels de CAO grand public sont souvent à la traîne, inadaptés aux exigences de conception spécifiques des additifs.
Une entreprise, cependant, vise à relever les défis de la conception pour la fabrication additive (DFAM).
Fondé il y a tout juste quatre ans, nTopology est rapidement devenu l'un des principaux outils logiciels génératifs, permettant aux ingénieurs de concevoir des géométries complexes pour la FA. Afin d'étendre les capacités au-delà de la conception en treillis, pour traiter l'ensemble du flux de travail d'ingénierie, la société a introduit la plate-forme nTop cet été.
Avec la sortie de nTop Platform, nous commençons à voir des outils de conception qui sont spécifiquement capables de tirer parti de la technologie d'impression 3D.
Par exemple, le logiciel permet aux utilisateurs pour créer des pièces plus légères et plus performantes avec des exigences fonctionnelles intégrées. La plate-forme nTop y parvient en important des conceptions CAO et en les convertissant en une représentation sur le terrain. Une fois cela fait, les ingénieurs utilisant la plate-forme peuvent effectuer très rapidement différentes opérations, telles que l'optimisation et la simulation de la topologie, qui seraient incroyablement compliquées avec d'autres outils distincts.
De plus, l'algorithme de nTop est très capable de gérer de grands modèles 3D qui seraient difficiles à gérer dans d'autres systèmes. Par exemple, simuler une grande surface de radiateur serait extrêmement difficile, mais est facile dans nTop Platform.
La réalisation d'un processus de conception d'impression 3D plus rapide et plus simple est l'une des principales tendances logicielles du secteur. Des solutions comme celle de nTopology pourraient finalement offrir la clé, débloquant un flux de travail de conception beaucoup plus optimisé pour l'impression 3D.
7. Logiciel de conception générative Apex de MSC
Plus tôt cette année, la société de logiciels Hexagon a acquis AMendate, un fournisseur allemand de logiciels d'optimisation de topologie pour la FA. AMendate a maintenant été ajouté au logiciel MSC d'Hexagon, qui fournit un logiciel de simulation CAE, la société annonçant le lancement de son logiciel de conception générative MSC Apex.
Le logiciel offre un degré élevé d'automatisation des processus de conception et aurait également le potentiel d'améliorer la productivité jusqu'à 80 % par rapport aux outils d'optimisation de topologie traditionnels.
L'impression 3D nécessite une nouvelle génération de solutions logicielles qui tirent pleinement parti des nouvelles libertés de conception rendues possibles par la technologie. Le logiciel MSC Apex pourrait devenir un tel outil. En tenant compte des exigences de conception, le logiciel générera plusieurs alternatives de conception légères qui offrent une répartition optimale des contraintes et un poids de pièce minimisé. Le logiciel utilise également une technologie de lissage intelligente qui garantit aux modèles 3D une finition lisse et professionnelle.
Combinés, ces avantages pourraient entraîner un flux de travail de conception simplifié et même réduire le nombre d'itérations de conception, ce qui peut en résulter. en un gain de temps important.
Matériaux
8. Jabil crée un centre d'innovation pour les matériaux
Le développement et la production de matériaux ont été parmi les principales tendances qui façonnent la fabrication additive en 2019.
L'année a débuté avec le lancement par Jabil d'une unité commerciale distincte, Jabil Engineered Materials, et d'un magasin de matériaux de 46 000 pieds carrés. Centre d'innovation.
Le choix limité de matériaux a été un obstacle important à l'adoption de l'impression 3D, selon l'entreprise. Pour surmonter cela, la nouvelle unité se concentre sur le développement, la validation et la mise sur le marché de matériaux d'ingénierie pour l'impression 3D industrielle.
Lors du développement de matériaux, Jabil prend en compte les exigences d'application - à partir de ses propres unités, en utilisant l'impression 3D ou externe clients – et les convertit en matériaux pouvant être imprimés.
Il est important de noter que Jabil utilisera non seulement de nouveaux matériaux en interne, mais les fournira également au marché libre, afin que davantage d'entreprises puissent bénéficier d'un choix matériel. Jusqu'à présent, la société a lancé PETg, PETg ESD, TPU 90 A et TPU 90 A ESD, mais elle prévoit d'en offrir plus à l'avenir.
