Comment 5 grands constructeurs automobiles utilisent l'impression 3D
3ERP a couvert de nombreuses façons différentes dont les constructeurs automobiles bénéficient des avantages que l'impression 3D apporte au premier plan. Alors que la technologie prend de plus en plus d'importance dans l'industrie automobile, de nombreuses entreprises en prennent note, mais beaucoup l'utilisent à des fins différentes et à des fins diverses. Ces besoins peuvent englober n'importe quoi, des outils aux pièces de rechange/gestion de la chaîne d'approvisionnement, en passant par les pièces d'utilisation finale et même les voitures complètes.
Il est intéressant de voir jusqu'où la technologie est arrivée, comment elle est utilisée par les grands noms de l'industrie et où ils la voient évoluer dans leurs futures chaînes de production. Cet article vise à donner un aperçu des nombreuses façons dont certains des plus grands constructeurs automobiles du monde utilisent l'impression 3D dans leur flux de travail.
BMW
Comme la plupart des impressions 3D sont utilisées pour de plus petits volumes de production, il y a beaucoup de place pour la personnalisation et l'ajout de complexité en utilisant les éléments uniques que l'impression 3D permet. BMW n'est pas étranger à ces formes de conception et de fabrication, utilisant l'impression 3D dans le pré-développement, la validation et les tests de véhicules, ou dans les concepts et les voitures d'exposition. Ils utilisent la technologie pour des volumes plus importants, mais des séries de production plus petites leur permettent de personnaliser les produits précisément en fonction des besoins de leurs clients.
L'entreprise a été prolifique dans son utilisation de la fabrication additive, notant qu'elle voit potentiellement "un grand potentiel futur pour la production en série et de nouvelles offres clients » (selon les experts de BMW en Allemagne). Ils ont utilisé la technologie pour améliorer les composants en plastique et en métal. Ils ont surtout travaillé avec HP pour fabriquer des produits sur leurs systèmes de fabrication à grande échelle.
Comme de nombreuses autres entreprises de cette liste, BMW l'utilise comme moyen de produire des pièces que d'autres technologies ne peuvent pas créer. Le capot supérieur de l'i8 Roadster en est un bon exemple. La réalisation du montage de ce composant n'aurait pas été possible en utilisant un procédé de moulage traditionnel. En plus d'élargir les possibilités de conception, la pièce automobile imprimée en 3D est plus durable et pèse également moins que les itérations précédentes.
De même, BMW a dévoilé le coureur de Formule E iFE.20 avec un arbre de refroidissement imprimé en 3D fabriqué à partir de fibres de lin. La pièce a été présentée fin 2019. Par rapport aux matériaux carbone habituels, le lin a une plus grande absorption et une plus grande résistance aux chocs, ce qui peut être avantageux sur les circuits urbains avec leurs bosses et glissières de sécurité, sur lesquels se déroule la Formule E. Cela en a fait la première voiture de course BMW mise en service par une équipe de travail avec des pièces en fibres textiles renouvelables, ce qui la rend également respectueuse de l'environnement.
