L'atelier s'améliore continuellement en adoptant des machines à transfert rotatif
Les ateliers d'usinage les plus performants sont ceux qui s'efforcent toujours de s'améliorer. C'est pourquoi les entreprises recherchent la meilleure technologie et s'efforcent de l'utiliser de la manière la plus efficace. Le fondateur d'American Turned Products (ATP) était dédié à l'amélioration, un état d'esprit qu'il a inculqué à la culture de l'entreprise. Cela a bien servi l'entreprise, l'amenant à passer d'un atelier d'usinage de vis à une entreprise qui utilise principalement des machines à transfert rotatif, se développant et s'étendant sur de nouveaux marchés en cours de route.

Jeff Prescott, technicien Hydromat, utilise deux machines Hydromat qui produisent la même pièce. Les deux sont des machines à 16 stations avec des unités de broches d'outils verticales et des robots Fanuc avec des ébauches alimentées par trémie.
Un héritage d'usinage
ATP a ses racines dans Eighmy Corp., qui a été fondée en 1956 par Harry Eighmy, un machiniste de métier. L'entreprise s'est implantée à Conneaut, Ohio, usinant des pièces simples pour l'industrie automobile. Elle exploitait des machines multibroches, fabriquait ses propres outils, effectuait des rectifications OD et ID et entreprenait la construction d'assemblages.
Le fils de Harry, Gerald B. "Jerry" Eighmy, diplômé de Conneaut High School, est allé travailler sur les bateaux minéraliers pour US Steel afin de rassembler l'argent dont il avait besoin pour l'université. Il a fréquenté le Heidelberg College, obtenant un diplôme en chimie. Peu de temps après avoir obtenu son diplôme, Jerry a commencé à travailler pour son père dans l'entreprise familiale d'usinage.
Après plusieurs décennies d'exploitation, Eighmy Corp. a décroché un nouveau contrat pour un projet d'arbre de ceinture de sécurité et a acheté trois Davenports. Cependant, les pièces nécessitaient un traitement thermique et un placage, qui à l'époque n'étaient pas disponibles à Conneaut. La ville la plus proche pour ces services était Erie, en Pennsylvanie. Ainsi, en 1984, Jerry a fondé American Turned Products à Erie. Il s'agissait d'une décision stratégique visant à réduire les délais de la chaîne d'approvisionnement et à consolider les partenariats avec les fournisseurs. Il a également créé une usine de fabrication de niche distincte avec tous les Davenports produisant des travaux automobiles. L'entreprise a finalement commencé à ajouter des machines et des services au fur et à mesure que de nouvelles opportunités se présentaient.
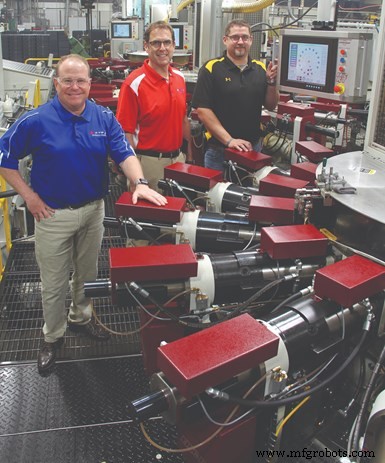
Le copropriétaire et directeur de l'exploitation d'ATP, Harry Eighmy (à gauche, photographié avec le vice-président des relations avec la clientèle Drew Hoffman et le directeur de l'ingénierie Nick Adams), ainsi que son frère, copropriétaire et PDG Scott Eighmy, s'efforcent de diversifier le travail de l'entreprise.
Pendant son séjour dans l'industrie de l'usinage, Jerry s'est fortement impliqué dans la National Screw Machine Products Association (NSMPA), maintenant connue sous le nom de Precision Machined Products Association (PMPA). Jerry a siégé à de nombreux comités, ainsi qu'au conseil d'administration et en tant que président de l'association. Il a également reçu le prix du mérite, la plus haute distinction de l'association, pour son service à l'association et à l'industrie. Il est décédé en 2018 après une longue maladie, laissant les rênes à ses deux fils :Scott Eighmy, copropriétaire et PDG, et Harry Eighmy, copropriétaire et COO.