Créer de nouveaux supports n'est qu'une façon pour Jabil de servir les utilisateurs AM. Établir la confiance dans les matériaux existants pour de nouvelles applications est un autre objectif poursuivi par l'entreprise.
De manière passionnante, Jabil anticipe un avenir dans lequel elle utilisera régulièrement l'impression 3D comme méthode de production à haut volume, avec des installations réparties dans le monde entier. Des matériaux fiables et prêts pour la production seront l'une des clés pour faire de cet avenir une réalité.
Jabil fait un effort concerté pour intégrer des matériaux dans son activité FA, afin d'offrir le package complet. Cet engagement dans l'impression 3D pourrait à terme contribuer à faire progresser l'industrie de la FA dans son ensemble.
9. Les composites diamantés Sandvik pour l'impression 3D
De nombreuses étapes ont également été franchies dans le segment de l'impression 3D composite. Le plus impressionnant d'entre eux est peut-être le tout premier composite diamant imprimable en 3D, développé par Sandvik.
Mais pourquoi imprimer en 3D un composite diamanté ?
Les diamants sont considérés comme l'une des structures les plus dures de la planète. En dehors des domaines de la joaillerie, les diamants sont largement utilisés pour des applications industrielles.
Bien que la création de diamants synthétiques ne soit pas nouvelle, le processus peut être à la fois coûteux et complexe, tandis que la production de formes complexes de ce matériau est presque impossible.
Et c'est là que L'impression 3D entre en jeu.
La technologie est saluée pour sa capacité à donner vie à des conceptions complexes, ce qui peut être difficile, voire impossible, à réaliser avec une fabrication conventionnelle.
Il est important de noter que Sandvik n'imprime pas directement avec des diamants mais avec un matériau composite. La majeure partie du matériau est du diamant, mais pour l'imprimer, il doit être cimenté dans un matériau à matrice dure, en conservant les propriétés physiques les plus importantes du diamant pur.
Après des tests, Sandvik a rapporté dureté et conductivité thermique exceptionnelles, ainsi que faible densité, résistance à la corrosion et bonne dilatation thermique de son nouveau matériau.
Nous sommes ravis de voir comment les industries utiliseront l'impression 3D composite diamant. Selon Sandvik, l'impact de ce nouveau matériau se fera sentir dans des applications industrielles avancées, des pièces d'usure aux programmes spatiaux, dans quelques années seulement.
10. Henkel rejoint le projet SYMPA pour développer des matériaux SLA pour l'automobile
« Nous avons un ensemble de matériaux qui sont assez bien acceptés aujourd'hui dans l'espace automobile. Ce que nous aimerions vraiment voir, c'est que l'industrie [AM] commence à adapter certains de ces matériaux. Cela rendrait nos tests et validations, ainsi que notre utilisation de l'application, beaucoup plus adaptés à l'impression 3D », déclare Harold Sears, responsable technique AM de Ford, s'exprimant dans une interview avec AMFG.
Et l'industrie semble répondre à cette demande. L'une des étapes franchies dans cette direction est la participation de Henkel au projet allemand SYMPA, visant à faire progresser de nouveaux matériaux et des procédés de stéréolithographie (SLA) pour le secteur automobile.
Les partenaires du projet voient un vaste potentiel dans l'utilisation des technologies SLA pour les applications automobiles, en particulier dans la production de pièces et de produits personnalisés. Ainsi, SYMPA vise à surmonter certaines des faiblesses des matériaux SLA actuels, notamment de faibles propriétés mécaniques, une faible durabilité et une faible stabilité aux UV.
L'un des domaines clés auxquels Henkel contribuera sera de développer de nouveaux polymères photosensibles, avec des propriétés thermiques et mécaniques à long terme accrues.
Grâce au projet, l'impression 3D automobile pourrait franchir une étape importante, permettant aux constructeurs automobiles de créer des pièces fiables et personnalisées pour les voitures.
Partenariats
11. Intégration de la FA métallique dans la production automobile en série
L'industrie automobile est l'un des secteurs offrant la plus grande opportunité d'adoption de l'impression 3D. C'est pourquoi les entreprises et les instituts de recherche s'efforcent de traduire l'impression 3D en processus de production industrialisés et hautement automatisés pour la construction automobile.
Le projet allemand d'industrialisation et de numérisation de la fabrication additive (IDAM) marque une étape importante pour l'impression 3D automobile.