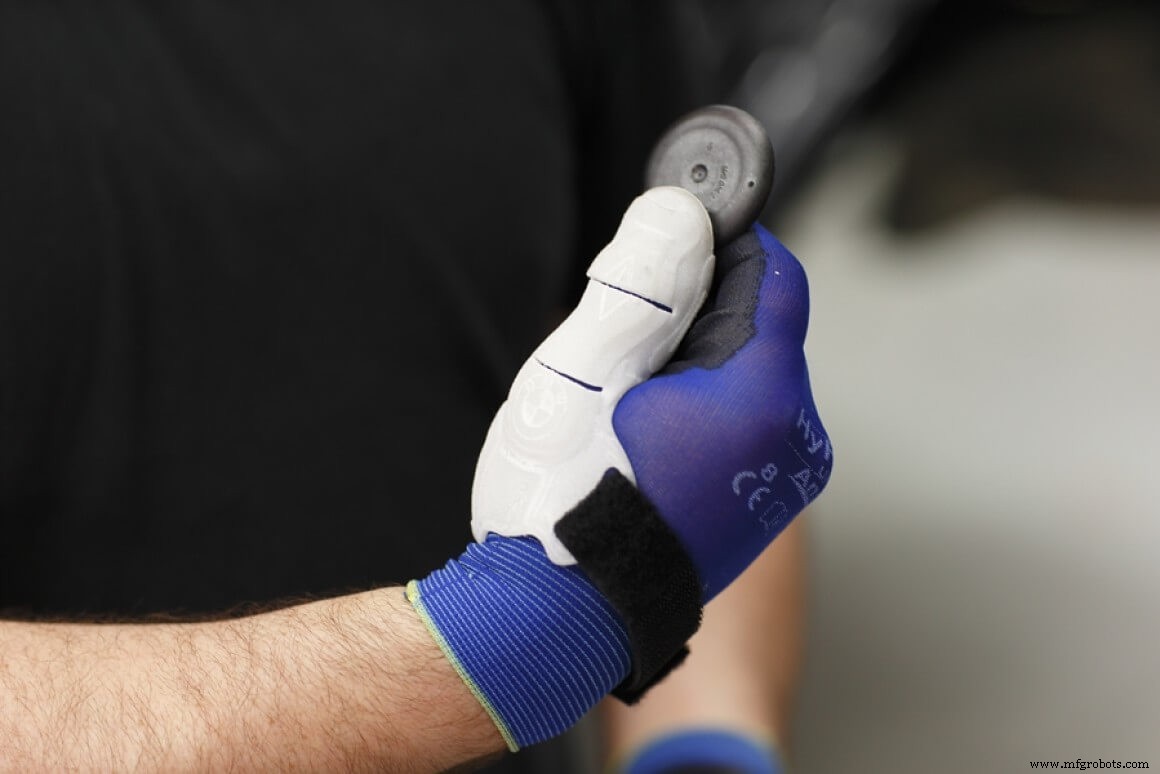
Gants BMW avec pouce protégé
L'entreprise utilise également l'impression 3D pour l'outillage et la sécurité. Un bon exemple de ceci est les gants spécialisés qu'ils utilisent pour finir les bouchons des trous de drainage. Ces butées doivent être réglées manuellement avec les doigts de l'ingénieur, ce qui signifie beaucoup de pression sur les pouces. Heureusement, ils ont trouvé la solution imprimée en 3D qui pouvait être installée sur les gants de travail.
Même en dehors de leur travail sur leurs propres automobiles, les ingénieurs de l'entreprise ont prêté main forte à des projets extérieurs. Un exemple est le développement des sièges imprimés en 3D sur mesure pour l'équipe britannique de basket-ball paralympique. À l'aide de scans corporels 3D et des dernières avancées en matière de fabrication additive, les ingénieurs de BMW ont construit toute une flotte de fauteuils roulants permettant aux joueurs d'afficher un niveau plus avancé de prouesses athlétiques.
