De nouveaux horizons dans le soudage des composites thermoplastiques
Ce blog accompagne l'article de septembre 2018 « Soudage des composites thermoplastiques ». Il s'agit d'une compilation d'images et de détails qui ne rentraient pas dans l'article imprimé, y compris une chronologie des développements du soudage par induction et des détails sur la qualification pour les futurs avions commerciaux, ainsi que de courtes sections sur la réparation, les développements pour l'automobile et le thermodurcissable en thermoplastique (TS -TP) soudage.
Juste pour réitérer pourquoi les assemblages composites thermoplastiques soudés (TPC) sont intéressants à la fois pour les structures légères de l'aérospatiale et de l'automobile, comparez les deux images ci-dessous de la cloison de pression arrière de l'Airbus A320. L'image du haut est la version actuelle en aluminium. Remarquez le grand nombre de rivets. Comparez maintenant cela avec le démonstrateur TPC soudé présenté par Premium Aerotec au salon aéronautique ILA 2018 à Berlin. Remarquez l'absence de rivets. Pour les composites, cela élimine non seulement le poids, le temps et le coût des fixations, mais également le temps et le coût de positionnement et de perçage des trous, ainsi que le nettoyage et l'inspection de ces trous. Cela signifie également des structures beaucoup plus légères sans les rembourrages stratifiés nécessaires pour compenser les coupures à travers les fibres porteuses.
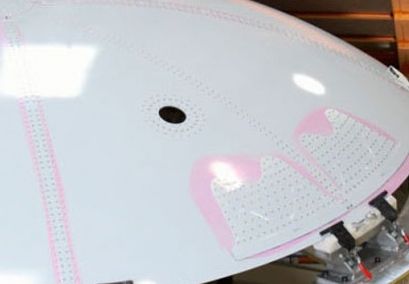
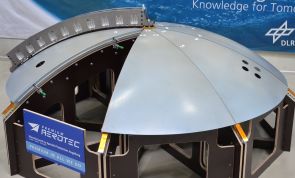
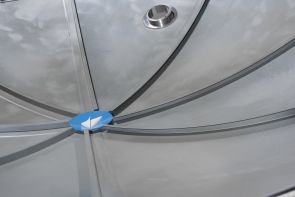
Une cloison de pression arrière en composite thermoplastique A320 soudée (en bas) offre une solution sans rivet par rapport à la construction actuelle en aluminium (en haut).
SOURCE :RUAG (en haut) et Premium Aerotec (en bas), DLR Center for Lightweight Production Technology (Augsbourg, Allemagne)
« Un autre avantage est que l'inspection des structures soudées est plus facile par rapport aux assemblages collés», explique le Dr Hans Luinge, directeur de la R&D et du développement de produits composites thermoplastiques pour le fournisseur de matériaux TPC TenCate-Toray Group. « C-scan fonctionne bien, montrant s'il n'y a pas de porosité dans le stratifié, ce qui signifie que la soudure est bonne. Pour les structures collées, vous pouvez avoir un lien de baiser ou des contaminants difficiles à détecter. Bien que TenCate-Toray ne développe pas lui-même la technologie de soudage, il prend en charge une variété de projets industriels et clients. « Nous optimisons nos matériaux selon les besoins », explique Luinge, « et essayons d'aider à orienter les développements dans la bonne direction sur la base de notre participation de longue date à des efforts tels que TAPAS et avec des partenaires tels que KVE Composites, le TPRC, des fournisseurs de niveau et des OEM. »
Développements en soudage par induction
KVE Composites a développé le soudage par induction pour les TPC depuis 2001. Les premières applications utilisaient des stratifiés de tissu de fibre de carbone/PPS, y compris les ascenseurs et le gouvernail pour les avions d'affaires Gulfstream G650 et Dassault Falcon 5X.
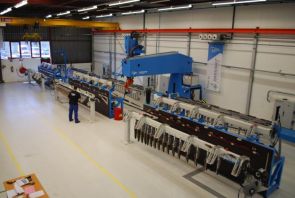
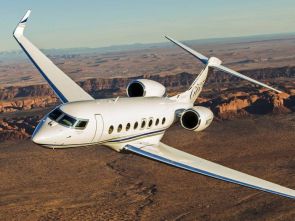
KVE Composites a aidé pour développer la production de GKN Fokker d'ascenseurs et de gouvernails soudés par induction (à gauche) pour les avions Gulfstream G650 (à droite) et Dassault Falcon 5X.