Douze partenaires du projet prévoient de créer des lignes de production AM capables de produire au moins 50 000 composants par an dans la production de pièces communes et plus de 10 000 pièces individuelles et de rechange sous la plus haute pression de qualité et de coût.
En outre, les coûts unitaires des composants métalliques imprimés en 3D doivent être divisés par plus de moitié, selon le projet.
Coordonné par le groupe BMW, le projet IDAM se déroulera sur les 3 prochaines années, contribuant à établir durablement l'impression 3D métal en production.
12. Partenariats d'AMFG avec EOS et Autodesk
Plus tôt ce mois-ci, nous avons annoncé nos partenariats avec EOS et Autodesk. Nous pensons que ces partenariats contribueront à rationaliser davantage les flux de travail de FA.
Le partenariat EOS vise à connecter des machines à des plates-formes logicielles pour permettre aux clients de machines EOS de gérer facilement l'ensemble de leurs opérations de fabrication additive, à l'aide de notre Manufacturing Execution System (MES).
Grâce au logiciel MES d'AMFG, les clients EOS peuvent également préparer des travaux de construction et définir des paramètres importants, tels que l'orientation des pièces. Les constructions peuvent ensuite être découpées et les données envoyées directement à un système d'impression 3D EOS.
Dans le cas du partenariat Autodesk, notre logiciel MES sera lié au logiciel de conception et de simulation d'Autodesk, Netfabb®, pour fournir un flux de travail numérique intégré de la conception à la production.
L'introduction de la connectivité et de l'interopérabilité dans le flux de travail AM est un élément crucial pour parvenir à un flux de travail véritablement de bout en bout. Enfin, la connexion des machines au sein d'une plate-forme unique permettra un flux de données transparent, ce qui fournira la traçabilité et l'évolutivité nécessaires pour aider à pousser la FA vers l'industrialisation.
Investissements et acquisitions
13. L'investissement de Stryker dans des implants imprimés en 3D
En 2019, l'impression 3D dans l'industrie médicale a connu de nombreuses activités d'investissement. Le plus important d'entre eux a sans doute été l'investissement de 200 millions d'euros de Stryker (environ 225,8 millions de dollars) dans la R&D dans ses installations en Irlande. Cet investissement inclut l'institut AMagine, qui est responsable du développement d'implants imprimés en 3D pour la colonne vertébrale, la tête et les articulations.
Un tel engagement de Stryker est révélateur de l'énorme potentiel de l'impression 3D pour les traitements orthopédiques.
Depuis plus d'une décennie, l'impression 3D est utilisée pour produire des implants qui présentent souvent de meilleures performances que les alternatives traditionnelles. De plus, l'impression 3D permet aux implants d'être spécifiquement conçus pour s'adapter à l'anatomie d'un patient, offrant une option de traitement, où la reconstruction avec un implant traditionnel aurait été difficile, voire impossible.
Avec cet investissement, Stryker fait progresser la médecine L'impression 3D et la création d'une opportunité pour un plus grand nombre de personnes de bénéficier d'implants plus durables et mieux ajustés, possible avec cette technologie.
14. Carbon lève plus de 260 millions de dollars pour financer sa croissance
Le financement de la croissance de Carbon de 260 millions de dollars a été l'une des nouvelles les plus importantes en matière d'investissement cette année. L'afflux de liquidités le plus récent a porté la collecte de fonds totale de l'entreprise à 680 millions de dollars et sa valorisation post-money à plus de 2,4 milliards de dollars.
Ayant été créé en 2013, Carbon a continué à étendre son portefeuille de matériel DLS et matériels, ainsi que d'assurer des mises à jour régulières de ses logiciels.
Ses machines sont désormais opérationnelles dans le monde entier, l'entreprise faisant état d'une multiplication par 33 des volumes d'impression et d'une multiplication par 5 des heures d'impression au cours des 12 derniers mois. Les utilisateurs incluent Adidas, Ford et Riddell, et avec cette vague d'investissements, la société semble prête à maintenir le cap vers la fabrication de pièces à grande échelle.
15. Prise de participation de Sandvik dans BeamIT
Au-delà des investissements, 2019 a vu de nombreux mouvements stratégiques de grands industriels. Cet été, par exemple, le groupe suédois d'outils d'ingénierie, Sandvik, a annoncé l'acquisition d'une participation de 30 pour cent dans le spécialiste de la FA métallique, BeamIT.
