Construire le musée du futur
Le musée du futur actuellement en construction à Dubaï, aux Émirats arabes unis (EAU), est l'une des structures les plus complexes jamais construites. Le bâtiment de 78 mètres de haut abrite sept étages dans une coque en forme de tore qui se trouve au sommet d'un podium de trois étages. La façade extérieure du tore comprend 1 024 panneaux composites ignifuges (FR). Revêtu d'acier inoxydable, chaque panneau a une forme 3D unique et intègre une calligraphie arabe moulée. Le script fluide forme des poèmes qui décrivent la vision de l'avenir de Dubaï par Son Altesse le cheikh Mohammed bin Rashid Al Maktoum, vice-président et premier ministre des Émirats arabes unis et dirigeant de l'émirat de Dubaï. Ils servent également de fenêtres au bâtiment, projetant la lumière du jour à travers l'intérieur sans colonnes et créant un effet dramatique la nuit grâce à 14 kilomètres d'éclairage LED intégré.
Conçu par Cheikh Mohammed comme un incubateur d'innovation et d'invention, le Musée du futur est considéré comme l'un des bâtiments les plus avancés au monde, un lieu où les gens peuvent expérimenter et rechercher de nouvelles technologies. C'est aussi un symbole d'architecture qui repousse les limites via la conception numérique et l'utilisation de matériaux plus efficaces. La conception paramétrique a été utilisée pour développer le sommier en acier - un cadre de 2 400 éléments en acier se coupant en diagonale - auquel des dalles de plancher en béton composite et 17 000 mètres carrés de revêtement composite sont fixés, ce dernier utilisant 1 million de mètres carrés de verre multiaxial et renforcé de fibres de carbone préimprégné époxy.
La société de Dubaï Affan Innovative Structures a fourni la conception composite des panneaux, ainsi que la fabrication et l'assistance pour l'installation. « C'est la première fois qu'un tel projet est entrepris », a déclaré le PDG de l'entreprise, le Dr Amer Affan. "Et aussi la première fois que des panneaux composites ont été utilisés pour intégrer plusieurs fonctions de construction via des formes aussi complexes."
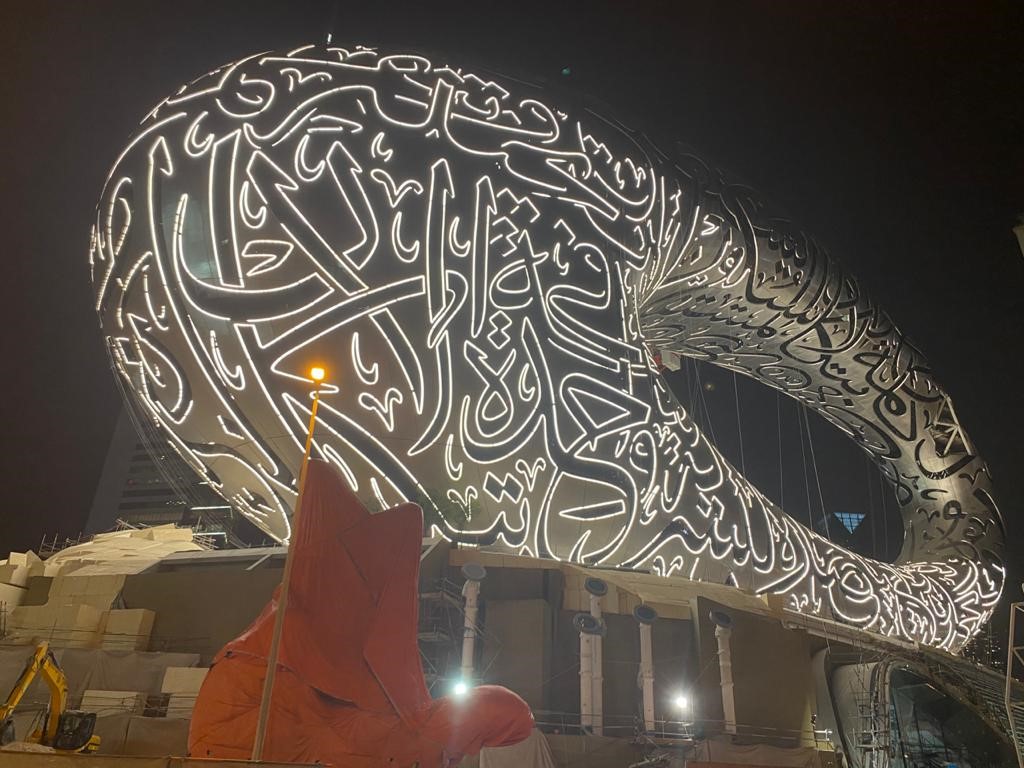
L'architecte principal Shaun Killa explique que ces extérieurs complexes sont normalement des écrans pare-pluie, avec un bâtiment derrière qui contient le système d'étanchéité. "Cela simplifie les choses car c'est un peu plus indulgent lors de la création de ces formes très tridimensionnelles", note-t-il. « Dans ce bâtiment, cependant, l'enveloppe fait l'imperméabilisation, l'étanchéité à l'air, la structure et l'éclairage. Affan concède que pour un si grand projet, son entreprise est de petite taille, "mais nous avons utilisé notre expertise technique pour réaliser quelque chose d'unique et avons montré comment les bâtiments seront construits à l'avenir."
Capacité en conceptions numériques complexes
Affan Innovative Structures a été initialement contacté par l'équipe d'ingénierie du Musée du Futur. « Il n'y avait pas beaucoup d'entreprises qui pouvaient faire les travaux requis pour le revêtement extérieur », note Affan. « Le seul autre concurrent proposait un mur-rideau normal avec des panneaux en aluminium ou en acier inoxydable à l'extérieur. » Les murs rideaux, généralement utilisés en plus d'une charpente métallique, sont minces et constitués de cadres en aluminium qui supportent des panneaux extérieurs en verre, en métal et/ou en pierre mince (voir « L'enveloppe du bâtiment :façades unitisées en PRF »). Cela a été rejeté par l'équipe d'ingénierie car trop difficile et incapable de fournir la même apparence que cela était possible en utilisant une façade en panneaux composites multifonctionnels intégrés. Ainsi, ce dernier, proposé par Affan Innovative Structures, a été retenu pour le projet. "Nous disposons également d'une technologie unique qui nous permet de fabriquer de grands panneaux", ajoute Affan, "jusqu'à 3 mètres de large sur 9 mètres de haut, courbés dans les deux sens, ce qui signifie moins de joints."
Affan Innovative Structures était parfaitement adapté à ce projet. Fondée en 2004 par le Dr Affan, l'entreprise fournit des solutions clés en main complètes — de la conception à l'installation et à l'entretien des bâtiments — gravitant vers des défis très techniques. Le curriculum vitae de la société comprend l'écran/le revêtement complexe et géométrique en aluminium du stade King Abdullah Sports City (Djeddah, Arabie saoudite), la verrière d'entrée en composite et 64 lucarnes en verre et en acier aux motifs complexes pour le centre commercial Yas (Abu Dhabi, Émirats arabes unis) , le toit extérieur composite de l'hôpital Sidra (Doha, Qatar) et de nombreux autres projets ambitieux. Cette capacité dans les assemblages complexes d'acier, de verre et de composite serait exactement ce dont avait besoin l'extérieur composite multifonctionnel du Musée du futur.