SOURCE :KVE Composites, GKN Fokker (à gauche) et Gulfstream (à droite).
D'autres applications TPC soudées par induction incluent les portes d'accès au réservoir de carburant produites par AVIACOMP S.A.S. (Launaguet, France et maintenant membre du Groupe Sogeclair) pour l'aile d'Airbus A220 (anciennement Bombardier CSeries). (Aviacomp a également produit les longerons du fuselage soudé TPC de STELIA présenté au salon du Bourget 2017.)
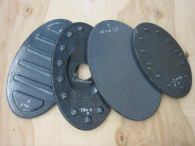
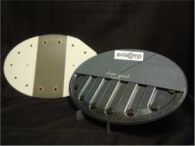
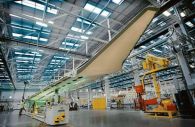
Aviacomp utilise l'induction technologie de soudage développée par KVE Composites dans sa production de portes d'accès aux réservoirs de carburant TPC pour l'avion à fuselage étroit Airbus A220.
SOURCE :Aviacomp, filiale du groupe Sogeclair.
Cette catégorie générale de portes d'accès est une opportunité pour le soudage TPC de réduire les coûts, comme le montre une étude de conception et de fabrication réalisée par KVE Composites. Même les avions plus petits peuvent avoir jusqu'à 60 de ces panneaux d'accès, tous de forme différente et généralement fabriqués en utilisant une construction sandwich composite avec un noyau en nid d'abeille usiné. « Si vous utilisez un assemblage thermoplastique soudé, vous pouvez fabriquer tous les différents panneaux d'accès pour un avion avec seulement 100 000 $ de coûts d'outillage, ce qui représente une économie considérable », explique Harm van Engelen, directeur général de KVE Composites. « Nous n'avons pas besoin d'usiner le noyau, nous utilisons simplement des composants « de type lego » - des tôles plates et des raidisseurs estampés - soudés ensemble pour former les différentes formes. De plus, notre outillage ressemble plus à un gabarit de soudage, donc un coût relativement faible par rapport à ce qu'ils utilisent aujourd'hui. Tous les panneaux d'accès d'un avion pourraient être réalisés dans une seule cellule de soudage. »
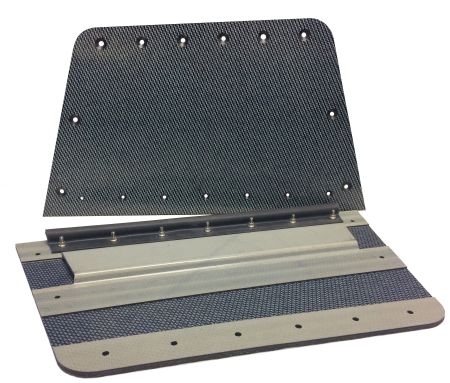
Boîte d'assemblage thermoplastique soudée pour panneaux de porte-à-faux d'avion être fabriqué à l'aide de cellules de formage et de soudage automatisées et économisez 100 000 $ en frais d'outillage. SOURCE : KVE Composites.
KVE Composites poursuit son développement des technologies de soudage TPC, comme illustré dans les chronologies ci-dessous. La cellule de production illustrée en bas pour 2019 est la machine Falko ATL (pose automatisée de ruban), produite par Boikon (Leek, Pays-Bas) à l'aide d'un effecteur de soudage par ultrasons développé par GKN Fokker. « Cette cellule robotisée permet un processus et un système de contrôle plus efficaces pour le prochain niveau de production de pièces TPC en volume par rapport aux méthodes de prélèvement et de placement utilisées aujourd'hui », explique Maarten Labordus, responsable R&D de KVE Composites. « Par exemple, vous pouvez mettre en place de manière entièrement automatique les stratifiés de peau et de côtes pour une surface de contrôle de jet régional (qui mesure environ 60 mm x 3 m), appliquer une étape de consolidation et de formage hors autoclave, puis terminer l'assemblage dans un cellule de soudage attenante. La machine Falko ATL démontre également le contrôle en boucle fermée déjà développé par GKN Fokker pour le soudage par ultrasons. « La machine est capable de contrôler le niveau d'énergie selon les besoins en fonction du type de matériau, de l'épaisseur et de la forme, mais une consolidation complète à l'état fondu de la préforme plate est nécessaire par la suite pendant le moulage de la pièce TPC finie », explique Arnt Offringa, responsable de la R&T des aérostructures pour GKN. Fokker.
