Entretien d'experts :Matthew Donovan, ingénieur principal d'Oerlikon pour l'AM, sur l'impression 3D pour l'aérospatiale
Oerlikon, un groupe mondial de technologie et d'ingénierie, sert certaines des industries les plus critiques en matière de sécurité, notamment l'aérospatiale et la défense . De plus en plus, la fabrication additive est devenue un élément clé de ses offres, la société ayant établi un centre d'innovation de 55 millions de dollars et une usine de production de composants avancés aux États-Unis plus tôt cette année.
Dans l'interview d'experts de cette semaine, nous nous asseyons avec Matthew Donovan, ingénieur principal pour la fabrication additive chez Oerlikon, pour discuter de la façon dont il continue de développer une installation de production de FA de bout en bout, des tendances passionnantes de la FA à surveillez et pourquoi les normes sont essentielles pour l'avenir de l'industrie.
Pourriez-vous me parler d'Oerlikon ?
Oerlikon est une entreprise mondiale et un leader de la fabrication dans ses segments des solutions de surface et des fibres artificielles. Oerlikon AM, qui fait partie du segment des solutions de surface, fournit des solutions de fabrication additive, des poudres métalliques au prototypage et à la production en série.
Comment êtes-vous arrivé à la fabrication additive ?
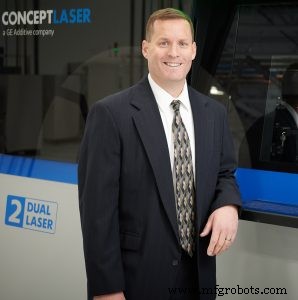
Mon expérience est dans l'aérospatiale. Avant de venir à Oerlikon, j'ai passé les 20 dernières années à travailler principalement sur les moteurs à turbine à gaz, les composants de la section chaude et les composants de la section de combustion.
J'ai une formation dans les systèmes d'alimentation en carburant, principalement pour les moteurs à turbine à gaz aérospatiaux, mais aussi pour les turbines à gaz industrielles et les reformeurs de piles à combustible. J'ai également travaillé sur divers efforts de R&D avec la NASA et d'autres entreprises. J'ai donc travaillé avec des matériaux à haute résistance et à haute température pour des environnements très exigeants.
J'ai commencé en tant qu'ingénieur de fabrication, apprenant les tenants et aboutissants de la fabrication et de la fabrication de pièces et dépensant du temps en tant qu'ingénieur qualité effectuant des enquêtes sur le terrain pour ces mêmes composants.
J'ai commencé à travailler dans la fabrication de pointe en 2006. J'ai commencé à rencontrer des géométries et des composants difficiles que nous ne pouvions pas vraiment fabriquer avec la fabrication conventionnelle.
À ce moment-là, je travaillais avec Morris Technologies sur des composants métalliques imprimés en 3D. Nous avons commencé à développer des composants pour injecteurs de carburant en utilisant la fabrication additive.
Au fil des années, j'ai développé quelques composants en utilisant la fabrication additive. J'ai travaillé pour United Technologies, aidant l'ensemble de l'entreprise à développer et à mettre en œuvre des technologies de FA, principalement en mettant l'accent sur le matériel de certification de vol.
Alors que nous travaillions à la mise en œuvre de ces composants, l'une des principales lacunes que j'ai découvertes était l'absence totale de normes sur la façon de fabriquer des pièces et de les certifier.
Une grande partie des coûts associés à l'aérospatiale ne sont pas nécessairement les composants eux-mêmes, mais la certification. Nous devons fournir une traçabilité complète pour chaque composant que nous fabriquons. Développer les normes sur la façon dont nous procédons et implémentons cela pour les additifs était tout un défi.
J'ai commencé à travailler sur les normes AM avec ASTM F42 vers 2009. J'ai aidé à rédiger certaines normes et par la suite siégé à quelques comités. J'ai co-écrit le guide de conception pour la fusion sur lit de poudre métallique par laser, ISO ASTM 52911, avec ISO/TC 261 et ASTM F42.
Grâce à notre collaboration avec United Technologies, en travaillant avec de nombreuses personnes très talentueuses et en ayant accès à un certain nombre de ressources formidables, nous avons pu proposer diverses innovations et développer des produits vraiment de pointe pour la FA. lit de poudre métallique.
En quoi consiste votre rôle chez Oerlikon ?
J'ai commencé chez Oerlikon en 2017, et mon rôle, maintenant, est celui d'ingénieur principal pour AM. Mon rôle a été fortement axé sur la mise en œuvre et le développement de technologies métalliques AM prêtes pour la production.
Nous avons commencé en tant que division de démarrage du groupe Surface Solutions. Nous avons construit une nouvelle installation à Huntersville, en Caroline du Nord, dans laquelle nous avons emménagé il y a un peu moins d'un an.