Ford
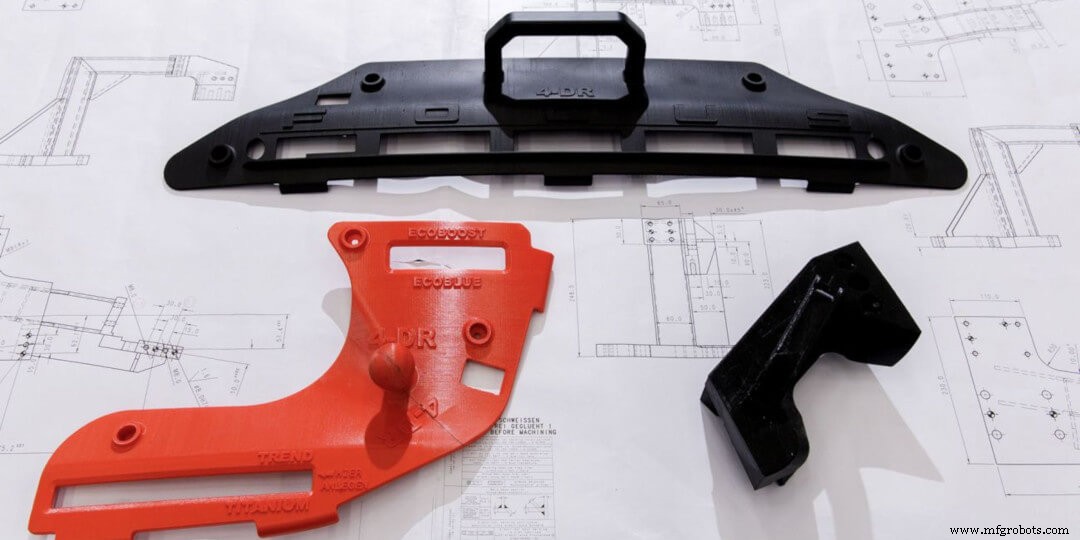
Gabarits et fixations Ford
En ce qui concerne l'engagement envers l'impression 3D, Ford se précipite tête première pour adopter la technologie. L'entreprise a mis en place un centre de fabrication additive et a largement utilisé ses opérations dans ses flux de travail. En termes de création d'impressions plastiques et métalliques, ils entretiennent un partenariat de longue date avec diverses sociétés telles qu'Ultimaker, Stratasys et GE Additive, qui fournissent des machines pour toutes sortes d'applications de fabrication additive tout au long de la chaîne de production.
Ils utilisent également l'impression 3D pour réduire les coûts et le temps d'outillage, car l'entreprise a constaté qu'il était plus rapide de fabriquer ses propres pièces sur place plutôt que d'attendre les fournisseurs et autres choses du genre. Ils appliquent également ces mêmes principes aux gabarits et aux montages, qu'ils développent dans des installations du monde entier.
Ils ont étendu leurs activités d'impression 3D au cours des dernières décennies, fabriquant à la fois des composants en métal et en plastique. Comme l'indique la société :"Au cours des dernières décennies, Ford a imprimé plus de 500 000 pièces et a économisé des milliards de dollars et des millions d'heures de travail. Là où il aurait fallu 4 à 5 mois et coûté 500 000 $ pour produire un prototype avec des méthodes traditionnelles, une pièce imprimée en 3D peut être produite en quelques jours ou quelques heures pour un coût de quelques milliers de dollars ”.
De même, les différentes filiales de Ford ont montré leurs côtelettes AM, notamment les équipes de conception derrière la Shelby GT500. Cette année, ils ont imprimé en 3D les conceptions les plus prometteuses pour la nouvelle GT500 en quelques jours, ce qui a énormément accéléré les étapes d'amélioration et de test. Ce rythme leur permet de peaufiner rapidement la Shelby GT500 petit à petit, en apportant de nouvelles conceptions physiques à des vitesses vertigineuses. Ils ont également développé une nouvelle conception hybride spoiler-aile que l'équipe appelle «la balançoire». Ce nouveau design est un facteur important dans les impressionnantes capacités aérodynamiques de la GT500.