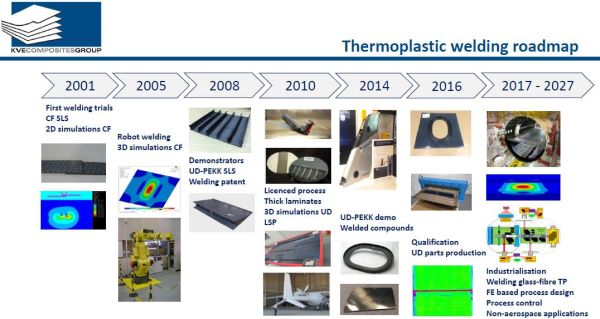
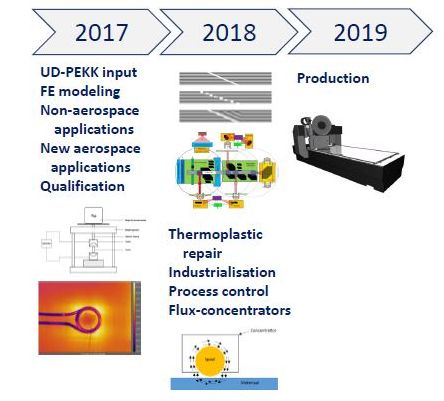
Qualification
Montré ci-dessus comme une initiative de développement clé en 2017, qualification des procédés de soudage par induction des aérostructures TPC est une priorité permanente. D'après le résumé de la prochaine présentation de KVE Composites au 4 th Int. Conf. et exposition sur les composites thermoplastiques (ITHEC, 30-31 octobre 2018 à Brême, Allemagne), au cours des dernières années, le soudage des composites thermoplastiques (TPC) a vu une évolution des polymères comme le PPS et le PEI vers des polymères haut de gamme tels que le PEEK , PEKK et maintenant Low Melt PAEK (LM PAEK, en savoir plus sur mon blog "PEEK vs. PEKK vs. PAEK ..."), ainsi que vers des rubans UD placés automatiquement et des stratifiés plus épais pour des structures plus fortement chargées. En réponse, KVE Composites a cherché à améliorer et à standardiser l'outillage et l'équipement ainsi que les modèles de simulation basés sur FEA.
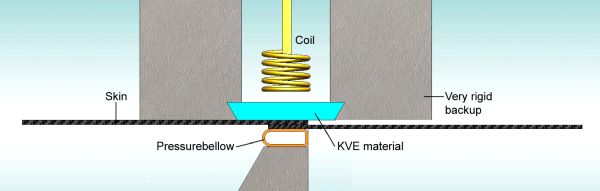
Mise en place standardisée pour la qualification du soudage par induction avec de nouveaux matériaux.
SOURCE : KVE Composites
Pour aider à la maturation et à la qualification du processus de soudage par induction avec ces nouveaux stratifiés composites, KVE Composites a développé une configuration standardisée pour le soudage par cisaillement simple et également des coupons de test de traction en L et en T. Cette configuration comprend :
- Un cadre rigide pour supporter les charges résultant de l'application de pression sur le stratifié pendant le soudage.
- Un bloc d'outils inférieur qui peut être positionné sous le cadre pour permettre un soudage reproductible des panneaux standard.
- Un mandrin gonflable (soufflet de pression dans la figure ci-dessus) dans le bloc d'outils inférieur qui peut se dilater dans une seule direction pour comprimer le stratifié à souder contre un dissipateur thermique spécial ("matériau KVE" dans la figure ci-dessus) pour confiner la chaleur au soudage interface.
En interchangeant les blocs d'outils inférieurs, une variété de coupons standard peuvent être soudés puis inspectés par ultrasons, après quoi des coupons plus petits peuvent être coupés et testés mécaniquement. Cette configuration standardisée a déjà été installée par :
- Centre de recherche sur les thermoplastiques (TPRC, Enschede, Pays-Bas)
- Centre McNair de l'Université de Caroline du Sud (Columbus, SC, États-Unis)
- Centre aérospatial des Pays-Bas (NLR, Marknesse, Pays-Bas).