« À l'intérieur de chaque panneau composite, il existe un système de [panneaux] de verre plat à l'intérieur de l'écriture arabe », explique Affan. « Le verre est presque encastré à l'intérieur des panneaux, jusqu'à 200 millimètres de profondeur. Cet évidement change non seulement du haut du bâtiment, avec moins d'évidement pour empêcher le piégeage de l'eau, vers le bas, où les panneaux verticaux et en contre-dépouille peuvent être profondément encastrés sans piéger l'eau, mais aussi à l'intérieur de chaque panneau, en s'inclinant et en diminuant pour produire un effet graduel et naturel bord pour le script. « L'emplacement et les bords de l'évidement variaient également en fonction de l'emplacement du verre dans le panneau, car le verre était plat mais les panneaux étaient incurvés », note Affan. « Cela n'était possible qu'avec la conception numérique et l'usinage CNC. » Cette précision serait également nécessaire pour garantir que le script, qui variait d'un panneau à l'autre, s'alignait précisément au fur et à mesure de l'installation des panneaux afin que les lettres et les mots s'écoulent correctement à l'extérieur du bâtiment.
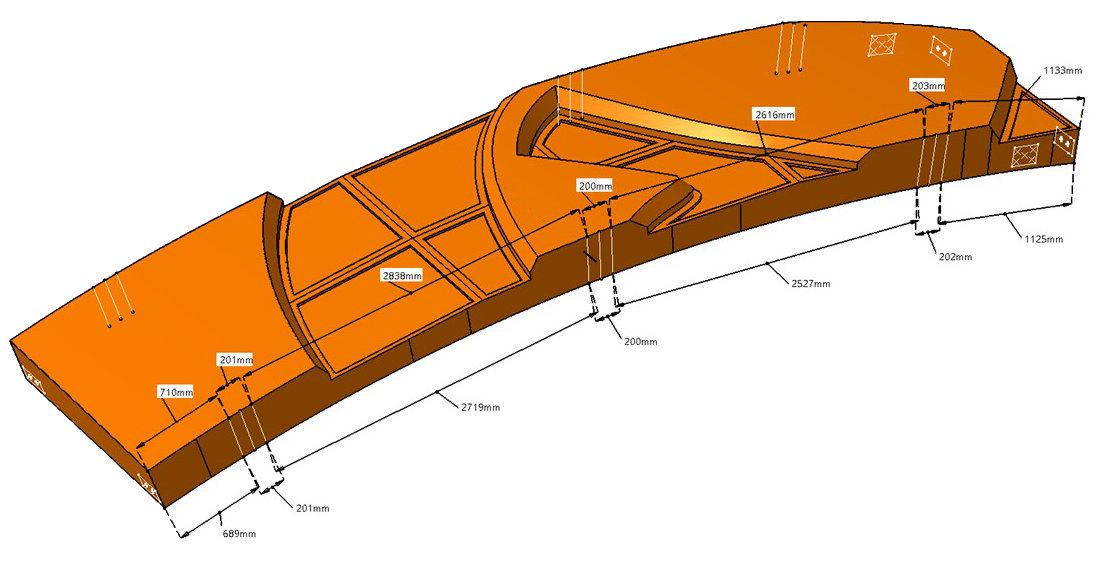
Pour Affan, la seule solution était de mouler l'écriture arabe et les évidements dans chaque panneau composite. « Les renforts seraient déposés dans des moules usinés CNC avec précision », explique-t-il. Fortuitement, le logiciel CATIA (Dassault Systèmes, Vélizy-Villacoublay, France) qu'Affan Innovative Solutions utilise pour piloter ses machines CNC est également le programme de CAO 3D utilisé par l'industrie aérospatiale pour concevoir des avions complexes et des structures composites. De plus, l'équipe de 28 ingénieurs d'Affan maîtrise également les logiciels Tekla BIM, Rhino 3D (Robert McNeel &Assoc., Seattle, Wash., États-Unis) et AutoCAD by Autodesk. « Nous avons réalisé tous les dessins dans CATIA, ainsi que la conception du stratifié, ce qui nous a permis de réaliser un usinage aussi complexe », explique Affan.
La conception, cependant, n'était pas triviale et devait répondre à une variété de charges structurelles et de vent. Par exemple, l'intérieur du tore a créé un effet de soufflerie, explique Affan. Ces panneaux doivent supporter jusqu'à 450 kg/m 2 (92 lb/pi 2 ) de la charge de vent. (Remarque, le Code international du bâtiment répertorie les charges de vent de 71 lb/pi 2 pour les zones à haut risque d'ouragan à West Palm Beach, en Floride, aux États-Unis). Les panneaux composites du Musée du Futur sont également conçus pour minimiser le poids. « Les panneaux utilisent 9 à 13 plis, qui varient selon l'emplacement et le chargement », explique Affan. Il ajoute que le Composite Technology Center (Stade, Allemagne), filiale d'Airbus et partenaire de longue date via l'organisation commerciale CFK Valley ev (Stade, Allemagne), « a fourni un contrôle tiers sur la conception, la déflexion et la rigidité de nos stratifiés. calculs."
Une complexité supplémentaire, et une innovation, est que les panneaux ont également intégré leur propre système de fixation. « Sur les bords, 24 plis forment la géométrie de fixation en forme de cassette pour se connecter au bâtiment », explique Affan. Un système de cassette est une méthode de fixation du revêtement extérieur, développée à l'origine pour les installations de type écran pare-pluie. Bien que les types et les géométries varient, les cassettes permettent généralement une surface extérieure plane et étanche à la pluie qui est fixée derrière la charpente porteuse du bâtiment. Pour les panneaux de façade du Musée du Futur, des pièces séparées n'étaient pas nécessaires pour former les bords de la cassette, mais étaient plutôt usinées dans chaque moule et ainsi intégrées dans chaque panneau composite.
Matériaux, moules et fabrication de panneaux
Même si les 10 000 mètres carrés d'espace de fabrication de composites d'Affan Innovative Structures disposent de 16 machines d'infusion de résine et de huit tables d'infusion de résine à plateau en verre et à base d'acier mesurant 3 mètres sur 20 mètres, elle a choisi d'utiliser du préimprégné. Pourquoi? « Atteindre les performances FR nécessaires nécessite de nombreux additifs, de sorte que la résine devient épaisse et ne coulera pas dans l'infusion », explique Affan. Dans ce cas, l'additif était du trihydrate d'aluminium (ATH, voir « Tenue au feu sans le poids »). Il poursuit :« Ainsi, nous avons travaillé avec Notus Composites [Ras Al Khaimah, Émirats Arabes Unis] pour développer un préimprégné époxy FR. Nous avons principalement utilisé de la fibre de verre mais aussi de la fibre de carbone dans certaines sections où il y avait des problèmes de déflexion. Approuvé par la défense civile de Dubaï, le préimprégné Notus Composites EPFR-609, en combinaison avec le film de surface NE11-FR, a satisfait aux exigences de feu NFPA 285, EN13051-1 et ASTM E1098 et E84 Classe A (voir « Les préimprégnés ignifuges permettent .. . » et « Un criblage meilleur et moins cher des matériaux de construction en PRF »).
