STELIA Aerospace Composites fait progresser le stockage de l'hydrogène
CW les lecteurs connaîtront STELIA Aerospace (Toulouse, France) grâce à notre couverture de son démonstrateur de fuselage en composite thermoplastique dans le projet ARCHES TP et ma visite de l'usine de Méaulte en 2019. La société dispose cependant d'un réservoir profond d'expertise en composites, couvrant plusieurs emplacements, pièces et processus. STELIA Aerospace Composites (Salaunes, France) est implantée en dehors de Bordeaux. Le site emploie 330 personnes avec 40 000 m² d'ateliers et son propre laboratoire d'essais intégré. Il comprend également trois segments d'activité principaux :les aérostructures, les composants de cabine d'avion et les systèmes de stockage de gaz à enroulement filamentaire. Ce dernier peut être utilisé pour tout, de l'oxygène à l'azote en passant par l'hydrogène, et constitue un segment d'activité principal depuis plus de 35 ans.
STELIA Aerospace Composites a été fondée en 1984 au sein d'Aerospatiale. Depuis 1985, cette usine de Salaunes a produit plus de 70 000 réservoirs haute pression composites suremballés (Type II, III et IV) pour des applications variées. Les travaux de l'entreprise sur le stockage de l'hydrogène ont débuté en 1998 avec le développement d'un réservoir de 9 litres/700 bars pour le Commissariat aux énergies alternatives et à l'énergie atomique (CEA, Paris). STELIA Aerospace Composites a également travaillé avec le constructeur automobile français Groupe PSA (Paris) - désormais fusionné avec Fiat Chrysler pour former Stellantis - et la société mondiale de gaz industriels Air Liquide (Paris, France). Il a également collaboré avec l'équipementier automobile de rang 1 Faurecia (Nanterre, France), qui souhaite devenir un leader des systèmes de véhicules à pile à combustible.
« STELIA Aerospace Composites est bien connu dans le domaine du stockage de gaz sous pression », déclare Christophe Blois, directeur technique de STELIA Aerospace Composites. "Mais maintenant, avec toutes les différentes annonces d'avions verts et la transition vers une économie à zéro émission soutenue par les gouvernements français et européens, nous avons de plus en plus d'entreprises qui nous contactent."
Expérience dans les chars aérospatiaux
En tant que filiale de STELIA Aerospace, l'essentiel de l'expérience de fabrication de STELIA Aerospace Composites a été réalisé avec des récipients sous pression pour des applications aérospatiales et de défense. « Nous avons une capacité d'enroulement filamentaire industriel pour des réservoirs jusqu'à 5 000 litres », explique Blois, « et nous sommes spécialisés dans la conception complète de réservoirs, adaptés aux besoins techniques de nos clients. Cela comprend le dimensionnement, les tests et la sélection des matériaux et la modélisation de l'analyse par éléments finis (FEA), ainsi que les tests de qualification (tels que les cycles de pression et l'éclatement) et le suivi des campagnes de certification pour répondre aux différentes normes et réglementations de l'industrie. »
Il précise qu'en moins de 18 mois, STELIA Aerospace Composites a achevé la conception d'une importante application de réservoir satellite, conforme aux normes de qualification de l'industrie spatiale et avec des coûts de production totalement optimisés. « Nous l'avons qualifié, industrialisé et nous sommes maintenant en train de terminer quatre séries de fabrication. »
Avancement des réservoirs d'hydrogène
STELIA Aerospace Composites a réalisé des réservoirs composites pour le stockage d'hydrogène allant de 2,4 à 143 litres et des pressions de 100 à 700 bars. « Nous sommes un leader dans la conception de réservoirs et nous avons un très grand écosystème avec lequel nous travaillons », déclare Blois.