Sandvik a rejoint le marché de la FA en 2013, cherchant à tirer parti de sa vaste expérience dans les matériaux et les méthodes de post-traitement pour mettre des alliages en poudre sur le marché et conseiller les clients tout au long du processus d'impression 3D.
Avant l'acquisition, la société a intégré sa division Powder dans sa division AM, afin de regrouper ces offres sous une seule unité commerciale. L'investissement dans BeamIT est conforme à l'ambition de l'entreprise d'avoir une présence croissante dans l'ensemble de l'industrie manufacturière - une présence qu'elle espère atteindre en investissant dans la FA.
Comme Sandvik, BeamIT a de grandes ambitions dans le espace additif, projetant une demande accrue de pièces dans les années à venir. Avec Sandvik comme partenaire et propriétaire, il est bien placé pour répondre à cette demande de front.
16. Acquisition de Forecast 3D par GKN
Une autre acquisition notable est venue du groupe industriel et automobile britannique GKN, qui a acquis cette année le fournisseur de services d'impression 3D basé aux États-Unis, Forecast 3D.
Avec cette acquisition, GKM, spécialisé dans l'impression 3D métal, va être en mesure de faire la promotion croisée de la FA à la fois en métal et en plastique.
Cette décision permet également à GKN d'avoir une plus grande portée sur le marché américain et d'exploiter un tout nouveau secteur d'activité, à savoir la fabrication de polymères AM.
GKN et Forecast 3D ont également été des pionniers dans l'utilisation des plates-formes HP pour les métaux et les plastiques. En tant que partenaires fondateurs du réseau de fabrication numérique HP, cette acquisition rassemble 2 fabricants de pièces pour accélérer encore la fabrication de pièces finales en masse pour les clients du monde entier.
17. Acquisition de Sculpteo par BASF
Il y a quelques semaines à peine, BASF, l'un des plus grands fabricants de produits chimiques au monde, annonçait l'acquisition du spécialiste français de l'impression 3D, Sculpteo.
L'acquisition permettra à Forward AM, une filiale de BASF dédiée à l'impression 3D, de commercialiser et de produire de nouveaux matériaux d'impression 3D à un rythme plus rapide.
Grâce à l'acquisition de Sculpteo, BASF sera également en mesure de fournir à ses clients et partenaires un accès plus rapide aux solutions d'impression 3D.
En fin de compte, l'expansion de la chaîne de valeur de la FA devient une tendance clé au sein de l'industrie, suggérant que les grands fabricants de matériaux reconnaissent désormais de plus en plus l'impression 3D comme une technologie viable pour la production industrielle de masse.
Activités de normalisation
18. Une collection de normes pour la FA métallique de la Metal Powder Industries Federation
La normalisation continue de jouer un rôle crucial dans l'instauration de la confiance dans la FA en tant que technologie de production. Bien que l'élaboration de normes soit un processus long et gourmand en ressources, il y a une forte pression de l'industrie pour plus de normes.
À la suite de cette initiative, la Metal Powder Industries Foundation (MPIF) a publié début 2019.
Compilation de 9 méthodes d'essai existantes, relatives aux matières premières en poudre métallique, le document est destiné à aider les concepteurs et les fabricants à mieux maîtriser la FA métallique.
Le mois dernier, MPIF a également publié une édition révisée de sa collection de normes AM.
19. Portail des normes
L'été dernier, America Makes et ANSI Additive Manufacturing Standardization Collaborative (AMSC) ont publié la deuxième version de sa « feuille de route de normalisation pour la fabrication additive ». La feuille de route identifie les normes et spécifications existantes, ainsi que celles en cours de développement, évalue les lacunes et fait des recommandations pour les domaines qui ont le plus besoin de normes.
AMSC ne s'est pas arrêté à cela, et cette année, il a présenté une nouvelle façon d'obtenir des informations actuelles sur les normes AM. Le mois dernier, il a annoncé la disponibilité d'un portail en ligne à travers lequel les membres et le public pourraient accéder facilement à la documentation actuelle.
Le portail offre un moyen pour la communauté d'observer et de suivre les progrès de l'AMSC, concernant le développement des normes AM, le portail affiche la feuille de route de développement des normes AMSC, où les visiteurs peuvent voir les prochaines étapes en cours.
