Rubans thermoplastiques multicouches, AFP et infusion de résine pour des composites plus démocratiques
Novotech (Naples, Italie) a débuté en tant que spin-off de l'Université de Naples « Federico II » dans le sud de l'Italie, fondée par le professeur Leonardo Lecce en 1992. « Nous avons soutenu des entreprises d'aviation générale et fourni des services de R&D dans toute l'Italie », explique Lecce qui est maintenant le PDG de Novotech. "Nous avons fourni des analyses structurelles pour des pièces d'avions et avons également aidé au développement d'avions."
Située à proximité de l'usine Leonardo qui fabrique les sections de fuselage composites du Boeing 787, Novotech a commencé à se concentrer sur les composites en 2014. Elle a acheté une cellule de placement automatisé de fibres (AFP) à Coriolis Composites (Queven, France) et développée à partir d'autoclave ( OOA), y compris l'infusion de résine et la fabrication de composites thermoplastiques, avec une expertise particulière dans la consolidation in-situ à l'aide de l'AFP.
Novotech a participé à de nombreux projets de recherche de l'industrie, notamment :
- MESEMA (Systèmes énergétiques magnétoélastiques pour des avions encore plus électriques)
- SARISTU (Structures d'avions intelligents intelligents)
- ASAM (Simulation avancée des mécanismes d'avion)
- LAMITECH (Méthodes de test innovantes pour la stratification automatique de matériaux composites hybrides)
- PROALATECH (Caractérisation structurelle et analyse des solutions de réparation des empennages CFRP innovants)
- VISAGE (Environnement de cabine d'avion convivial)
- AIRGREEN 2 - CLEAN SKY 2 (Développement de concepts et de méthodologies d'ailes innovantes pour les avions régionaux de prochaine génération)
- SISTER CHECK (Enquête et intégration d'un système innovant d'inspection non destructive AFP)
- TRINITI - CLEAN SKY 2 (Réservoirs d'azote haute pression thermoplastiques multi-matériaux pour aéronefs)
- NHYTE - H2020 (Nouvelles aérostructures composites thermoplastiques hybrides fabriquées par OOA)
« Nous entretenons également une relation spéciale avec Cytec au Royaume-Uni, en développant de nouveaux matériaux et procédés composites », déclare Lecce. Notez que Cytec a été acquise par Solvay et que l'emplacement référencé est Solvay Composite Materials à Heanor, Royaume-Uni - un site avec une longue histoire d'innovation, y compris le processus de formation de double diaphragme récemment testé via le programme RAPM. « Notre dernière activité de ce type consistait à développer un procédé thermoplastique OOA qui utilise une nouvelle presse innovante qui combine PEEK (polyétheréthercétone) et PEI (polyétherimide) dans un nouveau matériau composite. Ce nouveau matériau, équipement et procédé a maintenant été démontré dans un longeron d'avion en plastique renforcé de fibres de carbone (PRFC), fabriqué à l'aide de la consolidation et du soudage in situ AFP via le projet NHYTE.
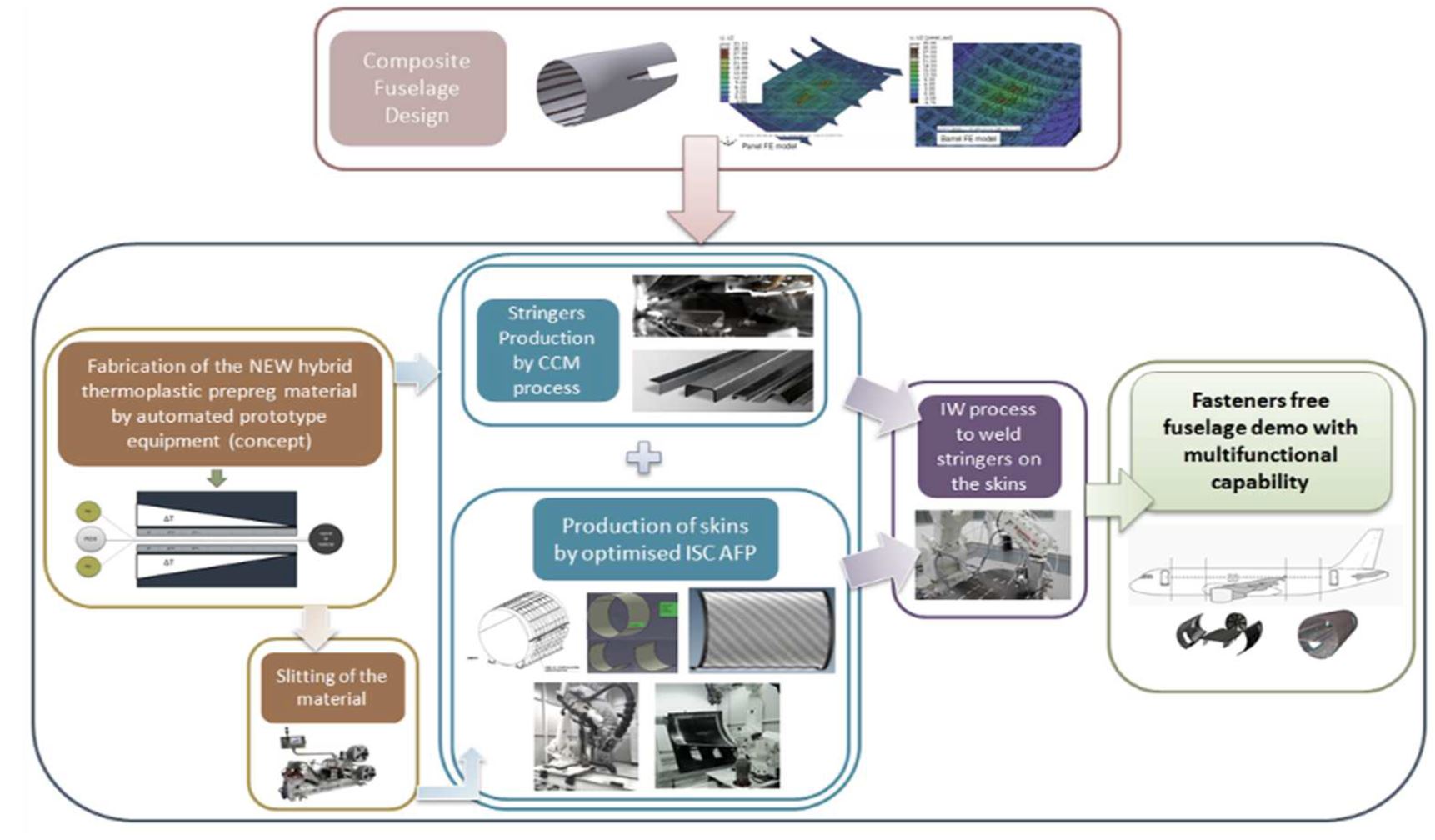
NHYTE
Financé par le programme Horizon 2020 de la Commission européenne, NHYTE est un projet de recherche mené de mai 2017 à octobre 2020. « NHYTE consiste à utiliser une liaison amorphe pour permettre des conditions de température et de traitement durables pour les composites thermoplastiques », explique le Dr Marco Barile, coordinateur du projet NHYTE. et CTO de Novotech. Ce collage amorphe (voir schéma ci-dessous) est un concept breveté par un autre partenaire de NHYTE, la division aérostructures de Leonardo (Rome, Italie) qui dispose de plusieurs sites de production dans le sud de l'Italie.
