Le prototype de boîtier d'airbag met les composites imprimés en 3D à l'épreuve
Depuis plus d'un siècle, Joyson Safety Systems (Auburn Hills, Michigan, États-Unis) est impliquée dans la conception, la fabrication et la vente de composants de sécurité pour divers marchés, notamment les airbags, les ceintures de sécurité, les volants et l'électronique de sécurité pour l'automobile. l'industrie.
L'entreprise a récemment mené une étude de faisabilité pour explorer le potentiel d'autres matériaux et processus existants pour améliorer des produits tels que son conteneur de boîtier d'airbag conducteur (DAB), menant à une preuve de concept qui a tiré parti de la fabrication additive composite.
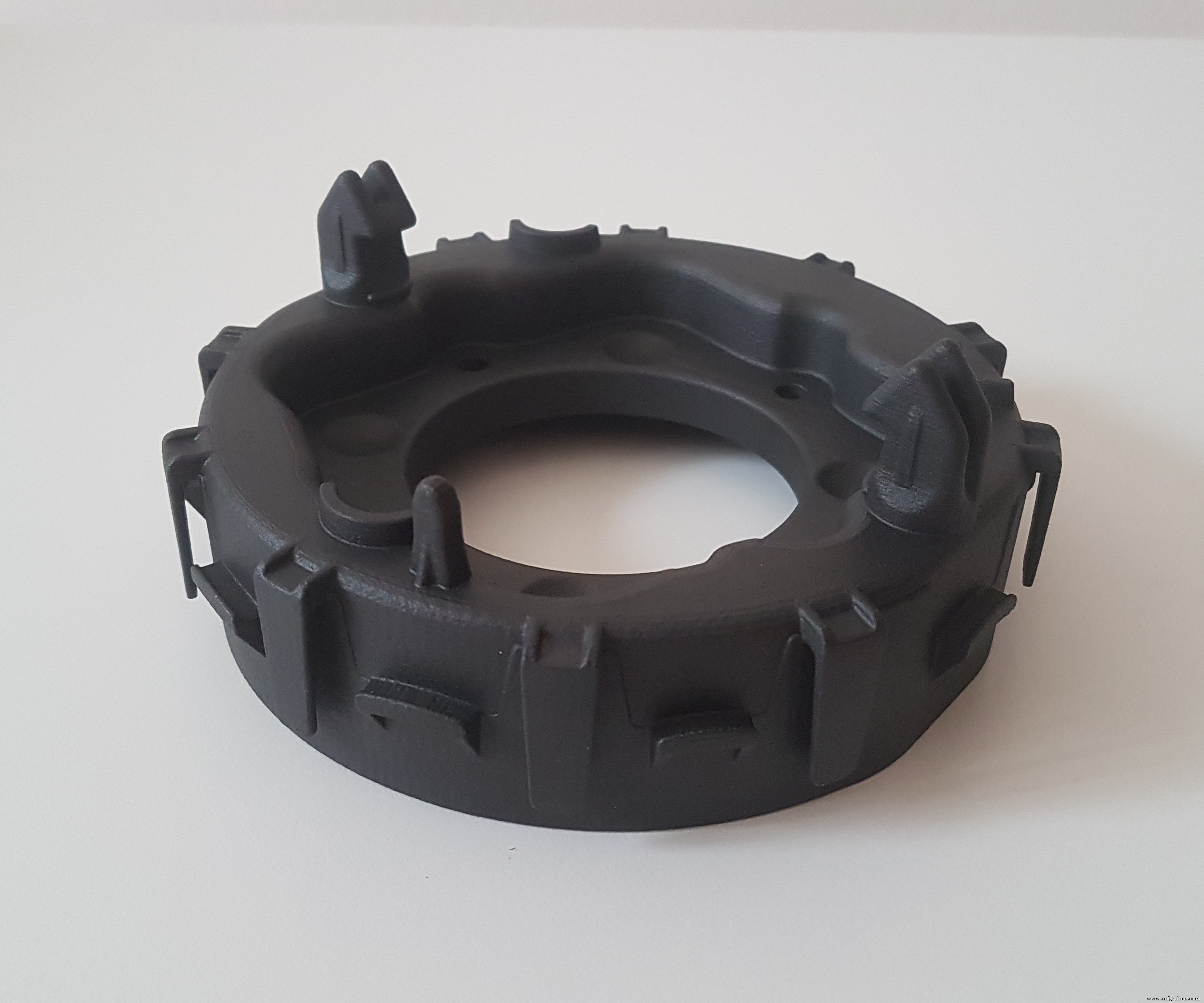
Un système d'airbag complet se compose d'un gonfleur, d'un coussin d'airbag, d'une housse et d'un boîtier avec des points de fixation au volant. Le coussin d'airbag lui-même est situé dans l'espace du boîtier et du couvercle.