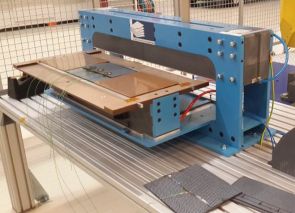

Soudage par induction standardisé installation au KVE (à gauche) et échantillon de fibre de carbone UD/PEKK soudé avec des thermocouples pour enregistrer la température sur la ligne de soudure (à droite).
SOURCE : KVE Composites.
Réparation
Un autre domaine de développement clé est la réparation des aérostructures TPC. « Nous nous concentrons d'abord sur les structures en tissu CF/PPS qui sont qualifiées et volantes », explique Labordus. « Le processus est fondamentalement le même que celui utilisé pour les réparations composites thermodurcissables :retirez le matériau endommagé, préparez cette zone avec un foulard effilé, puis collez un patch de réparation préimprégné. Labordus dit que l'un des problèmes est que le préimprégné thermoplastique à température ambiante est cartonné et ne colle pas, "il est donc difficile de faire correspondre la géométrie". Cependant, il pense que les systèmes de réparation robotisés développés par Airbus, Lufthansa et d'autres offrent une solution.
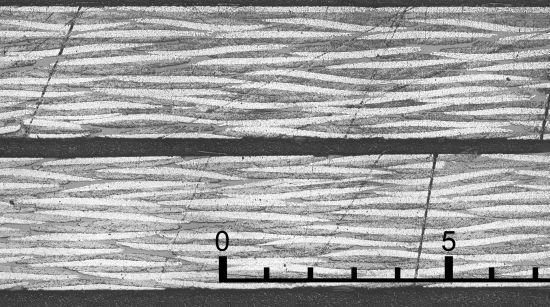
Dans le cadre de son développement continu de réparations composites thermoplastiques structurelles soudées, KVE Composites a réalisé des joints coniques linéaires 2D soudés par induction dans des stratifiés en tissu CF/PPS avec une épaisseur uniforme et 90 % de propriétés de matériau vierge.
SOURCE : KVE Composites.
De tels systèmes utilisent la métrologie pour mesurer avec précision les écharpes coniques usinées par robot, puis coller un patch préfabriqué qui a été usiné par robot pour correspondre. « Nous voulons utiliser le soudage par induction pour souder un patch thermoplastique à la structure d'origine », explique Labordus, mais il reste encore des problèmes à résoudre. « Selon la forme de la pièce et du patch, les courants de Foucault ne se forment pas partout, on peut donc avoir des zones de fraîcheur ou de surchauffe. KVE Composites a réussi à résoudre ce problème et a pu réaliser un joint conique linéaire 2D dans des stratifiés en tissu CF/PPS avec une épaisseur uniforme et une soudure parfaite. « Nous étions à moins de 10 % des propriétés des matériaux vierges », explique Labordus.
L'étape suivante consistera à souder par induction deux pièces rectangulaires chacune avec un bord effilé, puis à souder un patch conique à un trou circulaire/elliptique avec une écharpe conique, qui est essentiellement la méthode utilisée pour les réparations composites thermodurcissables. « Si cela fonctionne, nous passerons ensuite aux stratifiés UD fabriqués avec du PEEK et du PEKK », explique Labordus. Il note qu'un système permettant d'utiliser une bobine d'induction pour effectuer des réparations sur le terrain n'a pas encore été démontré, "mais peut le faire en laboratoire". Un autre problème est de savoir comment appliquer une pression pour un contact suffisamment étroit entre le patch de réparation et la surface conique. « Actuellement, la pression utilisée dans l'outil de laboratoire est de 5 bars. Je ne suis pas sûr que la pression du sac sous vide soit suffisante, mais avec un matériau UD plus plat, 1 bar du sac sous vide peut suffire.
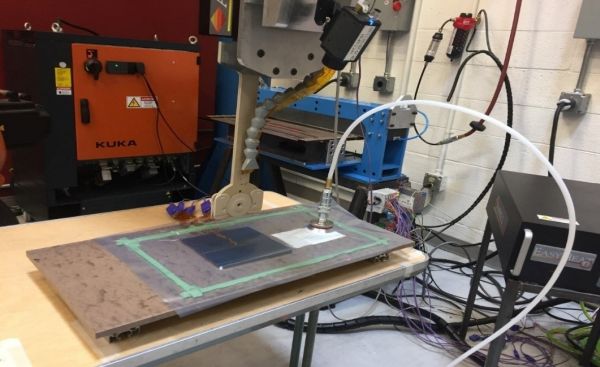
Le soudage par induction sous un sac sous vide - un catalyseur possible pour les futures réparations de composites thermoplastiques sur le terrain - est développé par Michel van Tooren et son équipe au McNair Center de l'Université de Caroline du Sud. SOURCE :Michel van Tooren.
