Composites comme renforts de carrosserie
Bien que les composites aient fait quelques percées dans les structures de carrosserie automobile en blanc (BIW), les matériaux utilisés dans cette zone du véhicule ont longtemps été dominés par l'acier et, plus récemment, l'aluminium. Pour cette raison, les constructeurs automobiles s'appuient fortement sur le soudage et les fixations mécaniques comme les boulons et les vis pour joindre les structures métalliques. Bien que généralement robustes, les joints soudés et les fixations peuvent échouer. Ils font également peu pour améliorer la rigidité (sans augmenter indûment la masse) ou pour atténuer le bruit/les vibrations/la dureté (NVH) ou l'énergie de collision traversant un véhicule. Une façon de relever ces défis consiste à renforcer les joints et les cavités BIW avec des composites couplés à des adhésifs structuraux.
Un exemple d'une telle solution est une classe de matériaux/technologies appelée solutions de corps composites (CBS). Il s'agit notamment d'inserts structurels 3D pour le renforcement des structures primaires de véhicules qui combinent des éléments du BIW ou d'autres sous-structures de véhicules, des supports thermoplastiques (avec renforcement en fibres continues ou discontinues) et des adhésifs structurels moussants activés par la chaleur. Les éléments CBS sont installés dans la partie atelier de carrosserie au début de la construction du véhicule, avant l'application du revêtement antirouille électrophorétique (E-coat).
Les composants CBS sont généralement produits dans un processus de surmoulage 2K/injection où le support - incorporant des languettes de soudage ou des emboîtements pour joindre temporairement le CBS aux composants métalliques BIW - est surmoulé de manière sélective avec un adhésif expansible et éventuellement un mastic supplémentaire (dans un processus 3K) pour des fonctionnalités supplémentaires. L'adhésif non durci sec au toucher (basé sur une chimie époxy personnalisée) peut être moulé dans des formes complexes, tout en permettant une couverture E-coat des éléments métalliques en maintenant un espace entre les surfaces composites et métalliques avant l'expansion induite par la chaleur pendant le post -Cuisson au four E-coat. Au fur et à mesure que la mousse se dilate, les espaces sont scellés entre le support et les composants environnants, les verrouillant ensemble dans une « macro-structure » en forme de boîte qui améliore les propriétés mécaniques, en particulier sous des charges élevées et dynamiques.
Lorsqu'ils sont incorporés tôt dans la conception du véhicule, les modules CBS sont des options économiques et économiques pour augmenter la rigidité BIW locale et globale et améliorer la sécurité et le confort des passagers à faible masse. Ils permettent également des solutions neutres ou à moindre coût par rapport à des solutions entièrement métalliques plus lourdes. Initialement juste utilisé dans l'automobile, un portefeuille croissant de supports et de matériaux adhésifs a élargi les utilisations de CBS, dont les points saillants suivent.
Conçu pour les défis de performance
La technologie CBS a été développée et commercialisée par L&L Products Inc. (Romeo, Michigan, États-Unis). Avec une longue histoire en tant que fournisseur automobile de produits d'étanchéité, de contre-mesures acoustiques et de renforts pour améliorer les performances BIW, L&L a développé la technologie pour aider les clients à améliorer la sécurité des passagers et à répondre aux exigences plus strictes en matière de collision automobile à un coût et un poids inférieurs tout en améliorant le traitement et l'assemblage pendant la construction du véhicule. .
Entre 1995 et 2004, CORE Products, une coentreprise entre L&L et Gurit Essex (Wattwil, Suisse), était responsable du développement des premières applications et de la fabrication de CBS. L&L a finalement acquis tous les actifs de CORE, qui opère désormais sous le nom de L&L Products Europe.
L&L a travaillé en étroite collaboration avec ses fournisseurs de matériaux lors du développement initial et de l'expansion ultérieure de la technologie CBS. L'une de ces entreprises, Lanxess AG (Cologne, Allemagne), fournit depuis longtemps des matériaux de support composites et une assistance à la simulation et à la caractérisation des matériaux à L&L en Europe.
