Relevez les défis permanents de l'usinage longue portée
Un certain nombre de tendances actuelles dans la fabrication amplifient la difficulté de créer des alésages de précision et d'effectuer des opérations de tournage avec des outils de grande longueur. La demande de tolérances plus strictes et d'une répétabilité sans faille ne cesse de croître. Les nouveaux matériaux de pièce à hautes performances sont plus difficiles à usiner, ce qui augmente les contraintes au sein du système d'usinage. Pour gagner du temps et de l'argent, les fabricants consolident plusieurs pièces en pièces monolithiques uniques qui nécessitent l'usinage d'alésages profonds et le tournage de composants complexes sur des machines-outils multitâches.
Les fabricants qui cherchent à surmonter ces défis doivent étudier tous les éléments de leurs systèmes d'usinage et appliquer des techniques et des outils qui assureront le succès. Parmi les éléments clés figurent la stabilité de la machine, le maintien de l'outil, le serrage de la pièce et la géométrie de l'outil de coupe. En général, une fixation solide, un outillage rigide et une application soignée des outils constituent la base de base pour des processus d'alésage et de tournage précis et productifs.
Les producteurs de pétrole et de gaz, de production d'électricité et de composants aérospatiaux sont des candidats de choix pour des outils et des techniques mis à jour, car ils traitent régulièrement de grandes pièces complexes avec des caractéristiques qui nécessitent l'utilisation d'outils de grande longueur. De nombreuses pièces sont fabriquées à partir d'alliages résistants difficiles à usiner et produisent ainsi des forces de coupe élevées et génératrices de vibrations. En général, presque tous les fabricants peuvent bénéficier d'une amélioration de la productivité et d'une réduction des coûts dans les opérations d'alésage à longue portée.
DÉFLEXION ET VIBRATION
L'alésage profond se distingue des autres opérations de coupe en ce que l'arête de coupe opère dans l'alésage à une distance étendue de la connexion à la machine. Les opérations de tournage intérieur à longue portée présentent des conditions similaires, et ces opérations d'alésage et de tournage peuvent impliquer des trous avec des coupes interrompues, comme c'est le cas sur des pièces telles que des carters de pompe ou de compresseur. La quantité de porte-à-faux résultant de l'outil est dictée par la profondeur du trou et peut entraîner une déviation de la barre d'alésage ou de l'outil de tournage de longueur étendue.
La déviation amplifie les forces changeantes dans un processus de coupe et peut provoquer des vibrations et des vibrations qui dégradent la qualité de la surface de la pièce, usent ou cassent rapidement les outils de coupe et endommagent les composants de la machine-outil, tels que les broches, et entraînent la nécessité de réparations coûteuses et de longues périodes d'arrêt. Les forces variables résultent des déséquilibres des composants de la machine, du manque de rigidité du système ou des vibrations sympathiques des éléments du système d'usinage. Les pressions de coupe changent également lorsque l'outil est périodiquement chargé et déchargé tandis que les copeaux se forment et se cassent. Les effets négatifs des vibrations d'usinage comprennent un mauvais état de surface, des dimensions d'alésage imprécises, une usure rapide de l'outil, des taux de matière réduits, une augmentation des coûts de production et des dommages aux porte-outils et aux machines-outils.
RIGIDITÉ DE LA MACHINE ET FIXATION DE LA PIÈCE
L'approche de base du contrôle des vibrations dans les opérations d'usinage consiste à maximiser la rigidité des éléments du système d'usinage. Pour limiter les mouvements indésirables, une machine-outil doit être construite avec des éléments structurels rigides et lourds renforcés de béton ou d'un autre matériau absorbant les vibrations. Les roulements et les bagues de la machine doivent être serrés et solides.
Les pièces doivent être localisées avec précision et solidement maintenues dans la machine-outil. Les fixations doivent être conçues avec la simplicité et la rigidité comme principales préoccupations, et les pinces doivent être situées aussi près que possible des opérations de coupe. Du point de vue de la pièce, les pièces à paroi mince ou les pièces soudées et celles dont les sections ne sont pas supportées sont sujettes aux vibrations lors de l'usinage. Les pièces peuvent être repensées pour améliorer la rigidité, mais de telles modifications de conception peuvent ajouter du poids et compromettre les performances du produit usiné.