Ce travail chez KVE Composites est prolongé par Michel van Tooren, directeur du SmartState Center for Multifunctional Materials and Structures, qui fait partie du McNair Center de l'Université de Caroline du Sud (Columbia, SC, US). « Nous soudons par induction des composites thermoplastiques sous un sac sous vide, ce qui est très similaire à la façon dont les réparations composites sur le terrain sont effectuées aujourd'hui avec un liant chaud et une couverture chauffante », explique-t-il. « Le sac sous vide se comporte comme un outillage souple pour la compression des deux parties. Vous appliquez un courant d'induction et réalisez une réparation par fusion. Il vous suffit de définir les limites et les paramètres du processus. À certains égards, c'est plus facile que la réparation thermodurcissable car vous pouvez toujours refondre la réparation si nécessaire, même à l'autre bout du monde ou après 20 ans de service. Et le résultat n'est pas une liaison adhésive mais plutôt une pièce cohésive, vous éliminez ainsi tous les problèmes de liaison et comment savoir si vous avez une bonne liaison dans une réparation thermodurcissable. Lui aussi pense qu'avec les technologies de réparation robotique automatisées en cours de développement, "le soudage par induction d'une réparation serait relativement simple".
Soudure thermodurcissable à thermoplastique
Van Tooren développe également le soudage par induction pour assembler des composites thermodurcissables et thermoplastiques. « Nous introduisons le thermoplastique dans un composite thermodurcissable, mais uniquement là où nous voulons souder », explique-t-il. « Nous greffons sur une nanoparticule et faisons un petit peu de polymérisation croisée. Le résultat est un îlot de thermoplastique implanté et co-fondu chimiquement avec le composite thermodurci. Je peux ensuite souder sur l'îlot thermoplastique. Encore une fois, la vision est des méthodes alternatives pour l'assemblage et l'assemblage de composites qui évitent de percer des trous et les problèmes associés au collage conventionnel.
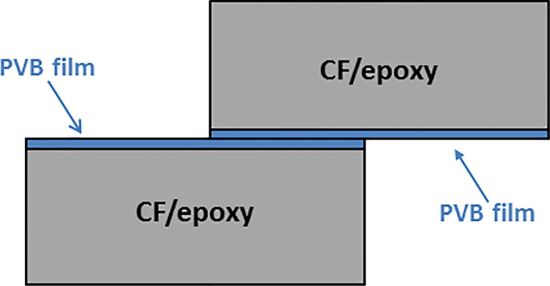
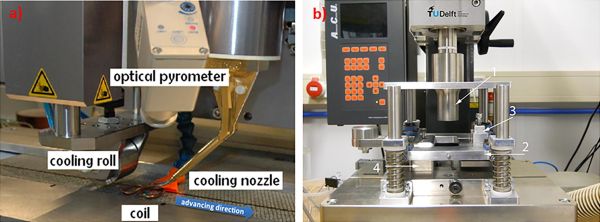
Schéma d'un joint TSC-TSC via couche de couplage thermoplastique PVB avant soudage (en haut). Configurations (en bas) pour le soudage par induction (à gauche) et le soudage par ultrasons (à droite).
SOURCE : « Soudage hybride des composites à base de CF/époxy ».
Le soudage de stratifiés composites thermodurcissables (TSC) aux stratifiés TPC (ou soudage TS-TP) est poursuivi par plusieurs organismes de recherche. Irene Fernandez Villegas de la TU Delft - qui est mentionnée dans l'article imprimé comme un leader dans le développement du soudage par ultrasons continu des TPC - est co-auteur d'un article de 2017 intitulé "Soudage hybride de composites à base d'époxyde renforcés de fibres de carbone" avec Francesca Lionetto au Université du Salento (Lecce, Italie), Silvio Pappadà au CETMA Composites (Brandisi, Italie), et autres. Les bases sont les suivantes :
- Le polyvynilbutyral (PVB) est un polymère thermoplastique semi-cristallin à faible coût avec une température de fusion de 150-170°C caractérisé par une excellente capacité de liaison et de formation de film et une adhérence à de nombreuses surfaces.