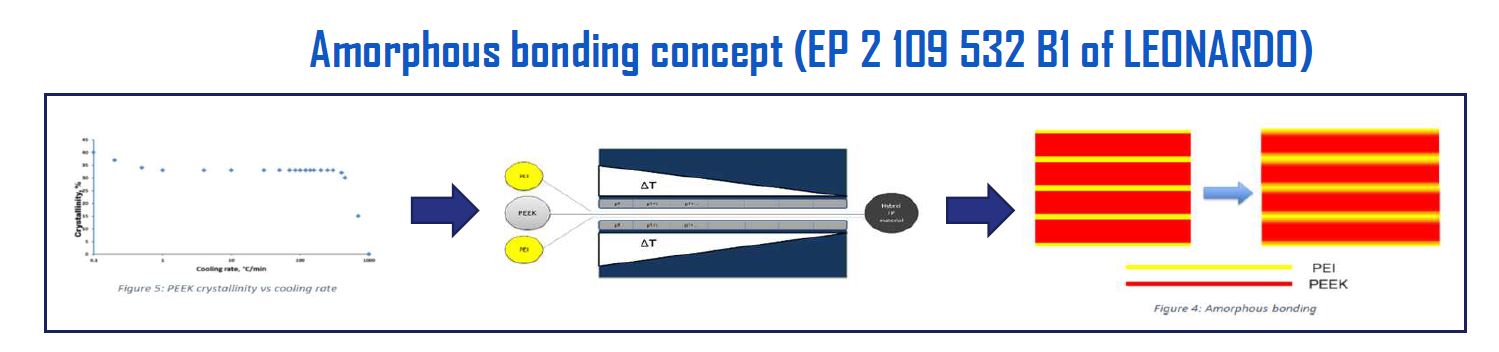
Crédit photo :projet NHYTE
« Avec le matériau développé dans NHYTE, nous pouvons surmonter les limitations actuelles des matériaux avec la consolidation in-situ AFP (ISC) des composites thermoplastiques (TPC). Au lieu de traiter à des températures légèrement inférieures à 400 degrés C pour les polymères semi-cristallins PEEK, nous pouvons chauffer juste au-dessus de la température de transition vitreuse (Tg) de 215 degrés pour la couche amorphe de PEI. La fusion et le refroidissement du PEI sont également plus rapides, n'ayant pas besoin d'être aussi contrôlés que le PEEK. » Barile note que ce concept peut utiliser d'autres thermoplastiques amorphes. Le PEI a été choisi car il adhère bien au PEEK, un matériau éprouvé dans plusieurs démonstrateurs d'aérostructure AFP.
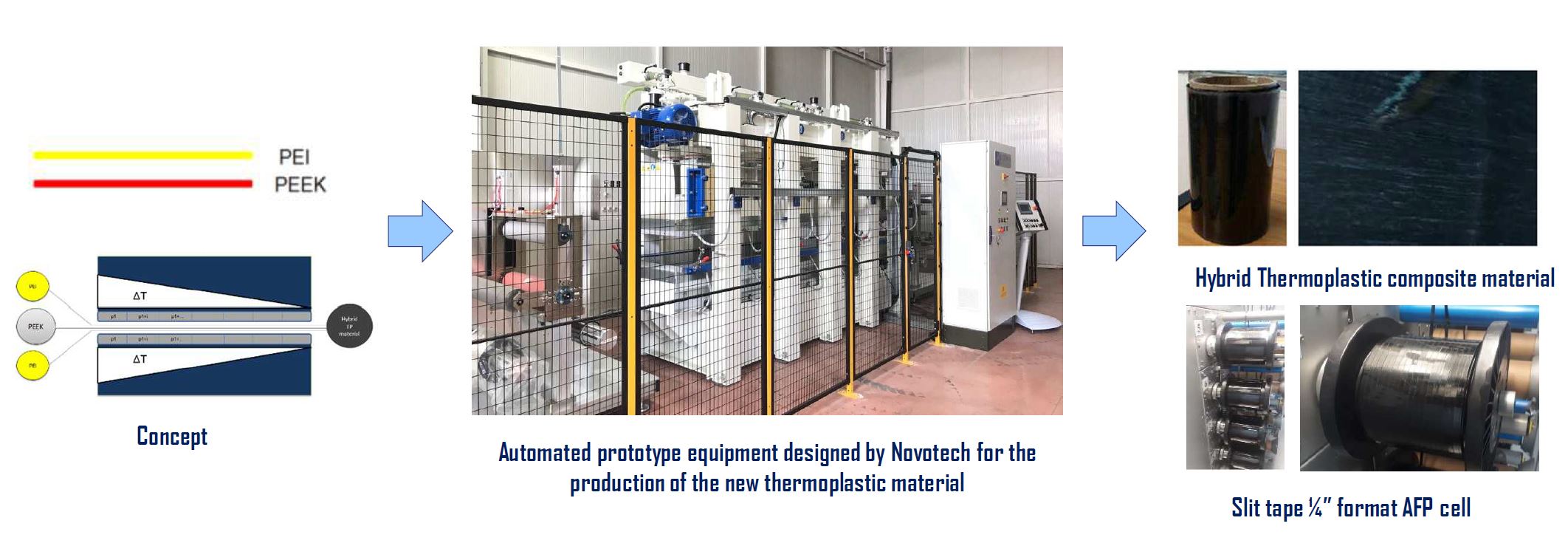
Ce nouveau matériau développé à NHYTE a été produit dans une presse continue conçue par NOVOTECH. Orma Macchine (Bergame, Italie) a fourni le corps de la presse et COMEC Innovative (Chieti, Italie) a fourni les modules d'enroulement et de déroulement. "Cette presse peut fabriquer un rouleau continu de matériau que nous découpons ensuite en ruban refendu pour une utilisation dans une machine AFP", explique Barile. Trois matériaux différents entrent dans la presse par la gauche, comme le montre l'image ci-dessus. "Nous avons PEI en haut et en bas, puis PEEK au milieu", explique Barile.