C'est une installation de 120 000 pieds carrés qui exploite actuellement 18 systèmes de lit de poudre métallique. Sur place, nous avons des capacités de four HIP (pressage isostatique à chaud) et sous vide, ainsi que des capacités de post-traitement, de manipulation de poudre et d'inspection.
L'objectif a été de faire de cette installation un véritable workflow de production de FA de bout en bout, avec le contrôle de chaque aspect de la chaîne d'approvisionnement, afin que nous puissions assurer la traçabilité à nos clients.
Mon rôle a été principalement dans la certification des machines. Je travaille en étroite collaboration avec les équipementiers de machines sur l'installation et la qualification de nos machines, puis je les certifie pour leur capacité et leur capacité croisée pour les composants de différentes machines.
Nous sommes alors en mesure de comprendre les capacités de la machine, la tolérance et la précision d'une machine individuelle pour produire la tolérance géométrique d'un composant AM et les différences entre nos machines, puis les régler afin que nous puissions livrer le même produit sur plusieurs machines.
La normalisation a été un très gros sujet de discussion, en particulier pour des industries comme l'aérospatiale. Comment les choses ont-elles évolué au fil du temps où vous avez été impliqué dans l'industrie, et quel est l'état actuel de la normalisation de la FA ?
Il y a eu de très bons développements.
Nous avons besoin de normes, en particulier dans l'aérospatiale, mais aussi dans d'autres domaines critiques pour la sécurité comme le médical, le nucléaire et l'énergie. L'élément clé des normes est qu'elles permettent à tout le monde de parler le même langage et de comprendre de quoi un produit est capable.
Avec l'absence de normes, tout le monde fabriquait effectivement des pièces et effectuait son travail de manière souvent très similaire, mais pas de la même manière. Ils ne parlaient pas la même langue. Il est très courant que les gens se réfèrent à des termes différents pour désigner le même processus, ou se réfèrent au même terme et signifient des processus radicalement différents.
Le développement de normes vous permet de parler dans le même langage à tous les niveaux et de comprendre ce que vous voulez dire lorsque vous faites référence, par exemple, à une construction de qualification, une matière première ou un niveau de qualification de machine.
Dans l'aérospatiale, si vous n'avez pas de norme contre laquelle vous pouvez certifier une pièce ou généralement, plusieurs normes pour identifier la pièce que vous fabriquez, ses propriétés mécaniques, ses performances et ses tolérances et pour pouvoir le retracer jusqu'au lot d'origine d'où il provient, jusqu'à la composition chimique des éléments qui le composent, alors vous ne pouvez pas le mettre sur une plate-forme aérospatiale.
Nous pouvons créer des géométries incroyablement complexes et fabriquer des pièces avec la FA qui ne sont tout simplement pas physiquement possibles autrement. Nous pouvons économiser beaucoup de poids, de temps, de matériel et d'argent en fabriquant des pièces via la FA.
La liberté de conception et de fabrication que nous offre AM est claire. Mais l'inconvénient est que c'est bien si vous pouvez faire la partie, mais si vous ne pouvez pas prouver que c'est une bonne partie, cela ne fait de bien à personne.
Les normes sont ce qui nous permet de franchir cette ligne pour pouvoir fabriquer et vendre des pièces et pouvoir les utiliser dans la production pour l'aérospatiale.
Les normes aérospatiales sont donc l'une des pièces clés du puzzle avant de pouvoir fabriquer des pièces.
Diverses organisations de développement travaillent très dur dans ce domaine depuis longtemps. Je travaille comme bénévole sur les normes ASTM depuis environ 10 ans maintenant, et j'ai vu les avantages de ce que nous faisons.
Comme je l'ai mentionné, j'ai contribué à la norme originale de titane pour la fusion sur lit de poudre. Ce premier m'a pris (ainsi qu'à plusieurs autres personnes), un peu plus de deux ans pour le faire valider. Par la suite, nous avons pu en transformer d'autres en environ la moitié de ce temps.
Les choses commencent vraiment à s'accélérer maintenant. L'ASTM a récemment lancé son centre d'excellence basé à Auburn, en Alabama, en collaboration avec l'Université d'Auburn.
L'intention derrière cela était d'appliquer un financement et des efforts ciblés de recherche et développement par l'intermédiaire de partenaires de collaboration pour atteindre plus rapidement des normes. Il y a eu beaucoup de collaboration entre l'industrie et les organismes gouvernementaux pour identifier les lacunes et les normes que nous percevons dans l'industrie, c'est ce dont nous avons besoin pour aller de l'avant.