Parce que les surfaces métalliques externes à Dubaï peuvent atteindre des températures de 80 °C (176 °F) en été, explique Affan, « nous avons durci le préimprégné à 120 °C pour garantir une Tg suffisante. (température de transition vitreuse) pour résister à la déviation de la tête. Ainsi, les moules ont été usinés dans une mousse de polyuréthane qui pouvait résister à cette température élevée, ce qui est plus coûteux. Nous avons essayé trois ou quatre mousses différentes, mais une seule pouvait résister à la température et à la pression du vide, tout en étant suffisamment souple pour être usiné CNC facilement et rapidement.
L'usinage CNC de chaque moule a pris de 12 à 72 heures et chacun des 1 024 panneaux composites a nécessité son propre moule . Les quatre machines CNC à 5 axes CMS (Zogno, Italie) d'Affan Innovative Structures - la plus grande mesurant 33 mètres de long sur 13 mètres de haut sur 2,5 mètres de haut - étaient nécessaires pour répondre à la cadence de production exigeante du musée. « Si une [machine] était en panne pour maintenance, les autres fonctionnaient en parallèle », explique Affan.
Les plis préimprégnés ont été coupés et assemblés à l'aide d'un (Bulmer, Mehrstetten, Allemagne) découpeuse automatisée. « Nous n'avons pas utilisé d'âme dans les panneaux car, contrairement à aujourd'hui, il n'y avait pas d'âme en mousse à l'époque qui pouvait répondre aux exigences FR », explique Affan. Même avec une telle automatisation, les 250 employés de l'entreprise, un total qu'elle avait atteint en 2015, étaient également nécessaires pour livrer la production, avec une moyenne de quatre panneaux par jour. Des équipes de six ouvriers, chacun avec un superviseur et un ensemble équilibré de compétences pour être efficace, ont disposé les panneaux. "Normalement, nous avions deux ou trois équipes travaillant sur un projet", note Affan, "mais pour respecter ce calendrier de production, nous avions 20 équipes travaillant à un moment donné."
Étapes de fabrication
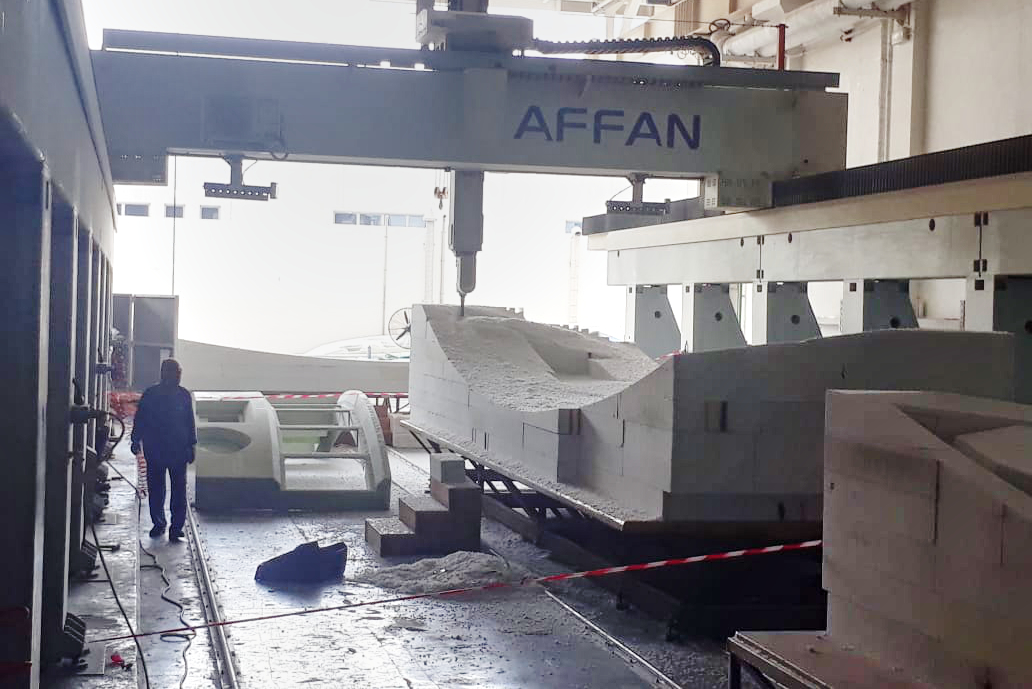
Étape 1La mousse de polyuréthane est broyée dans des moules de précision. Source de toutes les images des étapes de fabrication | Solutions innovantes Affan
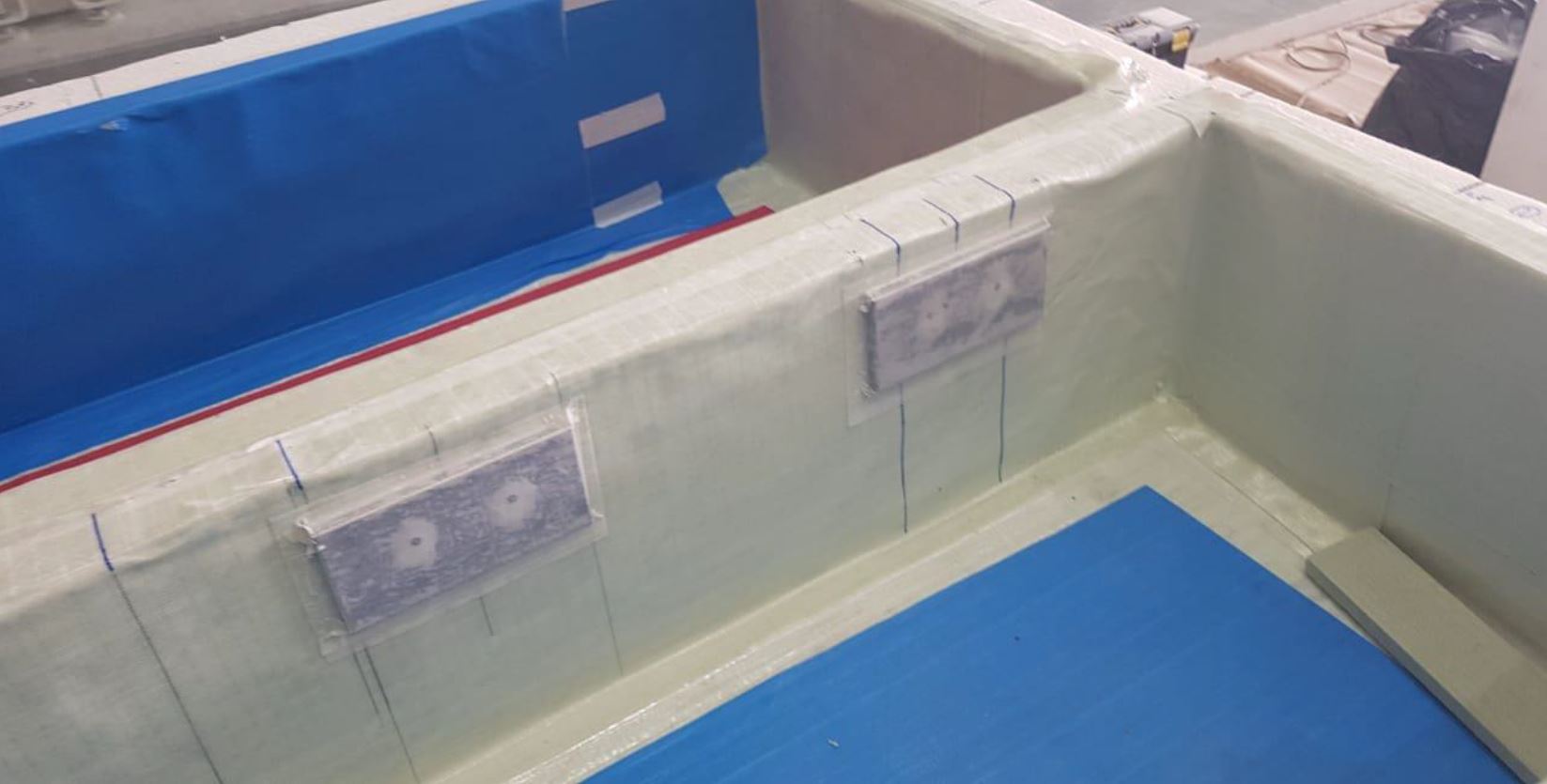
Étape 2Le préimprégné fibre de verre/époxy est déposé à la main dans les moules.