Amélioration continue
Parmi ses employés, Jerry était connu pour son dévouement aux principes d'amélioration continue et a toujours voulu disposer de données pour étayer ses recherches. "Il avait tous ces cahiers triés par machine et par travail, empilés dans son bureau", explique Nick Adams, responsable de l'ingénierie chez ATP. "Lorsqu'un point était débattu au sein de la famille, il en tirait un du bas d'une pile, tournait la page et disait :"Nick, regarde ça".
Cet accent mis sur l'amélioration a entraîné d'autres changements au sein de l'entreprise, notamment la mise en œuvre de la fabrication au plus juste il y a quatre ans. Ces principes, énoncés dans des livres tels que Two Second Lean de Paul A. Akers , comprennent la formation et la mise en œuvre de l'amélioration des processus 3S Lean (trier, balayer et standardiser). Selon les employés, ces changements ont contribué à améliorer les relations de travail entre les travailleurs de la production, l'ingénierie et la direction. "C'est facile de dire que c'est la responsabilité de quelqu'un d'autre. Nous encourageons chaque employé à changer ce qui les dérange », explique M. Adams. "Ensuite, nous documentons le problème, avant et après, les étapes pour le résoudre, et nous montrons comment il a été résolu en vidéo." Ces améliorations sont jugées pour recevoir des récompenses mensuelles. Certains sont petits, comme le nettoyage d'un poste de travail, et d'autres sont de grandes idées, comme la révision de toute la zone d'expédition. "Cela donne aux employés la propriété de leur travail quotidien et le pouvoir d'apporter des changements pour que le moral remonte", ajoute-t-il, "et arrête de pointer du doigt, et nous travaillons tous mieux en équipe."
Développer l'entreprise
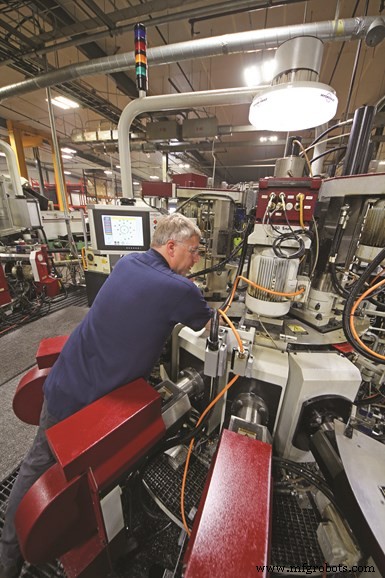
Jeff Prescott change un outil sur une machine Hydromat Epic R/T avec plusieurs unités verticales et des brides CNC à trois axes sur les broches d'outils horizontales. ATP a obtenu sa première machine à transfert rotatif Hydromat en 1989, et elle est depuis devenue la méthode de référence de l'entreprise pour la production de pièces tournées.
L'usine d'Erie de 50 000 pieds carrés d'ATP abrite actuellement trois machines Hydromat, ainsi que des machines CNC multibroches, des CNC bibroches et des tours CNC suisses monobroches qui produisent principalement des pièces automobiles et hydrauliques.
Lorsque le moment est venu pour les Eighmys de choisir entre s'agrandir à Erie ou construire une deuxième installation ailleurs, ils ont choisi ce dernier. La nouvelle usine de 45 000 pieds carrés à Fairview, en Pennsylvanie, à 15 miles sur la route d'Erie, a été créée en 1998. L'usine de Fairview, qui sert de siège social à l'entreprise, est principalement une installation de transfert rotatif avec six machines Hydromat en production et un de plus dans le processus de construction au siège social d'Hydromat à St. Louis, Missouri. Il abrite également des perceuses, des centres de tournage Emag et des tours Shimada-Kitako, et effectue certains processus secondaires tels que le meulage CNC, la finition des alésages et l'ébavurage thermique.
Pourquoi construire à Fairview plutôt qu'agrandir l'usine d'Erie? "Nous pensions qu'il serait plus facile de gérer une installation de 100 à 150 personnes plutôt qu'une seule usine énorme", déclare Harry Eighthmy. "Nous voulions construire une culture plus forte au sein de deux installations." Il admet que le modèle à deux usines a des inconvénients; il est plus coûteux d'exploiter deux installations et nécessite deux de tout. Mais Harry suggère que bien qu'il y ait des dépenses supplémentaires pour faire fonctionner deux installations, il peut également réaliser certaines économies d'échelle.