CBS en application
En plus des avantages déjà mentionnés, la technologie CBS offre une meilleure transition charge-chemin, une gestion de la charge multiaxiale et une meilleure absorption d'énergie ; une plus grande stabilité de section (résistance à l'effondrement ou à l'intrusion); NVH inférieur ; et une dynamique de conduite et des performances de collision améliorées à des charges plus élevées. De plus, il offre un délai de mise en œuvre plus rapide lors de la conception/reconception du véhicule et ne nécessite aucun changement de séquence d'assemblage dans l'atelier de carrosserie. Parce que la technologie CBS facilite le contrôle du transfert d'énergie à travers les structures de carrosserie tout en minimisant la déformation et/ou l'intrusion, elle est idéale pour les applications conçues pour résister aux collisions frontales, latérales ou arrière ou à l'écrasement du toit afin de mieux protéger les occupants, les compartiments passagers et les batteries. Il est également utile pour les structures qui doivent passer des protocoles exigeants tels que les tests de collision à faible chevauchement de l'Insurance Institute for Highway Safety (IIHS, Arlington, Virginie, États-Unis).
Ce qui a rendu CBS remarquable, c'est qu'il faisait partie des premières approches modulaires à matériaux mixtes, qu'il était facile à installer, qu'il offrait une stabilité thermique et chimique pour le revêtement E et qu'il ne modifiait pas le séquençage de l'assemblage du véhicule, mais améliorait les performances à faible masse et neutre/ à moindre coût — le Saint Graal de l'industrie automobile.
« La polyvalence de conception de la technologie CBS permet de simplifier l'assemblage dans les zones aux conditions complexes ou difficiles d'accès », explique Núria Ignés, responsable de l'ingénierie des produits structurels, L&L Products Reinforce chez L&L Products EMEA (Altorf, France). « Par exemple, l'utilisation de la technologie CBS sur les portes et autres fermetures réduit non seulement le poids et augmente la rigidité, mais peut également simplifier la fabrication des portes si elle est intégrée dès le début du processus de conception. Grâce aux outils CAE et à des décennies d'expérience, ainsi qu'à la combinaison de support et de mousse, qui fournit une fixation robuste au BIW une fois durci, nous pouvons utiliser la bonne quantité du bon matériau au bon endroit pour équilibrer la rigidité avec la masse et le coût ou l'absorption d'énergie avec l'acoustique et le coût. »