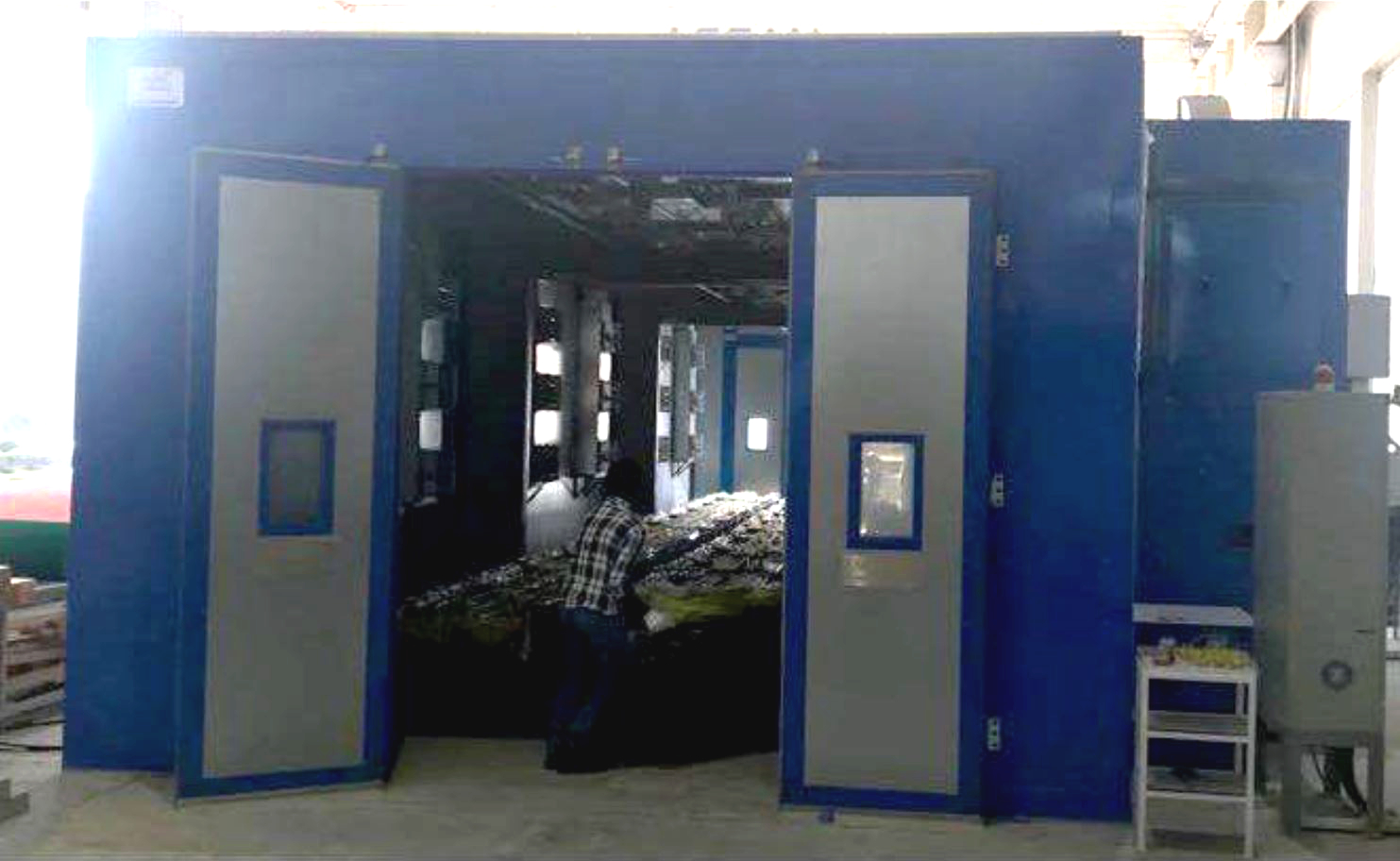
Étape 3Les couches de préimprégné sont emballées sous vide et durcies dans un four pendant 6 heures à 120 °C.