En tant que polymère semi-cristallin, le PEEK offre les propriétés mécaniques élevées nécessaires aux structures primaires, tandis que les couches amorphes de PEI offrent une fusion rapide et simple pour le collage. « Nous contrôlons la pression et le refroidissement du matériau le long des plaques de presse, à partir d'environ 400 degrés C au début de la presse à moins de 200 degrés C à la fin de la presse. Le résultat est un matériau qui est une combinaison des trois couches d'entrée. »
Ce nouveau type de ruban thermoplastique est déjà consolidé lors de la fabrication, de sorte qu'au cours de l'AFP, il suffit de le chauffer pour fondre et compacter les couches de PEI pour le collage amorphe. Le résultat est un stratifié comprenant un ruban PEEK à PEI entièrement consolidé et des couches PEI à PEI, comme le montre le brevet Leonardo. Ce processus AFP présente moins d'obstacles par rapport à l'AFP ISC actuelle utilisant des bandes PEEK et PEKK (polyétheréthercétone). Comme expliqué dans la partie 2 de mon article de 2018 sur la consolidation in situ, l'AFP ISC actuelle nécessite de chauffer le ruban et le substrat à la température de fusion, de placer le ruban sur le substrat, puis de consolider avec un rouleau afin que le processus de refroidissement soit contrôlé avec précision, permettant les polymères semi-cristallins pour obtenir une cristallinité suffisamment élevée (30-40 %) et de faibles vides (<3-5%) pour les propriétés structurelles.
Les critiques de l'AFP ISC prétendent qu'il est trop lent - un taux de dépôt de 60-100 mm/s contre 600-700 mm/s pour la méthode "en deux étapes" comprenant un dépôt rapide de l'AFP suivi d'une étape secondaire dans un four ou un autoclave pour complètement consolider/recuire la contrainte thermique dans le stratifié. "Avec notre matériau, vous pouvez atteindre des taux de dépôt AFP qui ne sont pas aussi lents que la consolidation in situ typique et le chauffage requis pendant l'AFP peut également être maintenu en dessous de 300 degrés C", explique Barile. « Vous pouvez combler l'écart de performance avec les matériaux standard que nous avons maintenant. » Ici, Barile compare AFP ISC des composites thermoplastiques aux composites thermodurcissables utilisés dans les avions Boeing 787 et Airbus A350. « Avec des composants volumineux tels que des sections de fuselage, le problème réside dans l'abordabilité lors de l'utilisation d'un durcissement à l'autoclave. Les thermoplastiques permettent un processus de production plus abordable, mais vous avez des températures élevées et des taux d'AFP lents avec les matériaux de qualité aérospatiale actuellement disponibles sur le marché. Notre approche permet de résoudre ces problèmes. Nous pouvons atteindre environ 30 pour cent de cristallinité dans la bande via la presse continue. Ainsi, vous avez cette cristallinité dans la pièce et vous ne travaillez qu'avec la couche amorphe pendant l'AFP. Bien qu'il s'agisse encore d'un matériau expérimental, qui peut être amélioré, l'objectif du projet NHYTE est d'avoir un processus de fabrication en une étape que vous pouvez utiliser dans des applications aérospatiales structurelles. »
Optimisation de la bande et de l'AFP
« Les premiers matériaux de bande multicouche ont été fabriqués ici à Novotech », explique Barile. Ces rubans utilisaient un film fendu non chargé Sabic (Riyad, Arabie saoudite) Ultem 1000 pour le ruban PEEK renforcé de fibres de carbone PEI et APC-2/AS4 de Solvay. L'épaisseur totale était d'environ 0,26 mm, comprenant des couches de PEI d'une épaisseur de 1 ou 2 mils (0,001 ou 0,002 pouce). Dans la première phase du projet, plusieurs coupons des deux variantes ont été testés pour la résistance au cisaillement interlaminaire (ILSS) afin de valider le processus de fabrication de matériau thermoplastique hybride. De petits coupons ont également été testés par le partenaire NHYTE Applus Laboratories (Barcelone, Espagne) pour une gamme complète de propriétés mécaniques, y compris la résistance et le module de traction et de compression, la compression à trou ouvert (OHC), la tension du trou rempli, la compression après impact (CAI), à peine visible dommages par impact (BVID) et propriétés après conditionnement du fluide.
« Nous n'avions pas la même expérience que les fournisseurs de rubans composites thermoplastiques, la qualité du matériau peut donc être améliorée. Par exemple, le volume des fibres varie de faible à élevé selon l'épaisseur, ce qui affecte les propriétés du ruban et du stratifié, y compris l'ILSS. Mais NHYTE visait à démontrer le concept, ce que nous avons fait. »
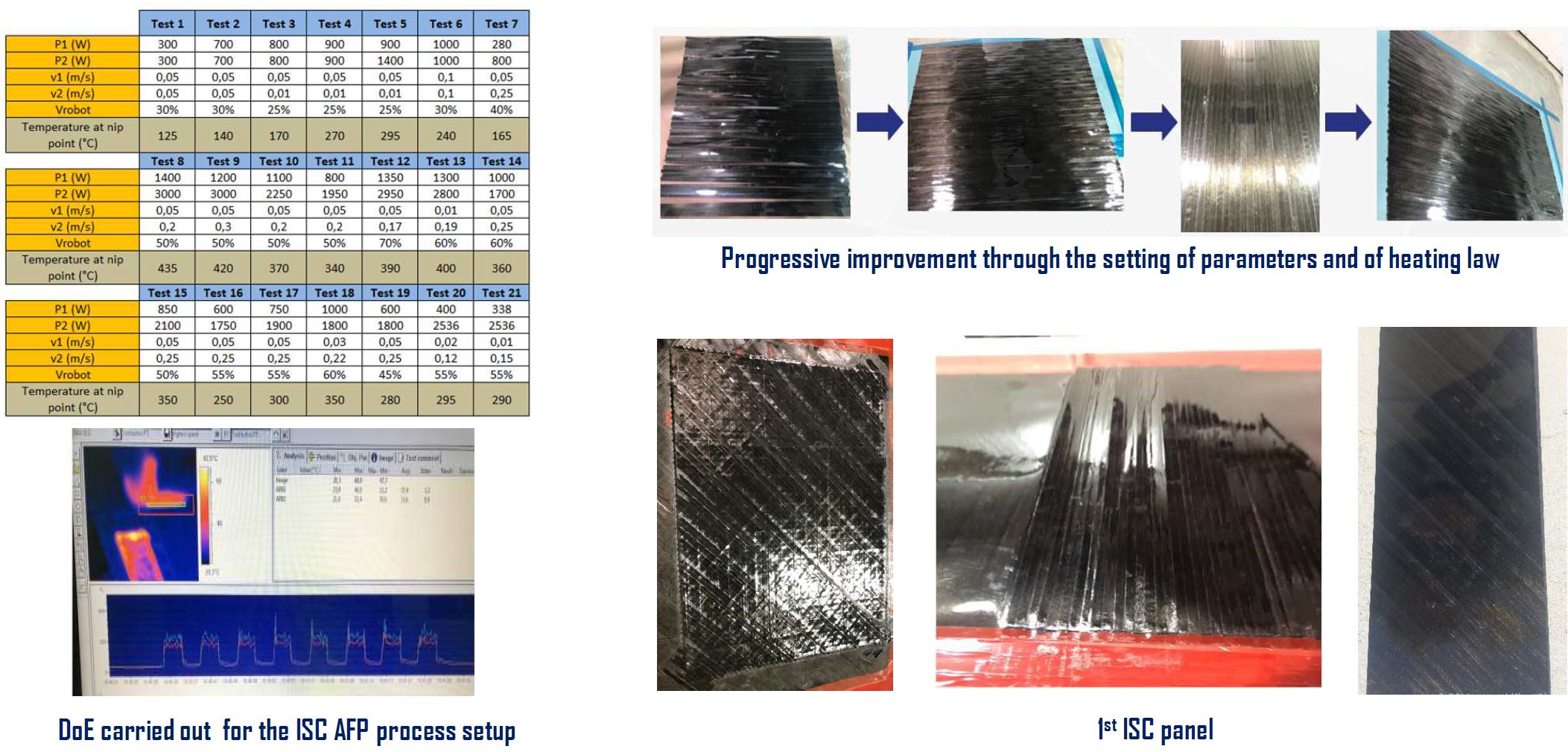
Comme le montrent les images ci-dessus, l'optimisation du processus AFP pour le nouveau matériau a nécessité un travail expérimental important. "Nous avons également utilisé une approche de plan d'expériences (DOE) pour optimiser les paramètres de l'AFP et un outil a été développé par le partenaire NHYTE de l'Université de Bretagne Sud (USB, Lorient, France) pour améliorer la charge de chauffage du laser via une simulation numérique prédictive." note Barile.