Vous avez peut-être entendu parler de la feuille de route ANSI. C'est un très bon document auquel certains d'entre nous dans l'industrie ont contribué, afin d'identifier nos principales lacunes, que nous devons combler pour atteindre une véritable production pour la fabrication additive.
Sur la dernière version de cette feuille de route, je crois qu'il y avait 91 lacunes identifiées, principalement dans les domaines des normes, et certaines d'entre elles sont très prioritaires. L'ASTM Center of Excellence est un véhicule utilisé pour appliquer la R&D afin de combler ces lacunes dans les normes.
Dans un autre domaine, SAE International a sa spécification des matériaux aérospatiaux (AMS). Les premiers pour la fusion additive sur lit de poudre étaient AMS 7000, 7001, 7002 et 7003 pour l'alliage de nickel 625, qui a été récemment publié.
Ce sont d'excellents travaux qui donneront beaucoup de résultats. Beaucoup d'entre nous utilisent déjà ces normes pour développer des pièces de production.
Avec votre expérience de l'adoption de la FA, quels ont été certains des défis liés à l'intégration de la technologie en interne et comment avez-vous navigué dans ce processus ?
Oerlikon AM a pour objectif de fournir des solutions de FA qui répondent aux exigences des industries les plus exigeantes, telles que l'aérospatiale et le médical, entre autres.
Dans nos différentes installations, nous avons mis en place les bons systèmes de qualité, tels que AS9100 pour l'aérospatiale et ISO 13485 pour le médical. Mais en ce qui concerne l'intégration de tous les systèmes nécessaires pour y parvenir, cela a été un défi, bien qu'il existe certaines solutions qui fournissent des pièces du puzzle.
Je dirais qu'il n'y a pas de solution unique qui couvre tous les aspects de ce dont nous avons besoin, de bout en bout. Mais il existe de nombreux bons outils qui couvrent des parties de toute cette chaîne d'approvisionnement de bout en bout.
L'un de nos défis est donc d'identifier les solutions qui couvrent les différents aspects de notre chaîne d'approvisionnement, apporter embarquer ceux qui couvrent les aspects dont nous avons besoin et les intégrer.
Par exemple, certaines solutions gèrent très bien les finances et les stocks, mais elles ne conviennent pas très bien aux workflows de fabrication. D'autres gèrent bien les workflows de fabrication et la planification de la production, mais ne gèrent pas, par exemple, l'estimation du temps de construction, les problèmes de révision des matériaux ou les problèmes de composants géométriques, tels que les plans et les modèles 3D.
Il y en a donc beaucoup de différents aspects, et notre défi est d'intégrer toutes ces différentes pièces pour avoir une solution de bout en bout transparente. C'est un processus assez manuel actuellement, mais nous travaillons pour le rendre beaucoup plus automatisé à mesure que nous avançons.
Êtes-vous en mesure de partager des histoires de réussite sur la façon dont vous avez utilisé la FA en production ?
Bien que je ne puisse pas spécifiquement faire référence à ces clients sans obtenir leur autorisation, nous avons plusieurs composants qui sont activement en production. Certains auxquels je peux penser, par cœur, sont des éléments liés à l'aérospatiale et à la défense.
Ainsi, l'un est un composant de vol qui fait partie d'un système de mission sur un hélicoptère militaire. Nous produisons ce composant depuis maintenant deux ans et avons livré avec succès plus de 200 unités à ce jour.
Nous fabriquons également un autre composant qui est utilisé pour un capteur au sol, où vous avez un système intégré de 80 composants individuels différents en une seule pièce monolithique. Celui-ci est également en production depuis près de deux ans.
Nous avons un certain nombre d'autres composants de production que nous fabriquons — pour les zones d'exploration pétrolière et gazière et sous-marine, qui sont en production active pour la robotique sous-marine — pour un autre de nos clients que nous fabriquons des pièces pour, qui sont activement utilisés à la fois dans le pétrole et le gaz, le forage et l'exploration, et la robotique sous-marine.
Comment voyez-vous l'évolution de la fabrication additive au cours des cinq prochaines années, à la fois en termes de technologie et d'industrie dans son ensemble ?
Au cours des cinq prochaines années, je vois la technologie évoluer avec davantage de systèmes multi-laser, ce qui permettra de produire des pièces plus rapidement, réduisant ainsi le coût des composants. Cela stimulera davantage la mise en œuvre des pièces AM.
Le coût des pièces est un facteur clé, et le temps laser est votre principal moteur pour le coût d'un composant de FA. Ainsi, si vous pouvez intégrer plus de lasers dans une pièce et être en mesure de certifier les composants, en utilisant ces systèmes multi-laser, vous pourrez construire la même pièce plus rapidement et donc moins cher.