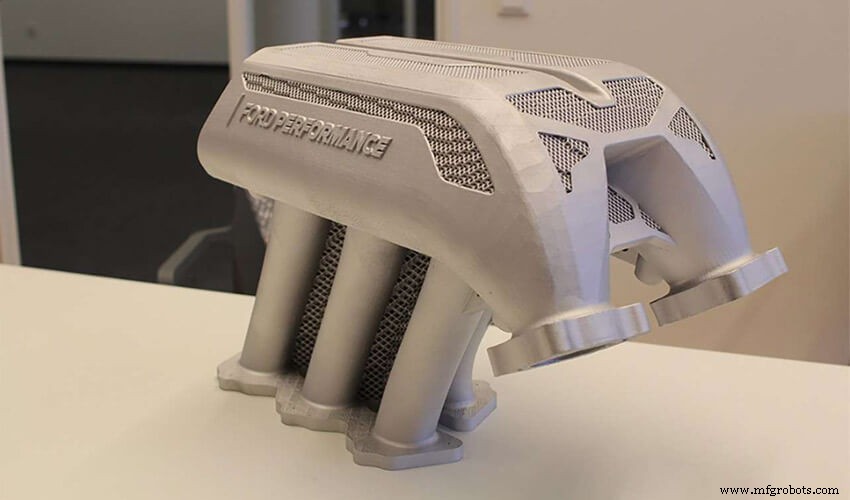
Moteur EcoBoost
La société a franchi une autre étape importante dans l'impression 3D en février. Leur division Ford Performance, qui traite des composants hautes performances, a imprimé en 3D ce qu'ils prétendent être la plus grande pièce automobile en métal pour un véhicule de travail de l'histoire de l'automobile. La partie métallique a été installée dans le Hoonitruck, un Ford F-150 de 1977 avec un moteur V6 EcoBoost biturbo de 3,5 litres. La pièce elle-même est une entrée de collecteur en aluminium, imprimée à l'aide du Concept Laser X LINE 2000R de GE Additive.
Volvo
Bien qu'il ne soit pas l'utilisateur le plus important de l'impression 3D automobile, Volvo a fait de grands progrès sur ce front ces dernières années. Comme beaucoup d'autres entreprises de cette liste, Volvo utilise l'impression 3D pour l'outillage et la gestion de la chaîne d'approvisionnement. L'utilisation de l'impression 3D a été particulièrement utile pour réapprovisionner les machines de l'entreprise avec de nouvelles impressions pour les pièces hors production. Volvo utilise principalement des pièces en plastique imprimées en 3D et envisage la mise en œuvre de pièces en métal dans un avenir proche.
En 2018, l'entreprise utilisait la fabrication additive principalement pour le prototypage et l'outillage. "Comme nous n'avons besoin de produire que de faibles volumes de pièces pour le prototypage, c'est un bon moyen de voir ce qui fonctionne", déclare Fredrick Andersson, ingénieur de développement pour l'installation du groupe motopropulseur des chargeuses sur pneus chez Volvo CE [construction equipment]. « Nous avons beaucoup de connaissances et nous pouvons apporter des modifications rapidement et facilement grâce à l'impression 3D. Et pour cette raison, cela signifie que le délai de mise sur le marché d'un nouveau produit est plus rapide, ce qui est très avantageux pour notre entreprise ."
La vitesse accrue du prototypage a été extrêmement utile à l'entreprise, comme le prouvent diverses nouvelles technologies qu'ils testaient. Par exemple, les ingénieurs de Volvo ont conçu de nouveaux carters de pompe à eau pour les véhicules A25G et A30G de l'entreprise. Ils ont effectué des simulations afin d'optimiser la conception des passages d'écoulement internes dans le boîtier, mais ont dû construire un prototype pour effectuer des tests fonctionnels afin de valider la nouvelle conception. Le coût de l'outillage pour ce projet aurait été d'environ 9 090 $, le coût des pièces étant d'environ 909 $. Le délai de réalisation du prototype aurait été de 20 semaines minimum. D'autre part, l'impression 3D du prototype a coûté 770 $ et n'a pris que deux semaines.
Cependant, en 2019, l'entreprise a fait monter les enchères en termes de processus de FA, notamment avec sa filiale Volvo Trucks. Leur usine de New River Valley (NRV) à Dublin, en Virginie, a fait la une des journaux cette année dans le monde de la fabrication. Ils utilisent principalement SLS, mais se sont également essayés à d'autres méthodes AM. Cette installation particulière produit plus de 500 outils et accessoires de fabrication utilisés dans l'atelier, produits à l'aide de l'impression 3D. L'installation est également une plaque tournante majeure pour l'ingénierie automobile nord-américaine.
Outre les automobiles commerciales, la société développe également des équipements de construction. Effectivement, l'impression 3D a également laissé sa marque sur cet aspect des opérations de l'entreprise. Volvo a appliqué l'impression 3D pour rééquiper ses tombereaux articulés, réduisant ainsi d'un dixième le coût du prototypage. Cela leur a également permis de réduire le temps passé de 20 à seulement 2 semaines.