Cela offre plus de transparence sur l'état actuel du développement des normes.
20. Les premières spécifications pour la FA polymère de SAE International
Alors que l'utilisation de l'impression 3D dans l'industrie aérospatiale se développe, il existe un besoin accru de normes pour permettre aux entreprises d'utiliser la technologie dans la production de pièces finales.
Pour répondre à ce besoin, SAE International a publié les premières spécifications AM Polymer pour l'industrie aérospatiale. Ces normes ont été créées suite à une demande des compagnies aériennes via l'EMG de l'Association du transport aérien international (IATA) pour pouvoir imprimer en 3D des pièces de cabine.
Les 2 normes spécifient les exigences pour la modélisation par dépôt de fusion (FDM ®) ou d'autres procédés d'extrusion de matériaux et matériaux utilisés avec cette technologie. Les utilisateurs peuvent utiliser les documents pour approuver de nouvelles machines, processus et matériaux, ainsi que pour vérifier la configuration appropriée et la méthodologie de test.
Nouvelles candidatures
21. Ford et Carbon lancent des pièces automobiles imprimées en 3D
Début 2019, Carbon a défrayé la chronique avec les premières pièces imprimées en 3D en production pour Ford.
Ensemble, les sociétés ont développé des pièces de rechange pour bras de levier Ford Focus HVAC (chauffage, ventilation et refroidissement), des prises auxiliaires Ford F-150 Raptor et des supports de frein de stationnement électrique Ford Mustang GT500.
Ces composants ont été créés à l'aide de la technologie d'impression 3D Digital Light Synthesis (DLS) de Carbon et du matériau EPX (époxy) 82 et ont satisfait à toutes les normes et exigences de performance de Ford.
Avec ces applications, il est clair que Ford est jeter les bases pour pouvoir faire des choses assez impressionnantes avec AM.
'La fabrication additive va continuer à être de plus en plus ancrée dans la partie quotidienne de ce que nous faisons en tant qu'entreprise', Ford's Le chef technique d'AM Technologies, Harold Sears, a expliqué dans la série d'entretiens d'experts d'AMFG. "Au lieu d'être une exception à la norme, cela va être beaucoup plus accepté comme tel. "
22. Le décollage de composants de vélo imprimés en 3D
Cette année, une poignée de fabricants de vélos spécialisés ont intégré des composants imprimés en 3D dans leurs produits.
Par exemple, Franco Bicycles a lancé une nouvelle gamme de vélos électriques, comportant un composite imprimé en 3D. cadre fabriqué par la start-up californienne Arevo. Faisant partie de la gamme de vélos Emery, le cadre est présenté dans le vélo électrique Emery ONE, ce qui en fait le premier vélo au monde avec un cadre imprimé en 3D.
L'un des aspects uniques de la production du cadre en fibre de carbone imprimé en 3D est qu'il a été fabriqué en une seule pièce, par opposition à un assemblage en plusieurs pièces typique des cadres de vélo traditionnels. Le processus d'impression 3D robotique propriétaire d'Arevo et son logiciel de conception générative breveté permettent cela.
Grâce à l'impression 3D, le délai de fabrication du cadre de vélo Emery ONE est passé d'un cycle de 18 mois à quelques jours seulement.
Ensuite, la société néerlandaise MX3D, réputée pour son pont en acier imprimé en 3D, a dévoilé son Arc Bike II avec un cadre en aluminium imprimé en 3D. Conçu pour être plus léger et facilement personnalisable, l'Arc Bike II a été imprimé en 3D en seulement 24 heures, en utilisant la technologie de fabrication additive Wire Arc, qui est très similaire au dépôt direct d'énergie.
Plus récemment, Gamux , un fabricant de composants de vélo, a lancé une nouvelle gamme de pièces de vélo imprimées en 3D. Parmi eux se trouvent les top caps, les entretoises de ressort et les entretoises de tube de direction Garmin. Ce dernier, par exemple, ne fait que 1,75 g (10 mm), ce qui en fait l'un des espaceurs les plus légers au monde, encore plus léger que ses homologues en carbone.
