Stratasys et Champion Motorsport s'associent pour tester la technologie de base imprimée en 3D
Le 27 juin, une Porsche GT2 RS Clubsport modifiée de Champion Motorsport (Pompano Beach, Floride, États-Unis) a terminé première de la division Time Attack 1 de la 99 e Pikes Peak International Hill Climb à Colorado Springs, Colorado, États-Unis
L'un des secrets du succès de l'équipe était les structures aérodynamiques de la voiture - les ailes, les virures de soubassement, le diffuseur et d'autres composants du véhicule qui déplacent l'air plus efficacement autour du véhicule pendant qu'il roule. Bon nombre de ces composants ont été imprimés en 3D par le partenaire Stratasys (Rehovet, Israël et Eden Prairie, Minnesota, États-Unis), y compris la première application réussie d'une nouvelle technologie de noyau sandwich enveloppé de fibre de carbone sans outil.
Prouvement des outils imprimés en 3D et des technologies de base
Champion Motorsport est client de Stratasys depuis plusieurs années, « mais le partenariat est devenu bien plus qu'une relation fournisseur/client typique », déclare Allen Kreemer, ingénieur d'applications stratégiques senior chez Stratasys. Par exemple, Stratasys et Champion ont déjà travaillé ensemble pour tester une nouvelle technique que Stratasys avait développée pour l'impression 3D d'outillage soluble. Avec cette technologie, un noyau en plastique soluble façonné pour un conduit ou une autre pièce en forme de tube est imprimé puis enveloppé d'un préimprégné de fibre de carbone. À l'aide d'un réservoir d'élimination de support soluble, l'outillage imprimé se dissout, laissant un conduit composite creux, fini et sans soudure.
"C'était vraiment le début de notre partenariat avec Champion Motorsport, où nous avons travaillé ensemble pour créer ce conduit en fibre de carbone très compliqué et sans couture d'une manière non traditionnelle, sans limites comme dans l'usinage ou le moulage CNC", a déclaré Patrick Carey, vice-président senior. – Amériques, produits et solutions chez Stratasys.
En 2019, les entreprises ont décidé de s'associer sur un projet pour tester une nouvelle itération de la même technologie :un noyau enveloppé de fibre de carbone imprimé en 3D qui n'est pas se dissoudre dans l'eau, c'est à la place un noyau structurel pour la pièce finie ou le prototype.
Kreemer explique que pour les composants sandwich, travailler avec et façonner des matériaux d'âme - qu'il s'agisse d'un nid d'abeille en aluminium flexible, d'une mousse structurelle rigide ou autre - peut être difficile et coûteux, nécessitant un façonnage ou un usinage puis un moulage avec les peaux composites en fibre de carbone dans un moule dédié. Stratasys imprime un noyau en nid d'abeille rigide à l'aide de plastique haute température SABIC (Riyad, Arabie saoudite) Ultem 1010. « Nous imprimons la forme exacte pour s'adapter à la voiture, puis nous l'enveloppons simplement avec de la fibre de carbone, le sac et le durcissement, sans utiliser de moule », explique Kreemer. "Nous avons commencé avec les noyaux solubles, que nos clients utilisent toujours, et maintenant nous sommes passés à ces noyaux sandwich, qui auront de larges applications dans l'aérospatiale et l'automobile."
"Nous l'appelons" sans outil ", et c'est vraiment la clé", ajoute Carey. « Nous avons créé cette application pour ignorer tout le processus de construction du moule, puis de mise en place dans le moule. » Il note que l'élimination de l'outillage permet également de modifier facilement la forme selon les besoins.