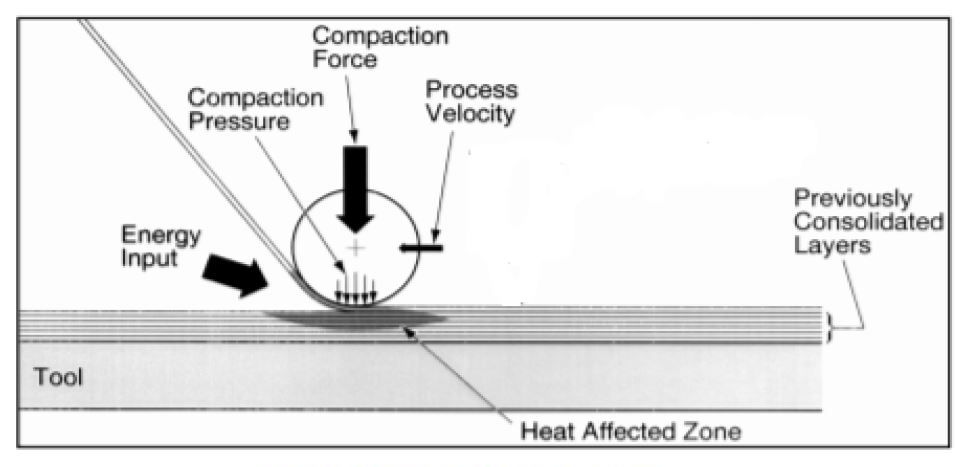
Cette simulation a d'abord été utilisée sur la bande APC-2 pour vérifier la qualité de l'outil prédictif, puis elle a été appliquée au nouveau matériau multicouche. Un article sur ce travail a été soumis pour publication dans la revue Composite Structures . « Vous modélisez les conductivités thermiques au point de pincement », explique Barile. « Nous vérifions ensuite expérimentalement ce qui a été prédit dans la simulation numérique. Ceci est nécessaire pour déterminer le meilleur compromis entre la vitesse de dépôt, la fluidité à chaud des polymères et le vieillissement [cuisson] de la feuille composite. C'est un équilibre de plusieurs variables au cours du processus de consolidation in situ. On regarde la baisse de température du ruban entrant sur le ruban déjà posé sur l'outil. Si vous pouvez gérer ce changement de température, vous pouvez réduire la contrainte résiduelle dans le stratifié. Nous avons donc travaillé à évaluer la variation de température lors de la pose. Vous devez personnaliser le chauffage en fonction de la forme du chemin et de l'orientation de la lame.
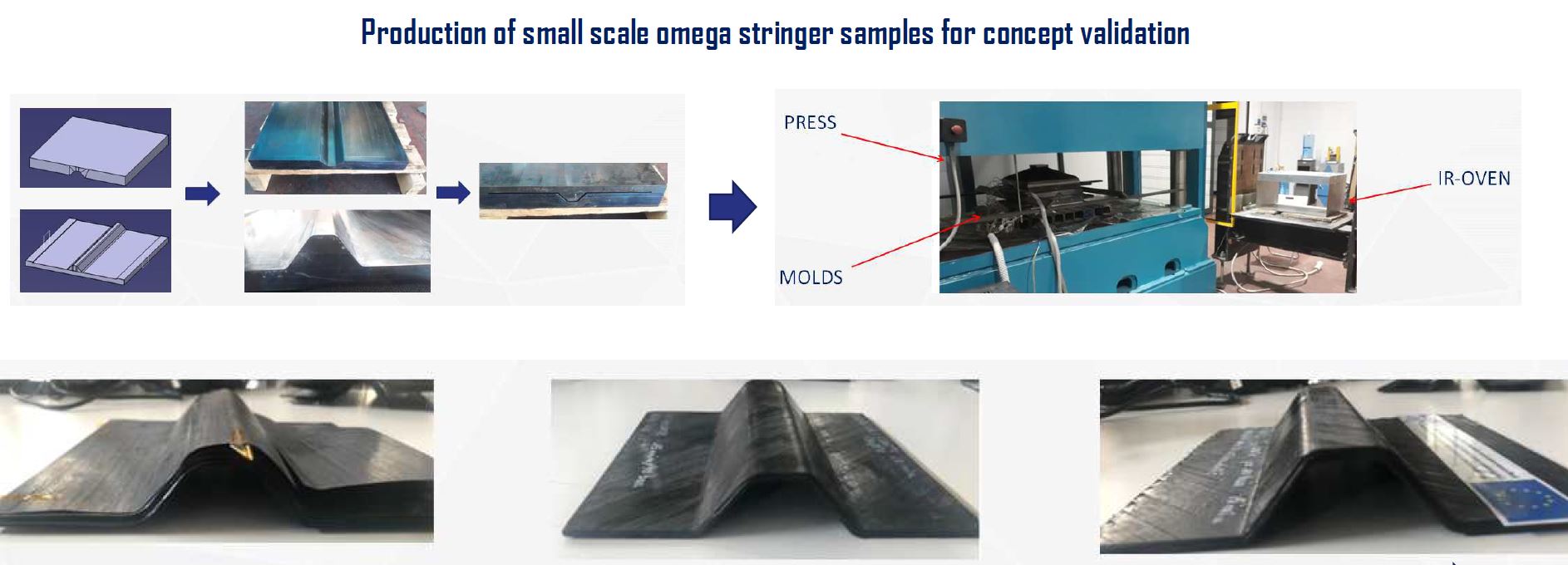
Démonstrateurs de longerons et de fuselage
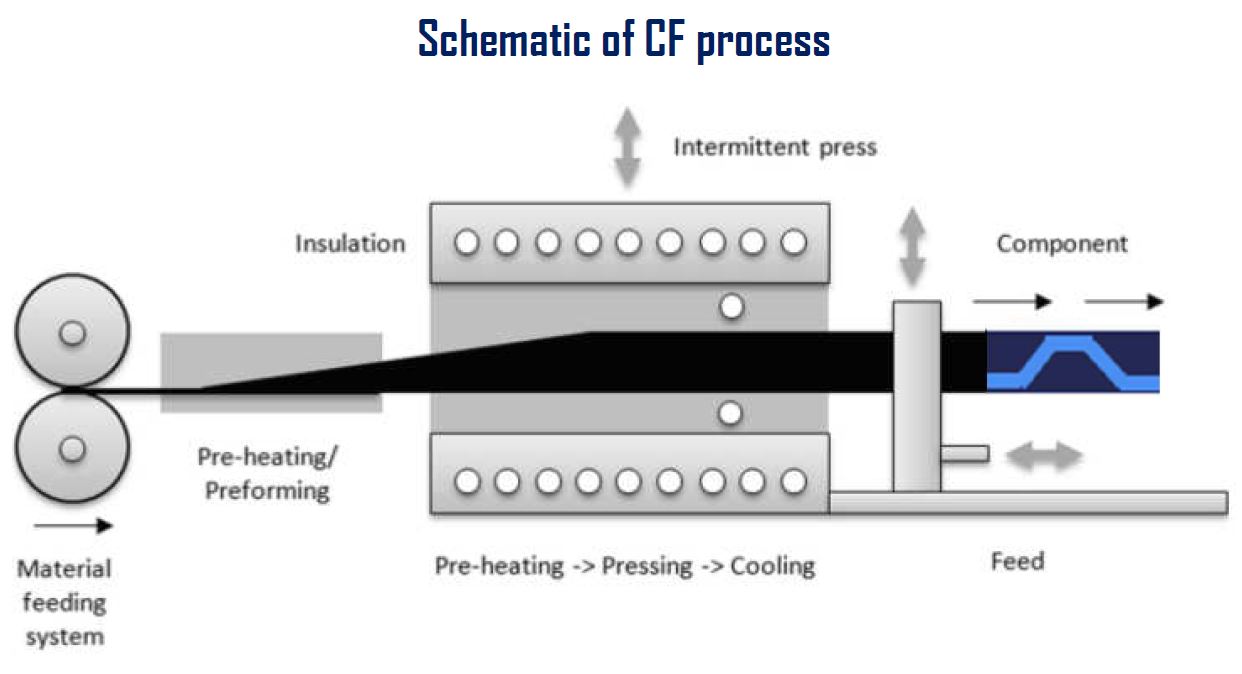
L'étape suivante consistait à produire des démonstrateurs de longerons, d'abord sous forme d'échantillons à petite échelle réalisés avec une presse fixe, puis en tant que démonstrateurs d'un processus de formation de longerons en continu pour vérifier ce qui serait requis pour la production de pièces industrielles. Ces longerons ont ensuite été fixés à un démonstrateur de panneau de peau de fuselage AFP par soudage par induction développé par l'organisme de R&D CETMA (Brindisi, Italie).