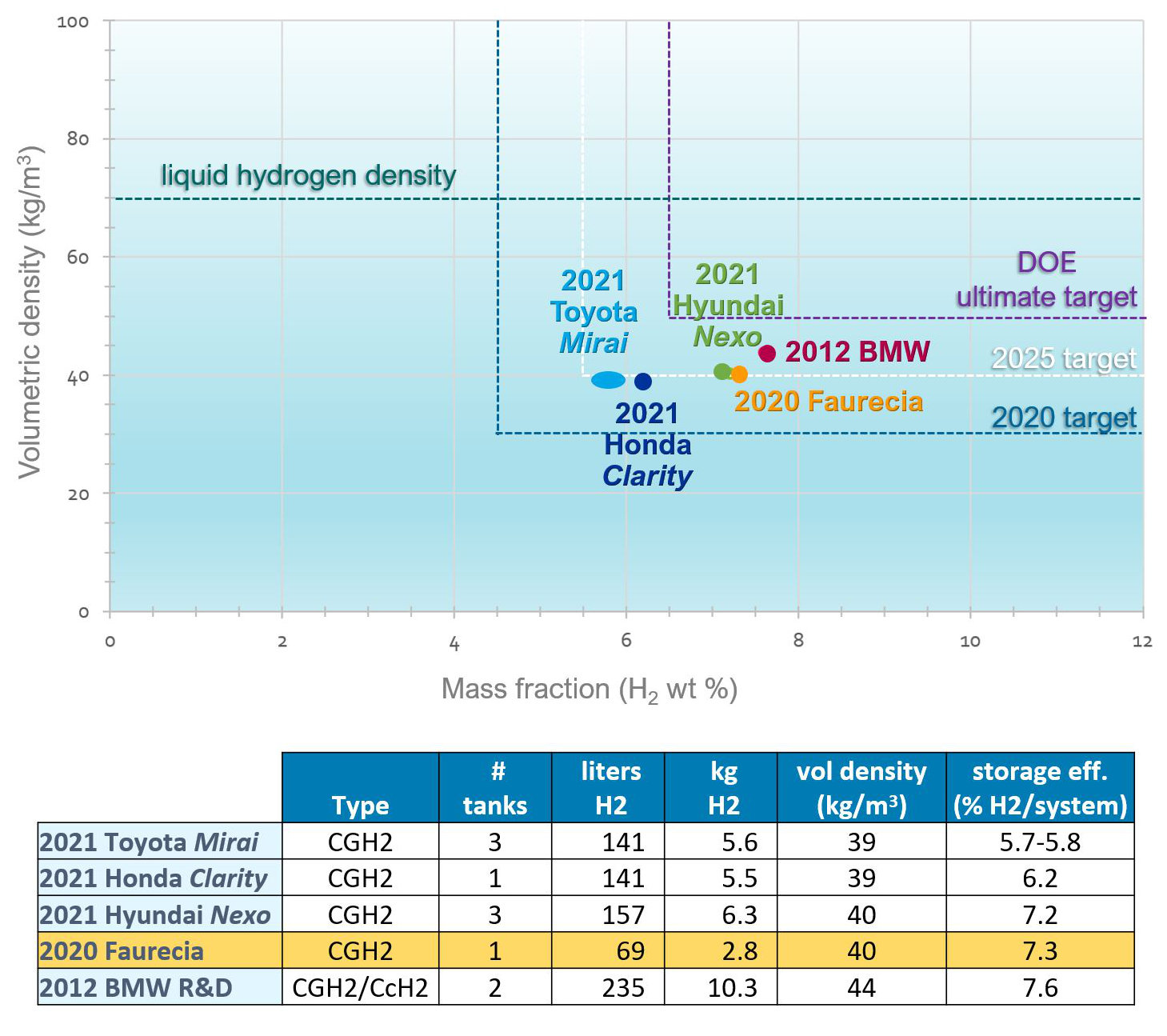
En novembre 2016, STELIA Aerospace Composites a annoncé avoir développé un nouveau réservoir de stockage d'hydrogène en composite fibre de carbone/époxy de 140 litres destiné à améliorer l'autonomie des véhicules électriques à pile à combustible (FCEV). C'est à peu près le même volume d'hydrogène stocké dans la Toyota Mirai 2021 et Honda Clarté FCEV, comme on peut le voir dans le tableau de la Fig. 1. Cependant, seule la Clarté utilise un seul réservoir. Les deux autres FCEV actuellement en production — le Mirai et la Hyundai Nexo — les deux utilisent trois réservoirs.
Faurecia a annoncé dans un communiqué de presse de mai 2017 avoir acquis une licence exclusive sur la propriété intellectuelle et le savoir-faire des procédés concernant les réservoirs d'hydrogène composites de STELIA Aerospace Composites. En avril 2018, les deux sociétés ont présenté conjointement un prototype de réservoir de stockage d'hydrogène de pointe lors de l'événement Hyvolution à Paris. Faurecia a expliqué qu'il visait à être un leader dans la technologie des piles à combustible, prévoyant que 5 millions de FCEV seront opérationnels d'ici 2035.