- Le PVB (Mowital, fourni par Kurakay) a été utilisé comme couche de couplage, ajouté et co-durci à un tissu en fibre de carbone 14 plis/stratifié époxy TSC (Hexcel 3501-6 préimprégné avec une teneur en volume de fibres de 58 % et 180 °C durcissement).
- L'emboîtement macro-mécanique entre la couche de couplage PVB et le composite CF/époxy a été obtenu par pénétration partielle de la résine PVB dans la première couche du TSC (typiquement entre 10 et plusieurs centaines de microns d'épaisseur) lors de la co-durcissement et diffusion des monomères époxy dans le film thermoplastique PVB.
- Les procédés de soudage par induction et de soudage par ultrasons ont permis d'obtenir des joints soudés suffisamment solides, les joints CF/époxy à CF/époxy soudés à travers les couches de couplage PVB présentant une résistance au cisaillement par recouvrement de ≈25 MPa, ce qui se situe dans la plage typique de valeurs de résistance pour les joints collés CF/époxy.
Automobile
Presque toutes les entreprises incluses dans l'article imprimé sur le soudage thermoplastique étudient les applications automobiles et aérospatiales. « Le soudage contribue à rendre les composites compétitifs par rapport à l'aluminium », déclare Offringa chez GKN Fokker. « L'automobile envisage également le soudage comme une alternative rapide au collage. Nous avons discuté avec plusieurs constructeurs automobiles concernant le traitement rapide des composites. Il souligne que les carrosseries de voitures en composite de fibre de carbone sont pour la plupart thermodurcissables, collées avec une épaisseur spécifiée d'adhésif. « Si vous pouviez fabriquer ces pièces en thermoplastique composites et d'éliminer les écarts entre les composants en soudant l'assemblage, vous pouvez alors créer une structure de carrosserie plus rigide, ce qui apporte des avantages en termes de poids, de coût et de performances. »
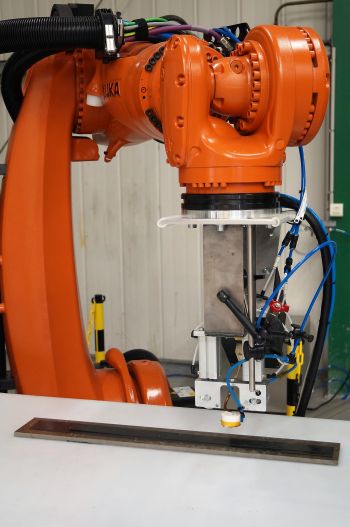
Dynamique de l'intégrité composite configuration du procédé de soudage par induction.
SOURCE :intégrité composite.
Jérôme Raynal, responsable du développement commercial de Composite Integrity voit également du potentiel. Son entreprise a travaillé avec STELIA Aerospace pour développer le procédé de soudage dynamique par induction utilisé pour assembler les longerons de ruban CF/PEKK UD et les peaux de fuselage dans le démonstrateur TP, dévoilé au salon du Bourget 2017. « Nous avons développé le soudage résistif pour l'automobile avec des composites à la fois de polyamide [PA, nylon] et de polypropylène [PP] », explique Raynal. « Nous avons une variété de technologies différentes pour cela. Par exemple, on peut noyer un fil métallique dans une pièce, le mettre en contact avec une autre pièce et injecter du courant. Nous pouvons également placer un patch résistif en fibre de carbone à l'interface de soudage pour générer la chaleur de soudage nécessaire. Dans un développement, deux composants en CF/PA ont été soudés à l'aide d'un patch résistif spécialement conçu avec le même polymère et un non-tissé en fibre de verre pour isoler électriquement le stratifié adjacent et concentrer l'énergie au niveau de la ligne de soudure. Qu'en est-il des inserts métalliques très typiques des pièces automobiles ? "Les pièces avec inserts métalliques ne posent aucun problème avec le soudage par résistance, et avec le soudage par induction, vous utiliseriez une bobine spécialement conçue ou modifieriez les champs électromagnétiques et le courant d'une autre manière", répond Raynal. "Cela serait à développer, mais c'est similaire à ce que nous avons déjà démontré pour la production automatisée de structures d'avions."