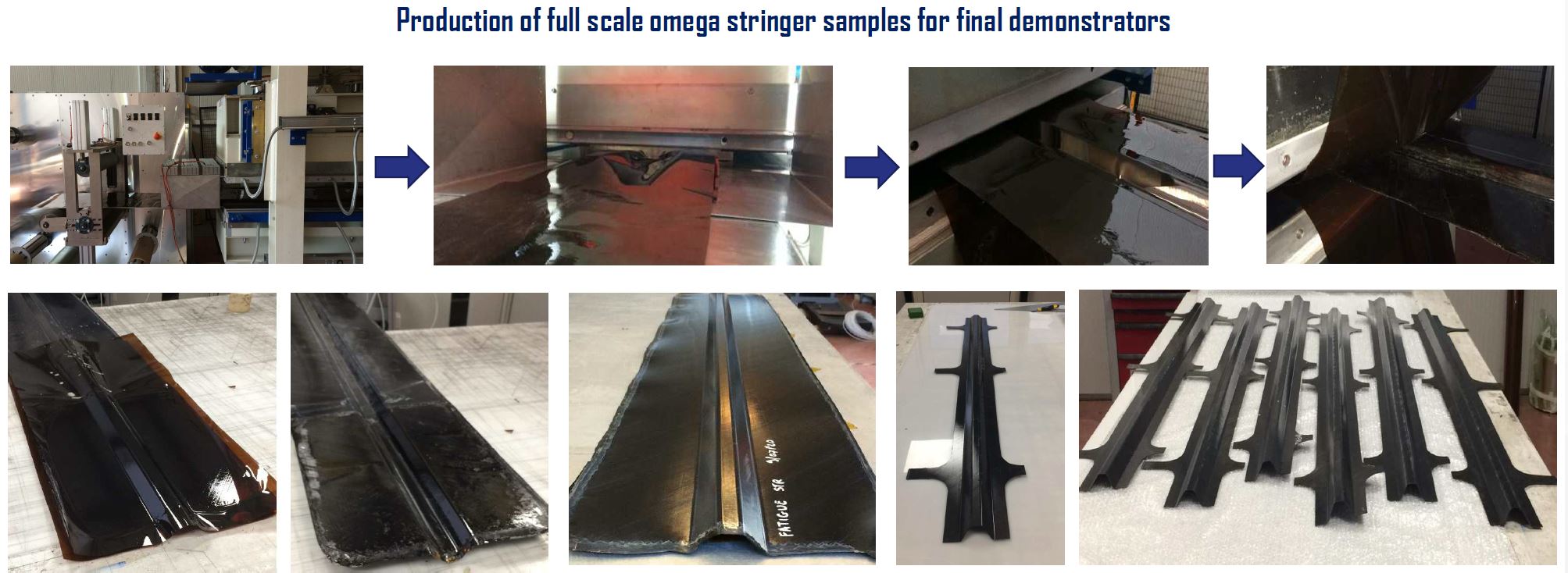
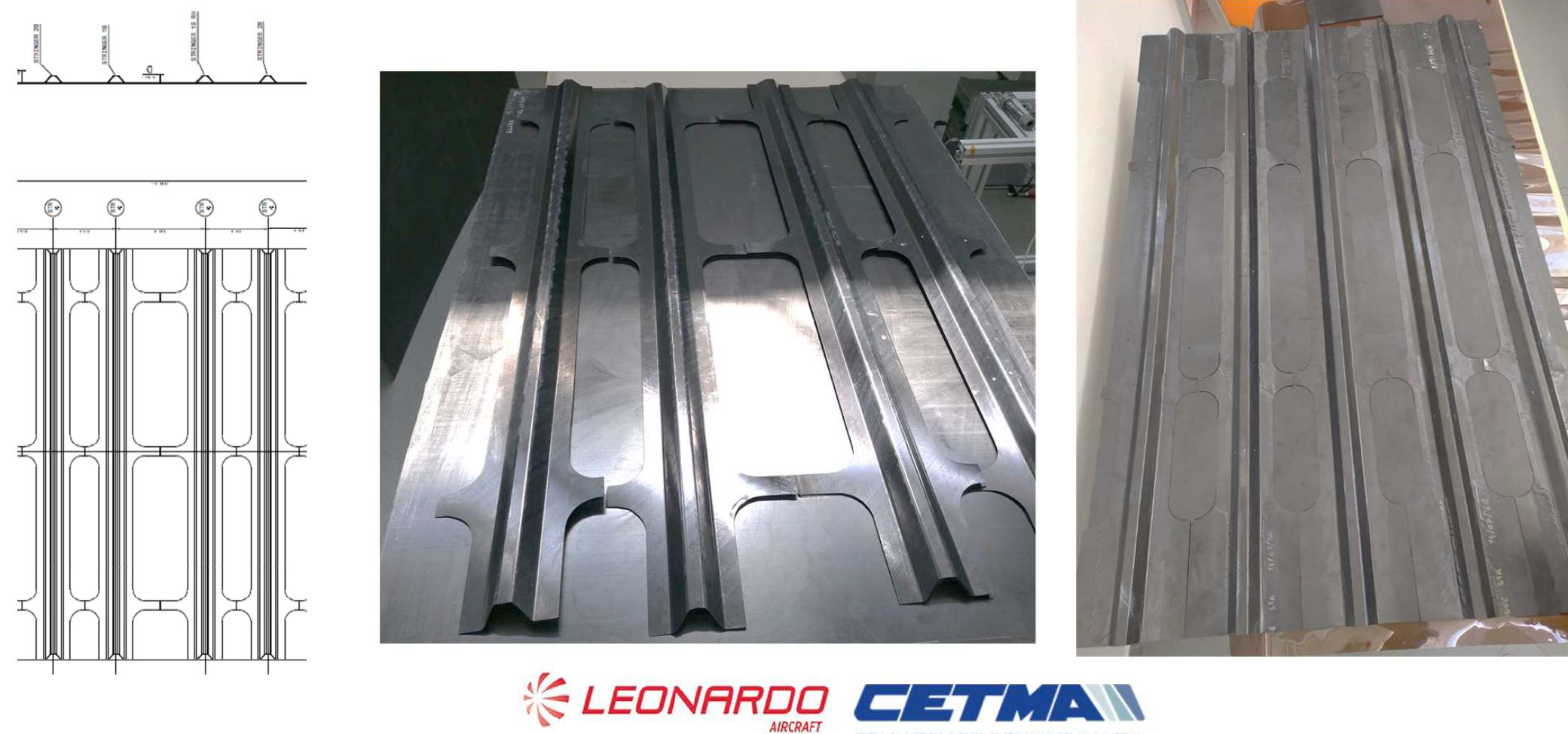
Le nouveau matériau multicouche offrait-il des avantages pour le soudage par induction ? "Cela a essentiellement traité de la même manière", explique Barile. « Cependant, il n'a pas été facile pour le CETMA de définir les paramètres du processus de soudage car notre nouveau matériau contient moins de fibres de carbone que les rubans standard. » Les démonstrateurs de longerons et le démonstrateur de panneau de fuselage final ont ensuite été testés par Applus. Les partenaires du projet NHYTE, l'Université de Bath (Bath, Royaume-Uni) et Leonardo Aircraft ont également utilisé le NDI pour évaluer la qualité des panneaux et des longerons.
« Nous avons fait beaucoup de coupons et de petites pièces, ainsi que le grand démonstrateur », note Barile. « Les résultats des tests d'Applus sont très bons compte tenu du coût inférieur du processus de fabrication par rapport à ce qui est standard actuellement. Nos propriétés de résistance et de rigidité sont de 20 à 25 % inférieures à celles des rubans thermoplastiques standard actuellement disponibles, mais nous avons identifié des améliorations du processus qui devraient contribuer à améliorer cela. »
NHYTE a pris fin le 30 octobre 2020. «Notre idée est de procéder à un nouveau projet pour inclure toutes les améliorations que nous avons en tête», explique Barile. « Nous avons prouvé comment fabriquer le matériau et comment le traiter en utilisant la consolidation in situ AFP, le formage continu et le soudage par induction. Nous devons maintenant optimiser davantage pour l'industrialisation. Novotech cherche à poursuivre avec le même consortium enrichi de nouveaux partenaires.
