Outillage personnalisé, aide à maintenir les rotors en forme
En développant un processus d'usinage plus précis pour l'accouplement rotors hélicoïdaux, les modèles de suralimentation de ce Whipple Supercharger peuvent forcer plus efficacement l'air dans un moteur pour des gains de puissance plus élevés. Des outils de serrage et de formage personnalisés permettent à l'entreprise de fraiser avec précision des rotors de suralimentation en une seule configuration sur son tournage-fraisage sur l'axe B.
Fondée par l'ancien chef d'équipe de course et propriétaire de voiture Art Whipple en 1987, Fresno's Whipple Superchargers fabrique des compresseurs à double vis pour les coureurs automobiles et marins, et d'autres qui cherchent à améliorer les performances de leur moteur. Ces types d '«additionneurs de puissance» (les turbocompresseurs et l'oxyde nitreux en sont d'autres) introduisent de l'air supplémentaire dans un moteur au-delà de ce que le moteur peut tirer par lui-même. Plus d'air signifie que plus de carburant peut être ajouté, ce qui augmente essentiellement la cylindrée d'un moteur ainsi que sa puissance.
La clé ici est l'engrènement précis et sans contact de deux rotors hélicoïdaux à l'intérieur du boîtier du compresseur. Avec la conception Whipple, le rotor mâle a trois lobes hélicoïdaux et la femelle en a quatre, explique le concepteur de Supercharger Garrett Bright. Ceux-ci tournent l'un contre l'autre et extrêmement étroitement. Au fur et à mesure que les lobes de chacun passent devant les orifices d'entrée d'air, l'air est emprisonné entre les rotors et le boîtier. La rotation du rotor réduit progressivement l'espace occupé par l'air en le comprimant. La compression se poursuit jusqu'à ce que l'espace du lobe interne soit exposé à un orifice de sortie, à travers lequel l'air est évacué à une pression supérieure à la pression atmosphérique dans le collecteur d'admission qui se trouve au sommet du moteur.
L'efficacité du compresseur dépend de l'efficacité de l'étanchéité entre les rotors correspondants et le carter. Auparavant, Whipple n'utilisait que des rotors fabriqués et fournis par une société extérieure. Il utilise toujours ces rotors fournis pour certains de ses modèles de compresseur. Cependant, la société a depuis commencé à concevoir et à usiner ses propres rotors en interne, et le processus d'usinage qu'elle a développé produit des rotors plus cylindriques et précis que ceux fournis par son fournisseur, ce qui se traduit par des conceptions de compresseurs 5% plus efficaces que celles en utilisant les rotors fournis.
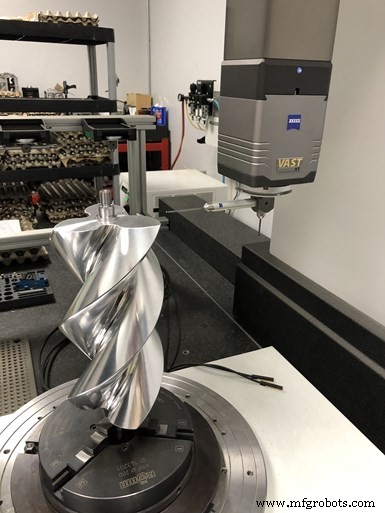
Les mesures prises sur ce CMM ont permis à Whipple de déterminer la précision de ses rotors fournis et des rotors des machines en interne. Son objectif est d'obtenir un jeu de 125 microns entre les rotors correspondants, ce qu'il peut désormais réaliser grâce à ses capacités d'usinage multitâches internes.
Bright explique que Whipple a été incité à usiner ses propres rotors après avoir vu les résultats des mesures des rotors de son fournisseur prises sur sa machine de mesure de coordonnées (MMT) Zeiss Accura. Cette MMT comprend une table rotative ainsi que la technologie de balayage Vast de Zeiss et l'option Gear Pro dans son logiciel de mesure Calypso. Bright dit que ce logiciel est particulièrement efficace pour mesurer les rotors d'accouplement car il peut attribuer des points de contrôle spécifiques sur les profils hélicoïdaux des rotors mâle et femelle où ils se rencontrent pour déterminer le jeu entre les deux à ces points. Il a déterminé que le profil de chaque rotor devait être de ± 63 microns dans le but d'obtenir un jeu d'environ 125 microns. Whipple n'obtenait pas cela de son fournisseur de rotor.