GM
General Motors et ses diverses autres branches sont les principaux utilisateurs (et développeurs) de la technologie d'impression 3D. En 2018, GM économisait 300 000 $ par an sur l'outillage et progressait suffisamment vers le développement de nouvelles technologies utilisant des sources de carburant alternatives. Le principal constructeur automobile a annoncé l'année dernière qu'il prévoyait de lancer 20 nouveaux modèles électriques et à pile à combustible dans le monde d'ici 2023.
Bien que leurs opérations d'impression 3D se soient largement concentrées sur le prototypage, elles se développent. La société prévoit en outre d'augmenter ses opérations d'impression pour produire "des dizaines de milliers de pièces à grande échelle à mesure que la technologie s'améliore », selon Kevin Quinn, directeur de la conception et de la fabrication additives chez GM. Ce plan est susceptible de se dérouler au cours des 5 prochaines années.
Le Warren Tech Center de la société produit environ 30 000 pièces prototypes chaque année. Les pièces sont constituées d'au moins neuf sortes de matériaux, utilisant des combinaisons de plastiques, de métaux et de poudres. Ils sont principalement utilisés pour le prototypage, mais l'entreprise étudie également les pièces d'utilisation finale. Ils sont également copropriétaires des laboratoires HRL avec Boeing, qui a fini de produire un alliage d'aluminium imprimé en 3D.
Dan Grieshaber, directeur de l'intégration mondiale de la fabrication chez GM, a déclaré que la majorité des usines de GM sont désormais équipées d'imprimantes 3D. L'entreprise prévoit de l'augmenter encore davantage, du moins dans ses usines nord-américaines. Cette décision permettra probablement à GM d'économiser chaque année des millions de dollars en coûts de production. GM investit depuis longtemps dans l'impression 3D et ses diverses technologies de sous-branche. Ils l'appliquent pour la construction rapide d'outils et d'accessoires pour les travailleurs de leurs usines. Cette année encore, l'entreprise a déclaré que la mise en place d'une machine d'impression 3D de 35 000 USD lui avait permis d'économiser 300 000 USD sur deux ans. Bien que la production d'outillage soit le rôle principal joué par l'imprimeur, il est possible que l'entreprise augmente le rôle de la fabrication additive dans ses opérations quotidiennes.
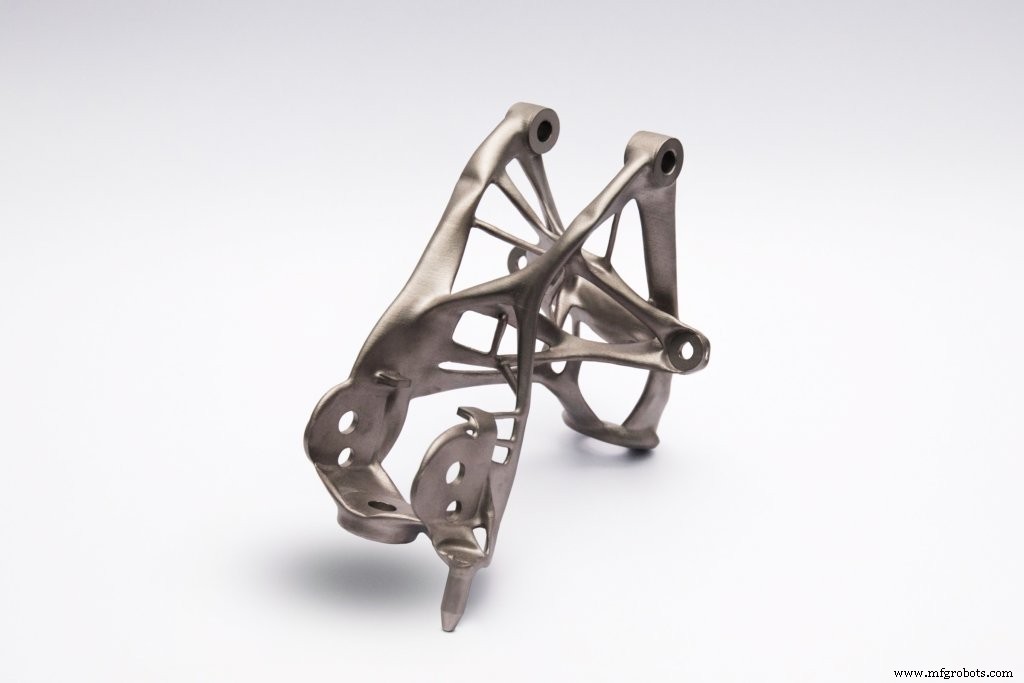
Support de GM développé en collaboration avec Autodesk
Leur partenariat avec Autodesk a été bénéfique dans la fabrication de pièces imprimées en 3D légères qui pourraient aider le constructeur automobile à atteindre ses objectifs d'ajouter des véhicules à carburant alternatif à sa gamme de produits. Faisant également partie de cette même collaboration, les deux sociétés ont présenté en 2019 un support de siège imprimé en 3D en acier inoxydable et développé avec la technologie Autodesk.