Aérodynamique primée imprimée en 3D
Pour le projet Champion Motorsport, trois technologies différentes sont entrées dans les 16 pièces aérodynamiques totales que Stratasys a construites pour le prototypage ou l'installation finale sur le véhicule de course, explique Carey. « Nous avons imprimé les noyaux Ultem 1010 [enrobés de fibre de carbone], nous avons imprimé en 3D certaines pièces en utilisant du nylon 12 chargé de fibres de carbone et nous avons imprimé des pièces en utilisant du nylon 6 lorsque la flexibilité et la résistance aux chocs étaient nécessaires. »
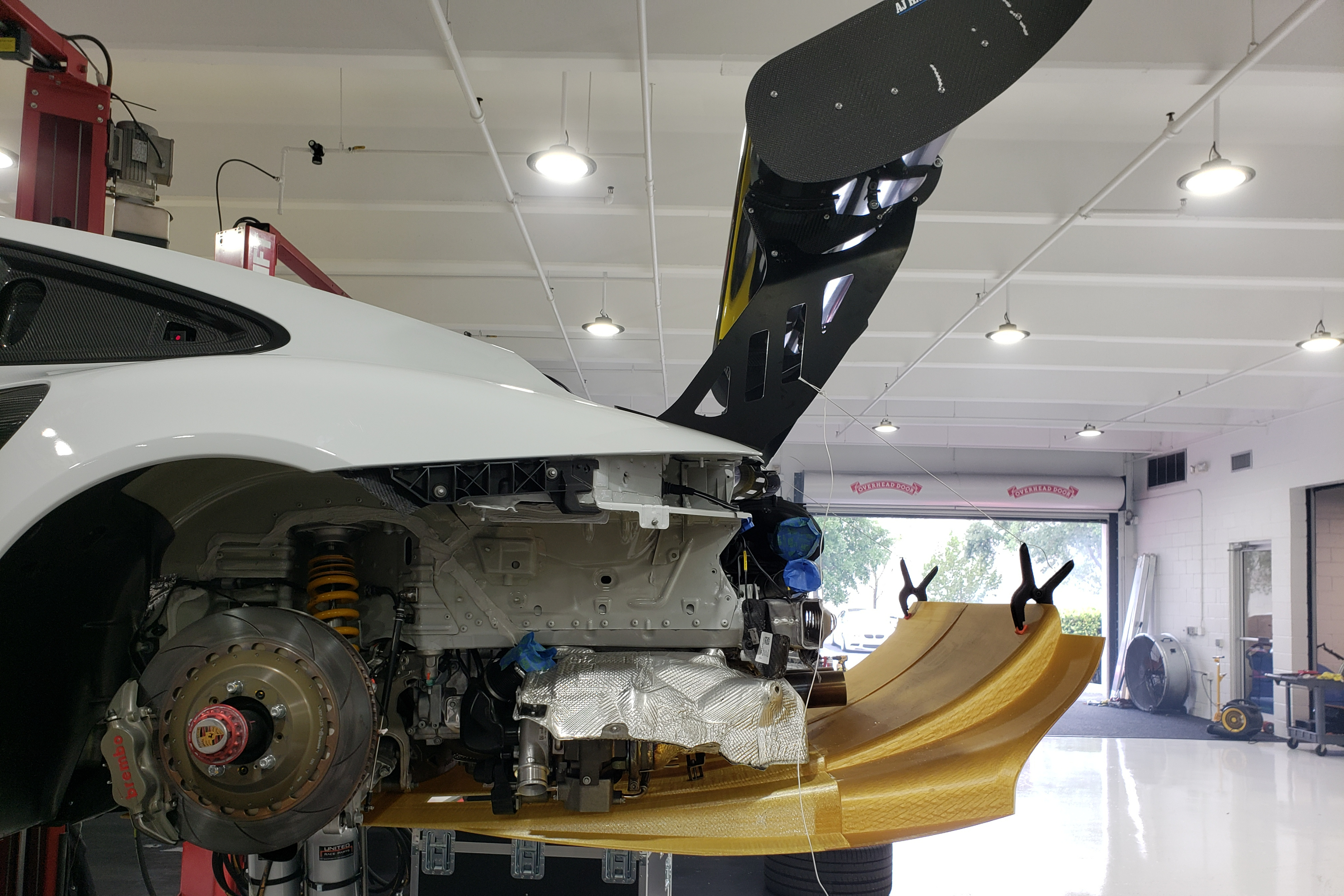
La plus grande partie était une pièce prototype de diffuseur arrière de 7 pieds de long et 5 pieds de large qui a été construite pour tester la conception finale de la pièce. Il a été imprimé en sept pièces sur une imprimante Stratasys de modélisation par dépôt de fusion (FDM) F900 utilisant un polymère polyétherimide (PEI) Ultem 1010, collé ensemble, enveloppé dans un préimprégné de fibre de carbone, ensaché et durci au four. Le délai d'exécution de la pièce était d'environ cinq jours pour l'impression et d'un peu plus de 24 heures pour le drapage et le durcissement :"C'était extrêmement rapide, et ce dont nous avions besoin à l'époque", note Chris Lyew, ingénieur en mécanique chez Champion Motorsport.