Notamment, Leonardo s'efforce également d'améliorer la consolidation in situ de l'AFP en utilisant le soudage par induction et le ruban TPC qui peut être chauffé et refroidi rapidement. Par ailleurs, des résultats encourageants sur les composites multicouches PEI/PEEK viennent d'être publiés par des chercheurs de l'IMDEA Materials Institute (Madrid, Espagne) et de la FIDAMC (Madrid, Espagne), cette dernière étant depuis de nombreuses années leader dans la consolidation in-situ d'AFP. Pour plus d'articles techniques, voir les publications de NHYTE.
Projet SWING
La Smart Wing pour la nouvelle aviation générale (SWING) est un projet qui a débuté avec l'approbation de Piaggio Aerospace (Villanova d'Albenga, Italie) et est cofinancé par le ministère italien du Développement économique (MISE). Outre Novotech, le consortium de projet italien comprend la société de développement technologique Protom (Naples) en tant que coordinateur, Laer Aeronautical Manufacturing (Airola), A. Abete Aerostructures (Nola) et le spécialiste de la conception aérospatiale ItalSystem (Avellino). L'un des objectifs de SWING est d'adapter les processus automatisés de composites hors autoclave (OOA) - y compris l'AFP et l'infusion de résine liquide (LRI) - pour une production rentable et durable d'avions plus petits, en utilisant le P.180 Avanti aile avant comme plate-forme de démonstration.