Comme je l'ai expliqué avec mon co-auteur Mike Favaloro dans l'article SAMPE 2021 intitulé « Taux de croissance projeté de l'utilisation de la fibre de carbone dans les véhicules à hydrogène », le principal problème pour les réservoirs de gaz comprimé est la faible densité volumétrique de l'hydrogène gazeux. Même à une pression de 700 bar, le gaz comprimé (CGH2 ) les réservoirs doivent être plus gros que l'hydrogène liquide (LH2 ) réservoirs. Par exemple, 5 kilogrammes d'hydrogène gaz peut être stocké dans un réservoir de 125 litres à 700 bar et à température ambiante tandis que 5 kilogrammes de liquide l'hydrogène peut être stocké dans un réservoir de 75 litres à pression ambiante et à -252,87°C cryogénique (source :« How is Hydrogen Stored ? » d'Air Liquide). C'est pourquoi l'industrie aéronautique se penche sur LH2 pour les avions et pourquoi les constructeurs automobiles cherchent des solutions aux problèmes d'espace et de poids de CGH2 réservoirs. En outre, la pression plus élevée et la grande taille nécessaires pour répondre à la gamme de véhicules requise par différents constructeurs de voitures et de camions augmentent la quantité de composite renforcé de fibres de carbone nécessaire, et donc le coût du réservoir.
En regardant le graphique et le tableau ci-dessus, le réservoir de 69 litres développé par Faurecia atteint une fraction massique plus élevée que les trois voitures FCEV 2021 actuellement en production. Remarque :la fraction massique est le rapport entre la masse d'hydrogène gazeux et la masse du système de réservoir et est également appelé efficacité de stockage. Le seul système avec une efficacité de stockage supérieure à celle rapportée par Faurecia est un prototype cryo-compressé (CcH2 ) réservoir/CGH2 combinaison de réservoirs développée par BMW et rapportée de 2012 à 2015. Ce système — qui n'est actuellement pas disponible pour les véhicules de production — est un hybride entre LH2 et CGH2 systèmes. En utilisant des températures froides (par exemple, 233°C à -193°C) mais également une pression (par exemple, 350 bars), BMW a affirmé qu'il était possible d'éliminer les problèmes d'évaporation dans les LH2 traditionnels. réservoirs tout en atteignant des densités de stockage bien supérieures à CGH2 et même LH2 systèmes.
Discussion sur le futur H2 développement de chars
Directeur technique de STELIA Aerospace Composites, Blois est dans l'entreprise depuis 30 ans. Je lui pose des questions sur le travail de son entreprise avec Air Liquide et si la société mondiale de gaz industriel pourrait être sérieuse dans le développement de réservoirs de stockage composites. « Ils s'intéressent aux réservoirs composites pour l'hydrogène, et nous avons travaillé avec eux », dit-il. « En général, les composites ne sont vraiment utilisés que pour les systèmes mobiles en raison de la quantité d'hydrogène nécessaire à l'autonomie du véhicule et de la volonté de réduire le poids pour étendre cette autonomie. Pour les applications stationnaires, il n'y a pas eu beaucoup d'intérêt pour une solution composites. Blois souligne également que la plupart des applications de stockage d'hydrogène stationnaire fonctionnent à des pressions plus basses. « Les réservoirs composites ont du sens si vous travaillez à 700 bars, mais pas si vous travaillez à des pressions allant jusqu'à 200 bars. Pour cela, vous pouvez utiliser un réservoir en métal."