Il semble que la tendance à l'utilisation de l'impression 3D pour la fabrication de vélos gagne vraiment du terrain, permettant à de plus en plus d'entreprises de créer des vélos légers et plus performants
23. Le 100e moteur de fusée imprimé en 3D de Rocket Lab
En juillet, Rocket Lab, une société aérospatiale basée en Californie, a achevé le 100e moteur de fusée Rutherford imprimé en 3D. La société utilise l'impression 3D pour tous ses principaux composants de moteur (y compris les chambres de combustion, les injecteurs, les pompes et les soupapes de propulsion principales) depuis 2013.
Neuf moteurs à propergol liquide Rutherford alimentent la fusée Electron de Rocket Lab, qui est fabriqué à partir de composites et peut transporter jusqu'à 225 kg de charge utile. Les pièces du moteur sont imprimées en 3D à l'aide de la technologie de fusion par faisceau d'électrons (EBM), censée produire des pièces de moteur moins chères que les procédés conventionnels.
Selon Peter Beck, fondateur et PDG de Rocket Lab, le moteur a « joué un rôle essentiel en permettant à Rocket Lab de faire du lancement fréquent et fiable une réalité pour les petits satellites ».
Récemment, Rocket Lab a une nouvelle fois prouvé la fiabilité des moteurs imprimés en 3D, en lançant avec succès 4 satellites en orbite avec son lanceur Electron.
24. Volvo Trucks imprime en 3D 500 outils et accessoires de fabrication
Ayant utilisé l'impression 3D pour le prototypage depuis plusieurs années, Volvo Trucks North America a récemment franchi le cap de la fabrication de 500 outils imprimés en 3D. Parmi eux se trouvent des jauges de joint de toit, des plaques d'installation de fusibles, des dispositifs de perçage, des supports d'adaptateur de direction assistée, des jauges d'écart de porte de bagage et des goupilles de porte de bagage.
Chacune de ces pièces a été produite dans le laboratoire Volvo Innovative Projects. Le laboratoire permet à l'entreprise de produire des composants en interne, en utilisant principalement des technologies de frittage laser sélectif (SLS).
L'adoption de l'impression 3D SLS permet aux ingénieurs de Volvo Trucks de concevoir des pièces et de les imprimer en un rien de temps. d'heures, ce qui se traduit par des délais d'exécution plus rapides et des économies de coûts.
In one example, Volvo says it was able to save over $1,000 per part for a one-piece diffuser used in the paint atomiser cleaning process. In this case, AM also enabled the company to consolidate the traditionally multi-component piece into one part.
While the technology has only been in use for several years, it’s already proving to be a valuable addition to the manufacturing process at Volvo Trucks, significantly saving production time and parts costs, and continually improving quality.
25. New Balance and Formlabs collaborate on 3D-printed sneakers
This year, the sneaker industry has also been shaken up by the partnership between New Balance and Formlabs.
In September, New Balance revealed that it had updated its TripleCell 3D printing platform with the addition of a new sneaker:the FuelCell Echo Triple.
The key innovation behind New Balance’s 3D printed shoes is the Rebound Resin material, which was co-developed with Formlabs. The material combines a number of sought-after characteristics for running shoes, including springiness, support and durability.
This material has been used to 3D print the heel of the 990 Sport sneakers and the forefoot of the latest FuelCell Echo Triple shoes, both featuring a complex lattice structure design.
According to New Balance, 3D printing allowed it to drastically shorten its design-to-manufacturing cycles and completely revamped how they approach the design of their shoes.
2019:Driving AM industrialisation
While these are some of the most prominent milestones in 2019, they are just the tip of the iceberg, with myriads of other developments, partnerships and applications shaping the industry in 2019.
Combined into a bigger picture, they point to an obvious, yet very exciting, trend:the AM industry is becoming stronger, bigger and more consolidated.
Despite the fact that there are still some challenges to overcome, the number of AM applications continues to grow, as industry stakeholders push for more technological solutions. With these advancements, 2020 looks set to continue its trajectory of new opportunities and growth.
impression en 3D
- Fabrication additive vs fabrication soustractive
- Avantages de la fabrication additive
- NatureWorks franchit les étapes clés de son expansion mondiale de la fabrication
- 2019 :prévisions de fabrication
- Principales tendances de fabrication :qu'est-ce qui motive la voiture connectée ?
- Fabrication additive dans les applications grand public
- Fabrication additive en électronique
- Fabrication additive dans l'aérospatiale
- Fabrication additive :une nouvelle force motrice