L'autre évolution est que nous aurons de meilleurs systèmes de surveillance en cours de processus. Il y en a quelques-uns différents actuellement disponibles par différents fabricants, mais j'ai l'impression que même si beaucoup d'entre eux sont de bons systèmes, ils n'ont pas encore le niveau de capacité dont les utilisateurs, comme moi, auraient besoin pour être en mesure de les mettre en œuvre. à un taux de production réel.
J'espère que nous aurons bientôt une véritable surveillance en cours de processus, afin que nous puissions surveiller ce qui se passe dans la machine pendant le processus et être en mesure d'identifier les problèmes avec un composant avant qu'il ne quitte le machine.
Le scénario idéal serait de disposer d'un logiciel intelligent capable d'identifier les problèmes et éventuellement d'apporter des corrections avec une assistance technique à la volée. Bien sûr, le mieux serait d'avoir des machines vraiment robustes qui n'ont aucun problème et qui fonctionnent 24h/24 et 7j/7.
Y a-t-il des tendances qui vous passionnent ?
Je suis enthousiasmé par divers développements, les systèmes de surveillance en cours de processus, comme je l'ai mentionné, en étant un.
De nouveaux supports sont également en cours de développement et de lancement. Nous développons quelques matériaux différents qui permettent à certains de nos clients de fabriquer des composants très révolutionnaires.
L'autre chose qui me passionne, c'est qu'il y a beaucoup plus de diversification des fabricants à travers le monde. Au début, la plupart des machines AM étaient produites dans une poignée de pays en Europe. Aujourd'hui, de nouveaux fabricants et divers pays appliquent des approches différentes et novatrices à la construction de machines.
Ils réduisent le coût des machines et apprennent, de leur utilisation dans l'ensemble de l'industrie, à les rendre plus intuitives pour les opérateurs.
Mon expérience des premières années avec ces machines, c'est qu'elles sont très pointilleuses et nécessitent beaucoup d'attention et de « baby-sitting ». Et franchement, une grande partie de la conception de la machine n'était pas très conviviale pour la fabrication.
Je vois maintenant beaucoup de convivialité dans les machines, car les fabricants de machines reçoivent les commentaires de leurs utilisateurs.
Mais aussi, la concurrence accrue de différents fabricants à travers la planète contribue, je pense, à stimuler l'innovation dans les systèmes, à réduire les coûts et à augmenter la convivialité des systèmes de machines.
Quelle est la prochaine étape pour Oerlikon, en particulier pour l'installation que vous aidez à superviser et à gérer ?
Notre objectif à court terme pour cette installation est d'installer et de certifier tout l'équipement que nous avons acheté. Nous avons donc 18 systèmes de lit de poudre métallique en ligne et opérationnels actuellement, et nous fabriquons du matériel de production sur bon nombre de ces systèmes.
Notre prochaine étape pour ceux-ci consiste à compléter les propriétés des matériaux pour tous nos systèmes de matériaux sur toutes nos machines et les ensembles de données correspondants. Mais cela prend beaucoup de temps et coûte cher.
Heureusement, nous avons beaucoup de gens très talentueux ici avec beaucoup d'expérience dans les matériaux, la métallurgie et l'ingénierie, et je suis très fier d'être membre de cette équipe.
L'autre objectif est de mettre en place tous les autres équipements pour réaliser cette véritable installation de production de fabrication de bout en bout.
Nous avons récemment mis en ligne notre four HIP et notre four à vide, et nous travaillons à les faire certifier.
Nous avons également apporté des équipements CNC, et nous avons également un nombre substantiel de fours supplémentaires et d'équipements CNC pour le post-traitement à apporter. L'objectif est donc d'installer, de certifier et d'intégrer tous ces équipements pour créer un système de fabrication complet et cohérent.
Pour en savoir plus sur Oerlikon, visitez : https://www.oerlikon.com/en/
impression en 3D
- Entretien avec un expert :professeur Neil Hopkinson, directeur de l'impression 3D chez Xaar
- Entretien avec un expert :Philip Cotton, fondateur de 3Dfilemarket.com
- Entretien avec un expert :Spencer Wright de pencerw.com et nTopology
- Entretien avec un expert :Dr Alvaro Goyanes de FabRx
- Entretien d'experts :Guillaume de Calan, PDG de Nanoe, sur l'avenir de l'impression 3D céramique
- Entretien d'experts :John Kawola, président d'Ultimaker, sur l'avenir de l'impression 3D
- Comment Ford Motor Company innove l'impression 3D pour l'industrie automobile :entretien d'expert avec Harold Sears
- Entretien d'experts :Simon Fried, cofondateur de Nano Dimension, sur l'essor de l'impression 3D pour l'électronique
- Entretien d'experts :Brian Alexander de Solvay sur le développement de polymères hautes performances pour l'impression 3D