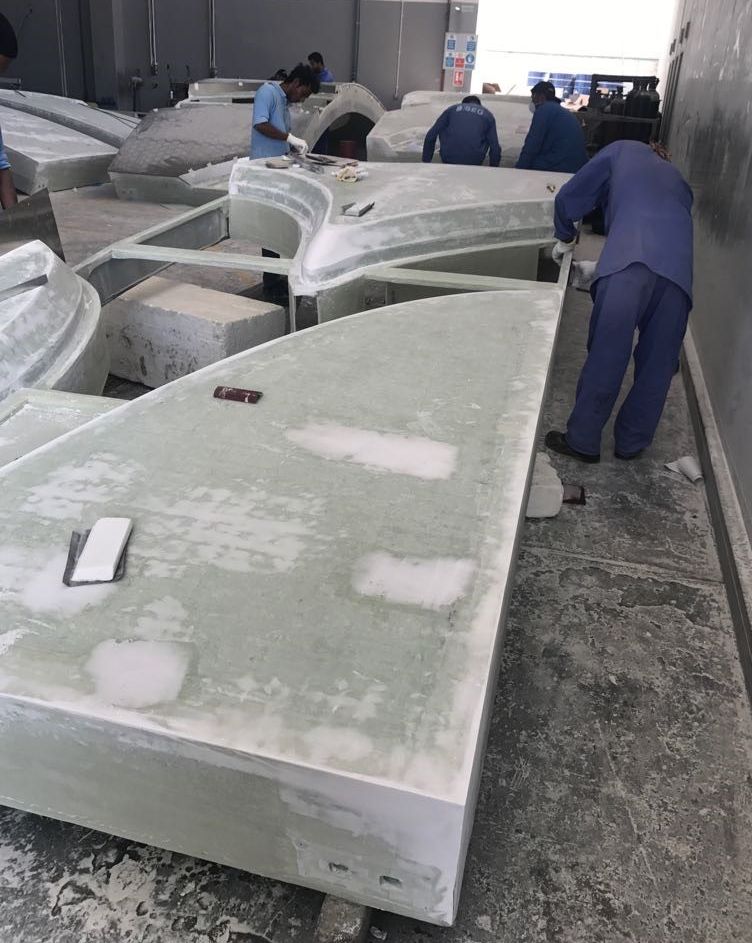
Étape 4Les panneaux démoulés sont préparés pour le collage de la finition en acier inoxydable.
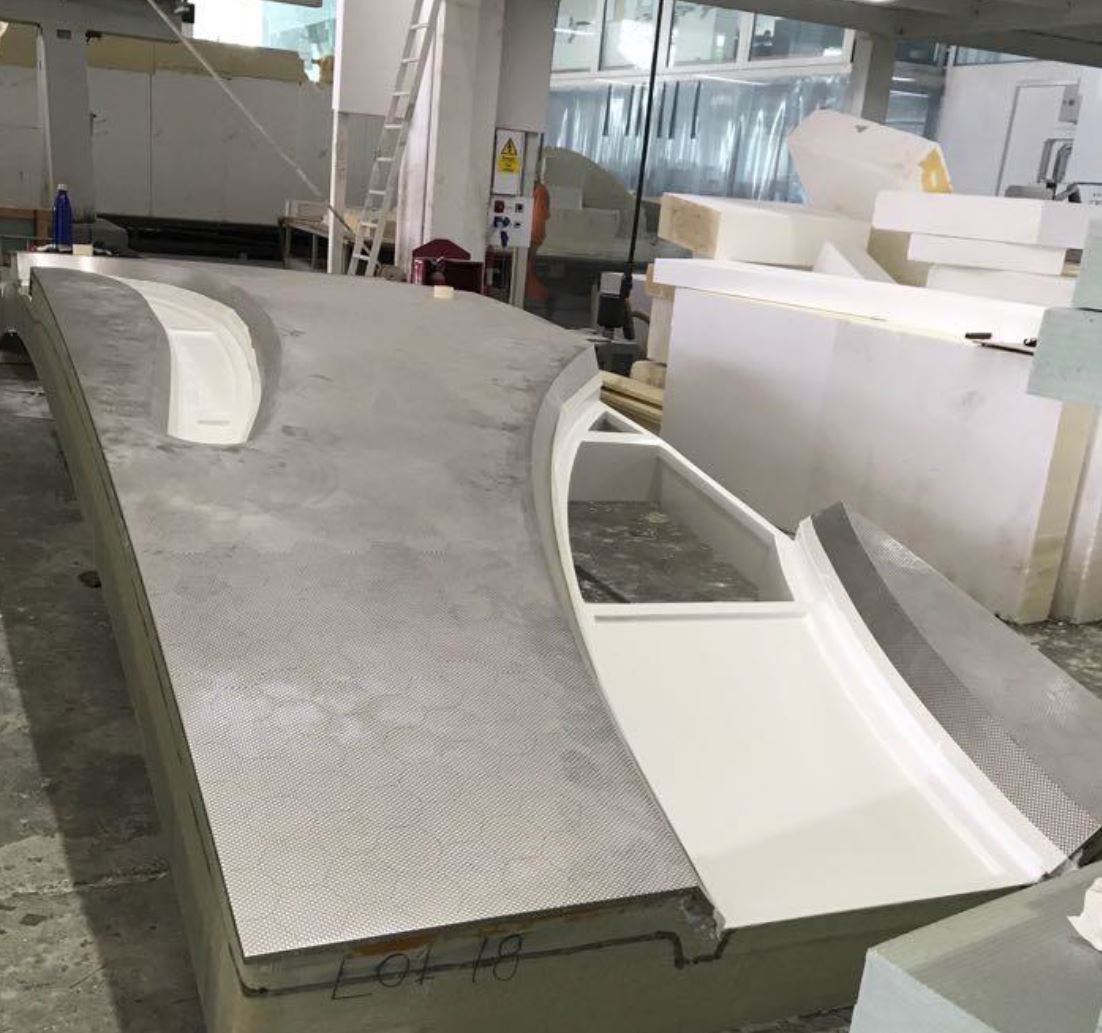
Étape 5Les hexagones en acier inoxydable sont collés et fixés mécaniquement aux panneaux de FRP.
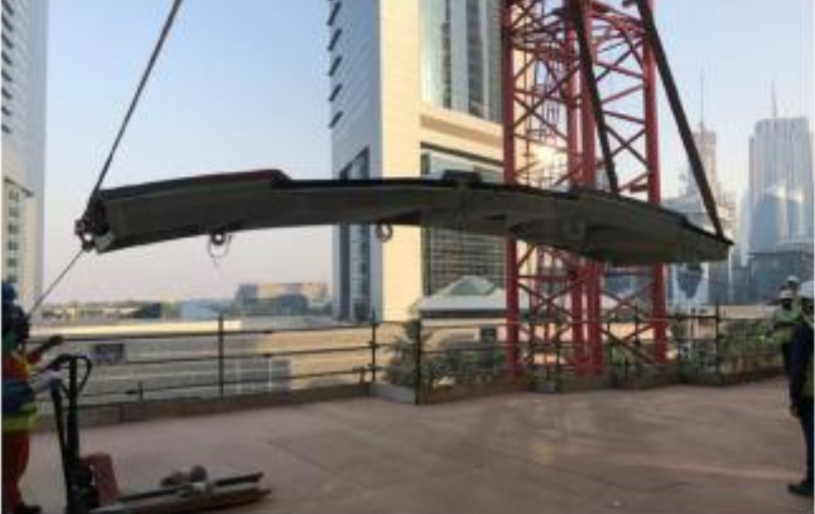
Étape 6Les panneaux finis sont soulevés pour l'installation.