Développements ultérieurs et autres projets
Une note concernant l'image d'ouverture. Il montre un rendu CAO du processus automatisé développé par le DLR Center for Lightweight Production Technology (DLR ZLP, Augsburg, Allemagne) à l'aide d'un soudage par ultrasons tête sur un robot industriel KUKA Quantec KR210 pour joindre huit sections TPC dans une cloison de pression arrière (RPB) pour un avion de type A320. Dans l'article imprimé d'accompagnement sur le soudage TPC, j'ai discuté du développement par DLR ZLP d'un soudage par résistance méthode qui a été utilisée sur le démonstrateur A320 RPB de Premium Aerotec exposé au salon aéronautique ILA 2018 à Berlin. Selon Lars Larsen, chef de groupe pour les technologies d'assemblage et d'assemblage chez DLR ZLP, « En parallèle au processus de soudage par résistance utilisant un « pont de soudage », nous avons également développé une tête de soudage à ultrasons actionnée par robot. Nous avons effectué des tests préliminaires pour déterminer les paramètres pertinents du processus de soudage et, dans les prochains mois, nous affinerons l'intégration de cet effecteur de soudage par ultrasons dans notre robot. Notre objectif est de développer un procédé industriel unique pour souder à la fois les longerons de fuselage d'avion et la cloison de pression arrière en composites thermoplastiques. »
D'autres projets que je n'ai pas eu la chance de couvrir cette fois-ci incluent EireComposites et sa participation aux projets Ybridio et Innova, poursuivant le potentiel du soudage pour réduire les coûts et augmenter l'automatisation. La société signale une capacité de soudage par induction et de soudage par résistance pour les composites CF/PEEK, CF/PEKK et GF/PP et que le soudage thermoplastique a été évalué pour l'aile Bombardier CSeries (maintenant l'Airbus A220).
Tods Aerospace, qui fait maintenant partie d'Unitech Aerospace, a participé à un programme national d'exploitation de la technologie aérospatiale (NATEP) parrainé par Rolls-Royce qui a examiné le développement d'une technique de soudage par résistance qui n'utilise pas d'implants métalliques intégrés. TenCate-Toray et le National Composites Center (Bristol, Royaume-Uni) étaient également partenaires.
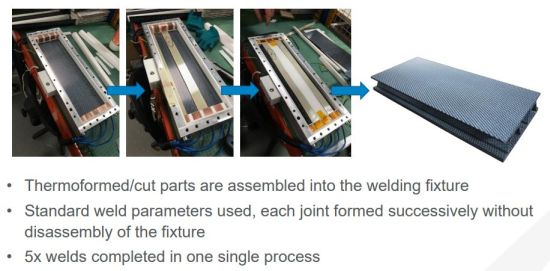
Ce démonstrateur de procédé a exploré une méthode de fabrication de structures TPC renforcées en chapeau. SOURCE :Unitech Aerospace (commencer à la section 6, p. 39)
Restez à l'écoute, car je prévois de couvrir les développements de Laser Zentrum Hannover (LZH) avec le soudage laser de composites thermoplastiques dans un avenir proche.
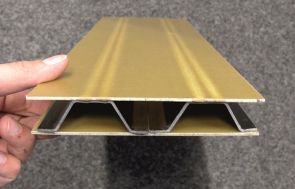
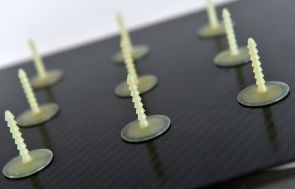
SOURCE :LZH Laser Zentrum Hanovre eV
Résine
- Covestro intensifie ses investissements dans les composites thermoplastiques
- Composites thermoplastiques chez Oribi Composites :CW Trending, épisode 4
- Le projet RECONTRAS valide l'utilisation des micro-ondes et du soudage laser pour obtenir des composites recyclables
- La nouvelle botte de randonnée Salewa est dotée de composites thermoplastiques
- Dépannage du thermoformage des composites thermoplastiques
- Composites thermoplastiques :support de pare-chocs structurel
- Le consortium IRG CosiMo sur les composites thermoplastiques dévoile de nouvelles installations
- Composites thermoplastiques :vue panoramique
- Soudage de composites thermoplastiques