"Un aspect vraiment intéressant de la technologie CBS est sa nature" bio-mimétique "", ajoute Peter Cate, responsable marketing stratégique mondial de L&L. « Tout comme les entretoises de renforcement cellulaire au centre des os sont la méthode naturelle la plus efficace en termes de masse pour ajouter de la rigidité et gérer les charges dans les structures creuses, une fois que l'adhésif se dilate, les unités CBS renforcent les cavités de la carrosserie du véhicule de la même manière, aidant les ingénieurs à optimiser la structure rigidité à la masse la plus faible. »
« En augmentant la rigidité locale et globale et en répartissant les charges plus efficacement sur une structure, les renforts CBS sont des solutions sur mesure pour résoudre les problèmes de rigidité localisée et de fatigue du métal sans ajouter de masse », poursuit Pal Swaminathan, directeur du développement commercial, Tepex Automotive, Lanxess Corp. (Pittsburgh, Pennsylvanie, États-Unis). « Les améliorations NVH sont également courantes lorsque la technologie CBS est intégrée aux structures corporelles. Encore une fois, une analyse technique minutieuse permet aux solutions de développement et d'optimisation de l'emplacement d'équilibrer les caractéristiques de conduite et de maniement. »
Applications précoces
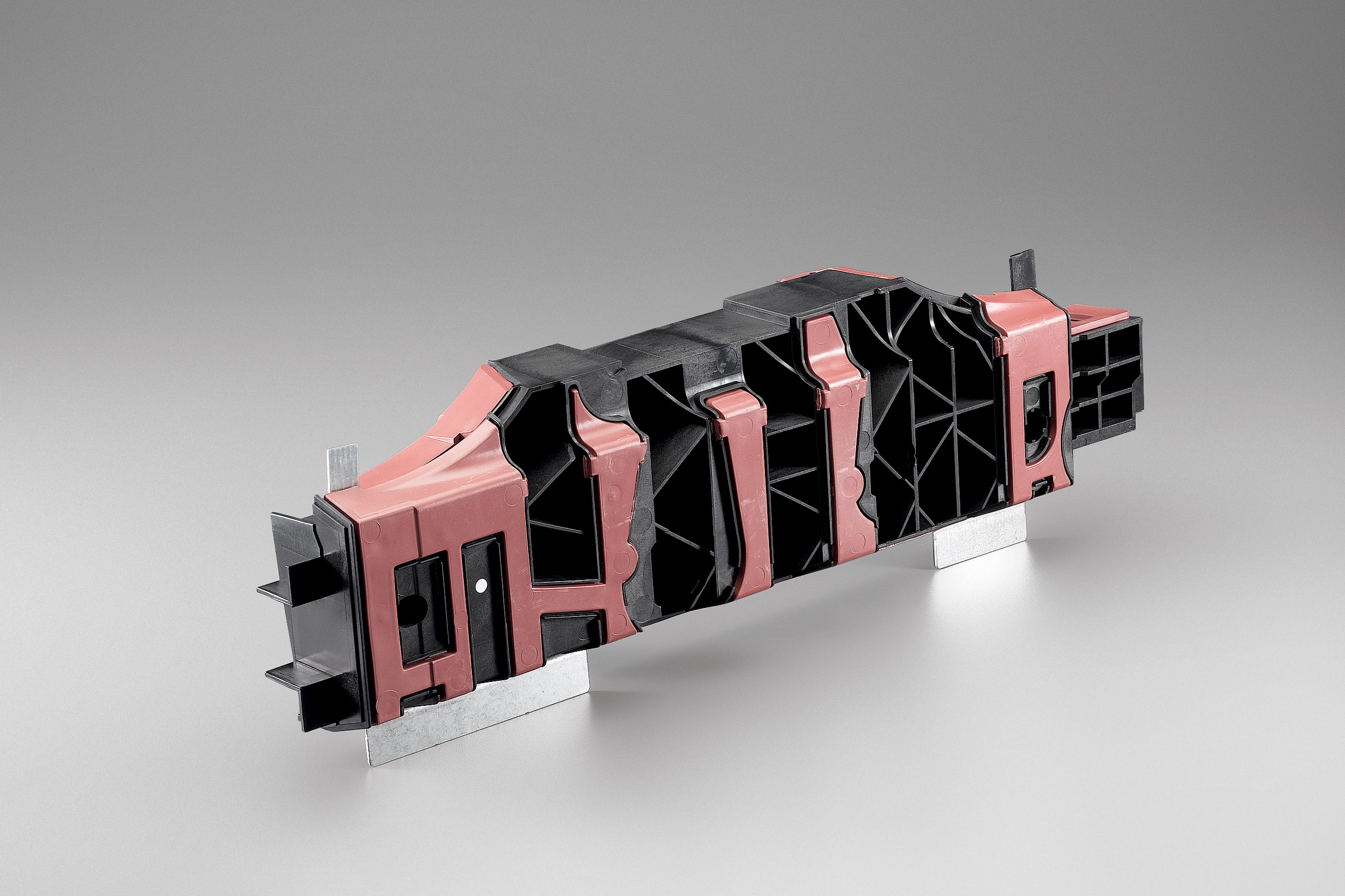
La première application automobile commerciale de CBS par L&L remonte à 1998 ; en 2002, la technologie était de plus en plus acceptée par le marché. Un bon exemple précoce a été mis en œuvre sur 2006 Citroën C4 Picasso berlines du Groupe PSA (Paris, France – maintenant Stellantis N.V., Amsterdam, Pays-Bas). Neuf composants CBS — sur les sections inférieures des montants A, les sections inférieures et supérieures des montants B et sur la traverse au-dessus de l'essieu arrière — ont réduit la masse du véhicule de 12 kilogrammes par rapport aux options métalliques. Certains inserts CBS ont augmenté de manière sélective la capacité de charge et minimisé l'intrusion dans l'habitacle lors d'un impact, améliorant ainsi la sécurité des occupants. D'autres ont amélioré les performances NVH du BIW. Tous les supports ont été moulés par injection à partir de 35 % en poids de verre court/polyamide 6 (PA6). Des unités CBS similaires ont été utilisées sur le Ford Transit 2012 fourgonnettes de Ford Motor Co. (Dearborn, Michigan, États-Unis).
Nouveau porte-bébé, options de mousse
Au fil des ans, L&L et ses fournisseurs ont étendu la technologie CBS avec de nouvelles formulations de mousse, une gamme plus large de résines de support et de renforts et en appliquant le concept à différentes structures.