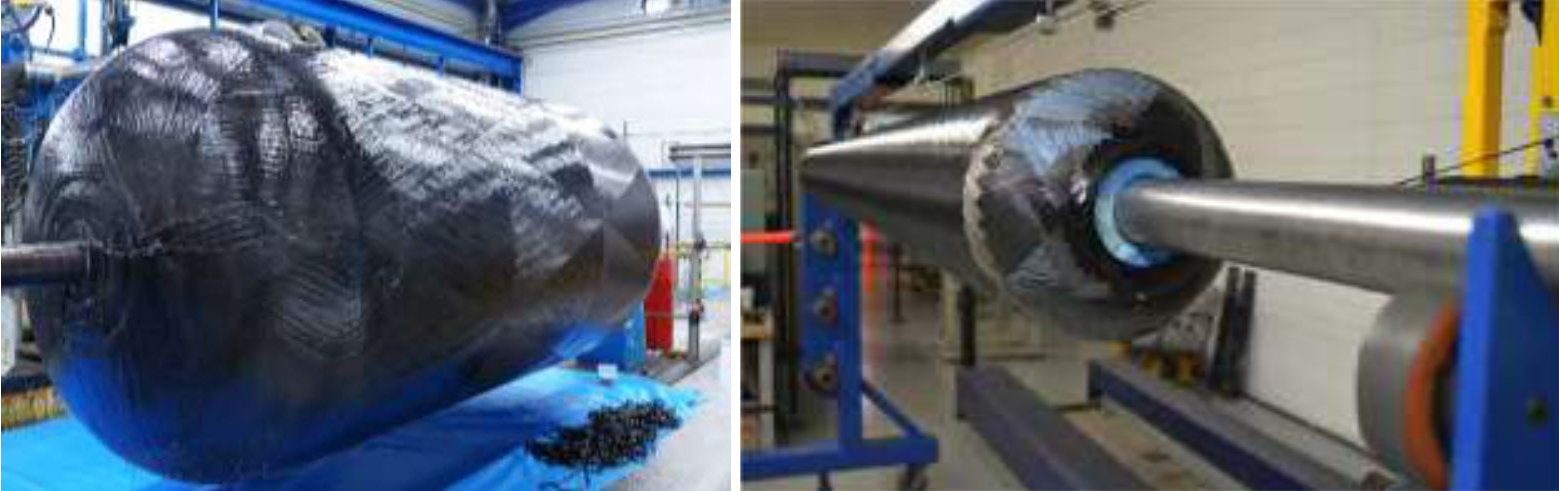
Les grands réservoirs peuvent-ils utiliser des pressions supérieures à 700 bars ? « Des pressions jusqu'à 1 000 bar peuvent être envisagées, précise Blois. « L'épaisseur des parois composites du réservoir est directement liée à la pression de service et au diamètre du réservoir. Actuellement, il existe une limite dans l'épaisseur de la paroi du réservoir au-delà de laquelle les performances des composites diminuent. »
Qu'en est-il de l'utilisation de l'hydrogène liquide plutôt que gazeux comprimé pour l'aviation ? « En raison de la grande quantité d'hydrogène nécessaire dans un avion, la densité plus élevée de gaz cryogénique est plus intéressante que le gaz comprimé », explique Blois. « Cependant, il est difficile de maintenir une température de 40°K à 80°K [-233°C à -193°C] dans des cuves aussi longtemps. Il faut encore travailler sur des solutions techniques. »
Est-il possible d'utiliser des composites thermoplastiques dans les réservoirs d'hydrogène ? « Pour la structure du navire dans les futurs réservoirs, mais pas pour aujourd'hui », précise Blois. « Pour les réservoirs de 700 bars à grande échelle aujourd'hui, il n'est pas efficace d'utiliser des composites thermoplastiques et d'atteindre les performances du navire-citerne. Cependant, la technologie des revêtements thermoplastiques (pour les réservoirs de type IV) est en effet la clé des performances du réservoir, et à l'avenir, un réservoir thermoplastique mondial pourrait être en mesure d'augmenter la recyclabilité et la durabilité. »
Où voyez-vous le marché des réservoirs de stockage d'hydrogène composites dans les cinq à dix prochaines années ? « Au cours des cinq premières années, nous pensons que les travaux se poursuivront sur les réservoirs de stockage d'hydrogène gazeux, et il nous reste encore beaucoup de travail à faire », déclare Blois. « Sachant que les premiers tests dans les avions sont maintenant effectués avec du stockage d'hydrogène gazeux, il faudra un certain temps pour développer la technologie nécessaire et atteindre la maturité sur le stockage d'hydrogène liquide, mais cela devrait être possible dans plusieurs années. »
Où STELIA Aerospace Composites continuera-t-il d'œuvrer pour faire progresser le stockage de l'hydrogène ? « Notre priorité est l'aéronautique et l'espace, précise Blois, mais nous sommes ouverts aux discussions et nous nous sentons très responsables d'aider à la transition vers le zéro émission. Nous sommes également en mesure de démarrer les opérations de production en série de réservoirs haute pression (700 bars) et de continuer à évaluer toutes les opportunités. »
Résine
- Alliage de stockage d'hydrogène titane-fer
- Les 10 principales avancées de la technologie de fabrication des composites
- Fabrication additive avec des composites dans l'aérospatiale et la défense
- La recherche AFRL fait progresser les composites CF/époxy imprimables en 3D
- L'université d'État de Wichita reçoit une subvention de 2 millions de dollars pour faire progresser les composites aérospatiaux
- Hexion présente une solution époxy à deux composants pour la production de composites aérospatiaux
- Le consortium des composites thermoplastiques vise une production à haut volume pour l'automobile et l'aérospatiale
- Composites hautes performances en Israël
- Point de mire sur l'aérospatiale :forage et fraisage de composites CFRP