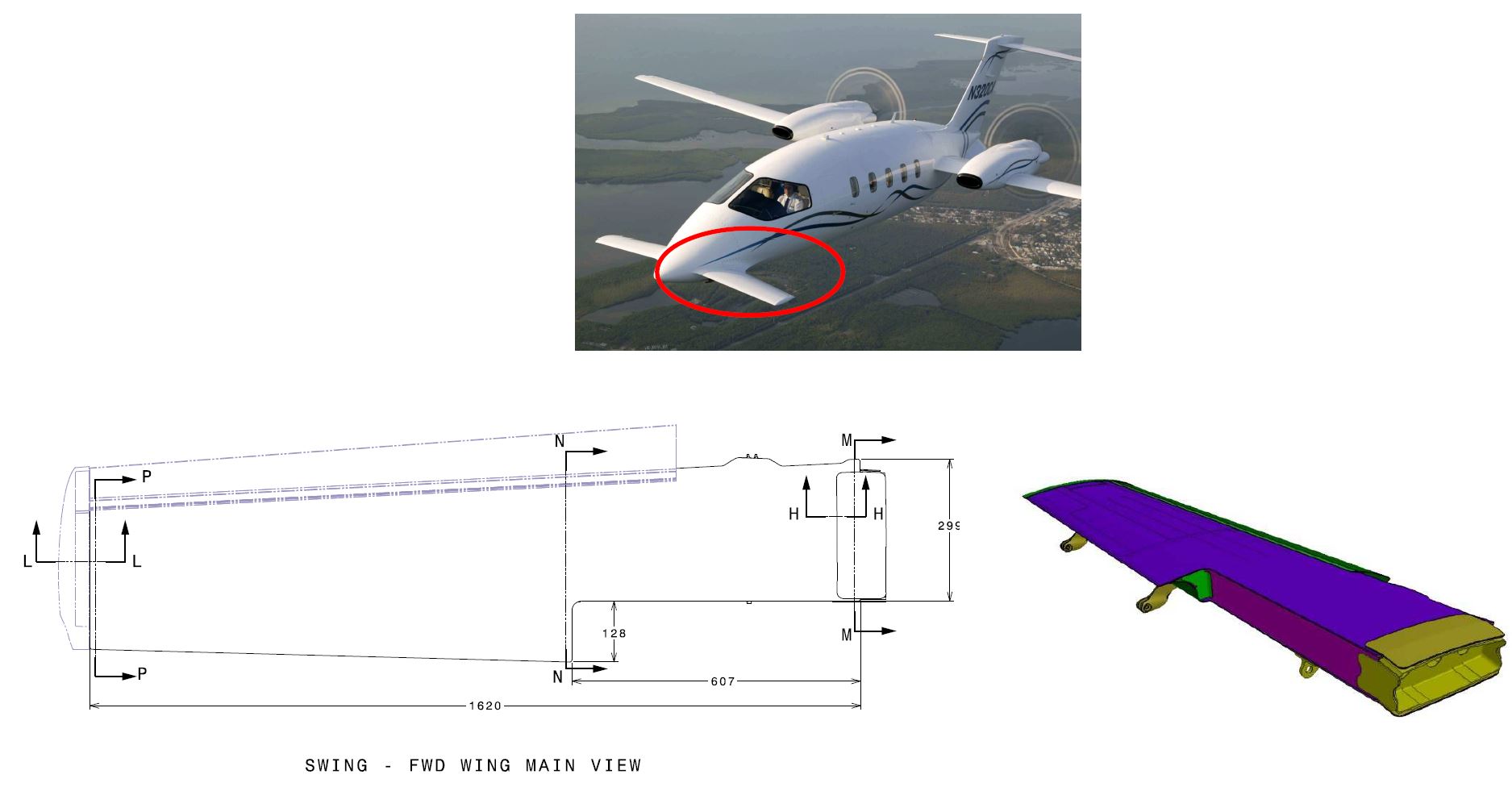
« L'idée est de produire l'aile avant du P.180 en seulement deux parties principales :un panneau supérieur et un panneau inférieur, tous deux moulés avec des longerons et des longerons intégrés », explique Lecce.
« Pour nous, cela a commencé avec notre travail en tant que laboratoire qualifié pour Solvay au Royaume-Uni. Nous coopérons depuis 2015 sur de nouveaux matériaux et procédés pour l'AFP, le LRI et les composites thermoplastiques. Nous fabriquions des préformes sèches en utilisant le ruban à fibres sèches PRISM TX1100 de Solvay pour une utilisation avec l'AFP. Ces préformes ont ensuite été infusées avec de la résine époxy durcie Solvay PRISM EP 2400 et durcies dans un four. Nous faisions ce travail dans le cadre du projet AIRGREEN 2 pour le programme Clean Sky 2 Green Regional Aircraft, puis nous avons continué dans le projet SWING. Notez que PRISM TX1100 et PRISM EP 2400 ont été qualifiés par United Aircraft Corporation pour la production de la première aile infusée de résine pour un avion commercial - l'avion de ligne monocouloir Irkut MS-21 fabriqué par AeroComposit.
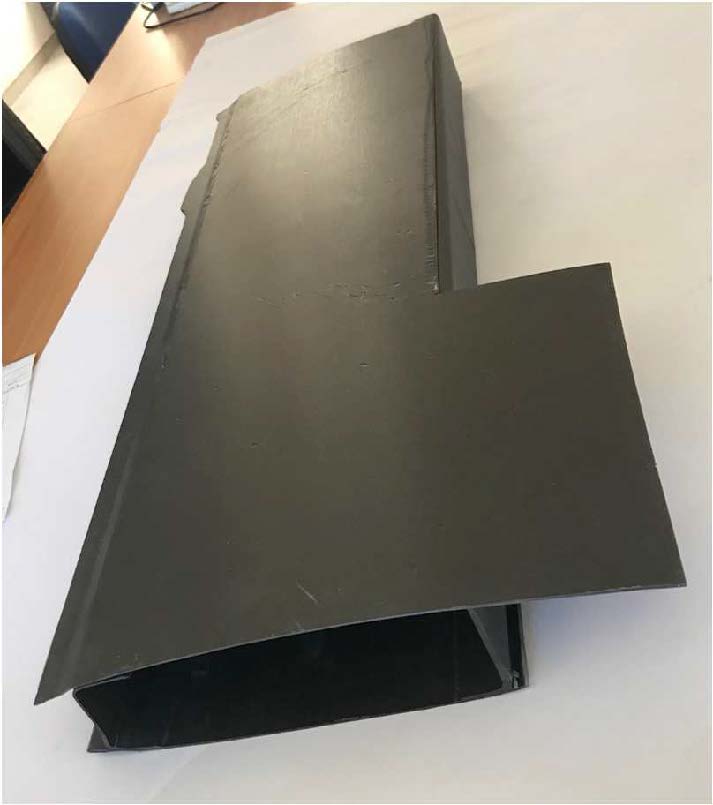
Les panneaux supérieurs et inférieurs moulés seront assemblés à l'aide d'un adhésif structurel puis testés statiquement l'année prochaine. « En parallèle, nous caractérisons un autre composite à base de ruban sec TX1100 et d'un mélange de résines de Covestro (Leverkusen, Allemagne) qui peut constituer une alternative valable aux résines de qualité aérospatiale, en particulier pour les secteurs qui nécessitent des cadences de production plus élevées », ajoute Barile. « Cette résine n'est pas aussi performante que ces systèmes, mais elle fonctionne bien avec l'infusion et répond aux exigences du caisson de voilure. Il doit y avoir un certain compromis si vous voulez réduire les coûts. Nous espérons que ce développement contribuera à introduire la technologie AFP dans l'aviation générale. Il pourrait également être utilisé dans le secteur automobile. »
TRINITI
Novotech travaille également dans le projet Clean Sky 2 TRINITI — Réservoirs d'azote haute pression thermoplastiques multi-matériaux pour avions — qui a débuté en 2019 et se terminera en 2021. L'entrée de Novotech dans ce projet a encore une fois évolué à partir d'un développement avec une société aérospatiale italienne. "Nous travaillions pour vérifier le potentiel de l'AFP en utilisant notre ruban multicouche dans la production de réservoirs de carburant cryogéniques pour les lanceurs par rapport aux procédés d'enroulement filamentaire actuellement utilisés", explique Barile. "Essentiellement, TRINITI développera un concept de matériau multicouche similaire à NHYTE, puis fabriquera un réservoir en utilisant la consolidation in-situ AFP."