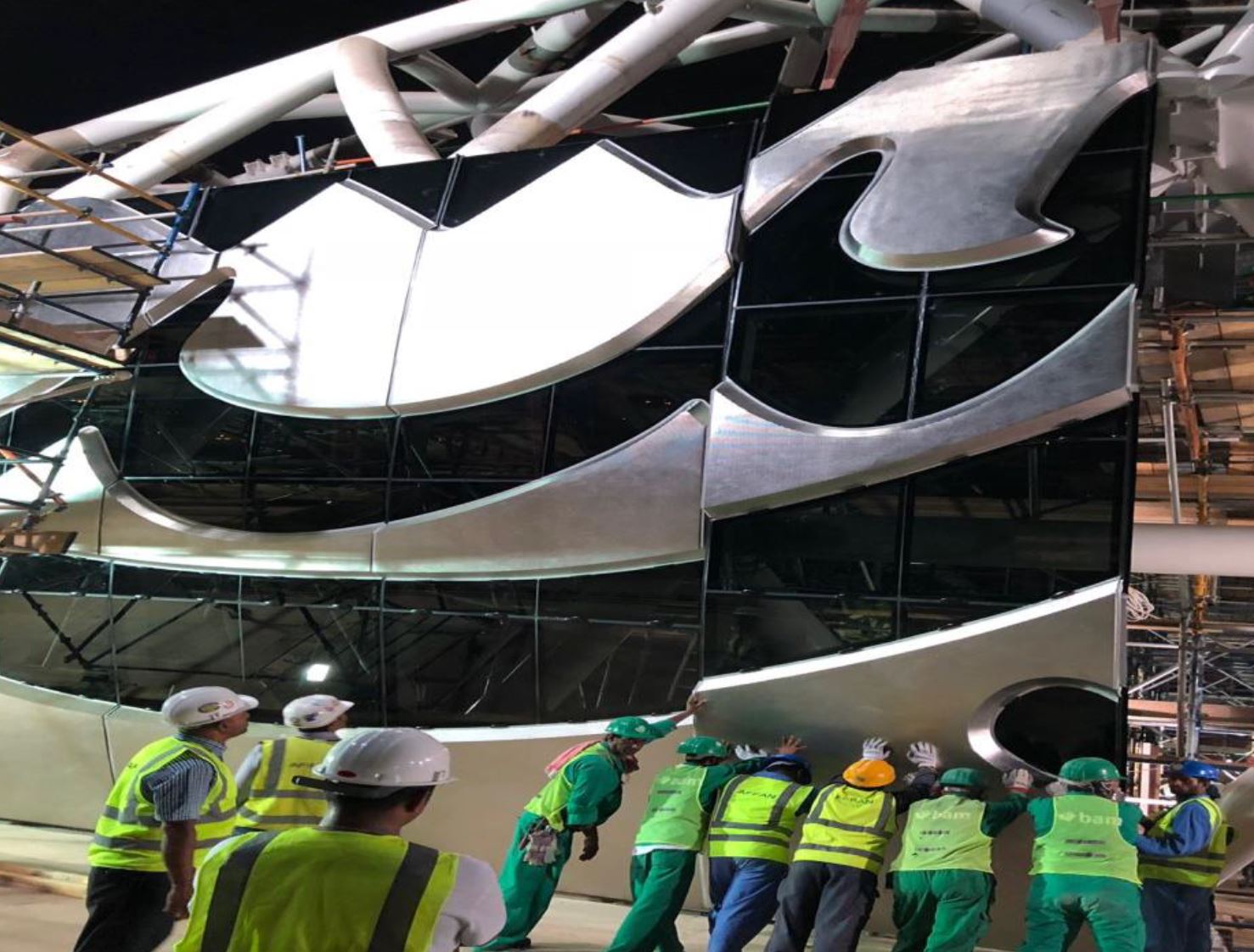
Étape 7Chaque panneau est ajusté via un « joint universel » 3D unique.
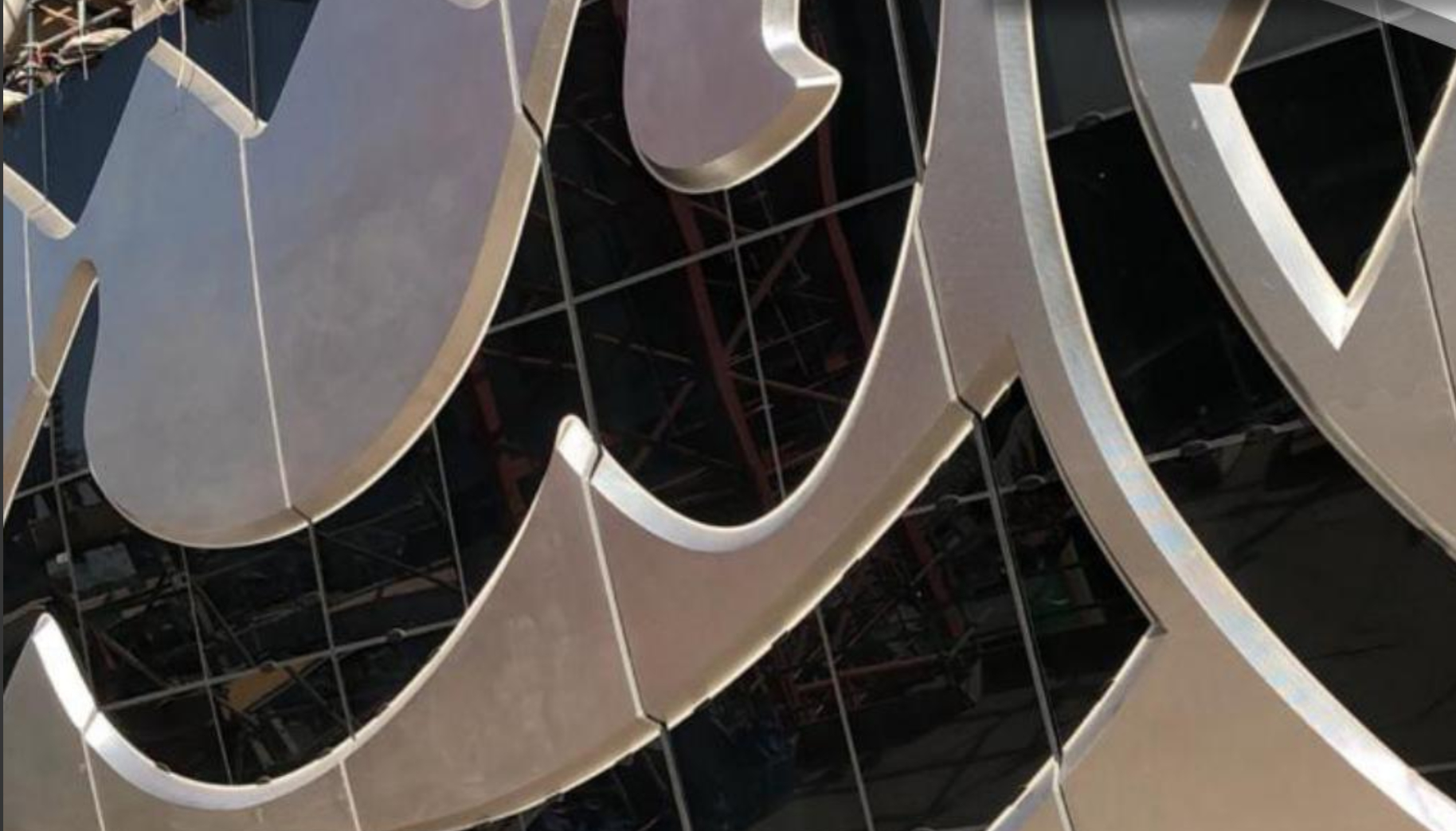
Étape 8 Chaque panneau est ajusté via un « joint universel » 3D unique pour obtenir une façade extérieure parfaitement alignée.