Causé par l'incertitude quant à la possibilité d'organiser des événements en personne cet été en raison de COVID-19, "le projet a été mis en ligne à la dernière minute et de nombreux systèmes devaient être traités en même temps", explique Lyew. "L'aérodynamique est l'un d'entre eux, et c'est normalement un processus très long" de conception, de test et d'itération des composants, dit-il. Les méthodes conventionnelles nécessiteraient la création d'un outillage, la pose à la main sur le moule et la découpe et l'ajustement du noyau. "Sans ce processus, nous n'aurions pas pu atteindre nos dates cibles pour tester la voiture sur la piste", déclare Lyew.
Le séparateur avant de la voiture a également été prototypé et testé de la même manière. Pour les pièces qui étaient des prototypes, les pièces de production finales ont été réalisées avec un outillage traditionnel, mais la pièce prototype a été utilisée comme modèle pour tester différentes itérations. Carey note : « Avec un processus sans outil, nous pouvons itérer plus rapidement, le tester, puis itérer plus rapidement, le tester. Avec les outils traditionnels, vous ne pourriez jamais itérer, vous n'en faites qu'un et vous êtes coincé avec. Ici, nous pouvons faire une vraie pièce, la tester et en tirer des leçons."
Un certain nombre de pièces de production plus petites ont également été produites par Stratasys. Par exemple, les ailettes de chaque côté du pare-chocs avant de la voiture ont été imprimées à partir de nylon 12 chargé à 35 % de fibres de carbone, les jupes latérales du véhicule ont également été imprimées en Ultem 1010 avec un remplissage interne en nid d'abeille, puis recouvertes de fibre de carbone.
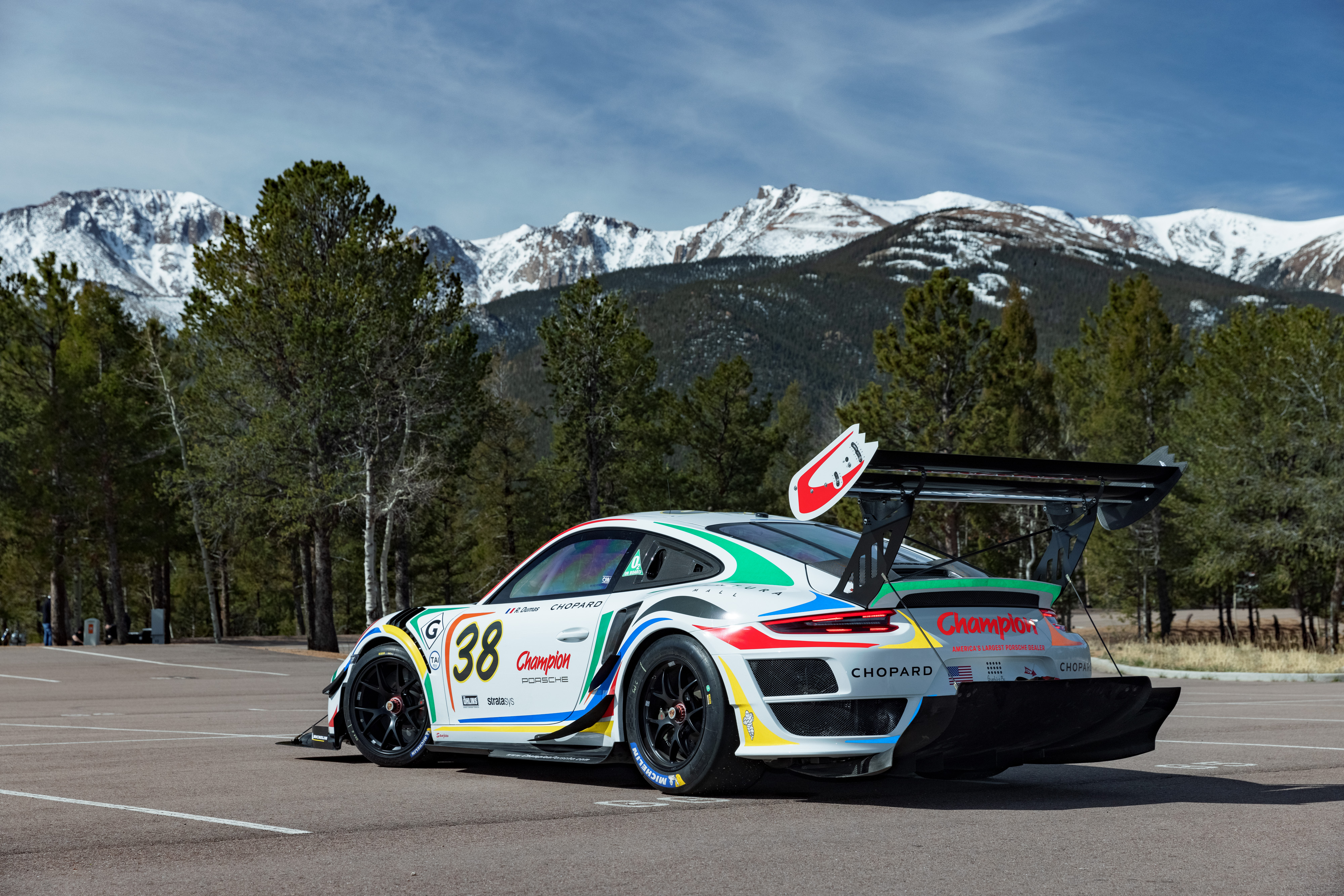
La plupart des "tranches" aérodynamiques de la voiture - de petites pièces en forme d'ailettes qui se boulonnent à l'extérieur du véhicule à des points stratégiques pour aider à contrôler le flux d'air autour du véhicule - ont également été imprimées à partir de nylon 12 chargé de fibres de carbone ou de nylon 6 non renforcé. les pièces sont conçues pour être facilement repensées ou remplacées au besoin en raison de dommages ou d'usure. "À