La performance de la partie boîtier DAB est critique. En plus de maintenir l'ensemble du système d'airbag en place pendant que le véhicule est en mouvement, la pièce doit également être capable de résister aux forces appliquées au système d'airbag lorsque l'airbag est déployé. Pour les tests, le matériau utilisé pour la pièce devait avoir une résistance, une résistance aux chocs et une stabilité thermique suffisantes dans une plage de températures de -35 °C à +85 °C.
Le conteneur d'origine a été fabriqué via un procédé de moulage par injection conventionnel, et a été fabriqué à partir de polyamide (PA) renforcé avec 40 % de fibre de verre. Pour l'étude de faisabilité, l'équipe Joyson Safety Systems visait à produire rapidement une pièce prototype fonctionnelle en quelques jours, et ils voulaient trouver un matériau qui présentait des propriétés mécaniques, thermiques et de performance similaires aux matériaux d'origine.
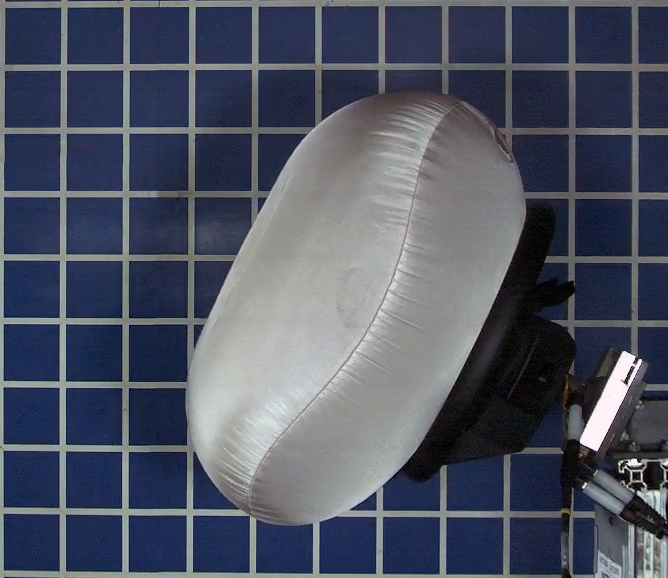
L'équipe Innovations de Joyson a réalisé une analyse de marché afin de trouver des matériaux adaptés, et s'est finalement tournée vers CRP Technology (Modène, Italie) pour sa gamme Windform TOP-LINE de matériaux composites hautes performances et son service d'impression 3D en interne.
Plus précisément, l'équipe a choisi le matériau en fibre de carbone/PA Windform SP de CRP, qui présente des propriétés encore plus élevées que les matériaux précédents qu'ils utilisaient pour la pièce. Les pièces seraient fabriquées avec un procédé de fabrication additive de frittage laser (SLS) sélectionné.
L'équipe a pu produire rapidement un prototype de pièce et la tester dans un module d'airbag complet, démontrant la haute résistance et la résistance aux chocs de la pièce repensée, ainsi que sa stabilité thermique dans une plage de températures. Par rapport au processus de moulage par injection d'origine, la nouvelle pièce pourrait également être produite plus rapidement à l'aide de SLS et éliminer le besoin d'un outillage coûteux.
"Cette opportunité a ouvert une variété de capacités et de considérations pour une coopération plus poussée avec CRP Technology", déclare Samer Ziadeh, ingénieur de développement au sein de l'équipe Core Engineering Materials chez Joyson Safety Systems.
fibre
- Hymne au prototype
- La question de la maintenance du contrat – Partie I
- Le développement de matériaux composites légers dans l'industrie médicale
- Un guide pour comprendre le processus de fabrication des composites
- Quel est l'avenir des composites dans l'industrie des articles de sport ?
- Plongée dans les applications des composites aérospatiaux
- 3 raisons pour lesquelles l'industrie maritime tire profit des composites
- Nèos International établit un nouveau siège, une usine de composites au Royaume-Uni
- La valeur du moulage de précision (Partie 2)