Par exemple, la plupart des supports CBS pour les applications de collision sont conçus à l'aide de PA6 renforcé de verre à 30 % en poids stabilisé thermiquement, car un équilibre entre la rigidité et la ductilité dans une forme 3D complexe est nécessaire. Deux de ces supports ont été utilisés sur les éléments longitudinaux avant d'une plate-forme de véhicule électrique (EV) majeure où, apparemment, ils ont non seulement simplifié l'assemblage (réduction du nombre de pièces) mais également réduit l'intrusion de collision dans le pare-feu de 20 %.
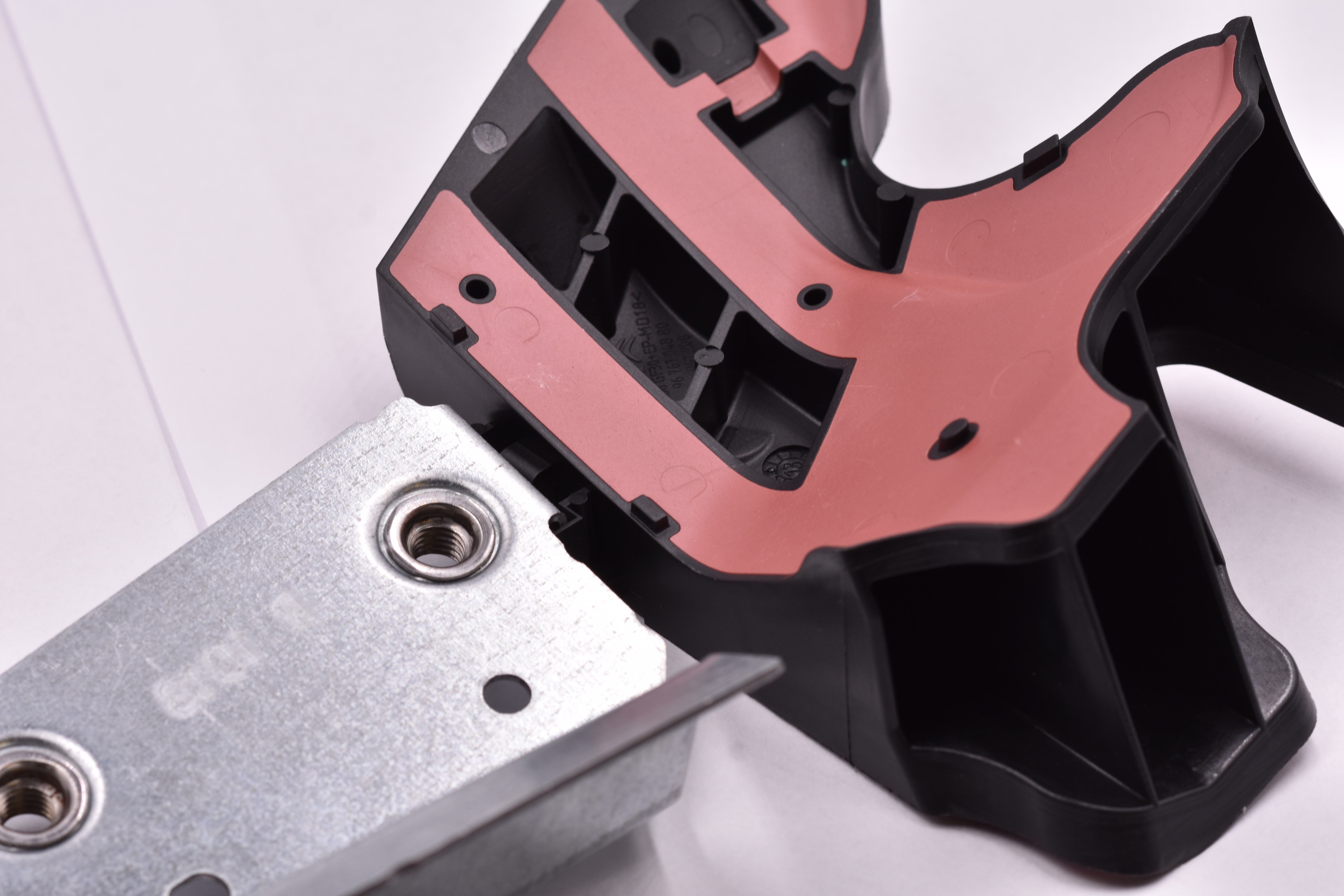
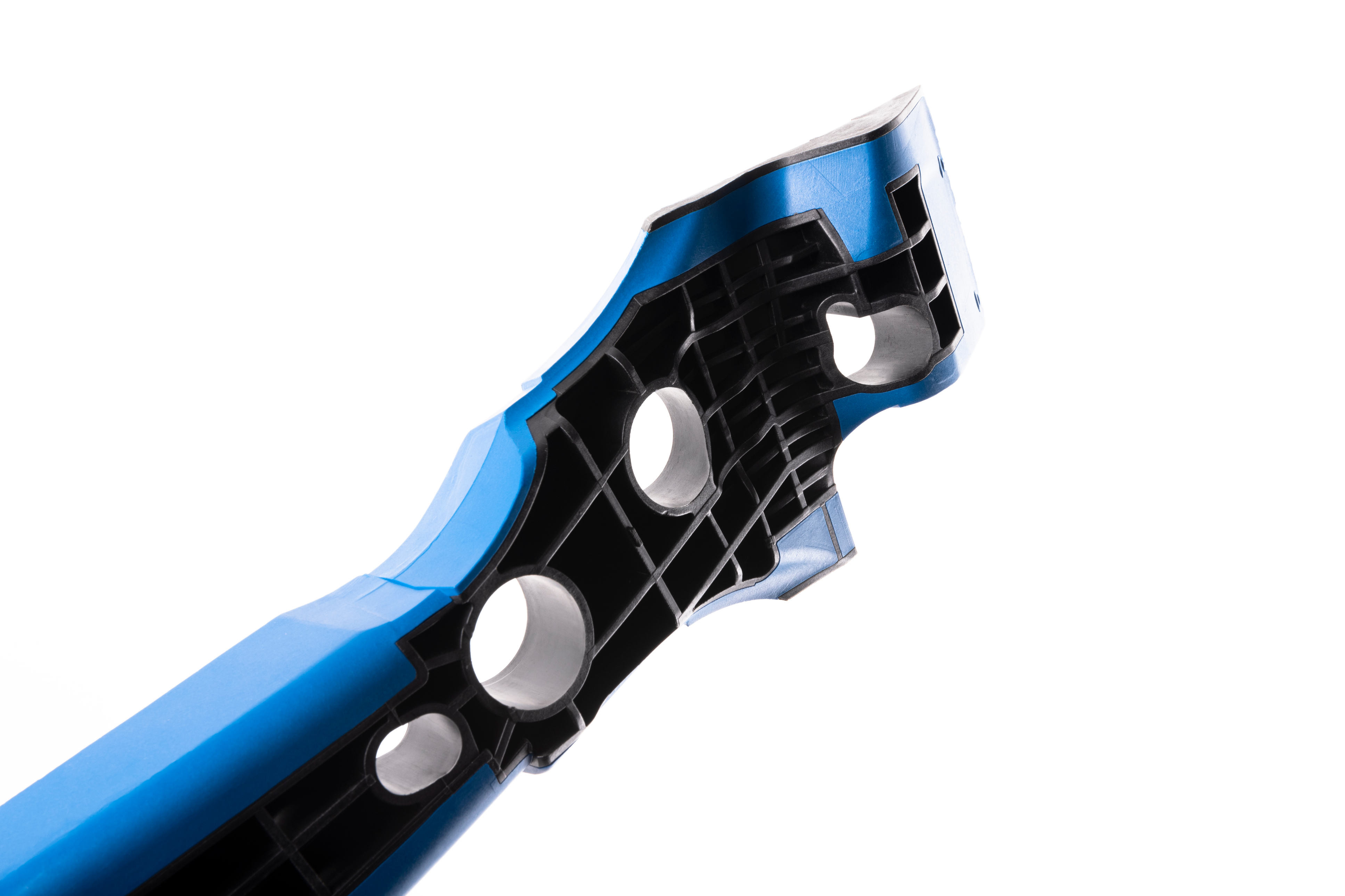
Pour les exigences d'impact plus élevées, des supports hybrides sont désormais disponibles, tels que ceux de renforcement des montants A sur la Porsche 911 Carrera Cabriolet 2019 à carrosserie en grande partie en aluminium. voiture de sport de Porsche AG (Stuttgart, Allemagne). Étant un cabriolet, le renforcement du cadre sans toit était essentiel pour protéger les passagers en cas de capotage. Pour garder les véhicules légers et agiles, Porsche a remplacé les lourds arceaux de sécurité tubulaires en acier par des inserts CBS dans les montants A. Les coques de pilier ont été produites en acier à haute résistance, qui ont été stabilisées et rigidifiées par des inserts CBS à l'intérieur de chaque pilier. Le corps principal du support était une feuille organique moulée par compression (47 % en volume de tissu de verre sergé/PA6), qui a été préchauffé, préformé, puis surmoulé par injection avec des nervures (30 % en poids de verre court/PA6/6). Le côté organosheet porte l'adhésif expansible L-5235 de L&L. Non seulement cette technologie hybride a atteint tous les objectifs de performances et de poids (ce que l'option en acier tubulaire n'aurait pas atteint), mais elle a également réduit la masse du véhicule de 5,4 kilogrammes, facilitant l'assemblage et réduisant le centre de gravité du véhicule, ce qui a amélioré la dynamique de conduite.