Au début de 2019, GM envisageait une nouvelle application de conception novatrice pour l'impression 3D. En collaboration avec Michellin, ils cherchaient à produire un nouveau type de pneu avec une durabilité supérieure. Le pneu Uptis est toujours en cours de développement, mais les entreprises sont passées à la phase de test. Ils affirment que les pneus seraient 100 % durables, résistants et capables de durer encore plus longtemps. Ils sont également une alternative beaucoup plus écologique, avec moins de déchets lors de la production. Récemment, les ingénieurs utilisaient une flotte de Chevrolet Bolt EVs pour tester les nouveaux pneus dans le Michigan, et ont évoqué la possibilité de les mettre à la disposition du public en 2024.
Porsche
Porsche utilise l'impression 3D à diverses fins, des principaux composants à la réinvention de la chaîne d'approvisionnement pour ses anciens modèles. Porsche utilise actuellement l'impression 3D pour produire des pièces de rechange très spécifiques, mais pas de manière aussi intensive. Cela est dû aux normes de qualité strictes qu'ils doivent respecter pour garantir que la sécurité est à la hauteur. L'entreprise travaille également avec un nombre global d'unités produites plus faible car il s'agit davantage de marques de voitures classiques et de luxe.
Pour le développement de composants hors production tels que le levier de débrayage de la Porsche 959, l'entreprise utilise la fusion au laser. Ils utilisent de l'acier à outils en poudre et extraient la pièce beaucoup plus efficacement qu'il ne serait autrement possible avec des méthodes alternatives.
L'utilisation de l'impression 3D a également permis à l'entreprise de s'orienter vers l'impression à la demande, ce qui permet de réduire considérablement les coûts associés aux matériaux, au transport et au stockage. Ceci est également avantageux car ces pièces ne sont pas plus demandées et sont souvent coûteuses à maintenir en production constante. Porsche a notamment collaboré avec Markfordged pour faire revivre ces pièces classiques.
Ils utilisent principalement SLM et SLS pour les différentes pièces qu'ils doivent produire. Porsche a déclaré que les pièces imprimées en 3D sont supérieures aux anciennes dans de nombreux cas. Bien qu'ils impriment actuellement un nombre limité de pièces, ils élargissent le portefeuille depuis 2018 et testent les futurs composants.
commande numérique par ordinateur
- Comment utilisons-nous le molybdène?
- Dans quelle mesure l'impression 3D industrielle est-elle durable ?
- Comment utiliser une fonction en VHDL
- Comment utiliser une machine de découpe acrylique pour couper l'acrylique
- Capteur d'outil du routeur CNC en bois, comment l'utiliser ?
- Comment l'impression 3D est utilisée dans l'industrie de la fabrication de moules
- Comment les fabricants peuvent utiliser l'analytique pour une meilleure expérience client
- Comment fonctionne l'impression offset ?
- Comment utiliser une meuleuse de coupe