En 1990, ATP a ouvert une usine de Davenport à El Paso, au Texas, pour les travaux automobiles. "Cette usine desservait les maquiladoras au Mexique en fournissant des pièces de ceintures de sécurité et d'airbags", explique Harry. "Nos clients avaient des usines au Mexique, donc pour éviter les frais de transport d'Erie jusqu'à Tijuana, Juarez, Reynosa et Monterrey, il était logique de localiser une usine au Texas." En 2006, l'usine d'El Paso a été vendue à Arrow Manufacturing, aujourd'hui Metal Seal Corp., permettant à Harry de rentrer chez lui pour se concentrer sur ses deux usines en Pennsylvanie.
La perturbation stimule l'innovation

Le technicien Hydromat Ron Mourton vérifie la précision des pièces. Entre 60 % et 70 % des revenus d'ATP sont générés sur les machines Hydromat en raison de leur capacité à fabriquer rapidement de grandes quantités de pièces de haute qualité.
ATP était principalement une maison de machines à vis Davenport et Acme pendant de nombreuses années, mais son ouverture à l'amélioration l'a finalement amené à changer sa vision de l'usinage de production. "Nous faisions un grand programme pour GE Home and Laundry Division et avons eu l'opportunité de produire beaucoup plus de ce programme," dit Harry. En raison de cette opportunité, l'entreprise cherchait de nouvelles façons de produire rapidement de grandes quantités de pièces de haute qualité. "Je connaissais des membres de la NSMPA (PMPA) qui avaient des Hydromats et qui en étaient très satisfaits", dit-il. Les Eighmys étaient intrigués par la machine Hydromat et la possibilité qu'elle puisse répondre aux besoins de l'entreprise.
En 1989, ATP a investi dans deux anciennes machines Hydromat 25-12. Il a rapidement constaté que ses calculs étaient corrects :les machines à transfert rotatif pouvaient fabriquer plus rapidement des pièces de haute qualité, produisant de plus grandes quantités. Par exemple, ATP fabriquait auparavant l'arbre de ceinture de sécurité spécialisé sur ses Davenports. "Nous avons équipé un Hydromat pour ces tiges de ceinture de sécurité, et nous avons pu réduire de moitié le temps de cycle en utilisant l'Hydromat par rapport au Davenport", déclare Harry. L'entreprise n'a pas regardé en arrière, et depuis lors, les Hydromats sont la machine incontournable pour la production de pièces tournées.
Deux ans après l'arrivée des premières machines, ATP a acheté une autre machine Hydromat, cette fois une 45-12. Ils ont découvert que ce nouvel ajout pouvait rendre la pièce d'arbre encore plus rapide et en plus grande quantité. Avec du temps libre sur les machines d'origine, l'entreprise a équipé l'un des 25-12 pour une pièce d'airbag automobile. Cela s'est avéré être un marché lucratif. "Dans les années 1990, les composants d'airbags sont devenus un énorme marché pour des voitures plus sûres", explique Harry. "Le public réclamait un véhicule plus sûr, et le nombre d'airbags par véhicule ne ferait qu'augmenter. Nous sommes entrés sur ce marché très tôt, et il s'agissait d'une fabrication de niche, nous avons donc pris pied dans le secteur des pièces d'airbag. »
Les machines à transfert rotatif n'étaient pas nécessairement un choix évident pour le travail d'ATP. Selon M. Adams, le serrage peut être un défi avec les machines à transfert rotatif, en particulier avec les types de pièces que l'entreprise produit. "Une grande partie de ce que nous faisons est de forme unique, ce ne sont pas de belles barres rondes", explique-t-il. Cependant, cela est devenu moins problématique avec le temps. "Au fil des ans, j'ai vu le serrage d'Hydromat s'améliorer - la cohérence, d'une station à l'autre", ajoute-t-il. "Dans l'économie d'aujourd'hui, je pense que c'est ce qui distingue Hydromat."
Selon M. Adams, l'avantage des Hydromats est leur rapidité et le volume de pièces qu'ils peuvent produire. Ces caractéristiques entrent en considération lorsque l'atelier décide d'exécuter un travail sur une multibroche ou sur un Hydromat. "Lorsque l'ATP a un volume élevé et qu'il faut de la vitesse, le travail finit par être dirigé vers l'Hydromat", dit-il.

Ron Mourton ajuste le programme Epic sur l'une des machines Hydromat R/T 32/45-16 d'ATP. L'entreprise s'efforce de réduire les temps de cycle en égalisant les temps de coupe à chaque station, en réorganisant les séquences pour réduire les temps de cycle d'aussi peu qu'une demi-seconde.