Précédent SuivantLes draps ont été posés à la main, emballés sous vide et durcis pendant 6 heures dans des fours mesurant 20 mètres de long sur 8 mètres de large et 3 mètres de haut. « Chaque machine CNC avait son propre four », explique Affan. « Nous n'avons pas groupé beaucoup de panneaux par cycle de durcissement. Au lieu de cela, lorsque chaque panneau était prêt, nous l'avons immédiatement durci pour maintenir un flux de production aussi élevé que possible. Nous avons ensuite démoulé les panneaux et utilisé un scanner 3D pour nous assurer que le panneau tel que fabriqué correspondait au fichier CATIA. Conformément à notre système de contrôle qualité total, nous avons dû vérifier les fichiers numériques à chaque étape du processus. »
Les panneaux finis ont ensuite reçu la finition extérieure en acier inoxydable. « L'acier inoxydable est collé à chaque panneau, puis fixé avec des attaches mécaniques, ce qui est un art en soi », explique Affan. « Le métal a été découpé en petits hexagones afin de recouvrir les panneaux 3D. La grille hexagonale variait d'une partie à l'autre en fonction de la quantité de courbure. Même si nous avons de l'expérience et de la confiance dans le collage, il ne pourrait y avoir aucun risque qu'un seul hexagone se désagrège pendant la durée de vie du bâtiment. Ainsi, chaque hexagone devait être attaché - nécessitant jusqu'à 200 à 300 pièces jointes pour un seul panneau. Les panneaux finis ont ensuite été envoyés sur le site pour être installés.
Installation sans problème avec l'aide de la NASA
L'installation a en fait été réalisée par l'entreprise de construction du bâtiment BAM International (Gouda, Pays-Bas). «Nous n'avons fourni que des superviseurs pour l'installation pour aider à la manipulation des panneaux», note Affan. «La façon dont chacun est soulevé est la clé. Les panneaux ont été conçus pour être suffisamment solides pour la position spécifique de chacun dans le bâtiment. Cependant, ils doivent être soulevés d'une manière spécifique, via au moins deux points de levage, tout comme les cassettes suspendues dans les méthodes de construction plus traditionnelles. »
Il y avait un problème supplémentaire qu'Affan était particulièrement qualifié pour résoudre. « Pour que chaque panneau repose sur la structure en acier tout en formant la surface lisse, nous avions besoin de pouvoir ajuster le panneau en profondeur, en orientation et en courbure en 3D - en d'autres termes, une sorte de joint universel avec trois degrés de liberté . En 1985, j'ai travaillé comme étudiant à la NASA en Californie sur l'amortissement des structures de stations spatiales. La clé était de pouvoir déplacer chaque structure et de l'ajuster lorsque la navette accoste afin que les vibrations soient amorties rapidement, un peu comme la suppression du bruit. J'ai utilisé la même technologie pour la fixation et le réglage du panneau lors de l'installation. »
De plus, comme les panneaux assuraient également l'étanchéité du bâtiment, il ne pouvait y avoir d'espace entre eux. « Les panneaux ne pouvaient pas aboutir directement, ou ils pouvaient se fissurer », explique Affan, expliquant qu'en raison d'une charge vive élevée de 1,5 tonne sur le 6 ème en porte-à-faux. zone d'exposition au sol, la structure en acier bouge réellement. « Nous avons maintenu un espacement espacé avec précision entre les panneaux et celui-ci a été rempli avec un joint spécial. » Ce joint, suffisamment souple pour se dilater, mais suffisamment rigide pour résister à la charge, offrait une fonctionnalité d'étanchéité tout en permettant l'aspect esthétique du bâtiment.
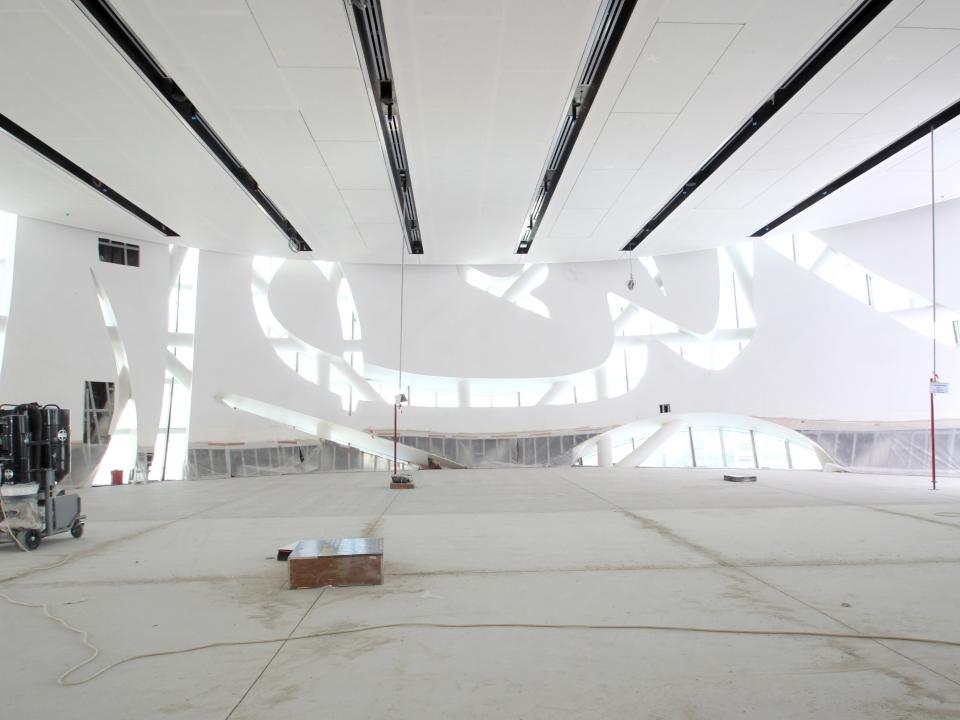
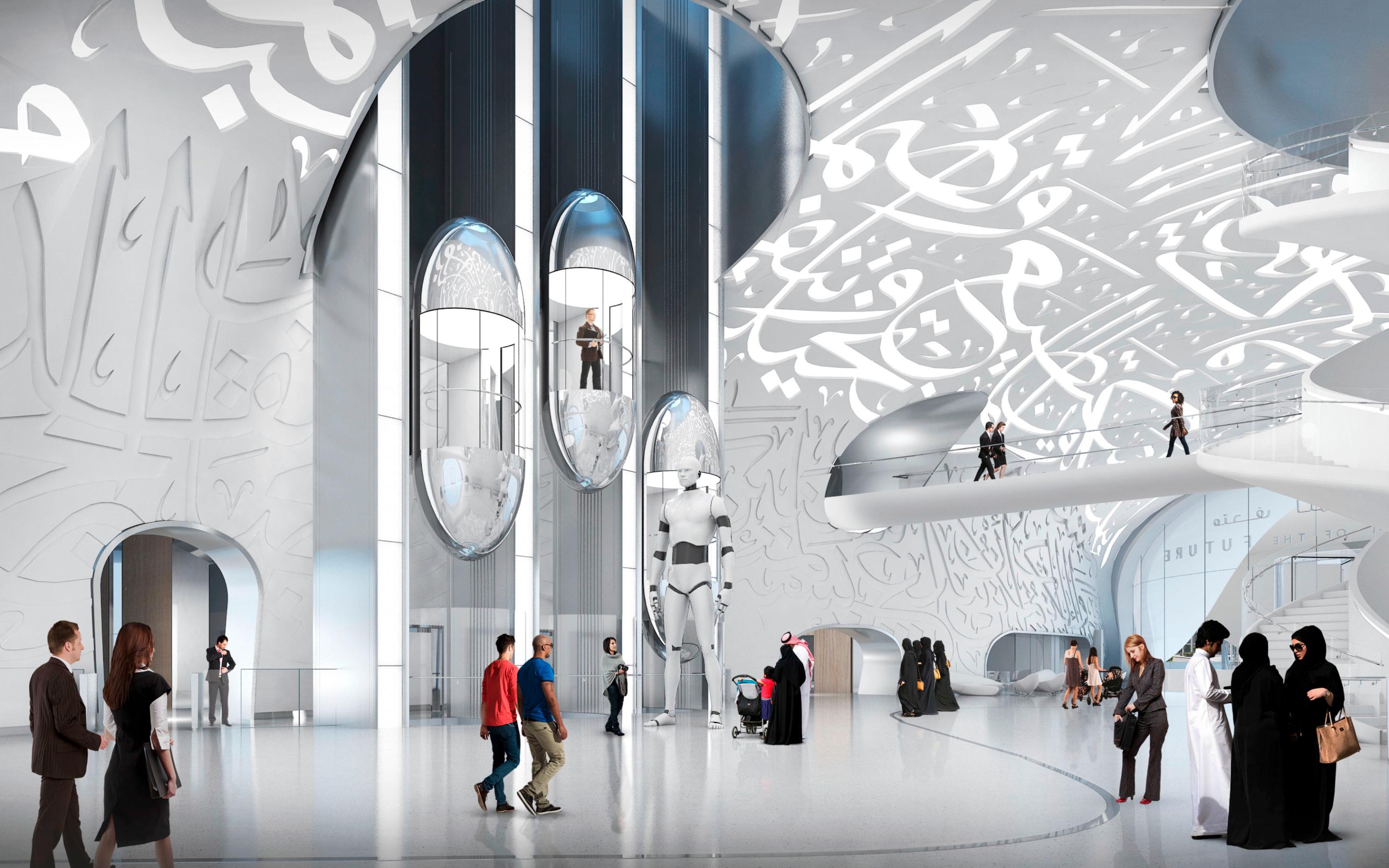