Apporter l'usinage en interne
Le processus interne d'usinage du rotor de l'entreprise à l'aide d'outils de forme est similaire à celui de son fournisseur, mais avec des modifications de serrage pour augmenter la rigidité.
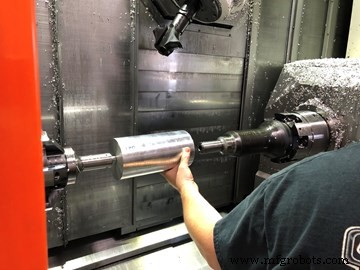
Lorsqu'un opérateur charge une ébauche de rotor en aluminium 6061 dans le tournage-fraisage, la broche principale de la machine puis la contre-broche serrent les tourillons en acier saillants de l'arbre.
La machine qu'elle a achetée il y a quelques années pour cette application est une fraiseuse-fraiseuse Mazak Integrex e-420H-S II avec tête de fraisage à axe B. En fait, ce tournage-fraisage n'effectue aucun tournage.
Les ébauches de rotor cylindriques en aluminium 6061 sont d'abord percées au centre longitudinalement sur une autre machine pour permettre d'y enfoncer un arbre en acier. Lorsqu'un opérateur charge une ébauche dans l'Integrex, la broche principale de la machine, puis la sous-broche, serrent les tourillons saillants de l'arbre. Ensuite, l'axe B de la machine est considérablement incliné pour orienter un outil de forme personnalisé qui correspond au profil de goujure de rotor souhaité lorsqu'il se trouve à cet angle. Enfin, l'outil de forme tournante est déplacé le long de l'axe Z pendant que le rotor tourne lentement pour créer chaque flûte en plusieurs passes.
Initialement, Whipple utilisait des pinces ER allongées de style pullback pour serrer les tourillons de l'arbre. La longueur étendue était nécessaire pour éloigner les ébauches de la sous-broche afin de fournir un dégagement suffisant pour que la broche de l'axe B s'incline aussi loin sur le mandrin de la sous-broche que nécessaire pour accueillir l'outil de forme. Cependant, la fonctionnalité de retrait de ces pinces rendait le chargement des ébauches de rotor long et difficile. Le serrage de la pince (entraînant un recul) a exercé une charge excessive sur la broche principale, ce qui signifie que la sous-broche de l'axe W a dû être enfoncée pour aider à composer la charge. Sinon, des vibrations ou des finitions de surface médiocres pourraient en résulter. En conséquence, les opérateurs serraient et resserraient continuellement jusqu'à ce que la majeure partie de la charge soit éliminée, ce qui prenait généralement 10 minutes. De plus, Whipple remplaçait constamment les pinces en raison de l'usure qu'ils subissaient en serrant et desserrant tant de fois.
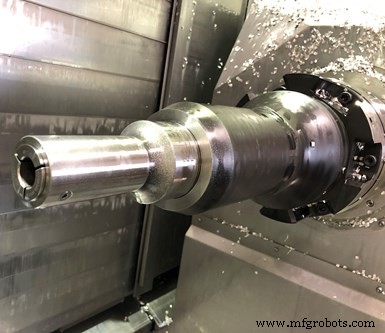
Contrairement aux pinces ER utilisées précédemment, dead- les pinces de longueur ne tirent pas sur les pièces et n'exercent pas de charge sur la broche principale qui devrait être éliminée. Cela a réduit les configurations de 10 à deux minutes.