Pour les applications où un processus au four n'est pas disponible pour activer l'adhésif expansible, ou lorsqu'un support supplémentaire est nécessaire dans l'atelier de peinture, L&L dit qu'il travaille sur d'autres solutions à durcissement ambiant.
Plusieurs technologies connexes basées sur CBS ont également été développées. Bientôt pour avoir sa première application commerciale, le système composite continu (CCS) de L&L combine des supports pultrudés renforcés de fibre de verre ou de carbone - par exemple, le polyuréthane (PUR) avec ou sans tissus ainsi que mèches — avec des mastics ou des adhésifs structuraux formulés sur mesure. Les éléments CCS, qui peuvent également incorporer des pièces CBS et des composants métalliques, améliorent la rigidité et la résistance des structures à section transversale constante à une masse inférieure (généralement 75 % de moins que l'acier et 30 % de moins que l'aluminium). Ils sont résistants à la corrosion, non conducteurs/isolants électriquement, offrent un faible coefficient de dilatation thermique linéaire (CLTE) et fournissent une gestion de l'énergie hautement prévisible, ce qui les rend idéaux pour renforcer les éléments structurels sur les véhicules monocoques ou les sections de châssis pour les véhicules à carrosserie sur châssis, plus des cadres de batterie pour les véhicules électriques.
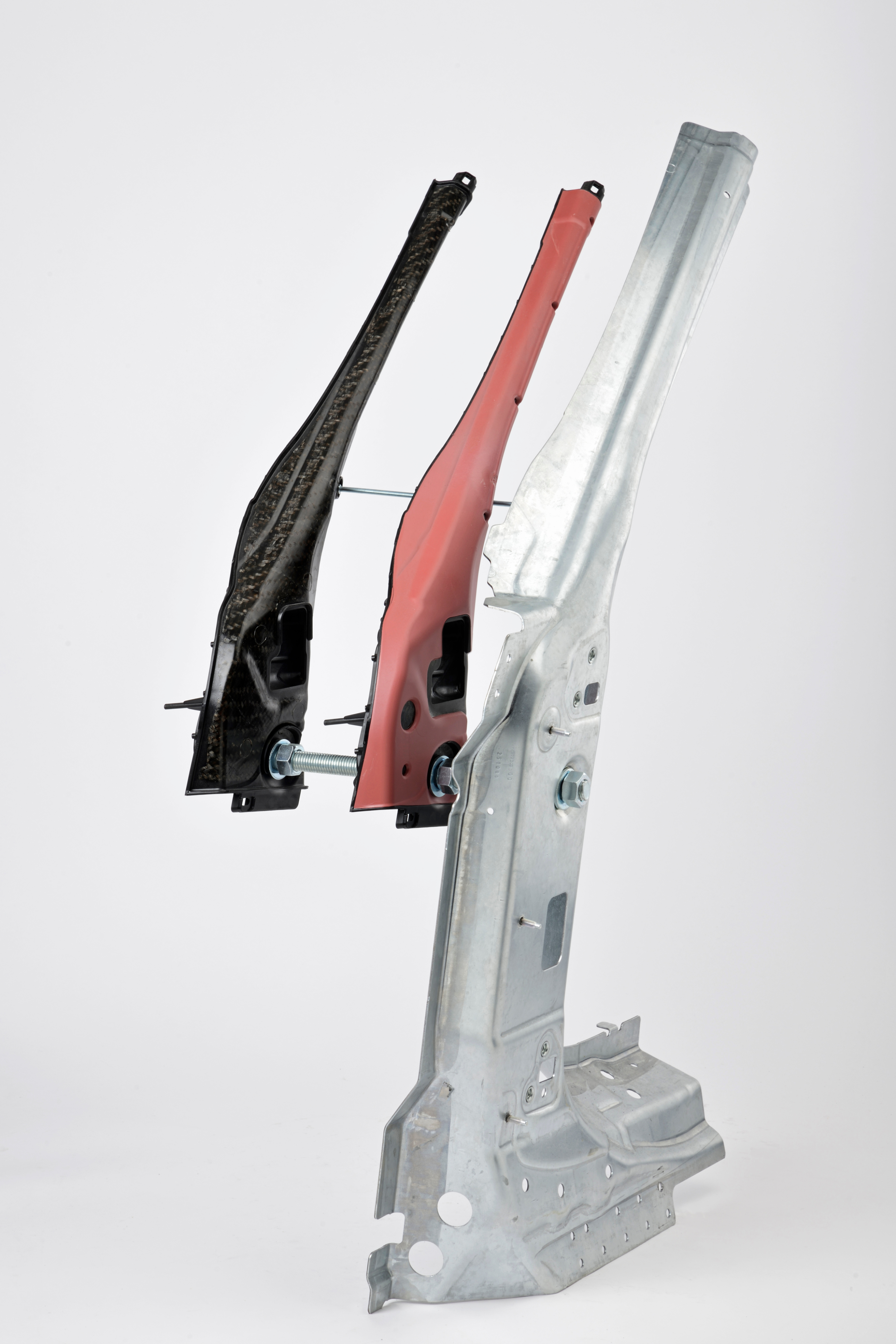
Les renforts de panneaux composites comprennent des adhésifs structurels autoadhésifs et expansibles co-extrudés avec un renfort en fibre de verre qui sont appliqués sur les surfaces des panneaux métalliques formés dans l'atelier de carrosserie. Le système améliore non seulement la rigidité (réduction de l'ondulation et du flambage) des panneaux de grande taille/relativement non soutenus, mais améliore également la NVH en raison d'un moment d'inertie accru. De plus, il offre la possibilité de réduire l'épaisseur des panneaux pour une masse et un coût inférieurs. Les applications commerciales comprennent les panneaux de porte, de toit et de plancher, les capots, les ailes, les hayons élévateurs et les hayons arrière d'automobiles ; les applications potentielles incluent les boîtiers de batterie.