De telles solutions sont un avantage, note Affan. « Parce que nous venons du milieu des structures, nous sommes capables de combiner de nombreux matériaux. C'est très important. Les composites ne sont qu'un des matériaux que nous utilisons. Ce n'était pas seulement un projet composite. Les résultats parlent d'eux-mêmes. « L'installation s'est bien passée; il n'y a eu aucun problème », explique Affan, qui note qu'il n'y avait aucun moyen de vérifier si le panneau conviendrait, sauf pour s'assurer de sa conformité avec le fichier numérique. « Nous n'avons pas encore eu de panneau qui n'a pas été adapté ou qui n'a pas la bonne forme ou le mot mal orthographié », a déclaré Bauly, chef de projet de Buro Happold, dans un article de la BBC par Elizabeth Bains.
Futur construction modulaire
« Nous avons géré l'ensemble du processus ensemble », ajoute Affan. « Le travail d'équipe au sein même de notre entreprise était également essentiel ; les groupes de conception et de layup devaient se coordonner les uns avec les autres. Nous n'avons jamais fait un travail aussi important, et c'était un défi, mais nous aimons les défis. »
Malheureusement, COVID-19 a fait des ravages. «Nous avons terminé ce travail juste avant le verrouillage de la pandémie», dit-il. « Maintenant, nous ne sommes plus qu’à moins de 30 personnes. C'est dévastateur. Mais cela a affecté tout le monde, pas seulement nous. Et pourtant, Affan voit de l'espoir pour l'avenir et pour le rôle que les composites joueront dans la réalisation de la durabilité et de l'innovation dont le monde a besoin dans la construction. « Surtout à Dubaï et au GCC (Gulf Cooperation Council), les gens veulent essayer de nouvelles idées. C'est la démonstration de l'avenir de l'architecture et de la construction. »
Cet avenir, souligne-t-il, sera pour ceux qui peuvent utiliser des systèmes de construction modulaires, « et COVID-19 accélère en fait cela. Les entreprises intégreront des modules et les enverront sur le site. Cela se développera car il déplace les inefficacités hors site et dans une usine, augmentant le contrôle et la qualité. Sur place, il faut coordonner l'ensemble des personnes. Cela fait perdre du temps à attendre d'autres sous-traitants. Vous êtes également dépendant de la météo et des arrêts de travail. La fabrication en usine élimine tout cela. Parce qu'ils sont suffisamment solides, légers et durables pour être transportés et installés facilement, les composites permettent ce type de construction modulaire et vous pouvez créer toutes les formes que vous voulez. »
Affan note que la construction modulaire est utilisée dans les navires de croisière depuis des années, où chaque cabine est préfabriquée, équipée de systèmes de chauffage/climatisation, d'électricité et de plomberie, puis assemblée dans la charpente en acier du navire comme des blocs LEGO. « Imaginez combien de temps vous gagnerez lorsque chaque module est déjà équipé. Nous étudions actuellement un projet de construction d'un immeuble de grande hauteur de cette manière en utilisant des composites », dit-il. « Si vous avez des résines FR, vous n'avez pas besoin des pièces qui étaient auparavant en métal. » Citant un hôtel Marriott construit de cette façon et achevé l'année dernière à New York, Affan ajoute :« ce bâtiment était en acier et en bois, mais nous pouvons le construire en composites ».
Résine
- La sécurité cloud est l'avenir de la cybersécurité
- L'avenir du logiciel de tranchage
- Edge computing :L'architecture du futur
- Visualiser l'avenir de la maintenance des usines
- L'avenir des centres de données
- Construire de meilleures chaînes d'approvisionnement pour l'avenir
- L'automatisation intelligente des bâtiments et l'avenir du développement immobilier dans les villes
- Construire l'avenir de l'expérience employé avec l'automatisation intelligente
- Comment Tech Mahindra construit l'usine du futur