Pikes Peak, il y a pas mal de caractéristiques de terrain accidenté qui pourraient potentiellement causer des dommages, donc la capacité de remplacer [les virures] facilement était la clé pour nous", ajoute Lyew. Plusieurs ensembles de rechange ont également été imprimés et livrés pour un remplacement facile pendant la course au besoin.
Au-delà de Pikes Peak
Pikes Peak s'est avéré être une course idéale pour tester cette technologie, explique Kreemer, en raison de l'environnement unique spécifique à cet événement, qui se déroule à 14 000 pieds d'altitude au point le plus élevé. "Toutes les voitures de course utilisent l'appui pour pousser la voiture sur la piste pour gagner en traction, mais ces voitures particulières sur Pikes Peak ne ressemblent à aucune autre forme de sport automobile dans le monde, car elles ont besoin d'effets aérodynamiques vraiment exagérés pour maintenir les voitures sur la piste [ à cette altitude]. Le résultat est des ailes plus grandes et d'autres composants aérodynamiques que ceux qui seraient utilisés sur n'importe quel autre type de voiture de course.
À l'avenir, Stratasys prévoit de présenter sa technologie de base imprimée sans outil à d'autres sociétés de course pour des pièces aérodynamiques similaires. Carey dit qu'il existe à l'avenir de nombreuses autres applications potentielles dans les pièces automobiles à faible volume, la marine de plaisance ou même l'aérospatiale intérieure. « Toute application nécessitant une itération ou une conception personnalisée, nous pensons pouvoir y ajouter de la valeur », dit-il.
Résine
- Matériaux :technologie de production en nid d'abeille léger au K 2019
- Evonik établit un nouveau centre de technologie d'impression 3D aux États-Unis
- Nouvelle forme de matériel imprimé en 3D visant à des conceptions de voitures plus légères et plus sûres et plus encore
- Comment garantir la sécurité de la technologie de pointe ADAS
- Technologie de production de panneaux en nid d'abeille thermoplastique EconCore
- Composite + métal :technologie hybride à profil creux
- Un joueur hautement spécialisé dans une équipe de classe mondiale
- Technologie de mouvement linéaire
- Arno Strotgen