PORTE-OUTILS
Pour maximiser la rigidité, une barre d'alésage ou une barre de tournage doit être aussi courte que possible mais rester suffisamment longue pour usiner toute la longueur de l'alésage ou du composant. Le diamètre de la barre d'alésage doit être le plus grand possible pour s'adapter à l'alésage tout en permettant une évacuation efficace des copeaux coupés.
Au fur et à mesure que les copeaux se forment et se cassent, les forces de coupe augmentent et diminuent. Les variations de force deviennent une source supplémentaire de vibrations qui peuvent interagir en sympathie avec le mode de vibration naturel du porte-outil ou de la machine et devenir auto-entretenues voire augmenter. D'autres sources de telles vibrations incluent les outils usés ou ceux qui ne passent pas assez profondément. Ceux-ci provoquent une instabilité du processus ou une résonance qui se synchronise également avec la fréquence naturelle de la broche d'une machine ou de l'outil pour générer ensuite des vibrations indésirables.
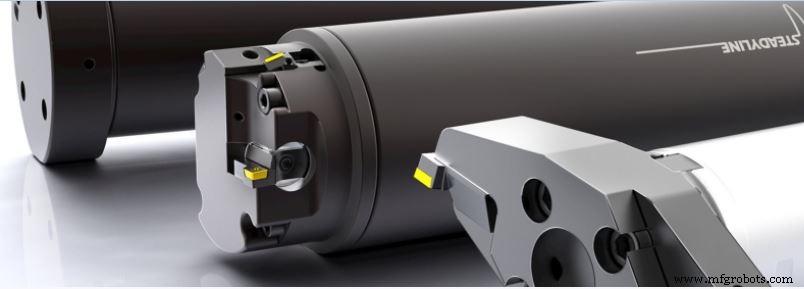
Un long porte-à-faux de la barre d'alésage ou de la barre de retournement peut déclencher des vibrations dans un système d'usinage. L'approche de base du contrôle des vibrations comprend l'utilisation d'outils courts et rigides. Plus le rapport entre la longueur de la barre et le diamètre est grand, plus le risque de vibration est élevé.
Différents matériaux de barre offrent un comportement vibratoire différent. Les barres d'acier sont généralement résistantes aux vibrations jusqu'à un rapport longueur/diamètre de la barre (L/D) de 4:1. Les barres de métaux lourds fabriquées à partir d'alliages de tungstène sont plus denses que l'acier et peuvent supporter des rapports L/D de barres de l'ordre de 6:1. Les barres en carbure monobloc offrent une plus grande rigidité et autorisent des rapports L/D jusqu'à 8:1, avec l'inconvénient possible d'un coût plus élevé, en particulier lorsqu'une barre de grand diamètre est requise.
Une autre façon d'amortir les vibrations implique une barre réglable. La barre comporte un amortisseur de masse interne conçu pour résonner en déphasage avec les vibrations indésirables, absorber son énergie et minimiser le mouvement vibratoire. Le Steadyline ® système de Seco Tools (voir encadré) , par exemple, comporte un amortisseur de vibrations préréglé constitué d'une masse d'amortissement en matériau à haute densité suspendue à l'intérieur de la barre porte-outils par l'intermédiaire d'éléments radiaux absorbants. La masse de l'amortisseur absorbe immédiatement les vibrations lorsqu'elles sont transmises par l'outil de coupe au corps de la barre.
Le contrôle actif des vibrations de l'outillage plus complexe et coûteux peut prendre la forme de dispositifs activés électroniquement qui détectent l'existence de vibrations et utilisent des actionneurs électroniques pour produire un mouvement secondaire dans le porte-outil afin d'annuler le mouvement indésirable.
MATÉRIAU DE LA PIÈCE
Les caractéristiques de coupe du matériau de la pièce peuvent contribuer à la génération de vibrations. La dureté du matériau, une tendance à l'écrouissage ou à l'écrouissage ou la présence d'inclusions dures modifient ou interrompent les efforts de coupe et peuvent générer des vibrations. Dans une certaine mesure, le réglage des paramètres de coupe peut minimiser les vibrations lors de l'usinage de certains matériaux.
GÉOMÉTRIE DE L'OUTIL DE COUPE
L'outil de coupe lui-même est soumis à une déviation tangentielle et radiale. La déviation radiale affecte la précision du diamètre d'alésage. En déviation tangentielle, l'insert est poussé vers le bas en s'éloignant de l'axe de la pièce. En particulier lors de l'alésage de trous de petit diamètre, le diamètre interne incurvé du trou réduit l'angle de dégagement entre la plaquette et l'alésage.