L'amélioration continue joue également un rôle dans le succès durable de l'entreprise avec l'utilisation des machines Hydromat. Cela signifie ajuster les temps de cycle en examinant la programmation et l'outillage, et réorganiser les stations. « Une fois que vous voyez comment toutes les stations fonctionnent ensemble, l'objectif est d'avoir des temps de coupe égaux à chaque station. L'ATP est bon pour égaliser les temps. Nous allons réorganiser la séquence pour obtenir aussi peu qu'une demi-seconde », déclare M. Adams. « Quand on travaille avec les gens d'Hydromat, ils pensent parfois que nous sommes fous. Nous demandons toujours l'impossible."
Changement de culture

Il y a actuellement six Hydromats à l'usine de Fairview, toutes alimentées par des barres. Trois machines produisent du travail à partir de l'automobile et d'autres travaux plus établis d'ATP. Les trois autres produisent environ 65 000 pièces pour des projets non automobiles nouvellement acquis.
L'introduction des machines à transfert rotatif a radicalement changé l'entreprise. « Dans les cinq à 10 ans suivant l'arrivée de nos premiers Hydromats, 60 à 70 % de nos revenus étaient générés avec nos Hydromats », explique Harry. « Aujourd'hui, on constate que le pourcentage est toujours à peu près le même. Nous sommes principalement un magasin Hydromat. Le vice-président des relations avec la clientèle de l'entreprise, Drew Hoffman, résume la philosophie de l'entreprise en ce qui concerne son utilisation des machines Hydromat :"Nous essayons de produire des pièces complètes rapidement, dans un processus stable, grâce à une machine à transfert rotatif."

Alan Sargent, technicien chez Hydromat, vérifie chaque pièce en aluminium produite sur cette machine Hydromat Epic R/T 32/45-16 alimentée en barres. Les six Hydromats de l'usine ATP de Fairview sont alimentés en barres et produisent des pièces pour une gamme d'industries.
Selon Harry, les changements sont durables. "Cela devient ancré dans votre culture", dit-il. "Ce que je veux dire par là, c'est que lorsque vous commencez à utiliser ce style de machine, vous ne voulez généralement pas faire venir un autre joueur. Nous avons un très bon partenariat avec Hydromat. Nous avons leurs machines depuis 30 ans maintenant."
Alors que Scott et Harry déplacent l'ATP vers l'avenir, ils prennent en considération les changements qui se produisent dans l'industrie automobile. L'entreprise a déjà connu des perturbations dans cette industrie - une pièce de direction hydraulique qu'elle utilise depuis de nombreuses années mourra bientôt, laissant la place à la direction électrique pour prendre complètement le relais. Leur travail sur les moteurs diesel de gros camions a diminué ces dernières années en raison de meilleurs moteurs ayant une durée de vie plus longue, une tendance qui se poursuivra. Et la révolution des véhicules électriques affectera leurs projets de combustibles fossiles à l'avenir. "Nous avons grandi avec l'automobile, donc nous ne sommes pas nécessairement totalement effrayés par les hauts et les bas de celle-ci et par sa compétitivité", conclut Harry. "Mais nous nous tournons certainement vers une gamme plus importante de projets pour la stabilité et la diversification de notre portefeuille de produits." Les frères s'efforcent de diversifier le travail de l'entreprise et d'ajouter plus de variété à sa production de pièces pour aider à aplanir les points difficiles.
En savoir plus
Voici un autre article sur ce sujet :
Une réussite américaine
Une entreprise qui produit des cadenas depuis plus de 150 ans a mis en place une machine à transfert rotatif d'Hydromat, qui a permis d'automatiser la production de pièces tout en maintenant la flexibilité.
Lien :gbm.media/hydromat
Équipement industriel
- Les services de fraisage CNC de haute précision sont très populaires
- Tour d'outillage
- Tour CNC
- Capital humain
- Machines d'impression :impression offset
- Machines d'impression flexo
- Comment l'ajout d'un chargeur de barres à un centre de tournage CNC améliore la valeur de vos machines
- Brocher sur un tour :Brochage rotatif
- Une entreprise de menuiserie haut de gamme améliore son efficacité et ses performances grâce à de nouvelles pompes à vide