« L'avantage de l'AFP par rapport à FW, poursuit-il, c'est que vous pouvez décider où vous voulez placer le matériel. Vous n'êtes pas contraint par le filament enroulé en continu autour de la pièce. Considérez un réservoir où vous avez beaucoup de matériau au niveau des embouts car vous ne pouvez pas couper le matériau pendant l'enroulement filamentaire. En coupant et en redémarrant les fibres/rubans où vous le souhaitez avec l'AFP, le matériau n'est utilisé que là où il est nécessaire. Ainsi, vous pouvez gérer les écarts entre les bandes, ce qui est important pour éviter la perméation des gaz. Pour ce faire avec l'enroulement filamentaire, vous devez augmenter la matière appliquée, même parce qu'avec l'AFP vous utilisez du ruban adhésif fendu et non du towpreg. Et puis avec la consolidation in-situ, il n'y a pas besoin d'autoclave. Nous avons démontré que l'AFP pouvait être une alternative faisable et très abordable. »
« Actuellement, le CETMA effectue des tests de perméation de gaz pour évaluer les performances des matériaux multicouches par rapport aux spécifications », explique Barile. Des exigences ont été fournies par le responsable du sujet, Diehl Aviation (Gilching et Dresde, Allemagne) pour un réservoir d'azote haute pression à long stockage utilisé dans les systèmes d'extinction d'incendie des avions. Ces réservoirs doivent résister à des températures de -55°C à 85°C au sol, de -40°C à 70°C en vol et à des pressions jusqu'à 1 000 bar.
« L'objectif est de réduire le poids et les étapes de fabrication », note-t-il. « Cependant, le coût de fabrication selon cette méthode doit être défini. Le poids est économisé en ne plaçant pas de matériau inutile, mais l'enroulement filamentaire est un processus plus rapide par rapport à l'AFP. Un autre facteur est que ce type de réservoir a généralement une doublure en métal ou en plastique recouverte de CFRP. Barile dit que TRINITI essaie un réservoir sans doublure (type V). « Nous éviterons la perméation des gaz en utilisant un stratifié AFP à faible vide. Nous testons actuellement au CETMA avec différentes combinaisons de matériaux et nous nous préparons à downselect. Nous construirons ensuite un prototype de réservoir, mais la conception du réservoir dépend du matériau sélectionné et du processus final. C'est donc ce vers quoi nous travaillons actuellement. L'activité de test sera réalisée par CTL Composites (Galway, Irlande).”
MOUETTE
Le projet ambitieux SEAGULL a été lancé il y a trois ans. « Notre objectif est de développer un petit hydravion de nouvelle génération qui intègre une nouvelle technologie de fabrication de composites, une propulsion électrique hybride et une aile repliable automatisée, que nous avons développée et brevetée », explique Lecce. "L'intention était un avion à décollage et atterrissage courts (STOL) qui soit compétitif avec les avions à décollage et atterrissage verticaux (VTOL) mais offre plus d'abordabilité. Nous pensons qu'il pourrait s'agir d'un avion personnel exploité à partir de n'importe quelle surface et qu'il s'agit d'une possibilité importante pour l'aéronautique et la mobilité futures. »
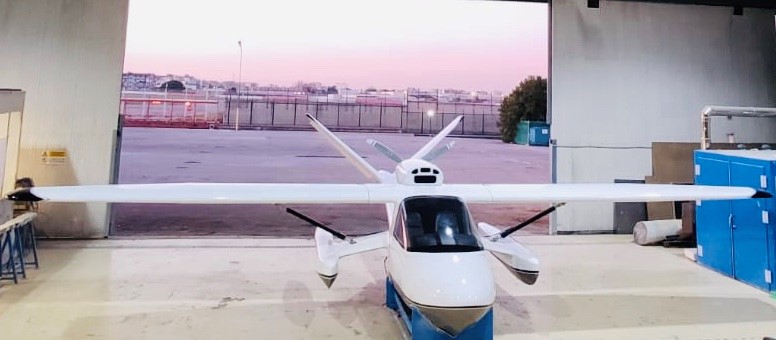
L'équipe SEAGULL a testé un système de propulsion hybride, construit un premier prototype sous-marin et commencé les tests sous-marins en octobre. « Une fois ces tests terminés, nous construirons ensuite un prototype volant dans quelques mois », explique Lecce. « C'est une équipe très expérimentée, composée d'entreprises importantes avec plus de 50 ans d'expérience dans l'aviation générale. »
Le prototype volant SEAGULL comportera un fuselage, une queue et une aile en composite. "Encore une fois, nous allons pousser l'application de la fabrication automatisée à l'aide de l'AFP et de l'infusion de résine", a déclaré Barile. « L'un des principaux problèmes des composites utilisant ces procédés est le coût des matériaux. En effet, ce que nous essayons de faire, c'est de trouver également une combinaison de matériel et de processus qui soit plus démocratique en termes de coût. »
Résine
- Fraunhofer IPT développe des composites thermoplastiques pour le stockage d'hydrogène, les aubes de moteur et plus encore
- Composites Evolution présente des préimprégnés hautes performances, de nouveaux rubans UD thermoplastiques
- Conception pour la fabrication automatisée de composites d'aérostructures de faible volume
- Les bandes thermoplastiques continuent de montrer un potentiel pour les aérostructures composites
- Karl Mayer lance une ligne de production de rubans thermoplastiques UD
- SWM lance le média d'écoulement Naltex pour l'infusion de résine
- Porte thermoplastique une première pour les composites automobiles
- Le consortium des composites thermoplastiques vise une production à haut volume pour l'automobile et l'aérospatiale
- Au service du monde des composites en Israël et aux États-Unis