La déviation tangentielle poussera l'outil vers le bas et l'éloignera de l'axe central du composant en cours d'usinage, réduisant ainsi l'angle de dégagement. La déviation radiale réduit la profondeur de coupe, affectant la précision d'usinage et modifiant l'épaisseur des copeaux. Les changements de profondeur de coupe modifient les forces de coupe et peuvent entraîner des vibrations.
Les caractéristiques de la géométrie de la plaquette, notamment le râteau, l'angle d'attaque et le rayon du bec, peuvent amplifier ou atténuer les vibrations. Les plaquettes à angle de coupe positif, par exemple, créent moins d'effort de coupe tangentiel. Mais la configuration à angle de coupe positif peut réduire le jeu, ce qui peut entraîner des frottements et des vibrations. Un grand angle de coupe et un petit angle de coupe produisent une arête de coupe nette, ce qui réduit les efforts de coupe. Cependant, le bord tranchant peut être soumis à des chocs ou à une usure inégale, ce qui affectera la finition de surface de l'alésage.
Un petit angle d'attaque de l'arête de coupe produit des forces de coupe axiales plus importantes, tandis qu'un grand angle d'attaque produit une force dans la direction radiale. Les forces axiales ont un effet limité sur les opérations d'alésage, un petit angle d'attaque peut donc être souhaitable. Mais un petit angle d'attaque concentre également les forces de coupe sur une plus petite section de l'arête de coupe qu'un grand angle d'attaque, avec un effet négatif possible sur la durée de vie de l'outil. De plus, l'angle d'attaque d'un outil affecte l'épaisseur des copeaux et la direction de l'écoulement des copeaux.
Le rayon du nez de la plaquette doit être inférieur à la profondeur de coupe pour minimiser les forces de coupe radiales.
CONTRÔLE DE LA PUCE
L'élimination des copeaux coupés de l'alésage est un problème clé dans les opérations d'alésage. La géométrie des plaquettes, les vitesses de coupe et les caractéristiques de coupe du matériau de la pièce influencent toutes le contrôle des copeaux. Les copeaux courts sont souhaitables en alésage car ils sont plus faciles à évacuer de l'alésage et minimisent les forces sur l'arête de coupe. Mais les géométries de plaquette très profilées conçues pour casser les copeaux ont tendance à consommer plus d'énergie et peuvent provoquer des vibrations.
Les opérations destinées à créer une bonne finition de surface peuvent nécessiter une faible profondeur de coupe qui produira des copeaux plus fins qui amplifient le problème de contrôle des copeaux. L'augmentation de la vitesse d'avance peut casser les copeaux, mais peut augmenter les forces de coupe et générer des vibrations, ce qui peut affecter négativement les finitions de surface. Des vitesses d'avance plus élevées peuvent également provoquer des arêtes rapportées lors de l'usinage d'aciers à faible teneur en carbone, de sorte que des vitesses d'avance de coupe plus élevées associées à une alimentation interne optimale en liquide de refroidissement peuvent constituer une solution de contrôle des copeaux lors de l'alésage de ces alliages d'acier plus malléables.
CONCLUSION
L'alésage et le tournage de trous profonds avec des outils de grande longueur sont des opérations de coupe de métal courantes et essentielles. La réalisation efficace de ces processus nécessite une évaluation du système d'usinage dans son ensemble pour s'assurer que les multiples facteurs impliqués dans la réduction des vibrations et la garantie de la qualité du produit fonctionnent ensemble pour atteindre une productivité et une rentabilité maximales.
Précédemment présenté sur le site d'actualités de SECO.
Technologie industrielle
- Les principales différences entre l'usinage 3 axes et 5 axes
- Déséquilibre :le problème caché que les ateliers d'usinage doivent résoudre
- Maîtriser les défis du tournage dur
- Usinage du titane :trouver les bons outils de fraisage pour les superalliages
- Mettre l'inspection de surface entre les mains de l'opérateur de la machine-outil
- Leçons d'usinage haute performance :n'oubliez pas les porte-outils
- L'importance des liquides de refroidissement dans l'usinage
- Les avantages de l'usinage CNC 5 axes
- Le cœur des machines-outils :les broches de machines-outils.