Les renforts des panneaux en nid d'abeille sont constitués d'époxy léger - sous forme de pâte pour une application manuelle ou de liquide à faible viscosité pour un pompage automatisé - qui, une fois durci, peut être usiné ou poncé. Ceux-ci sont conçus pour stabiliser les noyaux en nid d'abeille, principalement dans des emplacements stratégiques dans les intérieurs d'avions, par exemple, sans ajouter de masse excessive. D'autres utilisations incluent l'amélioration des bordures (étanchéité/renforcement des bords des panneaux composites), le collage des inserts et le renforcement local là où les charnières/inserts métalliques sont installés dans les panneaux composites.
Ce que l'avenir nous réserve
Depuis son premier brevet en 1999, L&L a déposé de nombreuses inventions pour la technologie CBS. Compte tenu de la large gamme d'options de supports et d'adhésifs désormais disponibles dans cette famille de produits, il n'est pas surprenant que les applications se soient étendues au-delà de l'automobile pour les camions et l'aérospatiale. Quelle est la prochaine étape ?
« Au fil des années, les produits CBS ont évolué pour répondre aux nouvelles exigences applicatives qui combinent les fonctions », ajoute Ignés. « Par exemple, ce qui n'était au départ qu'un renfort structurel a évolué non seulement pour se rigidifier, mais aussi pour améliorer les fonctions acoustiques ou pour augmenter l'absorption d'énergie. Compte tenu de la suite de propriétés hautement souhaitables offertes par la technologie CBS, nous nous attendons non seulement à une croissance de l'utilisation de l'automobile, mais également à une croissance dans d'autres industries. »
Résine
- CompositesWorld SourceBook 2022
- Dépannage du thermoformage des composites thermoplastiques
- L'évolution des composites additifs
- Personnes dans les composites – janvier 2019
- CAMX 2018 :aperçus des expositions
- Soudage de composites thermoplastiques
- Aperçu SPE ACCE 2018
- Composites hautes performances en Israël
- Impression 3D de composites avec fibre continue