Sur les conseils de Kellen Bush, l'ingénieur d'application de Mazak qui a travaillé avec Whipple sur ce projet, la société a contacté Hainbuch pour concevoir une approche alternative de serrage. Le directeur des ventes de Hainbuch, Tom Chambers, explique que la solution de serrage personnalisée de l'entreprise offre non seulement la portée étendue requise pour permettre à l'axe B de la machine de s'incliner à l'angle requis sans interférence, mais elle offre également une plus grande rigidité tout en simplifiant les changements. Ceci est possible en grande partie parce que des pinces de longueur morte sont utilisées à la place des types de retrait. Chambers dit que les pinces de longueur morte "serrent dans l'espace", ce qui signifie que les ébauches de rotor ne bougeront pas lorsque les pinces seront serrées. Par conséquent, aucune charge supplémentaire qui devrait être réglée n'est appliquée à la broche principale. Les changements ne prennent désormais que deux minutes.
Les outils de formage Kyocera Unimerco que Whipple utilise pour usiner ses rotors (tout comme le fournisseur de rotors de Whipple) ne sont en fait pas couramment utilisés pour couper le métal. Anders Varga, directeur des ventes chez Kyocera Unimerco, explique que ce type d'outil est généralement utilisé pour couper du bois, des composites et d'autres matériaux fibreux. Cela est principalement dû à la quantité de pression qui serait exercée sur l'outil en raison de la zone de contact élevée entre une pièce métallique et les longues arêtes de coupe de la plaquette. Le fait que ces outils puissent être utilisés dans cette application d'usinage de rotor témoigne de la rigidité de la machine avec interface de broche Capto et de son serrage personnalisé.
L'utilisation d'outils de forme qui correspondent au profil de cannelure hélicoïdale des rotors (profils que Bright a raffinés) élimine le polissage qui pourrait être nécessaire si plusieurs fraises en bout étaient utilisées pour tailler les cannelures. Les rotors sont usinés de sorte que leurs lobes soient aussi grands que possible, mais légèrement sous-dimensionnés pour permettre un revêtement exclusif ultérieur. Whipple conserve généralement deux outils d'ébauche et trois outils de finition à portée de main pour les rotors mâles et femelles. Les outils utilisent des plaquettes en carbure micro-grain non revêtues. Les inserts pour les outils d'ébauche sont fixés aux corps d'outils par des vis; les outils de finition y sont brasés.
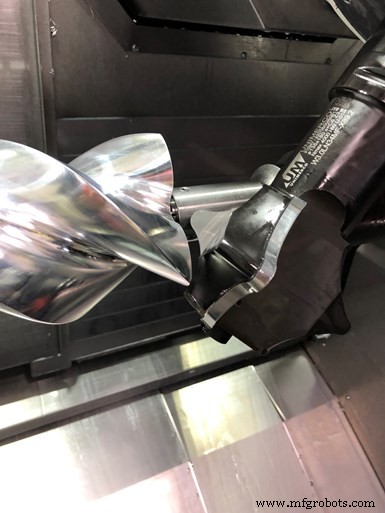
En utilisant des outils de formulaire, Whipple n'a pas pour effectuer la finition secondaire comme si elle utilisait des fraises en bout pour créer les cannelures du rotor.
Désormais, non seulement ce processus d'usinage atteint l'objectif de dégagement de 125 microns de Bright entre les rotors accouplés, mais la cylindricité du rotor de bout en bout est plus cohérente. Il dit qu'avec l'approche de serrage originale, la différence de cylindricité d'une extrémité d'un rotor par rapport à l'autre peut atteindre 10 microns. Cela a été réduit à 1 micron. Les temps de cycle du rotor sont également un peu plus rapides. Les temps de cycle pour un rotor mâle sont de 14 minutes et un rotor femelle prend 20 minutes. Mais, pour Whipple, c'est de la sauce. Ses principaux objectifs étaient d'obtenir une plus grande précision d'usinage du rotor et des changements de vitesse plus rapides, ce qu'il a réalisé.
Équipement industriel
- Mecademic Robotics se développe sur d'énormes marchés avec son petit robot
- Schilling Robotics va intégrer le logiciel Energid dans son robot sous-marin Gemini
- Service d'outillage rapide et ses applications efficaces
- Comment l'outillage imprimé en 3D peut façonner l'avenir du prototypage
- Outillage pour machines de type suisse
- Faire tourner les trucs difficiles
- Établir des connexions Lean
- Vous songez à vous lancer dans l'outillage en direct ? Voici ce que vous devez savoir
- 5 avantages clés de la fabrication en métal sur mesure